Introduzione
La progettazione degli stampi svolge un ruolo fondamentale nella produzione di prodotti in gomma siliconica di alta qualità. Gli stampi utilizzati per modellare e formare la gomma siliconica hanno un impatto diretto sulla qualità finale, sulla funzionalità e sull'efficienza; l'ottimizzazione del design degli stampi è diventata sempre più cruciale, dato che i prodotti in gomma siliconica continuano a guadagnare popolarità in numerosi settori.
Prodotti in gomma siliconica sono molto ricercati grazie alle loro notevoli proprietà, come la resistenza al calore, la flessibilità e la durata. La gomma siliconica ha trovato applicazione in numerosi settori, come l'automotive, l'elettronica, i dispositivi medici e la produzione di beni di consumo: la sua versatilità e affidabilità la rendono il materiale preferito dai produttori che desiderano sviluppare prodotti innovativi e ad alte prestazioni.
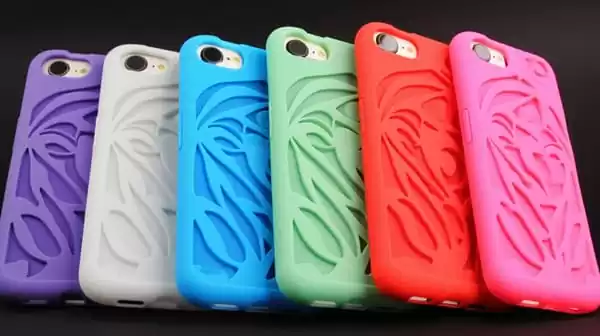
La progettazione di stampi ottimizzati può aiutare i produttori a sfruttare appieno il potenziale della gomma siliconica e a soddisfare la crescente domanda di prodotti di qualità da parte dei consumatori, in quanto garantisce un flusso di materiale efficiente, riduce i difetti e assicura una qualità costante dei pezzi. L'ottimizzazione della progettazione degli stampi non solo garantisce una maggiore produttività, ma contribuisce anche al successo e alla competitività sul mercato.
II. Conoscere i processi di stampaggio della gomma siliconica liquida (LSR)
A. Definizione di stampaggio LSR come processo di stampaggio a iniezione per prodotti in gomma siliconica
Lo stampaggio LSR (o stampaggio di gomma siliconica liquida) è una tecnica di processo di stampaggio a iniezione di liquidi utilizzata per produrre prodotti in gomma siliconica. La tecnica prevede l'iniezione di gomma siliconica liquida ad alta pressione e temperatura nelle cavità dello stampo, per ottenere la forma e le proprietà desiderate. Lo stampaggio LSR offre diversi vantaggi rispetto allo stampaggio a iniezione tradizionale, come l'elevata precisione, l'eccellente qualità dei pezzi e la capacità di produrre geometrie complesse.
L'inizio del processo prevede la creazione di materiale liquido in gomma siliconica, tipicamente costituito da due componenti - polimero siliconico di base e catalizzatore/reticolante - miscelati in proporzioni precise per ottenere le proprietà del materiale e le caratteristiche di polimerizzazione desiderate.
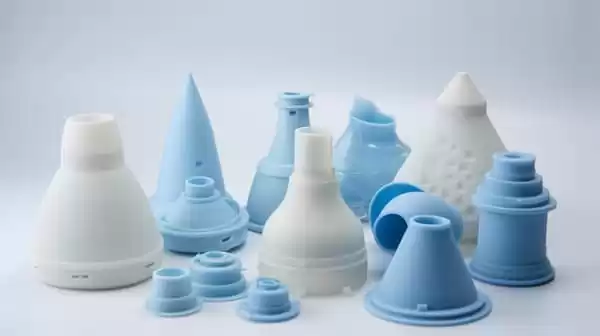
La gomma siliconica liquida viene introdotta in una macchina per lo stampaggio a iniezione, composta da una canna riscaldata, un meccanismo a vite o a stantuffo per l'erogazione del materiale e una cavità dello stampo. Qui il materiale viene riscaldato prima di essere forzato ad alta pressione nella forma e nella cavità dello stampo desiderate.
Una volta che la gomma siliconica liquida è stata iniettata in uno stampo, deve essere sottoposta a un processo di polimerizzazione in cui si può utilizzare il riscaldamento o il raffreddamento per promuovere la corretta polimerizzazione e solidificazione del materiale. Una volta completato, lo stampo può essere aperto e la parte in gomma siliconica solidificata può essere espulsa.
B. Panoramica della macchina per lo stampaggio a iniezione e del suo ruolo nel processo
La macchina per lo stampaggio a iniezione è un componente cruciale del processo di Processo di stampaggio LSR. È composto da diversi elementi chiave che facilitano l'iniezione e la modellazione della gomma siliconica liquida nel prodotto desiderato. Ecco una panoramica dei componenti principali e delle loro funzioni:
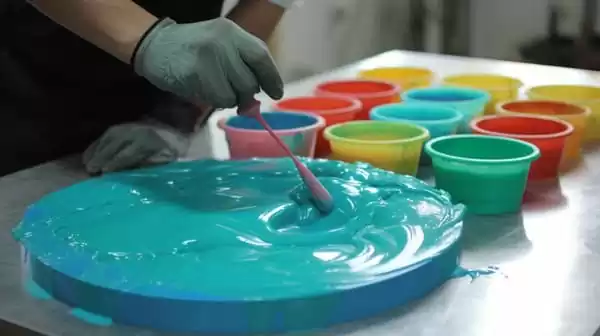
1.Canna e meccanismo a vite/pistone:
Il cilindro contiene il materiale liquido di gomma siliconica e lo riscalda a una temperatura controllata. Il meccanismo a vite o a stantuffo si sposta in avanti per iniettare il materiale nella cavità dello stampo.
2.Stampo Cavità:
La cavità dello stampo è lo spazio vuoto nello stampo che definisce la forma finale del prodotto in gomma siliconica. È progettata per accogliere la geometria, le caratteristiche e le dimensioni desiderate del pezzo.
3.Sistemi di riscaldamento e raffreddamento:
La macchina per lo stampaggio a iniezione comprende sistemi di riscaldamento e raffreddamento che regolano la temperatura dello stampo. Il riscaldamento è necessario per facilitare il flusso del materiale e la polimerizzazione, mentre il raffreddamento aiuta a solidificare il pezzo in gomma siliconica per l'espulsione.
4.Unità di serraggio:
L'unità di bloccaggio tiene unite le metà dello stampo durante il processo di iniezione, assicurando il corretto allineamento e prevenendo la fuoriuscita di materiale. Esercita la forza necessaria per mantenere lo stampo chiuso durante l'iniezione e l'apertura per l'espulsione dei pezzi.
La macchina per lo stampaggio a iniezione offre un controllo preciso della velocità di iniezione, della pressione, della temperatura e di altri parametri di processo, assicurando un'elevata uniformità. produzione e prodotti in gomma siliconica di alta qualità.
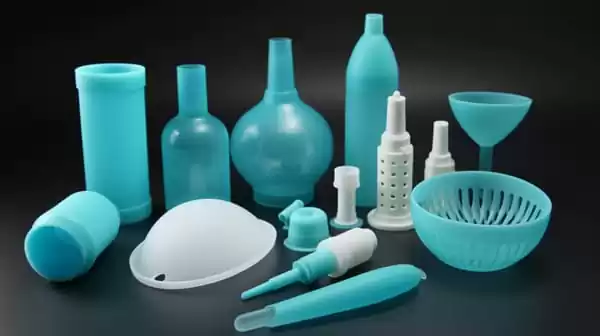
III. Considerazioni chiave per l'ottimizzazione della progettazione degli stampi
A. Importanza della comprensione dei requisiti del prodotto per una progettazione efficace degli stampi
Per ottimizzare la progettazione di stampi per prodotti in gomma siliconica, è fondamentale avere una comprensione completa dei requisiti del prodotto. Ciò include fattori quali le dimensioni, la complessità, la finitura superficiale e gli attributi funzionali. Grazie alla comprensione di questi requisiti, i produttori possono adattare la progettazione dello stampo alle esigenze specifiche, garantendo la produzione di prodotti in gomma siliconica di alta qualità in linea con le aspettative dei clienti.
B. Progettazione per la stampabilità: evitare geometrie complesse, angoli acuti e sottosquadri.
Progettare prodotti in gomma siliconica tenendo conto della stampabilità è essenziale per ottimizzare la progettazione degli stampi. È consigliabile evitare geometrie complesse, angoli acuti e sottosquadri, poiché possono creare problemi durante lo stampaggio e compromettere la qualità dei pezzi. È invece opportuno incorporare curve morbide e angoli di sformo per facilitare lo stampaggio e garantire un flusso corretto del materiale all'interno della cavità dello stampo.
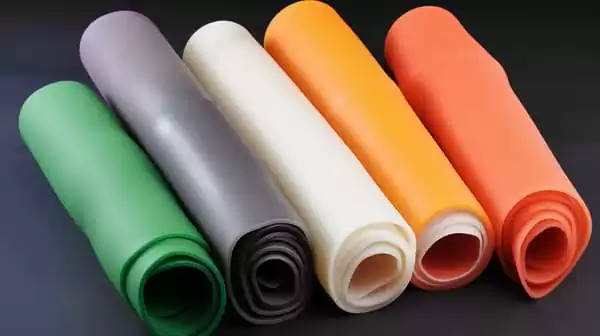
C. Considerazioni sullo spessore della parete e sull'impatto sulla qualità del pezzo e sul flusso del materiale
Il corretto spessore delle pareti è fondamentale per ottenere una progettazione ottimale dello stampo. Il mantenimento di uno spessore di parete appropriato e costante in tutto il prodotto in gomma siliconica garantisce una polimerizzazione uniforme e previene problemi quali le trappole d'aria o le limitazioni del flusso di materiale. Eventuali scostamenti nello spessore delle pareti possono comportare variazioni nella qualità dei pezzi, compresi difetti come deformazioni o segni di affossamento. Un'attenta considerazione dello spessore della parete durante il processo di progettazione è essenziale per ottenere una qualità uniforme del pezzo e un flusso di materiale.
D. Tecniche di ventilazione e degassificazione per un efficiente rilascio di aria e gas durante la polimerizzazione
Uno sfiato e un degasaggio efficaci sono fondamentali per l'ottimizzazione della progettazione degli stampi per i prodotti in gomma siliconica. L'inserimento di sfiati nello stampo consente all'aria o ai gas intrappolati di fuoriuscire durante il processo di polimerizzazione. Una corretta ventilazione impedisce la formazione di difetti come bolle d'aria o vuoti che possono compromettere l'integrità del prodotto. Un'attenta collocazione degli sfiati nelle aree in cui è probabile che l'aria o i gas rimangano intrappolati garantisce un'efficiente evacuazione dell'aria e una polimerizzazione ottimale.
E. Progettazione del sistema di raffreddamento e suo effetto sui tempi di ciclo e sulla stabilità dimensionale
Una progettazione efficiente del sistema di raffreddamento è essenziale per ottimizzare la progettazione dello stampo e ottenere tempi di ciclo più brevi e stabilità dimensionale nella produzione di prodotti in gomma siliconica. Un raffreddamento adeguato aiuta a controllare il processo di polimerizzazione, a ridurre il ritiro dei pezzi e a mantenere la precisione dimensionale. Il posizionamento strategico dei canali di raffreddamento all'interno dello stampo, insieme ai mezzi di raffreddamento appropriati, garantisce un raffreddamento uniforme e un'efficiente dissipazione del calore. Sistemi di raffreddamento ben progettati aumentano la produttività, riducono al minimo i tempi di polimerizzazione e contribuiscono alla qualità costante dei pezzi.
Considerando questi fattori chiave durante il processo di ottimizzazione della progettazione degli stampi, i produttori possono ottenere progetti di stampi ottimali che si traducono in prodotti in gomma siliconica di alta qualità. Queste considerazioni, tra cui i requisiti del prodotto, la stampabilità, lo spessore delle pareti, lo sfiato e il raffreddamento, svolgono un ruolo fondamentale nel migliorare la qualità dei pezzi, l'efficienza produttiva e la soddisfazione dei clienti.
IV. Tecniche avanzate per l'ottimizzazione della progettazione degli stampi
A. Lo stampaggio di inserti e i suoi vantaggi per l'incorporazione di componenti o inserti aggiuntivi
Lo stampaggio con inserti è una tecnica avanzata utilizzata per l'ottimizzazione della progettazione di stampi per prodotti in gomma siliconica. Consiste nell'inserire componenti aggiuntivi o inserti nella cavità dello stampo prima di iniettare la gomma siliconica liquida. I vantaggi dello stampaggio con inserti includono:
Maggiore funzionalità dei pezzi: Lo stampaggio a inserto consente di integrare componenti funzionali, come inserti metallici o connettori elettrici, direttamente nel pezzo. prodotto in gomma siliconica. Questo migliora le prestazioni e la funzionalità del prodotto.
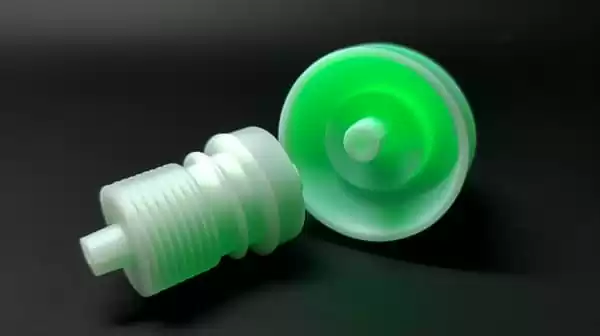
Maggiore resistenza e stabilità del pezzo: Legando saldamente gli inserti alla gomma siliconica, lo stampaggio di inserti migliora l'integrità strutturale e la stabilità del prodotto finale. Elimina la necessità di processi di assemblaggio secondari, riducendo i costi e i potenziali punti di rottura.
Flessibilità di progettazione: Lo stampaggio a inserto offre flessibilità di progettazione, consentendo la creazione di geometrie complesse e di prodotti multimateriale. Consente di combinare materiali diversi con proprietà variabili, ampliando la gamma di applicazioni dei prodotti in gomma siliconica.
B. Utilizzo di strumenti di simulazione e analisi a elementi finiti (FEA) per migliorare l'accuratezza della progettazione
Gli strumenti di simulazione e l'analisi degli elementi finiti (FEA) sono strumenti potenti per l'ottimizzazione della progettazione degli stampi. Aiutano a migliorare l'accuratezza della progettazione, a prevedere il flusso di materiale, a identificare potenziali difetti e a ottimizzare i parametri di processo. Utilizzando strumenti di simulazione e FEA, i produttori possono:
Visualizzazione e analisi del modello di riempimento: Gli strumenti di simulazione forniscono una rappresentazione visiva del flusso della gomma siliconica liquida all'interno della cavità dello stampo. Ciò consente di identificare potenziali problemi legati al flusso, come trappole d'aria, riempimento inadeguato o eccessivo taglio del materiale.
Ottimizzare le posizioni e le dimensioni dei gate: Gli strumenti di simulazione aiutano a determinare le posizioni e le dimensioni ottimali delle porte per i punti di iniezione. In questo modo si garantisce il corretto flusso del materiale, si riducono al minimo i difetti legati al flusso e si migliora la qualità dei pezzi.
Prevedere il ritiro e la deformazione dei pezzi: La FEA è in grado di prevedere il ritiro e la deformazione dei pezzi, consentendo di apportare modifiche alla progettazione per ridurre al minimo questi problemi. Assicura l'accuratezza dimensionale e riduce la probabilità di distorsioni post-stampaggio.
C. Considerazioni su sottosquadri, linee di troncatura e superfici di troncatura
Quando si ottimizza la progettazione degli stampi per i prodotti in gomma siliconica, è essenziale tenere conto delle considerazioni relative a sottosquadri, linee di separazione e superfici di separazione. Questi fattori includono:
- Sottotagli: I sottosquadri sono caratteristiche o rientranze nella geometria del prodotto che rendono difficile la rimozione dei pezzi. È possibile utilizzare tecniche innovative di progettazione degli stampi, come anime collassabili o guide meccaniche, per adattarsi ai sottosquadri e consentire uno stampaggio efficace.
- Linee di separazione: Le linee di separazione sono le aree in cui le metà dello stampo si incontrano, dando luogo a una linea visibile sul prodotto finito. È necessario prestare molta attenzione al posizionamento delle linee di divisione per ridurre al minimo il loro impatto sull'aspetto estetico e sulla funzionalità del prodotto.
- Superfici di separazione: Le superfici di separazione si riferiscono alle superfici dello stampo che separano le metà dello stampo. Garantire superfici di separazione lisce e precise aiuta a ottenere un allineamento corretto e previene la formazione di bolle durante il processo di stampaggio del silicone.
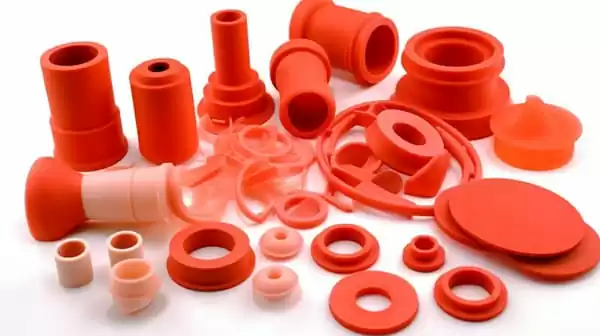
D. Ottimizzazione della temperatura dello stampo, della pressione di iniezione e della pressione della cavità per una qualità costante
L'ottimizzazione della temperatura dello stampo, della pressione di iniezione e della pressione della cavità è fondamentale per ottenere una qualità costante nei prodotti in gomma siliconica. Le considerazioni principali includono:
- Temperatura dello stampo: Il corretto controllo della temperatura dello stampo influenza il flusso del materiale, il tempo di polimerizzazione e la stabilità dimensionale. L'ottimizzazione della temperatura dello stampo garantisce una qualità costante dei pezzi e riduce al minimo le variazioni delle proprietà meccaniche.
- Pressione di iniezione: la pressione di iniezione influisce sul flusso del materiale, sul comportamento di riempimento e sulla riproduzione delle caratteristiche dello stampo. L'ottimizzazione della pressione di iniezione consente il riempimento completo della cavità dello stampo senza sollecitazioni eccessive sullo stampo o sul pezzo.
- Pressione della cavità: il monitoraggio della pressione della cavità durante il processo di stampaggio contribuisce a garantire la qualità costante del pezzo e la precisione dimensionale. Consente di regolare in tempo reale i parametri di iniezione, ottimizzando il processo di produzione.
Implementando queste tecniche avanzate nell'ottimizzazione della progettazione degli stampi, i produttori possono migliorare la funzionalità, la qualità e l'efficienza dei prodotti in gomma siliconica. Inserire
V. Vantaggi dello stampaggio LSR per i prodotti in gomma siliconica
A. Vantaggi dei materiali LSR, tra cui un'ampia gamma di proprietà meccaniche
Lo stampaggio LSR offre diversi vantaggi per i prodotti in gomma siliconica, soprattutto grazie alle proprietà uniche dei materiali in gomma siliconica liquida. Questi vantaggi includono:
- Ampia gamma di proprietà meccaniche: I materiali LSR possono essere formulati in modo da presentare un'ampia gamma di proprietà meccaniche, compresi vari livelli di durezza, flessibilità ed elasticità. Ciò consente ai produttori di personalizzare il materiale per soddisfare i requisiti specifici dei prodotti in diversi settori.
- Resistenza al calore e durata: I materiali LSR offrono un'eccellente resistenza al calore e durata, rendendoli adatti ad applicazioni che comportano l'esposizione a temperature elevate, ambienti difficili o uso frequente. Possono resistere a temperature estreme senza compromettere la loro integrità.
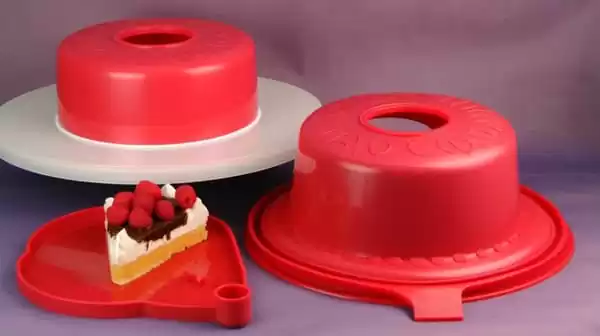
B. Aspetto estetico migliorato e superfici più lisce rispetto allo stampaggio tradizionale
Lo stampaggio LSR offre un aspetto cosmetico superiore e superfici più lisce rispetto ai metodi di stampaggio tradizionali. Ciò è dovuto alle caratteristiche uniche della gomma siliconica liquida, come la bassa viscosità e le proprietà autolivellanti. I vantaggi includono:
- Eliminazione dei difetti superficiali: I materiali LSR scorrono facilmente nella cavità dello stampo, assicurando una distribuzione uniforme e riducendo al minimo la comparsa di difetti superficiali, come segni di affossamento, linee di flusso o imperfezioni della superficie.
- Miglioramento dell'estetica dei pezzi: Lo stampaggio LSR consente di riprodurre dettagli intricati e caratteristiche fini con elevata precisione, ottenendo prodotti visivamente accattivanti. Le superfici lisce ottenute con lo stampaggio LSR contribuiscono all'eccellenza estetica complessiva dei pezzi in gomma siliconica.
C. Capacità di produzione di massa e idoneità a vari settori industriali
Lo stampaggio LSR è molto adatto per lo stampaggio di massa produzione di prodotti in gomma siliconica. I vantaggi includono:
- Tempi di ciclo più brevi: I materiali LSR polimerizzano rapidamente, consentendo tempi di ciclo di stampaggio più brevi rispetto ad altri processi di stampaggio della gomma. Ciò si traduce in una maggiore efficienza produttiva e in una maggiore produzione.
- Coerenza e ripetibilità: Lo stampaggio LSR consente una produzione coerente e ripetibile di prodotti in gomma siliconica, garantendo l'uniformità delle dimensioni, delle proprietà e della qualità dei pezzi. Si tratta di un aspetto cruciale per i settori che richiedono una produzione in grandi volumi con variazioni minime.
- Ampia applicabilità: Lo stampaggio LSR è applicabile in diversi settori, tra cui quello automobilistico, elettronico, sanitario e dei beni di consumo. Si adatta a diversi requisiti di prodotto, che vanno dai componenti medici alle guarnizioni industriali, alle guarnizioni e all'elettronica di consumo.
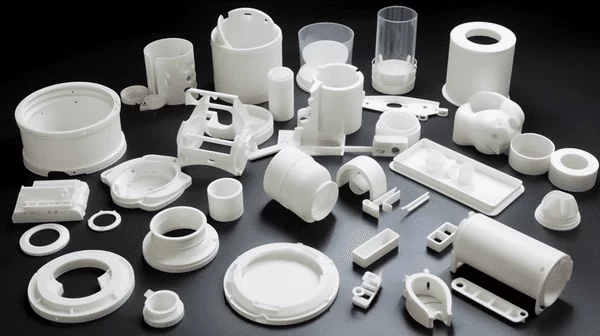
D. Impatto del corretto spessore della parete sull'integrità del pezzo e sui difetti estetici
L'ottimizzazione dello spessore delle pareti nello stampaggio LSR ha un impatto significativo sull'integrità del pezzo e sui difetti estetici. Le considerazioni principali includono:
- Integrità strutturale: Un adeguato spessore delle pareti garantisce l'integrità strutturale e la resistenza dei prodotti in gomma siliconica. Previene problemi quali deformazioni, distorsioni o guasti dovuti a una distribuzione inadeguata del materiale o a una polimerizzazione non uniforme.
- Difetti estetici: Il mantenimento di un corretto spessore delle pareti in tutto il prodotto riduce l'insorgere di difetti estetici, come variazioni superficiali, segni di affossamento o linee di flusso visibili. Uno spessore uniforme delle pareti favorisce una polimerizzazione e un flusso di materiale uniformi, con il risultato di ottenere pezzi esteticamente gradevoli.
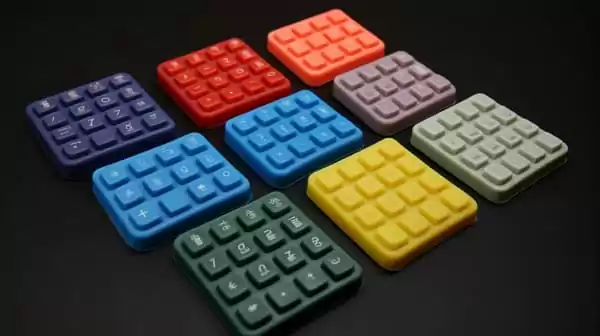
Sfruttando i vantaggi dello stampaggio LSR, i produttori possono produrre prodotti in gomma siliconica con proprietà meccaniche eccezionali, aspetto estetico migliorato e capacità di produzione di massa. La capacità di ottenere uno spessore di parete adeguato garantisce l'integrità del pezzo e riduce al minimo i difetti estetici, contribuendo al successo complessivo e alla competitività dei prodotti in gomma siliconica sul mercato.
Conclusione
In conclusione, l'ottimizzazione del processo di stampaggio a iniezione LSR e della progettazione è fondamentale per ottenere prodotti in gomma siliconica di alta qualità. Implementando strategie e considerazioni chiave, i produttori possono massimizzare il potenziale del processo di stampaggio della gomma siliconica liquida (LSR) e fornire prodotti precisi, durevoli e visivamente accattivanti.
Nel corso dell'articolo, abbiamo discusso l'importanza di comprendere i requisiti del prodotto, di progettare per la stampabilità, di considerare lo spessore delle pareti, di incorporare tecniche di sfiato e degassificazione e di ottimizzare i sistemi di raffreddamento. Questi fattori, tra gli altri, svolgono un ruolo fondamentale nella progettazione di stampi ottimali per la produzione di prodotti in gomma siliconica.
Una progettazione accurata degli stampi è essenziale per garantire una qualità costante dei pezzi, ridurre al minimo i difetti e aumentare la produttività. Considerando attentamente i sottosquadri, le linee di separazione e le superfici di separazione, i produttori possono ottimizzare il progetto dello stampo e ridurre al minimo i difetti estetici.
I vantaggi dello stampaggio LSR, tra cui l'ampia gamma di proprietà meccaniche offerte dai materiali LSR, l'aspetto estetico migliorato e l'idoneità alla produzione di massa, sottolineano ulteriormente l'importanza di ottimizzare la progettazione degli stampi. Lo stampaggio LSR consente di produrre prodotti in gomma siliconica con prestazioni, durata ed estetica eccezionali.
In sintesi, prestando molta attenzione all'ottimizzazione della progettazione dello stampo, i produttori possono sfruttare appieno il potenziale del processo di stampaggio LSR. In questo modo si ottengono prodotti in gomma siliconica di alta qualità che soddisfano le aspettative dei clienti, sono conformi agli standard industriali e ottengono un vantaggio competitivo sul mercato. Con una progettazione meticolosa degli stampi, i produttori possono garantire prodotti in gomma siliconica precisi, durevoli ed esteticamente accattivanti, in grado di soddisfare un'ampia gamma di applicazioni in vari settori.