Pendahuluan
Pembuatan cetakan kompresi adalah proses yang banyak digunakan untuk membuat material komposit dengan kekuatan dan daya tahan yang unggul. Proses ini melibatkan penerapan tekanan dan suhu yang tinggi pada material cetakan di dalam rongga cetakan, sehingga menghasilkan bentuk yang diinginkan. Bahan yang digunakan dalam pencetakan kompresi dapat berkisar dari bahan termoset seperti resin epoksi dan senyawa pencetakan massal (BMC), hingga komposit matriks polimer (PMC) dan senyawa pencetakan lembaran (SMC).
Viskositas material memainkan peran penting dalam pencetakan kompresi, menentukan ketahanannya terhadap aliran dan deformasi di bawah tekanan. Ini memainkan peran integral dalam mengontrol aliran material selama pencetakan, yang memengaruhi sifat mekanik serta akurasi dimensinya.
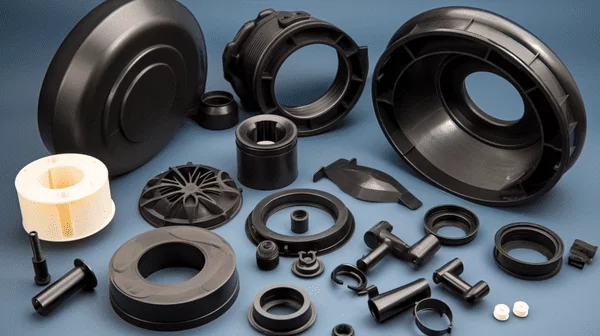
Dalam artikel ini, kita akan menyelidiki faktor-faktor yang memengaruhi cetakan kompresi proses dan bahan yang digunakan. Selain itu, kami akan membahas pertimbangan utama selama desain cetakan seperti viskositas bahan yang digunakan dalam cetakan kompresi. Selain itu, kami akan membahas berbagai proses pencetakan kompresi dan sifat mekaniknya, aplikasi pencetakan kompresi, dan potensi pengembangan di masa depan dalam bidang manufaktur.
II. Faktor-faktor yang Mempengaruhi Proses Pencetakan Kompresi
Pencetakan kompresi adalah proses manufaktur yang sangat terspesialisasi yang memerlukan pertimbangan cermat dari berbagai faktor. Ini termasuk persyaratan tekanan dan suhu tinggi, bahan dan komposisi cetakan, desain dan kompleksitas cetakan, proses dan waktu pengawetan.
Tekanan dan suhu yang diperlukan untuk pencetakan kompresi berbeda tergantung pada bahan yang dicetak dan kerumitan desain cetakan. Selain itu, jenis dan komposisi bahan cetakan memainkan peran penting dalam langkah ini; Anda harus mempertimbangkan dengan cermat bahan mana yang memenuhi persyaratan aplikasi Anda sebelum memulai langkah ini.
Desain dan kerumitan cetakan dapat secara signifikan memengaruhi seberapa besar tekanan dan suhu yang diperlukan, serta akurasi dimensi produk akhir. Mencapai desain cetakan yang tepat sangat penting untuk mencapai sifat mekanis yang diinginkan dan presisi dalam dimensi.
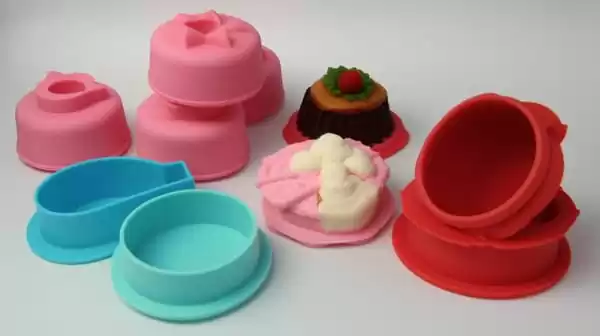
Proses dan waktu pengawetan merupakan elemen penting dalam cetakan kompresi. Durasi pengawetan tergantung pada bahan yang dicetak, desain cetakan, serta suhu dan tekanan yang diterapkan selama prosedur. Kontrol yang akurat atas variabel-variabel ini diperlukan untuk menghasilkan sifat mekanis yang diinginkan dan akurasi dimensi pada produk akhir.
Secara keseluruhan, pertimbangan yang tepat dari semua elemen ini sangat penting untuk mendapatkan hasil yang konsisten dan berkualitas tinggi apabila melakukan pencetakan kompresi.
III. Bahan yang Digunakan dalam Cetakan Kompresi
Cetakan kompresi dapat digunakan dengan berbagai bahan, yang paling populer adalah bahan termoset, komposit matriks polimer (PMC) dan senyawa cetakan lembaran (SMC).
Bahan termoset
Bahan termoset seperti resin epoksi dan senyawa cetakan massal (BMC), banyak digunakan dalam cetakan kompresi karena kekuatan, kekakuan, dan stabilitas dimensinya yang superior. Polimer ini mengalami reaksi kimia ketika dipanaskan dan diawetkan, menciptakan bahan yang sangat kuat dengan karakteristik mekanis yang sangat baik.
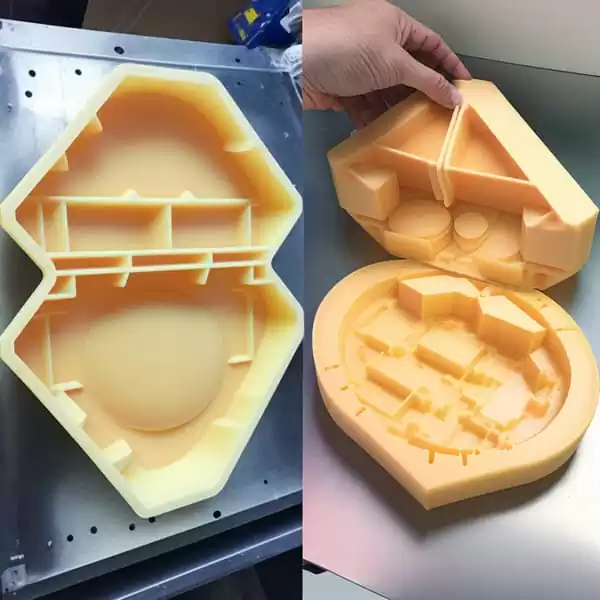
Komposit matriks polimer (PMC)
Komposit matriks polimer (PMC) adalah bahan lain yang biasa digunakan dalam cetakan kompresi. Komposit ini terdiri dari matriks resin polimer yang diperkuat dengan serat seperti kaca, karbon, atau aramid untuk meningkatkan kekuatan dan kekakuan. Dengan demikian, PMC memiliki aplikasi yang membutuhkan kekuatan tinggi.
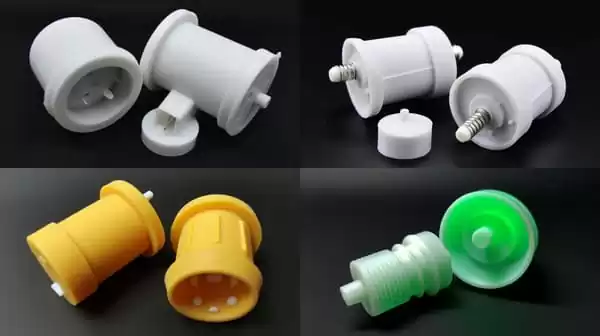
Senyawa cetakan lembaran (SMC) dan termoplastik alas kaca (GMT)
Senyawa cetakan lembaran (SMC) dan termoplastik alas kaca (GMT) keduanya digunakan dalam pencetakan kompresi. SMC terdiri dari matriks resin termoset, serat kaca cincang, dan pengisi mineral, sedangkan GMT memiliki matriks resin akrilik dengan serat kaca yang diorientasikan secara acak. Kedua bahan tersebut menawarkan kekuatan, kekakuan, dan stabilitas dimensi yang sangat baik saat dikompresi.
Ketika memilih material untuk cetakan kompresi, ada beberapa hal yang perlu dipertimbangkan: sifat mekanik yang diinginkan, efisiensi biaya dan volume produksi. Pemilihan material yang tepat adalah kunci dalam mencapai hasil yang diinginkan dalam pencetakan kompresi.
IV. Pertimbangan Desain Cetakan untuk Cetakan Kompresi
Apakah Anda berada di pasar untuk cetakan kompresi? Pertimbangkan faktor-faktor desain ini ketika membuat desain Anda.
Kapan mendesain cetakan untuk pencetakan kompresidesain cetakan sangat penting untuk mencapai kesuksesan. Pertimbangkan semua persyaratan yang relevan saat membuat desain Anda; berikut ini beberapa aspek utama yang perlu diingat saat membuat langkah penting ini:
Desain Rongga Cetakan dan Pemilihan Bahan
Apabila mendesain rongga cetakan, bentuk dan ukurannya harus dipertimbangkan. Selain itu, pastikan bahan yang digunakan memiliki konduktivitas termal yang sangat baik serta ketahanan terhadap keausan.
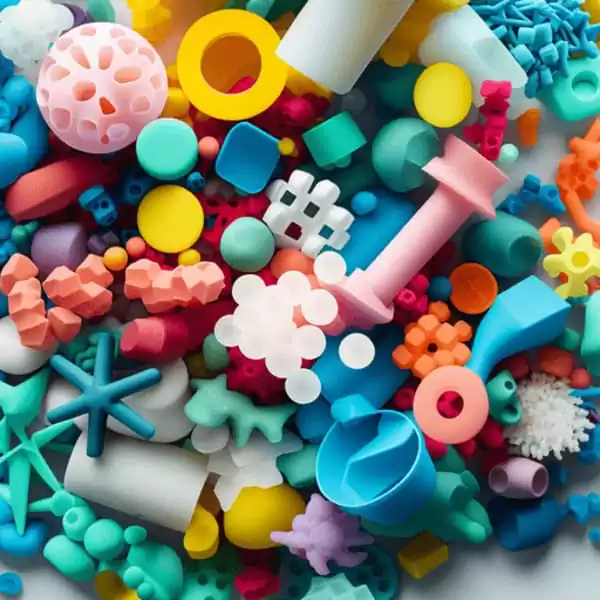
Struktur Internal Cetakan
Struktur internal cetakan, termasuk penempatan dan distribusi ventilasi dan gerbangnya, dapat memengaruhi aliran material selama pencetakan. Pengaturan dan distribusi ventilasi dan gerbang yang tepat membantu menjamin distribusi material yang merata di seluruh rongga.
Suhu dan Tekanan Cetakan
Suhu dan tekanan pencetakan harus dikontrol secara hati-hati, tergantung pada bahan yang dicetak dan kerumitan desain cetakan. Baik suhu maupun tekanan berpengaruh pada sifat mekanis serta akurasi dimensi produk akhir.
Permukaan Akhir dan Stabilitas Dimensi
Untuk mencapai estetika dan persyaratan fungsional yang diinginkan, komponen harus memiliki permukaan akhir yang halus dan mengkilap. Oleh karena itu, sangat penting bahwa cetakan harus dirancang untuk menghasilkan permukaan akhir yang diinginkan. Selain itu, stabilitas cetakan juga harus dipastikan; setiap perubahan dimensi selama pencetakan harus diminimalkan.
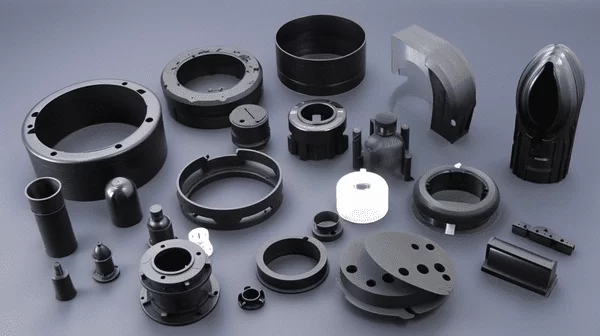
Tegangan Sisa pada Bagian yang Dibentuk
Tegangan sisa dapat berkembang pada bagian cetakan karena pendinginan dan pengawetan selama proses produksi. Oleh karena itu, desain cetakan harus dioptimalkan untuk meminimalkan tekanan ini, yang dapat berdampak negatif pada sifat mekanis dan akurasi dimensi produk akhir.
Pertimbangan yang memadai dari semua variabel ini ketika mendesain kompon cetakan lembaran penuh sangat penting untuk mendapatkan sifat mekanik yang diinginkan, akurasi dimensi, dan permukaan akhir produk akhir.
V. Peran Viskositas Material dalam Cetakan Kompresi
Definisi viskositas material
Viskositas bahan merupakan faktor penting dalam cetakan kompresi proses. Viskositas mengacu pada ketahanan material terhadap aliran dan deformasi di bawah tekanan yang diterapkan, dan dalam pencetakan kompresi, viskositas menentukan perilaku aliran selama pencetakan kompresi.
Bagaimana viskositas material memengaruhi pencetakan kompresi
Viskositas suatu bahan berpengaruh pada seberapa baik bahan tersebut mengisi rongga cetakan dan mendistribusikannya ke seluruh bagian cetakan. Viskositas tinggi membutuhkan tekanan dan suhu yang lebih tinggi untuk aliran yang tepat, sementara viskositas rendah mengalir terlalu bebas, yang menyebabkan flash atau distorsi pada material. Viskositas juga berpengaruh pada sifat mekanik serta akurasi dimensi produk akhir.
Pentingnya memilih viskositas yang tepat untuk bahan yang dicetak
Memilih viskositas yang tepat untuk suatu bahan yang akan dicetak sangat penting untuk mencapai hasil yang diinginkan. Faktor-faktor seperti suhu, tekanan, dan waktu pengawetan semuanya dapat disesuaikan untuk mencapai keseimbangan ini. Mencapai pengisian rongga cetakan yang seragam melalui kontrol viskositas yang tepat memastikan produk akhir yang merata dan berkualitas tinggi.
Terakhir, viskositas material memainkan peran penting dalam cetakan kompresi proses. Dengan mengelola dan mengontrol viskositas material dengan benar, seseorang dapat memastikan hasil yang konsisten dan berkualitas tinggi ketika melakukan pencetakan kompresi.
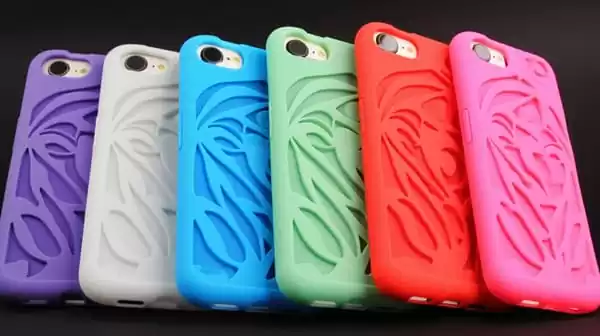
VI. Proses Pencetakan Kompresi
Pencetakan kompresi adalah teknik manufaktur populer yang digunakan untuk menciptakan material komposit berkekuatan tinggi. Ada berbagai proses pencetakan kompresi, seperti pencetakan kompresi basah, pencetakan transfer resin (RTM), dan pencetakan injeksi.
Cetakan kompresi basah
Pencetakan kompresi basah melibatkan peresapan serat penguat dengan resin cair sebelum menempatkannya ke dalam rongga cetakan. Setelah ditutup, tekanan dan panas diterapkan untuk mengawetkan material - metode yang efisien untuk memproduksi komponen komposit berkekuatan tinggi dan berkinerja tinggi.
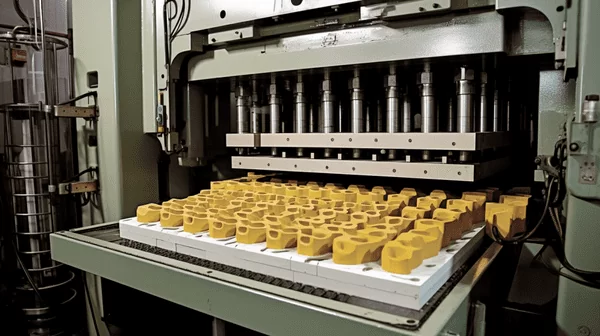
Resin Transfer Molding (RTM)
RTM adalah proses cetakan tertutup yang melibatkan penyuntikan resin cair ke dalam rongga cetakan. Serat penguat ditempatkan di dalam rongga sebelum injeksi resin di bawah tekanan untuk mengisinya dengan resin. Terakhir, panas diterapkan untuk mengawetkan material, membuat RTM populer untuk memproduksi komponen komposit besar dengan bentuk yang rumit.
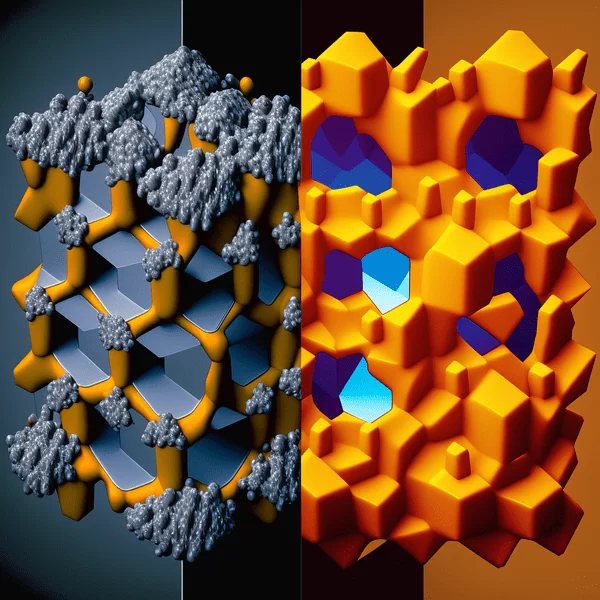
Cetakan Injeksi
Cetakan injeksi melibatkan penyuntikan bahan termoplastik ke dalam rongga cetakan. Setelah dingin dan mengeras, komponen dapat dilepaskan. Metode ini ideal untuk memproduksi komponen berbiaya rendah dalam jumlah besar dengan geometri yang rumit.
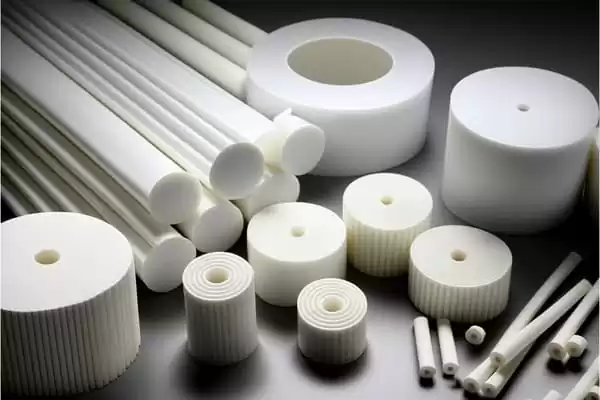
Perbedaan antara pencetakan kompresi dan teknik pencetakan lainnya
Pencetakan kompresi memiliki beberapa kesamaan dengan teknik pencetakan lainnya, seperti pencetakan injeksi. Namun, ada perbedaan utama di antara keduanya. Misalnya, pencetakan kompresi menggunakan tekanan dan suhu yang lebih tinggi yang menghasilkan bahan dengan kekuatan dan kekakuan yang lebih besar. Selain itu, pencetakan kompresi memungkinkan penggunaan serat penguat yang selanjutnya meningkatkan sifat material.
Secara keseluruhan, pencetakan kompresi menawarkan keunggulan yang berbeda dibandingkan proses pencetakan lainnya, sehingga menjadikannya pilihan populer untuk membuat material komposit berkekuatan tinggi.
VII. Sifat Mekanis Bagian Cetakan Kompresi
Komponen cetakan kompresi memiliki sifat mekanis yang diharapkan darinya, karena konstruksinya tidak memerlukan penguatan apa pun.
Komponen yang dicetak dengan kompresi harus memenuhi spesifikasi mekanis tertentu, tergantung pada komposisi material dan penguatan serat yang digunakan.
Komposit polimer sering digunakan dalam cetakan kompresiterdiri dari matriks resin polimer yang diperkuat dengan serat seperti kaca, karbon, atau aramid. Penguatan serat meningkatkan kekuatan dan kekakuan material, sehingga ideal untuk aplikasi yang membutuhkan kinerja mekanis tinggi.
Proses pencetakan kompresi menggunakan berbagai serat penguat, dengan jenis dan jumlah yang memiliki pengaruh penting pada sifat mekanik produk akhir. Serat karbon misalnya dapat menghasilkan bahan dengan kekuatan dan kekakuan yang unggul, sementara serat kaca menawarkan kekakuan yang lebih tinggi tetapi tingkat kekuatan yang lebih rendah.
Selain penguatan serat, polietilena densitas tinggi (HDPE) dalam cetakan kompresi juga dapat meningkatkan sifat termal material. Konduktivitas termal HDPE yang sangat baik membantu membuang panas secara lebih efektif, menghasilkan bahan dengan stabilitas termal yang lebih baik.
Secara keseluruhan, sifat mekanik komponen cetakan kompresi ditentukan oleh beberapa faktor, seperti komposisi material, jenis dan jumlah serat penguat yang digunakan, dan bahan tambahan seperti HDPE. Untuk mencapai performa mekanis yang diinginkan dari faktor-faktor ini, diperlukan pemilihan yang cermat.
VIII. Aplikasi Cetakan Kompresi
Cetakan kompresi adalah alat yang sangat baik untuk menciptakan berbagai produk dengan memberikan tekanan pada produk tersebut.
Pencetakan kompresi adalah proses manufaktur yang inovatif dengan banyak kegunaan dalam berbagai industri dan aplikasi. Contoh umum pencetakan kompresi meliputi:
Industri Otomotif
Compression moulding banyak digunakan dalam industri otomotif untuk membuat komponen mesin dan geometri kompleks lainnya. Karena kekuatan dan kekakuannya yang tinggi, material yang diproduksi melalui cetakan kompresi membuatnya ideal untuk aplikasi yang mengutamakan performa dan daya tahan.
Aplikasi Kedirgantaraan
Pencetakan kompresi sering digunakan dalam industri kedirgantaraan untuk membuat komponen komposit berkekuatan tinggi dan ringan. Keuntungan biaya dan proses produksi yang cepat yang terkait dengan pencetakan kompresi membuatnya menjadi pilihan yang diinginkan oleh produsen kedirgantaraan.
Industri Medis
Cetakan kompresi banyak digunakan dalam industri medis untuk memproduksi komponen seperti sumbat jarum suntik. Dengan presisi dan akurasi dimensi yang unggul, cetakan kompresi memberikan solusi ideal untuk membuat komponen dengan toleransi yang ketat.
Terakhir, compression moulding adalah proses manufaktur yang banyak digunakan dalam berbagai industri dan aplikasi. Kapasitasnya untuk memproduksi material berkekuatan tinggi dengan geometri yang rumit dan toleransi yang ketat membuatnya ideal untuk industri yang mengutamakan performa dan daya tahan.
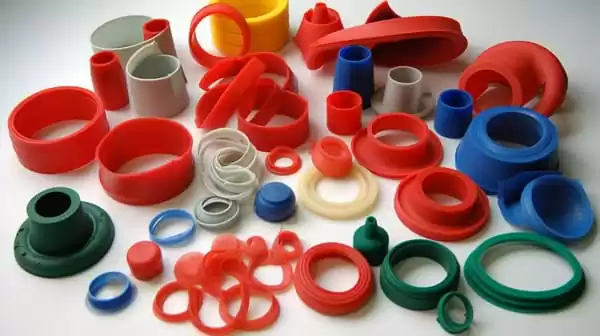
Kesimpulan
Compression moulding adalah proses manufaktur ekstensif yang digunakan di banyak industri dan aplikasi. Proses ini menggunakan tekanan dan suhu tinggi untuk menghasilkan material komposit yang kuat dengan geometri yang kompleks dan toleransi yang ketat.
Viskositas material memainkan peran penting dalam cetakan kompresikarena secara langsung memengaruhi perilaku aliran dan sifat mekanik produk akhir. Untuk mencapai hasil yang konsisten dan berkualitas tinggi, diperlukan kontrol yang tepat atas viskositas material selama pencetakan kompresi.
Perkembangan masa depan dalam pencetakan kompresi akan melibatkan penggunaan material canggih seperti nanokomposit dan material berbasis bio, serta metode manufaktur baru seperti manufaktur aditif. Inovasi-inovasi ini diharapkan dapat meningkatkan kinerja, efisiensi, dan keberlanjutan dalam proses pencetakan kompresi.
Secara keseluruhan, pencetakan kompresi adalah proses manufaktur yang dapat diandalkan dan hemat biaya dengan banyak keuntungan, seperti kekuatan dan kekakuan tinggi, geometri yang kompleks, dan toleransi yang ketat. Dengan memperhitungkan semua faktor yang terlibat dalam pencetakan kompresi dengan benar - termasuk viskositas material - seseorang dapat memastikan hasil yang diinginkan dan memenuhi persyaratan khusus untuk berbagai aplikasi.