1.シリコーン材料の特徴
A.シリコーン原料は一般にゲル状で、塑像にやや似ており、無色、半透明、無臭である。
B.その主な特徴は、耐高温性(最高300℃)と耐低温性(最低-100℃)の両方で、現在最高の耐寒性・耐高温性ゴムであると同時に、電気絶縁性に優れ、熱酸化やオゾンに対する安定性が高く、化学的に不活性である。
欠点は、機械的強度が低く、耐油性、耐溶剤性、耐酸性、耐アルカリ性に劣り、加硫が難しく、価格が割高である。使用温度:-60℃~+200℃。以上 シリコーンゴム マニュアルの
C.使用温度:前述の通り、一般的には-40℃~200℃に設定され、短時間で230℃に達することもある。
D.経年劣化の問題:耐油性、耐酸性、耐アルカリ性が悪く、応力とはあまり関係がない。
E.接着の問題:表面処理の前に、以下のものを使用する。 シリコーン製品 シリコーン部品と接着する接着剤としては、他の部品との接着が表面活性化されている必要があり、接着剤の表面は加硫によって硬化させることができる。
ゴムと反応し、ゴムを架橋させることができる物質を総称して加硫剤と呼び、架橋剤とも呼ばれる。加硫剤には多くの種類があり、現在も増え続けています。
使用されてきた加硫剤には、硫黄、セレン、テルル、硫黄含有化合物、金属酸化物、過酸化物、樹脂、キノン、アミンなどがある。
F.材料の硬度:ショア硬度によると、プラスチック部品は理論上、国内市場では10度から80度の間で選択できる。
一般的に手に入りやすいのは20度から70度で、よく使われるのは40度から50度だ。
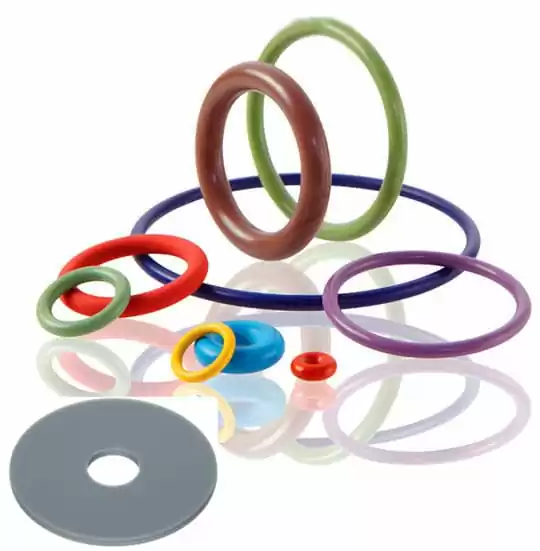
2.シリコーン製品の製造工程
A:原材料の形状と色
B:色合わせと混練の後、様々な色のフレークが乳白色のシリカゲルから変化する。
C:混練と成形の後、原料を短冊状にプレスし、短冊状に切断する。
D:加硫成形
E:トリミング、エッジ除去、検査、梱包
F:終了 シリコーン製品
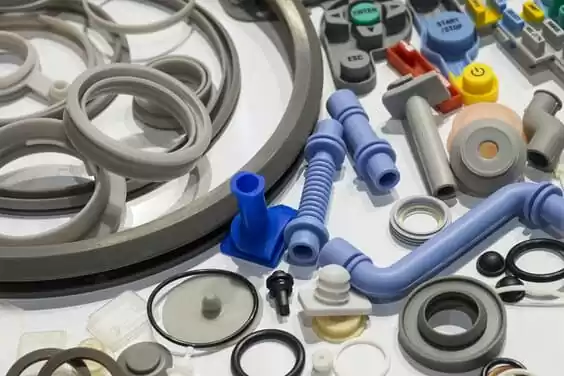
3.製品のサイズと特徴
A.限界サイズ:最も厚い部分は15~20MM、球体であれば直径は30MMまで可能です。一般的に、推奨される厚さは3MM以下です。
3MMより大きい場合、加硫に時間がかかり、コストが高くなる。最も薄い部分は理論的には0.2MMに達することができるが、設計では一般的に最も薄い0.3MMが取られ、0.4MMが推奨される。
B.相対的な大きさ:厚さの差に関しては、最も薄い部分と最も厚い部分が3倍を超えないようにすることが推奨される。このような問題は主に材料を加硫する際の温度と圧力に依存する。
C.収縮率:収縮率 シリコーン材料 は素材の硬度に関係する。メーカーから提供される副資材のほとんどは、1.022から1.042の間である。
40度から50度の素材の場合、収縮率は一般的に1.03である。プラスチックに比べ、シリコーン製品は収縮による見かけの表面欠陥が少ない。
D.寸法精度 シリコーンゴム製品 は1つの金型に複数のキャビティがあるため、プラスチック製品に比べてキャビティの数が非常に多い。そのため、プラスチック製品のようなサイズコントロールの利便性はない。
一般精度はプラスマイナス0.1、高精度品はプラスマイナス0.05です。プラスチック部品とボタンの穴合わせに使用する場合、最小クリアランスは片側0.1、推奨値は片側0.2です。
E.形状設計:ゴムスリーブ部品は、一般的に、製品の形状図に従って金型工場に原図を提供し、金型工場によって決定されるマッチング問題を説明するだけで十分です。
通常の場合、製品の大きさにもよりますが、ゴムスリーブと製品の間の調整は、一般的に片側で0.2~0.5小さい負の偏差です。
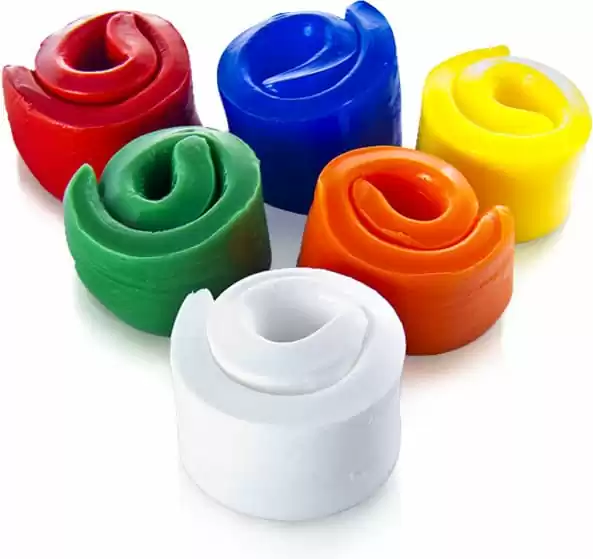
4.金型構造
A.型厚の上限:
仮に250mm、サイズは500X500に達することができ、製品の金型面積は400X400に達することができる。金型の構造は一般的に上型、下型、底板、上板、エジェクターピン、金型コア、ヒンジなどの補助部品に分けられる。設計時 シリコーン製品そのため、金型と製造工程の特徴に注意を払う必要がある:
B.脱型:
シリコーン製品の離型は、直接、強制的に行うことができます。設計上の欠陥がない製品の場合、強制離型に必要なサイズは、主に脱型時の金型コアの最大部分の円周と最小の閉鎖部分の比率にある。55°以下の製品では、2~3回行うことができる。開口部に割れや鋭利な角が生じることがある。
加硫時に180℃の温度が必要なため、脱型作業は金型自体の上下分離以外はほとんど手作業になる。従って、脱型の利便性と迅速性を考慮して部品を設計する必要がある。
そのため、脱型時間が長く、部品の加硫品質と量産効率に影響を与えない。シリコーンの離型方法は主に手作業であり、天板の作用ストロークも小さいので、シリコーン金型は従来の金型に比べて天板が傾斜していない。 プラスチック金型.一般的に、コアのプルは提供されない。
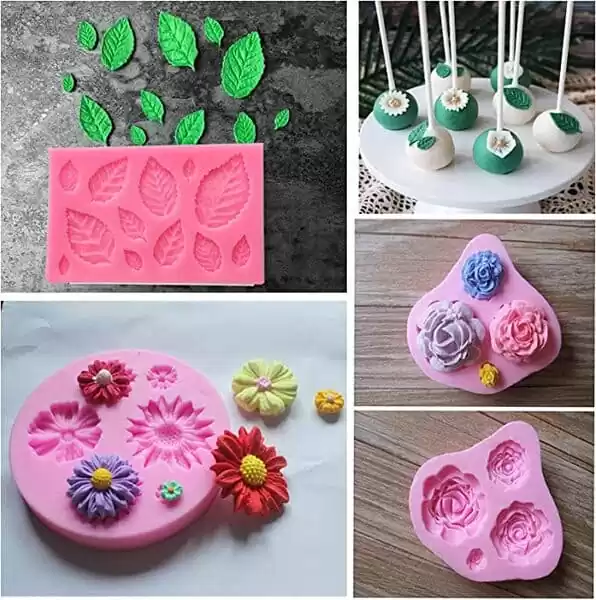
C.コアの固定:
プラスチック金型とは異なり、シリコーン金型の中子は、一般的に、製品部品が金型から取り出される際に一緒に取り出されます。 射出成形金型 を開いて部品を取り出す。そのため、プラスチック金型に比べて固定や正確な位置決めが難しく、金型コアの剛性も高い。
一般に中子は一緒に作られ、すべての中子が一度に固定される。あるいは、金型コアを補助ツールに通して、素早く位置決めできるようにする。型締め工程では大きな圧力がかかるため、金型コアが動かないように厳重に管理する必要がある。
D.コア抜き:
一般に自動移動はできないが、強制的に外すことは可能で、芯抜きは小規模な構造物にのみ使用される。コア抜き設定は プラスチック金型しかし、金型を開く際には手作業で取り除かれる。
また、中子抜きは金型内で大きなスペースを占めるため、余分な加工が煩雑になるだけでなく、金型が破損しやすくなる。 シリコンモールド 1つの金型に収まるが、金型スペースの利用率も低い。だから、コアはできるだけ抜かない。
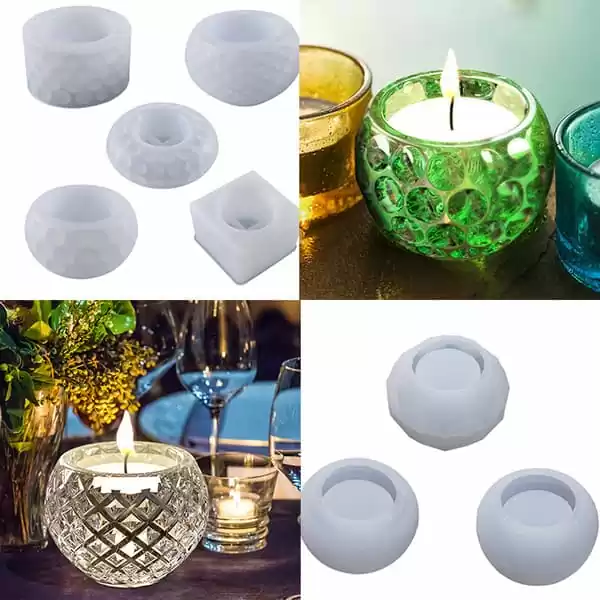
E.形:
シリコーン製品は、表面が無傷の状態では非常に強靭だが、ひとたび亀裂が入ると、外力の作用で亀裂が急速に拡大する。つまり, シリコーン製品 はひび割れに非常に敏感だ。
これらの問題を考慮すると、シリコーン部品の正しい金型設計に注意を払う必要がある:応力集中や亀裂を避けるために、すべての位置に鋭い角がないようにする。開口部のR角度は0.5以下でなければならない。
F.エッジは自分で取り外せる:
セルフリムーバブルエッジの主な機能:余分なゴムを収容することです。
自己除去エッジは、一般的に部品のパーティング面の薄いエッジと対応する比較的強い引き裂きエッジで構成されています。薄いエッジの厚さは一般的に0.1~0.2、引き裂きエッジの厚さは一般的に0.8、幅は一般的に1~2MMである。
G. 挿入:
シリコーン製品にはさまざまな種類のインサートを入れることができるが、いくつかの問題に注意する必要がある。 第一に、埋め込み部品の表面は、主に表面加硫や表面活性化などの前処理を施す必要がある。
そうしないと、インサートと接着剤をしっかりと接続することが難しくなる。もうひとつは、インサートの固定位置で、垂直方向は一方向に固定できるが、それ以外の方向は完全に固定しなければならない。金型全工程でインサートが動かないようにするためである。
3つ目は、インサート周囲の接着剤の厚さである。完全に封止されている部品(全表面が封止されているため、インサートが位置決めできない)の場合、インサートの周囲に最低0.5mmの厚みを使用すべきである。位置決めが可能なインサートの場合、周囲の接着剤層の厚さは0.4MM以上でなければならない。
H.その他の補助工程
グルーインジェクション(接着)工程:
に似ている。 射出成形 射出成形の工程では、まず射出する部品を固定し、射出中に原料が射出用に設計されていない部品を汚染しないように制御するために、金型の第一層を閉じます。次に2層目の金型が閉じられ、ゴムコンパウンドがプレスされて成形される。
圧延工程: 最初にゴムを作る
成形: この製造工程は、完全封入の場合にも使用できる。
ディッピング: ゴム(ラバー)本体の原料は流動性があり、ワークを原料に何度も浸す。原料の内層は加硫され、設計された厚さになるまで再び浸漬される。
エポキシ: 原料は塗料に似た良好な流動性を持ち、室温で加硫される。金型は比較的簡単で、一般に手作業で行われ、最初の層が素早く硬化したところで次のコーティングが施される。
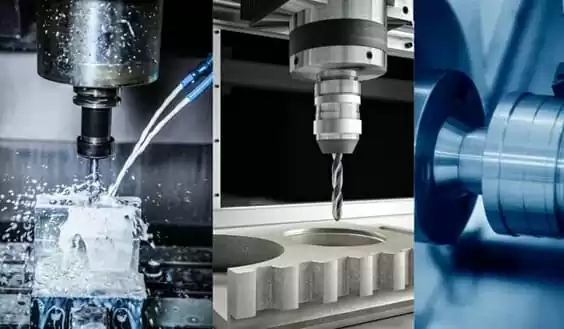
L.マルチカラー製品:
Aは2組の加硫金型に分け、Bは手彩色で、加硫した後、部品の彩色分離部分は一定の高さが必要で、混色導電性接着剤、二次加硫シリコーンの組み合わせを避けるためです。 シリコーン 接着 5.硬度測定と工具。
ゴムの硬さを測定する最も一般的な器具は、ショア(ショアとも呼ばれる)デュロメーターと呼ばれるものです。バネを使って金属製の圧子を材料の表面に押し付け、その圧子がどの程度深く浸透しているかを測定します。
この測定器は、ゼロから0.100インチまでの貫入深さを測定する。目盛りがゼロの場合は、圧子が限界深さまで貫入したことを意味し、100の場合は貫入深さがゼロであることを意味する。ショア硬さ試験機には、さまざまな硬さ範囲と自動化の度合いを持つものがあります。
最も一般的に使用される尺度のひとつにショアA尺度がある。ショアAデュロメーターは、鈍い圧子と中程度のバネを持っています。測定値が90以上になると、ショアAデュロメーターは不正確になります。このような硬い素材には、ショアDデュロメーターが使われます。ショアDデュロメーターは鋭い圧子と強いバネを持ち、深く浸透します。
硬いプラスチックを測定する場合は、ロックウェルデュロメーターのような、より鋭く弾力性のある圧子を持つデュロメーターを使用します。反対に、柔らかいゲルや発泡ゴムの測定には、ショア00デュロメーターが使われます。

ほとんどの複数の材料は初期応力に耐えることができますが、時間の経過とともにクリープと緩和により降伏します。デュロメーターの測定は、瞬時に行うことも、一定の遅延時間(通常は5~10秒)の後に行うこともできます。即座に測定した値は、遅延させて測定した値よりも常に高い(または硬い)値を示します。
遅れの測定値は、材料の硬さだけでなく、その弾性をよりよく表している。弱くて弾性の低い材料は、強くて弾性の高い材料よりもクリープを起こしやすい。
データの妥当性を保証するためには、正確な試験手順が必要です。正確な測定値を得るためには、圧子が支持面の影響を受けないように、平らで十分な厚みのある試験片が必要です。
通常、必要な厚さは0.200インチだが、より薄い厚さがあれば、変形の少ない硬い材料でも正確に試験できる。