Wprowadzenie:
Formowanie tłoczne gumy silikonowej jest szeroko stosowanym procesem produkcyjnym, który obejmuje kształtowanie i utwardzanie ciekłej gumy silikonowej we wnęce formy. Ta wszechstronna metoda jest znana ze swojej zdolności do wytwarzania trwałych i odpornych na ciepło produktów. Jednak w przypadku produkcji wielkoseryjnej mogą pojawić się pewne wyzwania, które wymagają starannego rozważenia i strategicznych rozwiązań.
Produkcja wielkoseryjna wiąże się z wyjątkowymi wyzwaniami w zakresie formowania tłocznego gumy silikonowej. Skala i szybkość produkcji mogą wpływać na takie czynniki, jak spójność wypełnienia formy, wydajność cyklu i występowanie wad, takich jak błysk. Wyzwania te mogą utrudniać produktywność, wpływać na jakość produktu i zwiększać koszty produkcji, jeśli nie zostaną odpowiednio rozwiązane.
Sprostanie tym wyzwaniom ma ogromne znaczenie dla udanej produkcji. Rozumiejąc i wdrażając skuteczne strategie, producenci mogą zoptymalizować proces formowania tłocznego, zminimalizować problemy produkcyjne i osiągnąć stałą jakość w produkcji wielkoseryjnej. Gwarantuje to, że produkty spełniają wymagania rynku, są zgodne z rygorystycznymi specyfikacjami i zapewniają niezawodne działanie.
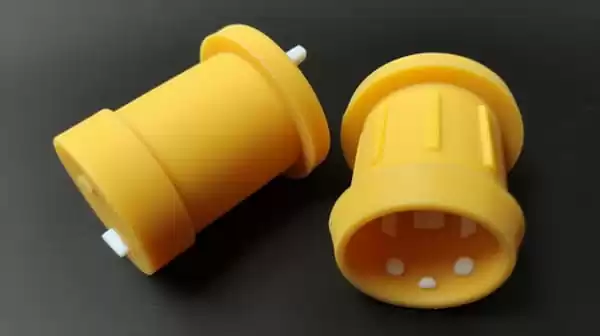
W kolejnych sekcjach zagłębimy się w konkretne wyzwania stojące przed Formowanie tłoczne gumy silikonowej na dużą skalę i poznać cenne wskazówki, jak skutecznie je pokonywać. Stawiając czoła tym wyzwaniom, producenci mogą uwolnić pełny potencjał produkcji wielkoseryjnej i dostarczać wyjątkowe produkty z gumy silikonowej do różnych branż.
Problemy z formowaniem tłocznym:
Formowanie tłoczne, choć jest powszechnie stosowanym procesem produkcyjnym, nie jest pozbawione wyzwań. Producenci często napotykają kilka typowych problemów, które mogą wpływać na wydajność produkcji i jakość produktu. Oto kilka kluczowych kwestii związanych z formowaniem tłocznym:
1. niespójne wypełnienie formy:
Osiągnięcie spójnego wypełnienia formy jest niezbędne do uzyskania jednolicie uformowanych produktów. W produkcji wielkoseryjnej mogą wystąpić różnice w przepływie i dystrybucji materiału, co skutkuje niespójnym wypełnieniem wnęk formy. Może to prowadzić do różnic w wymiarach części, defektów powierzchni i pogorszenia jakości produktu.
2. dłuższy czas cyklu:
W porównaniu z innymi technikami formowania, takimi jak proces formowania wtryskowego, formowanie tłoczne ma zazwyczaj dłuższy czas cyklu. Proces ten obejmuje ściskanie i utwardzanie gumy silikonowej w formie, co może zająć więcej czasu. W produkcji wielkoseryjnejDłuższe czasy cykli mogą ograniczyć ogólną wydajność i spowolnić proces produkcji.
3.Flash Formation:
Flash odnosi się do nadmiaru materiału, który wydostaje się z gniazda formy podczas formowania tłocznego. Występuje z powodu takich czynników, jak niewłaściwa konstrukcja formy, nadmierna ilość materiału lub niewystarczająca siła zacisku. Tworzenie się wypływek nie tylko powoduje marnowanie materiału, ale także wymaga dodatkowej obróbki końcowej w celu usunięcia lub przycięcia nadmiaru materiału. Powoduje to wzrost kosztów produkcji i potencjalne problemy z jakością.
Problemy te mogą znacząco wpływać na wydajność produkcji i jakość produktu w przypadku formowania tłocznego na dużą skalę. Niespójne wypełnienie formy może skutkować częściami o różnych wymiarach i defektach powierzchni, prowadząc do odrzucenia produktów i zwiększenia ilości odpadów. Dłuższe czasy cykli zmniejszają ogólną wydajność produkcji, wpływając na zdolność do sprostania wymaganiom rynku. Tworzenie się wypływek nie tylko zwiększa ilość odpadów materiałowych, ale także wymaga dodatkowego czasu i zasobów na obróbkę końcową, wpływając na ogólną produktywność i opłacalność procesu produkcyjnego.
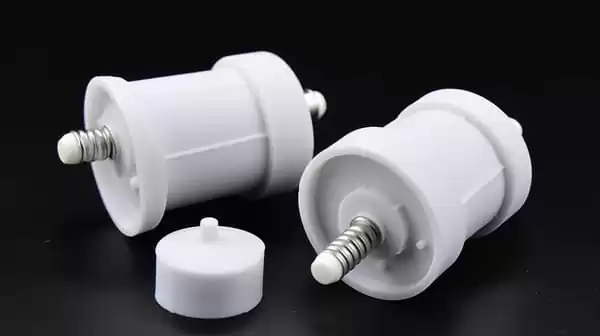
Rozwiązanie tych problemów ma kluczowe znaczenie dla zapewnienia wydajnej i wysokiej jakości produkcji. W poniższych sekcjach przeanalizujemy skuteczne strategie pozwalające sprostać tym wyzwaniom w następujących obszarach Kompresja gumy silikonowej o dużej objętości i formowania wtryskowego. Wdrażając te strategie, producenci mogą zoptymalizować proces, zwiększyć produktywność i dostarczać doskonałe produkty, aby sprostać wymaganiom rynku.
Główna wada formowania tłocznego:
Główną wadą formowania tłocznego, zwłaszcza w scenariuszach produkcji wielkoseryjnej, jest wolniejsza prędkość produkcji w porównaniu z innymi technikami formowania. W przeciwieństwie do szybszych procesów, takich jak formowanie wtryskowe, formowanie tłoczne obejmuje dodatkowe etapy, takie jak przygotowanie materiału, ręczne lub zautomatyzowane ładowanie formy oraz ściskanie i utwardzanie gumy silikonowej. Etapy te przyczyniają się do dłuższych czasów cyklu, co może ograniczać ogólną wydajność produkcji i wpływać na wydajność produkcji wielkoseryjnej.
Konsekwencje wolniejszej prędkości produkcji w formowaniu tłocznym na dużą skalę są znaczące. Po pierwsze, może to utrudniać dotrzymywanie napiętych terminów produkcji i nadążanie za wymaganiami rynku. Dłuższe czasy cyklu związane z formowaniem tłocznym mogą nie być zgodne z pożądanymi szybkościami produkcji potrzebnymi do realizacji dużych zamówień w krótkim czasie. Może to prowadzić do opóźnień w dostawie produktów i potencjalnie wpływać na zadowolenie klientów.
Co więcej, wolniejsze tempo produkcji może mieć konsekwencje finansowe. Produkcja wielkoseryjna często ma na celu osiągnięcie korzyści skali, gdzie większe ilości produkcji pomagają obniżyć koszty jednostkowe. Jednak wolniejsza prędkość formowania tłocznego może zmniejszyć ogólną wydajność, powodując wyższe koszty produkcji na jednostkę. Może to mieć wpływ na rentowność i konkurencyjność na rynku.
Ponadto wolniejsza prędkość produkcji może wpływać na zdolność do szybkiego dostosowywania się do zmian rynkowych lub wprowadzania nowych projektów produktów. W szybko rozwijających się branżach możliwość szybkiego reagowania na potrzeby rynku lub modyfikacje projektu ma kluczowe znaczenie. Czasochłonny charakter formowania tłocznego może ograniczać zwinność i elastyczność produkcji.
Pomimo tej wady, formowanie tłoczne oferuje zalety pod względem wszechstronności, opcji materiałowych i zdolności do obsługi złożonych geometrii części. Jest ono często preferowane w przypadku konkretnych zastosowań, które wymagają unikalnych właściwości lub skomplikowanych projektów. Wdrażając strategie optymalizacji procesu i minimalizacji czasów cykli, producenci mogą złagodzić wpływ wolniejszej prędkości produkcji i zmaksymalizować korzyści płynące z formowania tłocznego w scenariuszach produkcji wielkoseryjnej.
Czynniki wpływające na proces formowania tłocznego:
Kilka kluczowych czynników wpływa na proces formowania tłocznego, odgrywając kluczową rolę w wypełnianiu form, prasowaniu, rozformowywaniu i ogólnej jakości produktu. Zrozumienie i skuteczne zarządzanie tymi czynnikami jest niezbędne do osiągnięcia spójnych i wysokiej jakości wyników. Przyjrzyjmy się tym kluczowym czynnikom:
1. konstrukcja formy:
Konstrukcja formy odgrywa kluczową rolę w formowaniu tłocznym. Czynniki takie jak wnęki formy, systemy kanałów i linie podziału wpływają na przepływ materiału, wypełnienie formy i kompresję części. Dobrze zaprojektowane formy ułatwiają równomierne rozprowadzanie materiału, zapewniając spójne wymiary części i ograniczając występowanie wad.
2.Temperatura formy:
Kontrolowanie temperatury formy ma kluczowe znaczenie w formowaniu tłocznym. Temperatura formy wpływa na przepływ materiału, proces wulkanizacji i właściwości części. Właściwe zarządzanie temperaturą formy zapewnia optymalny przepływ materiału do wnęk formy, promuje równomierne utwardzanie i poprawia właściwości mechaniczne produktu końcowego.
3. siła zacisku:
Odpowiednia siła zacisku ma zasadnicze znaczenie dla osiągnięcia prawidłowego ściskania i konsolidacji części. Niewystarczająca siła zacisku może skutkować niepełnym wypełnieniem i niską jakością części, podczas gdy nadmierna siła może powodować powstawanie wypływek. Staranna kontrola siły zacisku zapewnia równomierne ściśnięcie w gniazdach formy, co prowadzi do uzyskania spójnych wymiarów części i wykończenia powierzchni.
4 Właściwości materiału:
Właściwości gumy silikonowej stosowanej w formowaniu tłocznym mają ogromny wpływ na proces i jakość produktu. Lepkość, czas utwardzania, wysoka konsystencja gumy i właściwości mechaniczne materiału wpływają na wypełnienie formy, przepływ i końcową wydajność części. Wybór właściwego materiału o odpowiednich właściwościach dla danego zastosowania ma kluczowe znaczenie dla osiągnięcia pożądanych rezultatów.
5.Środki antyadhezyjne:
Środki antyadhezyjne są stosowane w celu ułatwienia wyjmowania utwardzonych części z formy. Właściwe zastosowanie środków antyadhezyjnych minimalizuje przywieranie i zapewnia płynne usuwanie części, zmniejszając ryzyko uszkodzeń lub wad podczas wyjmowania z formy.
6. konstrukcja tulei wlewu:
Konstrukcja tulei wlewowej, która łączy formę z jednostką wtryskową, może mieć wpływ na przepływ materiału i wypełnienie gniazd formy. Wydajna konstrukcja tulei wlewowej pomaga kontrolować natężenie przepływu, zapobiegać uwięzieniu powietrza i zapewniać równomierne rozprowadzanie materiału w formie.
Czynniki te wspólnie wpływają na napełnianie formy, prasowanie, rozformowywanie i ogólną jakość produktu w formowaniu tłocznym. Optymalna konstrukcja formy, odpowiednia kontrola temperatury formy, precyzyjne zarządzanie siłą zacisku, odpowiedni dobór materiału, skuteczne stosowanie środków antyadhezyjnych i przemyślana konstrukcja tulei wlewowej przyczyniają się do stałych wymiarów części, zmniejszenia wad i poprawy jakości produktu końcowego.
Rozumiejąc i optymalizując te czynniki, producenci mogą zwiększyć wydajność procesu, osiągnąć pożądane właściwości części i zapewnić udaną produkcję. produkcja wysokiej jakości wyrobów z gumy silikonowej poprzez formowanie tłoczne.
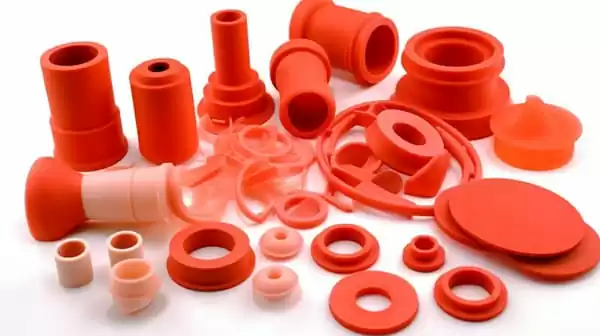
Wady formowania gumy:
Formowanie gumy, w tym proces formowania tłocznego gumy, może być podatne na różne wady, które mogą wpływać na funkcjonalność i wygląd produktu końcowego. Rozwiązanie i zminimalizowanie tych wad ma kluczowe znaczenie dla osiągnięcia wysokiej jakości wyników. Przyjrzyjmy się niektórym typowym wadom związanym z formowaniem gumy:
1.Flash:
Flash odnosi się do nadmiaru materiału, który wydostaje się z gniazda formy podczas procesu formowania. Zwykle występuje na liniach podziału lub w obszarach formy ze szczelinami lub niewspółosiowością. Flash może zagrozić dokładności wymiarowej produktu i skutkować nadmiarem materiału lub niepożądanymi występami na końcowej części. Może to wymagać dodatkowej obróbki końcowej, takiej jak przycinanie lub operacje wtórne, w celu usunięcia wypływki, co zwiększa czas i koszty produkcji.
2. uwięzienie w powietrzu:
Do uwięzienia powietrza dochodzi, gdy powietrze lub gaz zostają uwięzione w formowanej części podczas procesu formowania. Może to być spowodowane niewłaściwym odpowietrzeniem, nieodpowiednią konstrukcją formy lub niewystarczającym wypełnieniem formy. Uwięzienie powietrza może prowadzić do niekompletnego wypełnienia, słabości strukturalnych i powstawania pustych przestrzeni w części. Pustki te mogą wpływać na właściwości mechaniczne, takie jak wytrzymałość lub trwałość produktu końcowego, zagrażając jego funkcjonalności.
3. niedoskonałości powierzchni:
Niedoskonałości powierzchni mogą objawiać się jako zadrapania, skazy, chropowatość lub inne niespójności na powierzchni formowanego produktu. Niedoskonałości te mogą wynikać z takich czynników, jak wady powierzchni formy, słaby przepływ materiału lub nieodpowiednia kontrola temperatury formy. Niedoskonałości powierzchni nie tylko wpływają na estetyczny wygląd produktu, ale mogą również wpływać na jego funkcjonalność, szczególnie w zastosowaniach, w których gładka powierzchnia ma kluczowe znaczenie, takich jak powierzchnie uszczelniające lub kontaktowe.
4. niespójności wymiarowe:
Niespójności wymiarowe odnoszą się do różnic w rozmiarze, kształcie lub grubości formowanej części. Różnice te mogą wynikać z takich czynników, jak niewłaściwe projekt formyNieodpowiednie wypełnienie formy lub nierównomierna kompresja. Niespójności wymiarowe mogą wpływać na dopasowanie, montaż lub wydajność produktu końcowego, utrudniając osiągnięcie precyzyjnych tolerancji lub spełnienie określonych wymagań funkcjonalnych.
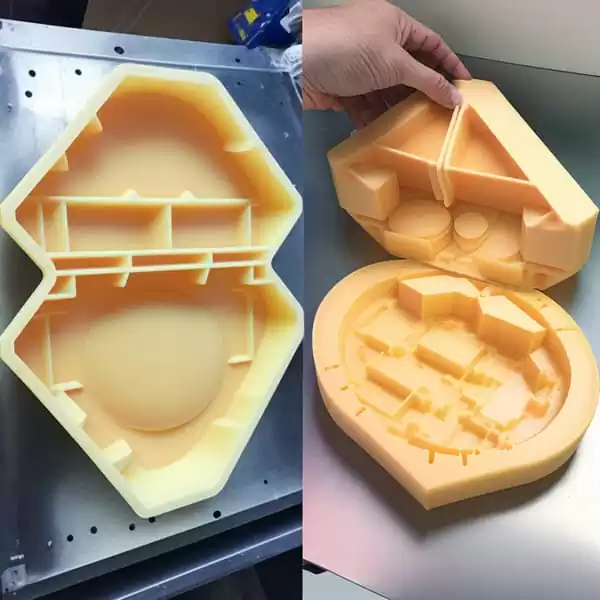
Wady te mogą mieć znaczący wpływ na funkcjonalność i wygląd produktu końcowego. Nadmiar wypływek może prowadzić do niskiej estetyki, zakłócać funkcjonalność produktu lub powodować trudności podczas montażu. Uwięzienie powietrza i puste przestrzenie mogą osłabić integralność strukturalną części, wpływając na jej wytrzymałość lub trwałość. Niedoskonałości powierzchni nie tylko pogarszają atrakcyjność wizualną, ale mogą również wpływać na właściwości funkcjonalne, takie jak tarcie, zdolność uszczelniania lub właściwości kontaktowe. Niespójności wymiarowe mogą utrudniać prawidłowe dopasowanie, kolidować ze współpracującymi częściami lub powodować niewspółosiowość, wpływając na ogólną wydajność lub funkcjonalność produktu.
Wdrażając skuteczny projekt procesu formowania transferowego, optymalizując parametry procesu i wdrażając rygorystyczne środki kontroli jakości, producenci mogą zminimalizować te wady w formowaniu gumy, zapewniając produkty wysokiej jakości, które spełniają pożądane wymagania funkcjonalne i estetyczne.
Strategie pokonywania wyzwań związanych z formowaniem tłocznym gumy silikonowej w dużych ilościach:
Pokonywanie wyzwań związanych z Formowanie tłoczne gumy silikonowej na dużą skalę wymaga systematycznego podejścia i wdrożenia skutecznych strategii. Oto kilka kluczowych strategii pozwalających sprostać tym wyzwaniom:
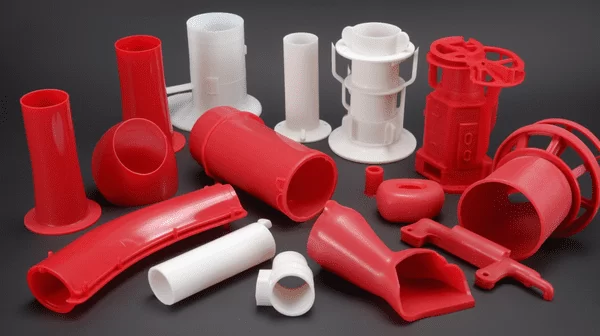
1. spójne wypełnienie formy:
Zoptymalizuj projekt formy, aby zapewnić odpowiednią konstrukcję kanału i systemu wlewowego dla równomiernego przepływu materiału.
Wykorzystanie zaawansowanych technik monitorowania procesu, takich jak wykrywanie ciśnienia i temperatury w czasie rzeczywistym, w celu identyfikacji zmian i wprowadzania niezbędnych regulacji.
Przeprowadzenie analizy przepływu formy w celu optymalizacji projekt formy i zapewnić spójne wypełnienie formy.
2.Efektywne czasy cyklu:
Wykorzystanie zaawansowanego oprogramowania do projektowania form i narzędzi symulacyjnych do identyfikacji potencjalnych wąskich gardeł i optymalizacji projektu formy w celu skrócenia czasu cyklu.
Wybierz wysoką wydajność mieszanki gumy silikonowej specjalnie opracowany do szybkiego utwardzania w celu skrócenia całkowitego czasu cyklu.
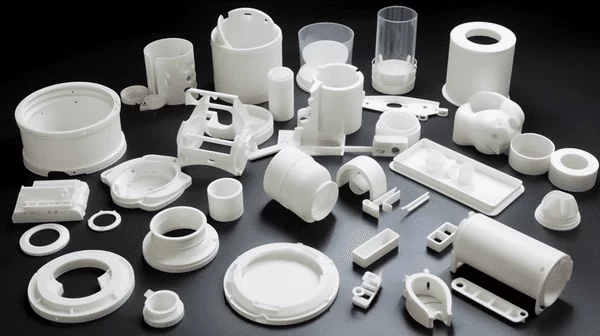
Zoptymalizuj parametry procesu, takie jak temperatura, ciśnienie i czas, aby zminimalizować czas utwardzania i zwiększyć wydajność produkcji.
3. sterowanie lampą błyskową:
Skoncentruj się na odpowiedniej konstrukcji formy i precyzyjnej kontroli siły zacisku, aby zminimalizować powstawanie wypływek.
Wdrożenie kontroli temperatury formy w celu zapewnienia prawidłowego przepływu materiału i zapobiegania nadmiernemu wypływowi.
Należy wdrożyć rygorystyczne środki kontroli jakości, w tym regularne inspekcje i monitorowanie, aby szybko identyfikować i usuwać usterki związane z lampami błyskowymi.
4.Konserwacja formy:
Ustal harmonogram konserwacji zapobiegawczej form, aby zapewnić ich długowieczność i stałą wydajność.
Regularnie czyść formy i używaj odpowiednich środków antyadhezyjnych, aby zapobiec przywieraniu i usprawnić rozformowywanie.
Wdrożenie odpowiednich technik przechowywania form, aby zapobiec uszkodzeniom i zapewnić gotowość form do wydajnej produkcji.
5. jakość materiału:
Ścisła współpraca z renomowanymi dostawcami materiałów w celu zapewnienia spójnego i wysokiej jakości mieszanki gumy silikonowej.
Ustanowienie jasnych specyfikacji i standardów dotyczących właściwości materiałów oraz przeprowadzanie regularnych testów w celu weryfikacji zgodności.
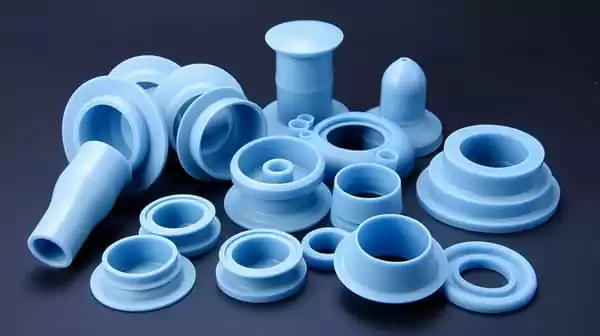
Przeprowadzenie rygorystycznych testów materiałowych w celu zapewnienia przydatności materiału gumowego do zamierzonego zastosowania i zminimalizowania wad.
6 Optymalizacja projektu formy:
Wykorzystanie zaawansowanego oprogramowania do projektowania form i narzędzi symulacyjnych do optymalizacji gniazd form, systemów kanałów i linii podziału w celu zapewnienia wydajnej produkcji i minimalnej ilości odpadów.
Projektowanie form z odpowiednimi systemami wentylacji i zasuw, aby zminimalizować uwięzienie powietrza i zapewnić równomierny przepływ materiału.
Weź pod uwagę takie czynniki, jak temperatura formy, konstrukcja tulei wlewowej i środki antyadhezyjne, aby promować prawidłowy przepływ materiału, wyjmowanie z formy i jakość powierzchni.
7.Monitorowanie i kontrola procesów:
Wdrożenie technik monitorowania procesów w czasie rzeczywistym w celu identyfikacji odchyleń i potencjalnych problemów podczas produkcji.
Regularna kontrola i monitorowanie procesu formowania tłocznego w celu zapewnienia zgodności ze standardami jakości i identyfikacji wszelkich odchyleń lub wad.
Wykorzystanie metod statystycznej kontroli procesu (SPC) do śledzenia i analizowania danych procesowych, umożliwiając proaktywne dostosowanie i ciągłe doskonalenie.
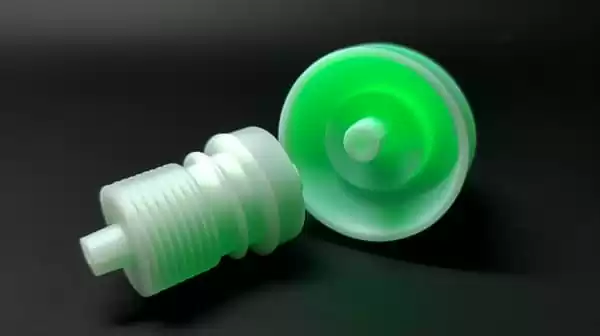
Wdrażając te strategie, producenci mogą sprostać wyzwaniom związanym z Formowanie tłoczne gumy silikonowej na dużą skalę. Konsekwentne wypełnianie form, wydajne czasy cykli, kontrola błysku, konserwacja form i jakość materiałów odgrywają kluczową rolę w osiąganiu pomyślnych wyników produkcyjnych. Optymalizacja projektu formy, monitorowanie procesu i współpraca z renomowanymi dostawcami materiałów przyczyniają się do poprawy wydajności, jakości produktu i opłacalności produkcji.
Wnioski:
Podsumowując, formowanie tłoczne gumy silikonowej na dużą skalę wiąże się z unikalnym zestawem wyzwań, którym należy sprostać, aby produkcja zakończyła się sukcesem. W tym artykule przeanalizowaliśmy te wyzwania i przedstawiliśmy cenne informacje na temat tego, jak skutecznie im sprostać.
Konsekwentne wypełnianie form, wydajne czasy cykli, kontrola wypływu, konserwacja form i jakość materiałów zostały podkreślone jako kluczowe obszary wymagające uwagi. Starannie planując i optymalizując te aspekty, producenci mogą znacznie zwiększyć wydajność i poprawić jakość produktów końcowych.
Sprostanie wyzwaniom związanym z formowaniem tłocznym gumy silikonowej na dużą skalę wymaga systematycznego podejścia i wdrożenia skutecznych strategii. Obejmuje to optymalizację formowania wtryskowego cieczy poprzez projektowanie, wykorzystanie zaawansowanych technik monitorowania procesu, przeprowadzanie regularnych inspekcji i współpracę z renomowanymi dostawcami materiałów.
Przezwyciężając te wyzwania, producenci mogą osiągnąć lepszą produktywność, wyższą jakość produktów i skutecznie sprostać wymaganiom rynku. Może to prowadzić do zwiększenia zadowolenia klientów, wyższej rentowności i przewagi konkurencyjnej w branży.
Podsumowując, staranne planowanie, optymalizacja i wdrażanie tych strategii są kluczowe dla producentów, aby odnieść sukces w formowaniu tłocznym gumy silikonowej na dużą skalę. Poprzez ciągłe ulepszanie i udoskonalanie swoich procesów, producenci mogą uwolnić pełny potencjał tej metody produkcji i dostarczać wyjątkowe produkty z gumy silikonowej, aby zaspokoić różnorodne potrzeby rynku.