Einführung
Das Formpressen ist ein wichtiger Fertigungsprozess mit tiefgreifenden Auswirkungen auf verschiedene Branchen. Dieser Artikel taucht in die Welt des Formpressens ein und untersucht seine Bedeutung, die Herausforderungen und die entscheidende Rolle, die die Simulationssoftware bei der Überwindung dieser Hürden spielt.
Das Formpressen ist eine weit verbreitete Fertigungstechnik zur Herstellung komplexer Bauteile aus einer Vielzahl von Materialien, darunter Kunststoffe, Verbundwerkstoffe und Gummi. Dieses Verfahren ist von immenser Bedeutung, denn es ermöglicht die Herstellung hochwertige Teile mit Präzision, was sie in Branchen wie der Automobilindustrie, der Luft- und Raumfahrt und der Konsumgüterindustrie unverzichtbar macht.
Obwohl das Formpressen zahlreiche Vorteile bietet, ist es nicht ohne Komplexität und Herausforderungen. Um optimale Ergebnisse beim Formpressen zu erzielen, ist ein empfindliches Gleichgewicht von Parametern erforderlich, darunter Temperatur, Druck, Materialeigenschaften und Formpressen Grundlagen und Design. Das Zusammenspiel dieser Faktoren kann kompliziert sein und zu Problemen wie Löchern, Verzug und uneinheitlichem Materialfluss führen. Diese Herausforderungen erfordern innovative Lösungen zur Verbesserung der Produktqualität, zur Verringerung des Ausschusses und zur Optimierung der Produktion.
An dieser Stelle kommt die Simulationssoftware ins Spiel. Simulationssoftware hat sich zu einem leistungsstarken Werkzeug entwickelt, mit dem die Hersteller die Feinheiten des Formpressens direkt angehen können. Durch die Erstellung virtueller Modelle und die Durchführung von Formfüllsimulationen können Hersteller Ergebnisse vorhersagen, Parameter optimieren und potenzielle Fehler erkennen - und das alles ohne teure physische Prototypen. Die Bedeutung der Finite-Elemente-Simulationssoftware bei der Bewältigung der Komplexität des Formpressens kann gar nicht hoch genug eingeschätzt werden, denn sie spielt eine entscheidende Rolle bei der Steigerung der Effizienz, der Verbesserung der Qualität und letztlich bei der Gestaltung der Zukunft der Fertigung.
In den folgenden Abschnitten werden wir uns eingehender mit den Formpressverfahren, die Möglichkeiten des effektiven Einsatzes von Simulationssoftware erforschen und praktische Einblicke in die Optimierung der Ergebnisse des Formpressens geben.
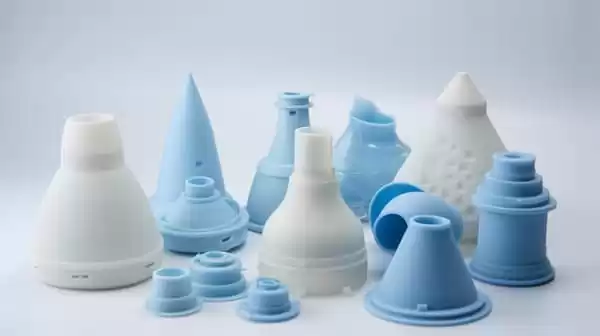
II. Verständnis des Formpressens
Das Formpressen ist ein Herstellungsprozess, der mehrere verschiedene Schritte und eine Vielzahl kritischer Parameter umfasst. In diesem Abschnitt werden die Grundlagen des Formpressverfahrens erläutert und die wichtigsten Parameter und Variablen, die sich erheblich auf die Ergebnisse auswirken, näher beleuchtet.
Die grundlegenden Schritte des Formpressens
1. Vorbereitung:
Das Formpressverfahren beginnt mit der Vorbereitung des Rohmaterials, das in der Regel in Form von Granulat oder Vorformlingen vorliegt. Dieses Material wird in einen Formhohlraum eingefüllt, der genau die endgültige Form des Produkts bestimmt.
2. Heizung:
Sobald der Formhohlraum mit Material gefüllt ist, wird er geschlossen, und das Material wird erhitzt. Die Hitze erweicht das Material, macht es formbarer und bereit zum Gießen.
3. Kompression:
Nachdem die gewünschte Temperatur erreicht ist, wird Druck auf das Material ausgeübt. Durch diese Kompression wird das Material gezwungen, den Formhohlraum vollständig auszufüllen und die Form des Werkzeugs anzunehmen.
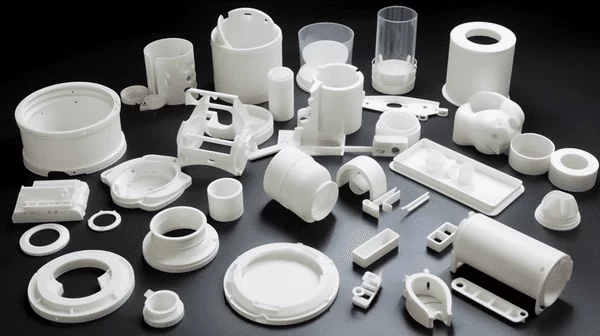
4. Kühlung:
Nach der Kompressionsphase wird die Form abgekühlt, um das Material zu verfestigen. Die Abkühlzeit wird sorgfältig kontrolliert, um sicherzustellen, dass das Material seine Form und strukturelle Integrität beibehält.
5. Rauswurf:
Sobald das Material ausreichend abgekühlt und verfestigt ist, wird das Endprodukt aus der Form ausgestoßen. Das Produkt ist dann für die weitere Verarbeitung oder Verwendung bereit.
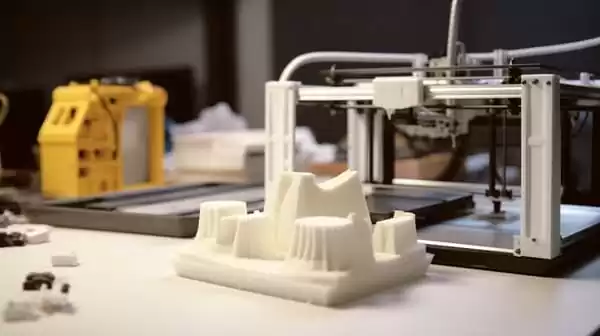
Schlüsselparameter und -variablen beim Formpressen
Das Erzielen optimaler Ergebnisse beim Formpressen hängt von einem sorgfältigen Gleichgewicht mehrerer kritischer Parameter und Variablen ab, darunter:
Temperatur: Die Temperatur, bei der das Material erwärmt wird, spielt eine grundlegende Rolle für das Verhalten des Materials während des Spritzprägevorgangs. Sie beeinflusst die Fließeigenschaften, die Aushärtung und die Gesamtleistung des Materials.
Druck: Die Anwendung von Druck ist notwendig, um sicherzustellen, dass das Material den Formhohlraum vollständig ausfüllt. Eine ordnungsgemäße Druckregelung verhindert Fehler und gewährleistet eine gleichmäßige Formfüllung.
Zeit: Die Dauer jeder Phase des Formprozesses, einschließlich Erhitzung, Kompression und Abkühlung, wirkt sich direkt auf die Qualität und die Eigenschaften des Endprodukts aus.
Materialeigenschaften: Materialeigenschaften wie Viskosität, Schmelzflussrate und Aushärteverhalten sind beim Formpressen von entscheidender Bedeutung. Die Wahl des Materials hat großen Einfluss auf den Formgebungsprozess und die Qualität des Endprodukts.
Formenbau: Die Geometrie und Faserausrichtung des Formhohlraums sowie Merkmale wie Entlüftungsöffnungen und Angusskanäle haben einen erheblichen Einfluss auf den Materialfluss und die Struktur des fertigen Teils.
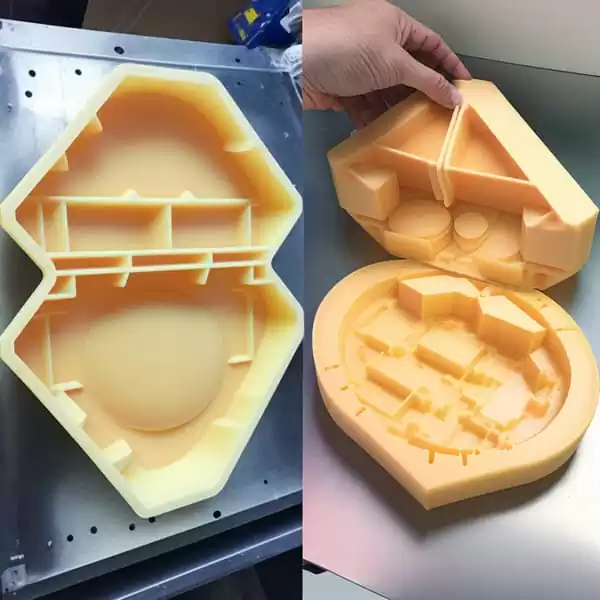
Abkühlungsrate: Die Geschwindigkeit, mit der die Oberschicht-Formmasse nach dem Verdichten abgekühlt wird, hat Auswirkungen auf die Kristallisation des Materials und damit auf seine mechanischen Eigenschaften.
Im nächsten Abschnitt werden wir untersuchen, wie Simulationssoftware genutzt werden kann, um diese Parameter und Variablen zu optimieren, was letztendlich zu besseren Ergebnissen beim Formpressen führt.
III. Die Rolle der Simulationssoftware
Simulationssoftware ist ein entscheidender Faktor im Bereich des Formpressens. In diesem Abschnitt stellen wir das Konzept der Simulationssoftware im Zusammenhang mit dem Formpressen vor und zeigen auf, wie sie als leistungsfähiges Werkzeug für die Vorhersage von Ergebnissen, die Optimierung von Prozessparametern, die Reduzierung von Fehlern, die Konstruktion von Formen, die Verbesserung der Materialauswahl und letztlich die Einsparung von Zeit und wertvollen Ressourcen dient.
Einführung in die Simulationssoftware
Simulationssoftware im Zusammenhang mit dem Formpressen bezieht sich auf fortschrittliche computergestützte Werkzeuge, mit denen Hersteller virtuelle Modelle des gesamten Formgebungsprozesses erstellen können. Diese virtuellen Modelle ahmen die realen Bedingungen nach und ermöglichen es Ingenieuren und Herstellern, wertvolle Erkenntnisse darüber zu gewinnen, wie sich verschiedene Parameter und Variablen auf das Endprodukt auswirken werden. Im Grunde handelt es sich um einen digitalen Sandkasten, in dem Experimente durchgeführt werden können, ohne dass physische Prototypen erforderlich sind.
Präzise Vorhersage von Resultaten
Einer der wichtigsten Vorteile der Simulationssoftware für das Formpressen ist die Fähigkeit, die Ergebnisse präzise vorherzusagen. Ingenieure können bestimmte Parameter, wie Temperatur, Druck und Materialeigenschaften, in die Simulation eingeben. Die Software berechnet dann, wie diese Parameter zusammenwirken, und vermittelt so ein klares Bild davon, was bei der tatsächlichen Produktion zu erwarten ist. Diese Vorhersagefähigkeit ermöglicht es den Herstellern, ihre Prozesse für optimale Ergebnisse fein abzustimmen.
Optimierung der Prozessparameter
Die Simulationssoftware beschränkt sich nicht nur auf die Vorhersage, sondern zeichnet sich auch durch ihre Optimierungsfähigkeit aus. Durch die Durchführung von Simulationen mit verschiedenen Parameterkombinationen können Hersteller die idealen Einstellungen für ihren Formpressprozess ermitteln. So können sie beispielsweise die optimale Temperatur-Druck-Kombination ermitteln, die zu kürzeren Zykluszeiten, niedrigeren Produktionskosten und einer besseren Produktqualität führt. Diese Optimierung ist ein entscheidender Schritt, um die bestmöglichen Simulationsergebnisse für den Formpressprozess zu erzielen.
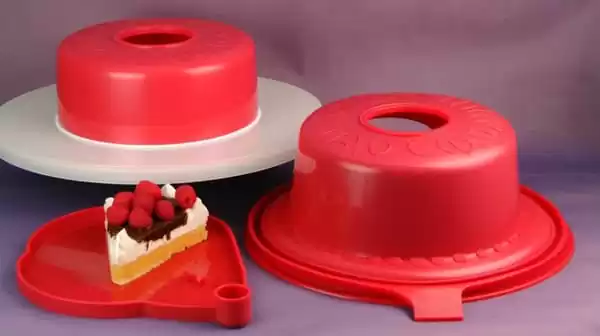
Defektreduzierung und Qualitätsverbesserung
Auf der Suche nach Spitzenleistungen dient die Simulationssoftware als leistungsstarkes Werkzeug zur Fehlerreduzierung. Durch die Simulation des Formprozesses können Hersteller potenzielle Fehler wie Hohlräume, Verformungen oder Probleme mit dem Materialfluss erkennen, bevor sie in der realen Produktion auftreten. Mit diesem Wissen können Anpassungen am Prozess vorgenommen werden, um Fehler effektiv zu reduzieren und die Gesamtqualität des Endprodukts zu verbessern.
Effiziente Formen entwerfen
Der Entwurf von Formen ist ein entscheidender Aspekt des Formpressens, und Simulationssoftware ist in diesem Bereich sehr hilfreich. Ingenieure können die Software nutzen, um Formen mit komplizierten Geometrien zu entwerfen, die durch Versuch und Irrtum allein nur schwer zu erreichen sind. Die Software stellt sicher, dass die Formen effizient sind und gleichbleibend qualitativ hochwertige Teile produzieren können.
Verbessern der Materialauswahl
Mit Hilfe von Simulationssoftware können Hersteller beurteilen, wie sich verschiedene Materialien beim Formpressen verhalten. Dies ist besonders wertvoll, wenn es um fortschrittliche Materialien wie faserverstärkte Verbundwerkstoffe geht. Durch die Simulation verschiedener Materialoptionen können Hersteller fundierte Entscheidungen darüber treffen, welches Material für eine bestimmte Anwendung am besten geeignet ist, um eine optimale Leistung zu gewährleisten.
Sparen Sie Zeit und Ressourcen
Einer der vielleicht überzeugendsten Aspekte von Simulationssoftware ist ihre Fähigkeit, sowohl Zeit als auch Ressourcen zu sparen. Herkömmliche Versuch-und-Irrtum-Methoden können kostspielig und zeitaufwendig sein und mehrere physische Prototypen und Iterationen erfordern. Mit Simulationssoftware entfällt ein Großteil dieser Versuch-und-Irrtum-Methoden, da die Ingenieure die Prozesse digital verfeinern können, bevor sie sich für die physische Produktion entscheiden.
Im nächsten Abschnitt werden wir uns mit den praktischen Schritten befassen, die Hersteller unternehmen können, um die Leistungsfähigkeit von Simulationssoftware im Formpressprozess effektiv zu nutzen.
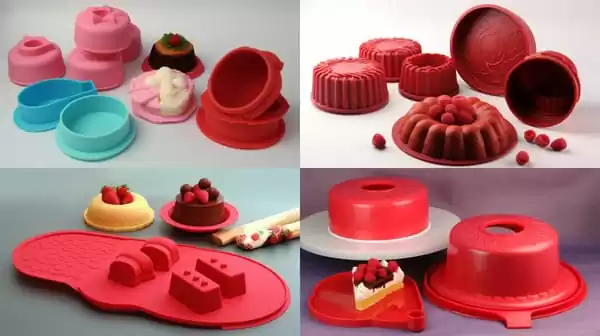
IV. Schritte zur effektiven Nutzung von Simulationssoftware
Der effektive Einsatz von Simulationssoftware beim Formpressen erfordert einen systematischen Ansatz. Hersteller können eine schrittweise Anleitung befolgen, um die Vorteile dieses leistungsstarken Werkzeugs zu maximieren. Hier finden Sie einen umfassenden Überblick über die wichtigsten Schritte:
1. Datenerhebung
Eine wirksame Simulation beginnt mit einer soliden Datenerfassung. Die Hersteller sollten alle relevanten Daten sammeln, einschließlich:
- Materialeigenschaften: Umfassende Informationen über das verwendete Material, wie z. B. Viskosität, Schmelzflussrate, Wärmeleitfähigkeit und Aushärteverhalten.
- Form-Spezifikationen: Detaillierte Spezifikationen der Form, einschließlich Abmessungen, Geometrie und Entlüftungsdetails.
- Prozessparameter: Genaue Daten über Prozessparameter wie Temperatur, Druck und Zykluszeiten.
- Historische Daten: Alle früheren Produktionsdaten oder Aufzeichnungen von Fehlern, die für den Simulationsprozess von Bedeutung sind.
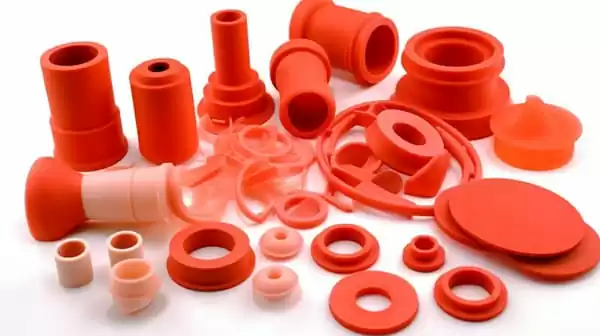
2. Modell-Erstellung
Mit den vorliegenden Daten wird in einem nächsten Schritt ein virtuelles Modell des Formpressverfahrens erstellt. Dies beinhaltet:
- Erstellung von Geometrien: Erstellung einer 3D-Darstellung der Form und des Materials in der Simulationssoftware.
- Parameter Eingabe: Eingabe aller erfassten Daten, einschließlich der Materialeigenschaften und Prozessparameter, in das Simulationsmodell.
- Randbedingungen: Festlegung von Randbedingungen, wie Anfangstemperaturen und -drücke.
3. Simulation
Sobald das Modell erstellt ist, wird eine Simulationssoftware eingesetzt, um virtuelle Formpressverfahren durchzuführen. Während dieser Phase:
- Simulieren Sie den Prozess: Die Software führt auf der Grundlage des definierten Modells Simulationen durch, die den tatsächlichen Formpressprozess nachbilden.
- Verhalten überwachen: Die Ingenieure können überwachen, wie das Material fließt, wie sich der Druck verteilt und wie sich die Temperatur in der virtuellen Form verändert.
4. Analyse
Nachdem die Simulationsläufe abgeschlossen sind, ist es Zeit für eine gründliche Analyse:
- Identifizierung von Mängeln: Prüfen Sie die Simulationsergebnisse, um mögliche Fehler oder Probleme im Prozess zu erkennen. Dazu können Hohlräume, Verformungen oder ein ungleichmäßiger Materialfluss gehören.
- Mechanische Eigenschaften: Analysieren Sie die voraussichtlichen mechanischen Eigenschaften des Endprodukts, wie Festigkeit, Steifigkeit und Elastizität.
- Materielles Verhalten: Verstehen, wie sich das Material unter verschiedenen Bedingungen und Drücken verhält.
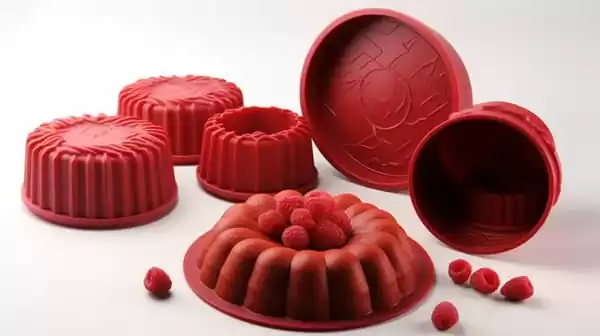
5. Optimierung
Mit einem klaren Verständnis der Simulationsergebnisse und der identifizierten Verbesserungsbereiche können die Hersteller mit der Optimierung fortfahren:
- Parameter-Einstellungen: Ändern Sie Prozessparameter wie Temperatur, Druck oder Zykluszeit, um den Formpressprozess zu optimieren.
- Auswahl der Materialien: Ziehen Sie anhand der Simulationsergebnisse verschiedene Materialien oder Materialmischungen in Betracht, die die Eigenschaften des Endprodukts verbessern können.
- Formenbau: Passen Sie die Formkonstruktion an, um den Materialfluss zu verbessern und Fehler zu minimieren.
6. Validierung
Die Validierung ist ein entscheidender Schritt, um sicherzustellen, dass die Simulationsergebnisse mit den Ergebnissen der realen Welt übereinstimmen:
- Vergleich mit Daten aus der realen Welt: Validieren Sie die Simulationsergebnisse, indem Sie sie mit tatsächlichen Produktionsdaten und physischen Prototypen vergleichen.
- Iterieren Sie, wenn nötig: Wenn Abweichungen festgestellt werden, nehmen Sie die erforderlichen Anpassungen am Simulationsmodell vor und führen Sie zusätzliche Tests durch, bis die Ergebnisse mit der realen Leistung übereinstimmen.
7. Umsetzung
Schließlich wird das optimierte Verfahren auf der Grundlage der Simulationsergebnisse umgesetzt:
- Prozessanpassung: Implementieren Sie die überarbeiteten Prozessparameter, Formdesigns oder Materialauswahlen in der tatsächlichen Produktion.
- Kontinuierliche Überwachung: Kontinuierliche Überwachung der Produktion, um sicherzustellen, dass die durch die Simulation erzielten Verbesserungen nachhaltig sind.
- Rückkopplungsschleife: Einrichtung einer Rückkopplungsschleife, in der Daten aus der realen Produktion zur weiteren Verfeinerung und Verbesserung des Simulationsmodells für die künftige Verwendung verwendet werden.
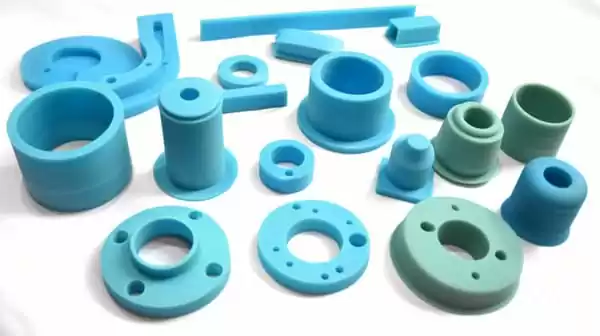
Wenn Sie diese Schritte systematisch befolgen, können Hersteller das volle Potenzial der Simulationssoftware beim Formpressen ausschöpfen, was zu einer verbesserten Produktqualität, weniger Fehlern und effizienteren Produktionsprozessen führt.
IV. Was ist Moldflow-Simulation?
In der komplizierten Welt der Kunststoffindustrie ist die Moldflow-Simulation ein spezielles und unverzichtbares Werkzeug. In diesem Abschnitt wird die Moldflow-Simulation definiert und erläutert und ihre Rolle beim Verständnis des Materialflusses und der Materialverteilung in den Formen beleuchtet.
Moldflow-Simulation definieren
Die Moldflow-Simulation ist ein hochspezialisiertes Softwaretool, das in der Kunststoffindustrie eingesetzt wird. Seine Hauptfunktion ist die virtuelle Darstellung des gesamten Spritzgießprozesses, die es den Herstellern ermöglicht, ein umfassendes Verständnis dafür zu gewinnen, wie geschmolzenes Kunststoffmaterial fließt und sich in den Formen verteilt. Dieses Werkzeug dient als virtuelles Labor, das Einblicke in das komplexe Verhalten von Materialien während des Spritzgießprozesses ermöglicht.
Verstehen von Materialfluss und Verteilung
Die Moldflow-Simulation zeichnet sich durch ihre Fähigkeit aus, den Materialfluss und die Materialverteilung mit einem hohen Maß an Präzision zu simulieren und zu analysieren. So erreicht sie dies:
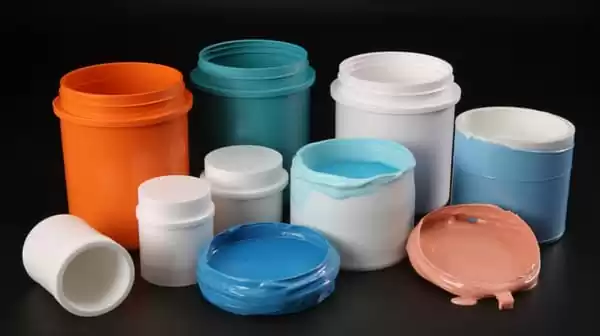
- Materielles Verhalten: Die Moldflow-Simulation beginnt mit der Berücksichtigung der Eigenschaften des verwendeten Kunststoffs. Dazu gehören Aspekte wie die Viskosität der Schmelze, das temperaturabhängige Verhalten und die rheologischen Eigenschaften.
- Geometrie-Analyse: Die Software berücksichtigt dann die Geometrie des Formhohlraums, einschließlich seiner komplizierten Merkmale, Anschnitte, Angüsse und Kühlkanäle. Diese Analyse ist entscheidend für das Verständnis, wie das Material in der Form fließen wird.
- Simulation der Einspritzung: Das Herzstück der Moldflow-Simulation liegt in der Fähigkeit, die Einspritzphase zu simulieren. Sie sagt voraus, wie das geschmolzene Kunststoffmaterial in die Form eintritt, wie es jeden Winkel ausfüllt und wie sich der Druck verteilt.
- Fluss-Visualisierung: Durch die Simulation erzeugt Moldflow visuelle Darstellungen des Materialflusses. Dazu können Fließfronten, Druckprofile und Temperaturgradienten gehören, die Ingenieuren und Herstellern ein klares Bild davon vermitteln, was sich im Inneren der Form abspielt.
- Identifizierung von Mängeln: Die Moldflow-Simulation ist auch in der Lage, potenzielle Fehler zu identifizieren, die während des Spritzgießprozesses auftreten können. Dazu gehören Probleme wie Lufteinschlüsse, Bindenähte, Einfallstellen und unvollständige Füllung.
Rolle bei der Konstruktion und Optimierung von Formen
Bei der Moldflow-Simulation geht es nicht nur um das Verständnis des Materialflusses, sondern auch um den Entwurf und die Optimierung von Formen. So geht's:
- Formenbau: Ingenieure können Moldflow-Simulationen zur Feinabstimmung von Werkzeugkonstruktionen verwenden, um sicherzustellen, dass der Materialfluss gleichmäßig ist und Fehler minimiert werden. Dies kann die Änderung von Anschnittpositionen, die Anpassung von Angusssystemen und die Optimierung von Kühlstrategien beinhalten.
- Auswahl der Materialien: Die Simulation ermöglicht die Bewertung verschiedener Materialien und ihres Verhaltens in der Form. Hersteller können anhand der Simulationsergebnisse das am besten geeignete Material auswählen.
- Optimierung: Die Moldflow-Simulation hilft bei der Optimierung von Prozessparametern wie Einspritzgeschwindigkeit, Schmelzetemperatur und Kühlrate, um die bestmöglichen Gussergebnisse zu erzielen.
Zusammenfassend lässt sich sagen, dass die Moldflow-Simulation ein spezielles Softwaretool ist, das für die Kunststoffindustrie entwickelt wurde. Es spielt eine zentrale Rolle beim Verständnis, wie geschmolzenes Kunststoffmaterial während des Spritzgießprozesses in Formen fließt und sich darin verteilt. Durch die Simulation des Materialverhaltens, der Werkzeuggeometrie und der Einspritzphase bietet Moldflow unschätzbare Einblicke in die komplexe Welt des Kunststoffspritzgusses. Moldflow hilft nicht nur bei der Identifizierung von Fehlern, sondern auch bei der Werkzeugkonstruktion und der Prozessoptimierung, was letztendlich zu effizienteren und besseren Ergebnissen führt. höherwertige Kunststoffkomponenten.
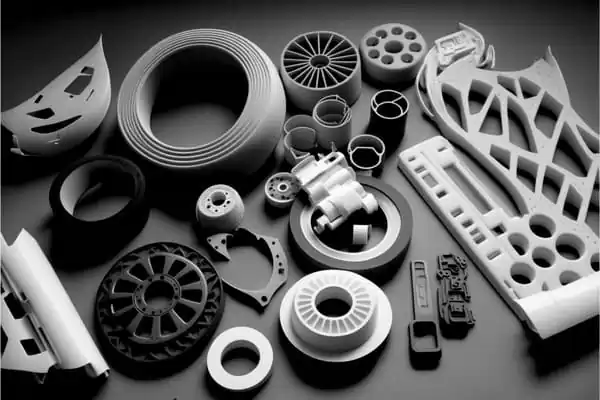
V. Kontrollierte Parameter im Formpressverfahren
Der Erfolg des Formpressverfahrens hängt von der sorgfältigen Kontrolle verschiedener Parameter und Variablen ab. In diesem Abschnitt werden wir die Kontrollparameter auflisten und erläutern, die für das Erreichen optimaler Ergebnisse beim Formpressen eine zentrale Rolle spielen:
1. Temperatur:
- Erläuterung: Die Temperaturregelung ist beim Formpressen von grundlegender Bedeutung. Sie beeinflusst das Materialverhalten, indem sie die Viskosität, den Schmelzfluss und die Aushärtungseigenschaften beeinflusst. Das genaue Temperaturprofil während der Heiz- und Kühlphase ist entscheidend für die Produktqualität.
2. Druck:
- Erläuterung: Druck ist ein weiterer wichtiger Parameter beim Formpressen. Ein richtig kontrollierter Druck gewährleistet eine gleichmäßige Materialverteilung, minimiert Defekte wie Hohlräume oder Verformungen und verdichtet das Material in die gewünschte Form innerhalb des Formhohlraums.
3. Zeit:
- Erläuterung: Die Zeit ist ein kritischer Parameter, der die Dauer der einzelnen Phasen des Formpressverfahrens bestimmt. Ein sorgfältiges Timing ist wichtig, um die gewünschte Aushärtung des Materials, die Kühlung und die Gesamteffizienz des Prozesses zu erreichen.
4. Materialeigenschaften:
- Erläuterung: Die Eigenschaften des zu formenden Materials wirken sich erheblich auf den Formpressprozess aus. Zu diesen Eigenschaften gehören Viskosität, Fließfähigkeit der Schmelze, Wärmeleitfähigkeit, Aushärteverhalten und sogar die rheologischen Eigenschaften des Materials. Das Verständnis und die Optimierung dieser Materialeigenschaften sind für eine erfolgreiche Formgebung unerlässlich.
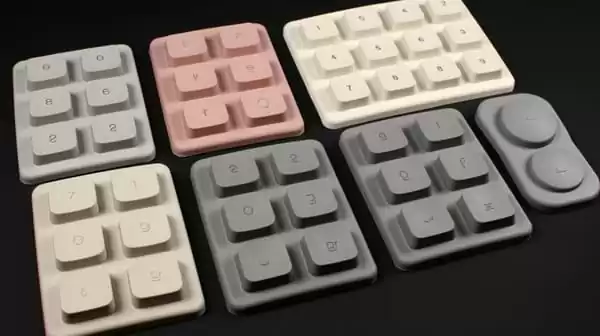
5. Formgestaltung:
- Erläuterung: Die Geometrie des Formhohlraums und andere Merkmale wie Entlüftungsöffnungen, Angüsse und Kühlkanäle haben einen großen Einfluss auf den Materialfluss, die Verteilung und die Qualität des fertigen Teils. Eine gut konzipierte Form gewährleistet eine effiziente Materialverdichtung und minimiert Fehler.
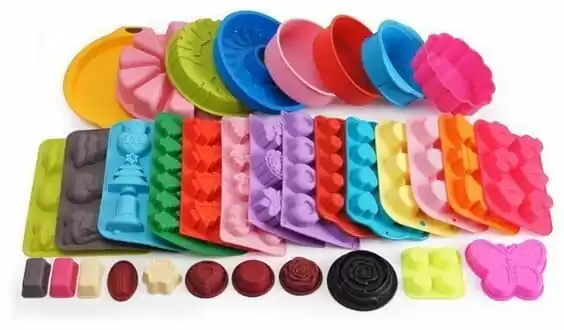
6. Druckverteilung:
- Erläuterung: Nicht nur der Gesamtdruck ist entscheidend, sondern auch die Verteilung des Drucks über die Formoberfläche. Eine gleichmäßige Druckverteilung gewährleistet eine gleichmäßige Materialverdichtung und minimiert Fehler wie ungleichmäßige Dicke oder Hohlräume im Endprodukt.
7. Abkühlungsrate:
- Erläuterung: Die Geschwindigkeit, mit der die Form nach dem Pressen abgekühlt wird, hat einen erheblichen Einfluss auf die Kristallisation des Materials und folglich auf seine mechanischen Eigenschaften. Eine präzise Steuerung der Abkühlgeschwindigkeit ist für das Erreichen der gewünschten Teileigenschaften von entscheidender Bedeutung.
8. Temperatur der Formoberfläche:
- Erläuterung: Die Kontrolle der Temperatur der Formoberfläche ist entscheidend für die ordnungsgemäße Aushärtung und Entformung des Materials. Die Temperatur der Formoberfläche beeinflusst das Verhalten des Materials sowohl in der Heiz- als auch in der Kühlphase.
9. Materialflussanalyse:
- Erläuterung: Das Verständnis des Materialflusses in der Form ist für die Kontrolle von Parametern wie Druck und Temperatur von entscheidender Bedeutung. Die Analyse des Materialflusses kann dazu beitragen, Problembereiche zu identifizieren und den Formgebungsprozess zu optimieren.
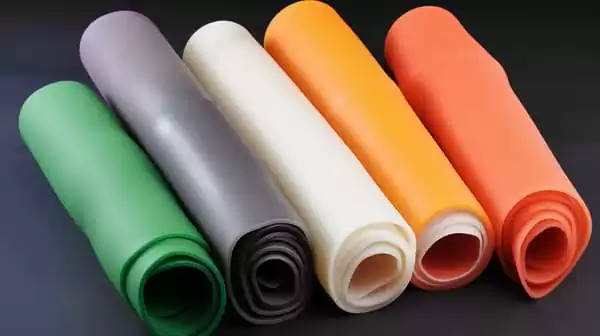
10. Belüftung und Entlüftung:
- Erläuterung: Eine ordnungsgemäße Entlüftung und Luftabfuhr sind notwendig, um den Einschluss von Luft oder Gas in der Form zu verhindern. Eine wirksame Entlüftung gewährleistet eine vollständige Materialverdichtung und minimiert Fehler.
Diese Kontrollparameter definieren die Bedingungen, unter denen das Formpressen stattfindet. Die präzise Steuerung dieser Parameter ist entscheidend, um gleichbleibend hochwertige Ergebnisse zu erzielen und die effiziente Produktion von Formteilen zu gewährleisten. Die Hersteller müssen jeden Parameter sorgfältig prüfen und optimieren, um ihre spezifischen Produktanforderungen und Qualitätsstandards zu erfüllen.
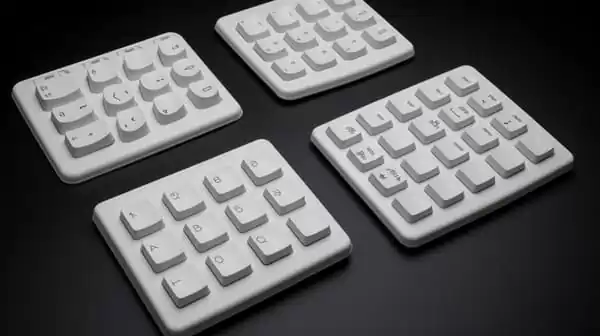
Schlussfolgerung
Zusammenfassend lässt sich sagen, dass dieser Artikel den Bereich des Formpressens erforscht und seine Bedeutung sowie die Feinheiten hervorgehoben hat, die zur Erzielung optimaler Ergebnisse erforderlich sind. Wir haben die zentrale Rolle der Simulationssoftware bei der Bewältigung dieser Herausforderungen und der Optimierung des Formpressprozesses hervorgehoben. Hier sind die wichtigsten Erkenntnisse:
- Bedeutung des Formpressens: Das Formpressen ist ein wichtiges Fertigungsverfahren, das in allen Branchen eingesetzt wird und die Herstellung komplexer Bauteile mit Präzision und Effizienz ermöglicht.
- Herausforderungen beim Formpressen: Um optimale Ergebnisse beim Formpressen zu erzielen, ist eine präzise Steuerung von Parametern wie Temperatur, Druck, Zeit, Materialeigenschaften und Formdesign erforderlich. Die Komplexität des Materialverhaltens und des Werkzeugdesigns kann zu Defekten und Ineffizienzen führen.
- Die Macht der Simulationssoftware: Simulationssoftware ist ein entscheidender Faktor für das Formpressen. Sie ermöglicht es Herstellern, virtuelle Modelle des Prozesses zu erstellen, Ergebnisse vorherzusagen, Parameter zu optimieren und Fehler zu reduzieren, bevor die physische Produktion beginnt.
- Schritte zum effektiven Einsatz von Simulationen: Hersteller können einen strukturierten Ansatz verfolgen, der Datenerfassung, Modellerstellung, Simulation, Analyse, Optimierung, Validierung und Implementierung umfasst, um die Simulationssoftware effektiv zu nutzen.
- Moldflow-Simulation: Die Moldflow-Simulation, ein spezielles Werkzeug für die Kunststoffindustrie, spielt eine entscheidende Rolle beim Verständnis des Materialflusses und der Materialverteilung in den Formen. Sie hilft bei der Identifizierung von Fehlern, der Konstruktion von Formen, der Materialauswahl und der Prozessoptimierung.
- Kontrollierende Parameter: Zu den wichtigsten Steuerungsparametern beim Formpressen gehören Temperatur, Druck, Zeit, Materialeigenschaften, Werkzeugkonstruktion, Druckverteilung, Kühlrate, Temperatur der Werkzeugoberfläche, Materialflussanalyse und Entlüftung. Die präzise Steuerung dieser Parameter ist für gleichbleibende und hochwertige Ergebnisse unerlässlich.
- Die Zukunft der Molding Simulation: Der Artikel schließt mit einem Hinweis auf die Bedeutung von Simulationssoftware für die Erzielung konsistenter und hervorragender Ergebnisse beim Formpressen. Die digitale Welt der Simulation ermöglicht es den Herstellern, innovativ zu sein, zu optimieren und sich an die sich entwickelnde Landschaft des Maschinenbaus und der Polymerverarbeitung anzupassen. Im Zuge des technologischen Fortschritts können wir davon ausgehen, dass Simulationswerkzeuge die Zukunft der Fertigung noch stärker mitgestalten werden.
In der sich ständig weiterentwickelnden Welt des Maschinenbaus und der Polymerverarbeitung ist die Simulationssoftware der Kompass, der uns zu mehr Effizienz, Innovation und Exzellenz beim Formpressen führt. Mit jeder Simulation kommen wir der Perfektionierung der Kunst der Herstellung von Präzisionsbauteilen ein Stück näher und sparen gleichzeitig wertvolle Zeit und Ressourcen. Mit Blick auf die Zukunft erwarten wir, dass die Simulationssoftware auch weiterhin die Grenzen des Machbaren in der Fertigung verschiebt und dafür sorgt, dass das Formpressen ein Eckpfeiler der modernen Produktion bleibt.