はじめに
シリコーンゴム圧縮成形プロセスは、高圧と熱を利用して液体シリコーンゴムを目的の製品に成形する製造方法である。この技術は、自動車、医療、消費財など様々な産業で応用されています。
近年、エネルギー効率は、環境への影響を軽減するだけでなく、メーカーのコスト削減にもつながるため、生産プロセスにおいてますます重要な要素となっている。エネルギー集約的な シリコーンゴム製造 シリコーンゴムの圧縮成形によってエネルギー効率を達成する方法を模索する必要がある。そうすることで、加工エネルギーの消費を抑えつつ、高品質な製品を効率よく生産することができる。今回は、液状シリコーンゴムの圧縮成形によるエネルギー効率化について、さまざまなアプローチを紹介する。
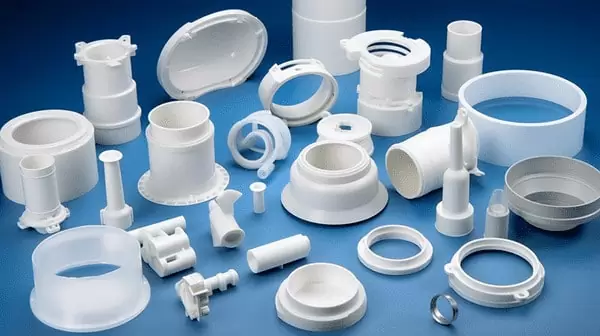
II.シリコーンゴム圧縮成形におけるエネルギー効率の達成
シリコーンゴムの圧縮成形は、様々な産業で使用されている一般的な生産プロセスである。しかし、この工程はエネルギーを大量に消費するため、生産コストと環境への影響が大きい。この問題に対処するため、製造業者は以下のようないくつかの戦略を実施し、エネルギー消費と効率の向上を実現することができる。 シリコーンゴム圧縮成形.
省エネ駆動システムの採用
先進技術を駆使してモーターの回転数、出力、トルクを制御し、成形工程でのエネルギー消費を削減します。これらのシステムは、必要なときだけ作動するようにプログラムすることができ、エネルギーの無駄を省きます。
補助成形技術の採用
追加の設備や工程は、生産効率を向上させ、エネルギー消費を削減することができる。ホットランナー金型は、ランナーやゲートの必要性をなくし、金型内での溶接や組み立ては、二次加工工程に起因するエネルギー消費を削減することができる。
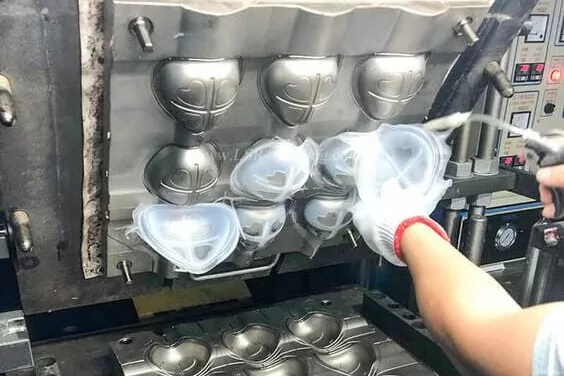
エネルギー回生システムの活用
これらのシステムは、成形工程で発生する廃エネルギーを回収して再利用する。例えば、エネルギー再生システムは、冷却水システムから熱を回収し、金型に入る前の材料を予熱するために再利用することができます。
冷暖房配管の改善
赤外線加熱や高効率冷却システムなど、高度な加熱・冷却システムを使用することで、成形工程におけるエネルギーの浪費や消費を抑えることができる。
正しい射出成形機の選択
液体 射出成形工場 射出成形機を選択する際には、機械の能力、推奨される射出成形プロセス、冷却効率を考慮する必要があります。そうすることで、エネルギーの無駄を最小限に抑え、エネルギー消費を減らすことができる。

プロセスパラメーターの最適化
溶融温度などのプロセスパラメーターを微調整することで、最適なエネルギー消費と生産効率を確保することができる。
廃棄物エネルギー削減と廃棄物防止
廃棄物を削減し、材料の無駄を防ぐことは、エネルギー消費と環境への影響を最小限に抑えることができます。金型キャビティ設計の最適化、ユニット化された成形スキーム、およびその他の加工技術は、より良い表面品質を促進し、材料の無駄を削減することができます。
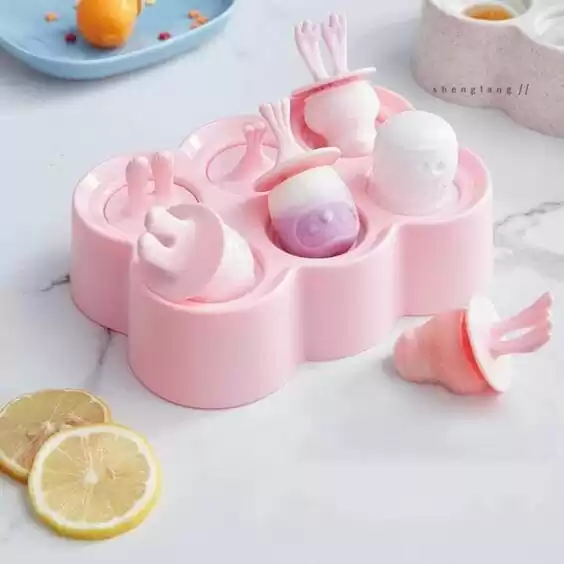
これらの戦略を実施することで、メーカーはエネルギー消費の大幅な削減を達成し、生産効率を高め、環境への影響を最小限に抑えることができる。
III.圧縮成形と射出成形シリコーン?
しかし シリコーンゴム 圧縮成形は広く使われている製造方法だが、射出成形にも利点と欠点がある。
圧縮成形は、高圧と熱によってシリコーンゴム材料を成形する技術です。この方法は、複雑なデザインの大型部品や厚みの異なる部品を作る場合に最適ですが、時間がかかり、効率も悪くなります。
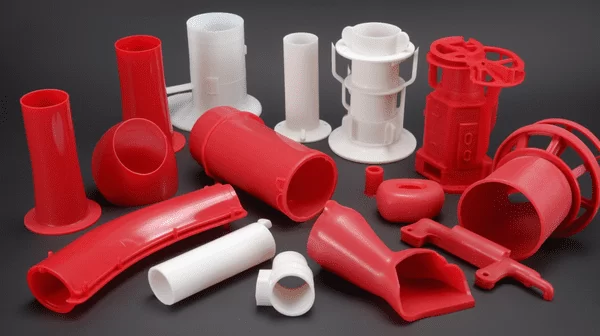
一方、射出成形シリコーンは、強い圧力下で材料をキャビティに注入します。この方法は、圧縮成形よりも速く効率的であるため、優れた精度と一貫性を持つ部品を製造するのに理想的です。しかし、大きな部品や厚みの異なる部品には不向きかもしれません。
圧縮成形には、厚みの異なる大型部品や複雑なデザインの部品を製造できるなど、いくつかの利点があります。さらに、少量生産には費用対効果が高いかもしれませんが、大量生産には理想的ではないかもしれません。
シリコーンの射出成形は、圧縮成形に比べて、部品の高精度と一貫性、大量生産、複雑な形状の部品など、いくつかの利点があります。しかし、射出成形シリコーンは、圧縮成形よりもコストが高く、より複雑な装置を必要とする可能性があります。
最後に、圧縮成形と射出成形のどちらを選択するかは、製造する部品のサイズや複雑さ、希望する生産量、使用可能な設備やリソースなど、いくつかの要因によって決まります。
IV.圧縮成形における生産効率の向上
シリコーンゴムの圧縮成形において効率が不可欠であるように、生産効率を高めることも製造業者にとって同様に不可欠である。ここでは、生産効率を高めるために採用できる戦略をいくつか紹介する:
圧縮成形の生産時間を短縮する3つの方法
製造業者は、高速硬化材料を使用し、設計を最適化し、高速圧縮成形機を使用することによって、生産時間を短縮することができます。これらの戦略は、サイクルタイムを短縮しながら生産率を高めるのに役立ちます。
金型流動解析と設計プロセスの重要性
金型流動解析は、設計の最適化と生産時間の短縮に役立ちます。金型内部の材料フローを分析することで、メーカーは材料が滞留し、欠陥の発生や生産の遅れにつながる可能性のある領域を特定することができます。さらに、金型設計を最適化することで、成形工程全体の効率が向上します。
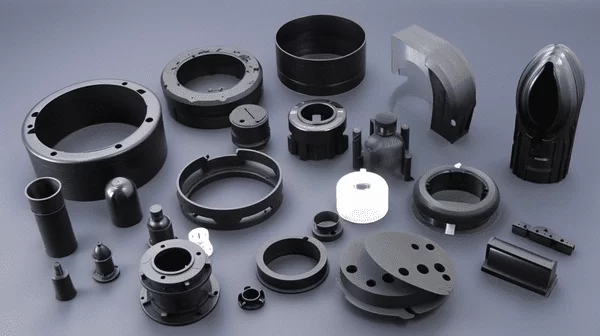
柔軟なエネルギー利用の導入
企業は、生産量に応じて調整するセンサーや制御システムを導入することで、生産需要に応じてエネルギー消費量を調整することができる。これにより、資源の効率的な利用が保証される。
新しい暖房技術の活用
電磁誘導加熱のような最新の加熱技術は、従来の方法よりも効率的に金型を加熱できるため、エネルギー消費を抑え、生産効率を高めることができる。
安定した生産管理と設備メンテナンス
信頼性の高い生産管理と機器のメンテナンスを確保することで、生産中断を防ぎ、ダウンタイムを最小限に抑えることができる。これは、適切なメンテナンス・スケジュールを作成し、機器の性能を監視し、問題を迅速に特定し修正する方法についてオペレーターを訓練することによって達成される。
これらの戦略は、メーカーが生産効率を高め、生産時間を短縮し、エネルギー使用を最適化するのに役立つ。
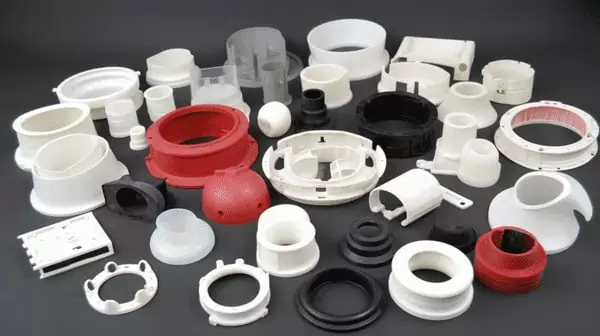
結論
最後に、シリコーンゴム圧縮成形におけるエネルギー効率は、コスト削減と環境への影響の最小化を望む製造業者にとって極めて重要である。省エネ駆動システムの使用、補助成形技術の採用、エネルギー回生システムの活用、加熱/冷却工程の最適化などの省エネ戦略を採用することで、メーカーはエネルギー消費量と廃棄物排出量を大幅に削減することができる。
エネルギー効率だけでなく、フロー分析、フレキシブルなエネルギー使用、安定した生産管理と設備メンテナンスなどの戦略によって、メーカーは生産効率を高めることができる。そうすることで、高品質のシリコーンゴム製品を効率的かつ持続的に生産することができます。
全体として、シリコーンゴム圧縮成形におけるエネルギー効率の重要性は、強調しすぎることはありません。省エネ戦略を採用することで、メーカーはコストを削減し、環境への影響を最小限に抑え、市場での競争力を維持することができる。新技術と新プロセスの継続的な進歩に伴い、シリコーンゴム圧縮成形によるエネルギー効率の達成は、時間の経過とともにさらに不可欠になるだろう。