1. Karakteristik bahan silikon
A. Bahan baku silikon umumnya berbentuk gel, agak mirip dengan plastisin, tidak berwarna, tembus cahaya, dan tidak berbau.
B. Fitur utamanya adalah tahan suhu tinggi (hingga 300°C) dan tahan suhu rendah (minimum -100°C), yang merupakan karet tahan dingin dan tahan suhu tinggi terbaik saat ini; pada saat yang sama, karet ini memiliki insulasi listrik yang sangat baik dan stabilitas yang tinggi terhadap oksidasi termal dan ozon, secara kimiawi inert.
Kerugiannya adalah kekuatan mekaniknya rendah, ketahanan oli, ketahanan pelarut, dan ketahanan asam dan alkali buruk, sulit untuk divulkanisir, dan harganya lebih mahal. Suhu pengoperasian: -60 ℃ ~ + 200 ℃. Di atas adalah deskripsi dari karet silikon dalam buku panduan.
C. Gunakan suhu: Seperti disebutkan di atas, umumnya ditetapkan ke -40°C hingga 200°C, dan dapat mencapai 230°C dalam waktu singkat.
D. Masalah penuaan: ketahanan terhadap minyak, asam, dan alkali buruk, dan tidak ada hubungannya dengan stres.
E. Masalah adhesi: Sebelum perawatan permukaan, selain menggunakan produk silikon sebagai perekat untuk mengikat dengan bagian silikon, daya rekat ke bagian lain harus diaktifkan di permukaan, dan permukaan lem dapat disembuhkan dengan vulkanisasi.
Semua zat yang dapat bereaksi dengan karet atau membuatnya memiliki ikatan silang secara kolektif disebut sebagai zat vulkanisasi, yang juga dikenal sebagai zat pengikat silang. Ada banyak jenis zat vulkanisasi, dan jumlahnya terus bertambah.
Bahan vulkanisir yang telah digunakan termasuk sulfur, selenium, telurium, senyawa yang mengandung sulfur, oksida logam, peroksida, resin, kuinon, dan amina.
F. Kekerasan material: Menurut kekerasan Shore, komponen plastik secara teoretis dapat dipilih antara 10 derajat dan 80 derajat di pasar domestik.
Yang dapat dengan mudah ditemukan pada umumnya adalah 20 hingga 70 derajat, dan yang paling umum digunakan adalah 40 hingga 50 derajat.
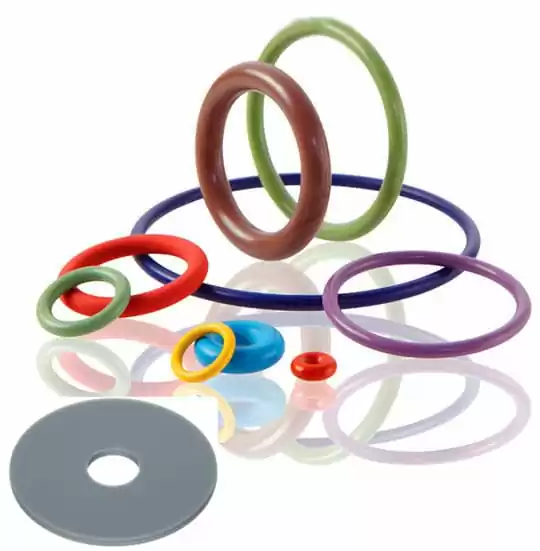
2. Proses produksi produk silikon
J: Bentuk dan warna bahan baku
B: Setelah pencocokan warna dan adonan, serpihan berbagai warna diubah dari gel silika putih susu
C: Setelah diuleni dan dibentuk, bahan mentah ditekan menjadi potongan-potongan dan dipotong-potong
D: Cetakan vulkanisasi
E: Pemangkasan, penghilangan tepi, inspeksi, pengemasan
F: Selesai produk silikon
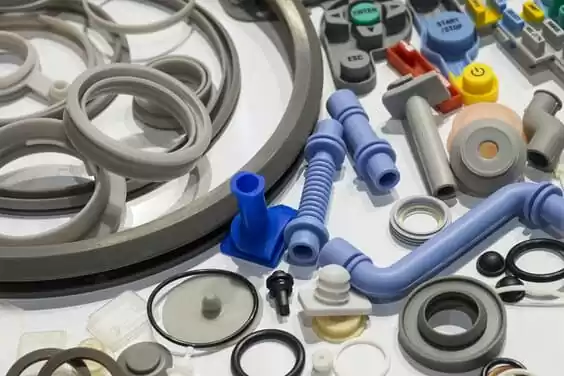
3. Ukuran dan karakteristik produk
A. Batasi ukuran: Bagian yang paling tebal bisa 15 ~ 20 MM, jika berbentuk bola, diameternya bisa 30 MM. Umumnya, ketebalan yang disarankan tidak lebih dari 3 MM.
Jika lebih besar dari 3 MM, maka akan membutuhkan lebih banyak waktu vulkanisasi dan meningkatkan biaya. Bagian tertipis secara teoritis dapat mencapai 0,2 MM, tetapi 0,3 MM tertipis umumnya diambil dalam desain, dan 0,4 MM direkomendasikan.
B. Ukuran relatif: Dalam hal perbedaan ketebalan, direkomendasikan bahwa bagian yang paling tipis dan bagian yang paling tebal tidak boleh melebihi 3 kali. Masalah tersebut terutama bergantung pada persyaratan suhu dan tekanan saat material divulkanisir.
C. Tingkat penyusutan: Tingkat penyusutan dari bahan silikon terkait dengan kekerasan material. Sebagian besar bahan sekunder yang disediakan oleh produsen memiliki nilai antara 1,022 dan 1,042.
Untuk bahan dengan derajat 40 hingga 50 derajat, tingkat penyusutan umumnya 1,03. Dibandingkan dengan plastik, produk silikon tidak mengalami cacat permukaan yang tampak jelas akibat penyusutan.
D. Akurasi dimensi: Karena sebagian besar produk karet silikon adalah satu cetakan dengan banyak rongga, jumlah rongga sangat besar dibandingkan dengan produk plastik. Oleh karena itu, tidak senyaman produk plastik dalam hal kontrol ukuran.
Akurasi umum plus atau minus 0,1, dan produk presisi tinggi plus atau minus 0,05. Apabila digunakan untuk mencocokkan lubang bagian plastik dan tombol, jarak bebas minimum adalah 0,1 per sisi, dan nilai yang direkomendasikan adalah 0,2 per sisi.
E. Desain bentuk: Untuk bagian selongsong karet, umumnya cukup memberikan gambar asli ke pabrik cetakan sesuai dengan gambar bentuk produk, dan menjelaskan masalah pencocokan, yang diputuskan oleh pabrik cetakan.
Dalam keadaan normal, tergantung pada ukuran produk, koordinasi antara selongsong karet dan produk umumnya memiliki deviasi negatif 0,2 ~ 0,5 kecil di satu sisi.
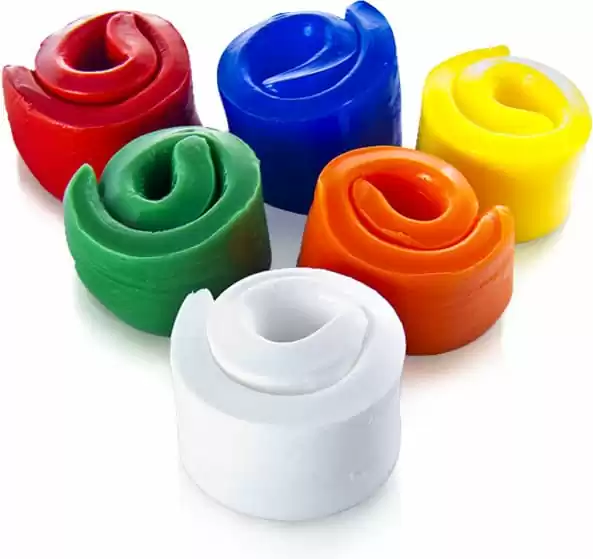
4. Struktur cetakan
A. Batas atas ketebalan cetakan:
Untuk sementara 250mm, ukurannya bisa mencapai 500X500, dan produk bisa mencapai 400X400 di area cetakan. Struktur cetakan umumnya dibagi menjadi cetakan atas, cetakan bawah, pelat bawah, pelat atas, pin ejektor, inti cetakan, engsel, dan bagian tambahan lainnya. Saat mendesain produk silikonharus memperhatikan karakteristik cetakan dan proses produksinya:
B. Demoulding:
Pelepasan produk silikon dapat dilakukan secara langsung dan paksa. Untuk produk tanpa cacat desain, persyaratan ukuran untuk pelepasan paksa terutama terletak pada rasio keliling bagian terbesar dari inti cetakan dengan bagian penutup terkecil selama demolding. Untuk produk di bawah 55°, dapat dilakukan 2-3 kali. Mungkin ada celah dan sudut tajam pada bukaannya.
Karena suhu 180 derajat Celcius diperlukan selama vulkanisasi, maka, pekerjaan demoulding hampir semuanya dilakukan secara manual, kecuali untuk pemisahan bagian atas dan bawah cetakan itu sendiri. Oleh karena itu, kenyamanan dan kecepatan pelepasan harus dipertimbangkan dalam desain komponen.
Agar tidak mempengaruhi kualitas vulkanisasi dan efisiensi produksi massal suku cadang karena waktu demoulding yang lama. Karena metode pelepasan silikon terutama manual, dan langkah aksi pelat atas juga kecil, cetakan silikon tidak memiliki bagian atas yang miring dibandingkan dengan cetakan plastik. Umumnya, tidak ada tarikan inti yang disediakan.
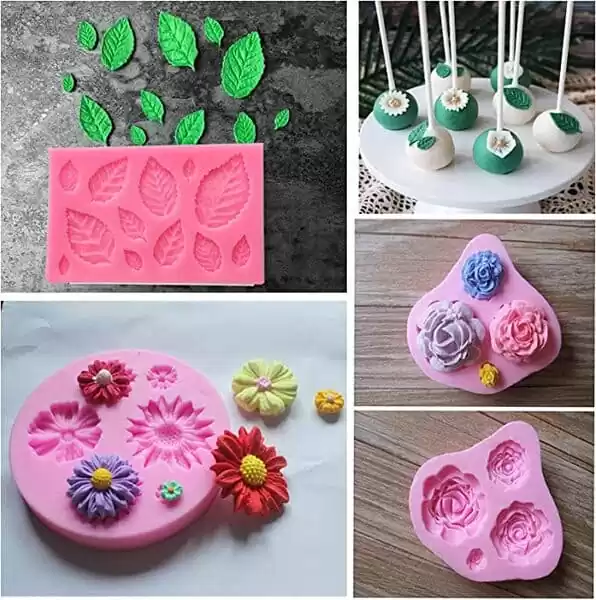
C. Memperbaiki inti:
Tidak seperti cetakan plastik, inti cetakan silikon umumnya dilepas bersama dengan bagian produk saat cetakan injeksi dibuka dan bagian-bagiannya dikeluarkan. Oleh karena itu, fiksasi dan pemosisian yang akurat dari inti cetakan lebih sulit ditangani daripada cetakan plastik, dan kekakuan inti cetakan lebih tinggi.
Inti umumnya dibuat bersama-sama dan semua inti dipasang sekaligus. Atau melewatkan inti cetakan melalui alat bantu agar dapat diposisikan dengan cepat. Karena ada banyak tekanan dalam proses penjepitan cetakan, maka perlu untuk secara ketat mencegah inti cetakan bergerak.
D. Penarikan inti:
Pada umumnya, ini tidak dapat dipindahkan secara otomatis, tetapi dapat dipaksa, dan penarikan inti hanya digunakan untuk struktur berukuran kecil. Pengaturan penarikan inti mirip dengan pengaturan cetakan plastiktetapi dilepas secara manual ketika cetakan dibuka.
Selain itu, penarikan inti menempati ruang yang besar dalam cetakan, yang tidak hanya rumit untuk diproses secara berlebihan cetakan silikon dalam satu cetakan tetapi juga memiliki pemanfaatan ruang cetakan yang rendah. Jadi sebisa mungkin jangan menarik inti sebanyak mungkin.
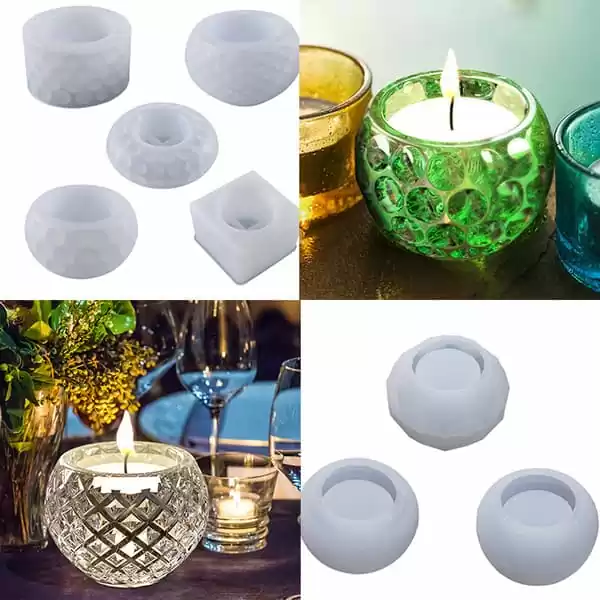
E. Bentuk:
Produk silikon memiliki ketangguhan yang luar biasa ketika permukaannya utuh, tetapi begitu ada retakan, retakan akan meluas dengan cepat di bawah pengaruh kekuatan eksternal. Dengan kata lain, produk silikon sangat sensitif terhadap retakan.
Dengan mempertimbangkan masalah ini, perhatian harus dicurahkan ke desain cetakan komponen silikon yang benar: tidak boleh ada sudut yang tajam pada semua posisi, untuk menghindari konsentrasi tegangan dan keretakan. Sudut R pada bukaan tidak boleh kurang dari 0,5.
F. Tepi yang dapat dilepas sendiri:
Fungsi utama tepi yang dapat dilepas sendiri: adalah untuk menampung karet berlebih; memfasilitasi pembuangan cetakan; mudah untuk memangkas lampu kilat.
Tepi yang dapat dilepas sendiri umumnya terdiri dari tepi tipis pada permukaan perpisahan bagian dan tepi sobek yang relatif kuat. Ketebalan tepi tipis umumnya 0,1 ~ 0,2, ketebalan tepi sobek umumnya 0,8, dan lebar umumnya 1 ~ 2 MM.
G. Masukkan:
Berbagai jenis sisipan dapat ditempatkan pada produk silikon, tetapi beberapa masalah harus diperhatikan, Pertama, permukaan bagian yang disematkan harus diolah terlebih dahulu, terutama vulkanisasi permukaan atau aktivasi permukaan.
Kalau tidak, akan sulit untuk menyambungkan sisipan dan lem secara kuat. Yang kedua adalah pemosisian tetap sisipan, yang dapat ditetapkan pada satu arah pada arah vertikal, tetapi harus ditetapkan sepenuhnya pada arah lainnya. Untuk menghindari pergerakan sisipan selama proses cetakan penuh.
Yang ketiga adalah ketebalan lem di sekeliling sisipan. Untuk komponen yang dienkapsulasi sepenuhnya (di mana semua permukaan dienkapsulasi, sehingga sisipan tidak dapat diposisikan), ketebalan minimum 0,5mm harus digunakan di sekeliling sisipan. Untuk sisipan dengan pemosisian, ketebalan lapisan perekat periferal harus di atas 0,4 MM.
H. Proses tambahan lainnya:
Proses injeksi lem (perekatan):
Mirip dengan cetakan injeksi Dalam proses ini, bagian yang akan diinjeksikan diperbaiki terlebih dahulu, dan lapisan cetakan pertama ditutup untuk mengontrol agar bahan baku tidak mencemari bagian yang tidak dirancang untuk injeksi selama injeksi. Kemudian lapisan kedua cetakan ditutup, dan senyawa karet ditekan ke dalam bentuk.
Proses penggulungan: bentuk karet secara langsung dengan tangan pertama
Cetakan: Proses manufaktur ini dapat digunakan dalam kasus enkapsulasi penuh.
Mencelupkan: Bahan baku bodi karet (karet) adalah cairan, dan benda kerja dicelupkan ke dalam bahan baku berkali-kali. Lapisan dalam bahan baku divulkanisir dan kemudian dicelupkan lagi sampai ketebalan desain tercapai.
Epoxy: Bahan bakunya memiliki fluiditas yang bagus, mirip dengan cat, dan divulkanisir pada suhu kamar. Cetakan adalah operasi yang relatif sederhana, umumnya manual, dan pelapisan berikutnya diterapkan ketika lapisan pertama cepat sembuh.
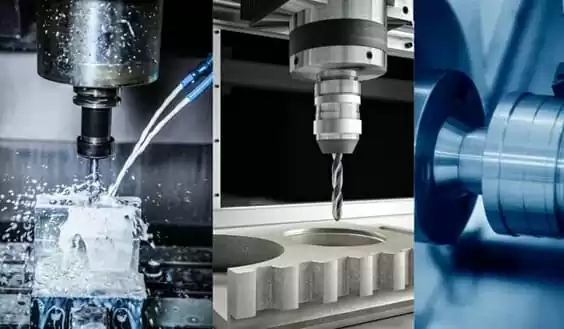
L. Produk multi-warna:
A dibagi menjadi 2 set cetakan vulkanisasi, dan B diwarnai dengan tangan, setelah divulkanisir, bagian pemisah warna dari bagian-bagian tersebut harus memiliki ketinggian tertentu, untuk menghindari kombinasi pencampuran warna perekat konduktif, silikon vulkanisasi sekunder dan silikon (karet) dapat langsung divulkanisir tanpa perawatan Pengikatan 5. Pengukuran dan alat kekerasan.
Instrumen yang paling umum digunakan untuk mengukur kekerasan karet disebut durometer Shore (juga dikenal sebagai Shore). Gunakan pegas untuk menekan indentor logam ke permukaan material dan ukur seberapa dalam penetrasi.
Instrumen ini mengukur kedalaman penetrasi dari nol hingga 0,100 inci. Angka nol pada skala berarti indentor telah menembus batas kedalaman, sedangkan angka 100 berarti kedalaman penetrasi nol. Ada berbagai penguji kekerasan pantai dengan rentang kekerasan dan tingkat otomatisasi yang berbeda.
Salah satu timbangan yang paling umum digunakan adalah timbangan Shore A. Durometer Shore A memiliki indentor tumpul dan pegas sedang. Ketika pembacaan di atas 90, durometer Shore A menjadi tidak akurat. Untuk material yang lebih keras, durometer Shore D digunakan. Durometer ini memiliki indentor yang tajam dan pegas yang kuat untuk penetrasi yang dalam.
Saat mengukur plastik yang lebih keras, gunakan durometer dengan indentor yang lebih tajam dan lebih tangguh, seperti durometer Rockwell. Di sisi yang berlawanan, durometer Shore 00 digunakan untuk mengukur gel lembut dan karet busa.

Sebagian besar bahan dapat menahan tekanan awal, tetapi seiring waktu akan menyerah karena mulur dan relaksasi. Pembacaan durometer dapat dilakukan seketika atau setelah waktu tunda tertentu, biasanya 5 hingga 10 detik. Pembacaan langsung akan selalu menunjukkan pembacaan yang lebih tinggi (atau lebih keras) daripada pembacaan yang tertunda.
Pembacaan penundaan lebih mewakili, tidak hanya kekerasan bahan tetapi juga elastisitasnya. Bahan yang lebih lemah dan kurang elastis lebih mudah mulur daripada bahan yang lebih kuat dan lebih elastis.
Untuk memastikan validitas data, diperlukan prosedur pengujian yang tepat. Untuk mendapatkan pembacaan yang akurat, Anda harus memiliki benda uji yang rata dan cukup tebal sehingga indentor tidak terpengaruh oleh permukaan penyangga.
Biasanya ketebalan yang diperlukan adalah 0,200 inci, tetapi bahan yang kaku dengan deformasi yang lebih sedikit dapat diuji secara akurat apabila terdapat ketebalan yang lebih tipis.