1. خصائص مادة السيليكون
A. تكون مواد السيليكون الخام بشكل عام شبيهة بالهلام، وتشبه إلى حد ما البلاستيسين، وهي عديمة اللون وشفافة وعديمة الرائحة.
B. وتتمثل ميزاته الرئيسية في كل من مقاومة درجات الحرارة العالية (حتى 300 درجة مئوية) ومقاومة درجات الحرارة المنخفضة (بحد أدنى -100 درجة مئوية)، وهو أفضل مطاط مقاوم للبرودة ومقاوم لدرجات الحرارة العالية في الوقت الحاضر؛ وفي الوقت نفسه، يتمتع بعزل كهربائي ممتاز وثبات عالٍ للأكسدة الحرارية والأوزون، خامل كيميائياً.
العيب هو أن القوة الميكانيكية منخفضة، ومقاومة الزيت، ومقاومة المذيبات، ومقاومة الأحماض والقلويات ضعيفة، ومن الصعب الفلكنة، والسعر أغلى. درجة حرارة التشغيل: -60 ℃ ~ + 200 ℃. ما سبق هو وصف مطاط السيليكون في الدليل
C. درجة حرارة الاستخدام: كما ذكرنا أعلاه، يتم ضبطها بشكل عام على -40 درجة مئوية إلى 200 درجة مئوية، ويمكن أن تصل إلى 230 درجة مئوية في وقت قصير.
D. مشكلة الشيخوخة: مقاومة الزيت ومقاومة الأحماض والقلويات ضعيفة ولا علاقة لها بالإجهاد.
E. مشكلة الالتصاق: قبل المعالجة السطحية، بالإضافة إلى استخدام منتجات السيليكون كمواد لاصقة للالتصاق بأجزاء السيليكون، يجب أن يكون الالتصاق بالأجزاء الأخرى منشطًا على السطح، ويمكن معالجة سطح الغراء بالفلكنة.
ويشار إلى جميع المواد التي يمكن أن تتفاعل مع المطاط أو تجعله يتفاعل مع المطاط أو تجعله يترابط بشكل جماعي باسم عوامل الفلكنة، والمعروفة أيضاً باسم عوامل الربط المتقاطع. وهناك أنواع عديدة من عوامل الفلكنة، ولا تزال تتزايد.
تشمل عوامل الفلكنة التي تم استخدامها الكبريت والسيلينيوم والتيلوريوم والمركبات المحتوية على الكبريت وأكاسيد المعادن والبيروكسيدات والراتنجات والكوينونات والأمينات.
F. صلابة المواد: وفقًا لصلابة Shore، يمكن نظريًا اختيار الأجزاء البلاستيكية بين 10 درجات و80 درجة في السوق المحلية.
وتتراوح درجة الحرارة التي يمكن العثور عليها بسهولة بين 20 و70 درجة بشكل عام، وتتراوح درجة الحرارة الأكثر استخداماً بين 40 و50 درجة.
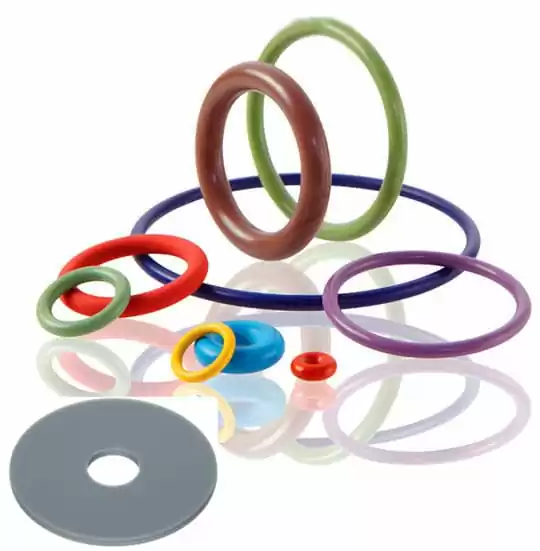
2. عملية إنتاج منتجات السيليكون
ج: شكل ولون المواد الخام
ب: بعد مطابقة الألوان والعجن، يتم تحويل الرقائق ذات الألوان المختلفة من هلام السيليكا الأبيض اللبني
ج: بعد العجن والتشكيل، يتم ضغط المواد الخام إلى شرائح وتقطيعها إلى شرائح
د: القولبة بالحرارة
E: التشذيب وإزالة الحواف والفحص والتعبئة والتغليف
و: انتهى منتجات السيليكون
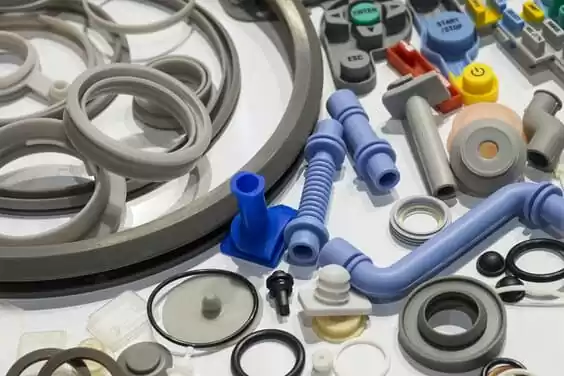
3. حجم المنتج وخصائصه
A. الحد من الحجم: يمكن أن يكون الجزء الأكثر سُمكًا 15 ~ 20 مم، إذا كان كرويًا، يمكن أن يكون القطر 30 مم. بشكل عام، السمك الموصى به لا يزيد عن 3 مم.
عندما يكون أكبر من 3 مم، سوف يستغرق وقتًا أطول للفلكنة ويزيد من التكلفة. يمكن أن يصل أنحف جزء من الناحية النظرية إلى 0.2 مم، ولكن يتم أخذ أنحف 0.3 مم بشكل عام في التصميم، ويوصى بـ 0.4 مم.
B. الحجم النسبي: من حيث اختلاف السماكة، يوصى بألا يتجاوز الجزء الأرفع والجزء الأكثر سماكة 3 مرات. وتعتمد هذه المشاكل أساساً على متطلبات درجة الحرارة والضغط عند فلكنة المادة.
C. معدل الانكماش: معدل انكماش مادة السيليكون يرتبط بصلابة المادة. معظم المواد الثانوية المقدمة من الشركة المصنعة تتراوح صلابتها بين 1.022 و1.042.
بالنسبة للمواد التي تتراوح درجتها من 40 إلى 50 درجة، يكون معدل الانكماش بشكل عام 1.03. ومقارنةً بالبلاستيك، لا تعاني منتجات السيليكون من عيوب سطحية ظاهرة مماثلة بسبب الانكماش.
D. دقة الأبعاد: لأن معظم منتجات مطاط السيليكون هي قالب واحد ذو تجاويف متعددة، وعدد التجاويف كبير جدًا مقارنة بالمنتجات البلاستيكية. لذلك، فهي ليست مريحة مثل المنتجات البلاستيكية في التحكم في الحجم.
الدقة العامة زائد أو ناقص 0.1، والمنتج عالي الدقة زائد أو ناقص 0.05. عند استخدامه لمطابقة ثقب الجزء البلاستيكي والزر، فإن الحد الأدنى للخلوص هو 0.1 لكل جانب، والقيمة الموصى بها هي 0.2 لكل جانب.
E. تصميم الشكل: بالنسبة لأجزاء الأكمام المطاطية، يكفي عمومًا تقديم الرسم الأصلي لمصنع القوالب وفقًا لرسم شكل المنتج، وشرح مشكلة المطابقة، والتي يقررها مصنع القوالب.
في ظل الظروف العادية، واعتمادًا على حجم المنتج، يكون التنسيق بين الغلاف المطاطي والمنتج عمومًا انحرافًا سلبيًا يتراوح بين 0.2 و0.5 صغيرًا على جانب واحد.
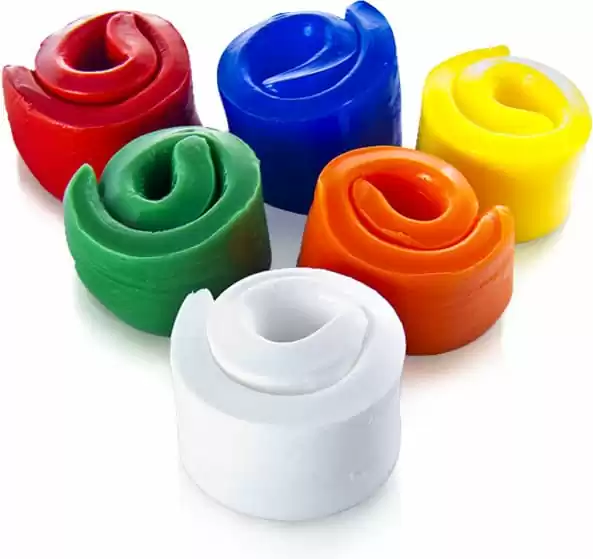
4. هيكل القالب
A. الحد الأعلى لسُمك القالب:
مبدئيًا 250 مم، يمكن أن يصل الحجم إلى 500 × 500، ويمكن أن يصل حجم المنتج إلى 400 × 400 في منطقة القالب. ينقسم هيكل القالب بشكل عام إلى القالب العلوي والقالب السفلي واللوحة السفلية واللوحة السفلية واللوحة العلوية ودبوس القاذف وقلب القالب والمفصلة والأجزاء المساعدة الأخرى. عند تصميم منتجات السيليكون، يجب الانتباه إلى خصائص قوالبها وعمليات إنتاجها:
B. إزالة القوالب:
يمكن تحرير تحرير منتجات السيليكون مباشرة وبقوة. بالنسبة للمنتجات التي لا تحتوي على عيوب في التصميم، يكمن الحجم المطلوب للإفراج القسري بشكل أساسي في نسبة محيط الجزء الأكبر من قلب القالب إلى أصغر جزء إغلاق أثناء عملية إزالة القالب. بالنسبة للمنتجات التي تقل عن 55 درجة، يمكن القيام بذلك 2-3 مرات. قد تكون هناك انشقاقات وزوايا حادة عند الفتحة.
ونظرًا لأن درجة حرارة 180 درجة مئوية مطلوبة أثناء عملية الفلكنة، فإن أعمال إزالة القوالب كلها تقريبًا يدوية باستثناء الفصل العلوي والسفلي للقالب نفسه. لذلك، يجب مراعاة راحة وسرعة الإزالة في تصميم الأجزاء.
حتى لا تؤثر على جودة الفلكنة وكفاءة الإنتاج الضخم للأجزاء بسبب طول وقت إزالة القالب. نظرًا لأن طريقة تحرير السيليكون يدوية بشكل أساسي، كما أن شوط عمل اللوحة العلوية صغير أيضًا، فإن قالب السيليكون ليس له سطح مائل مقارنةً ب قالب بلاستيك. بشكل عام، لا يتم توفير أي سحب أساسي.
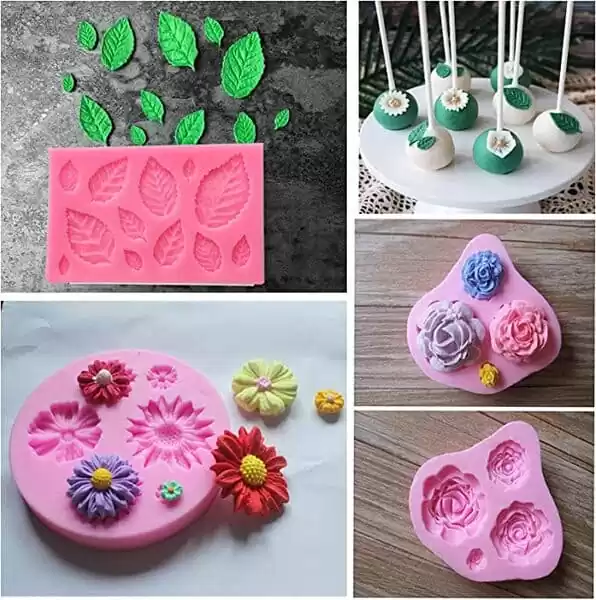
C. تثبيت النواة:
على عكس القوالب البلاستيكية، تتم إزالة أنوية قوالب السيليكون بشكل عام مع أجزاء المنتج عند قالب الحقن يتم فتحه وإخراج الأجزاء. ولذلك، يكون التثبيت والتثبيت الدقيق لقلب القالب أكثر صعوبة من القالب البلاستيكي، وتكون صلابة قلب القالب أعلى.
يتم تصنيع القوالب بشكل عام معًا ويتم تثبيت جميع القوالب مرة واحدة. أو يتم تمرير قلب القالب من خلال أدوات مساعدة لتمكين وضعه بسرعة. ونظرًا لوجود ضغط كبير في عملية تثبيت القالب، فمن الضروري منع قلب القالب من الحركة بشكل صارم.
D. السحب الأساسي:
بشكل عام، لا يمكن تحريكه تلقائيًا، ولكن يمكن إجباره على الإيقاف، ويستخدم السحب الأساسي فقط للهياكل صغيرة الحجم. يتشابه إعداد السحب الأساسي مع إعدادات قالب بلاستيكولكن يتم إزالته يدويًا عند فتح القالب.
بالإضافة إلى ذلك، يحتل السحب الأساسي مساحة كبيرة في القالب، وهو أمر ليس معقدًا فقط في المعالجة الزائدة قالب سيليكون في قالب واحد ولكن لديها أيضًا استخدام منخفض لمساحة القالب. لذا لا تسحب القلب قدر الإمكان.
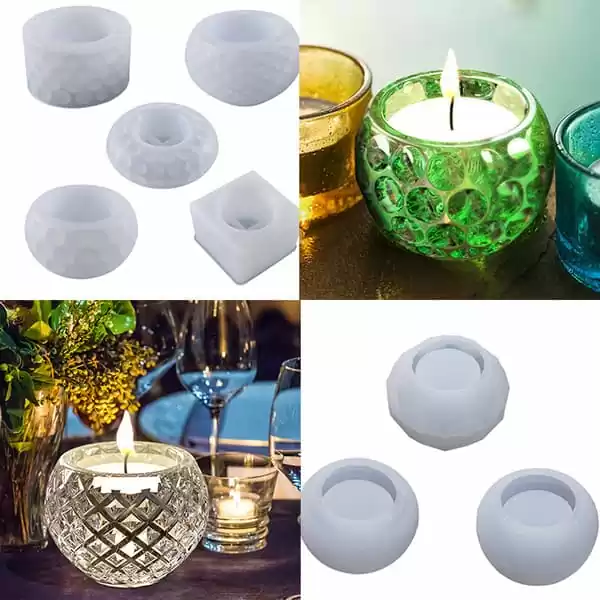
E. الشكل:
تتمتع منتجات السيليكون بصلابة كبيرة عندما يكون السطح سليمًا، ولكن بمجرد وجود تشققات، فإن التشققات ستتوسع بسرعة تحت تأثير القوة الخارجية. ومع ذلك, منتجات السيليكون حساسة جداً للتشققات.
وبالنظر إلى هذه المشاكل، يجب الانتباه إلى التصميم الصحيح لقطع السيليكون في القالب: يجب ألا تكون هناك زوايا حادة في جميع المواضع، لتجنب تركيز الإجهاد والتشققات. يجب ألا تقل زاوية R عند الفتحة عن 0.5.
F. حافة ذاتية الإزالة:
الوظيفة الرئيسية للحافة ذاتية الإزالة: هي استيعاب المطاط الزائد؛ وتسهيل عادم القالب؛ وسهولة تقليم الوميض.
تتكون حافة الإزالة الذاتية بشكل عام من حافة رقيقة عند السطح الفاصل للجزء وحافة تمزيق قوية نسبيًا مقابلة. يتراوح سمك الحافة الرفيعة بشكل عام بين 0.1 و0.2، وسمك حافة التمزيق بشكل عام 0.8، والعرض بشكل عام 1 إلى 2 مم.
ز. إدراج:
يمكن وضع أنواع مختلفة من الإدخالات في منتجات السيليكون، ولكن يجب الانتباه إلى عدة أمور أولاً، يجب معالجة سطح الأجزاء المدمجة مسبقًا، وخاصةً الفلكنة السطحية أو تنشيط السطح.
وإلا، سيكون من الصعب ربط الملحق والغراء بإحكام. والثاني هو الموضع الثابت للإدخال، والذي يمكن تثبيته في اتجاه واحد في الاتجاه الرأسي ولكن يجب أن يكون ثابتًا تمامًا في الاتجاهات الأخرى. لتجنب حركة الإدخال أثناء عملية القالب الكاملة.
والثالث هو سمك الغراء حول الحشوة. بالنسبة للأجزاء المغلفة بالكامل (حيث تكون جميع الأسطح مغلفة، بحيث لا يمكن وضع الملحق)، يجب استخدام سمك لا يقل عن 0.5 مم حول الملحق. بالنسبة للإدخالات ذات التموضع، يجب أن تكون سماكة الطبقة اللاصقة المحيطية أعلى من 0.4 مم.
H. عمليات مساعدة أخرى:
عملية الحقن بالغراء (اللصق):
على غرار القولبة بالحقن في هذه العملية، يتم تثبيت الأجزاء المراد حقنها أولاً، ويتم إغلاق الطبقة الأولى من القالب للتحكم في أن المواد الخام لن تلوث الأجزاء غير المصممة للحقن أثناء الحقن. ثم يتم إغلاق الطبقة الثانية من القالب، ويتم ضغط المركب المطاطي في شكله.
عملية التدوير: تشكيل المطاط أولاً بأول
القوالب: يمكن استخدام عملية التصنيع هذه في حالة التغليف الكامل.
الغمس: تكون المادة الخام للجسم المطاطي (المطاط) سائلة، ويتم غمس قطعة العمل في المادة الخام عدة مرات. يتم تفلكن الطبقة الداخلية من المادة الخام ثم تغمس مرة أخرى حتى يتم الوصول إلى سمك التصميم.
إيبوكسي: تتميز المادة الخام بسيولة جيدة، تشبه الطلاء، ويتم فلكنتها في درجة حرارة الغرفة. والقالب عملية بسيطة نسبيًا، وعادةً ما تكون يدوية، ويتم تطبيق الطلاء التالي عندما يتم معالجة الطبقة الأولى بسرعة.
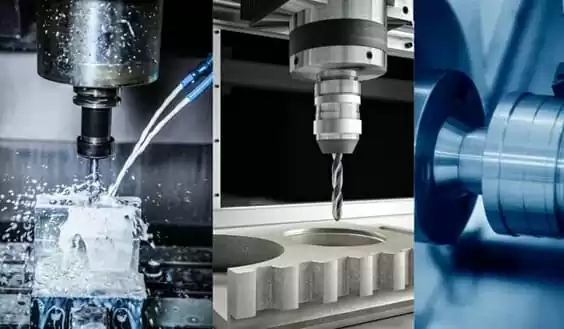
L. منتجات متعددة الألوان:
ينقسم "أ" إلى مجموعتين من قوالب الفلكنة، و"ب" ملونة يدويًا، وبمجرد أن يتم الفلكنة، يجب أن يكون الجزء الفاصل بين الألوان في الأجزاء على ارتفاع معين، لتجنب الجمع بين مزيج من خلط الألوان الموصلة اللاصقة الموصلة والسيليكون المفلكن الثانوي و السيليكون (المطاط) يمكن أن تكون مفلكنة مباشرة دون معالجة الترابط 5. قياس الصلابة والأدوات.
يُطلق على الأداة الأكثر استخداماً لقياس صلابة المطاط اسم مقياس شور (المعروف أيضاً باسم شور). استخدم زنبركاً للضغط على أداة معدنية في سطح المادة وقياس مدى عمقها.
تقيس الأداة أعماق الاختراق من صفر إلى 0.100 بوصة. تعني قراءة الصفر على المقياس أن أداة القياس قد اخترقت العمق المحدد، بينما تعني قراءة 100 أن عمق الاختراق هو صفر. هناك العديد من أجهزة اختبار صلابة الشاطئ ذات نطاقات صلابة ودرجات مختلفة من الأتمتة.
أحد المقاييس الأكثر استخدامًا هو مقياس Shore A. تحتوي مقاييس التحمل Shore A على مقياس Shore A على نقطة إزاحة غير حادة ونابض متوسط. عندما تكون القراءات أعلى من 90، يصبح مقياس التحمل Shore A غير دقيق. بالنسبة لمثل هذه المواد الأكثر صلابة، يتم استخدام مقياس التحمل Shore D. وهو مزود بمقياس متانة حاد ونابض قوي للاختراق العميق.
عند قياس المواد البلاستيكية الأكثر صلابة، استخدم مقياس تحمّل مزود بمقياس تحمّل أكثر حدة ومرونة، مثل مقياس التحمل Rockwell. وفي الطرف المقابل، تُستخدم مقاييس التحمل Shore 00 لقياس المواد الهلامية اللينة والمطاط الرغوي.

يمكن لمعظم المواد المتعددة تحمل الإجهاد الأولي، ولكن بمرور الوقت ستخضع بسبب الزحف والاسترخاء. يمكن أخذ قراءات مقياس التحمل على الفور أو بعد فترة تأخير معينة، عادةً من 5 إلى 10 ثوانٍ. ستُظهر القراءات الفورية دائمًا قراءات أعلى (أو أصعب) من القراءات المتأخرة.
لا تمثل قراءات التأخير أكثر تمثيلاً ليس فقط لصلابة المادة ولكن أيضًا لمرونتها. فالمادة الأضعف والأقل مرونة تكون أكثر عرضة للزحف من تلك الأقوى والأكثر مرونة.
لضمان صحة البيانات، يلزم وجود إجراءات اختبار دقيقة. وللحصول على قراءة دقيقة، يجب أن يكون لديك قطعة اختبار مسطحة وسميكة بما فيه الكفاية بحيث لا تتأثر المسافة البادئة بسطح الدعم.
عادةً ما تكون السماكة المطلوبة هي 0.200 بوصة، ولكن يمكن اختبار المواد الصلبة ذات التشوه الأقل سُمكًا بدقة عند وجود سماكة أقل.