Введение:
Компрессионное формование силиконовой резины - это широко распространенный производственный процесс, который включает в себя формование и отверждение жидкой силиконовой резины в полости формы. Этот универсальный метод известен своей способностью производить прочные и термостойкие изделия. Однако, когда речь идет о крупносерийном производстве, могут возникнуть определенные проблемы, требующие тщательного рассмотрения и стратегических решений.
Крупносерийное производство порождает уникальные проблемы при компрессионном формовании силиконовой резины. Масштабы и скорость производства могут влиять на такие факторы, как стабильность заполнения формы, эффективность цикла и возникновение дефектов, таких как вспышки. Эти проблемы могут препятствовать производительности, влиять на качество продукции и увеличивать производственные затраты, если их не решать должным образом.
Решение этих проблем имеет огромное значение для успешного производства. Понимая и внедряя эффективные стратегии, производители могут оптимизировать процесс компрессионного формования, свести к минимуму производственные проблемы и добиться стабильного качества при крупносерийном производстве. Это гарантирует, что продукция будет отвечать требованиям рынка, соответствовать строгим спецификациям и обеспечивать надежную работу.
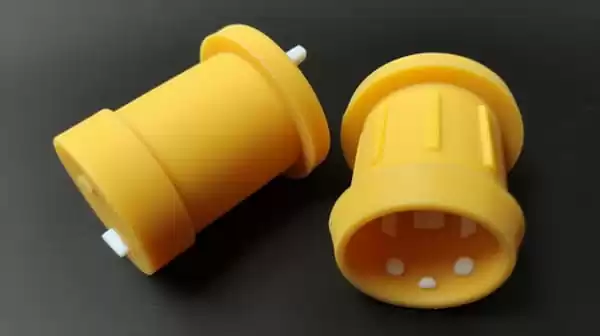
В следующих разделах мы более подробно рассмотрим конкретные проблемы, с которыми приходится сталкиваться в Компрессионное формование силиконовой резины в больших объемах и изучить ценные сведения о том, как их эффективно преодолеть. Решив эти проблемы, производители смогут полностью раскрыть потенциал крупносерийного производства и поставлять исключительные изделия из силиконовой резины в различные отрасли промышленности.
Проблемы компрессионного формования:
Компрессионное формование, хотя и является широко распространенным производственным процессом, не лишено своих проблем. Производители часто сталкиваются с рядом общих проблем, которые могут повлиять на эффективность производства и качество продукции. Вот некоторые ключевые проблемы, связанные с компрессионным формованием:
1. Непостоянное заполнение формы:
Достижение равномерного заполнения пресс-формы необходимо для получения равномерно отформованных изделий. При крупносерийном производстве могут возникать отклонения в подаче и распределении материала, что приводит к неравномерному заполнению полостей пресс-формы. Это может привести к изменению размеров деталей, дефектам поверхности и снижению качества продукции.
2. Более длительное время цикла:
По сравнению с другими методами формования, такими как литье под давлением, компрессионное формование обычно имеет более длительное время цикла. Этот процесс включает в себя сжатие и отверждение силиконового каучука в пресс-форме, что может занять больше времени. При крупносерийном производствеБолее длительное время цикла может ограничить общую производительность и замедлить производственный процесс.
3.Формирование вспышки:
Вспышка - это избыток материала, который выходит из полости формы во время компрессионного формования. Она возникает из-за таких факторов, как неправильная конструкция пресс-формы, чрезмерное количество материала или недостаточное усилие смыкания. Образование вспышек не только приводит к потере материала, но и требует дополнительной постобработки для удаления или обрезки излишков материала. Это приводит к увеличению производственных затрат и потенциальным проблемам с качеством.
Эти проблемы могут существенно повлиять на эффективность производства и качество продукции при крупносерийном компрессионном формовании. Непоследовательное заполнение пресс-формы может привести к получению деталей с различными размерами и дефектами поверхности, что приведет к браку и увеличению отходов. Увеличение времени цикла снижает общий объем производства, что влияет на способность удовлетворить рыночный спрос. Образование вспышек не только увеличивает отходы материала, но и требует дополнительного времени и ресурсов для последующей обработки, что влияет на общую производительность и экономическую эффективность производственного процесса.
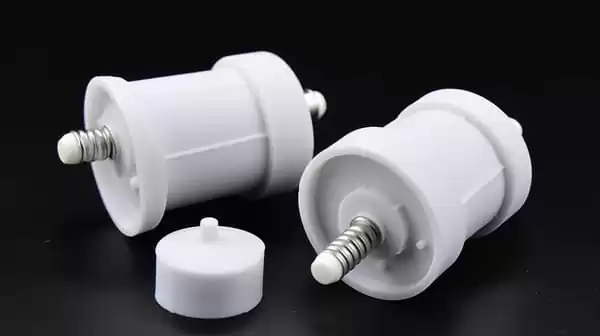
Решение этих проблем имеет решающее значение для обеспечения эффективного и высококачественного производства. В следующих разделах мы рассмотрим эффективные стратегии по преодолению этих проблем в сжатие силиконовой резины в больших объемах и литья под давлением. Внедряя эти стратегии, производители могут оптимизировать процесс, повысить производительность и выпускать превосходную продукцию, отвечающую требованиям рынка.
Основной недостаток компрессионного формования:
Основным недостатком компрессионного формования, особенно в условиях крупносерийного производства, является низкая скорость производства по сравнению с другими методами формования. В отличие от более быстрых процессов, таких как литье под давлением, компрессионное формование включает в себя дополнительные этапы, такие как подготовка материала, ручная или автоматизированная загрузка формы, сжатие и отверждение силиконового каучука. Эти этапы приводят к увеличению времени цикла, что может ограничить общий объем производства и повлиять на эффективность крупносерийного производства.
Снижение скорости производства при крупносерийном компрессионном формовании имеет значительные последствия. Во-первых, это может помешать соблюдению жестких сроков производства и соответствовать требованиям рынка. Более длительное время цикла, связанное с компрессионным формованием, может не соответствовать желаемой скорости производства, необходимой для выполнения крупных заказов в короткие сроки. Это может привести к задержкам в поставке продукции и потенциально повлиять на удовлетворенность клиентов.
Более того, снижение скорости производства может иметь финансовые последствия. Крупносерийное производство часто направлено на достижение эффекта масштаба, когда увеличение объемов производства позволяет снизить затраты на единицу продукции. Однако более низкая скорость компрессионного формования может снизить общий объем производства, что приведет к увеличению производственных затрат на единицу продукции. Это может повлиять на рентабельность и конкурентоспособность на рынке.
Кроме того, более низкая скорость производства может повлиять на способность быстро адаптироваться к изменениям на рынке или внедрять новые модели продуктов. В быстро развивающихся отраслях способность оперативно реагировать на требования рынка или изменения в конструкции имеет решающее значение. Трудоемкость компрессионного формования может ограничивать гибкость и оперативность производства.
Несмотря на этот недостаток, компрессионное формование имеет преимущества в плане универсальности, выбора материалов и возможности обработки деталей сложной геометрии. Оно часто предпочтительно для специфических применений, требующих уникальных свойств или сложного дизайна. Внедряя стратегии по оптимизации процесса и минимизации времени цикла, производители могут смягчить последствия снижения скорости производства и максимально использовать преимущества компрессионного формования в сценариях крупносерийного производства.
Факторы, влияющие на процесс компрессионного формования:
На процесс компрессионного формования влияют несколько ключевых факторов, играющих решающую роль в заполнении формы, сжатии, распалубке и общем качестве продукции. Понимание и эффективное управление этими факторами необходимо для достижения стабильных и высококачественных результатов. Давайте рассмотрим ключевые факторы:
1.Mold Design:
Конструкция пресс-формы играет важную роль в компрессионном формовании. Такие факторы, как полости пресс-формы, системы бегунков и разделительные линии, влияют на поток материала, заполнение пресс-формы и сжатие деталей. Хорошо спроектированные пресс-формы способствуют равномерному распределению материала, обеспечивая стабильные размеры деталей и уменьшая количество дефектов.
2.Температура плесени:
Контроль температуры пресс-формы имеет решающее значение при компрессионном формовании. Температура пресс-формы влияет на поток материала, процесс вулканизации и свойства деталей. Правильное управление температурой пресс-формы обеспечивает оптимальный поток материала в полости формы, способствует равномерному отверждению и улучшает механические свойства конечного продукта.
3.Зажимное усилие:
Соответствующее усилие зажима необходимо для достижения правильного сжатия и консолидации детали. Недостаточное усилие смыкания может привести к неполному заполнению и низкому качеству детали, а чрезмерное усилие - к образованию вспышек. Тщательный контроль усилия смыкания обеспечивает равномерное сжатие по всей полости пресс-формы, что приводит к постоянным размерам деталей и качеству поверхности.
4.Свойства материалов:
Свойства силиконового каучука, используемого при компрессионном формовании, значительно влияют на процесс и качество продукции. Вязкость, время вулканизации, высокая консистенция резины и механические свойства материала влияют на заполнение формы, расход и качество конечной детали. Выбор правильного материала с подходящими свойствами для конкретного применения имеет решающее значение для достижения желаемых результатов.
5.Mold Release Agents:
Разделительные агенты используются для облегчения извлечения затвердевших деталей из формы. Правильное применение разделительных агентов сводит к минимуму прилипание и обеспечивает плавное извлечение деталей, снижая риск повреждения или дефектов во время распалубки.
6.Конструкция втулки для литника:
Конструкция втулки литника, соединяющей пресс-форму с узлом впрыска, может влиять на поток материала и заполнение полостей пресс-формы. Эффективная конструкция втулки литника помогает контролировать скорость потока, предотвращать захват воздуха и обеспечивать равномерное распределение материала в пресс-форме.
Эти факторы в совокупности влияют на заполнение пресс-формы, сжатие, распалубку и общее качество продукции при компрессионном формовании. Оптимальная конструкция пресс-формы, соответствующий температурный контроль, точное управление усилием смыкания, подходящий выбор материала, эффективное использование разделительных средств и продуманная конструкция втулки литника способствуют стабильным размерам деталей, уменьшению дефектов и повышению качества конечной продукции.
Понимая и оптимизируя эти факторы, производители могут повысить эффективность процесса, добиться желаемых свойств деталей и обеспечить успешную производство высококачественных изделий из силиконовой резины с помощью компрессионного формования.
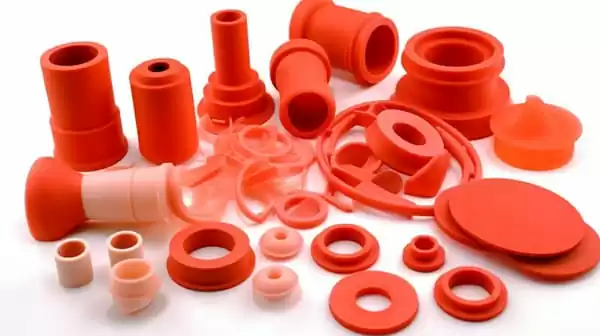
Дефекты резинового литья:
Формование резины, в том числе процесс компрессионного формования, может быть подвержено различным дефектам, которые могут повлиять на функциональность и внешний вид конечного продукта. Устранение и минимизация этих дефектов имеет решающее значение для достижения высококачественных результатов. Давайте рассмотрим некоторые распространенные дефекты, связанные с формованием резины:
1.Flash:
Вспышка - это избыток материала, который выходит из полости формы в процессе формования. Обычно он возникает на линиях разъема или в местах формы с зазорами или несоосностью. Вспышка может нарушить точность размеров изделия и привести к появлению излишков материала или нежелательных выступов на конечной детали. Для устранения вспышки может потребоваться дополнительная обработка, например, обрезка или вторичные операции, что увеличивает время и стоимость производства.
2.Воздушная ловушка:
Захват воздуха происходит, когда воздух или газ оказываются в ловушке внутри формованной детали в процессе формования. Это может быть вызвано неправильной вентиляцией, неадекватной конструкцией формы или недостаточным заполнением формы. Захват воздуха может привести к неполному заполнению, структурным недостаткам и образованию пустот внутри детали. Эти пустоты могут повлиять на механические свойства, такие как прочность или долговечность, конечного изделия, нарушив его функциональность.
3.Поверхностные дефекты:
Несовершенства поверхности могут проявляться в виде царапин, изъянов, шероховатостей или других несоответствий на поверхности формованного изделия. Эти дефекты могут быть вызваны такими факторами, как дефекты поверхности пресс-формы, плохая подача материала или недостаточный температурный контроль пресс-формы. Несовершенство поверхности не только влияет на эстетический вид изделия, но и на его функциональность, особенно в тех случаях, когда гладкая поверхность имеет решающее значение, например, для уплотнения или контактных поверхностей.
4.Несоответствие размеров:
Несоответствие размеров - это отклонения в размере, форме или толщине формованной детали. Эти отклонения могут возникать из-за таких проблем, как неправильное проектирование пресс-формнеадекватное заполнение формы или неравномерное сжатие. Несоответствие размеров может повлиять на посадку, сборку или характеристики конечного продукта, что затрудняет достижение точных допусков или удовлетворение конкретных функциональных требований.
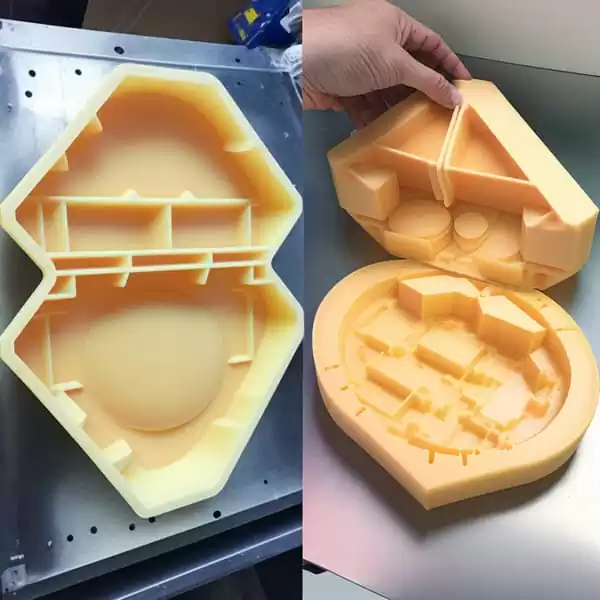
Эти дефекты могут существенно повлиять на функциональность и внешний вид конечного продукта. Излишняя вспышка может привести к ухудшению эстетики, нарушить функциональность изделия или вызвать трудности при сборке. Попадание воздуха и пустоты могут ослабить структурную целостность детали, повлиять на ее прочность или долговечность. Несовершенство поверхности не только ухудшает внешний вид, но и может повлиять на функциональные характеристики, такие как трение, герметичность или контактные свойства. Несоответствие размеров может препятствовать правильной посадке, мешать сопряжению деталей или приводить к перекосам, влияя на общую производительность или функциональность изделия.
Внедряя эффективную схему процесса трансферного формования, оптимизируя параметры процесса и применяя строгие меры контроля качества, производители могут минимизировать эти дефекты при формовании резины, обеспечивая высокое качество продукции, отвечающей необходимым функциональным и эстетическим требованиям.
Стратегии преодоления трудностей при компрессионном формовании силиконового каучука в больших объемах:
Преодоление трудностей Компрессионное формование силиконовой резины в больших объемах требует системного подхода и реализации эффективных стратегий. Вот несколько ключевых стратегий для решения этих проблем:
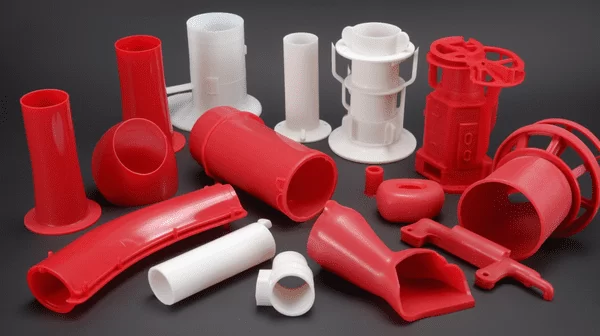
1. Постоянное заполнение формы:
Оптимизация конструкции пресс-формы для обеспечения правильной конструкции бегунов и литниковой системы для равномерного потока материала.
Использование передовых методов мониторинга процесса, таких как измерение давления и температуры в режиме реального времени, для выявления отклонений и внесения необходимых корректировок.
Проведите анализ потока в пресс-форме для оптимизации проектирование пресс-форм и обеспечить равномерное заполнение формы.
2.Эффективное время цикла:
Использование передового программного обеспечения для проектирования пресс-форм и инструментов моделирования для выявления потенциальных узких мест и оптимизации конструкции пресс-формы для ускорения времени цикла.
Выберите высокопроизводительный силиконовые резиновые смеси Специально разработаны для быстрого отверждения, чтобы сократить общее время цикла.
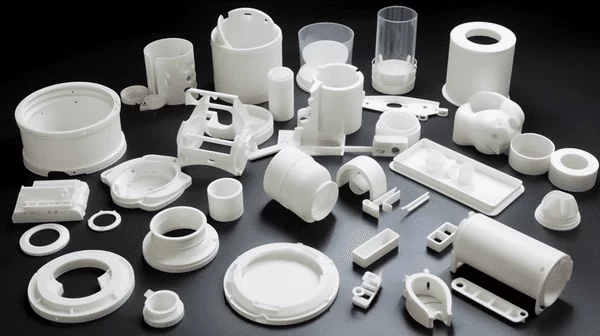
Оптимизируйте параметры процесса, такие как температура, давление и время, чтобы минимизировать время отверждения и повысить эффективность производства.
3.Управление вспышкой:
Сосредоточьтесь на правильной конструкции пресс-формы и точном контроле усилия смыкания, чтобы свести к минимуму образование вспышек.
Обеспечьте контроль температуры в пресс-форме для обеспечения надлежащего потока материала и предотвращения избыточной вспышки.
Применяйте строгие меры контроля качества, включая регулярные проверки и мониторинг, для своевременного выявления и устранения дефектов, связанных со вспышками.
4.Mold Maintenance:
Составьте график профилактического обслуживания пресс-форм, чтобы обеспечить их долговечность и стабильную работу.
Регулярно очищайте формы и используйте соответствующие разделительные средства для предотвращения прилипания и улучшения процесса распалубки.
Применяйте надлежащие методы хранения пресс-форм, чтобы предотвратить их повреждение и обеспечить их готовность к эффективному производству.
5.Качество материала:
Работайте в тесном контакте с авторитетными поставщиками материалов, чтобы обеспечить последовательное и высококачественные силиконовые резиновые смеси.
Установите четкие спецификации и стандарты на свойства материалов и регулярно проводите испытания для проверки их соответствия.
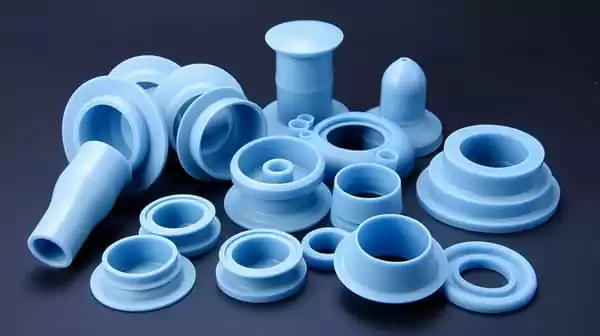
Проведите тщательное тестирование материала, чтобы убедиться в пригодности резинового материала для предполагаемого применения и свести к минимуму количество дефектов.
6.Оптимизация конструкции пресс-формы:
Использование современного программного обеспечения для проектирования пресс-форм и инструментов моделирования для оптимизации полостей пресс-форм, систем обкатки и линий разъема для эффективного производства и минимального количества отходов.
Дизайн форм с надлежащими системами вентиляции и задвижками для минимизации захвата воздуха и обеспечения равномерного потока материала.
Учитывайте такие факторы, как температура пресс-формы, конструкция втулки литника и разделительные средства для пресс-формы, чтобы обеспечить правильную подачу материала, распалубку и качество поверхности.
7.Мониторинг и инспекция процессов:
Внедрение методов мониторинга процессов в режиме реального времени для выявления отклонений и потенциальных проблем в процессе производства.
Регулярно проверяйте и контролируйте процесс компрессионного формования для обеспечения соблюдения стандартов качества и выявления любых отклонений или дефектов.
Использование методов статистического контроля процессов (SPC) для отслеживания и анализа данных о процессах, что позволяет вносить упреждающие коррективы и постоянно совершенствовать их.
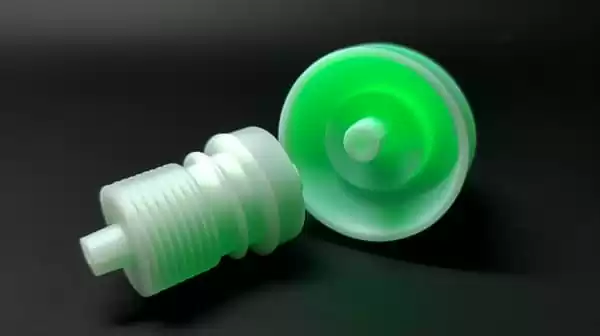
Реализуя эти стратегии, производители смогут преодолеть такие проблемы, как Компрессионное формование силиконовой резины в больших объемах. Последовательное заполнение пресс-формы, эффективное время цикла, контроль вспышек, обслуживание пресс-формы и качество материалов играют жизненно важную роль в достижении успешных результатов производства. Оптимизация конструкции пресс-формы, контроль процесса и сотрудничество с надежными поставщиками материалов способствуют повышению производительности, улучшению качества продукции и экономичности производства.
Заключение:
В заключение следует отметить, что компрессионное формование силиконовой резины в больших объемах представляет собой уникальный набор проблем, которые необходимо решить для успешного производства. В этой статье мы рассмотрели эти проблемы и дали ценные рекомендации по их эффективному решению.
Последовательное заполнение пресс-форм, эффективное время цикла, контроль вспышек, обслуживание пресс-форм и качество материалов были выделены в качестве ключевых областей, требующих внимания. Тщательно спланировав и оптимизировав эти аспекты, производители могут значительно повысить производительность и качество конечной продукции.
Решение проблем, связанных с крупносерийным компрессионным литьем силиконовой резины, требует систематического подхода и реализации эффективных стратегий. Это включает в себя оптимизацию процесса литья под давлением, использование передовых методов мониторинга процесса, проведение регулярных проверок и сотрудничество с надежными поставщиками материалов.
Преодолевая эти трудности, производители могут добиться повышения производительности, улучшения качества продукции и эффективного удовлетворения потребностей рынка. Это может привести к повышению удовлетворенности клиентов, увеличению рентабельности и конкурентному преимуществу в отрасли.
В заключение следует отметить, что тщательное планирование, оптимизация и реализация этих стратегий имеют решающее значение для успеха производителей в области компрессионного формования силиконовой резины в больших объемах. Постоянно улучшая и совершенствуя свои процессы, производители смогут раскрыть весь потенциал этого метода производства и выпускать исключительные изделия из силиконовой резины, отвечающие самым разнообразным потребностям рынка.