مقدمة:
إن قولبة مطاط السيليكون بالضغط هي عملية تصنيع مستخدمة على نطاق واسع تتضمن تشكيل مطاط السيليكون السائل ومعالجته في تجويف قالب. تشتهر هذه الطريقة متعددة الاستخدامات بقدرتها على إنتاج منتجات متينة ومقاومة للحرارة. ومع ذلك، عندما يتعلق الأمر بالإنتاج بكميات كبيرة، يمكن أن تنشأ بعض التحديات التي تتطلب دراسة متأنية وحلولاً استراتيجية.
يجلب الإنتاج بكميات كبيرة تحديات فريدة من نوعها في قولبة مطاط السيليكون بالضغط. يمكن أن يؤثر حجم الإنتاج وسرعته على عوامل مثل اتساق تعبئة القالب، وكفاءة وقت الدورة، وحدوث عيوب مثل الوميض. يمكن أن تعيق هذه التحديات الإنتاجية، وتؤثر على جودة المنتج، وتزيد من تكاليف التصنيع إذا لم يتم معالجتها بشكل صحيح.
تعتبر معالجة هذه التحديات ذات أهمية قصوى للتصنيع الناجح. من خلال فهم الاستراتيجيات الفعالة وتنفيذها، يمكن للمصنعين تحسين عملية القولبة بالضغط، وتقليل مشكلات الإنتاج، وتحقيق جودة متسقة في الإنتاج بكميات كبيرة. وهذا يضمن تلبية المنتجات لمتطلبات السوق، والالتزام بالمواصفات الصارمة، وتوفير أداء موثوق به.
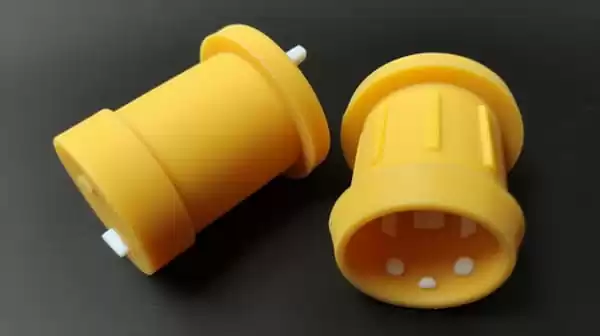
في الأقسام التالية، سوف نتعمق في الأقسام التالية في التحديات المحددة التي تواجهنا في قولبة مطاط السيليكون عالي الحجم بالضغط واستكشاف رؤى قيمة حول كيفية التغلب عليها بفعالية. من خلال معالجة هذه التحديات بشكل مباشر، يمكن للمصنعين إطلاق الإمكانات الكاملة للإنتاج بكميات كبيرة وتقديم منتجات مطاط السيليكون الاستثنائية لمختلف الصناعات.
مشاكل القولبة بالضغط:
على الرغم من أن القولبة بالضغط عملية تصنيع مستخدمة على نطاق واسع، إلا أنها لا تخلو من التحديات. غالبًا ما يواجه المصنعون العديد من المشاكل الشائعة التي يمكن أن تؤثر على كفاءة الإنتاج وجودة المنتج. فيما يلي بعض المشكلات الرئيسية المرتبطة بالقولبة بالضغط:
1- تعبئة قوالب غير متناسقة:
يعد تحقيق ملء القوالب بشكل متسق أمرًا ضروريًا للحصول على منتجات مصبوبة بشكل متسق. في الإنتاج بكميات كبيرة، يمكن أن تحدث اختلافات في تدفق المواد وتوزيعها، مما يؤدي إلى ملء غير متسق لتجاويف القالب. يمكن أن يؤدي ذلك إلى اختلافات في أبعاد القِطع، وعيوب في السطح، وضعف جودة المنتج.
2- أوقات الدورات الأطول:
بالمقارنة مع تقنيات القولبة الأخرى مثل عملية القولبة بالحقن، فإن عملية القولبة بالضغط تستغرق وقتًا أطول للدورة بشكل عام. تنطوي العملية على ضغط مطاط السيليكون ومعالجته داخل القالب، وهو ما قد يستغرق وقتًا أطول. في الإنتاج بكميات كبيرةفإن أزمنة الدورات الأطول يمكن أن تحد من الإنتاج الكلي وتبطئ عملية التصنيع.
3- تشكيل الوميض:
يشير الوميض إلى المواد الزائدة التي تتسرب من تجويف القالب أثناء التشكيل بالضغط. ويحدث ذلك بسبب عوامل مثل التصميم غير السليم للقالب أو كمية المواد الزائدة أو قوة التثبيت غير الكافية. لا يؤدي تكوّن الوميض إلى إهدار المواد فحسب، بل يتطلب أيضًا معالجة إضافية بعد المعالجة لإزالة أو تقليم المواد الزائدة. ويؤدي ذلك إلى زيادة تكاليف الإنتاج ومشاكل محتملة في الجودة.
يمكن أن تؤثر هذه المشاكل بشكل كبير على كفاءة الإنتاج وجودة المنتج في التشكيل بالضغط بكميات كبيرة. يمكن أن يؤدي الملء غير المتناسق للقالب إلى قطع ذات أبعاد وعيوب سطحية متفاوتة، مما يؤدي إلى رفض المنتجات وزيادة النفايات. يقلل زمن الدورة الأطول من إجمالي الإنتاج، مما يؤثر على القدرة على تلبية متطلبات السوق. لا يؤدي تشكيل الوميض إلى زيادة هدر المواد فحسب، بل يتطلب أيضًا وقتًا وموارد إضافية للمعالجة اللاحقة، مما يؤثر على الإنتاجية الإجمالية وفعالية تكلفة عملية التصنيع.
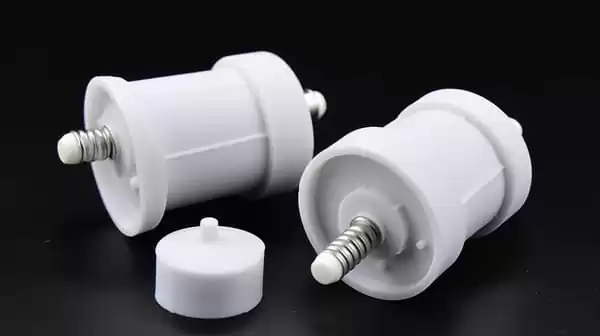
إن معالجة هذه المشاكل أمر بالغ الأهمية لضمان إنتاج فعال وعالي الجودة. وسنستكشف في الأقسام التالية الاستراتيجيات الفعالة للتغلب على هذه التحديات في ضغط مطاط السيليكون عالي السيليكون عالي الحجم وتطبيقات القولبة بالحقن. من خلال تنفيذ هذه الاستراتيجيات، يمكن للمصنعين تحسين العملية وتعزيز الإنتاجية وتقديم منتجات فائقة الجودة لتلبية متطلبات السوق.
العيوب الرئيسية للقولبة بالضغط:
العيب الرئيسي للقولبة بالضغط، خاصةً في سيناريوهات الإنتاج بكميات كبيرة، هو بطء سرعة الإنتاج مقارنةً بتقنيات القولبة الأخرى. على عكس العمليات الأسرع مثل القولبة بالحقن، فإن القولبة بالضغط تتضمن خطوات إضافية مثل تحضير المواد، والتحميل اليدوي أو الآلي للقالب وضغط مطاط السيليكون ومعالجته. وتساهم هذه الخطوات في إطالة زمن الدورة، مما قد يحد من الإنتاج الكلي ويؤثر على كفاءة التصنيع بكميات كبيرة.
إن الآثار المترتبة على تباطؤ سرعة الإنتاج في القولبة بالضغط بكميات كبيرة كبيرة كبيرة. أولاً، يمكن أن يعيق القدرة على الوفاء بالمواعيد النهائية الضيقة للإنتاج ومواكبة متطلبات السوق. قد لا تتماشى أزمنة الدورات الأطول المرتبطة بالقولبة بالضغط مع معدلات الإنتاج المطلوبة لتلبية الطلبات الكبيرة في إطار زمني قصير. وقد يؤدي ذلك إلى التأخير في تسليم المنتج وربما يؤثر على رضا العملاء.
علاوة على ذلك، يمكن أن يكون لبطء سرعة الإنتاج آثار مالية. وغالبًا ما يهدف الإنتاج بكميات كبيرة إلى تحقيق وفورات الحجم، حيث تساعد كميات الإنتاج الأعلى على خفض تكاليف الوحدة الواحدة. ومع ذلك، فإن السرعة الأبطأ للقولبة بالضغط يمكن أن تقلل من الإنتاج الكلي، مما يؤدي إلى ارتفاع تكاليف الإنتاج لكل وحدة. ويمكن أن يؤثر ذلك على الربحية والقدرة التنافسية في السوق.
بالإضافة إلى ذلك، يمكن أن تؤثر سرعة الإنتاج البطيئة على القدرة على التكيف بسرعة مع تغيرات السوق أو إدخال تصميمات جديدة للمنتجات. في الصناعات سريعة الوتيرة، تعد القدرة على الاستجابة السريعة لمتطلبات السوق أو تعديلات التصميم أمرًا بالغ الأهمية. يمكن للطبيعة التي تستغرق وقتًا طويلاً للقولبة بالضغط أن تحد من خفة الحركة والمرونة في التصنيع.
وعلى الرغم من هذا العيب، فإن القولبة بالضغط تقدم مزايا من حيث تعدد الاستخدامات وخيارات المواد والقدرة على التعامل مع الأشكال الهندسية المعقدة للأجزاء. وغالبًا ما تكون مفضلة لتطبيقات محددة تتطلب خصائص فريدة أو تصميمات معقدة. من خلال تنفيذ استراتيجيات لتحسين العملية وتقليل أزمنة الدورات، يمكن للمصنعين التخفيف من تأثير تباطؤ سرعة الإنتاج وتعظيم فوائد القولبة بالضغط في سيناريوهات الإنتاج بكميات كبيرة.
العوامل المؤثرة في عملية القولبة بالضغط:
تؤثر العديد من العوامل الرئيسية على عملية التشكيل بالضغط، حيث تلعب دورًا حاسمًا في ملء القالب والضغط وإزالة القوالب وجودة المنتج بشكل عام. يعد فهم هذه العوامل وإدارتها بفعالية أمرًا ضروريًا لتحقيق نتائج متسقة وعالية الجودة. دعونا نستكشف العوامل الرئيسية:
1- تصميم القالب:
يلعب تصميم القالب دورًا حيويًا في التشكيل بالضغط. تؤثر عوامل مثل تجاويف القالب، وأنظمة العدّاء، وخطوط التقسيم على تدفق المواد، وملء القالب، وضغط القِطع. تعمل القوالب المصممة جيدًا على تسهيل توزيع المواد بشكل موحد، مما يضمن اتساق أبعاد القِطع وتقليل حدوث العيوب.
2- درجة حرارة القالب:
يعد التحكم في درجة حرارة القالب أمرًا بالغ الأهمية في التشكيل بالضغط. تؤثر درجة حرارة القالب على تدفق المواد، وعملية الفلكنة، وخصائص الأجزاء. تضمن الإدارة السليمة لدرجة حرارة القالب التدفق الأمثل للمواد في تجاويف القالب، وتعزز المعالجة المنتظمة، وتعزز الخواص الميكانيكية للمنتج النهائي.
3-قوة التثبيت:
تعتبر قوة التشبيك المناسبة ضرورية لتحقيق الضغط المناسب وتوحيد الجزء. يمكن أن تؤدي قوة التشبيك غير الكافية إلى ملء غير كامل وجودة رديئة للقطع، في حين أن القوة المفرطة يمكن أن تسبب تكوين وميض. ويضمن التحكم الدقيق في قوة التشبيك بعناية ضغطًا موحدًا عبر تجاويف القالب، مما يؤدي إلى اتساق أبعاد القِطع وصقل السطح.
4- خواص المواد:
تؤثر خصائص مادة مطاط السيليكون المستخدمة في التشكيل بالضغط تأثيرًا كبيرًا على العملية وجودة المنتج. تؤثر اللزوجة ووقت المعالجة والمطاط عالي القوام والخصائص الميكانيكية للمادة على ملء القالب والتدفق وأداء الجزء النهائي. يعد اختيار المادة المناسبة ذات الخصائص المناسبة للتطبيق أمرًا بالغ الأهمية لتحقيق النتائج المرجوة.
5- عوامل إطلاق القوالب:
تُستخدم عوامل تحرير القوالب لتسهيل إزالة القوالب من الأجزاء المعالجة من القالب. يقلل الاستخدام السليم لعوامل تحرير القوالب من الالتصاق ويضمن إزالة الأجزاء بسلاسة، مما يقلل من مخاطر التلف أو العيوب أثناء إزالة القوالب.
6- تصميم جلبة سبرو:
يمكن أن يؤثر تصميم جلبة الذريعة، التي تربط القالب بوحدة الحقن، على تدفق المواد وملء تجاويف القالب. يساعد التصميم الفعال لجلبة الذؤابة على التحكم في معدلات التدفق، ومنع انحباس الهواء، وضمان توزيع المواد بشكل موحد داخل القالب.
تؤثر هذه العوامل مجتمعة على تعبئة القالب، والضغط، وإزالة القوالب، وجودة المنتج بشكل عام في التشكيل بالضغط. يساهم التصميم الأمثل للقوالب، والتحكم المناسب في درجة حرارة القالب، والإدارة الدقيقة لقوة التثبيت، واختيار المواد المناسبة، والاستخدام الفعال لعوامل تحرير القوالب، والتصميم المدروس لجلبة الذرب في تحقيق أبعاد متناسقة للقطع، وتقليل العيوب، وتحسين جودة المنتج النهائي.
من خلال فهم هذه العوامل وتحسينها، يمكن للمصنعين تعزيز كفاءة العملية وتحقيق خصائص القطع المرغوبة وضمان نجاح إنتاج منتجات مطاط السيليكون عالية الجودة من خلال القولبة بالضغط.
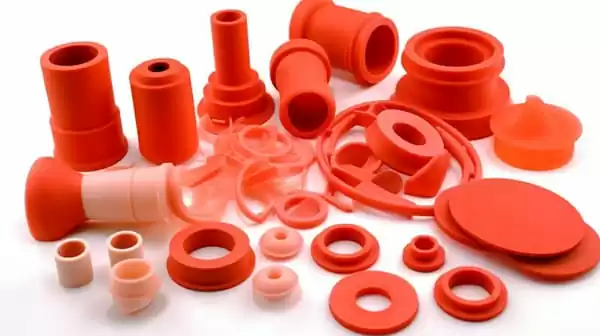
عيوب القوالب المطاطية:
يمكن أن تكون عملية قولبة المطاط، بما في ذلك عملية قولبة المطاط بالضغط، عرضة لعيوب مختلفة يمكن أن تؤثر على وظيفة المنتج النهائي ومظهره. إن معالجة هذه العيوب وتقليلها أمر بالغ الأهمية لتحقيق نتائج عالية الجودة. دعونا نستكشف بعض العيوب الشائعة المرتبطة بقولبة المطاط:
1.فلاش 1:
يشير الوميض إلى المواد الزائدة التي تتسرب من تجويف القالب أثناء عملية التشكيل. ويحدث عادةً عند الخطوط الفاصلة أو مناطق القالب ذات الفجوات أو المحاذاة الخاطئة. يمكن أن يؤثر الوميض على دقة أبعاد المنتج وينتج عنه مواد زائدة أو نتوءات غير مرغوب فيها على الجزء النهائي. وقد يتطلب الأمر معالجة إضافية بعد المعالجة، مثل التشذيب أو العمليات الثانوية، لإزالة الوميض، مما يزيد من وقت الإنتاج والتكاليف.
2- الاحتباس الهوائي:
يحدث انحباس الهواء عندما ينحصر الهواء أو الغاز داخل الجزء المقولب أثناء عملية التشكيل. يمكن أن يحدث ذلك بسبب التهوية غير السليمة، أو التصميم غير الملائم للقالب أو عدم كفاية ملء القالب. يمكن أن يؤدي انحباس الهواء إلى ملء غير مكتمل، وضعف هيكلي، وتكوين فراغات داخل الجزء. يمكن أن تؤثر هذه الفراغات على الخواص الميكانيكية، مثل القوة أو المتانة، للمنتج النهائي، مما يؤثر على وظائفه.
3- عيوب السطح:
يمكن أن تظهر عيوب السطح على شكل خدوش أو عيوب أو خشونة أو غيرها من التناقضات على سطح المنتج المصبوب. يمكن أن تنتج هذه العيوب عن عوامل مثل عيوب سطح القالب، أو ضعف تدفق المواد، أو عدم كفاية التحكم في درجة حرارة القالب. لا تؤثر عيوب السطح على المظهر الجمالي للمنتج فحسب، بل يمكن أن تؤثر أيضًا على وظيفته، خاصةً في التطبيقات التي يكون فيها السطح الأملس أمرًا بالغ الأهمية، مثل أسطح الختم أو الأسطح الملامسة.
4- تناقضات الأبعاد:
تشير التباينات في الأبعاد إلى الاختلافات في الحجم أو الشكل أو سمك الجزء المصبوب. يمكن أن تنشأ هذه الاختلافات بسبب مشكلات مثل عدم ملائمة تصميم القالبأو الملء غير الكافي للقالب أو الضغط غير المتساوي. يمكن أن تؤثر التناقضات في الأبعاد على ملاءمة المنتج النهائي أو تجميعه أو أدائه، مما يجعل من الصعب تحقيق تفاوتات دقيقة أو تلبية متطلبات وظيفية محددة.
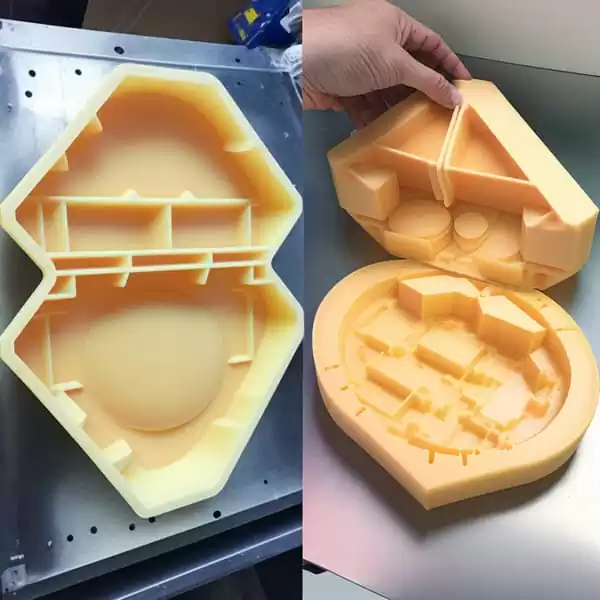
يمكن أن يكون لهذه العيوب آثار كبيرة على وظيفة المنتج النهائي ومظهره. يمكن أن يؤدي الوميض الزائد إلى ضعف المظهر الجمالي أو يتداخل مع وظائف المنتج أو يسبب صعوبات أثناء التجميع. يمكن أن يؤدي انحباس الهواء والفراغات إلى إضعاف السلامة الهيكلية للجزء، مما يؤثر على قوته أو متانته. لا تؤثر عيوب السطح على المظهر المرئي فحسب، بل يمكن أن تؤثر أيضًا على الخصائص الوظيفية مثل الاحتكاك أو القدرة على الإغلاق أو خصائص التلامس. يمكن أن تعيق التناقضات في الأبعاد الملاءمة المناسبة، أو تتداخل مع أجزاء التزاوج، أو تؤدي إلى اختلال في المحاذاة، مما يؤثر على الأداء العام أو وظيفة المنتج.
من خلال تنفيذ تصميم فعال لعملية التشكيل بالنقل، وتحسين معايير العملية، وتنفيذ تدابير صارمة لمراقبة الجودة، يمكن للمصنعين تقليل هذه العيوب في قولبة المطاط، مما يضمن منتجات عالية الجودة تلبي المتطلبات الوظيفية والجمالية المطلوبة.
استراتيجيات للتغلب على التحديات في قولبة مطاط السيليكون عالي الحجم بالضغط:
التغلب على تحديات قولبة مطاط السيليكون عالي الحجم بالضغط يتطلب اتباع نهج منهجي وتنفيذ استراتيجيات فعالة. وفيما يلي بعض الاستراتيجيات الرئيسية لمواجهة هذه التحديات:
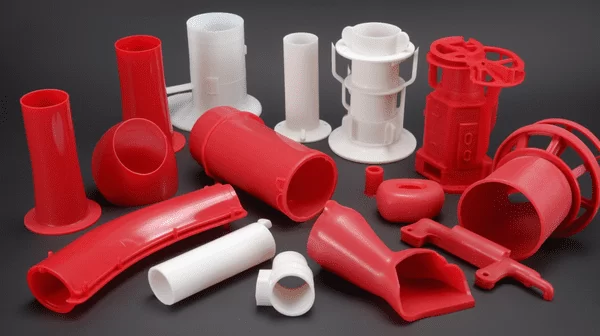
1- ملء القالب بشكل متناسق:
تحسين تصميم القالب لضمان تصميم نظام العداء والبوابات المناسب لتدفق المواد بشكل موحد.
استخدام تقنيات مراقبة العمليات المتقدمة مثل استشعار الضغط ودرجة الحرارة في الوقت الحقيقي لتحديد الاختلافات وإجراء التعديلات اللازمة.
إجراء تحليل تدفق القالب لتحسين تصميم القالب وضمان ملء القالب بشكل متناسق.
2- أوقات الدورات الفعالة:
الاستفادة من برامج تصميم القوالب المتقدمة وأدوات المحاكاة لتحديد الاختناقات المحتملة وتحسين تصميم القالب من أجل تسريع زمن الدورة.
اختر الأداء العالي مركبات مطاط السيليكون مصممة خصيصًا للمعالجة السريعة لتقليل زمن الدورة الكلية.
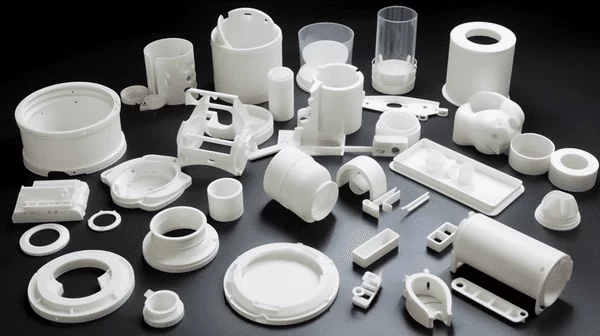
تحسين معلمات العملية مثل درجة الحرارة والضغط والوقت لتقليل وقت المعالجة وزيادة كفاءة الإنتاج.
3- التحكم في الوميض:
ركز على التصميم المناسب للقالب والتحكم الدقيق في قوة التشبيك لتقليل تكوين الوميض.
تنفيذ التحكم في درجة حرارة القالب لضمان التدفق المناسب للمواد ومنع الوميض الزائد.
تنفيذ إجراءات صارمة لمراقبة الجودة، بما في ذلك الفحص والمراقبة المنتظمة، لتحديد العيوب المتعلقة بالوميض ومعالجتها على الفور.
4.4 صيانة القالب:
وضع جدول زمني للصيانة الوقائية للقوالب لضمان طول عمرها وأداءها الثابت.
تنظيف القوالب بانتظام واستخدام عوامل تحرير القوالب المناسبة لمنع الالتصاق وتحسين عملية إزالة القوالب.
تنفيذ تقنيات تخزين القوالب المناسبة لمنع التلف وضمان جاهزية القوالب للإنتاج الفعال.
5- جودة المواد:
العمل بشكل وثيق مع موردي المواد ذوي السمعة الطيبة لضمان اتساق و مركبات مطاط السيليكون عالية الجودة.
وضع مواصفات ومعايير واضحة لخصائص المواد وإجراء اختبارات منتظمة للتحقق من الامتثال.
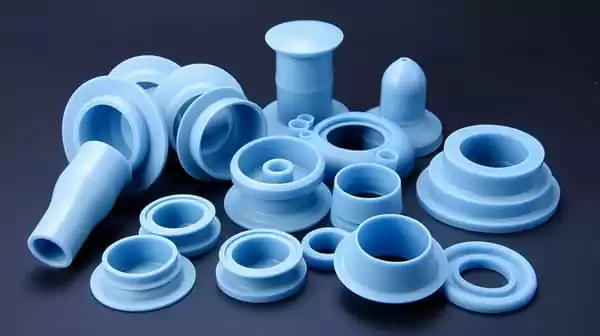
إجراء اختبارات صارمة للمواد لضمان ملاءمة المادة المطاطية للاستخدام المقصود وتقليل العيوب.
6- تحسين تصميم القالب:
الاستفادة من برامج تصميم القوالب المتقدمة وأدوات المحاكاة لتحسين تجاويف القوالب وأنظمة العداءات وخطوط التقسيم لتحقيق إنتاج فعال وأقل قدر من الهدر.
تصميم القوالب مع أنظمة تنفيس وبوابات مناسبة لتقليل احتباس الهواء وضمان تدفق المواد بشكل منتظم.
ضع في اعتبارك عوامل مثل درجة حرارة القالب، وتصميم جلبة الذربة، وعوامل تحرير القالب لتعزيز التدفق المناسب للمواد، وإزالة القوالب، وجودة السطح.
7- مراقبة العمليات والتفتيش عليها:
تنفيذ تقنيات مراقبة العمليات في الوقت الفعلي لتحديد الاختلافات والمشكلات المحتملة أثناء الإنتاج.
فحص ومراقبة عملية التشكيل بالضغط بانتظام لضمان الالتزام بمعايير الجودة وتحديد أي انحرافات أو عيوب.
استخدام أساليب التحكم في العمليات الإحصائية (SPC) لتتبع بيانات العمليات وتحليلها، مما يتيح إجراء تعديلات استباقية وتحسين مستمر.
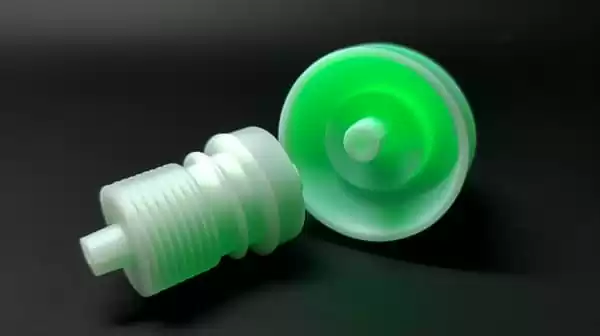
من خلال تنفيذ هذه الاستراتيجيات، يمكن للمصنعين التغلب على تحديات قولبة مطاط السيليكون عالي الحجم بالضغط. تلعب التعبئة المتسقة للقوالب، وأوقات الدورات الفعالة، والتحكم في الوميض، وصيانة القوالب، وجودة المواد أدوارًا حيوية في تحقيق نتائج إنتاج ناجحة. يساهم تحسين تصميم القوالب ومراقبة العملية والعمل مع موردي المواد ذوي السمعة الطيبة في تحسين الإنتاجية وتحسين جودة المنتج والتصنيع الفعال من حيث التكلفة.
الخلاصة:
في الختام، تقدم عملية التشكيل بضغط مطاط السيليكون بكميات كبيرة مجموعة فريدة من التحديات الخاصة بها والتي يجب معالجتها من أجل التصنيع الناجح. وقد استكشفنا خلال هذه المقالة هذه التحديات وقدمنا رؤى قيمة حول كيفية التغلب عليها بفعالية.
تم تسليط الضوء على الملء المتسق للقوالب، وأوقات الدورات الفعالة، والتحكم في الوميض، وصيانة القوالب، وجودة المواد كمجالات رئيسية تتطلب الاهتمام. من خلال التخطيط الدقيق لهذه الجوانب وتحسينها، يمكن للمصنعين تحسين الإنتاجية بشكل كبير وتحسين جودة المنتجات النهائية.
تتطلب مواجهة تحديات القولبة بضغط مطاط السيليكون بكميات كبيرة اتباع نهج منظم وتنفيذ استراتيجيات فعالة. ويشمل ذلك تحسين قولبة حقن السوائل عن طريق التصميم، واستخدام تقنيات مراقبة العمليات المتقدمة، وإجراء عمليات تفتيش منتظمة، والعمل مع موردي المواد ذوي السمعة الطيبة.
من خلال التغلب على هذه التحديات، يمكن للمصنعين تحقيق إنتاجية محسنة، وتحسين جودة المنتج، وتلبية متطلبات السوق بفعالية. ويمكن أن يؤدي ذلك إلى زيادة رضا العملاء وزيادة الربحية والميزة التنافسية في الصناعة.
وفي الختام، يُعد التخطيط الدقيق لهذه الاستراتيجيات وتحسينها وتنفيذها أمرًا بالغ الأهمية للمصنعين لتحقيق النجاح في قولبة مطاط السيليكون المضغوط بكميات كبيرة. ومن خلال تحسين عملياتهم وصقلها باستمرار، يمكن للمصنعين إطلاق الإمكانات الكاملة لطريقة التصنيع هذه وتقديم منتجات مطاط السيليكون الاستثنائية لتلبية الاحتياجات المتنوعة للسوق.