Einführung
Die Gestaltung der Formnester ist der Dreh- und Angelpunkt für erfolgreiches Formpressen und hat die Macht, die Zukunft zahlreicher Branchen zu gestalten. Dieser kritische Aspekt der Fertigung darf nicht unterschätzt werden, da er die Fähigkeit besitzt, qualitativ hochwertige und konsistente Ergebnisse zu liefern - ein wahrer Beweis für seine Bedeutung.
In einer Welt, in der Innovation und Präzision an erster Stelle stehen, erweist sich das Formpressen als vielseitiges und unverzichtbares Fertigungsverfahren. Mit Anwendungen, die sich über eine Vielzahl von Branchen erstrecken, darunter die Automobil-, Elektronik- und Konsumgüterindustrie, spielt es eine zentrale Rolle bei der Gestaltung der Produkte, auf die wir uns täglich verlassen. Von Automobilkomponenten, die auf Leistung und Langlebigkeit ausgelegt sind, bis hin zu elektrischen Isoliermaterialien, die unsere Sicherheit gewährleisten, berührt das Formpressen nahezu alle Facetten unseres Lebens.
Während wir tiefer in das Reich der Formhohlraumgestaltung für das Formpressenbegeben wir uns auf eine Reise, auf der wir das komplizierte Gewebe dieses Prozesses enträtseln. Wir erforschen die Nuancen dieses Verfahrens und zeigen, wie die richtige Formnestgestaltung eine Welt der Möglichkeiten eröffnen kann, um Produkte herzustellen, die unsere Erwartungen nicht nur erfüllen, sondern oft übertreffen. Begleiten Sie uns auf dieser Entdeckungsreise durch die Kunst und Wissenschaft des Formpressens, bei der die Gestaltung der Kavitäten der Kompass ist, der uns zum Inbegriff von Fertigungsqualität führt.
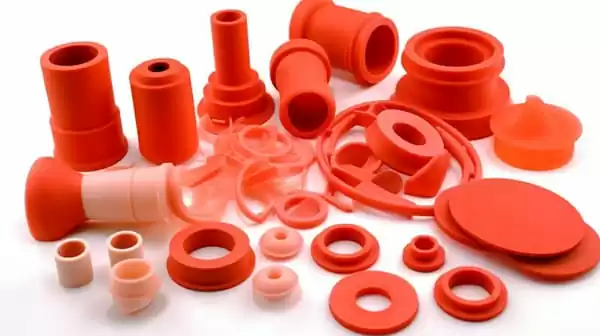
Verständnis der Verfahren des Formpressens
Das Formpressen ist ein vielseitiges und weit verbreitetes Herstellungsverfahren, das in verschiedenen Branchen Anwendung findet. Um das Wesen dieser Technik zu erfassen, ist es wichtig, sie in ihre Kernkomponenten zu zerlegen.
1. Das Formpressverfahren:
Ihr Kernstück, Formpressen ist ein Verfahren, bei dem Materialien durch Hitze und Druck geformt werden. Es handelt sich um die folgenden Schritte:
Materialaufbereitung: Der Prozess beginnt mit der Aufbereitung von Rohstoffen, in der Regel in Form von Granulaten, Pellets oder Sheet Molding Compounds (SMC).
Erhitzen: Die Form, die oft aus zwei Hälften besteht, wird um das Material herum geschlossen. Dann wird Wärme zugeführt, um das Material zu erweichen oder zu schmelzen und es biegsam zu machen.
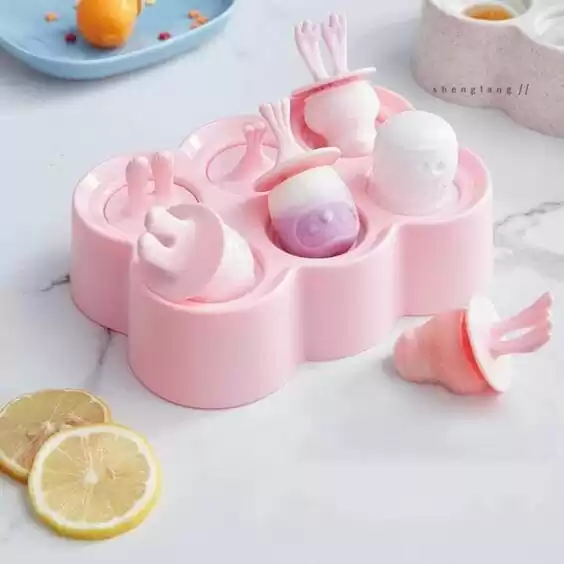
Komprimierung: Druck wird auf den Formhohlraum ausgeübt, wodurch das Material verdichtet wird und die gewünschte Form des Endprodukts annimmt.
Abkühlen: Sobald das Material die Form angenommen hat, wird es abgekühlt, damit es sich verfestigt und die erhitzte Form aushärtet und die gewünschte Form beibehält.
Auswerfen: Zum Schluss wird das Formteil aus dem Formhohlraum ausgestoßen und ist bereit für die weitere Verarbeitung oder Verwendung.
2. Konstruktion von Pressformen:
Die Grundlage eines erfolgreichen Formpressvorgangs liegt in der Gestaltung des Formhohlraums. Konstruktion der Pressform umfasst mehrere entscheidende Elemente:
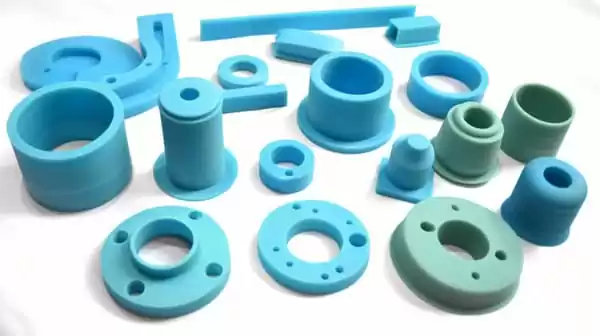
Geometrie: Die Geometrie des Formhohlraums muss genau der vorgesehenen Form des Endprodukts entsprechen. Dazu gehören Aspekte wie die Dicke des Teils, Entformungswinkel und Hinterschneidungen, um einen reibungslosen Ausstoß zu gewährleisten.
Entlüftung: Eine wirksame Entlüftung ist wichtig, damit eingeschlossene Luft und Gase während des Formens entweichen können. Eine ordnungsgemäße Entlüftung verhindert Mängel wie Lufteinschlüsse oder Hohlräume im Endprodukt.
Trennebene: Die Trennlinie gibt an, wo sich die Form trennt, um das Formteil freizugeben. Sie muss gut definiert sein und darf die Ästhetik und Funktionalität des Produkts nicht beeinträchtigen.
Anschnittdesign: Der Anschnitt dient als der Punkt, durch den das geschmolzene Material in den Formhohlraum eintritt. Ein sorgfältiges Anschnittdesign gewährleistet eine gleichmäßige Füllung und minimiert Fehler. Zu den Anschnittarten gehören Kantenanschnitte, Stiftanschnitte und Tunnelanschnitte.
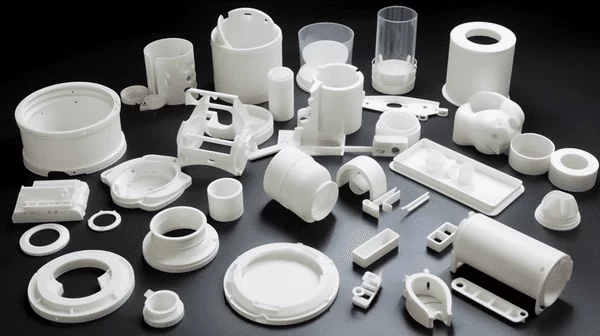
Kühlsystem: Effiziente Kühlkanäle in der Form tragen dazu bei, dass das Formteil schnell erstarrt, Verformungen verhindert und die Zykluszeiten verkürzt werden.
Oberfläche: Je nach den Anforderungen des Produkts kann die Oberfläche des Formhohlraums poliert, strukturiert oder beschichtet werden, um die Ästhetik des Endprodukts zu verbessern.
3. Materialien, die beim Formpressen verwendet werden:
Das Formpressen ist mit einer Vielzahl von Materialien kompatibel, darunter duroplastische Materialien wie Epoxidharz, Silikonkautschuk und Polymerharze. Besonders gut eignet es sich für faserverstärkte Kunststoffe wie Glasfaser- oder Kohlefaserverbundwerkstoffe. Diese Materialien bieten eine hervorragende mechanische Leistung, Temperaturbeständigkeit und chemische Beständigkeit.
4. Vorteile und Nachteile des Formpressens:
Vorteile:
Kostengünstig: Beim Formpressen werden häufig recycelte thermoplastische Materialien und Materialien mit relativ niedrigem Schmelzpunkt verwendet, was die Produktionskosten senkt.
Breiter Temperaturbereich: Es können Formen für Teile mit großen Temperaturbereichen und hohen Anforderungen an die chemische Beständigkeit hergestellt werden.
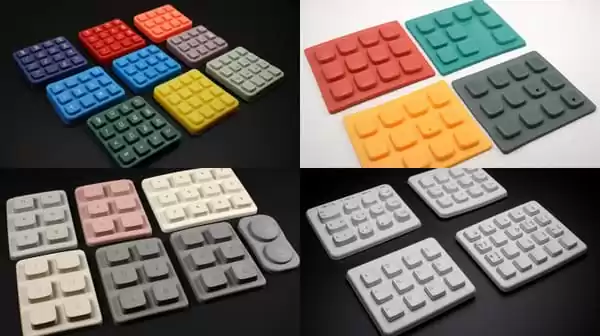
Zusammengesetzte Materialien: Ideal für die Bearbeitung von Verbundwerkstoffen wie Glas- und Kohlefasern, die die Herstellung von hochfesten und leichten Bauteilen ermöglichen.
Benachteiligungen:
Komplexe Geometrien: Möglicherweise nicht geeignet für die Herstellung von Bauteilen mit extrem komplexen Geometrien oder engen Toleranzen.
Langsamerer Prozess: Das Formpressen kann im Vergleich zu anderen Formverfahren wie dem Spritzgießen langsamer sein, was sich auf die Produktionsraten auswirken kann.
Das Verständnis des Formpressverfahrens, der Rolle der Formpresskonstruktion, der Vielseitigkeit der verwendeten Materialien und der Vor- und Nachteile dieses Verfahrens bildet die Grundlage für die Nutzung seines Potenzials in verschiedenen Branchen. Es ist ein Verfahren, das Präzision, Kreativität und Technik kombiniert, um aus Rohstoffen die Produkte zu formen, die unsere Welt zum Funktionieren bringen.
Abschnitt 2: Arten des Formpressens
Im Bereich des Formpressens spielen die Formtypen eine entscheidende Rolle für das Ergebnis des Prozesses. Die Wahl des Werkzeugs kann die Produktqualität, die Komplexität und die Produktionseffizienz erheblich beeinflussen. Im Folgenden werden die drei wichtigsten Formtypen für das Formpressen vorgestellt und ihre Eigenschaften und Anwendungen erläutert:
1. Open-Flash-Form:
Merkmale:
Flash-Management: Das charakteristische Merkmal von Freiformwerkzeugen ist, dass während des Formpressens überschüssiges Material, der so genannte "Grat", entweichen kann. Dieser Grat wird später abgeschnitten und hinterlässt das gewünschte Produkt.
Anwendungen:
Teile mit geringer Präzision: Offene Formen werden in der Regel eingesetzt, wenn Präzision keine kritische Anforderung ist. Sie sind ideal für die Herstellung von Teilen, bei denen kein hohes Maß an Maßgenauigkeit erforderlich ist.
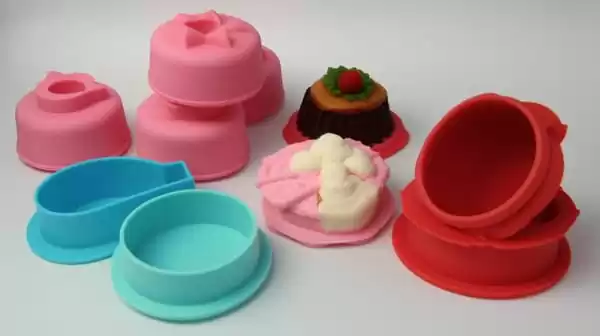
2. Geschlossene Form:
Merkmale:
Präzision: Geschlossene Formen sind so konzipiert, dass sie während des gesamten Formpressvorgangs ein hohes Maß an Präzision gewährleisten. Sie sind so konstruiert, dass sie den Grat minimieren und enge Toleranzen im Endprodukt gewährleisten.
Anwendungen:
Kritische Präzision: Geschlossene Formen finden ihre Nische in Anwendungen, bei denen Präzision an erster Stelle steht. Sie werden in Szenarien eingesetzt, in denen Produktkonsistenz und die Einhaltung enger Toleranzen nicht verhandelbar sind.
3. Halbgeschlossene Form:
Merkmale:
Hybrid-Ansatz: Halbgeschlossene Formen kombinieren Elemente von offenen und geschlossenen Formen. Sie lassen zwar einen Teil des Grates entweichen, bieten aber auch Kontrolle über die Abmessungen der Teile.
Anwendungen:
Ausgewogene Anforderungen: Halbgeschlossene Formen werden gewählt, wenn eine mäßige Präzision erforderlich ist und das Gratmanagement wichtig, aber nicht so kritisch ist wie bei geschlossenen Formen. Sie bieten einen ausgewogenen Ansatz, der sich für ein breites Spektrum von Produktanforderungen eignet.
Im Wesentlichen hängt die Wahl zwischen offenen, geschlossenen und halbgeschlossenen Formen beim Formpressen von den spezifischen Anforderungen des herzustellenden Produkts ab. Offene Werkzeuge eignen sich, wenn Präzision nicht die oberste Priorität ist, geschlossene Werkzeuge zeichnen sich bei Anwendungen aus, die äußerste Präzision erfordern, und halbgeschlossene Werkzeuge bilden ein Gleichgewicht zwischen diesen beiden Extremen. Durch die Auswahl des geeigneten Formentyps können Hersteller ihre Formpressverfahren optimieren, um den einzigartigen Anforderungen ihrer Produkte und Branchen gerecht zu werden.
Abschnitt 3: Arten von Formpresswerkstoffen
In der Welt des Formpressens ist die Wahl der Materialien für formgepresste Produkte von entscheidender Bedeutung für die Eigenschaften und Merkmale des Endprodukts. Zwei in diesem Verfahren häufig verwendete Materialien sind Sheet Molding Compound (SMC) und Bulk Molding Compound (BMC). Im Folgenden werden diese Werkstoffe näher erläutert und die Vorteile der Verwendung von duroplastischen Werkstoffen beim Formpressen beleuchtet:
1. Sheet Molding Compound (SMC):
Merkmale:
Faserverstärkt: SMC ist ein faserverstärktes Material, das wärmehärtende Harze mit zerkleinerten Glasfasern kombiniert. Diese Verstärkung verleiht dem Material eine hervorragende Festigkeit und Steifigkeit.
Blattform: SMC wird in der Regel in Form von flachen Platten oder Rollen geliefert. Diese Platten sind mit Harz vorimprägniert und lassen sich leicht zuschneiden und in den Formhohlraum schichten.
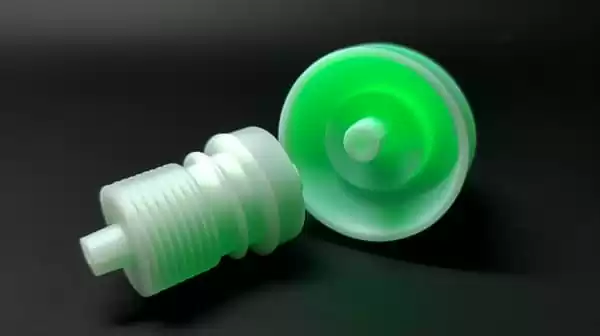
Anwendungen:
Automobilkomponenten: SMC wird in der Automobilindustrie aufgrund seiner hohen Festigkeit, Schlagzähigkeit und Korrosionsbeständigkeit häufig zur Herstellung von Bauteilen wie Karosserieteilen, Motorhauben und Außenverkleidungen verwendet.
Elektrische Schaltschränke: Seine elektrisch isolierenden Eigenschaften machen SMC zu einer bevorzugten Wahl für elektrische Gehäuse und Schalttafeln.
2. Bulk Molding Compound (BMC):
Merkmale:
Duroplastisches Material: BMC ist ebenfalls ein wärmehärtendes Material, das aus einer Mischung aus wärmehärtendem Harz, Füllstoffen und Verstärkungsfasern (in der Regel Glas) besteht.
Körnige Form: Im Gegensatz zu SMC wird BMC in Granulatform geliefert. Diese körnige Konsistenz ermöglicht ein präzises Formen von komplexen Formen.
Anwendungen:
Automobilindustrie: BMC wird in der Automobilindustrie für die Herstellung komplexer Komponenten wie Ventildeckel, Ansaugkrümmer und Teile unter der Motorhaube verwendet. Seine Dimensionsstabilität und Beständigkeit gegen Chemikalien und Hitze machen es zu einer idealen Wahl.
Elektrotechnik und Elektronik: BMC wird aufgrund seiner hervorragenden elektrischen Isolationseigenschaften und seiner Flammbeständigkeit in der Elektrotechnik und Elektronik eingesetzt.
Vorteile der Verwendung duroplastischer Materialien beim Formpressen:
Die Wahl von duroplastischen Werkstoffen, wie sie in SMC und BMC verwendet werden, bietet mehrere Vorteile beim Formpressen:
Temperaturbeständigkeit: Duroplastische Werkstoffe eignen sich hervorragend für Umgebungen mit hohen Temperaturen. Sie können hohen Temperaturen standhalten, ohne sich zu verformen, und eignen sich daher für Anwendungen, die eine Beständigkeit gegen Hitze und Temperaturwechsel erfordern.
Chemische Beständigkeit: Diese Materialien weisen eine ausgezeichnete chemische Beständigkeit auf und eignen sich daher ideal für Anwendungen, bei denen mit der Einwirkung verschiedener Chemikalien zu rechnen ist.
Dimensionsstabilität: Duroplastische Werkstoffe behalten ihre Form und Abmessungen unter Druck und hohen Temperaturen bei und gewährleisten so Konsistenz und Präzision des Endprodukts.
Elektrische Isolierung: Sowohl SMC als auch BMC verfügen über hervorragende elektrische Isolationseigenschaften, die sie für Anwendungen in der Elektrotechnik und Elektronik unverzichtbar machen.
Komplexe Formen: Die körnige Form von BMC und die Schichtungsfähigkeit von SMC ermöglichen das Formen komplexer und komplizierter Formen und bieten eine große Designvielfalt.
Zusammenfassend lässt sich sagen, dass Sheet Molding Compound (SMC) und Bulk Molding Compound (BMC) beispielhafte Beispiele für duroplastische Materialien sind, die beim Formpressen verwendet werden. Ihre inhärenten Vorteile, wie Temperatur- und Chemikalienbeständigkeit, Dimensionsstabilität und elektrische Isolationseigenschaften, machen sie zu einer wertvollen Wahl bei der Herstellung verschiedenster Produkte in allen Branchen. Die Verwendung dieser Materialien in Verbindung mit der Präzision der FormpressenDas Ergebnis sind hochwertige Bauteile mit maßgeschneiderten Eigenschaften und Leistungen.
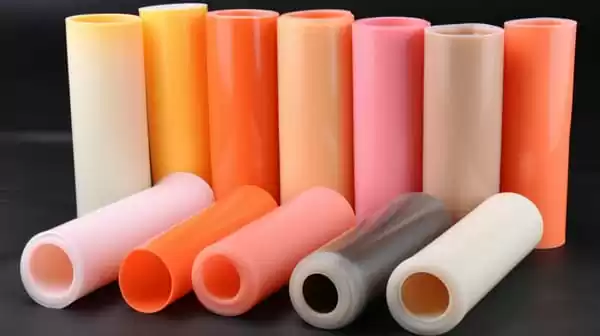
Abschnitt 4: Das eigentliche Formpressverfahren
Um die Feinheiten des Formpressens wirklich zu verstehen, ist es wichtig, sich mit dem Kern des Verfahrens selbst zu befassen. In diesem Abschnitt werden wir die wesentlichen Komponenten des Presswerkzeugs untersuchen, die Bedeutung des Hochdruckverfahrens verstehen und den Aushärtungsprozess, der für die Verfestigung des Formteils verantwortlich ist, entschlüsseln:
1. Bestandteile der Pressform:
Die Pressform ist das Herzstück des Formpressverfahrens. Sie besteht aus mehreren entscheidenden Komponenten:
Formhohlraum: Hier geschieht die Magie. Der Formhohlraum bestimmt die Form und die Abmessungen des Endprodukts. Sie muss sorgfältig entworfen werden, um die gewünschte Geometrie aufzunehmen, einschließlich Faktoren wie Teiledicke, Entformungswinkel und Oberflächengüte.
Heizungsanlage: Pressformen sind mit einem Heizsystem ausgestattet, das die Temperatur im Formhohlraum anhebt. Diese Heizung ist wichtig, um das Rohmaterial zu erweichen oder zu schmelzen, damit es geschmeidig und formbar wird.
Kühlsystem: Effiziente Kühlkanäle oder -systeme verlaufen durch die Form, um das geformte Teil schnell abzukühlen und zu verfestigen, sobald es seine Form angenommen hat. Eine ordnungsgemäße Kühlung sorgt dafür, dass die gewünschte Form erhalten bleibt, und verhindert Verformungen oder Verwerfungen.
Druck-Mechanismus: Das Formpressen ist bekannt für seine Hochdruckeigenschaften. Die Form verfügt über einen Mechanismus, der erheblichen Druck auf den Formhohlraum ausübt. Dieser Druck verdichtet das Material und sorgt dafür, dass es jeden Winkel der Form ausfüllt, was letztlich die Dichte und strukturelle Integrität des Teils bestimmt.
2. Der Hochdruckcharakter des Formpressens:
Das Formpressen zeichnet sich durch einen hohen Druck aus, der eine entscheidende Rolle bei der Formgebung des Endprodukts spielt. Die Bedeutung dieser Hochdruckumgebung liegt in mehreren Aspekten:
Material Kompression: Der hohe Druck, der beim Formpressen angewendet wird, verdichtet das Material innerhalb des Formhohlraums. Durch diese Verdichtung wird sichergestellt, dass sich das Material genau an die Geometrie der Form anpasst, was zu einer ausgezeichneten Reproduktion und Maßgenauigkeit der Teile führt.
Dichtheitskontrolle: Der Druck bestimmt die Dichte des Endprodukts. Durch sorgfältige Steuerung des Drucks können die Hersteller bestimmte Materialdichten erreichen, die die mechanischen Eigenschaften und die Leistung des Teils beeinflussen.
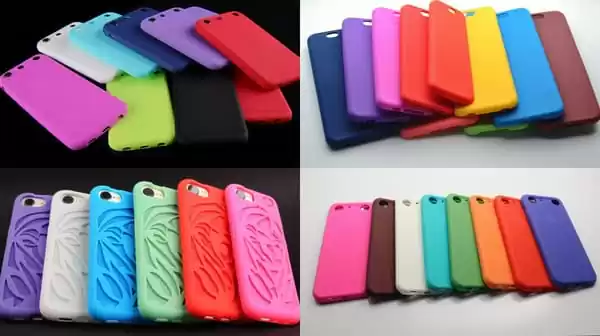
Einheitliche Füllung: Hoher Druck hilft bei der gleichmäßigen Füllung des Formhohlraums. Dies minimiert das Risiko von Hohlräumen, Lufteinschlüssen oder anderen Defekten im Endprodukt und trägt so zu dessen Qualität bei.
3. Der Aushärtungsprozess:
Nachdem das Material die gewünschte Form im Formhohlraum angenommen hat, kommt der Aushärtungsprozess ins Spiel. Das Aushärten ist der Schritt, der für die Verfestigung des Formteils verantwortlich ist und ihm seine endgültige strukturelle Integrität verleiht. Und so funktioniert es:
Hitze und Druck: Die erhöhte Temperatur in der Form löst in Verbindung mit dem ausgeübten Druck eine chemische Reaktion in dem duroplastischen Material aus. Diese Reaktion bewirkt, dass das Material aushärtet und seine Form annimmt.
Kühlung: Sobald der Aushärtungsprozess abgeschlossen ist, wird das Kühlsystem der Form aktiviert, um die Temperatur schnell zu senken. Diese Kühlphase trägt zur Verfestigung des Teils bei, so dass es starr und bereit für den Ausstoß aus der Form ist.
Zusammenfassend lässt sich sagen, dass das Verständnis der Komponenten der Pressform, der Bedeutung der Hochdruckumgebung und des Aushärtungsprozesses wertvolle Einblicke in die Mechanik des Pressformens bietet. Dieses komplizierte Zusammenspiel von Hitze, Druck und Feinmechanik ermöglicht die Herstellung von hochwertige Komponenten mit der gewünschten Form, Dichte und mechanischen Eigenschaften. Es ist die Verkörperung von Fertigungsexzellenz und liefert Produkte, die den höchsten Standards für Leistung und Zuverlässigkeit entsprechen.
Abschnitt 5: Gestaltung des Formhohlraums
Der Formhohlraum ist das Herzstück des Formpressverfahrens. In diesem Abschnitt werden wir die entscheidende Rolle des Formhohlraumdesigns untersuchen, das Design von Presswerkzeugen definieren und uns mit der Berechnung der Tonnage befassen - einem entscheidenden Faktor beim Formpressen:
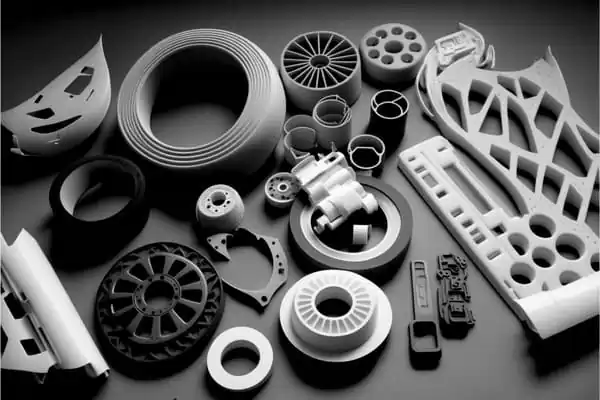
1. Die Bedeutung der Formhohlraumgestaltung:
Die Gestaltung des Formhohlraums ist von entscheidender Bedeutung für den Erfolg des Formpressverfahrens. Hier erfahren Sie, warum sie so wichtig ist:
Präzision und Konsistenz: Der Formhohlraum bestimmt die endgültige Form und die Abmessungen des Produkts. Eine gut gestaltete Kavität gewährleistet Präzision und Konsistenz in jedem geformten Teil und erfüllt die höchsten Qualitätsstandards.
Materialfluss: Die Geometrie des Formhohlraums bestimmt, wie das Material fließt und die Form füllt. Eine unsachgemäße Konstruktion kann zu einer ungleichmäßigen Materialverteilung führen, was Defekte oder Unstimmigkeiten im Endprodukt zur Folge hat.
Belüftung und Kühlung: Wirksame Entlüftungskanäle oder Nuten im Formhohlraum lassen eingeschlossene Luft und Gase entweichen und verhindern so Defekte wie Lufteinschlüsse. Das Kühlsystem in der Kavität trägt dazu bei, dass das Teil schnell erstarrt, was die Zykluszeiten verkürzt.
Oberfläche: Auch die Gestaltung des Formhohlraums spielt eine Rolle, wenn es darum geht, die gewünschte Oberflächenbeschaffenheit des Formteils zu erreichen. Sie kann poliert, strukturiert oder beschichtet werden, um bestimmte ästhetische und funktionale Anforderungen zu erfüllen.
2. Was ist die Konstruktion von Pressformen?
Konstruktion der Pressform ist der Prozess der sorgfältigen Herstellung eines Formhohlraums, der den hohen Drücken und Temperaturen beim Formpressen standhalten kann. Er umfasst mehrere kritische Aspekte:
Geometrie: Der Formhohlraum muss genau der vorgesehenen Form des Endprodukts entsprechen. Dies beinhaltet die Berücksichtigung von Teiledicke, Entformungswinkeln und Hinterschneidungen für einen reibungslosen Ausstoß.
Entlüftung: Geeignete Entlüftungskanäle oder -nuten lassen eingeschlossene Luft und Gase während des Formens entweichen und verhindern so Defekte wie Lufteinschlüsse oder Hohlräume im Endprodukt.
Abschiedsgruß: Die Trennlinie gibt an, wo sich die Form trennt, um das Formteil freizugeben. Sie muss gut definiert sein und darf die Ästhetik und Funktionalität des Produkts nicht beeinträchtigen.
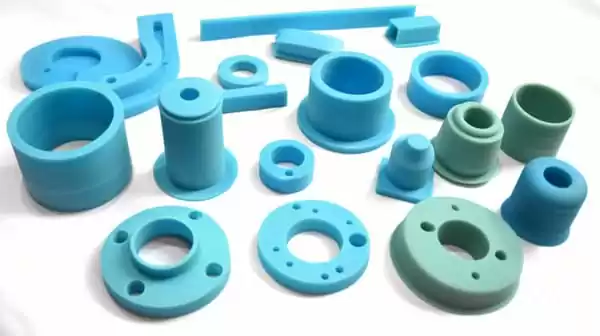
Tor-Design: Der Anschnitt dient als der Punkt, durch den das geschmolzene Material in den Formhohlraum eintritt. Ein sorgfältiges Anschnittdesign gewährleistet eine gleichmäßige Füllung und minimiert Fehler. Zu den Anschnittarten gehören Kantenanschnitte, Stiftanschnitte und Tunnelanschnitte.
Kühlsystem: Effiziente Kühlkanäle in der Form tragen dazu bei, dass das Formteil schnell erstarrt, Verformungen verhindert und die Zykluszeiten verkürzt werden.
Oberfläche: Je nach den Anforderungen des Produkts kann die Oberfläche des Formhohlraums poliert, strukturiert oder beschichtet werden, um die Ästhetik des Endprodukts zu verbessern.
3. Wie berechnet man die Tonnage beim Formpressen?
Tonnage in Formpressen bezieht sich auf die Kraft, die erforderlich ist, um das Material im Formhohlraum zu verdichten. Sie ist ein entscheidender Faktor für das Erreichen einer angemessenen Materialverdichtung und Teiledichte. Um die Tonnage zu berechnen, können Sie die folgende Formel verwenden:
Tonnage = Druck × Fläche
Druck: Der Druck wird normalerweise in PSI (Pounds per Square Inch) gemessen.
Gebiet: Fläche stellt die projizierte Fläche des zu formenden Teils dar.
Durch die Berechnung der erforderlichen Tonnage können die Hersteller sicherstellen, dass die im Formpressverfahren eingesetzte Presse die erforderliche Kraft ausübt, um die gewünschte Kompression und Dichte des Materials im Formhohlraum zu erreichen.
Die Gestaltung des Formhohlraums ist der Eckpfeiler des erfolgreichen Formpressens. Sie bestimmt die Produktqualität, Präzision und Konsistenz. Die Konstruktion von Presswerkzeugen umfasst Geometrie, Entlüftung, Trennlinien, Anschnittkonstruktion, Kühlsysteme und Oberflächenbehandlung - allesamt auf die spezifischen Anforderungen des gewünschten Teils zugeschnitten. Das Verständnis und die Berechnung der Tonnage stellen außerdem sicher, dass das Formpressverfahren optimal funktioniert und qualitativ hochwertige Komponenten produziert, die die Industriestandards erfüllen oder übertreffen.
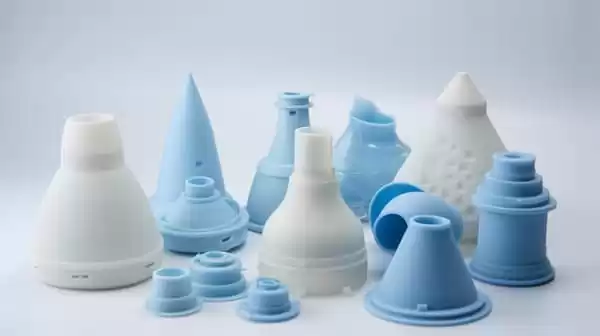
Schlussfolgerung
In dieser umfassenden Untersuchung des Formpressens und der Konstruktion von Formhohlräumen haben wir die komplizierte Welt eines Herstellungsprozesses aufgedeckt, der unauslöschliche Spuren in einer Vielzahl von Branchen hinterlässt.
Zum Abschluss unserer Untersuchung möchten wir die Leser ermutigen, das Formpressen für ihre Fertigungsanforderungen in Betracht zu ziehen. Seine Präzision, Vielseitigkeit und Fähigkeit, qualitativ hochwertige Komponenten zu liefern, machen es zu einem Verfahren, das es wert ist, für eine breite Palette von Anwendungen erforscht zu werden. Indem sie sich das Formpressen zu eigen machen und die Leistungsfähigkeit der richtigen Formhöhlenkonstruktion nutzen, können Hersteller eine Welt der Möglichkeiten erschließen und Produkte herstellen, die nicht nur die höchsten Standards in der Fertigung erfüllen, sondern übertreffen.