Einführung
Das Design von Formen spielt eine entscheidende Rolle bei der Herstellung hochwertiger Silikongummiprodukte. Formen, die zum Formen von Silikonkautschuk verwendet werden, wirken sich direkt auf die endgültige Qualität, Funktionalität und Effizienz aus. Die Optimierung dieses Formdesigns wird immer wichtiger, da Silikonkautschukprodukte in zahlreichen Branchen immer beliebter werden.
Produkte aus Silikonkautschuk sind aufgrund ihrer bemerkenswerten Eigenschaften wie Hitzebeständigkeit, Flexibilität und Haltbarkeit sehr begehrt. Silikonkautschuk wird in zahlreichen Branchen wie der Automobilindustrie, der Elektronik, der Medizintechnik und der Konsumgüterproduktion eingesetzt. Seine Vielseitigkeit und Zuverlässigkeit machen es zum bevorzugten Material für Hersteller, die innovative und dennoch leistungsstarke Produkte entwickeln wollen.
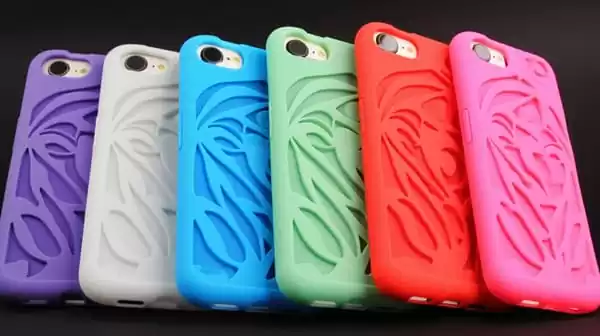
Optimierte Formenkonstruktionen können Herstellern helfen, das volle Potenzial von Silikonkautschuk auszuschöpfen und die steigenden Anforderungen der Verbraucher an Qualitätsprodukte zu erfüllen, da sie einen effizienten Materialfluss gewährleisten, Fehler reduzieren und eine gleichbleibende Qualität der Teile sicherstellen. Die Optimierung der Formgestaltung sorgt nicht nur für eine höhere Produktivität, sondern trägt auch zu ihrem Erfolg und ihrer Wettbewerbsfähigkeit auf dem Markt bei.
II. Verständnis von Flüssigsilikonkautschuk (LSR)-Formverfahren
A. Definition des LSR-Spritzgießens als Spritzgießverfahren für Silikonkautschukprodukte
Das LSR-Spritzgießen (oder Flüssigsilikonkautschuk-Spritzgießen) ist eine Technik des Flüssigspritzgießens, die zur Silikonkautschukprodukte herstellen. Bei dieser Technik wird flüssiger Silikonkautschuk unter hohem Druck und hoher Temperatur in die Hohlräume der Form gespritzt, um die gewünschte Form und die gewünschten Eigenschaften zu erzielen. Das LSR-Spritzgießen bietet mehrere Vorteile gegenüber dem konventionellen Spritzgießen, z. B. hohe Präzision, hervorragende Teilequalität und die Möglichkeit, komplexe Geometrien herzustellen.
Zu Beginn des Prozesses wird ein flüssiges Siliconkautschukmaterial hergestellt, das in der Regel aus zwei Komponenten besteht - einem Basis-Siliconpolymer und einem Katalysator/Vernetzer -, die in einem genauen Verhältnis gemischt werden, um die gewünschten Materialeigenschaften und Vernetzungsmerkmale zu erzielen.
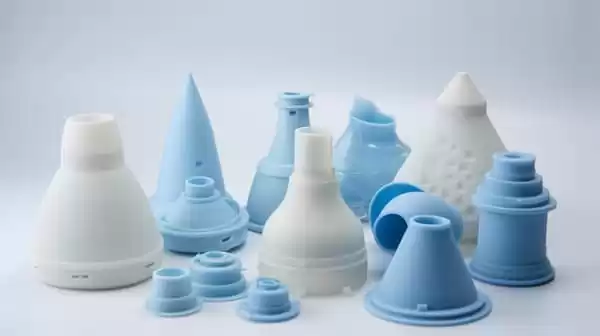
Flüssiger Silikonkautschuk wird in eine Spritzgießmaschine eingespeist, die aus einem beheizten Zylinder, einem Schnecken- oder Kolbenmechanismus für die Materialzufuhr und einem Formhohlraum besteht. Hier wird das Material erhitzt, bevor es unter hohem Druck in die gewünschte Form und Kavität gepresst wird.
Nach dem Einspritzen des flüssigen Silikongummis in eine Form muss er einen Aushärtungsprozess durchlaufen, bei dem er entweder erhitzt oder gekühlt werden kann, um die ordnungsgemäße Aushärtung und Verfestigung des Materials zu fördern. Danach kann die Form geöffnet und das verfestigte Silikongummiteil entnommen werden.
B. Überblick über die Spritzgießmaschine und ihre Rolle im Prozess
Die Spritzgießmaschine ist eine entscheidende Komponente in der LSR-Formprozess. Es besteht aus mehreren Schlüsselelementen, die das Einspritzen und Formen von flüssigem Silikonkautschuk in das gewünschte Produkt erleichtern. Hier finden Sie einen Überblick über die wichtigsten Komponenten und ihre Funktionen:
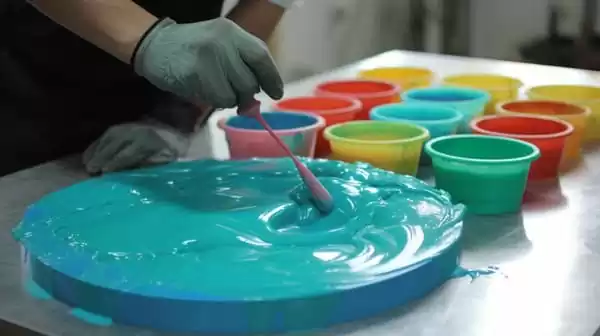
1. das Gehäuse und der Schrauben-/Drückermechanismus:
Der Zylinder enthält das flüssige Silikonkautschukmaterial und erhitzt es auf eine kontrollierte Temperatur. Die Schnecke oder der Kolbenmechanismus bewegt sich dann nach vorne, um das Material in den Formhohlraum zu spritzen.
2. Formhohlraum:
Der Formhohlraum ist der Hohlraum in der Form, der die endgültige Form des Silikonkautschukprodukts bestimmt. Er ist so gestaltet, dass er die gewünschte Geometrie, die Merkmale und die Abmessungen des Teils aufnehmen kann.
3) Heiz- und Kühlsysteme:
Die Spritzgießmaschine umfasst Heiz- und Kühlsysteme, die die Temperatur der Form regulieren. Die Heizung ist notwendig, um den Materialfluss und die Aushärtung zu erleichtern, während die Kühlung dazu beiträgt, das Silikonkautschukteil für den Ausstoß zu verfestigen.
4. die Klemmeinheit:
Die Schließeinheit hält die Werkzeughälften während des Einspritzvorgangs zusammen, um eine korrekte Ausrichtung zu gewährleisten und Materialverluste zu verhindern. Sie übt die nötige Kraft aus, um das Werkzeug während des Einspritzens geschlossen zu halten und zum Auswerfen der Teile zu öffnen.
Die Spritzgießmaschine bietet eine präzise Steuerung der Einspritzgeschwindigkeit, des Drucks, der Temperatur und anderer Prozessparameter und gewährleistet so eine konsistente Produktion und hochwertige Silikonkautschukprodukte.
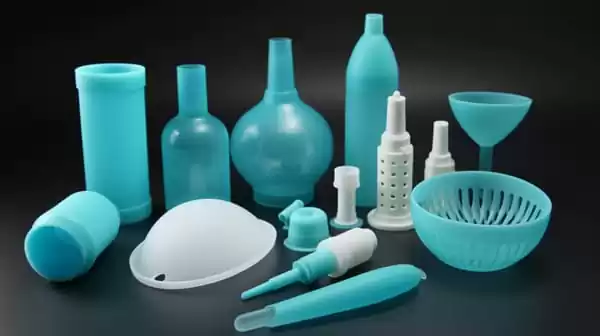
III. Wichtige Überlegungen zur Optimierung der Formgestaltung
A. Die Bedeutung des Verständnisses der Produktanforderungen für eine erfolgreiche Formgestaltung
Um den Formenbau für Silikonkautschukprodukte zu optimieren, ist ein umfassendes Verständnis der Produktanforderungen unerlässlich. Dazu gehören Faktoren wie Abmessungen, Komplexität, Oberflächenbeschaffenheit und funktionale Eigenschaften. Durch das Verständnis dieser Anforderungen können die Hersteller den Formenentwurf auf die spezifischen Bedürfnisse zuschneiden und so die Herstellung hochwertiger Silikonkautschukprodukte sicherstellen, die den Erwartungen der Kunden entsprechen.
B. Design für die Formbarkeit: Vermeidung von komplizierten Geometrien, scharfen Ecken und Hinterschneidungen
Der Entwurf von Silikonkautschukprodukten unter Berücksichtigung der Formbarkeit ist für eine erfolgreiche Optimierung des Formdesigns unerlässlich. Es ist ratsam, komplexe Geometrien, scharfe Ecken und Hinterschneidungen zu vermeiden, da sie beim Entformen Probleme bereiten und die Qualität der Teile beeinträchtigen können. Stattdessen sollten Sie sanfte Kurven und Entformungswinkel einbeziehen, um eine reibungslose Entformung zu erleichtern und einen ordnungsgemäßen Materialfluss innerhalb des Formhohlraums zu gewährleisten.
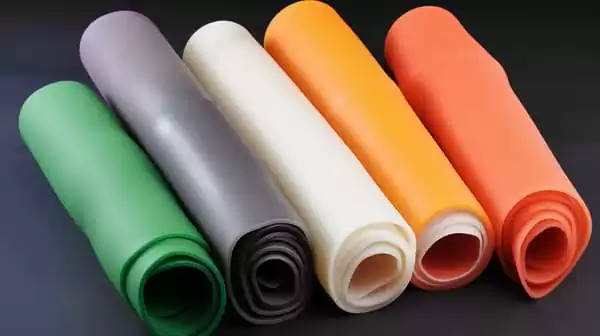
C. Überlegungen zur Wanddicke und zu den Auswirkungen auf die Teilequalität und den Materialfluss
Die richtige Wandstärke ist entscheidend für eine optimale Formgestaltung. Die Beibehaltung einer gleichmäßigen und angemessenen Wandstärke im gesamten Silikonkautschukprodukt gewährleistet eine gleichmäßige Aushärtung und verhindert Probleme wie Lufteinschlüsse oder Materialflussbeschränkungen. Abweichungen in der Wandstärke können zu Schwankungen in der Teilequalität führen, einschließlich Defekten wie Verzug oder Einfallstellen. Die sorgfältige Berücksichtigung der Wanddicke während des Designprozesses ist für das Erreichen einer einheitlichen Teilequalität und eines gleichmäßigen Materialflusses unerlässlich.
D. Entlüftungs- und Entgasungstechniken für effiziente Luft- und Gasabgabe während der Aushärtung
Eine wirksame Entlüftung und Entgasung sind entscheidend für die Optimierung des Formdesigns von Silikonkautschukprodukten. Der Einbau von Entlüftungsöffnungen in die Form ermöglicht das Entweichen eingeschlossener Luft oder Gase während des Aushärtungsprozesses. Eine ordnungsgemäße Entlüftung verhindert die Bildung von Defekten wie Luftblasen oder Hohlräumen, die die Integrität des Produkts beeinträchtigen können. Eine sorgfältige Platzierung der Entlüftungsöffnungen in Bereichen, in denen Luft- oder Gaseinschlüsse wahrscheinlich sind, gewährleistet eine effiziente Entlüftung und optimale Aushärtung.
E. Kühlsystemdesign und seine Auswirkungen auf Zykluszeiten und Maßhaltigkeit
Ein effizientes Kühlsystem ist eine wesentliche Voraussetzung für die Optimierung des Formdesigns und das Erreichen kürzerer Zykluszeiten und Maßhaltigkeit bei der Herstellung von Silikonkautschukprodukten. Eine ordnungsgemäße Kühlung trägt dazu bei, den Aushärtungsprozess zu steuern, die Schrumpfung der Teile zu reduzieren und die Maßhaltigkeit zu erhalten. Die strategische Platzierung von Kühlkanälen in der Form zusammen mit geeigneten Kühlmedien gewährleistet eine gleichmäßige Kühlung und effiziente Wärmeableitung. Gut durchdachte Kühlsysteme steigern die Produktivität, minimieren die Aushärtezeit und tragen zu einer gleichbleibenden Teilequalität bei.
Durch die Berücksichtigung dieser Schlüsselfaktoren während des Optimierungsprozesses des Formdesigns können Hersteller optimale Formdesigns erzielen, die zu hochwertigen Silikonkautschukprodukten führen. Diese Überlegungen, einschließlich Produktanforderungen, Formbarkeit, Wandstärke, Entlüftung und Kühlung, spielen eine entscheidende Rolle bei der Verbesserung der Teilequalität, Produktionseffizienz und Kundenzufriedenheit.
IV. Fortgeschrittene Techniken zur Optimierung der Formgestaltung
A. Insert Molding und seine Vorteile beim Einbau zusätzlicher Komponenten oder Einsätze
Insert Molding ist eine fortschrittliche Technik, die bei der Optimierung des Formdesigns für Silikonkautschukprodukte eingesetzt wird. Dabei werden vor dem Einspritzen des flüssigen Silikongummis zusätzliche Komponenten oder Einsätze in den Formhohlraum eingebracht. Zu den Vorteilen des Insert Molding gehören:
Verbesserte Funktionalität der Teile: Insert Molding ermöglicht die Integration von funktionalen Komponenten, wie z. B. Metalleinsätzen oder elektrischen Anschlüssen, direkt in das Bauteil. Silikonkautschuk-Produkt. Dadurch werden die Leistung und die Funktionalität des Produkts verbessert.
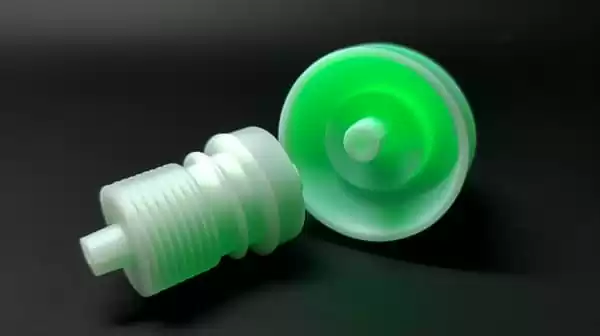
Verbesserte Festigkeit und Stabilität der Teile: Durch die sichere Verbindung der Einsätze mit dem Silikonkautschuk verbessert das Insert Molding die strukturelle Integrität und Stabilität des Endprodukts. Dadurch werden sekundäre Montageprozesse überflüssig, was Kosten und potenzielle Fehlerquellen reduziert.
Flexibilität beim Design: Das Spritzgießen bietet Designflexibilität und ermöglicht die Herstellung komplexer Geometrien und Produkte aus mehreren Materialien. Es ermöglicht die Kombination verschiedener Materialien mit unterschiedlichen Eigenschaften und erweitert damit das Anwendungsspektrum von Silikonkautschukprodukten.
B. Einsatz von Simulationswerkzeugen und Finite-Elemente-Analyse (FEA) zur Verbesserung der Entwurfsgenauigkeit
Simulationswerkzeuge und Finite-Elemente-Analysen (FEA) sind leistungsstarke Hilfsmittel für die Optimierung der Werkzeugkonstruktion. Sie helfen bei der Verbesserung der Konstruktionsgenauigkeit, der Vorhersage des Materialflusses, der Identifizierung potenzieller Defekte und der Optimierung der Prozessparameter. Durch den Einsatz von Simulationswerkzeugen und FEA können Hersteller:
Visualisieren und analysieren Sie das Füllmuster: Simulationswerkzeuge bieten eine visuelle Darstellung des Fließverhaltens des flüssigen Silikonkautschuks in der Formkavität. Dies ermöglicht die Identifizierung potenzieller fließbedingter Probleme, wie Lufteinschlüsse, unzureichende Füllung oder übermäßige Materialscherung.
Optimieren Sie Anschnittstellen und -größen: Simulationswerkzeuge helfen bei der Bestimmung der optimalen Anschnittpositionen und -größen für Einspritzpunkte. Dies gewährleistet einen ordnungsgemäßen Materialfluss, minimiert fließbedingte Fehler und verbessert die Teilequalität.
Vorhersage von Teileschrumpfung und Verzug: FEA kann die Schwindung und den Verzug von Teilen vorhersagen und ermöglicht so Designanpassungen, um diese Probleme zu minimieren. Dies gewährleistet Maßgenauigkeit und verringert die Wahrscheinlichkeit von Verformungen nach dem Gießen.
C. Überlegungen zu Hinterschneidungen, Trennebenen und Trennebenen
Bei der Optimierung des Formdesigns für Silikongummiprodukte müssen unbedingt Überlegungen zu Hinterschneidungen, Trennebenen und Trennflächen angestellt werden. Zu diesen Faktoren gehören:
- Hinterschneidungen: Hinterschneidungen sind Merkmale oder Vertiefungen in der Produktgeometrie, die die Entnahme von Teilen erschweren. Innovative Techniken der Werkzeugkonstruktion, wie z. B. einklappbare Kerne oder mechanische Schieber, können eingesetzt werden, um Hinterschneidungen zu berücksichtigen und eine erfolgreiche Entformung zu ermöglichen.
- Trennebenen: Trennebenen sind die Bereiche, in denen sich die Formhälften treffen, was zu einer sichtbaren Linie auf dem fertigen Produkt führt. Die Platzierung der Trennlinien sollte sorgfältig überlegt werden, um ihre Auswirkungen auf das kosmetische Erscheinungsbild und die Funktionalität des Produkts zu minimieren.
- Trennebenen: Als Trennflächen werden die Formflächen bezeichnet, die die Formhälften voneinander trennen. Die Sicherstellung glatter und präziser Trennflächen trägt zu einer korrekten Ausrichtung bei und verhindert die Bildung von Graten während des Silikonformverfahrens.
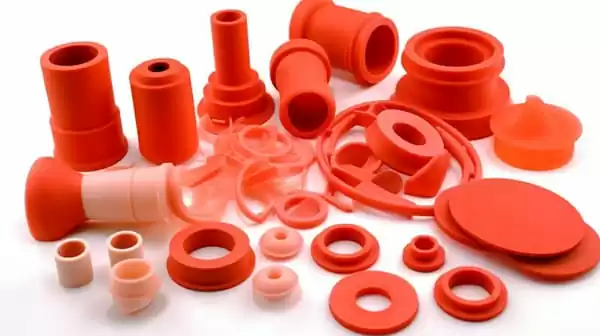
D. Optimierung von Werkzeugtemperatur, Einspritzdruck und Werkzeuginnendruck für gleichbleibende Qualität
Die Optimierung der Werkzeugtemperatur, des Einspritzdrucks und des Werkzeuginnendrucks ist entscheidend für eine gleichbleibende Qualität von Silikonkautschukprodukten. Zu den wichtigsten Überlegungen gehören:
- Formtemperatur: Die ordnungsgemäße Steuerung der Formtemperatur beeinflusst den Materialfluss, die Aushärtungszeit und die Dimensionsstabilität. Die Optimierung der Formtemperatur gewährleistet eine gleichbleibende Teilequalität und minimiert Schwankungen der mechanischen Eigenschaften.
- Einspritzdruck: Der Einspritzdruck beeinflusst den Materialfluss, das Füllverhalten und die Nachbildung der Formmerkmale. Die Optimierung des Einspritzdrucks ermöglicht eine vollständige Füllung des Formhohlraums ohne übermäßige Beanspruchung der Form oder des Teils.
- Werkzeuginnendruck: Die Überwachung des Werkzeuginnendrucks während des Formprozesses trägt dazu bei, eine gleichbleibende Teilequalität und Maßhaltigkeit zu gewährleisten. Sie ermöglicht Echtzeit-Anpassungen der Einspritzparameter und optimiert so den Produktionsprozess.
Durch die Anwendung dieser fortschrittlichen Techniken bei der Optimierung des Formenbaus können Hersteller die Funktionalität, Qualität und Effizienz von Silikonkautschukprodukten verbessern. Einsatz
V. Vorteile des LSR-Formens für Silikongummiprodukte
A. Vorteile von LSR-Materialien, einschließlich eines breiten Spektrums an mechanischen Eigenschaften
Das LSR-Spritzgießen bietet mehrere Vorteile für Silikonkautschukprodukte, vor allem aufgrund der einzigartigen Eigenschaften von Flüssigsilikonkautschukmaterialien. Zu diesen Vorteilen gehören:
- Breites Spektrum an mechanischen Eigenschaften: LSR-Materialien können so formuliert werden, dass sie ein breites Spektrum an mechanischen Eigenschaften aufweisen, darunter unterschiedliche Härtegrade, Flexibilität und Elastizität. Dadurch können Hersteller das Material auf spezifische Produktanforderungen in verschiedenen Branchen zuschneiden.
- Hitzebeständigkeit und Haltbarkeit: LSR-Materialien bieten eine ausgezeichnete Hitzebeständigkeit und Haltbarkeit und eignen sich daher für Anwendungen, die hohen Temperaturen, rauen Umgebungen oder häufigem Gebrauch ausgesetzt sind. Sie können extremen Temperaturen standhalten, ohne ihre Integrität zu beeinträchtigen.
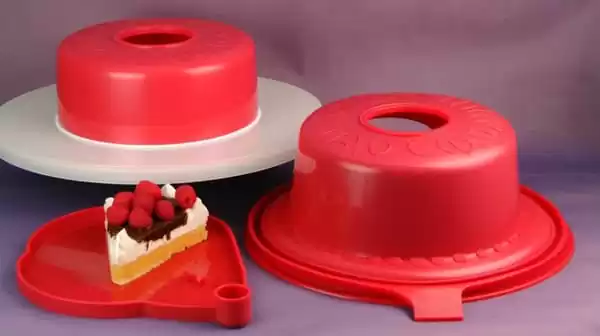
B. Verbessertes kosmetisches Erscheinungsbild und glattere Oberflächen im Vergleich zu herkömmlichen Gussformen
LSR-Formen bieten ein besseres kosmetisches Erscheinungsbild und glattere Oberflächen als herkömmliche Formgebungsverfahren. Dies ist auf die einzigartigen Eigenschaften von Flüssigsilikonkautschuk zurückzuführen, wie z. B. seine niedrige Viskosität und seine selbstnivellierenden Eigenschaften. Zu den Vorteilen gehören:
- Beseitigung von Oberflächendefekten: LSR-Materialien fließen leicht in den Formhohlraum, was eine gleichmäßige Verteilung gewährleistet und das Auftreten von Oberflächenfehlern wie Einfallstellen, Fließlinien oder Oberflächenmängeln minimiert.
- Verbesserte Ästhetik der Teile: LSR-Formen ermöglichen die Nachbildung komplizierter Details und feiner Merkmale mit hoher Präzision, was zu visuell ansprechenden Produkten führt. Die glatten Oberflächen, die durch LSR-Formen erzielt werden, tragen zur kosmetischen Gesamtqualität von Silikonkautschukteilen bei.
C. Möglichkeiten der Massenproduktion und Eignung für verschiedene Branchen
LSR-Formen eignen sich hervorragend für die Massenproduktion Herstellung von Silikonkautschukprodukten. Zu den Vorteilen gehören:
- Kürzere Zykluszeiten: LSR-Materialien härten schnell aus, was im Vergleich zu anderen Gummiformverfahren kürzere Formungszyklen ermöglicht. Dies führt zu einer höheren Produktionseffizienz und einem höheren Ausstoß.
- Konsistenz und Wiederholbarkeit: LSR-Formen ermöglichen eine konsistente und wiederholbare Produktion von Silikongummiprodukten, die eine Einheitlichkeit der Abmessungen, Eigenschaften und Qualität der Teile gewährleistet. Dies ist von entscheidender Bedeutung für Branchen, die hohe Stückzahlen mit minimalen Abweichungen benötigen.
- Breite Anwendbarkeit: LSR-Spritzgießen ist in verschiedenen Branchen anwendbar, z. B. in der Automobil-, Elektronik-, Gesundheits- und Konsumgüterindustrie. Es erfüllt die unterschiedlichsten Produktanforderungen, von medizinischen Komponenten bis hin zu industriellen Dichtungen, Dichtungen und Unterhaltungselektronik.
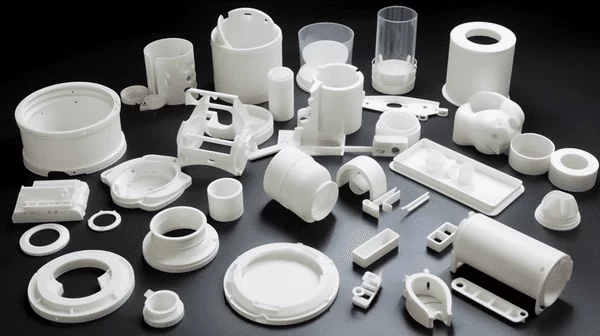
D. Auswirkung der richtigen Wanddicke auf die Integrität des Teils und kosmetische Mängel
Die Optimierung der Wandstärke beim LSR-Spritzgießen hat einen erheblichen Einfluss auf die Integrität der Teile und kosmetische Mängel. Zu den wichtigsten Überlegungen gehören:
- Strukturelle Integrität: Eine angemessene Wandstärke gewährleistet die strukturelle Integrität und Festigkeit von Silikonkautschukprodukten. Sie verhindert Probleme wie Verformungen, Verwerfungen oder das Versagen von Teilen aufgrund einer unzureichenden Materialverteilung oder ungleichmäßiger Aushärtung.
- Kosmetische Mängel: Die Beibehaltung der richtigen Wandstärke im gesamten Produkt verringert das Auftreten von kosmetischen Mängeln wie Oberflächenabweichungen, Einfallstellen oder sichtbaren Fließlinien. Eine gleichmäßige Wanddicke fördert die gleichmäßige Aushärtung und den Materialfluss, was zu optisch ansprechenden Teilen führt.
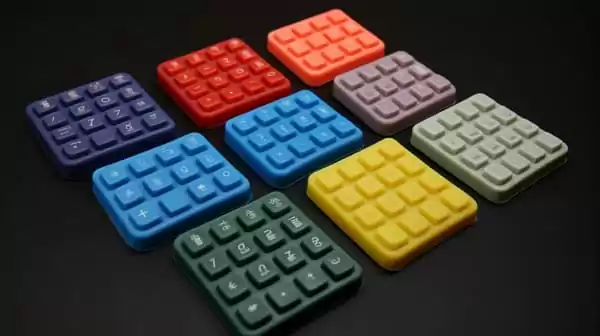
Durch die Nutzung der Vorteile des LSR-Formens können Hersteller Silikonkautschukprodukte herstellen mit außergewöhnlichen mechanischen Eigenschaften, einem verbesserten kosmetischen Erscheinungsbild und der Möglichkeit der Massenproduktion. Die Fähigkeit, die richtige Wandstärke zu erreichen, gewährleistet die Integrität der Teile und minimiert kosmetische Mängel, was zum Gesamterfolg und zur Wettbewerbsfähigkeit von Silikonkautschukprodukten auf dem Markt beiträgt.
Schlussfolgerung
Zusammenfassend lässt sich sagen, dass die Optimierung des LSR-Spritzgießprozesses und des Designs für die Herstellung hochwertiger Silikonkautschukprodukte von entscheidender Bedeutung ist. Durch die Umsetzung wichtiger Strategien und Überlegungen können Hersteller das Potenzial des Flüssigsilikonkautschuk (LSR)-Spritzgussverfahrens maximieren und präzise, langlebige und optisch ansprechende Produkte liefern.
Im gesamten Artikel haben wir die Bedeutung des Verständnisses der Produktanforderungen, der Gestaltung der Formbarkeit, der Berücksichtigung der Wandstärke, der Einbeziehung von Entlüftungs- und Entgasungstechniken sowie der Optimierung von Kühlsystemen erörtert. Diese und andere Faktoren spielen eine entscheidende Rolle bei der optimalen Formgestaltung für die Herstellung von Silikonkautschukprodukten.
Eine sorgfältige Werkzeugkonstruktion ist für die Gewährleistung einer gleichbleibenden Teilequalität, die Minimierung von Fehlern und die Steigerung der Produktivität unerlässlich. Durch die sorgfältige Berücksichtigung von Hinterschneidungen, Trennebenen und Trennflächen können Hersteller die Formgestaltung optimieren und kosmetische Fehler minimieren.
Die Vorteile des LSR-Formens, einschließlich des breiten Spektrums an mechanischen Eigenschaften von LSR-Materialien, des verbesserten kosmetischen Aussehens und der Eignung für die Massenproduktion, unterstreichen die Bedeutung eines optimierten Formdesigns. LSR-Formen ermöglichen die Herstellung von Silikonkautschukprodukten mit außergewöhnlicher Leistung, Haltbarkeit und Ästhetik.
Zusammenfassend lässt sich sagen, dass Hersteller das volle Potenzial des LSR-Formprozesses ausschöpfen können, wenn sie der Optimierung des Formdesigns große Aufmerksamkeit schenken. Das Ergebnis sind hochwertige Silikongummiprodukte, die die Erwartungen der Kunden erfüllen, den Industriestandards entsprechen und einen Wettbewerbsvorteil auf dem Markt bieten. Mit einer sorgfältigen Formgestaltung können Hersteller präzise, langlebige und optisch ansprechende Silikongummiprodukte für eine breite Palette von Anwendungen in verschiedenen Branchen sicherstellen.