Введение
Дизайн пресс-форм играет жизненно важную роль в производстве высококачественных изделий из силиконовой резины. Формы, используемые для придания формы силиконовой резине, напрямую влияют на ее конечное качество, функциональность и эффективность; оптимизация конструкции форм становится все более важной, поскольку изделия из силиконовой резины продолжают набирать популярность во многих отраслях промышленности.
Изделия из силиконовой резины пользуются большим спросом благодаря своим замечательным свойствам, таким как термостойкость, гибкость и долговечность. Силиконовая резина находит применение во многих отраслях, таких как автомобилестроение, электроника, медицинское оборудование и производство потребительских товаров - ее универсальность и надежность делают ее востребованным материалом для производителей, стремящихся создавать инновационные и высокопроизводительные продукты.
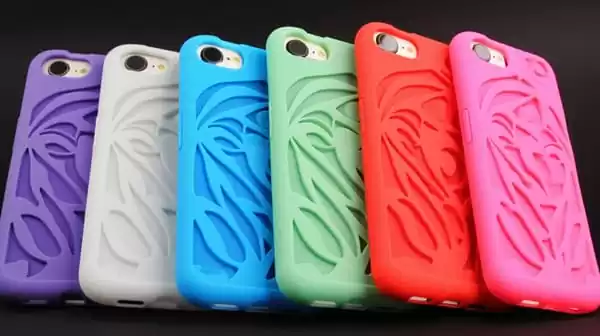
Оптимизированные конструкции пресс-форм могут помочь производителям раскрыть весь потенциал силиконовой резины и удовлетворить растущие требования потребителей к качеству продукции, поскольку они обеспечивают эффективный поток материала, уменьшают количество дефектов и гарантируют стабильное качество деталей. Оптимизация конструкции пресс-формы не только обеспечивает более высокую производительность, но и способствует успеху и конкурентоспособности на рынке.
II. Понимание процессов формования жидкого силиконового каучука (LSR)
A. Определение литья LSR как процесса литья под давлением изделий из силиконовой резины
Литье LSR (или литье жидкой силиконовой резины) - это технология литья под давлением, используемая для производить изделия из силиконовой резины. Технология предполагает впрыскивание жидкого силиконового каучука под высоким давлением и температурой в полости пресс-формы для достижения желаемой формы и свойств. Литье LSR имеет ряд преимуществ перед обычным литьем под давлением, таких как высокая точность, отличное качество деталей и возможность получения сложных геометрических форм.
В начале процесса создается жидкий силиконовый каучук, обычно состоящий из двух компонентов - базового силиконового полимера и катализатора/сшивателя, - смешанных в точных пропорциях для получения желаемых свойств материала и характеристик полимеризации.
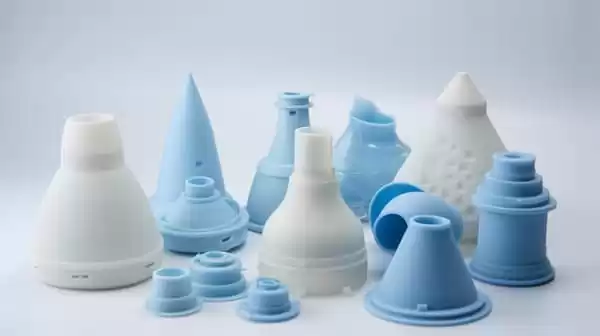
Жидкий силиконовый каучук подается в машину для литья под давлением, состоящую из нагреваемого ствола, шнекового или плунжерного механизма для подачи материала и полости формы. Здесь материал нагревается, а затем под высоким давлением вдавливается в нужную форму и полость формы.
После того как жидкая силиконовая резина была закачана в форму, она должна пройти процесс полимеризации, в ходе которого может использоваться как нагрев, так и охлаждение для обеспечения надлежащей полимеризации и затвердевания материала. После этого форму можно открыть и извлечь из нее затвердевшую часть силиконовой резины.
B. Обзор машины для литья под давлением и ее роль в процессе
Термопластавтомат является важнейшим компонентом в Процесс формования LSR. Он состоит из нескольких ключевых элементов, которые облегчают впрыск и формовку жидкой силиконовой резины в желаемое изделие. Ниже представлен обзор основных компонентов и их функций:
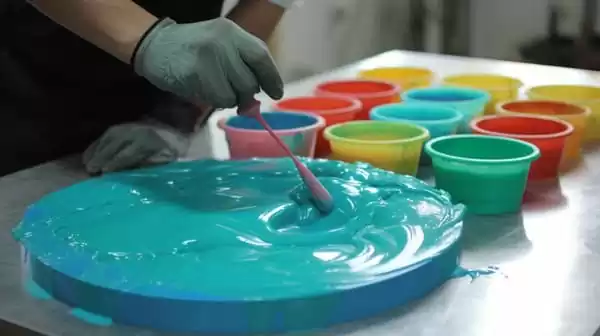
1.Ствол и винтовой/плунжерный механизм:
В бочке находится жидкий силиконовый каучук, который нагревается до контролируемой температуры. Затем шнек или плунжерный механизм перемещается вперед, чтобы впрыснуть материал в полость формы.
2.Mold Cavity:
Полость формы - это полое пространство в форме, которое определяет конечную форму изделия из силиконовой резины. Она предназначена для размещения желаемой геометрии, характеристик и размеров детали.
3.Системы отопления и охлаждения:
Машина для литья под давлением включает в себя системы нагрева и охлаждения, которые регулируют температуру формы. Нагрев необходим для облегчения течения материала и его полимеризации, а охлаждение помогает затвердеть детали из силиконовой резины для извлечения.
4.Зажимное устройство:
Зажимное устройство удерживает половинки пресс-формы вместе во время процесса впрыска, обеспечивая правильное выравнивание и предотвращая утечку материала. Он прикладывает необходимое усилие для удержания пресс-формы закрытой во время впрыска и открытой для выталкивания детали.
Термопластавтомат обеспечивает точный контроль над скоростью впрыска, давлением, температурой и другими параметрами процесса, обеспечивая постоянный производство и высококачественные изделия из силиконовой резины.
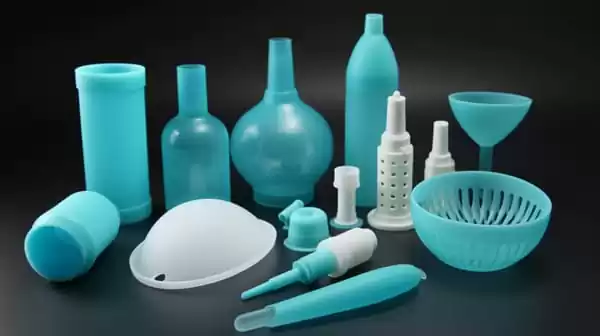
III. Ключевые соображения при оптимизации конструкции пресс-формы
A. Важность понимания требований к продукту для успешного проектирования пресс-формы
Чтобы оптимизировать конструкцию пресс-формы для изделий из силиконовой резины, очень важно иметь полное представление о требованиях к изделию. Сюда входят такие факторы, как размеры, сложность, обработка поверхности и функциональные характеристики. Понимая эти требования, производители могут адаптировать конструкцию пресс-формы для удовлетворения конкретных потребностей, обеспечивая производство высококачественных изделий из силиконовой резины, соответствующих ожиданиям клиентов.
B. Проектирование для удобства формования: избегайте сложных геометрических форм, острых углов и подрезов
Проектирование изделий из силиконовой резины с учетом удобства формования является важным условием успешной оптимизации конструкции пресс-формы. Рекомендуется избегать сложных геометрических форм, острых углов и подрезов, поскольку они могут создавать трудности при формовании и влиять на качество деталей. Вместо этого следует использовать плавные изгибы и углы вытяжки, чтобы облегчить процесс распалубки и обеспечить надлежащий поток материала в полости формы.
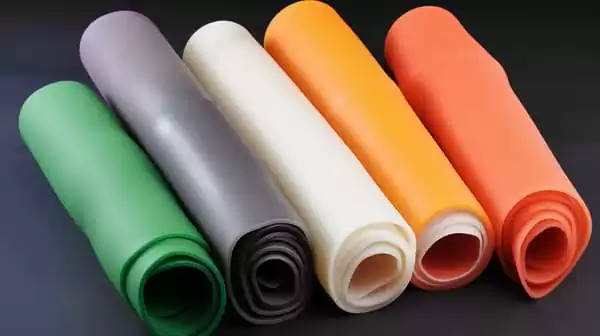
C. Учет толщины стенок и влияние на качество деталей и поток материала
Правильная толщина стенок имеет решающее значение для достижения оптимальной конструкции пресс-формы. Поддержание постоянной и соответствующей толщины стенок по всему изделию из силиконовой резины обеспечивает равномерное отверждение и предотвращает такие проблемы, как воздушные ловушки или ограничения потока материала. Отклонения в толщине стенок могут привести к изменению качества деталей, включая такие дефекты, как коробление или раковины. Тщательный учет толщины стенок в процессе проектирования необходим для достижения равномерного качества деталей и потока материала.
D. Методы вентиляции и дегазации для эффективного выпуска воздуха и газов во время отверждения
Эффективное удаление воздуха и дегазация имеют решающее значение для оптимизации конструкции пресс-формы для изделий из силиконовой резины. Наличие вентиляционных отверстий в пресс-форме позволяет задержанному воздуху или газам выходить во время процесса вулканизации. Правильная вентиляция предотвращает образование дефектов, таких как воздушные пузырьки или пустоты, которые могут нарушить целостность изделия. Тщательное размещение вентиляционных отверстий в местах возможного скопления воздуха или газов обеспечивает эффективный отвод воздуха и оптимальное отверждение.
E. Конструкция системы охлаждения и ее влияние на время цикла и стабильность размеров
Эффективная конструкция системы охлаждения необходима для оптимизации конструкции пресс-формы и достижения более короткого времени цикла и стабильности размеров при производстве изделий из силиконовой резины. Правильное охлаждение помогает контролировать процесс вулканизации, уменьшать усадку деталей и поддерживать точность размеров. Стратегическое размещение каналов охлаждения в пресс-форме, а также соответствующие охлаждающие среды обеспечивают равномерное охлаждение и эффективный отвод тепла. Хорошо продуманные системы охлаждения повышают производительность, минимизируют время вулканизации и способствуют стабильному качеству деталей.
Учитывая эти ключевые факторы в процессе оптимизации конструкции пресс-формы, производители могут добиться оптимальной конструкции пресс-формы, которая приведет к получению высококачественных изделий из силиконовой резины. Эти факторы, включая требования к изделию, формоустойчивость, толщину стенок, вентиляцию и охлаждение, играют важную роль в повышении качества деталей, эффективности производства и удовлетворенности клиентов.
IV. Передовые методы оптимизации конструкции пресс-форм
A. Формование со вставками и его преимущества для встраивания дополнительных компонентов или вставок
Формование со вставками - это передовая техника, используемая при оптимизации конструкции пресс-форм для изделий из силиконовой резины. Она предполагает размещение дополнительных компонентов или вставок в полости формы перед впрыском жидкой силиконовой резины. Преимущества формования со вставками включают:
Повышенная функциональность деталей: Формование со вставками позволяет интегрировать функциональные компоненты, такие как металлические вставки или электрические разъемы, непосредственно в деталь. изделие из силиконовой резины. Это повышает производительность и функциональность изделия.
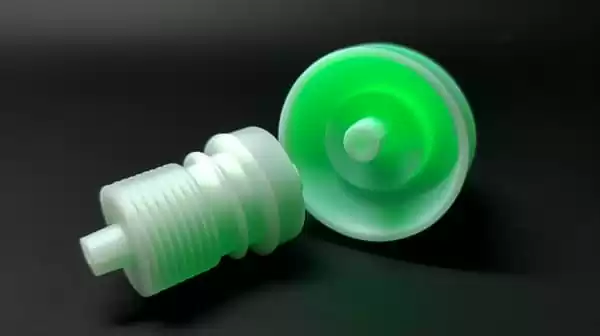
Повышенная прочность и стабильность деталей: Благодаря надежному соединению вставок с силиконовой резиной формование со вставками повышает структурную целостность и стабильность конечного продукта. Оно устраняет необходимость во вторичных процессах сборки, снижая затраты и потенциальные точки отказа.
Гибкость конструкции: Формование со вставкой обеспечивает гибкость конструкции, позволяя создавать изделия сложной геометрии и из нескольких материалов. Оно позволяет комбинировать различные материалы с разными свойствами, расширяя спектр применения изделий из силиконовой резины.
B. Использование инструментов моделирования и анализа конечных элементов (FEA) для повышения точности проектирования
Средства моделирования и конечно-элементный анализ (КЭА) являются мощными инструментами для оптимизации конструкции пресс-форм. Они помогают повысить точность проектирования, спрогнозировать расход материала, выявить потенциальные дефекты и оптимизировать технологические параметры. Используя инструменты моделирования и FEA, производители могут:
Визуализация и анализ схемы заполнения: Инструменты моделирования обеспечивают визуальное представление того, как жидкая силиконовая резина течет в полости пресс-формы. Это позволяет выявить потенциальные проблемы, связанные с потоком, такие как воздушные ловушки, недостаточное заполнение или чрезмерный сдвиг материала.
Оптимизируйте расположение и размеры затворов: Инструменты моделирования помогают определить оптимальное расположение и размеры затворов для точек впрыска. Это обеспечивает надлежащий поток материала, минимизирует дефекты, связанные с потоком, и повышает качество деталей.
Прогнозирование усадки и коробления деталей: FEA может предсказать усадку и коробление детали, что позволяет скорректировать конструкцию для минимизации этих проблем. Это обеспечивает точность размеров и снижает вероятность возникновения деформаций после формовки.
C. Учет подрезов, линий раздела и поверхностей раздела
При оптимизации конструкции пресс-формы для изделий из силиконовой резины необходимо учитывать факторы, связанные с подрезами, линиями раздела и поверхностями раздела. К этим факторам относятся:
- Подрезы: Подрезы - это особенности или углубления в геометрии изделия, которые затрудняют извлечение деталей. Инновационные методы конструирования пресс-форм, такие как разборные стержни или механические направляющие, могут быть использованы для приспособления к подрезам и успешной распалубки.
- Линии разъема: Линии раздела - это места соприкосновения половинок пресс-формы, в результате чего на готовом изделии образуется видимая линия. Необходимо тщательно продумать расположение линий раздела, чтобы минимизировать их влияние на косметический вид и функциональность изделия.
- Разделительные поверхности: Разделительные поверхности - это поверхности формы, разделяющие половинки формы. Обеспечение гладких и точных поверхностей раздела помогает достичь правильного выравнивания и предотвращает образование вспышек в процессе литья силикона.
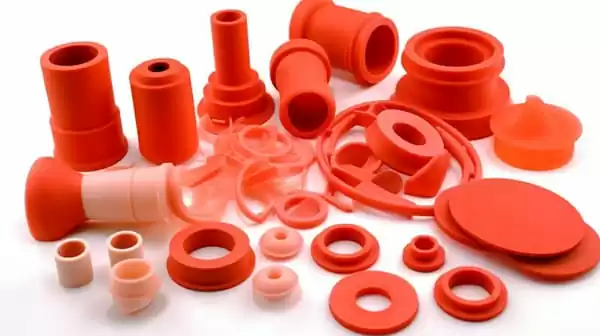
D. Оптимизация температуры пресс-формы, давления впрыска и давления в полости для обеспечения стабильного качества
Оптимизация температуры пресс-формы, давления впрыска и давления в полости имеет решающее значение для достижения стабильного качества изделий из силиконовой резины. К ключевым моментам относятся:
- Температура пресс-формы: Правильный контроль температуры пресс-формы влияет на расход материала, время отверждения и стабильность размеров. Оптимизация температуры пресс-формы обеспечивает стабильное качество деталей и минимизирует колебания механических свойств.
- Давление впрыска: Давление впрыска влияет на поток материала, заполнение и воспроизведение особенностей формы. Оптимизация давления впрыска позволяет полностью заполнить полость формы без чрезмерной нагрузки на форму или деталь.
- Давление в полости: Контроль давления в полости в процессе формования помогает обеспечить стабильное качество деталей и точность размеров. Он позволяет в режиме реального времени корректировать параметры впрыска, оптимизируя производственный процесс.
Применяя эти передовые методы оптимизации конструкции пресс-формы, производители могут повысить функциональность, качество и эффективность изделий из силиконовой резины. Вставка
V. Преимущества литья LSR для изделий из силиконовой резины
A. Преимущества материалов LSR, включая широкий диапазон механических свойств
Литье LSR предлагает ряд преимуществ для изделий из силиконовой резины, в первую очередь благодаря уникальным свойствам материалов из жидкой силиконовой резины. К этим преимуществам относятся:
- Широкий диапазон механических свойств: Материалы LSR могут иметь широкий спектр механических свойств, включая различные уровни твердости, гибкости и эластичности. Это позволяет производителям адаптировать материал для удовлетворения специфических требований к продукции в различных отраслях промышленности.
- Термостойкость и долговечность: Материалы LSR обладают превосходной термостойкостью и долговечностью, что делает их пригодными для применения в условиях высоких температур, жесткой окружающей среды или частого использования. Они могут выдерживать экстремальные температуры, не нарушая своей целостности.
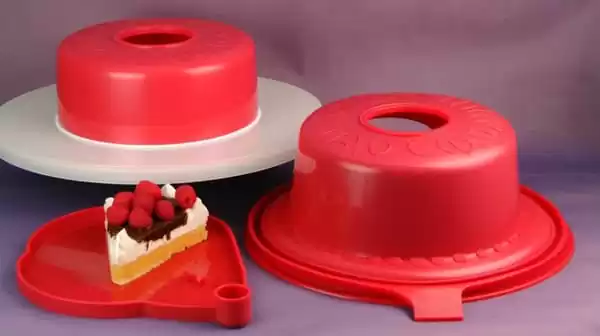
B. Улучшенный косметический вид и более гладкие поверхности по сравнению с обычным формованием
Формование из LSR обеспечивает превосходный косметический вид и более гладкие поверхности по сравнению с традиционными методами формования. Это объясняется уникальными характеристиками жидкой силиконовой резины, такими как низкая вязкость и самовыравнивающиеся свойства. Преимущества включают в себя:
- Устранение поверхностных дефектов: Материалы LSR легко поступают в полость формы, обеспечивая равномерное распределение и сводя к минимуму появление поверхностных дефектов, таких как следы раковин, линии растекания или дефекты поверхности.
- Улучшенная эстетика деталей: Литье LSR позволяет с высокой точностью воспроизводить сложные детали и мелкие элементы, в результате чего получаются визуально привлекательные изделия. Гладкие поверхности, полученные в результате формования LSR, способствуют общему косметическому совершенству деталей из силиконовой резины.
C. Возможности массового производства и пригодность для различных отраслей промышленности
Литье LSR очень подходит для массового производства производство изделий из силиконовой резины. К преимуществам относятся:
- Сокращение времени цикла: Материалы LSR быстро отверждаются, что позволяет сократить время цикла формования по сравнению с другими процессами формования резины. Это позволяет повысить эффективность производства и увеличить объем выпускаемой продукции.
- Последовательность и повторяемость: Формование LSR обеспечивает последовательное и повторяемое производство изделий из силиконовой резины, гарантируя однородность размеров, свойств и качества деталей. Это очень важно для отраслей, где требуется крупносерийное производство с минимальными отклонениями.
- Широкое применение: Формование из LSR применимо в различных отраслях промышленности, включая автомобилестроение, электронику, здравоохранение и потребительские товары. Оно отвечает самым разнообразным требованиям к продукции, начиная от медицинских компонентов и заканчивая промышленными уплотнениями, прокладками и бытовой электроникой.
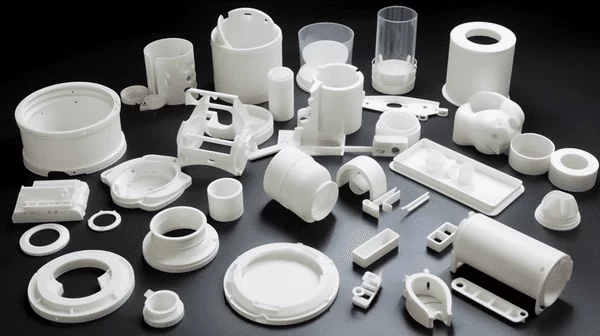
D. Влияние надлежащей толщины стенок на целостность детали и косметические дефекты
Оптимизация толщины стенок при формовании LSR оказывает значительное влияние на целостность деталей и косметические дефекты. Ключевые соображения включают:
- Структурная целостность: Правильная толщина стенок обеспечивает структурную целостность и прочность изделий из силиконовой резины. Она предотвращает такие проблемы, как коробление, деформация или разрушение детали из-за недостаточного распределения материала или неравномерного отверждения.
- Косметические дефекты: Поддержание надлежащей толщины стенок по всему изделию снижает возникновение косметических дефектов, таких как неровности поверхности, следы раковины или видимые линии растекания. Равномерная толщина стенок способствует равномерному отверждению и подаче материала, в результате чего детали получаются визуально привлекательными.
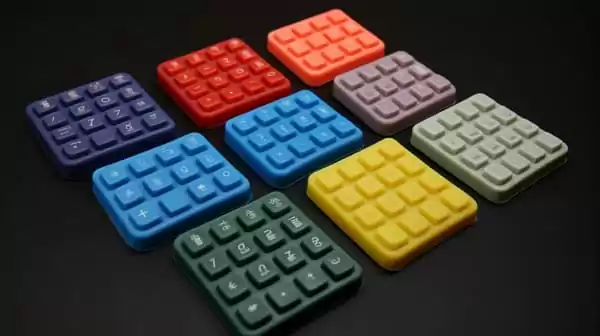
Используя преимущества литья LSR, производители могут производить изделия из силиконовой резины с исключительными механическими свойствами, улучшенным косметическим видом и возможностью массового производства. Возможность достижения необходимой толщины стенок обеспечивает целостность деталей и минимизирует косметические дефекты, способствуя общему успеху и конкурентоспособности изделий из силиконовой резины на рынке.
Заключение
В заключение следует отметить, что оптимизация процесса литья под давлением и дизайна lsr имеет решающее значение для получения высококачественных изделий из силиконовой резины. Применяя ключевые стратегии и соображения, производители могут максимально использовать потенциал процесса литья жидкой силиконовой резины (LSR) и выпускать точные, прочные и визуально привлекательные изделия.
На протяжении всей статьи мы обсуждали важность понимания требований к продукту, проектирования для формования, учета толщины стенок, включения методов вентиляции и дегазации, а также оптимизации систем охлаждения. Эти факторы, помимо прочего, играют важнейшую роль в достижении оптимальной конструкции пресс-формы для производства изделий из силиконовой резины.
Тщательное проектирование пресс-форм необходимо для обеспечения стабильного качества деталей, минимизации дефектов и повышения производительности. Тщательно продумывая подрезы, линии раздела и поверхности раздела, производители могут оптимизировать конструкцию пресс-формы и свести к минимуму косметические дефекты.
Преимущества литья LSR, включая широкий диапазон механических свойств, предлагаемых материалами LSR, улучшенный косметический вид и пригодность для массового производства, еще раз подчеркивают важность оптимизации конструкции пресс-формы. Формование LSR позволяет производить изделия из силиконовой резины с исключительными характеристиками, долговечностью и эстетической привлекательностью.
Таким образом, уделяя пристальное внимание оптимизации конструкции пресс-формы, производители могут раскрыть весь потенциал процесса формования LSR. В результате получаются высококачественные изделия из силиконовой резины, которые отвечают ожиданиям клиентов, соответствуют отраслевым стандартам и получают конкурентное преимущество на рынке. Благодаря тщательному проектированию пресс-форм производители могут обеспечить точность, долговечность и визуальную привлекательность изделий из силиконовой резины, которые удовлетворяют широкому спектру применений в различных отраслях промышленности.