Силиконовая резина не имеет запаха и нетоксична, не боится высоких температур и низких характеристик, при температуре 300 градусов Цельсия и минус 90 градусов Цельсия "спокойна", "лицо не меняет цвет", и при этом обладает хорошей прочностью и эластичностью.
Силиконовая резина также обладает хорошей электроизоляцией, кислородостойкостью и устойчивостью к старению, светостойкостью и устойчивостью к старению, а также устойчивостью к плесени, химической стабильностью и т.д.
С момента появления высокотемпературного вулканизированного диметилсиликонового каучука началось стремительное развитие силиконовой резины, производство силиконовой резины широко используется.
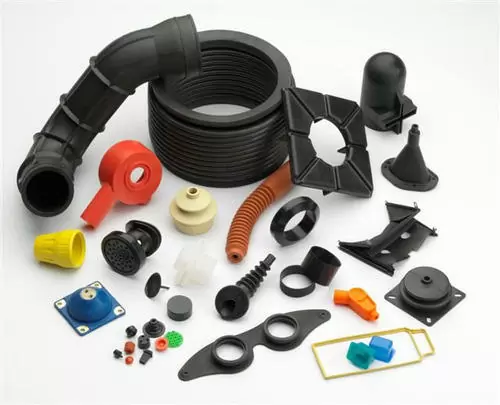
Структурные характеристики и превосходные эксплуатационные качества силиконовой резины
1. Высокая энергия молекулярной связи
Энергия связи C-C составляет 348 КДж/моль; энергия связи Si-O достигает 444 КДж/моль; в то время как энергия ультрафиолетового излучения (300 нм) составляет всего 400 КДж/моль. Молекулярная цепь имеет спиралевидную форму, угол связи силикона больше (130°-160°), а межмолекулярные силы малы.
2. Уникальные свойства силиконовой резины
Отличные погодные характеристики, устойчивость к ультрафиолету, O2, O3, солевому туману и т.д.
Низкая поверхностная энергия, отличные водоотталкивающие свойства и водоотталкивающая миграция.
Отличные изоляционные характеристики и стабильные диэлектрические свойства в широком диапазоне температур и частот. Очень хорошая дугостойкость и сопротивление утечке.
Хорошая устойчивость к высоким температурам может использоваться непрерывно при 180-200℃. Хотя прочность силиконовой резины при комнатной температуре составляет лишь половину от прочности натурального каучука или некоторых синтетических каучуков, в высокотемпературной среде выше 200℃, силиконовая резина может сохранять определенную степень гибкости, упругости и твердости поверхности, при этом механические свойства не претерпевают значительных изменений.
Хорошая эластичность и гибкость при низких температурах, может использоваться при -50 ℃. Температура стеклования силиконовой резины обычно составляет -70~-50℃, а специальная формула может достигать -100℃, что свидетельствует о ее превосходных низкотемпературных характеристиках. Это очень важно для авиационной и аэрокосмической промышленности.
Хорошие огнезащитные свойства, при горении практически не выделяются токсичные и вредные газы. Из него можно изготавливать прозрачные изделия, а такие дефекты, как пузырьки или примеси, легко обнаруживаются при визуальном осмотре.
По сравнению с резиной общего назначения, все три основных типа силиконовой резины имеют относительно простые сопрягаемые компоненты, как и горячая вулканизация.
В дополнение к сырой резине, в состав агента соответствия в основном входит армирующий агент, вулканизирующий агент и некоторые специальные добавки, как правило, всего 5-6 компонентов для формирования практической формулы.
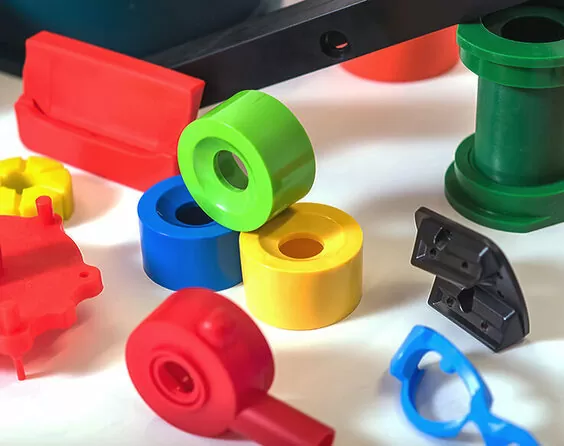
При разработке рецептуры силиконовой резины необходимо учитывать следующие моменты:
(1) Силиконовая резина для высокой насыщенности сырой резины, как правило, не может использовать серу желтой вулканизации, и использование горячей вулканизации.
При горячей вулканизации в качестве вулканизующего агента используется органическая перекись, поэтому резина не должна содержать активных веществ, которые могут взаимодействовать с продуктами разложения перекиси, иначе это повлияет на вулканизацию.
(2) Изделия из силиконовой резины обычно используются при высоких температурах, соединение должно оставаться стабильным при высоких температурах, поэтому в качестве упрочняющих агентов обычно используются неорганические оксиды.
(3) Силиконовая резина в следовых количествах кислоты или щелочи и других полярных химических реагентов легко вызывает расщепление и перестройку силиконовых связей, что приводит к снижению термостойкости силиконовой резины.
Поэтому при выборе сочетающихся агентов необходимо учитывать их кислотность и щелочность, а также принимать во внимание кислотность продуктов разложения перекиси, чтобы не повлиять на характеристики вулканизированной резины.
Выбор сырой резины
При разработке рецептуры необходимо выбрать сырую резину с различными характеристиками в зависимости от производительности и условий использования продукта.
В общем изделия из силиконовой резины Для использования при температуре в диапазоне -70 ℃ ~ 250 ℃, можно использовать виниловую силиконовую резину; при использовании продуктов, требующих более высокой температуры (-90 ~ 300 ℃), можно использовать низкофенильную силиконовую резину; когда продукты требуют высокой и низкой термостойкости и должны противостоять топливу или растворителю, следует использовать фторсиликоновую резину.
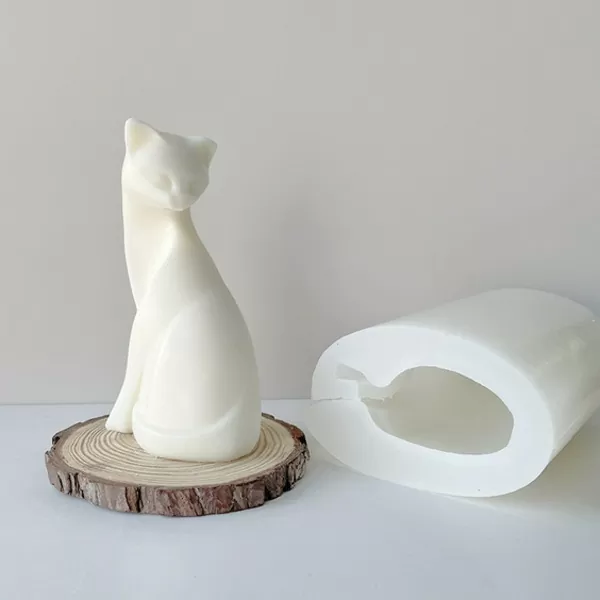
Вулканизирующий агент
Вулканизующий агент, используемый для горячей вулканизации силиконовой резины, в основном состоит из органической перекиси, алифатических азосоединений, неорганических соединений, высокоэнергетических лучей и т.д., из которых наиболее часто используется органическая перекись.
Это связано с тем, что органические пероксиды обычно более стабильны при комнатной температуре, но при более высоких температурах вулканизации могут быстро разлагаться с образованием свободных радикалов, что приводит к сшиванию силиконового каучука.
Пероксиды можно разделить на две категории по степени активности. Один тип - общего назначения, т.е. с высокой активностью, который может быть использован для вулканизации всех видов силиконовая резина; другой тип - винил-специфический, т.е. с низкой активностью, который может быть вулканизирован только для силиконовой резины, содержащей винил.
Помимо вышеперечисленных общих различий между двумя типами пероксидов, каждый пероксид имеет свои особенности. Вулканизующий агент BP - наиболее часто используемый вулканизующий агент для формованных изделий, обладающий высокой скоростью вулканизации и высокой эффективностью производства, но не подходящий для производства толстых изделий.
Вулканизирующий агент DCBP, потому что его продукты не легко улетучиваются, вулканизация без давления также будет производить пузырьки, особенно подходит для прессованных продуктов горячего воздуха непрерывной вулканизации, но его температура разложения низкая, легко вызвать ожог, время хранения резины короткое.
Вулканизирующий агент BP и DCBP представляют собой кристаллический порошок, взрывоопасный, для безопасной работы и подходит для дисперсии, они обычно используются для дисперсии в силиконовом масле или силиконовая резина в прошлом, что общее содержание 50%. Температура кипения вулканизирующего агента составляет 110℃, что является очень летучим.
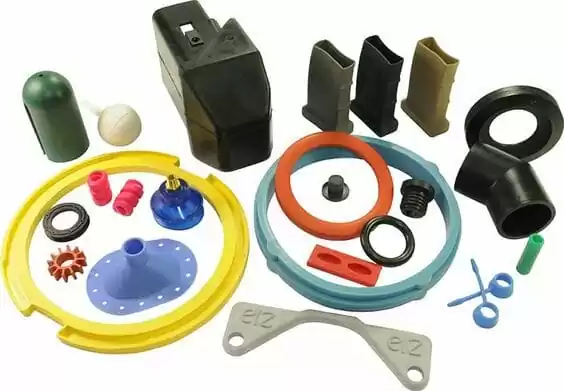
Вулканизующий агент испаряется при хранении каучука при комнатной температуре и лучше всего использовать его в виде молекулярного сита в качестве носителя. Вулканизующий агент DTBP не вступает в реакцию с воздухом или сажей и может использоваться при производстве токопроводящей резины и изделий со сложными операциями формования.
Вулканизующий агент DBPMH аналогичен DTBP, но он не улетучивается при комнатной температуре, а продукты его разложения летучи, что позволяет сократить время второй стадии вулканизации.
Вулканизующий агент DCP не улетучивается при комнатной температуре, обладает характеристиками винила особого типа, при этом летучесть продуктов разложения также низкая, и может использоваться для вулканизации при небольших внешних давлениях. Вулканизующий агент TBPB используется в производстве губчатых изделий.
Количество перекиси зависит от множества факторов. Например, вид сырого каучука, тип и количество наполнителя, технология обработки и т. д. В целом, вулканизирующего агента должно быть как можно меньше, пока можно достичь желаемой сшивки.
Но фактическое количество значительно превышает теоретическое, поскольку необходимо учитывать множество факторов переработки, таких как неравномерное перемешивание, потеря перекиси при хранении резины, вулканизация воздухом и блокирование других компаундов.
Для винила формованные изделия из силиконовой резины с каучуком, различные перекиси общего диапазона весовых частей следующие.
Вес компонента
Тиксотропный агент BP 0,5 ~ 1
Тиксотропное средство DCBP 1~2
Тиксотропное средство DTBP 1~2
Тиксотропный агент DCP 0.5~1
Сернистый агент DBPMH 0.5~1
Тиксотропный агент TBPB 0.5~1
С увеличением содержания винила количество пероксида должно уменьшаться. Количество пероксида в клеевой пасте для прессованных продуктов и клея должно быть выше, чем в формованном клее.
В некоторых случаях использование двух пероксидов позволяет уменьшить количество вулканизирующего агента и соответствующим образом снизить температуру вулканизации, улучшая эффект вулканизации.
Укрепляющее вещество
Прочность неармированной вулканизированной силиконовой резины очень низкая, всего около 0,3 МПа, что не имеет практического значения. Использование соответствующего армирующего агента может довести прочность вулканизированной силиконовой резины до 3,9-9,8 МПа, что чрезвычайно важно для улучшения характеристик силиконовой резины и продления срока службы изделий.
При выборе армирующего наполнителя для силиконовой резины следует учитывать высокотемпературное использование силиконовой резины и вулканизацию перекисью, особенно неблагоприятное воздействие кислотных и щелочных веществ на силиконовую резину.
Первые имеют диаметр 10-50 нм и удельную поверхность 70-400 м²/г, что обеспечивает лучший эффект армирования; вторые - 300-10000 нм, с удельной поверхностью 30 м²/г или меньше, с худшим эффектом армирования.
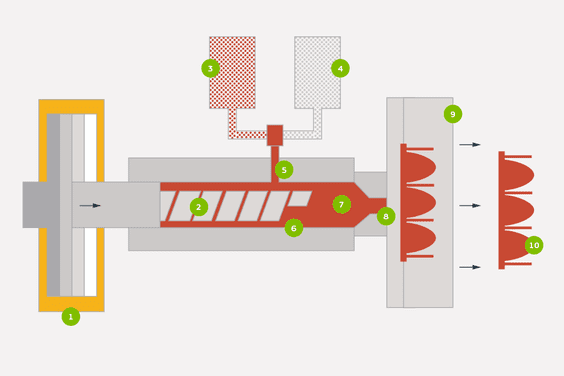
Наполнитель для армирования
(1) Тип и характеристики кремнезема, армирующий наполнитель для силиконовой резины в основном относится к синтетическому кремнезему, также известному как диоксид кремния. Кремнезем подразделяется на расплавленный и осажденный кремнезем.
a. Размер, удельная поверхность, свойства поверхности и структура частиц фумированного диоксида кремния зависят от соотношения сырьевого газа, скорости горения, времени пребывания ядер SiO2 в камере сгорания и других факторов.
Чем мельче частицы фумированного кремнезема, тем больше его удельная поверхность и тем лучше эффект армирования, но хуже эксплуатационные характеристики. Напротив, если его частицы крупнее, а удельная поверхность меньше, эффект армирования плохой, но эксплуатационные характеристики лучше.
Окаменевший диоксид кремния является одним из наиболее часто используемых армирующих агентов для силиконовая резина, а усиленная им резина обладает высокой механической прочностью и хорошими электрическими свойствами вулканизированной резины. Фумированный диоксид кремния также может быть использован с другими армирующими агентами или слабыми армирующими агентами для получения различных требований к использованию резины.
Осажденный диоксид кремния
На характеристики осажденного диоксида кремния влияют такие условия осаждения, как кислотность и температура.
По сравнению с силиконовая резиновая смесь армированного фумированным кремнеземом, механическая прочность компаунда, армированного осажденным кремнеземом, несколько ниже, а диэлектрические свойства, особенно после увлажнения, хуже, но теплостойкие свойства старения лучше, а стоимость компаунда значительно ниже. Если механическая прочность продукта невысока, можно использовать осажденный кремнезем или применять его вместе с фумированным кремнеземом.
Кремнезем можно обработать соответствующими соединениями, чтобы сделать поверхность гидрофобным веществом. Существует два основных метода обработки: в жидкой и газовой фазе.
При жидкофазном методе легко контролировать условия, качество продукта стабильно и эффект обработки хороший, но процесс сложный и растворитель необходимо регенерировать; газофазный метод прост, но качество продукта недостаточно стабильно и эффект обработки плохой.
В качестве агентов для обработки поверхности используются, в принципе, следующие вещества, которые могут взаимодействовать с гидроксильными группами на поверхности кремнезема.
- Спирты
- Хлорсиланы
- Алкоксисилан
- Гексаметилдисилиловый эфир
- Силазан
(2) Механизм упрочнения кремнезема, химия поверхности кремнезема на силиконовая резина. Считается, что существует два следующих вида.
Адсорбция каучука частицами наполнителя адсорбирует полимер, так что сегменты молекулярной цепи каучука непосредственно фиксируются вблизи частиц наполнителя, или ориентируются вдоль поверхности наполнителя, или удерживаются агрегатами наполнителя.
b. Частицы резины и наполнителя в сочетании с частицами наполнителя и сегментами полимерной цепи, объединенными для получения эффективной сшивки и полимерного опутывания частиц наполнителя.
Исходя из двух вышеперечисленных эффектов, диоксид кремния оказывает укрепляющее действие на силиконовый каучук.
Кислотность и щелочность кремнезема зависят от способа его производства. Окуренный диоксид кремния является кислотным, а осажденный диоксид кремния - щелочным.
Значение pH чистого фумированного кремнезема без HCL составляет 6, что обусловлено диссоциацией гидроксильных групп на поверхности кремнезема в воде с образованием H+. Значение pH ниже 4,6 обусловлено наличием HCL, сохранившейся при высокотемпературном гидролизе.
(3) Метод измерения физических и химических свойств диоксида кремния
Физические и химические свойства диоксида кремния напрямую отражают его качество, поэтому очень важно точно измерить различные требования к использованию. В настоящее время показатели зарубежных производителей не одинаковы, но некоторые важные показатели признаны для измерения каждой семьей.
Наиболее важными показателями являются показатели, отражающие первичную структуру, такие как размер и дисперсность частиц, удельная площадь поверхности; показатели, отражающие вторичную структуру, такие как величина поглощения масла и т.д.; показатели, отражающие химический состав поверхности, такие как концентрация различных гидроксильных групп на поверхности и т.д.
Размер частиц и распределение частиц по размерам обусловлены условиями образования и различиями в росте частиц, поэтому диаметр частиц кремнезема не является однородным, обычный диаметр частиц имеет лишь значение среднего статистического показателя.
Определение удельной площади поверхности является показателем размера внешней поверхности порошкового материала, для пористого порошкового материала его удельная площадь поверхности представляет собой сумму площади поверхности и внешней поверхности пор.
Вообще говоря, размер частиц порошкообразного вещества находится в обратной зависимости от его удельной поверхности, поэтому определение удельной поверхности может качественно отразить размер частиц порошка. Поскольку электронный микроскоп имеется не во всех промышленных предприятиях, размер частиц порошка недоступен, поэтому определение удельной площади поверхности имеет важное практическое значение.
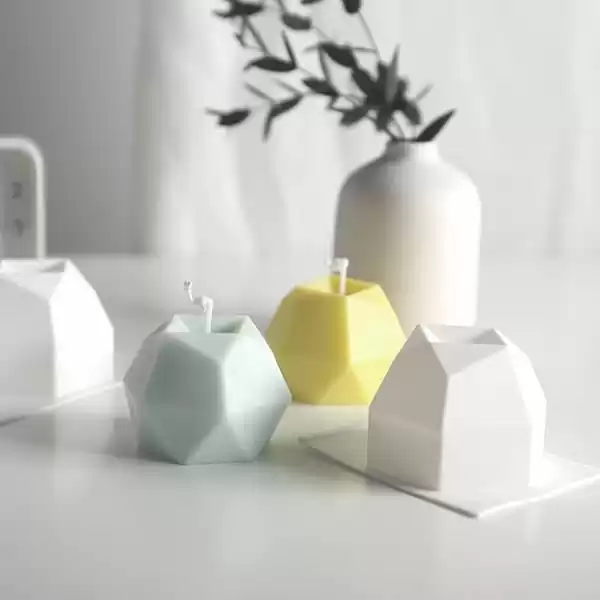
c. Определение поверхностной гидроксильной группы На поверхности кремнезема присутствуют силанольные группы, и многие применения кремнезема напрямую связаны с такими группами, поэтому очень важно количественно определить поверхностную гидроксильную группу.
Данные для определения поверхностной гидроксильной группы кремнезема обычно включают общую гидроксильную группу, соседнюю гидроксильную группу и изолированную гидроксильную группу.
Две последние объединяются на поверхности кремнезема в виде Si-OH, которые в совокупности называются объединенной гидроксильной группой; общая гидроксильная группа представляет собой сумму объединенной гидроксильной группы и гидроксильной группы в молекулах воды, адсорбированных на поверхности кремнезема, и эти данные гидроксильной группы могут быть определены при различных условиях соответственно. Условия измерения следующие.
(1) Гидроксильная группа, измеренная путем прямого отбора проб из мешочка с диоксидом кремния, представляет собой общее количество гидроксила.
(2) Гидроксильная группа, измеренная при сушке диоксида кремния при 110°C в течение 3 часов, является связанной гидроксильной группой.
(3) Гидроксильная группа, измеренная после сушки диоксида кремния при 600°C в течение 3 часов, представляет собой выделенную гидроксильную группу.
(4) Разница между объединенной гидроксильной группой и изолированной группой заключается в соседней гидроксильной группе.
d. Определение вторичной структуры За рубежом принято считать, что степень вторичной структуры напрямую влияет на поведение армирующего наполнителя, поэтому определение вторичной структуры также очень важно.
Но до сих пор не существует хорошего метода определения, наиболее широко используются два метода: первый - определение кажущегося удельного объема при сжатии; второй - определение величины поглощения масла.
Слабо армирующий наполнитель
Слабый армирующий наполнитель можно также назвать инертным наполнителем, только небольшой армирующий эффект на силиконовой резине, они, как правило, не используются в одиночку в силиконовая резинаНо с ролью кремнезема, чтобы отрегулировать твердость силиконовой резины, улучшить процесс производительности резины и вулканизации резины маслостойкость и растворимые свойства, снизить стоимость резины.
В качестве слабых армирующих добавок обычно используются кизельгур, кварцевый порошок, оксид цинка, диоксид титана, силикат циркония, карбонат кальция и т.д.