「従来の熱伝導性材料は、Ag、Cu、A1などの金属、A12O3、MgO、BeOなどの金属酸化物、グラファイト、カーボンブラック、Si3N4、A1Nなどの非金属材料がほとんどであった。
工業生産と科学技術の発展に伴い、人々は熱伝導性材料に対する新たな要求を打ち出し、その材料が優れた総合性能を持つことを望んでいる。
例えば、電気・電子分野では、集積化技術や組立技術の急速な発展により、電子部品や論理回路の体積が数千分の1になり、高い熱伝導率の絶縁材料が必要とされている。
ここ数十年、高分子材料の応用分野は拡大しており、伝統的な産業で使用される様々な材料、特に金属材料を合成高分子材料に置き換えることが、世界の科学的研究努力の方向性の一つとなっている。"
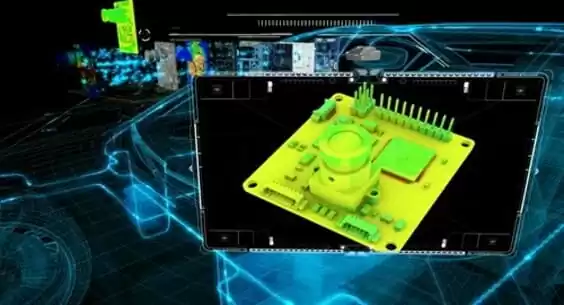
熱伝導性シリコーンフィルムとは?
熱伝導性シリコーンフィルムは、シリコーンを基材とし、金属酸化物などの様々な補助材料を用いて特殊なプロセスで合成される熱伝導性媒体材料の一種です。
熱伝導性シリコーンゴム は、シリコーン樹脂を結合材とするポリマー複合材料で、熱伝導性の目的を達成するために熱伝導性粉末を充填している。
一般的な熱伝導性シリコーンフィルムのマトリックス材料とフィラー
シリコーン樹脂(基礎原料)
1.絶縁熱伝導フィラー:酸化アルミニウム、酸化マグネシウム、窒化ホウ素、窒化アルミニウム、酸化ベリリウム、石英、その他のシリコーン可塑剤
2.難燃剤:水酸化マグネシウム、水酸化アルミニウム
3. 無機着色料(色の区別)
4. 架橋剤(接着性能要件)
5. 触媒(プロセス成形要件)
注: 熱伝導シリコーンフィルムは熱伝導の役割を果たし、加熱体とヒートシンクの間に良好な熱経路を形成し、ヒートシンク、構造固定具(ファン)などが一緒になってヒートシンクモジュールを形成する。
フィラーには、以下の金属フィラーと無機フィラーが含まれる。
1.金属粉フィラー: 銅粉.アルミニウム粉鉄粉錫粉ニッケル粉など
2.金属酸化物:酸化アルミニウム酸化ビスマス。酸化ベリリウム。酸化マグネシウム。酸化亜鉛。
3.金属窒化物:窒化アルミニウム。窒化ホウ素。窒化ケイ素。
4.無機非金属:黒鉛。炭化ケイ素。炭素繊維。カーボンナノチューブ。グラフェン。炭化ベリリウム など
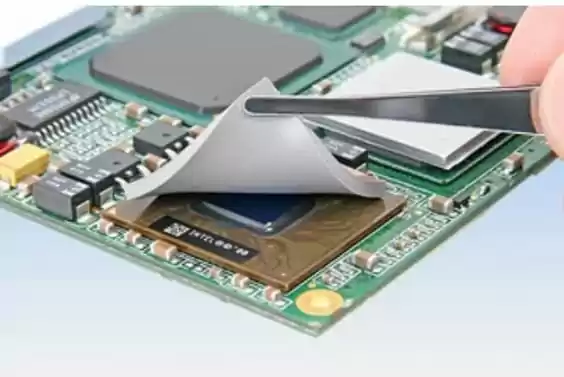
熱伝導性シリカゲルの分類
熱伝導性シリコーンは次のように分けられる。 熱伝導性シリコーンガスケット および非シリコーンガスケットに使用されています。大半の熱伝導性シリカゲルの電気絶縁性能は、最終的にはフィラー粒子の絶縁性能によって決まります。
1.熱伝導性シリコーンガスケット
熱伝導性シリコーンガスケットは、それぞれ異なる特性を持つ多くのサブカテゴリーに細分化されています。
2.非シリコンガスケット
非シリコンガスケットは高熱伝導性材料で、両面に自己粘着性があり、電子部品組立に使用した場合、低圧縮力で低熱抵抗と良好な電気絶縁特性を示す。それは-40℃~150℃で安定して働くことができる。UL94V0難燃グレードに適合しています。
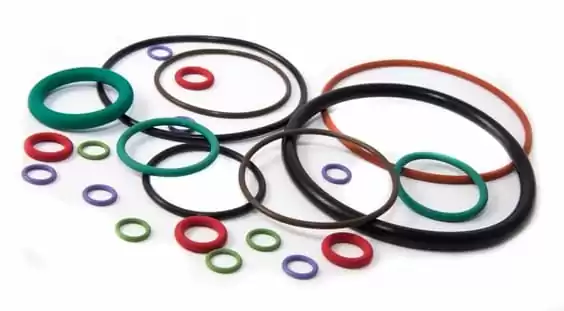
熱伝導性シリカゲルの熱伝導メカニズム
熱伝導性シリカゲルの熱伝導率は、ポリマーと熱伝導性フィラーとの相互作用に依存する。フィラーの種類によって熱伝導メカニズムが異なります。
1.金属フィラーの熱伝導率
金属フィラーの熱伝導性は主に電子の移動によるもので、電子の移動の過程には高熱の移動が伴う。
2.非金属フィラーの熱伝導率
非金属フィラーの熱伝導率は主にフォノン熱伝導率に依存し、その熱拡散率は主に隣接原子または結合基の振動に依存する。金属酸化物、金属窒化物、炭化物を含む。
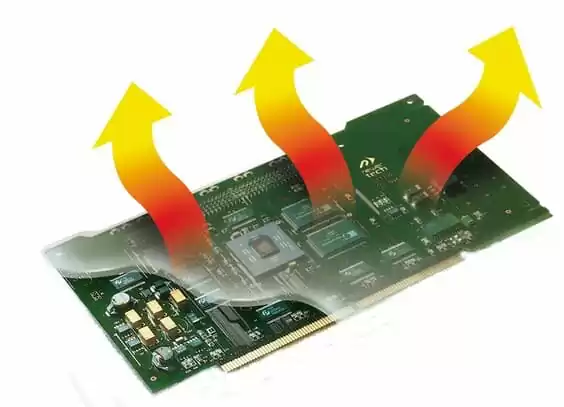
熱伝導性シリコーン・フィルムの使い方は?
熱伝導性シリコンフィルムは一般的に、設計の初期段階で構造設計やハードウェア・回路設計に加えられる。
考慮すべき要素は、熱伝導率への配慮、構造への配慮、EMCへの配慮、振動・吸音への配慮、設置試験などである。
1.1.過度の放熱ソリューションを選択:電子製品は現在、短いと薄い傾向に、受動的な放熱の一般的な使用は、従来のヒートシンクのソリューションが主である;現在の傾向は、ヒートシンクを排除することです、構造ヒートシンク(金属ブラケット、金属シェル)の使用;
あるいは、ヒートシンクソリューションと放熱構造部品プログラムの組み合わせ、異なるシステム要件と環境では、最高の費用対効果のソリューションを選択します。
2.ヒートシンクプログラムの場合、熱伝導率の低い両面接着剤を直接使用することはお勧めしません。 熱伝導性シリコーングリース 衝撃吸収機能がないため、金属フックまたはプラスチックプッシュピンを使用することを推奨し、熱伝導性シリコーンフィルムの0.5mm厚を選択し、これらの2つのプログラムを使用して簡単にインストールして動作します。
しかし、また、接着剤によって使用することはできません、転送熱放散効果は、熱伝導性両面接着剤よりもはるかに良い、より安全で信頼性の高いものになります。単価、人件費、設備などのトータルコストは、より競争力のあるものになります。
3.放熱構造部品の選択 クラスの放熱は、プロセスの構造とサイズの局所的な突出、局所的な回避などの形態の構造の接触面における放熱構造部品を考慮する必要がある。 熱伝導性シリコーン 良いバランスを選ぶために。
工程が許す条件下では、特に厚い熱伝導性シリコーンフィルムを選択しないことが推奨される。ここでは、操作の利便性から片面粘着剤を使用し、粘着面を放熱構造に貼り付けることが一般的に推奨される;
ここでは特に、熱伝導性シリコーンフィルムに一定の圧力がかかるように、圧縮比を選ぶ必要がある。
熱伝導性シリコーンフィルムの厚さは、放熱構造と熱源との間の理論的な隙間よりも大きくなければならず、一般的には1mm~2mm以上である。
放熱構造部品の選択はまた、コンポーネントの位置のPCBレイアウトで考慮されるべきである、ねえ、htとパッケージの形式は、いくつかの熱源を定期的に配置することができ、放熱構造部品のコストを削減します。
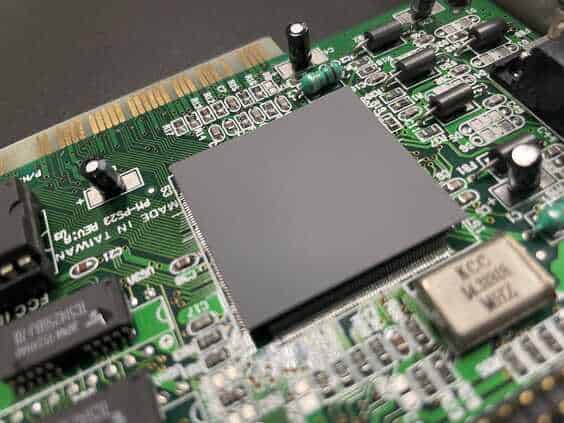
熱伝導性シリコーンフィルムの選び方
熱伝導率の選択
熱伝導率の選択は、主に熱源の消費電力の大きさ、ヒートシンクの大きさや放熱能力の熱構造によって決まる。
一般的なチップの温度仕様パラメータが比較的低い、または温度に対してより敏感である、または熱流密度が比較的大きい(一般的に0.6w/cm3より大きい放熱処理を行う必要があり、一般的な表面は0.04w/cm2未満である唯一の自然対流処理を必要とすることができます)これらのチップまたは熱源は、放熱処理する必要があり、熱伝導性シリコーンフィルムの熱伝導率の高い係数を選択しようとします。
民生用電子機器業界では一般的に、チップのジャンクション温度が85度より高くなることは許されておらず、高温テストではチップの表面を75度以下に制御することも推奨されている。
表面の最初の外観または表面による最終顧客は、室温での推奨温度に接触することができます45度未満でなければなりません。高い熱伝導率の熱伝導性のシリコーンのフィルムを選ぶことは設計条件を満たし、ある設計余裕を保つことができる。
注記 熱流密度: は、単位時間(1秒)あたりに単位面積(1平方メートル)あたりの断面を通過する熱量として定義される。
ジャンクション温度は通常、ケース温度やデバイス表面温度よりも高い。ジャンクション温度は、半導体ウェハーからパッケージ・デバイス・シェルへの放熱に要する時間と熱抵抗を測定することができます。
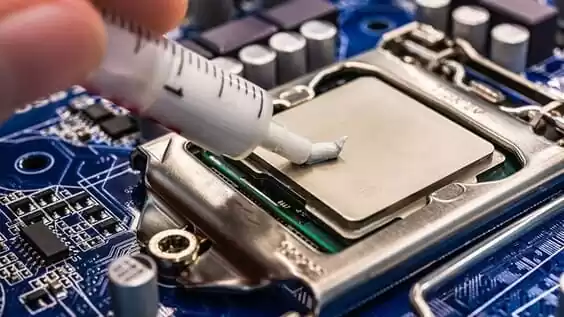
サーマルシリコーンの熱伝導率に影響を与える要因
1.ポリマーマトリックス材料の種類と特性
マトリックス材料の優れた熱伝導率は非常に高く、マトリックス中のフィラーの分散が良いほど、またマトリックスとフィラーの組み合わせが良いほど、熱伝導性複合材料の熱伝導率は向上する。
2.フィラーの種類
フィラーの熱伝導率が高いほど、熱伝導性複合熱インターフェース材料の熱伝導率は向上する。
3.フィラーの形状
一般的に、熱伝導経路を形成しやすい順に、ウィスカー>ファイバー>フレーク>グラニュールとなり、熱伝導経路を形成しやすいフィラーほど熱伝導率が良い。
4.フィラーの含有量
ポリマー中のフィラーの分布は、複合材料の熱伝導率を決定する。フィラーの含有量が少ない場合、熱伝導率の影響は明らかではありません。フィラーの含有量が多すぎる場合、複合材料の機械的特性に大きな影響を与えます。
フィラー含有量がある値まで増加すると、フィラー同士が相互作用して系内にネット状または鎖状の熱伝導性網目鎖を形成し、熱伝導性網目鎖の方向が熱の流れ方向と一致するときに熱伝導率が最もよくなる。したがって、熱伝導性フィラーの量には臨界値がある。
5.フィラーと基材界面の接合特性
フィラーと基材の結合度が高いほど熱伝導率が向上し、フィラーの表面処理に適したカップリング剤を選択することで、10%~20%で優れた熱伝導率を向上させることができる。