يُستخدم مطاط EPDM (مطاط EPDM)، كمطاط صناعي يتمتع بمرونة جيدة، ومقاومة جيدة للتآكل، ومقاومة التآكل، ومقاومة الحرارة، ومقاومة الطقس، ومقاومة الأوزون، ومقاومة المياه العذبة ومقاومة مياه البحر، ويستخدم على نطاق واسع في منتجات مطاط السيارات، مثل أختام الأبواب والنوافذ، وخراطيم وموانع تسرب الفرامل الهيدروليكية، وقنوات تهوية تكييف الهواء، وموانع التسرب في أنظمة تبريد المحرك وأنظمة تبريد تكييف الهواء، وخراطيم نقل سائل التبريد، إلخ.
مطاط EPDM هي بنية غير قطبية ومشبعة. ما يسمى "غير قطبية"، أي أن الجزيئات التي يتكون منها البوليمر لا تحتوي على مجموعات قطبية بداخلها.
ما يسمى "المشبعة"، أي أن تركيبة البوليمر لا تحتوي على روابط مزدوجة داخل الجزيء. وبصفة عامة، يمكن تقسيم المطاط واللدائن البلاستيكية الحرارية إلى هياكل "قطبية" و"غير قطبية"، و"مشبعة" و"غير مشبعة" عدة هياكل.
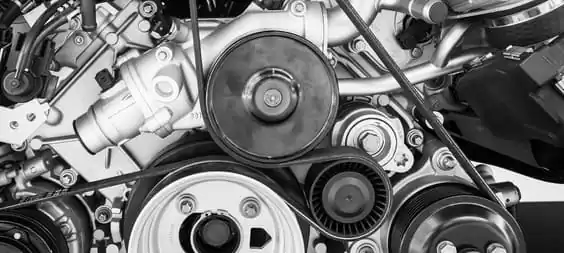
المواد التي تحتوي جزيئاتها نفسها على مجموعات قطبية هي مواد "قطبية" بشكل عام. ويحدد التركيب "القطبي" مقاومة البوليمرات للمذيبات، ويتبع ذلك عموماً مبدأ الذوبان المتماثل، أي أن المذيبات القطبية تذيب أو تنتفخ البوليمرات القطبية، والعكس صحيح.
يرتبط التركيب "المشبع" بمقاومة البوليمرات للتقادم الجوي (الأكسدة). إذا كان جزيء البوليمر يحتوي على رابطة مزدوجة، لأن الرابطة المزدوجة تتأكسد بسهولة، وبالتالي يكون البوليمر غير مستقر وسهل التحلل.
لذا فإن مادة EPDM "غير القطبية" مقاومة للوسائط القطبية، مثل الماء الساخن والبخار، والمنظفات، والأحماض العضوية وغير العضوية، والمذيبات القطبية (مثل الإيثانول، والأسيتون، والإسترات، إلخ)، وسوائل الفرامل القائمة على الجليكول، إلخ.
وليس مقاومًا للوسائط غير القطبية، مثل الزيوت المعدنية والبنزين والدهون الحيوانية والنباتية والزيوت وزيت السيليكون، وما إلى ذلك، ويستخدم على نطاق واسع في أنظمة سائل الفرامل القائم على الجليكول (SL-DOT4)، وأنظمة تبريد المحرك التي تحتوي على مضاد التجمد؛ كما أن مادة EPDM "المشبعة"، ذات المقاومة الممتازة للأوزون والعوامل الجوية، تستخدم على نطاق واسع في إنتاج الهواء والماء، وما إلى ذلك.
تتراوح درجة حرارة استخدام EPDM في درجة حرارة استخدام السيارات بشكل عام من -40 ℃ إلى 120 ℃. فيما يلي مقدمة محددة لاستخدام منتجات EPDM في السيارات، ومتطلبات أداء المواد المقابلة لها، وتحليل حالات الفشل الشائعة.
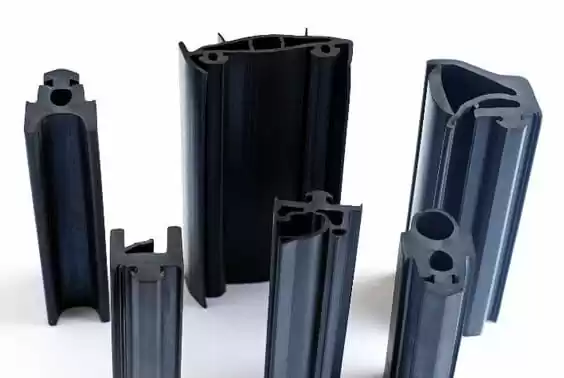
التطبيق في منتجات ختم السيارات
يتم إنتاج الغالبية العظمى من موانع تسرب السيارات بواسطة معدات البثق ذات المقطع العرضي المتناسق والطول اللانهائي (عند استخدامها، يتم اعتراضها وفقًا للطول المطلوب)، بينما يتم إنتاج عدد قليل من المنتجات غير المنتظمة بواسطة قوالب الفلكنة.
تتم عملية المنتجات المبثوقة على النحو التالي: المكونات ← خلط المطاط ← مواد متعددة (قد تشمل: المطاط الصلب، والمطاط اللين، والمطاط الإسفنجي، والمطاط الإسفنجي، والمطاط الملون، والهيكل المعدني، وأسلاك التسليح، إلخ)
البثق المركب ← الفلكنة بالتسخين (ربما: الفلكنة بالهواء الساخن، والفلكنة بخزان الفلكنة، والفلكنة بالموجات الدقيقة، والفلكنة بالموجات الدقيقة، والفلكنة بالطبقة المغلية بالخرز الزجاجي، والفلكنة بحمام الملح، إلخ) ← المعالجة اللاحقة (القطع، وصلة الفلكنة، والتدفق الكهروستاتيكي، والطلاء بالغمر السطحي، والترابط، إلخ).
تُستخدم على نطاق واسع في الزجاج الأمامي والخلفي والأبواب والنوافذ وحجرة المحرك وصندوق السيارة وأجزاء أخرى من السيارة، وتستخدم لملء الفجوة بين أجزاء الجسم، مع امتصاص الصدمات ومقاومة للماء والغبار وعزل الصوت والديكور وحماية السائقين والركاب وغيرها من الوظائف.
مثل منتجات مطاط السيليكون تكون بشكل أساسي على اتصال بأشعة الشمس والماء والأوزون، واستخدام درجات الحرارة في -40 ℃ ~ 100 ℃، يمكن أن تصل درجة الحرارة المقاومة للحرارة على المدى القصير إلى 125 ℃.
مادة EPDM المستخدمة لشريط الختم المطاطي صلابة عامة (Shore A) في 40 ~ 90 بين الاختيار ؛ يجب أن تكون قوة الشد أكثر من 7 ميجا باسكال ؛ يجب أن تكون الاستطالة عند الكسر بشكل عام في 150% ~ 500% ؛ يجب أن يكون تشوه الضغط (85 ℃، 22 ساعة) أقل من 45%.
يجب أن تكون قوة التمزق أكبر من 5 نيوتن/م؛ يجب ألا يكون هناك تشققات في تقادم الأوزون (50pphm، التمدد 20%، 72 ساعة)؛ تقادم مصباح الزينون (باستخدام مصباح الزينون 1200 جهاز، الرطوبة النسبية 80% ~ 95%، درجة حرارة اللوحة السوداء 55 ℃ ~ 60 ℃، 1000 ساعة) لا يمكن أن تتجاوز قوة الشد واستطالة الانخفاض 15%.
درجة حرارة التحول الزجاجي (TR) بحد أقصى -50 درجة مئوية؛ اختبار التقادم الحراري (100 درجة مئوية، 70 ساعة)، يجب أن يكون تغير صلابته ± 5، وتغير قوة الشد ± 15%، ويجب ألا يتجاوز استطالة الانخفاض 30%.
بشكل عام، فإن العمر التشغيلي لموانع تسرب السيارات المصنوعة من مطاط EPDM يمكن أن تصل إلى أكثر من عشر سنوات. ومع ذلك، في الإنتاج والتطبيق الفعلي، واجهنا أيضًا تشققًا في السطح، وفقدانًا في أداء الختم، وتجميد السطح، وظواهر فشل أخرى في أختام الأبواب والنوافذ بعد عام واحد من التركيب.
التشقق السطحي لاختبار المنتج، واختبار مقاومة الأوزون بعد 20 ساعة من التشقق، وفشل في تلبية المتطلبات القياسية. بعد التحقيق في هذه الدفعة من المنتجات دون المستوى المطلوب، فإن خطأ التركيبة (مطاط EPDM المحتوى أقل) كان سببه؛ صقيع سطح المطاط الختم (الإزهار).
تحليل الأسباب:
(1) تركيبات مصممة بشكل غير صحيح. أصفر كبريتي أصفر، مسرع، منشط، مضاد للأكسدة، إلخ في المكونات، بسبب غمر التشبع؛ غمر كربونات الكالسيوم غير العضوي المملوء بكربونات الكالسيوم.
(2) التشغيل غير السليم لعملية الخلط، وقت قصير جدًا، مما يؤدي إلى تشتت غير متساوٍ للحشو، محلي أكثر من التشبع. من خلال تعديل الصيغة، وزيادة وقت الخلط، وأخيرًا يمكن حل مشكلة الفيضان.
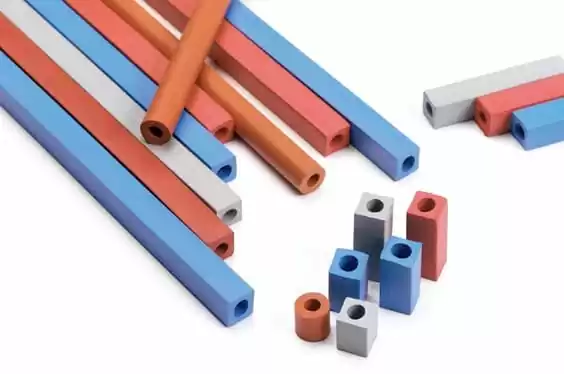
استخدام مادة EPDM في خراطيم المكابح الهيدروليكية وموانع التسرب الدائرية
سائل الفرامل EPDM المقاوم لسائل الفرامل (DOT3، DOT4، DOT5 (القائم على زيت السيليكون)، المستخدم في إنتاج الطبقة المطاطية الداخلية لخرطوم الفرامل الهيدروليكية وموانع تسرب مضخة الفرامل.
هذه منتجات EPDM ملامسة لسائل المكابح المتوسط الرئيسي، واستخدام درجات حرارة تتراوح بين -40 ℃ ~ 120 ℃، ودرجات حرارة مقاومة للحرارة على المدى القصير تصل إلى 135 ℃.
هذه الأجزاء المستخدمة EPDM، الصلابة (Shore A) هي 80 ؛ يجب أن تكون قوة الشد أكثر من 10.5 ميجا باسكال ؛ الاستطالة عند الكسر بشكل عام أعلى من 175% ؛ في معدل الاستطالة 50% من إجهاد التمديد الثابت من 2.5 ~ 4MPa ؛ في معدل الاستطالة 100% من إجهاد التمديد الثابت 8MPa أو أكثر.
يجب أن يكون تشوه الضغط (100 ℃، 22 ساعة) أقل من 40%؛ يجب أن تكون درجة حرارة التحول الزجاجي (TR) بحد أقصى -50 ℃؛ يجب ألا يكون هناك تشققات في الأوزون (50pphm، 20% استطالة 72 ساعة)؛ اختبار سائل الفرامل (وضع العينة في سائل الفرامل، 150 ℃، 70 ساعة) يجب أن يكون تغير صلابتها 5.
يجب أن يكون تغيير قوة الشد ± 20%، يجب أن يكون تغيير الاستطالة -15% ~ 20%، يجب أن يكون تغيير الحجم في حدود ± 20%. 20%، يجب أن يكون تغير الحجم في حدود ± 5%؛ الاختبار الحراري (125 ℃، 70 ساعة)، يجب أن يكون تغير الصلابة ± 5، وتغير قوة الشد يجب أن يكون ± 15%، واستطالة الانخفاض لا يمكن أن تتجاوز 15%.
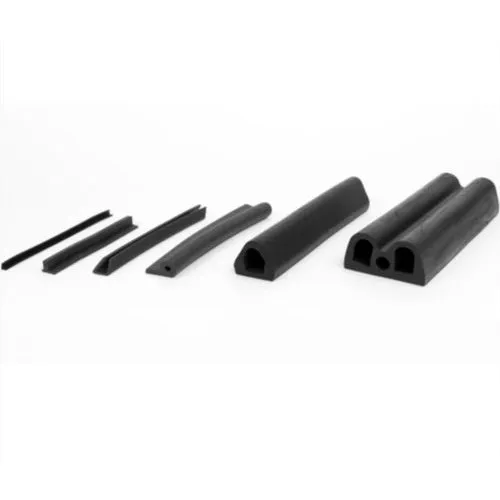
مادة EPDM في تطبيقات خراطيم التدفئة والتهوية وتكييف الهواء
يتكون الخرطوم المطاطي بشكل عام من ثلاث طبقات، وهي الطبقة الداخلية وطبقة التعزيز الوسطى (نسيج الألياف الكيميائية أو الأسلاك الفولاذية) والطبقة الخارجية. يجب اختيار المواد المستخدمة للطبقات الثلاث وفقًا للمتطلبات الفعلية.
يجب أن تكون الطبقة الداخلية مقاومة لتآكل الوسط الذي يتم توصيله، بينما يجب أن تكون الطبقة الخارجية ذات قوة ميكانيكية وأن تتكيف مع البيئة الخارجية.
لذلك، غالبًا ما يكون المطاط الداخلي والخارجي غير مطاطي. وقد استخدم EPDM على نطاق واسع في خراطيم التدفئة والتهوية داخل الطبقة المطاطية وخارجها، وخراطيم تكييف الهواء في الطبقة المطاطية الخارجية لأن المادة تتمتع بمقاومة جيدة للهواء والماء والأوزون وتقادم أشعة الشمس ومرونة في درجات الحرارة المنخفضة.
مثل هذه الأجزاء التي تستخدم EPDM، صلابة (Shore A) لـ 70؛ يجب أن تكون قوة الشد أكثر من 10.5 ميجا باسكال؛ الاستطالة عند الكسر بشكل عام أكثر من 300%؛ يجب أن يكون التشوه المتبقي بالضغط (100 ℃، 22 ساعة) أقل من 40%;
درجة حرارة التحول الزجاجي (TR) بحد أقصى -45 درجة مئوية؛ يجب ألا يكون هناك تشقق في الأوزون (50pphm، تمدد 20%، 72 ساعة)؛ اختبار زيت IRM902 (وضع العينة في زيت IRM902، 100 ℃، 70 ساعة) الحد الأقصى لتخفيض صلابتها 15، والحد الأقصى لتخفيض قوة الشد 30%.
الحد الأقصى لتخفيض قوة التمزق 30%، يجب أن يكون تغير الحجم في حدود 80%؛ اختبار الشيخوخة الحرارية (125 ℃، 70 ساعة)، يجب أن يكون تغير صلابته ± 5، يجب أن يكون تغير قوة الشد ± 15%، لا يمكن أن يتجاوز تخفيض الاستطالة 40%.
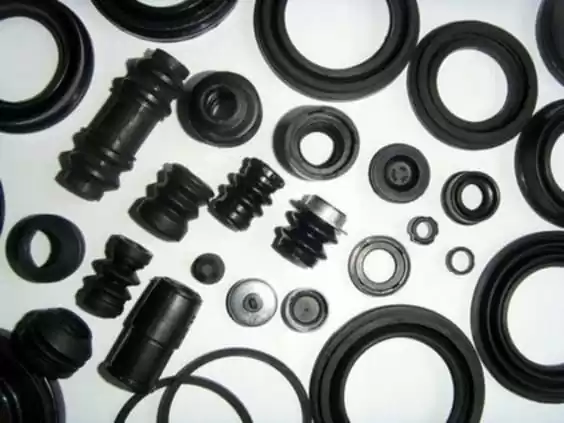
مادة EPDM في تطبيق سحب الحزام
يمكن لهذا النوع من الأجزاء، المستخدم بشكل أساسي للتوصيل بين غطاء العجلة، وتثبيت غطاء صندوق البطارية، وما إلى ذلك، أن يتحمل الحمل الديناميكي والميكانيكي العالي، في استخدام العملية ويكون دائمًا في حالة توتر.
هذه منتجات مطاط السيليكون يتعرضون بشكل أساسي لأشعة الشمس والماء والأوزون، واستخدام درجات الحرارة في -40 ℃ ~ 85 ℃، يمكن أن تصل درجة الحرارة المقاومة للحرارة على المدى القصير إلى 100 ℃.
مادة EPDM المستخدمة في صنع مثل هذه الأجزاء، تكون الصلابة (Shore A) بشكل عام 60 ~ 80 ؛ يجب أن تكون قوة الشد أكثر من 14MPa ؛ الاستطالة عند الكسر بشكل عام 200% ~ 400% ؛ يجب أن تكون قوة التمزق أكبر من 7N / م;
يجب أن يكون التشوه المتبقي بالضغط (85 ℃، 22 ساعة) أقل من 45%؛ يجب أن يكون التشوه المتبقي بالضغط (-20 ℃، 22 ساعة) أقل من 45%؛ يجب ألا تكون مقاومة تقادم الأوزون (50pphm، التمدد 20%، 72 ساعة) أي تشققات; تقادم مصباح الزينون (باستخدام معدات مصباح الزينون 1200، الرطوبة النسبية 80% ~ 95%، درجة حرارة اللوحة السوداء 55 ℃ ~ 60 ℃، 1000 ساعة) يجب ألا تتجاوز قوة الشد واستطالة الانخفاض 15%;
درجة حرارة التحول الزجاجي (TR) من -50 ℃ كحد أقصى؛ اختبار الشيخوخة الحرارية (100 ℃، 70 ساعة)، يجب أن يكون تغير صلابته ± 75، يجب أن يكون تغير قوة الشد ± 15%، يجب ألا يتجاوز انخفاض الاستطالة 40%.
تم إنتاج كسر حزام غطاء البطارية والشقوق على سطح حزام واقي العجلة بعد نصف عام من التحميل. بعد فشل قوة الشد للمنتج، وقوة التمزق، واختبار تقادم الأوزون، كانت النتائج الفعلية المحققة هي قوة الشد 8.5 ميجا باسكال، وقوة التمزق 5 نيوتن/متر، والتشقق الناتج عن تقادم الأوزون لمدة 42 ساعة، وهي لا ترقى إلى المتطلبات القياسية.
الشركات المصنعة الفردية لشريط السحب على أهمية الصيغة المطاطية ليست مفهومة بما فيه الكفاية، طالما أن مطاط EPDM مصنوع من شريط سحب المطاط يمكن أن يكون، في الواقع، بسبب التركيبات المختلفة، قد يختلف أداء المنتج بشكل كبير.
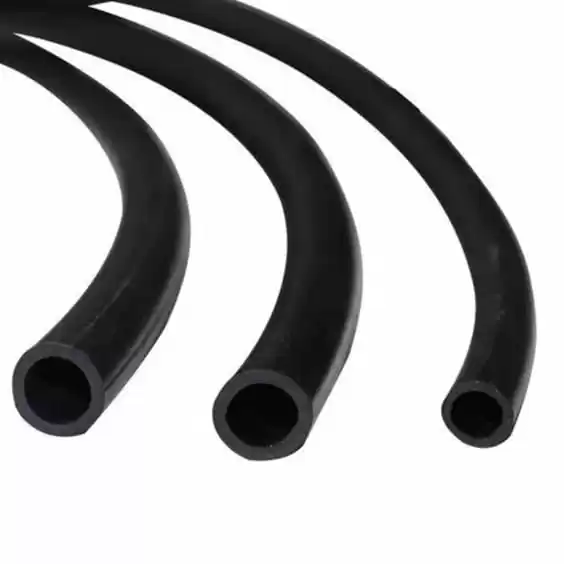
استخدام مادة EPDM في نظام تبريد المحرك وموانع تسرب نظام التكييف والتبريد
يستخدم EPDM لصنع الأختام في أنظمة تبريد المحرك. هذه المنتجات في اتصال مع الوسط هو مضاد للتجمد، وأشعة الشمس، والماء، والأوزون، واستخدام درجة الحرارة في -40 ℃ ~ 125 ℃، ودرجات حرارة مقاومة للحرارة على المدى القصير تصل إلى 135 ℃.
هذه الأجزاء التي تستخدم EPDM، صلابة (Shore A) لـ 60 ~ 80 (75 لتطبيق الأختام المستديرة في نظام التبريد)؛ يجب أن تكون قوة الشد أكثر من 10.5 ميجا باسكال؛ الاستطالة عند الكسر بشكل عام أكثر من 175%؛ في معدل الاستطالة 50% من إجهاد التمديد الثابت من 1 ~ 2MPa؛ في معدل الاستطالة 100% من إجهاد التمديد الثابت من 2 ~ 5MPa أعلاه؛ يجب أن يكون تشوه الانكماش (150 ℃، 22 ساعة) أقل من 20%;
يجب أن تكون درجة حرارة مقاومته للحرارة حتى 135 ℃. (22 ساعة) أقل من 20%؛ درجة حرارة انتقال الزجاج (TR) هي -50 ℃ كحد أقصى؛ يجب ألا تكون مقاومة تقادم الأوزون (50pphm، تمدد 20%، 72 ساعة) أي تشققات;
بالنسبة لموانع التسرب المستخدمة في أنظمة تبريد المحرك، يجب إجراء اختبار التبريد (يجب إجراء اختبار التبريد (عينة الاختبار الموضوعة في مضاد التجمد، 150 درجة مئوية، 166 ساعة، ضغط الاختبار حوالي 0.4 ميجا باسكال)، ويجب أن يكون التغير في الصلابة ± 5، والتغير في قوة الشد ± 20%، والتغير في الاستطالة عند الكسر ± 15% إلى 20%، والتغير في الحجم ± 5%;
بالنسبة لموانع التسرب المستخدمة في أنظمة تكييف الهواء، يجب إجراء اختبار المبردات (العينة الموضوعة في اختبار P (وضع العينة في PAG، مبرد ND8، 100 ℃، 70 ساعة) يجب أن يكون تغير الصلابة حتى ± 5، تغير قوة الشد حتى ± 20%، الاستطالة عند الكسر تغير يصل إلى -15% ~ 20%، يجب أن يكون تغير الحجم في حدود ± 5%; اختبار الشيخوخة الحرارية (150 ℃، 70 ساعة)، يجب أن يكون تغير الصلابة ± 5، يجب أن يكون انخفاض قوة الشد أقل من 10%، لا يمكن أن يتجاوز انخفاض الاستطالة 10%.
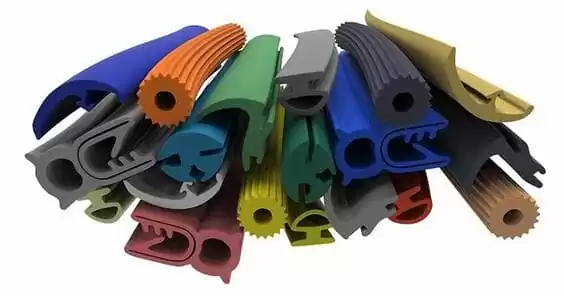
مادة EPDM في تطبيق خرطوم سائل التبريد
يُستخدم EPDM في صناعة خرطوم مياه المحرك، حيث تُصنع طبقاته المطاطية الداخلية والخارجية من مادة EPDM. وهذه منتجات EPDM عند التلامس مع الوسط هي مضاد التجمد، وأشعة الشمس، والماء، والأوزون، واستخدام درجة الحرارة في -40 ℃ ~ 125 ℃، يمكن أن تصل درجة الحرارة المقاومة للحرارة على المدى القصير إلى 150 ℃.
مثل هذه الأجزاء المستخدمة EPDM، صلابة (Shore A) ل 65 ؛ يجب أن تكون قوة الشد أعلى من 10.5 ميجا باسكال ؛ الاستطالة عند الكسر في أكثر من 300% ؛ في معدل الاستطالة 50% من إجهاد التمدد الثابت من 1 ~ 2MPa ؛ معدل الاستطالة 100% من إجهاد التمدد الثابت من 2 ~ 4.5MPa أعلاه ؛ يجب أن يكون التشوه المتبقي للضغط (100 ℃، 22 ساعة) أقل من 20%;
يجب أن تكون درجة حرارة التحول الزجاجي (TR) بحد أقصى -50 درجة مئوية؛ يجب ألا تكون هناك تشققات؛ اختبار سائل التبريد (العينة الموضوعة في مضاد التجمد، 150 درجة مئوية، 166 ساعة، ضغط الاختبار حوالي 0.4 ميجا باسكال).
يجب أن يكون تغير الصلابة ± 5، وتغير قوة الشد يجب أن يكون ± 20%، والاستطالة عند الكسر يجب أن تكون -15% ~ 20%، وتغير الحجم يجب أن يكون ± 5%. اختبار التقادم الحراري (150 ℃، 70 ساعة)، يجب أن يكون التغير في الصلابة ± 5، ويجب أن تكون قوة الشد أقل من 10%، ويجب ألا تتجاوز الاستطالة عند الانخفاض 10%.