はじめに
ラバー・カラーリングには、ちょっとした経験と色の構成に関する基本的な知識が必要だ。色は基本的に3原色で構成されている。天然色カードを購入するための特別な標準番号があり、色の組成と比率もありますが、これは一般的な方向性の参考としてしか使えません。なぜなら、カラーマスターバッチは同じではなく、基材も異なり、さらにゴムはまだ加硫する必要があり、高温後に変化するからです。硫黄が添加されている場合、それは黄色っぽくなります。また、促進剤や老化防止剤も異なる色を作り出すのに影響を与えるので、専門的な知識と豊富な経験が必要になります。
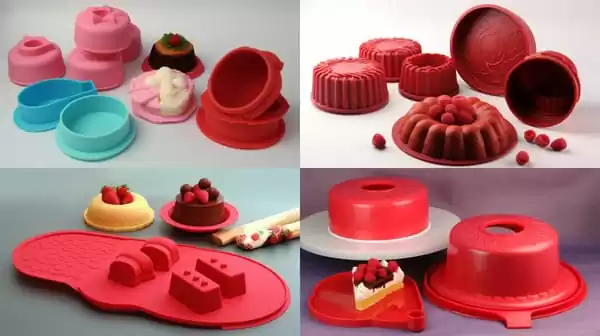
色彩感覚も非常に重要だ。色の調節が早く、感覚が鋭敏な人もいる。もちろん、調整すればするほど、練習すればするほど完璧になる。大まかな方向が見本の色に近く、ゴム素材の組成も同じという製品が簡単に見つかることもある。3回でも5回でも微調整すれば、ちゃんとできるようになる。スイッチしても何も感じないときは本当に困る。
シリコーンゴム製品の一般的な調色方法
ソリューションカラーミキシング
この方法は、溶解することである。 シリコーンゴム その良溶媒で一定濃度の溶液にし、トナーと 液状シリコーンゴム 硫黄以外の配合剤を溶液に入れ、均一に攪拌混合し、一定温度で乾燥して溶剤を除去し、最後に硫黄を加えてゴム練り機を製造する。操作が複雑で、分散にムラがあり、色差があり、溶剤の回収が難しく、環境を汚染するため、ほとんど使用されていない。
カラーミキシング方式
この方法は現在、射出成形で最も一般的に使用されている方法である。 シリコーン製品.それは、トナーを直接添加するか、または最初にキャリアと混合してからゴムコンパウンドに添加し、ゴムミキサーを通して均一に混合してシリコーンゴムに着色することである。具体的な方法は以下の通りである。
ドライパウダー・カラーリング
シリコーンゴムに粉末状のトナーや小粒径の原料を直接加え、オープンミルで混合する。操作が簡単で低コストという利点があるが、混合時に粉塵が発生し、環境を汚染し、均一に分散しにくく、色差がある。また、粒子が硬すぎたり厚すぎたりすると、特注色の斑点や縞模様、クロマトグラムの相互汚染など品質上の問題が生じるため、ほとんど使用されない。
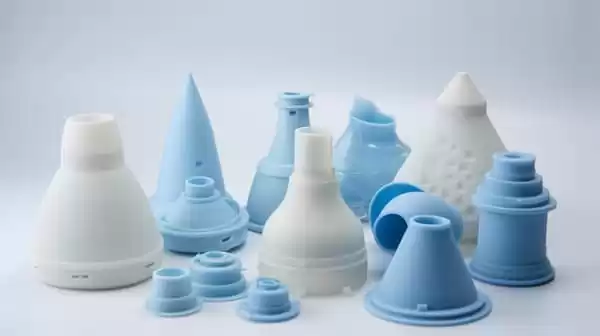
カラーペーストの調色
まず、トナーと液体配合剤(可塑剤など)を混合し、3本ローラー機で粉砕してペースト状またはスラリー状にし、それを シリコーンゴム を一定の割合で混合する。この方法は、粉塵の飛散を避け、トナーがゴム中に分散しやすく、均一な色を得ることができる。しかし、カラーペースト中のトナー含有量が少なく、調色性が高くなく、輸送量が多く、損失が大きく、使用者にとって不便である。
粒状カラーミキシング
トナーペレットの調製には、主に2つの方法がある。第一の方法は、他の粉末状配合剤の造粒方法と同じである。粉末状のトナーをまず界面活性剤で浸漬し、ワックスで溶融するか樹脂で溶融して押し出し造粒する方法、第二の方法は 剤を界面活性剤で浸漬した後、機械的な力でトナー粒子を微細化して一定濃度の分散液を形成し、これをラテックスと混合して共沈させ、乾燥した後、圧延または成型して顆粒にする方法である。
粒状トナーは使いやすく、分散性に優れ、粉塵が飛散せず、環境を汚染せず、色が鮮やかで、発色が均一で、色差がない。色の安定性が期待できる混合方法である。しかし、粒状トナーの調製工程は複雑で、コストが高いため、幅広い応用が制限されている。
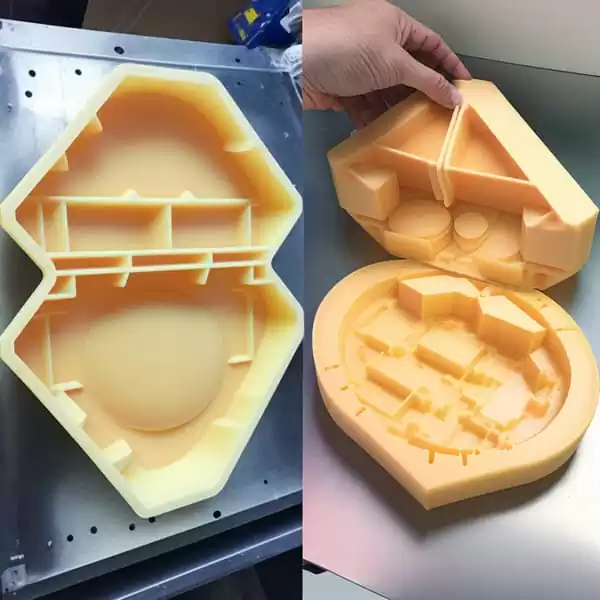
着色シリコーン製品を加工する際の注意点
色のりの組成と材料が基準を満たしているかどうか。
多くの製品に見られる色の違いや、原料に色斑や変色が見られるのは、主に色のりの成分が適切に調製されていないためである!
ミキシング・プロセス
色糊と原料の混合時間が短すぎるため、製品の成分の色にムラが生じ、局所的な色のグラデーションが大きくなる!
製品製造プロセス
原材料の配置によってマテリアルマークが発生する。この現象は、成形ウェルの一部分に製品材料が滞留していることが原因であることが多い。原材料を分散させることができます!
色を混ぜるとき
原材料と色糊の比率は正確ではありません。一般的に色糊と糊の比率は1:10と言われています。そのため、工程管理では、変色を防ぐために、色糊と糊の配合や重量をできるだけ正確に管理する必要がある。変化があります!
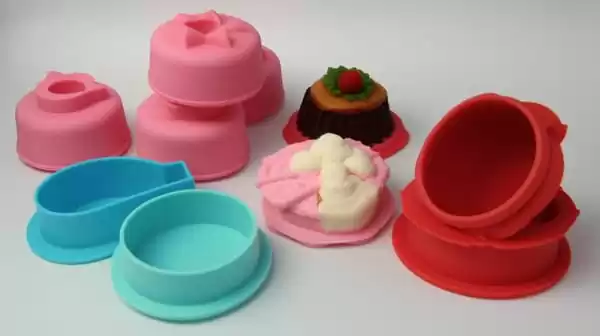
結論
の中で シリコーンゴム 色合わせのプロセスでは、使用する着色顔料はシンプルであればあるほどよい。2色で合わせられる場合、3色を使うのはお勧めできない。顔料を入れすぎると「補色」が起こり、色が濃くなってしまうからだ。特に、色付き風船や家庭用手袋のようなラテックス製の最終製品に使われる着色料は要注意。使わないようにしよう。明るさを失わないための3色同時に、シリコーンゴムのカラーマッチングに使用する顔料を選択する場合、耐熱安定性に大きな差があるため、加硫過程の温度変化による色の変化を避けるために、耐熱特性が似ている品種を選択することに注意する必要があります。また、ラテックス用の着色剤は、耐アルカリ性と分散性を考慮して選定する必要がある。
シリコーンゴムの色合わせは、シリコーンゴム完成品の生産と製造に欠かせないリンクである。高度な技術と経験を要し、長期にわたる練習と蓄積が必要である。使用する顔料、ステイン、調合ステインなど、さまざまな見本のデータベースを作っておくとよい。現在生産されているゴム見本と着色ゴム材料は、将来の比較と使用のため、また同じメーカーと配合の着色ゴム材料の異なるロット間の色の違いを最小限に抑えるために、別々にアーカイブして保管する必要があります。ゴムの調色技術は複雑であるが、真摯で厳格な作業態度を持ち、様々な顔料や着色剤とゴムの性能、用量、相溶性、分散性、環境安全性などを学び、実験を重ねていけば、より多くのゴムの調色技術を総合的に習得することができるだろう。