1. Eigenschaften von Silikonmaterial
A. Siliconrohstoffe sind im Allgemeinen gelartig, ähnlich wie Knetmasse, farblos, durchscheinend und geruchlos.
B. Seine Haupteigenschaften sind sowohl Hochtemperaturbeständigkeit (bis zu 300°C) als auch Tieftemperaturbeständigkeit (mindestens -100°C). Es handelt sich um den derzeit besten kälte- und hochtemperaturbeständigen Kautschuk; gleichzeitig verfügt er über eine ausgezeichnete elektrische Isolierung und eine hohe Stabilität gegenüber thermischer Oxidation und Ozon und ist chemisch inert.
Der Nachteil ist, dass die mechanische Festigkeit gering ist, die Ölbeständigkeit, Lösungsmittelbeständigkeit und Säure- und Alkalibeständigkeit schlecht sind, es ist schwierig zu vulkanisieren, und der Preis ist teurer. Betriebstemperatur: -60℃~+200℃. Die oben ist die Beschreibung der Silikonkautschuk im Handbuch.
C. Verwendungstemperatur: Wie oben erwähnt, wird sie im Allgemeinen auf -40°C bis 200°C eingestellt und kann in kurzer Zeit 230°C erreichen.
D. Alterungsproblem: Öl-, Säure- und Alkalibeständigkeit sind schlecht, und es hat wenig mit der Belastung zu tun.
E. Adhäsionsproblem: Vor der Oberflächenbehandlung, zusätzlich zur Verwendung von Silikonprodukte Als Klebstoffe für die Verbindung mit Silikonteilen muss die Haftung zu anderen Teilen oberflächenaktiviert werden, und die Klebstoffoberfläche kann durch Vulkanisierung ausgehärtet werden.
Alle Stoffe, die mit Kautschuk reagieren oder ihn vernetzen können, werden als Vulkanisiermittel, auch Vernetzungsmittel genannt, bezeichnet. Es gibt viele Arten von Vulkanisiermitteln, und es werden immer mehr.
Zu den verwendeten Vulkanisationsmitteln gehören Schwefel, Selen, Tellur, schwefelhaltige Verbindungen, Metalloxide, Peroxide, Harze, Chinone und Amine.
F. Materialhärte: Nach der Shore-Härte können die Kunststoffteile auf dem Binnenmarkt theoretisch zwischen 10 und 80 Grad ausgewählt werden.
Die leicht zu findenden liegen im Allgemeinen zwischen 20 und 70 Grad, die am häufigsten verwendeten zwischen 40 und 50 Grad.
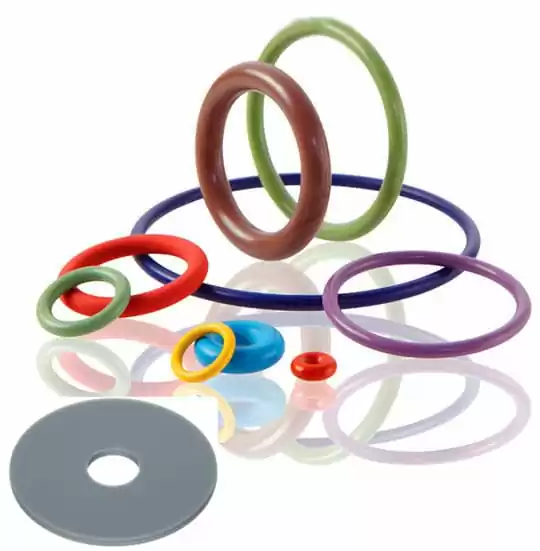
2. Der Herstellungsprozess von Silikonprodukten
A: Form und Farbe der Rohmaterialien
B: Nach der Farbabstimmung und dem Kneten werden die verschiedenfarbigen Flocken aus milchig-weißem Kieselgel hergestellt.
C: Nach dem Kneten und Formen werden die Rohmaterialien in Streifen gepresst und in Streifen geschnitten
D: Vulkanisationsgießen
E: Beschneiden, Kantenentfernung, Kontrolle, Verpackung
F: Beendet Silikonprodukte
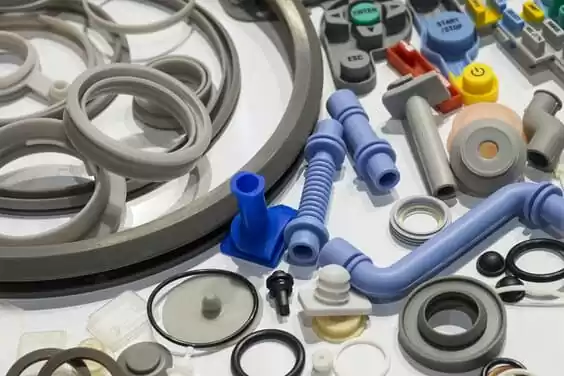
3. Größe und Merkmale des Produkts
A. Begrenzte Größe: Der dickste Teil kann 15~20MM sein, wenn es eine Kugel ist, kann der Durchmesser 30MM sein. Im Allgemeinen ist die empfohlene Dicke nicht mehr als 3MM.
Wenn sie größer als 3 mm ist, dauert die Vulkanisierung länger und die Kosten steigen. Das dünnste Teil kann theoretisch 0,2 mm erreichen, aber die dünnste 0,3 mm wird im Allgemeinen in der Konstruktion genommen, und 0,4 mm wird empfohlen.
B. Relative Größe: In Bezug auf den Dickenunterschied wird empfohlen, dass der dünnste Teil und der dickste Teil das Dreifache nicht überschreiten sollten. Solche Probleme hängen hauptsächlich von den Temperatur- und Druckanforderungen bei der Vulkanisierung des Materials ab.
C. Schrumpfungsrate: Die Schrumpfungsrate des Silikonmaterial steht im Zusammenhang mit der Härte des Materials. Die meisten der vom Hersteller gelieferten Sekundärwerkstoffe liegen zwischen 1.022 und 1.042.
Bei Materialien mit einer Temperatur von 40 bis 50 Grad liegt die Schrumpfungsrate im Allgemeinen bei 1,03. Im Vergleich zu Kunststoff leiden Silikonprodukte nicht unter ähnlichen offensichtlichen Oberflächenfehlern aufgrund von Schrumpfung.
D. Maßhaltigkeit: Da die meisten der Silikonkautschuk-Produkte sind eine Form mit mehreren Kavitäten, die Anzahl der Kavitäten ist sehr groß im Vergleich zu den Kunststoffprodukten. Daher ist es nicht so bequem wie Kunststoffprodukte in der Größenkontrolle.
Die allgemeine Genauigkeit liegt bei plus/minus 0,1, die des Hochpräzisionsprodukts bei plus/minus 0,05. Wenn es verwendet wird, um das Loch des Kunststoffteils und den Knopf anzupassen, beträgt der Mindestabstand 0,1 pro Seite, und der empfohlene Wert ist 0,2 pro Seite.
E. Formgestaltung: Für Gummihülsenteile reicht es im Allgemeinen aus, dem Formenbauunternehmen die Originalzeichnung entsprechend der Produktformzeichnung zur Verfügung zu stellen und das Anpassungsproblem zu erklären, das vom Formenbauunternehmen entschieden wird.
Unter normalen Umständen, abhängig von der Größe des Produkts, ist die Koordination zwischen der Gummimanschette und dem Produkt in der Regel eine negative Abweichung von 0,2 ~ 0,5 kleine auf einer Seite.
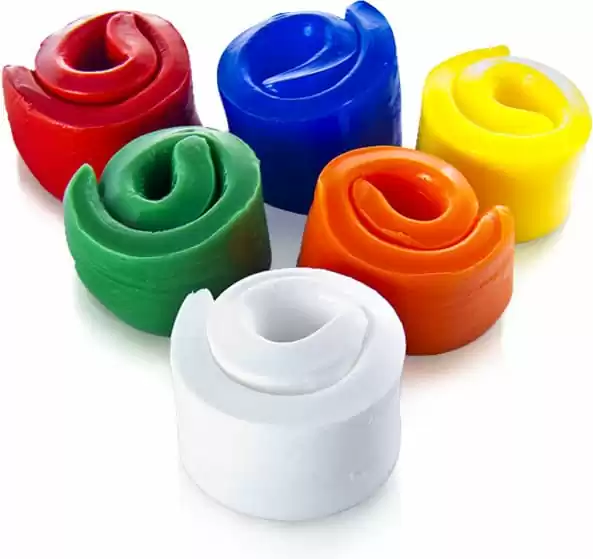
4. Struktur der Form
A. Obergrenze der Formdicke:
Vorläufig 250mm, die Größe kann 500X500 erreichen, und das Produkt kann bis zu 400X400 im Formbereich sein. Die Formstruktur ist in der Regel in die obere Form, untere Form, Bodenplatte, obere Platte, Auswerferstift, Formkern, Scharnier und andere Hilfsteile unterteilt. Beim Entwurf SilikonprodukteBei der Herstellung der Produkte ist auf die Eigenschaften ihrer Formen und Produktionsverfahren zu achten:
B. Entformung:
Die Entformung von Silikonprodukten kann direkt und zwangsweise erfolgen. Bei Produkten ohne Konstruktionsfehler liegt die Größenanforderung für die Zwangsentformung hauptsächlich im Verhältnis des Umfangs des größten Teils des Formkerns zum kleinsten Schließteil bei der Entformung. Bei Produkten unter 55° kann dies 2-3 Mal erfolgen. An der Öffnung kann es zu Rissen und scharfen Ecken kommen.
Da bei der Vulkanisierung eine Temperatur von 180 Grad Celsius erforderlich ist, erfolgt die Entformung fast ausschließlich manuell, mit Ausnahme der oberen und unteren Trennung der Form selbst. Daher sollten die Bequemlichkeit und Schnelligkeit der Entnahme bei der Konstruktion der Teile berücksichtigt werden.
Um die Vulkanisierungsqualität und die Effizienz der Massenproduktion der Teile nicht durch die lange Entformungszeit zu beeinträchtigen. Da die Auslösemethode des Silikons hauptsächlich manuell ist, und der Aktionshub der oberen Platte auch klein ist, hat die Silikonform keine geneigte Oberseite im Vergleich zu der Plastikform. Im Allgemeinen ist kein Kernzug vorgesehen.
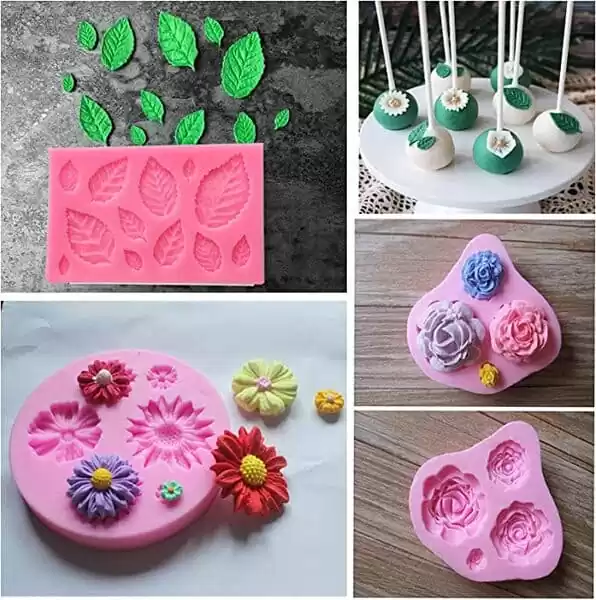
C. Fixierung des Kerns:
Im Gegensatz zu Kunststoffformen werden die Kerne von Silikonformen im Allgemeinen zusammen mit den Produktteilen entfernt, wenn die Spritzgussform wird geöffnet und die Teile werden entnommen. Daher sind die Fixierung und die genaue Positionierung des Formkerns schwieriger zu handhaben als bei der Kunststoffform, und die Steifigkeit des Formkerns ist höher.
Die Kerne werden in der Regel gemeinsam hergestellt und alle Kerne werden auf einmal befestigt. Oder der Formkern wird durch Hilfswerkzeuge geführt, damit er schnell positioniert werden kann. Da beim Aufspannen der Form ein hoher Druck entsteht, muss streng darauf geachtet werden, dass sich der Formkern nicht bewegt.
D. Kernziehen:
Im Allgemeinen kann er nicht automatisch verschoben werden, aber er kann zwangsweise entfernt werden, und das Kernziehen wird nur für kleine Strukturen verwendet. Die Einstellung für das Kernziehen ist ähnlich wie die des PlastikformSie wird jedoch manuell entfernt, wenn die Form geöffnet wird.
Darüber hinaus nimmt das Kernziehen einen großen Raum in der Form ein, was nicht nur die Verarbeitung im Übermaß erschwert. Silikonform in einer Form, hat aber auch eine geringe Ausnutzung des Formraums. Ziehen Sie den Kern also nicht so weit wie möglich heraus.
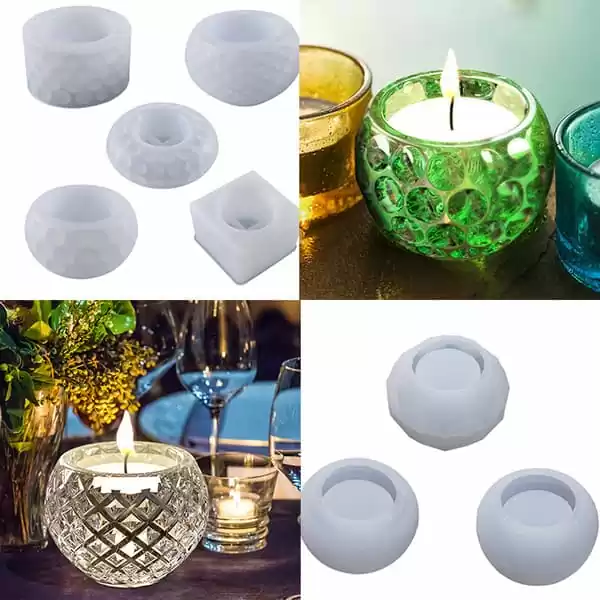
E. Die Form:
Silikonprodukte haben eine große Zähigkeit, wenn die Oberfläche intakt ist, aber sobald es Risse gibt, dehnen sich die Risse unter der Einwirkung einer äußeren Kraft schnell aus. Das heißt, Silikonprodukte sind sehr empfindlich gegenüber Rissen.
In Anbetracht dieser Probleme sollte auf die korrekte Formgestaltung von Silikonteilen geachtet werden: Es sollte keine scharfen Ecken in allen Positionen geben, um Spannungskonzentrationen und Risse zu vermeiden. Der R-Winkel an der Öffnung sollte nicht kleiner als 0,5 sein.
F. Selbstablösende Kante:
Die Hauptfunktion des selbstablösenden Randes: ist es, überschüssiges Gummi aufzunehmen; erleichtert das Ausblasen der Form; einfach, den Grat zu trimmen.
Die selbstablösende Kante besteht im Allgemeinen aus einer dünnen Kante an der Trennfläche des Teils und einer entsprechenden relativ starken Abrisskante. Die Dicke der dünnen Kante ist in der Regel 0,1-0,2, die Dicke der Abrisskante ist in der Regel 0,8 und die Breite beträgt in der Regel 1~2MM.
G. Einfügen:
Es können verschiedene Arten von Einlagen in Silikonprodukte eingesetzt werden, wobei jedoch mehrere Punkte zu beachten sind Erstens sollte die Oberfläche der eingebetteten Teile vorbehandelt werden, vor allem durch Oberflächenvulkanisierung oder Oberflächenaktivierung.
Andernfalls wird es schwierig sein, die Einlage und den Klebstoff fest miteinander zu verbinden. Der zweite Punkt ist die feste Positionierung des Einsatzes, der in der vertikalen Richtung in einer Richtung fixiert werden kann, in den anderen Richtungen jedoch vollständig fixiert werden muss. So wird verhindert, dass sich die Einlage während des gesamten Formprozesses bewegt.
Der dritte Punkt ist die Dicke des Klebstoffs um die Einlage herum. Bei vollständig gekapselten Teilen (bei denen alle Oberflächen gekapselt sind, so dass die Einlage nicht positioniert werden kann), sollte eine Mindestdicke von 0,5 mm um die Einlage herum verwendet werden. Bei Einsätzen mit Positionierung sollte die Dicke der peripheren Klebeschicht über 0,4 mm liegen.
H. Andere Hilfsprozesse:
Verfahren der Leimeinspritzung (Verleimung):
Ähnlich wie bei der Spritzgießen Beim Spritzgussverfahren werden die zu spritzenden Teile zunächst fixiert, und die erste Formschicht wird geschlossen, um zu verhindern, dass die Rohstoffe während des Spritzvorgangs die nicht für den Spritzguss bestimmten Teile verunreinigen. Dann wird die zweite Schicht der Form geschlossen und die Gummimischung in Form gepresst.
Rollendes Verfahren: Handformung des Gummis
Gießen: Dieses Herstellungsverfahren kann im Falle einer Vollkapselung angewendet werden.
Eintauchen: Das Rohmaterial des Gummikörpers ist flüssig, und das Werkstück wird mehrmals in das Rohmaterial getaucht. Die innere Schicht des Rohmaterials wird vulkanisiert und dann erneut eingetaucht, bis die gewünschte Dicke erreicht ist.
Epoxid: Das Rohmaterial hat eine gute Fließfähigkeit, ähnlich wie Farbe, und wird bei Raumtemperatur vulkanisiert. Die Form ist ein relativ einfacher, meist manueller Vorgang, und die nächste Beschichtung wird aufgetragen, wenn die erste Schicht schnell ausgehärtet ist.
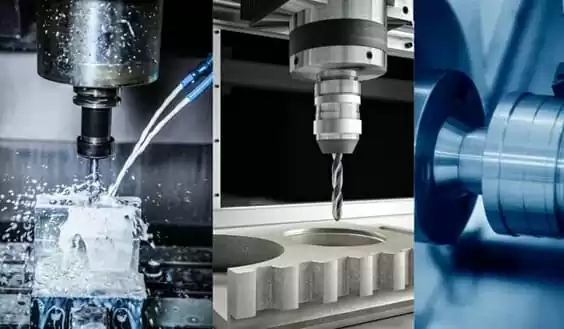
L. Mehrfarbige Produkte:
A ist in 2 Sätze von Vulkanisation Formen unterteilt, und B ist von Hand gefärbt, einmal vulkanisiert, die Farbe Trennung Teil der Teile ist erforderlich, um eine bestimmte Höhe haben, um die Kombination von Farbmischung leitfähigen Klebstoff, sekundäre Vulkanisation Silikon und vermeiden Silikon (Gummi) kann ohne Behandlung direkt vulkanisiert werden Bonding 5. Härtemessung und Werkzeuge.
Das am häufigsten verwendete Instrument zur Messung der Gummihärte ist das Shore-Durometer (auch als Shore bekannt). Mit einer Feder wird ein Metalleindringkörper in die Oberfläche des Materials gedrückt und gemessen, wie tief er eindringt.
Das Gerät misst Eindringtiefen von null bis 0,100 Zoll. Ein Messwert von Null auf der Skala bedeutet, dass der Eindringkörper die Grenztiefe durchdrungen hat, während ein Messwert von 100 bedeutet, dass die Eindringtiefe Null ist. Es gibt verschiedene Shore-Härteprüfgeräte mit unterschiedlichen Härtebereichen und Automatisierungsgraden.
Eine der am häufigsten verwendeten Skalen ist die Shore-A-Skala. Shore-A-Durometer haben einen stumpfen Eindringkörper und eine mittlere Feder. Wenn die Messwerte über 90 liegen, wird das Shore-A-Durometer ungenau. Für solche härteren Materialien wird ein Shore-D-Durometer verwendet. Es hat einen scharfen Eindringkörper und eine starke Feder für tiefes Eindringen.
Für die Messung härterer Kunststoffe verwenden Sie ein Durometer mit einem schärferen und elastischeren Eindringkörper, z. B. ein Rockwell-Durometer. Im Gegensatz dazu werden Shore 00-Durometer zur Messung von weichen Gelen und Schaumgummis verwendet.

Die meisten Mehrfachwerkstoffe können der anfänglichen Belastung standhalten, geben aber mit der Zeit aufgrund von Kriechen und Relaxation nach. Durometer-Messungen können sofort oder nach einer bestimmten Verzögerungszeit, in der Regel 5 bis 10 Sekunden, vorgenommen werden. Sofortige Ablesungen zeigen immer höhere (oder härtere) Werte als verzögerte Ablesungen.
Verzögerungswerte sind nicht nur repräsentativer für die Härte des Materials, sondern auch für seine Elastizität. Ein schwächeres, weniger elastisches Material neigt eher zum Kriechen als ein stärkeres und elastischeres Material.
Um die Gültigkeit der Daten zu gewährleisten, sind präzise Prüfverfahren erforderlich. Um einen genauen Messwert zu erhalten, müssen Sie ein Prüfstück haben, das flach und dick genug ist, damit der Eindringkörper nicht von der Auflagefläche beeinflusst wird.
In der Regel beträgt die erforderliche Dicke 0,200 Zoll, aber auch starre Materialien mit geringerer Verformung können bei geringeren Dicken genau geprüft werden.