서문
실리콘 고무는 분자의 주쇄에 실리콘-산소 구조를 포함하는 합성 고무 및 반무기 고분자 탄성 재료의 일종입니다. 디메틸디클로로실란과 같은 이중 기능성 실리콘 모노머의 가수분해 및 중축합에 의해 형성됩니다. 실리콘 고무는 일반 천연 고무와 매우 흡사하지만 실리콘 고무는 높은 수준의 열 안정성과 탄성을 가지고 있습니다. 60~300°C 범위 내에서 원래의 특성을 유지합니다. 고온에서 압축해도 수축이 거의 없으며, 외력이 제거되면 원래의 모양으로 돌아갑니다. 화학 책. 실리콘 고무 는 가황 방식에 따라 고온 가황 방식과 상온 가황 방식으로 나뉩니다. 후자가 더 빨리 발달합니다.
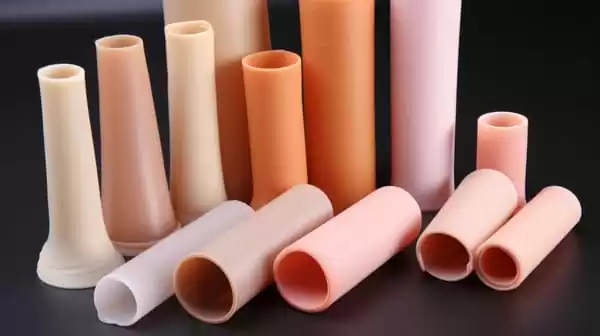
실리콘 고무 층은 전선, 케이블, 금속 부품의 보호 층, 절연 부품, 개스킷 씰 화학 원료, 밀봉 제품에는 자동차 엔진 크랭크 축 후면 밀봉 링, 연료 펌프 씰, 에어컨 버퍼 씰, 전위차계 절연 부싱 및 포팅 재료 등이 포함되며 생리적, 무독성 및 비 감작 특성을 활용하여 인공 심장 판막, 인공 폐, 인공 식도 및 성형 수술 재료 제조에 이상적인 의료용 폴리머 재료로 사용할 수 있습니다. 고온에 강한 단열 씰, 의료용 재료, 고전압 케이블, 접착제 등을 제조하는 데 사용됩니다. 그러나 생산 과정에서 실리콘 고무 제품에 기포가 발생하는 경우가 많습니다. 기포와 기공의 모양은 제품의 품질에 영향을 미칩니다. 따라서 실리콘 고무 제품 공장에서 제품의 품질을 향상시키고 싶다면 제품의 거품을 피하는 것부터 시작할 수 있습니다. 이 기사에서는 거품의 원인과 해결책에 대해 설명합니다. 실리콘 고무 제품.
II. 거품 발생의 원인
(1) 고무 재료 가황 온도 제어 시스템이 너무 낮거나 가황 온도가 너무 높아 열 전도성 실리콘 시트에서 블리스터링의 주요 원인 중 하나입니다. 가황 온도는 실리콘 고무를 성형할 때 중요한 매개 변수입니다. 일반적으로 실리콘 제품은 섭씨 160~200도로 설정됩니다. 그러나 때때로 너무 오랜 이형 작업이나 기타 이유로 인해 가황기에서 금형이 오랫동안 가열되지 않는 경우가 있습니다. 그 결과, 가황기의 온도가 실리콘 몰딩 몰드 가 낮고 실리콘의 가황 온도가 낮아 열 전도성 실리콘 시트가 형성된 후 제품에 기포가 발생할 수 있습니다. 이를 위해 성형 온도를 높이거나 빈 금형을 기계에 넣고 일정 시간 동안 가열하여 문제를 해결하면됩니다. 가황 온도가 너무 높고 성형 온도가 너무 높으면 열 전도성 실리콘 시트에 기포가 생길 수도 있습니다. 왜 그럴까요? 성형 온도가 너무 높으면 금형 폐쇄 및 가압 공정 중에 금형 표면의 실리콘 원료가 형성되기 시작했습니다. 이때 공기가 내부에 갇혀 배출이 어렵기 때문에 열 전도성 실리콘 시트 성형에 기포가 발생합니다. 따라서 성형 온도를 적절히 낮추기만 하면 됩니다.
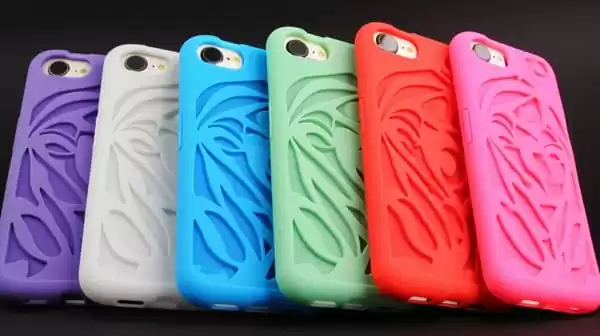
(2) 실리콘 제품에 기포가 발생하는 이유는 배기가 불충분하기 때문입니다. 실리콘 고무 재료를 실리콘 금형에 넣은 후 금형 배기 라인을 닫는 순간 많은 공기가 유입됩니다. 공기가 실리콘 원료와 통합되는 것은 불가능합니다. 그렇지 않으면 공기가 배출되어 실리콘 버튼 또는 금형 배기 라인이 형성된 후 표면에 기포가 나타납니다.
(3) 금형의 구조가 불합리합니다. 실리콘 몰딩 금형 캐비티 실내 습도의 불합리한 설계는 또한 거품을 일으킬 수 있습니다. 실리콘 몰딩. 예를 들어, 금형의 배기 라인 구멍 분배 제품의 배열, 분할 방법, 금형 분할 방법, 금형 크기 설계 등은 모두 기포가 좋지 않습니다. 그러나 금형 세트를 여는 데 드는 비용이 매우 높고 수정하기가 쉽지 않습니다.
(4) 가황 시간이 너무 짧습니다. 가황 온도와 마찬가지로 가황 시간도 열 전도성 실리콘 시트의 성형에 중요한 매개 변수 중 하나입니다. 가황 시간의 길이에 따라 열 전도성 실리콘 시트가 완전히 가황 될 수 있는지 여부가 결정됩니다. 가황 시간이 너무 짧으면 성형 후 열 전도성 실리콘 시트가 부드러워 질뿐만 아니라 열 전도성 실리콘 시트 표면에 기포가 쉽게 형성 될 수 있습니다. 이러한 결함이 발생하면 실리콘의 가황 시간을 적절히 연장할 수 있습니다.
(5) 생산 공정도 중요합니다. 노화 방지제 RD는 오픈 밀의 혼합 작업 중에 기포가 발생하기 쉽습니다. 이것은 주로 노화 방지제 RD의 융점과 두 번째로 오픈 밀의 낮은 작동 온도에 의해 발생합니다. 혼합 고무와 관련하여, 혼합하는 동안 산화 아연의 분산에 특별한주의를 기울여야합니다. 균일 한 분산은 또한 실리콘 시트의 발포를 유발하므로 고무 혼합 공정도 매우 중요한 단계입니다.
(6) 배합에 사용되는 원료의 수분 함량과 혼합 작업 중 및 제품이 물로 압출 및 냉각 된 후 건조의 적절성은 주로 가황 첨가 중 수분의 힘에 의해 발생합니다.
III. 버블 방지를 위한 솔루션 조치
1. 실리카겔 입자 비율 조정
실리콘 기포의 원인 중 하나는 제품에 과도한 양의 실리카겔이 함유되어 있기 때문에 이 문제를 해결하려면 이 비율을 적절히 조정하여 기포 발생을 줄이고 기포를 아예 방지해야 합니다. 이 전략을 최종적으로 결정하기 전에 테스트 및 실험적 검증이 필요할 수 있습니다.
2. 진공 추출 장비 사용
실리콘 제품을 생산할 때 진공 배기 장비를 사용하면 제품 안에 포함된 가스를 배출하고 기포를 효과적으로 줄일 수 있습니다. 생산 공정 중 기포 문제를 해결하려면 진공 배기를 솔루션 계획의 일부로 반드시 사용해야 합니다.
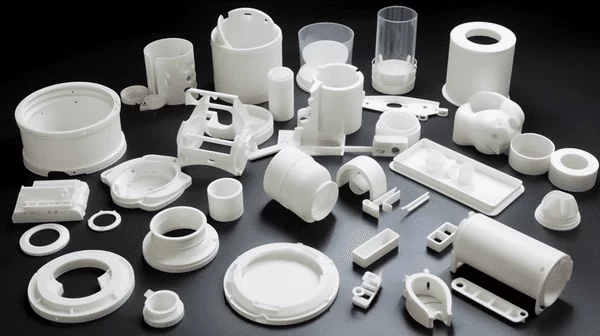
3. 생산 온도 설정
온도를 잘못 선택하면 기포가 발생할 수 있기 때문에 실리콘 제품 제조에 있어 온도는 필수적인 요소입니다. 따라서 생산 과정에서 온도를 적절히 설정하여 기포 생성을 최대한 억제하고 기포 생성을 최소화하기 위해 현재 상황에 따라 적절한 제어를 유지해야 합니다.
4. 계면 활성제 추가
실리콘 제품은 생산 과정에서 기포 문제가 종종 발생합니다. 계면활성제는 실리카겔 분자가 서로 더 효율적으로 흡착하고 기포 형성을 줄임으로써 생산 공정을 개선하는 동시에 품질을 높이는 데 도움이 될 수 있습니다.
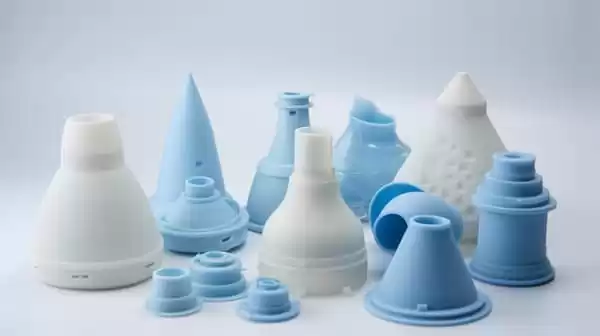
결론
버블의 생성은 한 가지 요인으로 인해 발생하는 것이 아니라 여러 가지 이유가 복합적으로 작용하여 발생하는 경우가 많습니다. 버블 문제를 해결할 때는 일반적인 규칙을 따르기 어렵고 구체적인 문제를 자세히 분석해야 합니다. 먼저 거품의 근본 원인을 파악하고 그 원인에 따라 문제를 해결할 수 있는 아이디어와 방법을 찾아야 합니다. 해결책은 하나 이상의 해결책이 있는 경우가 많으므로 다각적인 접근 방식을 사용하는 것이 가장 좋습니다. 거품 발생을 방지하는 것이 가장 좋습니다. 한편으로는 금형을 설계 할 때 적절한 배기 설정을해야하며, 다른 한편으로는 가황 전에 고무 블랭크 및 기타 재료를 미리 구우면 고무 재료 내부의 휘발을 효과적으로 제거 할 수 있습니다. 이는 제품의 거품을 방지하는 효과적인 수단입니다.