Введение
Формование силиконовой резины - это стандартный метод, используемый для производства высококачественных резиновых компонентов для самых разных изделий - от уплотнений и прокладок до сложных медицинских инструментов и автомобильных компонентов. Компрессионное формование выделяется среди различных методов формования как основной метод производства высококачественных силиконовых резиновых сильфонов и диафрагм.
Сильфоны и диафрагмы - важнейшие компоненты в различных отраслях промышленности, от здравоохранения до автомобилестроения и аэрокосмической промышленности, используемые для регулирования давления, контроля жидкости и гашения вибраций. Компрессионное формование оказалось эффективным процессом для массового производства этих деталей с неизменным качеством при соблюдении строгих допусков. В этой статье мы рассмотрим этот метод применительно к сильфонам и диафрагмам из силиконовой резины, его преимущества и недостатки, а также различные формы, используемые в процессе формования. формование резины компрессионным формованием процессы.
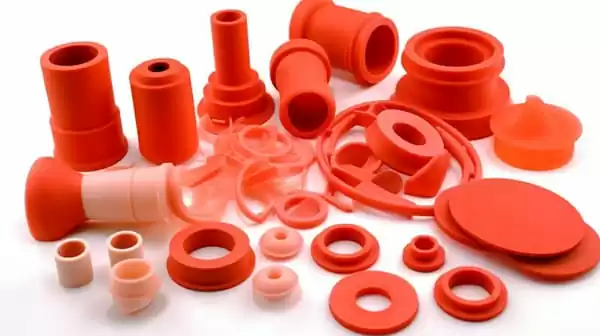
Процесс компрессионного формования силиконовой резины
Производство компрессионного формования Процесс, при котором нагретый материал из силиконовой резины помещается в полость формы под высоким давлением и сжимается до тех пор, пока не примет форму предполагаемой полости формы. После отверждения при определенной температуре в течение определенного периода времени форма открывается и извлекается, чтобы освободить деталь для де-формовки.
Компрессионное формование силиконовой резины имеет множество преимуществ, включая производство больших объемов продукции с неизменным качеством и допусками, которые соответствуют или превосходят спецификации заказчика, экономичность при небольших объемах производства, универсальность при использовании жидких силиконовых каучуков для производства сложных геометрических форм с жесткими допусками, а также широкий выбор материалов, которые позволяют использовать их в процессе компрессионного формования силикона.
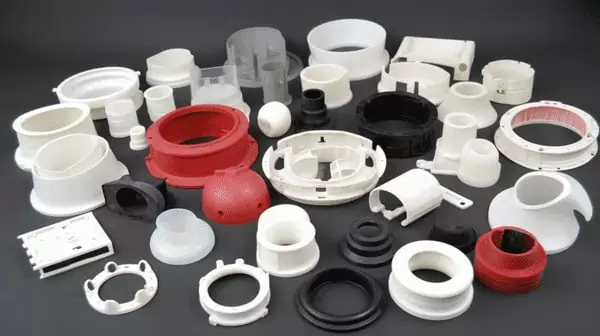
Однако у компрессионного формования есть и свои недостатки. Например, оно может занимать много времени и сил по сравнению с литьем под давлением; кроме того, контроль процесса отверждения может оказаться сложным; в результате избыточного процесса отверждения может потребоваться обрезка лишнего материала с готовых изделий. Тем не менее компрессионное формование остается популярным выбором, когда производство формованных резиновых деталей на заказ например, сильфоны и диафрагмы для колоколов или диафрагм.
Пригодность компрессионного формования для сильфонов и диафрагм
Компрессионное формование - идеальный метод для производства сильфонов и диафрагм из силиконовой резины, благодаря его способности производить детали с неизменно высоким качеством и жесткими допусками. Кроме того процесс компрессионного формования позволяет изготавливать детали различной толщины со сложной геометрией, что очень важно при производстве сильфонов и диафрагм.
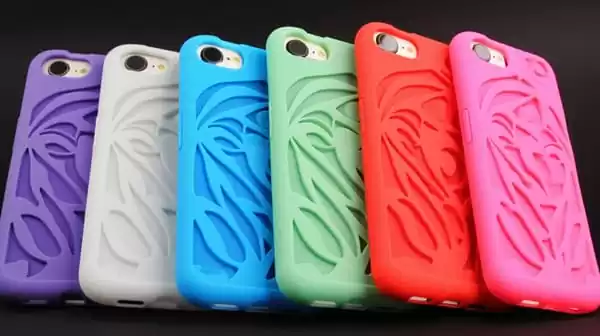
Компрессионное формование обладает рядом преимуществ по сравнению с другими методами формования, такими как литье под давлением или трансферное формование, например, литье под давлением. Компрессионное формование лучше подходит для производства деталей с более толстыми стенками или сложной формы, чем его конкуренты, такие как литье под давлением или трансферное формование; кроме того, благодаря более низким требованиям к объему производства оно позволяет более экономно использовать материальные ресурсы, чем его альтернативы.
С другой стороны, литье под давлением идеально подходит для крупносерийного производства и создания деталей с очень тонкими стенками или сложными деталями. Кроме того, этот процесс намного быстрее по сравнению с компрессионным формованием, в результате чего образуется меньше отходов, а детали в целом производятся быстрее. Трансферное формование обладает преимуществами обеих технологий, но требует более сложного оборудования и оснастки.
Компрессионное формование остается более экономичным решением для производства высококачественных сильфонов и диафрагм из силиконовой резины, особенно при небольших объемах производства с деталями различной толщины или сложной геометрии.
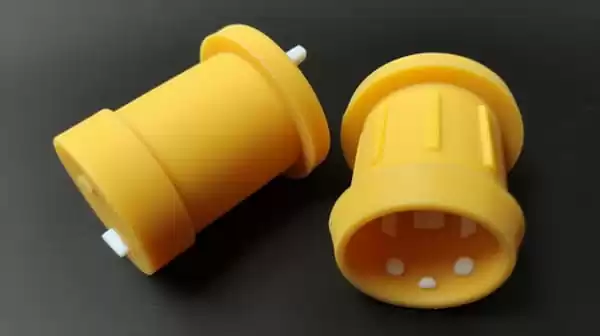
Типы пресс-форм для компрессионного формования
Существуют различные пресс-формы для компрессионного формования. производить высококачественные детали из силиконовой резины например, сильфоны и диафрагмы, в том числе сильфонные. Некоторые из наиболее часто используемых пресс-форм включают:
Открытые пресс-формы: Эти формы являются самыми простыми в использовании и состоят из двух плоских пластин, расположенных вместе для образования полости, внутри которой могут быть изготовлены детали с равномерной толщиной и легким извлечением из формы. Открытые пресс-формы хорошо подходят для производства простых деталей с равномерной толщиной, требующих быстрой расформовки.
Закрытые формы: Закрытые пресс-формы предназначены для производства более сложных деталей с неоднородной толщиной и сложной геометрией, например, деталей из нетканых материалов или сложных пластиковых форм. Они состоят из нескольких пластин, предназначенных для открытия и закрытия по определенным схемам, чтобы получить желаемые формы.
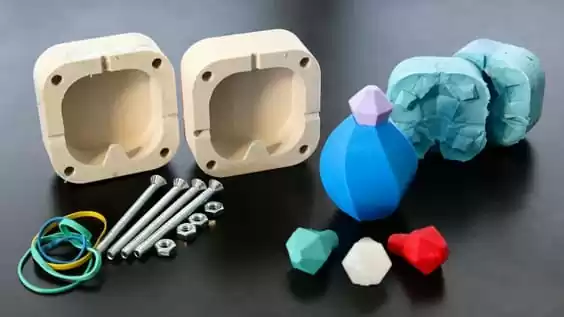
Компрессионные формы для переноса: Компрессионные пресс-формы напоминают традиционные закрытые пресс-формы, в которых материал перемещается между полостями во время формования; эти пресс-формы могут помочь в создании деталей с переменной толщиной или содержанием материала, а также в применении оверфолдинга.
Выбор материала пресс-формы и конструктивных особенностей зависит от ряда факторов, включая сложность детали, используемый материал, требуемый объем производства и желаемый объем производства. Обычно для изготовления пресс-форм используются такие материалы, как алюминий, сталь и эпоксидная смола, каждый из которых обладает своими преимуществами и недостатками, такими как стоимость, долговечность и простота обработки.
При проектировании пресс-форм для компрессионного формования из силиконовой резины учитываются углы осадки, толщина стенок и расположение затвора. Углы вытяжки должны быть достаточными для легкого извлечения пресс-формы, а толщина стенок должна оставаться равномерной для поддержания постоянного качества деталей. Расположение затвора играет важную роль в управлении потоком материала в полость формы, чтобы избежать образования воздушных карманов или дефектов, которые могут ухудшить качество детали.
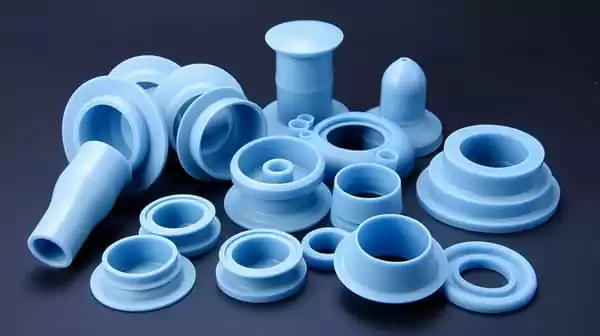
Выбор подходящего компрессионное формование Жидкость для литья под давлением и материал - неотъемлемые составляющие производства высококачественных деталей из силиконовой резины, таких как сильфоны и диафрагмы, с учетом простоты и последовательности производства. Необходимо также учитывать конструктивные особенности, чтобы гарантировать стабильное качество деталей и снизить затраты на производство.
Материалы, используемые для компрессионного формования
Силиконовая резина - это чрезвычайно гибкий синтетический эластомерный материал, обычно используемый в компрессионном формовании для производства сильфонов и диафрагм. Будучи синтетическим эластомером, силиконовая резина обладает рядом уникальных характеристик, включая теплостойкость, химическую стойкость и электроизоляционные свойства, не говоря уже о том, что она может быть разных цветов и уровней твердости для производственных целей.
Силиконовая резина имеет множество преимуществ перед другими эластомерными материалами, такими как натуральный каучук и EPDM, включая термостойкость, которая достигает 200 градусов Цельсия. Кроме того, химическая стойкость делает ее идеальной для применения при высоких температурах, поскольку она устойчива к кислотам, щелочам и другим потенциально агрессивным веществам.
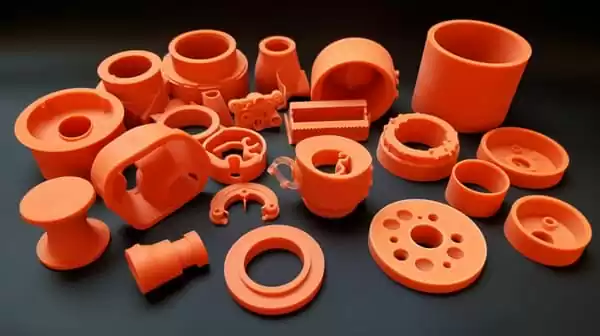
Натуральный каучук более экономичен, поэтому его обычно предпочитают использовать в тех случаях, когда стоимость является главным фактором. Он обладает отличной эластичностью и стойкостью к истиранию, что делает его пригодным для изготовления шин и уплотнений; однако из-за низкой химической и температурной стойкости это может ограничить его применение в некоторых областях.
EPDM - еще один широко используемый эластомер с отличной погодоустойчивостью и гибкостью при низких температурах, часто встречающийся в автомобильных приложениях, таких как накладки и прокладки. К сожалению, EPDM не обладает высокой термостойкостью и химической стойкостью по сравнению со своим аналогом из силиконового каучука и не может выдерживать температуру выше 140 F в течение длительного времени.
В целом, силиконовая резина остается привлекательным материалом для компрессионного формования благодаря своим уникальным свойствам и универсальности; однако выбор материала в конечном итоге зависит от индивидуальных потребностей и критериев эффективности.
Процесс производства сильфонов и диафрагм для компрессионного формования
Производство сильфонов и диафрагм методом компрессионного формования требует множества этапов: от разработки и подготовки формы, выбора материала, процессов формования и отверждения и, наконец, снятия формы.
Проектирование и подготовка пресс-форм: Чтобы начать процесс литья, сначала необходимо разработать форму в соответствии с предпочтительной формой сильфона или диафрагмы. Форма должна соответствовать толщине, форме, любым вырезам и особенностям детали, а также быть чистой и смазанной для обеспечения бесперебойного процесса формовки.
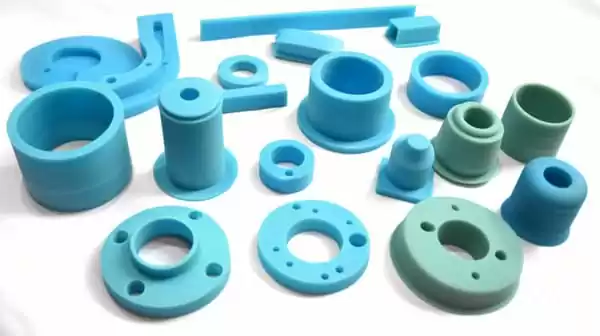
После выбора детали необходимо выбрать подходящий материал, например силиконовый каучук, жидкий силиконовый каучук или другие эластомеры, а затем смешать с ними любые добавки и красители, необходимые для придания нужных свойств.
Формование и отверждение: После помещения в полость формы материал сжимается под высоким давлением с помощью гидравлического пресса, а затем нагревается до идеальной температуры для длительного отверждения - это обеспечивает ему все желаемые свойства, такие как гибкость и твердость, - перед выпуском в производство.
Де-молдинг: После того как деталь застынет, форму следует открыть и извлечь из нее деталь. Излишки материала необходимо обрезать, а окончательные штрихи, такие как текстурирование поверхности или покраска, можно нанести по желанию.
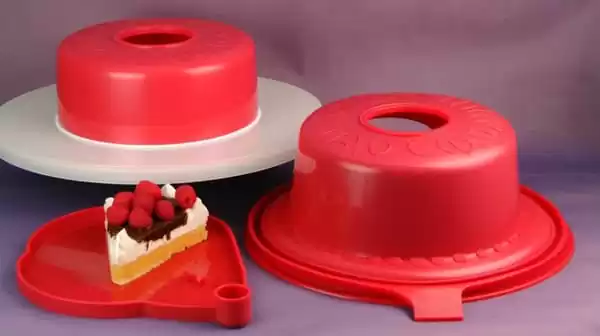
Компрессионное формование может быть рассчитано как на малые, так и на большие объемы производства, причем ручные прессы обычно служат для малых объемов, в то время как автоматические прессы могут быть более подходящими для больших объемов. Требования вашего проекта и объемы деталей определят, какой пресс подойдет.
Компрессионное формование сильфонов и диафрагм включает в себя несколько ключевых этапов, начиная с проектирования и подготовки пресс-формы, выбора и смешивания материалов, формования, отверждения, снятия формы и формовки. Она может применяться как для малосерийного производства, так и для крупносерийного, в котором используются детали с переменной толщиной или сложной геометрией.
Области применения сильфонов и диафрагм, изготовленных методом компрессионного формования
Сильфоны и мембраны, изготовленные методом литья под давлением, являются неотъемлемыми компонентами во многих отраслях, включая здравоохранение, автомобилестроение, аэрокосмическую промышленность и промышленное производство. Они используются для регулирования давления, управления жидкостями и гашения вибраций.
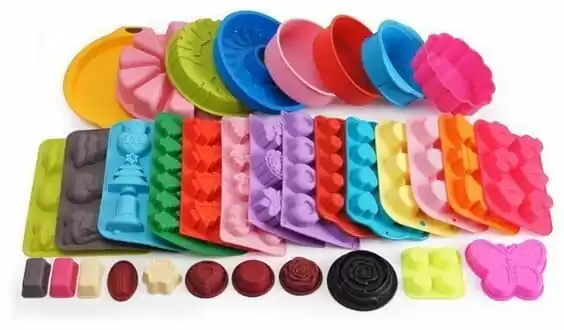
Сильфоны и мембраны, изготовленные методом литья под давлением, широко используются в медицинской промышленности, часто в качестве компонентов таких устройств, как молокоотсосы, ингаляторы и шприцы. Мембраны для молокоотсосов, изготовленные из силиконовой резины, должны выдерживать многократное использование, а также регулярные процессы очистки, не разрушаясь со временем.
В автомобильной промышленности сильфоны и диафрагмы, изготовленные методом компрессионного формования, широко используются в таких компонентах, как топливные насосы, тормозные системы и системы управления двигателем. Мембранные клапаны также играют важную роль в управлении потоками жидкостей и газов в автомобильной среде.
Сильфоны и мембраны, изготовленные методом литья под давлением, являются неотъемлемой частью многих аэрокосмических компонентов, таких как системы кондиционирования воздуха и топливные системы, и изготавливаются из таких материалов, как силиконовый каучук или EPDM, чтобы выдерживать экстремальные условия, связанные с космическими путешествиями.
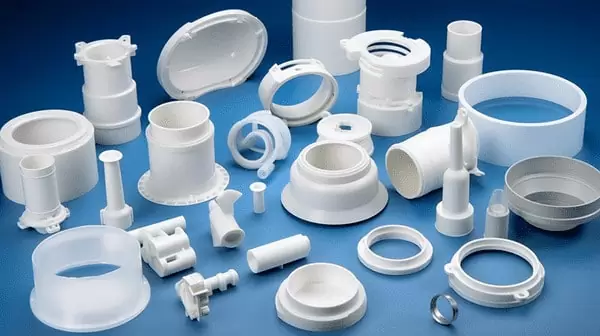
Сильфоны и мембраны, изготовленные методом компрессионного формования, находят широкое применение в промышленном производстве: от насосов и датчиков давления до регуляторов давления и литой резины и сапог, защищающих оборудование от пыли и мусора, изготовленных по технологии компрессионного формования.
Сильфоны и мембраны, изготовленные методом литья под давлением, играют незаменимую роль во многих отраслях промышленности и сферах применения, обеспечивая высокое давление, регулируя поток жидкости и гася вибрации - ключевые характеристики, необходимые для эффективной и бесперебойной работы систем.
Преимущества компрессионного формования сильфонов и диафрагм
Компрессионное формование обладает многочисленными преимуществами при производстве высококачественных сильфонов и диафрагм, в том числе:
Высокое качество: Компрессионное формование позволяет получить детали с неизменным качеством и точными допусками благодаря использованию технологий формования под высоким давлением и равномерному распределению материала в процессе формования.
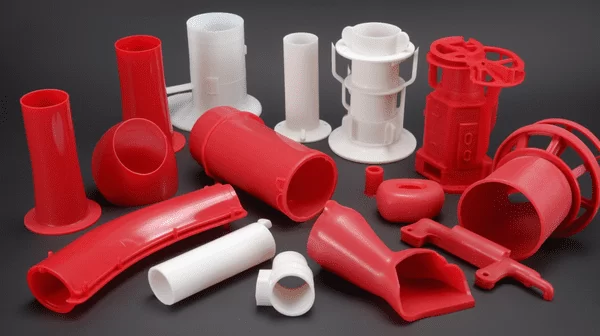
Компрессионное формование обеспечивает жесткий контроль допусков, что гарантирует неизменный уровень точности и аккуратности каждой изготовленной детали.
Экономичность: Компрессионное формование - это экономичный вариант для малосерийного производства, поскольку не требует дорогостоящего оборудования для литья под давлением или большого количества материала.
При компрессионном формовании могут использоваться различные материалы, в том числе жидкая силиконовая резина. Это позволяет производителям изготавливать детали со сложной геометрией и жесткими допусками.
По сравнению с методами литья под давлением и трансферного формования, компрессионное формование имеет ряд неоспоримых преимуществ перед ними. Оно идеально подходит для производства деталей с более толстыми стенками и сложной формы, а его малосерийное производство не требует дорогостоящего оборудования и больших объемов материала.
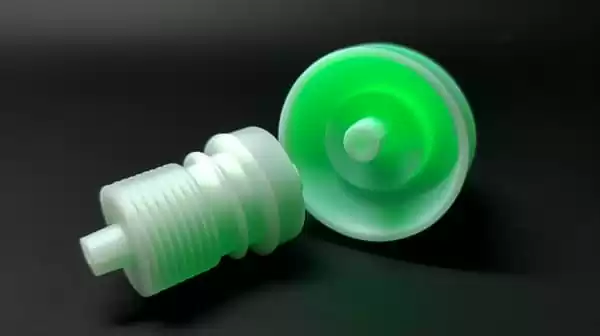
С другой стороны, литье под давлением идеально подходит для крупносерийного производства, поскольку позволяет получать детали с очень тонкими стенками и сложными деталями. Кроме того, этот процесс быстрее, чем компрессионное формование, и дает меньше отходов; трансферное формование сочетает в себе элементы обеих технологий, но требует более сложного оборудования и оснастки для реализации.
Компрессионное формование остается эффективным средством производства сильфонов и диафрагм высшего качества благодаря постоянному производству с жестким контролем допусков.
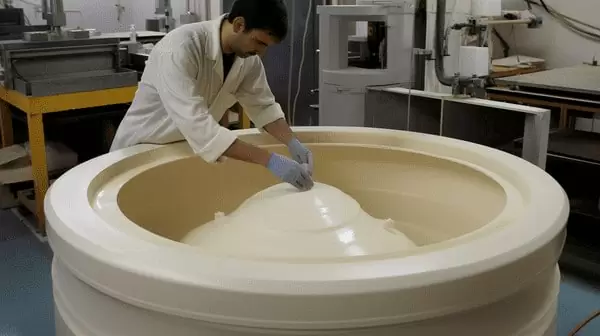
Заключение
Компрессионное формование является незаменимым методом производства высококачественных сильфонов и диафрагм из силиконовой резины, обеспечивающим стабильное качество с жесткими допусками - важный фактор при производстве деталей, требующих жесткого контроля качества.
Компрессионное формование может быть экономичным решением для малосерийного производства и быстрого создания прототипов. Оно позволяет использовать различные материалы, в том числе жидкий силиконовый каучук, а также изготавливать детали со сложной геометрией и жесткими допусками.
В целом, компрессионное формование это надежный и гибкий способ производства высококачественных сильфонов и диафрагм, используемых в таких отраслях, как медицина, автомобилестроение и аэрокосмическая промышленность. Благодаря своей способности стабильно производить высококачественные детали при низких затратах, компрессионное формование предоставляет производителям идеальный способ производство компонентов из силиконовой резины при жестком контроле допусков, оставаясь при этом экономически эффективными.