Introduction
Mold cavity design stands as the linchpin of successful compression molding, holding the power to shape the future of numerous industries. This critical facet of manufacturing is not to be underestimated, as it wields the capability to deliver high-quality, consistent results—a true testament to its significance.
In a world where innovation and precision reign supreme, compression molding emerges as a versatile and indispensable manufacturing process. With applications spanning across a multitude of industries, including automotive, electronics, and consumer goods, it plays a pivotal role in shaping the products we rely on daily. From automotive components engineered for performance and durability to electrical insulation materials ensuring our safety, compression molding touches nearly every facet of our lives.
As we delve deeper into the realm of mold cavity design for compression molding, we embark on a journey that unravels the intricate tapestry of this process. Exploring its nuances, we’ll unveil how the right mold cavity design can unlock a world of possibilities, crafting products that not only meet but often exceed our expectations. Join us in this exploration of the art and science behind compression molding, where mold cavity design is the compass guiding us toward the epitome of manufacturing excellence.
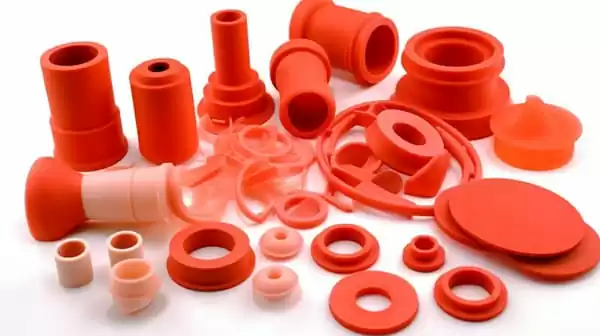
Understanding Compression Molding processes
Compression molding is a versatile and widely utilized manufacturing process with applications across various industries. To grasp the essence of this technique, it’s crucial to break it down into its core components.
1. The Compression Molding Process:
At its heart, compression molding is a process that involves shaping materials using heat and pressure. The steps involved are as follows:
Material Preparation: The process begins with the preparation of raw materials, typically in the form of granules, pellets, or sheet molding compounds (SMC).
Heating: The mold, often consisting of two halves, is closed around the material. Heat is then applied to soften or melt the material, making it pliable.
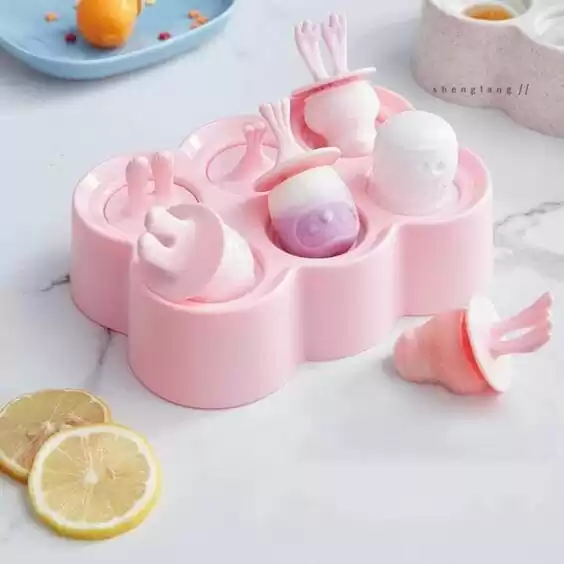
Compression: Pressure is applied to the mold cavity, compacting the material and taking on the desired shape of the final product.
Cooling: Once the material has assumed the mold’s shape, it is cooled to solidify and the heated mold harden, maintaining the desired form.
Ejection: Finally, the molded part is ejected from the mold cavity, ready for further processing or use.
2. Compression Mold Design:
The foundation of a successful compression molding operation lies in the design of the mold cavity. Compression mold design encompasses several crucial elements:
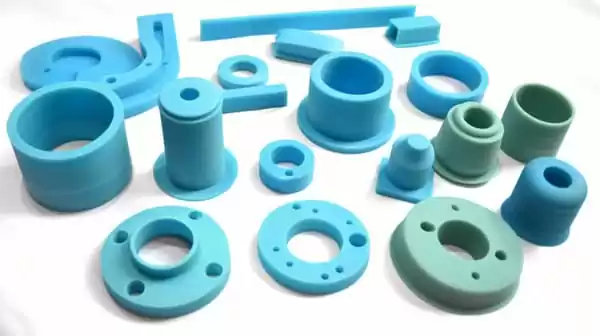
Geometry: The mold cavity’s geometry must precisely match the intended shape of the final product. This includes considerations like part thickness, draft angles, and undercuts, ensuring smooth ejection.
Venting: Effective venting is essential to allow trapped air and gases to escape during molding. Proper venting prevents defects like air pockets or voids in the final product.
Parting Line: The parting line designates where the mold separates to release the molded part. It must be well-defined and unobtrusive to the product’s aesthetics and functionality.
Gate Design: The gate serves as the point through which the molten material enters the mold cavity. Careful gate design ensures uniform filling and minimizes defects. Gate types include edge gates, pin gates, and tunnel gates.
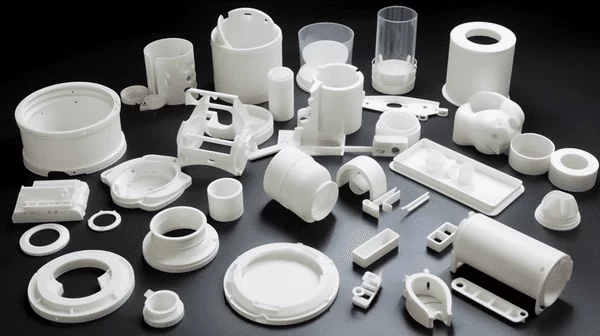
Cooling System: Efficient cooling channels within the mold help solidify the molded part quickly, prevent warping or distortion, and improve cycle times.
Surface Finish: Depending on the product’s requirements, the mold cavity’s surface finish can be polished, textured, or coated to enhance the final product’s aesthetics.
3. Materials Used in Compression Molding:
Compression molding is compatible with a wide range of materials, including thermoset materials like epoxy resin, silicone rubber, and polymer resins. It particularly excels with fiber-reinforced resin materials, such as glass fiber or carbon fiber composites. These materials offer excellent mechanical performance, temperature resistance, and chemical resistance.
4. Advantages and Disadvantages of Compression Molding:
Advantages:
Cost-Effective: Compression molding often utilizes recycled thermoplastic materials and materials with relatively low melting points, reducing production costs.
Wide Temperature Range: It can create molds for parts with wide temperature ranges and high chemical resistance requirements.
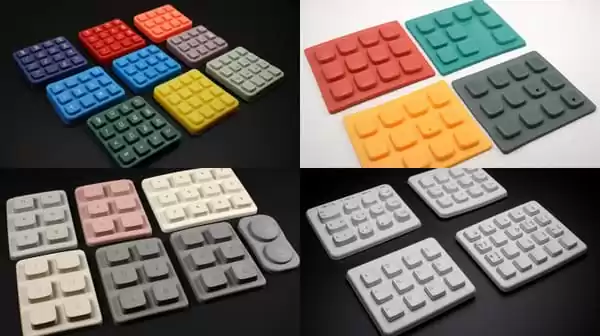
Composite Materials: Ideal for working with composite materials like glass fibers and carbon fibers, enabling the production of high-strength, lightweight components.
Disadvantages:
Complex Geometries: May not be suitable for producing components with extremely complex geometries or tight tolerances.
Slower Process: Compression molding can be slower compared to other molding processes like injection molding, which can impact production rates.
In essence, understanding the compression molding process, the role of compression mold design, the versatility of materials used, and the pros and cons of this method lays the groundwork for harnessing its potential across various industries. It’s a process that combines precision, creativity, and engineering to mold raw materials into the products that make our world function.
Section 2: Types of Compression Molding
In the realm of compression molding, mold types play a pivotal role in determining the outcome of the process. The choice of mold can significantly impact product quality, complexity, and production efficiency. Let’s delve into the three primary mold types for compression molding and unravel their characteristics and applications:
1. Open-Flash Mold:
Characteristics:
Flash Management: The defining characteristic of open-flash molds is the allowance for excess material, known as “flash,” to escape during the compression molding process. This flash is later trimmed off, leaving behind the desired product.
Applications:
Low Precision Parts: Open-flash molds are commonly employed when precision is not a critical requirement. They are ideal for producing parts where a high degree of dimensional accuracy is not necessary.
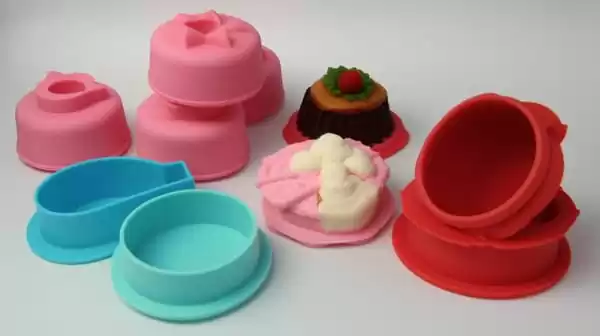
2. Closed Mold:
Characteristics:
Precision: Closed molds are designed to maintain a high degree of precision throughout the compression molding process. They are engineered to minimize flash and ensure tight tolerances in the final product.
Applications:
Critical Precision: Closed molds find their niche in applications where precision is paramount. They are employed in scenarios where product consistency and adherence to tight tolerances are non-negotiable.
3. Semi-Closed Mold:
Characteristics:
Hybrid Approach: Semi-closed molds combine elements of both open and closed molds. While they allow some flash to escape, they also provide control over part dimensions.
Applications:
Balanced Requirements: Semi-closed molds are chosen when there is a need for moderate precision, and flash management is essential but not as critical as in closed molds. They offer a balanced approach that suits a wide range of product requirements.
In essence, the choice between open-flash, closed, and semi-closed molds in compression molding depends on the specific demands of the product being manufactured. Open-flash molds are suitable when precision is not the top priority, closed molds excel in applications requiring utmost precision, and semi-closed molds strike a balance between these two extremes. By selecting the appropriate mold type, manufacturers can optimize their compression molding processes to meet the unique needs of their products and industries.
Section 3: Types of Compression Molding Materials
In the world of compression molding, the choice of materials for compression molded products is pivotal in determining the final product’s properties and characteristics. Two commonly used materials in this process are Sheet Molding Compound (SMC) and Bulk Molding Compound (BMC). Let’s delve into these materials and shed light on the advantages of utilizing thermoset materials in compression molding:
1. Sheet Molding Compound (SMC):
Characteristics:
Fiber-Reinforced: SMC is a fiber-reinforced material that combines thermosetting resins with chopped glass fibers. This reinforcement imparts excellent strength and stiffness to the material.
Sheet Form: SMC is typically supplied in the form of flat sheets or rolls. These sheets are pre-impregnated with resin and can be easily cut and layered within the mold cavity.
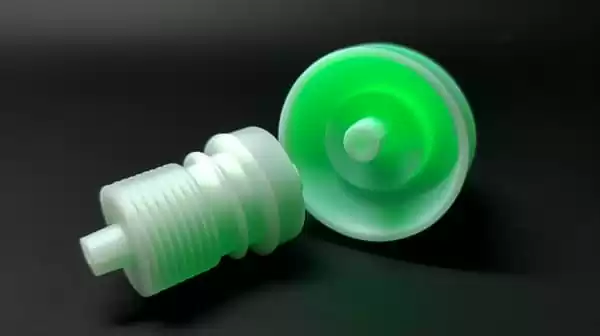
Applications:
Automotive Components: SMC is extensively used in the automotive industry to manufacture components such as body panels, hoods, and exterior trim due to its high strength, impact resistance, and corrosion resistance.
Electrical Enclosures: Its electrical insulating properties make SMC a preferred choice for electrical enclosures and panels.
2. Bulk Molding Compound (BMC):
Characteristics:
Thermosetting Material: BMC is also a thermosetting material, composed of a mixture of thermosetting resin, filler materials, and reinforcement fibers (typically glass).
Granular Form: Unlike SMC, BMC is supplied in a granular form. This granular consistency allows for precise molding of complex shapes.
Applications:
Automotive Industry: BMC finds its place in the automotive industry for producing complex components such as valve covers, intake manifolds, and under-the-hood parts. Its dimensional stability and resistance to chemicals and heat make it an ideal choice.
Electrical and Electronics: BMC is used in electrical and electronics applications due to its excellent electrical insulating properties and flame resistance.
Advantages of Using Thermoset Materials in Compression Molding:
The choice of thermoset materials, such as those used in SMC and BMC, offers several advantages in the compression molding process:
Temperature Resistance: Thermoset materials excel in high-temperature environments. They can withstand elevated temperatures without deforming, making them suitable for applications that require resistance to heat and thermal cycling.
Chemical Resistance: These materials exhibit excellent chemical resistance, making them ideal for applications where exposure to various chemicals is expected.
Dimensional Stability: Thermoset materials maintain their shape and dimensions under pressure and high temperatures, ensuring consistency and precision in the final product.
Electrical Insulation: Both SMC and BMC possess outstanding electrical insulating properties, making them indispensable in electrical and electronics applications.
Complex Shapes: The granular form of BMC and the layering capability of SMC enable the molding of complex and intricate shapes, providing versatility in design.
In summary, Sheet Molding Compound (SMC) and Bulk Molding Compound (BMC) are exemplary examples of thermoset materials used in compression molding. Their inherent advantages, including temperature and chemical resistance, dimensional stability, and electrical insulation properties, make them valuable choices in the manufacturing of diverse products across industries. The utilization of these materials, combined with the precision of compression molding, results in high-quality components with tailored characteristics and performance.
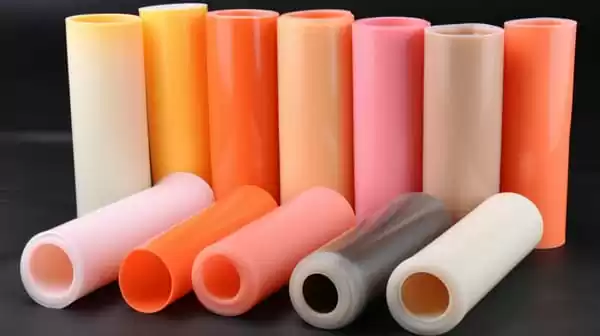
Section 4: The Compression Molding Process Itself
To truly grasp the intricacies of compression molding, it’s essential to delve into the core of the process itself. In this section, we will explore the essential components of the compression mold, understand the significance of its high-pressure nature, and unravel the curing process responsible for solidifying the molded part:
1. Components of the Compression Mold:
The compression mold is the heart of the compression molding process. It consists of several crucial components:
Mold Cavity: This is where the magic happens. The mold cavity defines the shape and dimensions of the final product. It must be meticulously designed to accommodate the desired geometry, including factors like part thickness, draft angles, and surface finish.
Heating System: Compression molds are equipped with a heating system that raises the temperature within the mold cavity. This heating is essential for softening or melting the raw material to make it pliable and amenable to molding.
Cooling System: Efficient cooling channels or systems run through the mold to rapidly cool and solidify the molded part once it has taken shape. Proper cooling ensures the preservation of the desired form and prevents warping or distortion.
Pressure Mechanism: Compression molding is known for its high-pressure nature. The mold incorporates a mechanism for applying substantial pressure to the mold cavity. This pressure is responsible for compacting the material, ensuring it fills every nook and cranny of the mold, and ultimately defining the part’s density and structural integrity.
2. The High-Pressure Nature of Compression Molding:
Compression molding is characterized by its inherent high-pressure nature, which plays a pivotal role in shaping the final product. The significance of this high-pressure environment lies in several aspects:
Material Compression: The high pressure applied during compression molding compacts the material within the mold cavity. This compression ensures that the material conforms precisely to the mold’s geometry, resulting in excellent part reproduction and dimensional accuracy.
Density Control: The pressure dictates the density of the final product. By carefully controlling the pressure, manufacturers can achieve specific material densities, which influence the part’s mechanical properties and performance.
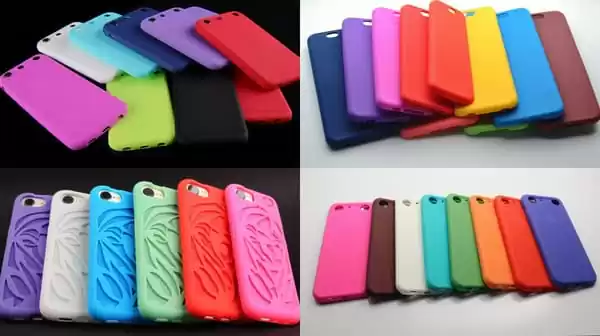
Uniform Filling: High pressure aids in uniformly filling the mold cavity. This minimizes the risk of voids, air pockets, or other defects in the final product, contributing to its quality.
3. The Curing Process:
After the material has assumed the desired shape within the mold cavity, the curing process comes into play. Curing is the step responsible for solidifying the molded part and giving it its final structural integrity. Here’s how it works:
Heat and Pressure: The elevated temperature within the mold, in conjunction with the applied pressure, triggers a chemical reaction in the thermosetting material. This reaction causes the material to harden and set its shape.
Cooling: Once the curing process is complete, the mold’s cooling system is activated to rapidly reduce the temperature. This cooling phase helps solidify the part, making it rigid and ready for ejection from the mold.
In conclusion, understanding the components of the compression mold, the high-pressure environment’s significance, and the curing process provides valuable insights into the mechanics of compression molding. This intricate interplay of heat, pressure, and precision engineering enables the production of high-quality components with the desired shape, density, and mechanical properties. It is the embodiment of manufacturing excellence, delivering products that meet the highest standards of performance and reliability.
Section 5: Designing the Mold Cavity
The mold cavity is at the very heart of the compression molding process. In this section, we’ll explore the critical role of mold cavity design, define compression mold design, and delve into the calculation of tonnage—a crucial factor in compression molding:
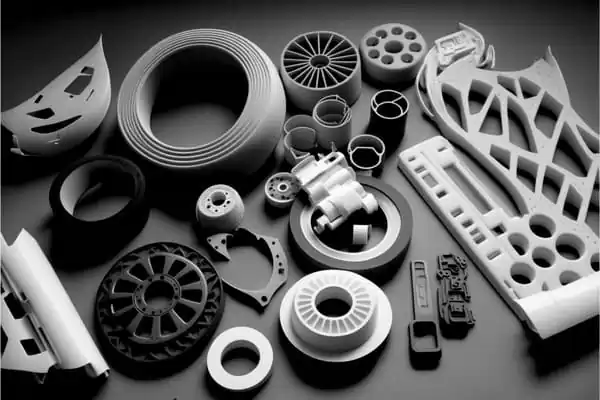
1. The Importance of Mold Cavity Design:
The design of the mold cavity is paramount in ensuring the success of the compression molding process. Here’s why it holds such significance:
Precision and Consistency: The mold cavity defines the final shape and dimensions of the product. A well-designed cavity ensures precision and consistency in every molded piece, meeting the highest quality standards.
Material Flow: The mold cavity’s geometry determines how the material flows and fills the mold. An improper design can lead to uneven material distribution, resulting in defects or inconsistencies in the final product.
Venting and Cooling: Effective venting channels or grooves in the mold cavity allow trapped air and gases to escape, preventing defects like air pockets. The cooling system within the cavity helps solidify the part quickly, reducing cycle times.
Surface Finish: Mold cavity design also plays a role in achieving the desired surface finish on the molded part. It can be polished, textured, or coated to meet specific aesthetic and functional requirements.
2. What is Compression Mold Design?
Compression mold design is the process of meticulously creating a mold cavity that can withstand the high pressures and temperatures inherent in compression molding. It encompasses several critical aspects:
Geometry: The mold cavity must precisely match the intended shape of the final product. This includes considering part thickness, draft angles, and undercuts for smooth ejection.
Venting: Proper venting channels or grooves allow trapped air and gases to escape during molding, preventing defects like air pockets or voids in the final product.
Parting Line: The parting line designates where the mold separates to release the molded part. It must be well-defined and unobtrusive to the product’s aesthetics and functionality.
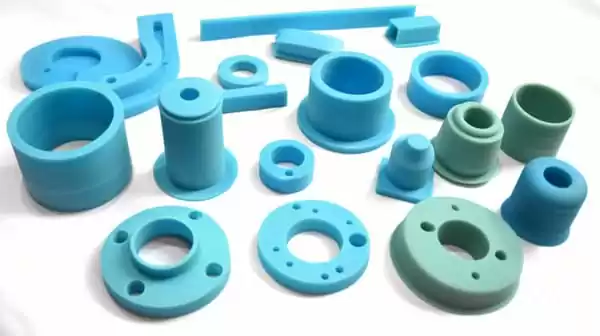
Gate Design: The gate serves as the point through which the molten material enters the mold cavity. Careful gate design ensures uniform filling and minimizes defects. Gate types include edge gates, pin gates, and tunnel gates.
Cooling System: Efficient cooling channels within the mold help solidify the molded part quickly, prevent warping or distortion, and improve cycle times.
Surface Finish: Depending on the product’s requirements, the mold cavity’s surface finish can be polished, textured, or coated to enhance the final product’s aesthetics.
3. How to Calculate Tonnage for Compression Molding:
Tonnage in compression molding refers to the force required to compress the material within the mold cavity. It’s a crucial factor in achieving proper material compression and part density. To calculate tonnage, you can use the following formula:
Tonnage = Pressure × Area
Pressure: Pressure is typically measured in PSI (Pounds per Square Inch).
Area: Area represents the projected area of the part being molded.
By calculating the required tonnage, manufacturers can ensure that the press used in the compression molding process exerts the necessary force to achieve the desired compression and density of the material within the mold cavity.
In essence, mold cavity design is the cornerstone of successful compression molding. It dictates product quality, precision, and consistency. Compression mold design encompasses geometry, venting, parting lines, gate design, cooling systems, and surface finish—all tailored to meet the specific requirements of the desired part. Understanding and calculating tonnage further ensures that the compression molding process operates optimally, producing high-quality components that meet or exceed industry standards.
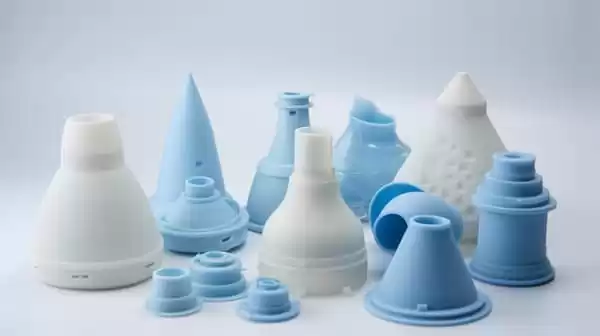
Conclusion
In this comprehensive exploration of compression molding and mold cavity design, we’ve uncovered the intricate world of a manufacturing process that leaves an indelible mark on a multitude of industries.
As we conclude our exploration, we encourage readers to consider compression molding for their manufacturing needs. Its precision, versatility, and ability to deliver high-quality components make it a process worth exploring for a wide range of applications. By embracing compression molding and harnessing the power of proper mold cavity design, manufacturers can unlock a world of possibilities, crafting products that not only meet but exceed the highest standards of excellence in manufacturing.