シリコーンゴムは無臭、無毒で、高温と低温の特性を恐れず、摂氏300度、摂氏マイナス90度でも「穏やか」で、「顔は色を変えない」。
シリコーンゴムはまたよい電気絶縁材、酸素抵抗および老化抵抗、耐光性および老化抵抗、また鋳型の抵抗、化学安定性、等を有する。
高温加硫ジメチルシリコーンゴムの登場以来、シリコーンゴムは急速に発展した、 シリコーンゴム製造 広く使われている。
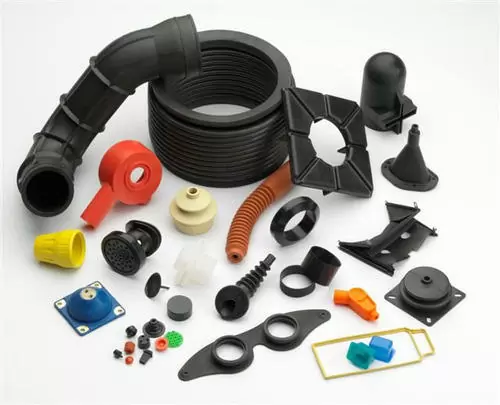
シリコーンゴムの構造特性と優れた性能
1.高い分子結合エネルギー
C-C結合エネルギーは348KJ/mol、Si-O結合エネルギーは444KJ/molと高いが、紫外線(300nm)のエネルギーはわずか400KJ/molである。分子鎖はらせん状で、シリコーンの結合角は大きく(130°~160°)、分子間力は小さい。
2.シリコーンゴムのユニークな特性
耐候性に優れ、UV、O2、O3、塩水噴霧などに耐える。
表面エネルギーが低く、撥水性に優れ、撥水移行性がある。
絶縁性能に優れ、幅広い温度と周波数範囲で安定した誘電特性を示す。非常に優れた耐アーク性と耐リーク性。
耐高温性に優れ、180~200℃での連続使用が可能。常温でのシリコーンゴムの強度は、天然ゴムや一部の合成ゴムの半分程度ですが、200℃以上の高温環境では、シリコーンゴムの強度は、天然ゴムや一部の合成ゴムの半分程度となります、 シリコーンゴム は、ある程度の柔軟性、弾力性、表面硬度を維持することができ、機械的特性に大きな変化はない。
弾性がよく、低温柔軟性があり、-50℃でも使用できる。シリコーンゴムのガラス転移温度は一般的に-70~-50℃であり、特殊配合は-100℃に達することができ、優れた低温性能を示す。これは航空・宇宙産業ラインにとって重要なことである。
難燃性に優れ、燃焼時に有毒ガスや有害ガスがほとんど発生しない。透明な製品にすることができ、気泡や不純物などの欠陥は目視で容易に発見できる。
汎用ゴムに比べ、シリコーンゴムの3大タイプはいずれも相手部品が比較的単純であり、熱加硫タイプも同様である。
原料ゴムのほか、配合剤には主に補強剤、加硫剤、いくつかの特殊添加剤が含まれ、一般的には5~6成分だけで実用的な配合を形成する。
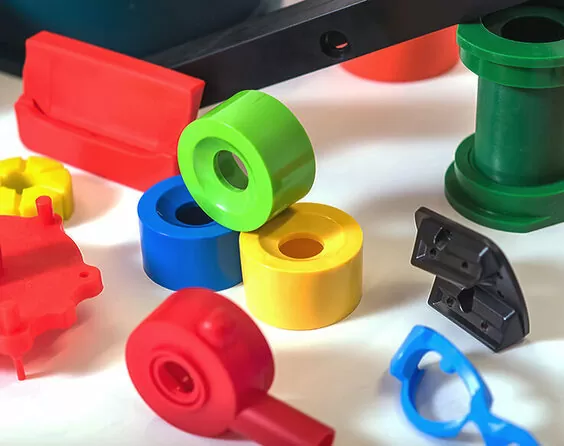
シリコーンゴムの配合設計は、以下の点を考慮する必要がある:
(1)シリコーンゴムは生ゴムの飽和度が高くて、普通は硫黄の黄色の加硫を使うことができなくて、熱い加硫を使います。
熱間加硫は有機過酸化物を加硫剤として使用するため、ゴムに過酸化物の分解生成物と相互作用できる活性物質が含まれていないと、加硫に影響を与えます。
(2) シリコーンゴム製品 は一般に高温で使用されるため、化合物は高温でも安定した状態を保つ必要がある。
(3)シリコーンゴムに微量の酸やアルカリなどの極性化学試薬を加えると、シリコーン結合の切断や転位が起こりやすくなり、シリコーンゴムの耐熱性が低下する。
そのため、加硫ゴムの性能に影響を与えないよう、マッチング剤の選択には酸性度とアルカリ性を考慮する必要があり、過酸化物分解生成物の酸性度も考慮する必要がある。
生ゴムの選択
配合を設計する際には、製品の性能と使用条件に応じて、特性の異なる原料ゴムを選択する必要がある。
一般的に シリコーンゴム製品 製品の使用がより高い温度(-90〜300℃)を必要とする場合、低フェニルシリコーンゴムを使用することができます;製品は、高および低温耐性を必要とし、燃料や溶剤に抵抗する必要がある場合、-70℃〜250℃の範囲の温度の使用を必要とする、ビニルシリコーンゴムを使用することができます。
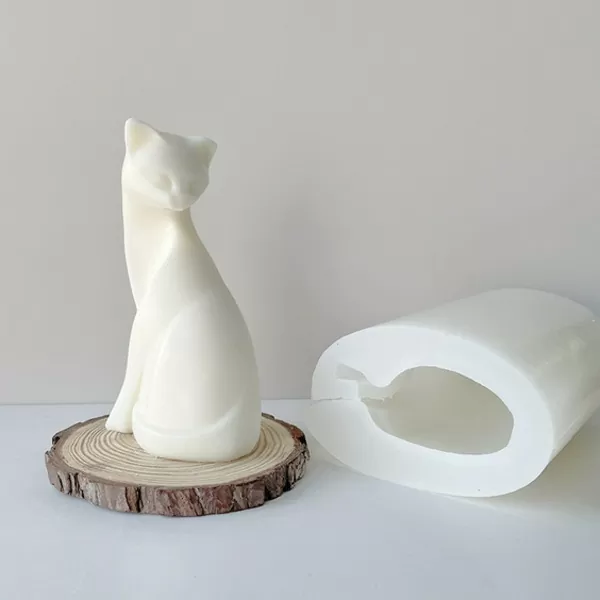
加硫剤
熱間加硫シリコーンゴムに使用される加硫剤は、主に有機過酸化物、脂肪族アゾ化合物、無機化合物、高エネルギー線などであり、中でも最もよく使用されるのは有機過酸化物である。
有機過酸化物は一般に室温では安定だが、加硫温度が高くなると急速に分解してフリーラジカルを生成し、シリコーンゴムを架橋させるからだ。
過酸化物はその活性レベルによって2つのカテゴリーに分けられる。一つは汎用タイプ、すなわちあらゆる種類の加硫が可能な高活性タイプである。 シリコーンゴムもう1つのタイプは、ビニルを含むシリコーンゴムにのみ加硫可能な、ビニルに特化した、すなわち活性の低いものである。
上記の2種類の過酸化物の一般的な違いのほかに、それぞれの過酸化物には特徴がある。加硫剤BPは成形品に最もよく使われる加硫剤で、加硫速度が速く、生産効率が高いが、厚い製品の生産には適さない。
加硫剤DCBPは製品が揮発しにくいので、圧力をかけずに加硫しても気泡が発生し、特に熱風連続加硫のプレス製品に適しているが、分解温度が低く、焦げが発生しやすく、ゴムの貯蔵時間が短い。
加硫剤BPとDCBPは結晶性の粉末で、爆発性があり、安全な操作と分散に適しているため、通常、シリコーンオイルに分散して使用される。 シリコーンゴム 過去、一般的な含有量は50%だった。加硫剤の沸点は110℃で、揮発性が高い。
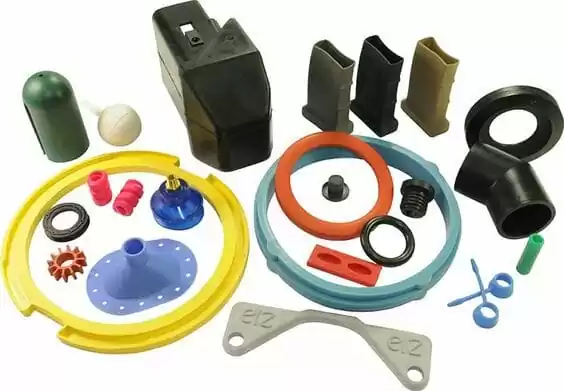
加硫剤はゴムを室温で保存すると蒸発するため、分子ふるいの形で担体として使用するのが最適である。加硫剤DTBPは空気やカーボンブラックと反応しないため、導電性ゴムや成形が難しい製品の製造に使用できる。
加硫剤DBPMHはDTBPと似ているが、室温では揮発せず、分解生成物が揮発するため、第二段階の加硫時間を短縮できる。
加硫剤DCPは常温で揮発せず、ビニル特殊タイプの特性を持ち、分解生成物の揮発性も低く、外圧の小さい加硫に使用できる。加硫剤TBPBはスポンジ製品の製造に使用される。
過酸化物の量は様々な要因に影響される。例えば、原料ゴムの種類、充填剤の種類と量、加工技術などである。一般的には、所望の架橋が達成できる限り、加硫剤はできるだけ少なくてよい。
しかし、実際の配合量は、不均一な混合、ゴムの貯蔵における過酸化物の損失、空気の加硫、その他の配合剤のブロック化など、さまざまな加工要因を考慮しなければならないため、理論配合量よりもはるかに多くなる。
ビニール用 シリコーンゴム成形品 ゴムと、過酸化物の様々な一般的な重量部の範囲は次のとおりです。
コンポーネント重量
チキソトロピー剤 BP 0.5~1
チキソトロピー剤 DCBP 1~2
チキソトロピー剤 DTBP 1~2
チキソトロピー剤 DCP 0.5~1
硫化剤 DBPMH 0.5~1
チキソトロピー剤 TBPB 0.5~1
ビニル含有量の増加に伴い、過酸化物の量を減らすべきである。粘着剤ペーストの粘着剤と接着剤の過酸化物の量は、成形された粘着剤の過酸化物の量よりも高くする必要があります。
場合によっては、2種類の過酸化物を使用することで、加硫剤の量を減らすことができ、加硫温度を適切に下げることができ、加硫効果を向上させることができる。
補強剤
非強化シリコーンゴム加硫ゴムの強度は非常に低く、約0.3MPaしかなく、実用価値がない。適切な補強剤を使用すると、シリコーンゴム加硫ゴムの強度を3.9~9.8MPaにすることができ、シリコーンゴムの性能を向上させ、製品の寿命を延ばすために非常に重要である。
シリコーンゴム補強充填剤の選択は、シリコーンゴムの高温使用と過酸化物による加硫、特に酸性物質とアルカリ性物質がシリコーンゴムに及ぼす悪影響を考慮すべきである。
前者は直径10~50nm、比表面積70~400m²/gで補強効果が高く、後者は300~10000nm、比表面積30m²/g以下で補強効果が劣る。
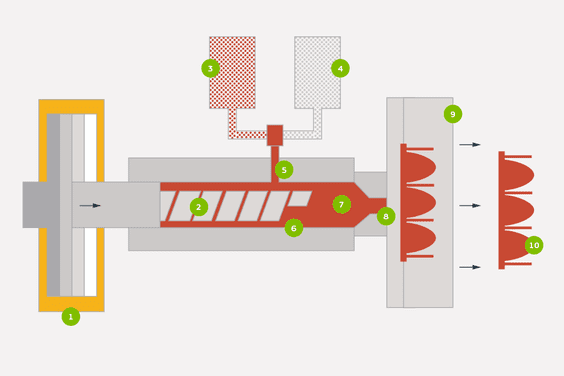
補強用充填材
(1) シリカ、シリコーンゴム補強フィラーの種類と特徴は、主に合成シリカを指し、シリカとも呼ばれる。シリカはヒュームドシリカと沈殿シリカに分けられます。
a.ヒュームドシリカ粒子の大きさ、比表面積、表面性状、構造は、原料ガスの比率、燃焼速度、燃焼室内でのSiO2核の滞留時間などに関係する。
フュームドシリカは粒子が細かいほど比表面積が大きく、補強効果は高いが、操業性は悪くなる。逆に、粒子が粗く比表面積が小さいと、補強効果は劣るが、操作性は良くなる。
フュームドシリカは、以下の補強剤として最も一般的に使用されている。 シリコーンゴムフュームドシリカで補強されたゴムは、加硫ゴムの高い機械的強度と良好な電気的特性を有する。フュームドシリカは、他の補強剤や弱い補強剤と一緒に使用することもでき、ゴムの用途に応じてさまざまな条件を作り出すことができます。
沈殿シリカ
沈殿シリカの性能は、酸性度や温度などの沈殿条件に影響される。
と比べると シリコーンゴムコンパウンド ヒュームドシリカで強化したコンパウンドの機械的強度は若干低く、誘電特性、特に湿った後の誘電特性は劣るが、耐熱老化特性は良く、コンパウンドのコストはずっと低い。製品の機械的強度が高くない場合は、沈殿シリカを使用するか、ヒュームドシリカと併用することができます。
シリカは適切な化合物で処理することで、表面を疎水性物質にすることができる。処理には主に液相と気相の2つの方法がある。
液相法は条件制御が容易で、製品の品質が安定し、処理効果も高いが、工程が複雑で溶媒を回収する必要がある。気相法は簡便だが、製品の品質が十分に安定せず、処理効果も低い。
表面処理剤として使用される物質は、原則として、シリカ表面の水酸基と相互作用できる以下の物質である。
- アルコール類
- クロロシラン
- アルコキシシラン
- ヘキサメチルジシリルエーテル
- シラザン
(2) シリカの補強メカニズム、シリカの表面化学的性質 シリコーンゴム.以下の2種類があると考えられている。
フィラー粒子吸着ポリマーによるゴム吸着は、ゴム分子鎖セグメントがフィラー粒子の近傍に直接固定されるか、フィラー表面に沿って配向するか、フィラー凝集体に保持される。
b.ゴムとフィラー粒子を組み合わせたもの、フィラー粒子とポリマー鎖セグメントを組み合わせたもので、フィラー粒子の効果的な架橋とポリマーの絡み合いを生じさせる。
以上の2つの効果から、シリカにはシリコーンゴムを補強する効果がある。
シリカの酸性とアルカリ性はその製造方法によって異なる。ヒュームドシリカは酸性で、沈殿シリカはアルカリ性です。
最も純粋なHCLを含まないフュームドシリカのpH値は6であり、これは水中でシリカ表面の水酸基が解離してH+を生成するためである。4.6以下のpH値は、高温加水分解によって保持されたHCLによるものである。
(3) シリカの物理的・化学的特性の測定方法
シリカの物理的、化学的特性は品質に直接反映されるため、使用するための様々な要件を正確に測定することが非常に重要です。現在、海外メーカーの指標は同じではありませんが、いくつかの重要な指標は各ファミリーで測定することが認められています。
最も重要な指標は、粒子径や分散度、比表面積などの一次構造を反映する指標、吸油価などの二次構造を反映する指標、表面の各種水酸基濃度などの表面化学を反映する指標などである。
シリカの粒径は均一ではなく、通常の粒径は統計的平均の意味しか持ちません。
比表面積の測定は、粉末材料の外部表面積の大きさを示す指標であり、多孔質粉末材料の場合、その比表面積は表面積と細孔の外部表面積の合計である。
一般に、粉体物質の粒子径と比表面積は反比例の関係にあり、比表面積を測定することで、粉体の粒子径を定性的に反映することができます。電子顕微鏡はすべての工業単位で利用可能ではないので、粉末の粒子径が利用できないため、比表面積の測定は重要な実用的価値があります。
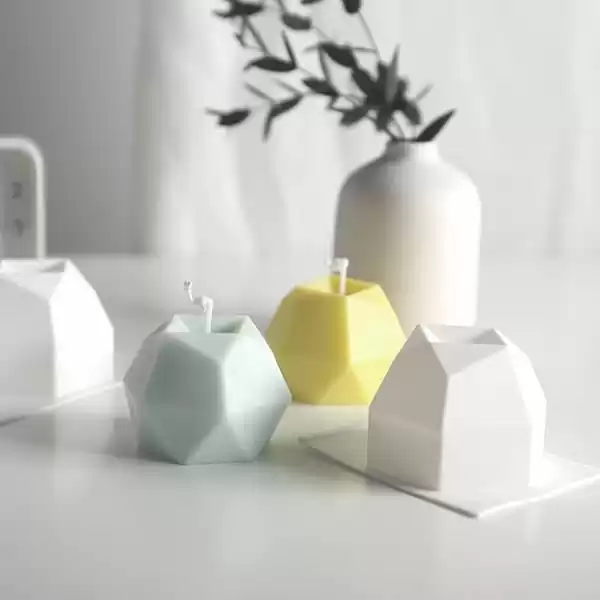
c.シリカの表面にはシラノール基があり、シリカの多くの用途はこのような基と直接関係しているため、表面水酸基を定量的に測定することは非常に重要である。
シリカの表面水酸基を測定するためのデータには、一般に、全水酸基、隣接水酸基、孤立水酸基が含まれる。
後者の2つはシリカ表面でSi-OHの形で結合しており、これらを総称して結合水酸基と呼ぶ。全水酸基は、結合水酸基とシリカ表面に吸着した水分子中の水酸基の和であり、これらの水酸基データはそれぞれ異なる条件で測定することができる。測定条件は
(1) シリカバッグから直接サンプリングして測定した水酸基量を総水酸基量とする。
(2) シリカを110℃で3時間乾燥して測定した水酸基は、結合水酸基である。
(3)シリカを600℃で3時間乾燥した後に測定した水酸基は、単離された水酸基である。
(4) 結合水酸基と単離された基の違いは、隣接水酸基である。
d.二次構造の決定 海外では一般に、二次構造の程度がフィラー補強の挙動に直接影響すると考えられているため、二次構造の決定も非常に重要である。
1つは圧縮時の見かけの比容積を測定する方法、もう1つは吸油量を測定する方法である。
弱補強フィラー
弱い補強の注入口はまた不活性の注入口、シリコーン ゴムの小さい補強の効果だけ、一般にで単独で使用されません呼ばれることができます。 シリコーンゴムしかし、シリカの役割で、シリコーンゴムの硬度を調整し、ゴムと加硫ゴムの耐油性と可溶性のプロセス性能を向上させ、ゴムのコストを削減します。
一般的に使用される弱補強剤は、珪藻土、石英粉、酸化亜鉛、二酸化チタン、ケイ酸ジルコニウム、炭酸カルシウムなどである。