1. Caratteristiche del materiale siliconico
A. Le materie prime siliconiche sono generalmente gel, in qualche modo simili alla plastilina, incolori, traslucide e inodori.
B. Le sue caratteristiche principali sono la resistenza alle alte temperature (fino a 300°C) e alle basse temperature (minimo -100°C), che rappresenta attualmente la migliore gomma resistente al freddo e alle alte temperature; allo stesso tempo, ha un eccellente isolamento elettrico e un'elevata stabilità all'ossidazione termica e all'ozono, chimicamente inerte.
Lo svantaggio è che la resistenza meccanica è bassa, la resistenza agli oli, ai solventi, agli acidi e agli alcali è scarsa, è difficile da vulcanizzare e il prezzo è più elevato. Temperatura di esercizio: -60℃~+200℃. Quanto sopra è la descrizione di gomma siliconica nel manuale.
C. Temperatura di utilizzo: Come già detto, è generalmente impostata su una temperatura compresa tra -40°C e 200°C, e può raggiungere i 230°C in breve tempo.
D. Problema di invecchiamento: la resistenza all'olio, agli acidi e agli alcali è scarsa e ha poco a che fare con lo stress.
E. Problema di adesione: prima del trattamento della superficie, oltre all'uso di prodotti in silicone Come adesivi per l'incollaggio di parti in silicone, l'adesione ad altre parti deve essere attivata in superficie e la superficie della colla può essere vulcanizzata.
Tutte le sostanze che possono reagire con la gomma o farla reticolare sono chiamate collettivamente agenti vulcanizzanti, noti anche come agenti reticolanti. Esistono molti tipi di agenti vulcanizzanti e sono in continuo aumento.
Gli agenti vulcanizzanti utilizzati includono zolfo, selenio, tellurio, composti contenenti zolfo, ossidi metallici, perossidi, resine, chinoni e ammine.
F. Durezza del materiale: In base alla durezza Shore, le parti in plastica possono teoricamente essere selezionate tra 10 e 80 gradi nel mercato nazionale.
Quelli facilmente reperibili sono in genere da 20 a 70 gradi, mentre quelli più comunemente utilizzati sono da 40 a 50 gradi.
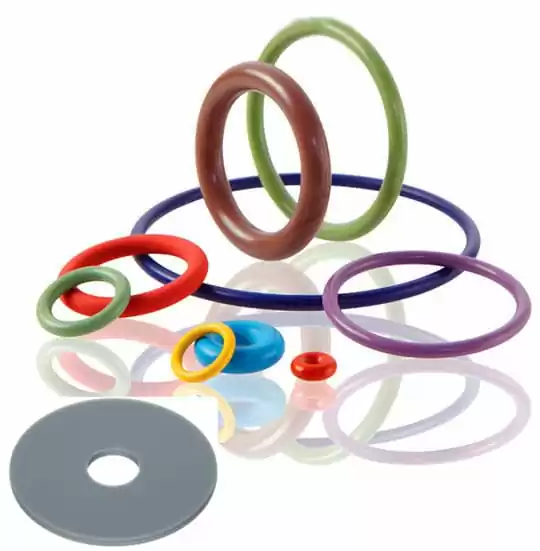
2. Il processo di produzione dei prodotti in silicone
A: Forma e colore delle materie prime
B: Dopo l'abbinamento dei colori e l'impastamento, i fiocchi di vari colori si trasformano in gel di silice bianco latte.
C: Dopo l'impasto e la modellatura, le materie prime vengono pressate in strisce e tagliate in strisce.
D: Stampaggio a vulcanizzazione
E: Rifilatura, rimozione dei bordi, ispezione, imballaggio
F: Finito prodotti in silicone
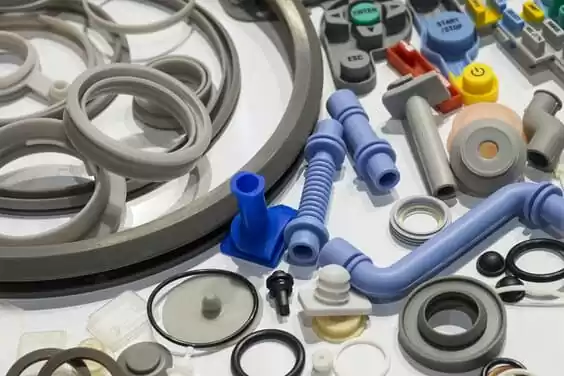
3. Dimensioni e caratteristiche del prodotto
A. Dimensione limite: La parte più spessa può essere di 15~20MM, se si tratta di una sfera, il diametro può essere di 30MM. In generale, lo spessore consigliato non supera i 3MM.
Se è superiore a 3MM, richiederà più tempo di vulcanizzazione e aumenterà il costo. La parte più sottile può teoricamente raggiungere i 0,2MM, ma in genere nella progettazione si adotta lo spessore di 0,3MM e si consiglia di utilizzare 0,4MM.
B. Dimensione relativa: In termini di differenza di spessore, si raccomanda che la parte più sottile e quella più spessa non superino le 3 volte. Tali problemi dipendono principalmente dai requisiti di temperatura e pressione durante la vulcanizzazione del materiale.
C. Tasso di ritiro: Il tasso di ritiro del materiale in silicone è legato alla durezza del materiale. La maggior parte dei materiali secondari forniti dal produttore ha una durezza compresa tra 1,022 e 1,042.
Per i materiali con un grado da 40 a 50 gradi, il tasso di ritiro è generalmente pari a 1,03. Rispetto alla plastica, i prodotti in silicone non presentano gli stessi difetti superficiali apparenti dovuti al ritiro.
D. Precisione dimensionale: poiché la maggior parte dei prodotti in gomma siliconica sono uno stampo con più cavità, il numero di cavità è molto elevato rispetto ai prodotti in plastica. Pertanto, non è conveniente come i prodotti in plastica per quanto riguarda il controllo delle dimensioni.
L'accuratezza generale è di più o meno 0,1, mentre il prodotto ad alta precisione è di più o meno 0,05. Quando viene utilizzato per far combaciare il foro della parte in plastica e il pulsante, il gioco minimo è di 0,1 per lato e il valore consigliato è di 0,2 per lato.
E. Progettazione della forma: Per i manicotti in gomma, in genere è sufficiente fornire il disegno originale alla fabbrica di stampi in base al disegno della forma del prodotto e spiegare il problema della corrispondenza, che viene deciso dalla fabbrica di stampi.
In circostanze normali, a seconda delle dimensioni del prodotto, la coordinazione tra il manicotto di gomma e il prodotto è generalmente una deviazione negativa di 0,2~0,5 piccoli da un lato.
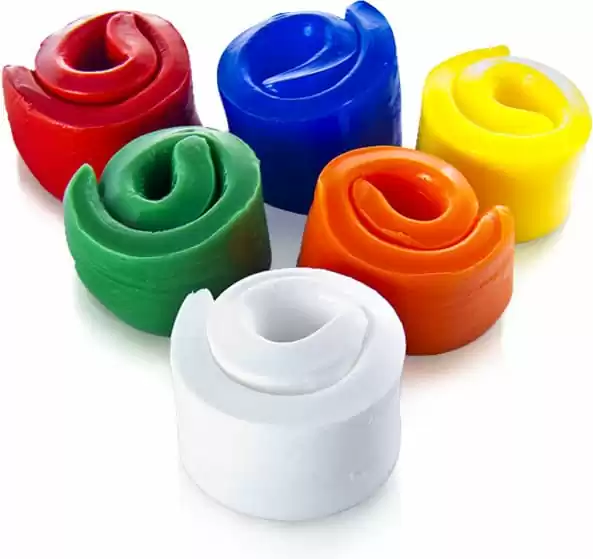
4. Struttura dello stampo
A. Limite superiore dello spessore dello stampo:
Tendenzialmente 250 mm, la dimensione può raggiungere 500X500 e il prodotto può arrivare a 400X400 nell'area dello stampo. La struttura dello stampo è generalmente suddivisa in stampo superiore, stampo inferiore, piastra inferiore, piastra superiore, perno di espulsione, anima dello stampo, cerniera e altre parti ausiliarie. Quando si progetta prodotti in silicone, occorre prestare attenzione alle caratteristiche dei loro stampi e dei processi produttivi:
B. Sformatura:
Il rilascio dei prodotti in silicone può essere diretto e forzato. Per i prodotti senza difetti di progettazione, il requisito dimensionale per il rilascio forzato risiede principalmente nel rapporto tra la circonferenza della parte più grande del nucleo dello stampo e la parte di chiusura più piccola durante lo stampaggio. Per i prodotti al di sotto dei 55°, l'operazione può essere eseguita 2-3 volte. È possibile che si verifichino spaccature e angoli vivi in corrispondenza dell'apertura.
Poiché durante la vulcanizzazione è richiesta una temperatura di 180 gradi Celsius, il lavoro di sformatura è quasi tutto manuale, ad eccezione della separazione superiore e inferiore dello stampo stesso. Pertanto, la praticità e la rapidità della rimozione devono essere considerate nella progettazione dei pezzi.
Per non compromettere la qualità della vulcanizzazione e l'efficienza della produzione di massa dei pezzi a causa dei lunghi tempi di sformatura. Poiché il metodo di rilascio del silicone è principalmente manuale e la corsa d'azione della piastra superiore è anch'essa ridotta, lo stampo in silicone non ha un piano inclinato rispetto a quello della piastra superiore. stampo in plastica. In genere, non è prevista alcuna trazione del nucleo.
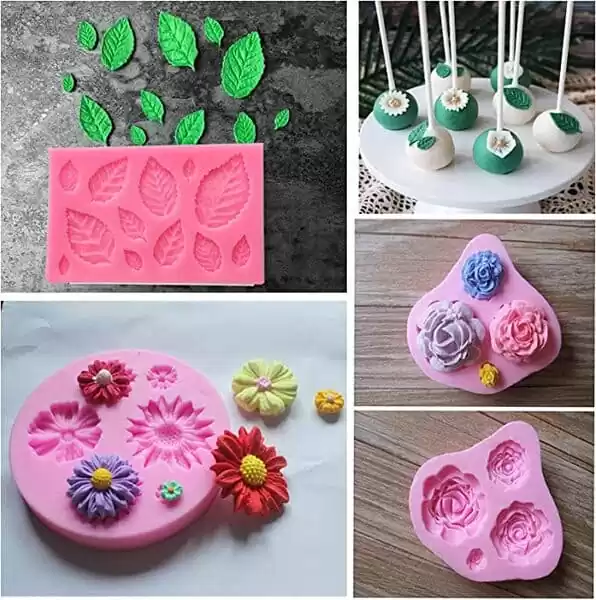
C. Fissaggio del nucleo:
A differenza degli stampi in plastica, le anime degli stampi in silicone vengono generalmente rimosse insieme alle parti del prodotto quando la stampo a iniezione viene aperto e le parti vengono estratte. Pertanto, il fissaggio e il posizionamento preciso del nucleo dello stampo sono più difficili da gestire rispetto allo stampo in plastica e la rigidità del nucleo dello stampo è maggiore.
Le anime sono generalmente realizzate insieme e tutte le anime vengono fissate in una sola volta. Oppure si fa passare l'anima dello stampo attraverso strumenti ausiliari per consentirne il rapido posizionamento. Poiché il processo di bloccaggio dello stampo esercita una forte pressione, è necessario impedire rigorosamente che l'anima dello stampo si muova.
D. Trazione del nucleo:
In genere, non può essere spostato automaticamente, ma può essere forzato e il tiraggio del nucleo è utilizzato solo per strutture di piccole dimensioni. L'impostazione del tiraggio del nucleo è simile a quella della stampo in plasticama viene rimosso manualmente all'apertura dello stampo.
Inoltre, l'estrazione dell'anima occupa un grande spazio nello stampo, che non solo è complicato da lavorare in eccesso. stampo in silicone in uno stampo, ma ha anche un basso utilizzo dello spazio dello stampo. Quindi non tirate il nucleo il più possibile.
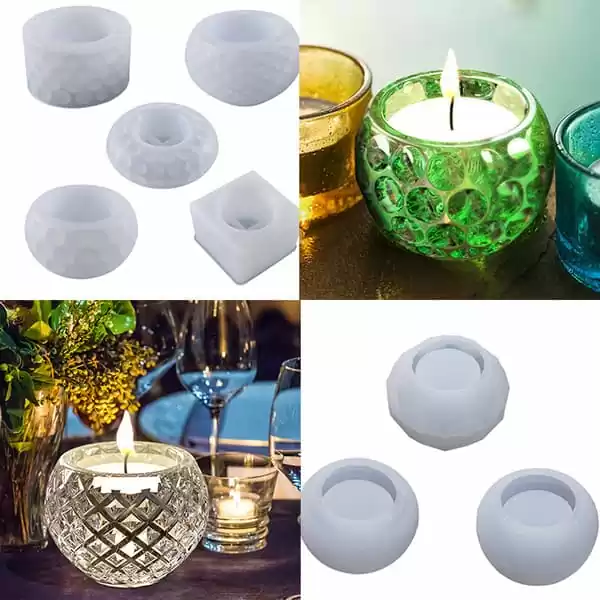
E. Forma:
I prodotti in silicone hanno una grande resistenza quando la superficie è intatta, ma quando si formano delle crepe, queste si espandono rapidamente sotto l'azione di forze esterne. Ciò detto, prodotti in silicone sono molto sensibili alle crepe.
Considerando questi problemi, è necessario prestare attenzione alla corretta progettazione dello stampo delle parti in silicone: non ci devono essere angoli vivi in tutte le posizioni, per evitare la concentrazione di stress e le crepe. L'angolo R in corrispondenza dell'apertura non deve essere inferiore a 0,5.
F. Bordo autosvuotante:
La funzione principale del bordo auto-rimovente: è quella di accogliere la gomma in eccesso; facilitare lo scarico dello stampo; facilitare la rifinitura del flash.
Il bordo auto-rimovente è generalmente composto da un bordo sottile sulla superficie di separazione del pezzo e da un corrispondente bordo a strappo relativamente forte. Lo spessore del bordo sottile è generalmente di 0,1~0,2, lo spessore del bordo di strappo è generalmente di 0,8 e la larghezza è generalmente di 1~2MM.
G. Inserire:
È possibile inserire vari tipi di inserti nei prodotti in silicone, ma è necessario prestare attenzione a diversi aspetti. Innanzitutto, la superficie delle parti incorporate deve essere pretrattata, soprattutto con la vulcanizzazione o l'attivazione della superficie.
In caso contrario, sarà difficile collegare saldamente l'inserto e la colla. Il secondo è il posizionamento fisso dell'inserto, che può essere fissato in una direzione in verticale, ma deve essere completamente fissato nelle altre direzioni. Per evitare il movimento dell'inserto durante il processo di stampaggio completo.
Il terzo è lo spessore della colla intorno all'inserto. Per i pezzi completamente incapsulati (in cui tutte le superfici sono incapsulate, quindi l'inserto non può essere posizionato), è necessario utilizzare uno spessore minimo di 0,5 mm intorno all'inserto. Per gli inserti con posizionamento, lo spessore dello strato adesivo periferico deve essere superiore a 0,4 mm.
H. Altri processi ausiliari:
Processo di iniezione di colla (incollaggio):
Simile al stampaggio a iniezione Nel processo, le parti da iniettare vengono prima fissate e il primo strato dello stampo viene chiuso per controllare che le materie prime non contaminino le parti non destinate all'iniezione durante l'iniezione. Quindi viene chiuso il secondo strato dello stampo e la mescola di gomma viene pressata in forma.
Processo di laminazione: prima mano-preformare la gomma
Stampaggio: Questo processo di produzione può essere utilizzato in caso di incapsulamento completo.
Immersione: La materia prima del corpo in gomma (caucciù) è fluida e il pezzo da lavorare viene immerso più volte nella materia prima. Lo strato interno di materia prima viene vulcanizzato e poi immerso nuovamente fino a raggiungere lo spessore desiderato.
Epossidico: La materia prima ha una buona fluidità, simile alla vernice, e viene vulcanizzata a temperatura ambiente. Lo stampo è un'operazione relativamente semplice, generalmente manuale, e il rivestimento successivo viene applicato quando il primo strato è rapidamente indurito.
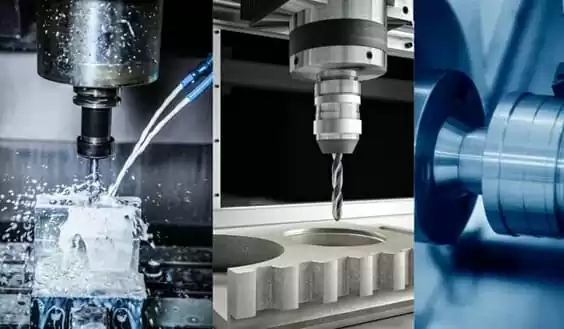
L. Prodotti multicolore:
A è diviso in 2 serie di stampi di vulcanizzazione, e B è colorato a mano, una volta vulcanizzato, la parte di separazione del colore delle parti è necessario avere una certa altezza, per evitare la combinazione di colore miscelazione adesivo conduttivo, silicone vulcanizzazione secondaria e silicone (gomma) possono essere vulcanizzati direttamente senza trattamento Incollaggio 5. Misurazione della durezza e strumenti.
Lo strumento più comunemente usato per misurare la durezza della gomma è il durometro Shore (noto anche come Shore). Utilizzando una molla, si preme un penetratore metallico sulla superficie del materiale e si misura la profondità della penetrazione.
Lo strumento misura le profondità di penetrazione da zero a 0,100 pollici. Una lettura di zero sulla scala significa che il penetratore ha raggiunto la profondità limite, mentre una lettura di 100 significa che la profondità di penetrazione è pari a zero. Esistono vari misuratori di durezza Shore con diversi intervalli di durezza e gradi di automazione.
Una delle scale più comunemente utilizzate è la scala Shore A. I durometri Shore A hanno un penetratore smussato e una molla media. Quando le letture sono superiori a 90, il durometro Shore A diventa impreciso. Per i materiali più duri, si usa un durometro Shore D. Ha un penetratore affilato e una molla forte per una penetrazione profonda.
Per misurare le materie plastiche più dure, utilizzare un durometro con un penetratore più affilato e più resistente, come un durometro Rockwell. All'estremo opposto, i durometri Shore 00 sono utilizzati per misurare gel morbidi e gomme espanse.

La maggior parte dei materiali multipli è in grado di resistere alle sollecitazioni iniziali, ma con il tempo cedono a causa del creep e del rilassamento. Le letture del Durometro possono essere effettuate istantaneamente o dopo un certo tempo di ritardo, di solito da 5 a 10 secondi. Le letture immediate mostreranno sempre valori più alti (o più duri) rispetto alle letture ritardate.
Le letture del ritardo sono più rappresentative non solo della durezza del materiale, ma anche della sua elasticità. Un materiale più debole e meno elastico è più incline allo scorrimento rispetto a quelli più resistenti ed elastici.
Per garantire la validità dei dati, sono necessarie procedure di prova precise. Per ottenere una lettura accurata, è necessario disporre di un pezzo di prova sufficientemente piatto e spesso in modo che il penetratore non venga influenzato dalla superficie di appoggio.
In genere lo spessore richiesto è di 0,200 pollici, ma i materiali rigidi con minore deformazione possono essere testati con precisione in presenza di spessori inferiori.