Wprowadzenie
Produkcja formowania tłocznego jest szeroko stosowanym procesem tworzenia materiałów kompozytowych o doskonałej wytrzymałości i trwałości. Polega on na zastosowaniu intensywnego ciśnienia i temperatury do materiału formującego wewnątrz wnęki formy, powodując, że przybiera on pożądany kształt. Materiały stosowane w formowaniu tłocznym mogą obejmować materiały termoutwardzalne, takie jak żywica epoksydowa i masa formierska (BMC), kompozyty z matrycą polimerową (PMC) i masy formierskie w arkuszach (SMC).
Lepkość materiału odgrywa znaczącą rolę w formowaniu tłocznym, określając jego odporność na przepływ i odkształcenia pod wpływem naprężeń. Odgrywa ona integralną rolę w kontrolowaniu przepływu materiału podczas formowania, wpływając na jego właściwości mechaniczne oraz dokładność wymiarową.
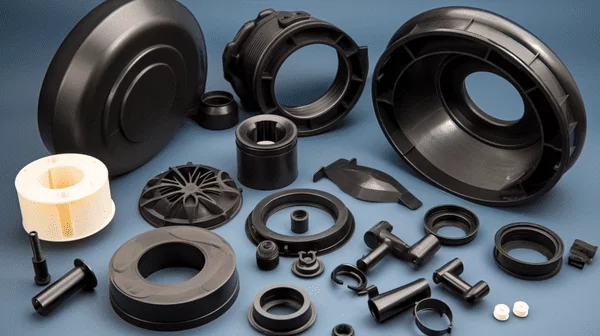
W tym artykule przeanalizujemy czynniki wpływające na formowanie tłoczne proces i stosowane materiały. Dodatkowo omówimy kluczowe kwestie podczas projektowania form, takie jak lepkość materiałów stosowanych w formowaniu tłocznym. Ponadto omówimy różne procesy formowania tłocznego i ich właściwości mechaniczne, zastosowania formowania tłocznego oraz potencjalne przyszłe zmiany w produkcji.
II. Czynniki wpływające na proces formowania tłocznego
Formowanie tłoczne to wysoce wyspecjalizowany proces produkcyjny, który wymaga starannego rozważenia wielu czynników. Należą do nich wymagania dotyczące wysokiego ciśnienia i temperatury, materiał formierski i jego skład, konstrukcja i złożoność formy, proces i czas utwardzania.
Ciśnienie i temperatura potrzebne do formowania tłocznego różnią się w zależności od formowanego materiału i złożoności projektu formy. Ponadto rodzaj i skład materiału do formowania odgrywają znaczącą rolę na tym etapie; przed rozpoczęciem tego etapu należy dokładnie rozważyć, który materiał spełnia wymagania aplikacji.
Konstrukcja i złożoność formy może znacząco wpływać na wymagany poziom ciśnienia i temperatury, a także na dokładność wymiarową produktu końcowego. Osiągnięcie właściwego projektu formy jest niezbędne do uzyskania pożądanych właściwości mechanicznych i precyzji wymiarów.
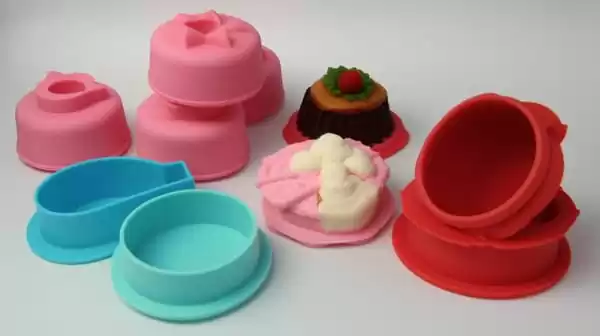
Proces i czas utwardzania są kluczowymi elementami formowanie tłoczne. Czas utwardzania zależy od formowanego materiału, konstrukcji formy, a także temperatury i ciśnienia stosowanego podczas procedury. Dokładna kontrola nad tymi zmiennymi jest niezbędna do uzyskania pożądanych właściwości mechanicznych i dokładności wymiarowej produktu końcowego.
Ogólnie rzecz biorąc, właściwe uwzględnienie wszystkich tych elementów jest niezbędne do uzyskania spójnych i wysokiej jakości wyników podczas formowania tłocznego.
III. Materiały stosowane w formowaniu tłocznym
Formowanie tłoczne może być stosowane z szeregiem materiałów, z których najpopularniejsze to materiały termoutwardzalne, kompozyty o osnowie polimerowej (PMC) i mieszanki do formowania arkuszy (SMC).
Materiały termoutwardzalne
Materiały termoutwardzalne, takie jak żywica epoksydowa i mieszanka do formowania masowego (BMC), są szeroko stosowane w formowanie tłoczne ze względu na ich doskonałą wytrzymałość, sztywność i stabilność wymiarową. Polimery te ulegają reakcji chemicznej po podgrzaniu i utwardzeniu, tworząc niezwykle wytrzymały materiał o doskonałych właściwościach mechanicznych.
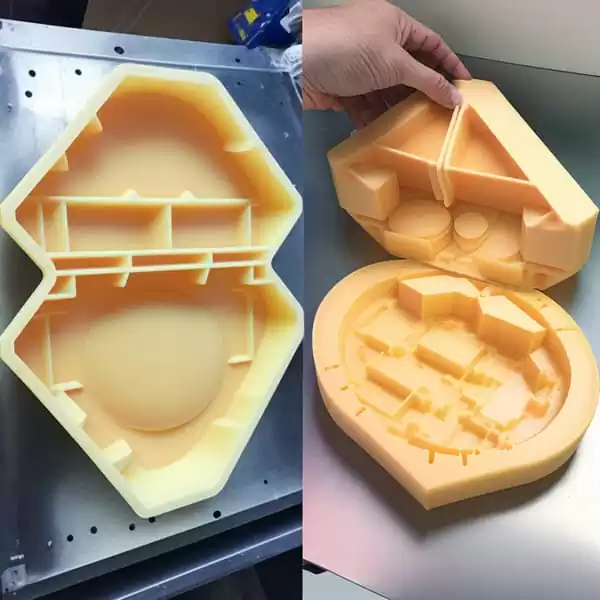
Kompozyty o osnowie polimerowej (PMC)
Kompozyty o osnowie polimerowej (PMC) są kolejnym materiałem powszechnie stosowanym w formowaniu tłocznym. Kompozyty te składają się z matrycy z żywicy polimerowej wzmocnionej włóknami, takimi jak szkło, węgiel lub aramid, w celu zwiększenia wytrzymałości i sztywności. Jako takie, PMC mają zastosowania tam, gdzie wymagana jest wysoka wytrzymałość.
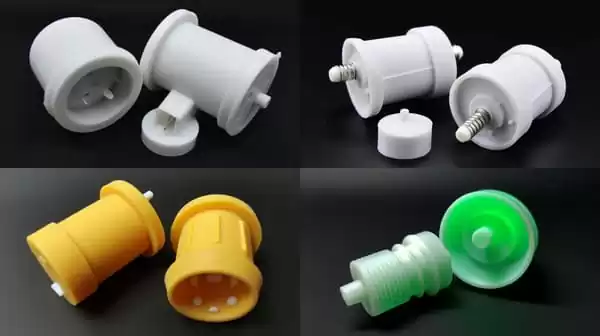
Mieszanki do formowania arkuszy (SMC) i termoplastyczne maty szklane (GMT)
Mieszanki do formowania arkuszy (SMC) i termoplastyczne maty szklane (GMT) są stosowane w formowaniu tłocznym. SMC składa się z matrycy z żywicy termoutwardzalnej, ciętych włókien szklanych i wypełniaczy mineralnych, podczas gdy GMT ma matrycę z żywicy akrylowej z losowo zorientowanymi włóknami szklanymi. Oba materiały oferują doskonałą wytrzymałość, sztywność i stabilność wymiarową po ściśnięciu.
Wybierając materiał do formowania tłocznego, należy wziąć pod uwagę kilka kwestii: pożądane właściwości mechaniczne, efektywność kosztową i wielkość produkcji. Prawidłowy dobór materiału jest kluczem do osiągnięcia pożądanych rezultatów w formowaniu tłocznym.
IV. Rozważania dotyczące projektowania form do formowania tłocznego
Czy jesteś na rynku forma do prasowania? Podczas tworzenia projektu należy wziąć pod uwagę te czynniki.
Kiedy projektowanie formy do formowania tłocznegoProjekt formy ma kluczowe znaczenie dla osiągnięcia sukcesu. Podczas tworzenia projektu należy wziąć pod uwagę wszystkie istotne wymagania; oto kilka kluczowych aspektów, o których należy pamiętać podczas tworzenia tego ważnego kroku:
Projekt gniazda formy i wybór materiału
Podczas projektowania gniazda formy należy wziąć pod uwagę jego kształt i rozmiar. Ponadto należy upewnić się, że zastosowany materiał ma doskonałą przewodność cieplną, a także odporność na zużycie.
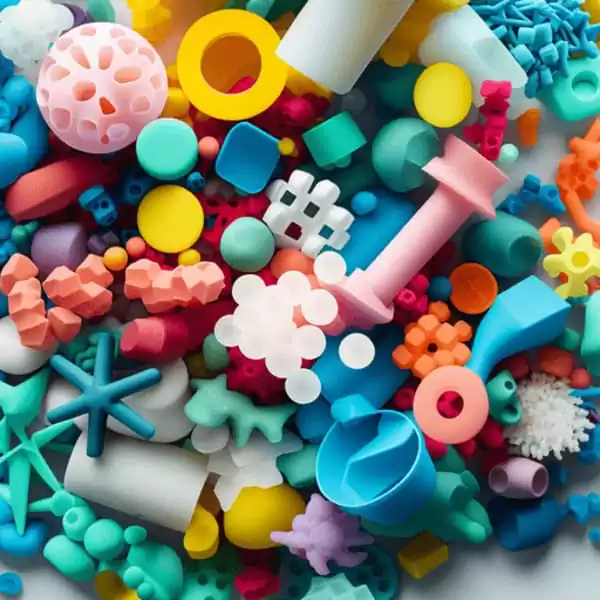
Struktura wewnętrzna formy
Wewnętrzna struktura formy, w tym umiejscowienie i rozmieszczenie otworów wentylacyjnych i zasuw, może wpływać na przepływ materiału podczas formowania. Odpowiednie rozmieszczenie otworów wentylacyjnych i zasuw pomaga zagwarantować równomierną dystrybucję materiału w całej formie.
Temperatura i ciśnienie formy
Temperatura i ciśnienie formowania powinny być dokładnie kontrolowane w zależności od formowanego materiału i złożoności projektu formy. Zarówno temperatura, jak i ciśnienie mają wpływ na właściwości mechaniczne oraz dokładność wymiarową produktu końcowego.
Wykończenie powierzchni i stabilność wymiarowa
Osiągnięcie pożądanej estetyki i wymagań funkcjonalnych wymaga, aby części miały gładkie, błyszczące wykończenie powierzchni. Dlatego ważne jest, aby forma była zaprojektowana tak, aby uzyskać pożądane wykończenie powierzchni. Ponadto należy również zapewnić stabilność formy; wszelkie zmiany wymiarów podczas formowania powinny być zminimalizowane.
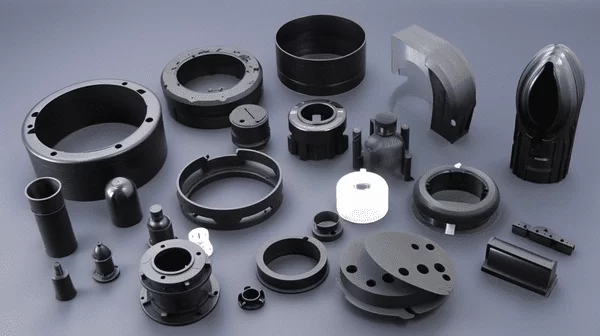
Naprężenia szczątkowe w formowanych częściach
Naprężenia szczątkowe mogą powstawać w formowanych częściach z powodu chłodzenia i utwardzania podczas procesu produkcyjnego. Dlatego projekt formy powinien być zoptymalizowany w celu zminimalizowania tych naprężeń, które mogą negatywnie wpłynąć na właściwości mechaniczne i dokładność wymiarową produktu końcowego.
Odpowiednie uwzględnienie wszystkich tych zmiennych podczas projektowania mieszanki do formowania całych arkuszy jest niezbędne do uzyskania pożądanych właściwości mechanicznych, dokładności wymiarowej i wykończenia powierzchni produktu końcowego.
V. Rola lepkości materiału w formowaniu tłocznym
Definicja lepkości materiału
Lepkość materiału jest krytycznym czynnikiem w formowanie tłoczne proces. Lepkość odnosi się do odporności materiału na płynięcie i odkształcanie pod wpływem przyłożonego naprężenia, a w przypadku formowania tłocznego określa jego zachowanie podczas formowania tłocznego.
Jak lepkość materiału wpływa na formowanie tłoczne
Lepkość materiału ma wpływ na to, jak dobrze wypełnia on gniazdo formy i rozprowadza się w nim. Materiały o wysokiej lepkości wymagają wyższych ciśnień i temperatur do prawidłowego przepływu, podczas gdy materiały o niskiej lepkości przepływają zbyt swobodnie, co prowadzi do wypływania lub zniekształcania materiału. Lepkość ma również wpływ na właściwości mechaniczne oraz dokładność wymiarową produktu końcowego.
Znaczenie wyboru odpowiedniej lepkości dla formowanego materiału
Wybór odpowiedniej lepkości materiału do formowania jest niezbędny do osiągnięcia pożądanych rezultatów. Czynniki takie jak temperatura, ciśnienie i czas utwardzania mogą być regulowane w celu osiągnięcia tej równowagi. Osiągnięcie jednolitego wypełnienia wnęki formy poprzez odpowiednią kontrolę lepkości zapewnia równomierny i wysokiej jakości produkt końcowy.
Wreszcie, lepkość materiału odgrywa kluczową rolę w formowanie tłoczne proces. Odpowiednie zarządzanie i kontrolowanie lepkości materiału pozwala zapewnić spójne i wysokiej jakości wyniki podczas formowania tłocznego.
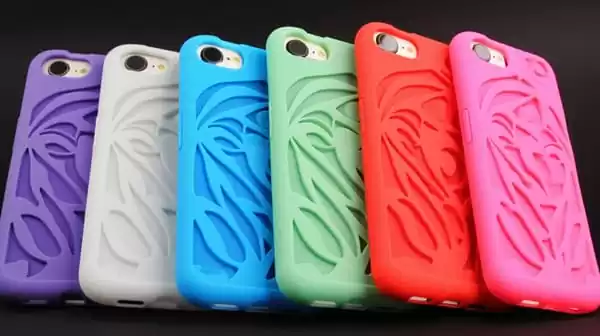
VI. Procesy formowania tłocznego
Formowanie tłoczne to popularna technika produkcji wykorzystywana do tworzenia materiałów kompozytowych o wysokiej wytrzymałości. Istnieją różne procesy formowania tłocznego, takie jak formowanie tłoczne na mokro, formowanie z transferem żywicy (RTM) i formowanie wtryskowe.
Formowanie tłoczne na mokro
Formowanie tłoczne na mokro polega na impregnacji włókien wzmacniających płynną żywicą przed umieszczeniem ich w gnieździe formy. Po zamknięciu, ciśnienie i ciepło są stosowane w celu utwardzenia materiału - jest to skuteczna metoda produkcji wysokowytrzymałych, wysokowydajnych części kompozytowych.
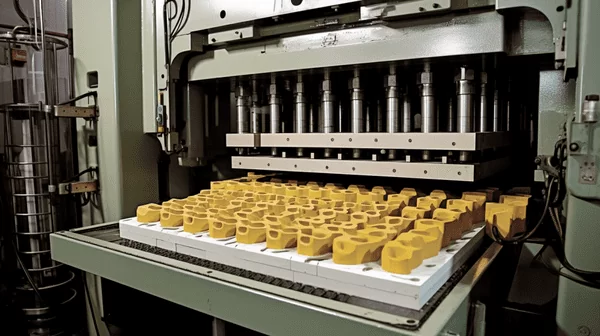
Formowanie z przeniesieniem żywicy (RTM)
RTM to proces polegający na wtryskiwaniu ciekłej żywicy do wnęki formy. Włókna wzmacniające są umieszczane wewnątrz wnęki przed wtryskiem żywicy pod ciśnieniem, aby nasycić je żywicą. Na koniec stosuje się ciepło w celu utwardzenia materiału, dzięki czemu RTM jest popularny do produkcji dużych części kompozytowych o złożonych kształtach.
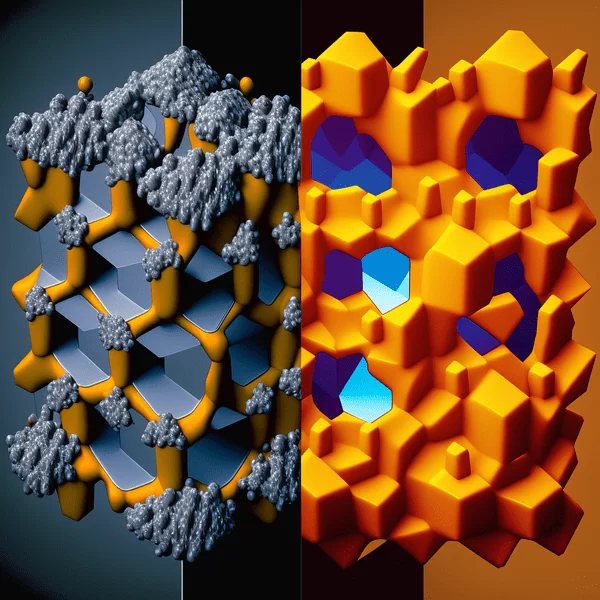
Formowanie wtryskowe
Formowanie wtryskowe polega na wtryskiwaniu materiału termoplastycznego do gniazda formy. Po ostygnięciu i zestaleniu, część może zostać uwolniona. Metoda ta jest idealna do produkcji dużej liczby tanich części o złożonej geometrii.
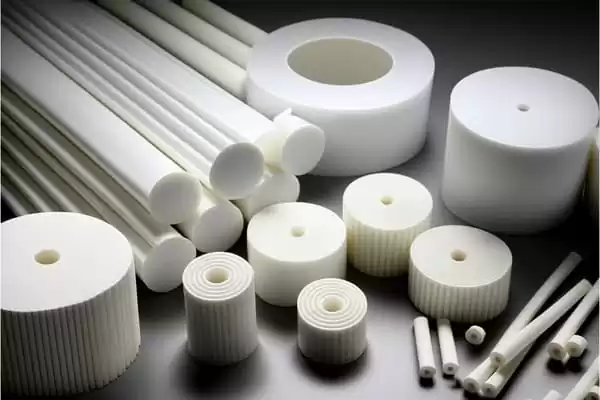
Różnice między formowaniem tłocznym a innymi technikami formowania
Formowanie tłoczne wykazuje pewne podobieństwa do innych technik formowania, takich jak formowanie wtryskowe. Istnieją jednak między nimi kluczowe różnice. Na przykład, formowanie tłoczne wykorzystuje wyższe ciśnienie i temperaturę, co skutkuje materiałami o większej wytrzymałości i sztywności. Ponadto, formowanie tłoczne pozwala na zastosowanie włókien wzmacniających, które dodatkowo poprawiają właściwości materiału.
Ogólnie rzecz biorąc, formowanie tłoczne oferuje wyraźne zalety w porównaniu z innymi procesami formowania, dzięki czemu jest popularnym wyborem do tworzenia materiałów kompozytowych o wysokiej wytrzymałości.
VII. Właściwości mechaniczne części formowanych tłocznie
Części formowane tłocznie mają oczekiwane właściwości mechaniczne, ponieważ ich konstrukcja nie wymaga żadnego wzmocnienia.
Części formowane ciśnieniowo muszą spełniać określone specyfikacje mechaniczne w zależności od składu materiału i zastosowanego wzmocnienia włóknami.
Kompozyty polimerowe są często stosowane w formowanie tłoczneTworzywo to składa się z matrycy z żywicy polimerowej wzmocnionej włóknami, takimi jak szklane, węglowe lub aramidowe. Wzmocnienie włóknami zwiększa wytrzymałość i sztywność materiału, czyniąc go idealnym do zastosowań wymagających wysokiej wydajności mechanicznej.
Procesy formowania tłocznego wykorzystują różne włókna wzmacniające, a ich rodzaj i ilość mają istotny wpływ na właściwości mechaniczne produktu końcowego. Włókna węglowe mogą na przykład wytwarzać materiały o doskonałej wytrzymałości i sztywności, podczas gdy włókna szklane oferują wyższą sztywność, ale niższe poziomy wytrzymałości.
Oprócz wzmocnienia włóknami, polietylen o wysokiej gęstości (HDPE) w formowaniu tłocznym może również poprawić właściwości termiczne materiału. Doskonała przewodność cieplna HDPE pomaga skuteczniej rozpraszać ciepło, tworząc materiały o lepszej stabilności termicznej.
Ogólnie rzecz biorąc, właściwości mechaniczne części formowanych tłocznie zależą od kilku czynników, takich jak skład materiału, rodzaj i ilość użytych włókien wzmacniających oraz dodatków, takich jak HDPE. Osiągnięcie pożądanej wydajności mechanicznej z tych czynników wymaga starannego doboru.
VIII Zastosowania formowania tłocznego
Formowanie tłoczne jest doskonałym narzędziem do tworzenia różnych produktów poprzez wywieranie na nie nacisku.
Formowanie tłoczne to innowacyjny proces produkcyjny o licznych zastosowaniach w różnych branżach i aplikacjach. Typowe przykłady formowania tłocznego obejmują:
Przemysł motoryzacyjny
Formowanie tłoczne jest szeroko stosowane w przemyśle motoryzacyjnym do produkcji elementów silnika i innych złożonych geometrii. Ze względu na wysoką wytrzymałość i sztywność, materiały wytwarzane metodą formowania tłocznego idealnie nadają się do zastosowań, w których wydajność i trwałość są kluczowymi czynnikami.
Zastosowania lotnicze i kosmiczne
Formowanie tłoczne jest często stosowane w przemyśle lotniczym do produkcji lekkich części kompozytowych o wysokiej wytrzymałości. Korzyści kosztowe i szybkie procesy produkcyjne związane z formowaniem tłocznym sprawiają, że jest to pożądana opcja dla producentów z branży lotniczej.
Przemysł medyczny
Formowanie tłoczne jest szeroko stosowane w przemyśle medycznym do produkcji elementów takich jak zatyczki do strzykawek. Dzięki doskonałej precyzji i dokładności wymiarowej, formowanie tłoczne stanowi idealne rozwiązanie do wytwarzania części o wąskich tolerancjach.
Wreszcie, formowanie tłoczne jest szeroko stosowanym procesem produkcyjnym wykorzystywanym w różnych branżach i zastosowaniach. Jego zdolność do wytwarzania materiałów o wysokiej wytrzymałości o złożonej geometrii i wąskich tolerancjach czyni go idealnym dla branż, w których wydajność i trwałość są istotnymi czynnikami.
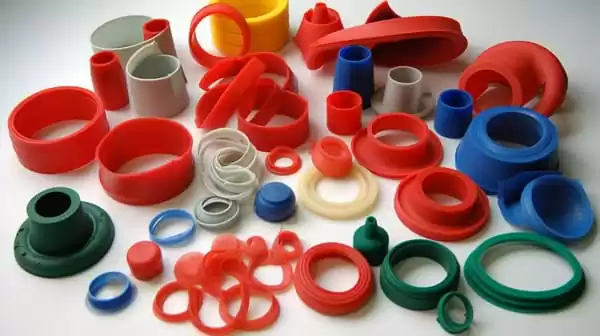
Wnioski
Formowanie tłoczne to rozległy proces produkcyjny wykorzystywany w wielu branżach i zastosowaniach. Wykorzystuje on wysokie ciśnienie i temperaturę do produkcji wytrzymałych materiałów kompozytowych o złożonej geometrii i wąskich tolerancjach.
Lepkość materiału odgrywa znaczącą rolę w formowanie tłoczneponieważ ma ona bezpośredni wpływ na zachowanie przepływu i właściwości mechaniczne produktu końcowego. Osiągnięcie spójnych, wysokiej jakości wyników wymaga odpowiedniej kontroli lepkości materiału podczas formowania tłocznego.
Przyszły rozwój formowania tłocznego będzie obejmował wykorzystanie zaawansowanych materiałów, takich jak nanokompozyty i materiały pochodzenia biologicznego, a także nowych metod produkcji, takich jak produkcja addytywna. Oczekuje się, że innowacje te zwiększą wydajność, efektywność i zrównoważony rozwój w procesie formowania tłocznego.
Ogólnie rzecz biorąc, formowanie tłoczne jest niezawodnym i opłacalnym procesem produkcyjnym o licznych zaletach, takich jak wysoka wytrzymałość i sztywność, złożone geometrie i wąskie tolerancje. Dzięki odpowiedniemu uwzględnieniu wszystkich czynników związanych z formowaniem tłocznym - w tym lepkości materiału - można zapewnić pożądany rezultat i spełnić określone wymagania dla różnych zastosowań.