Silicone products are an important part of many industries because they can be used in many different ways, resist wear and tear, and remain strong when direct heat. Whether you work in electronics manufacturing, need silicone for precision circuits, or make automotive parts that must perform well at high speeds. Understanding and optimizing silicone cure times can be the difference between meeting deadlines and losing productivity.
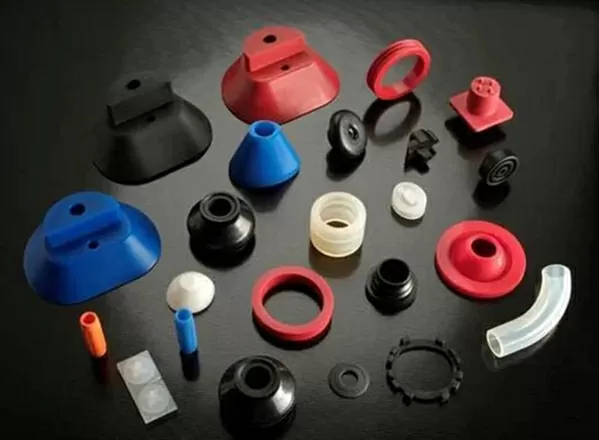
Silicone is found in a variety of products from medical devices to kitchen tools. The material is popular because it can withstand high temperatures, is durable and bends easily, but there’s one aspect of it that can cause problems in fast-paced manufacturing processes: how quickly it sets (cures) after application quick.
Today, we’ll take a closer look at the complex molding process behind silicone curing and how to speed up the entire process during the final molding stage while still ensuring the end result is just right. If you want a way to shorten the cure time of your silicone without compromising quality, then read on: because what follows is an exhaustive examination that will take you inside the inner workings of accelerated cure.
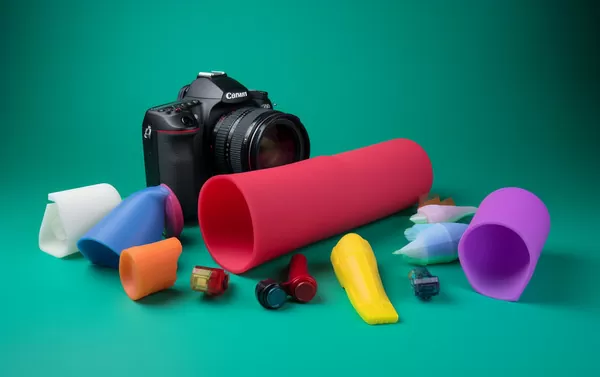
Understanding the Silicone Curing Process
The curing process of silicone is not a consistently simple process and can be affected by many different factors. Generally speaking, silicone cures by contact with moisture, and the silane molecules in the silicone cross-link with each other when they come into contact with water molecules. This cross-linking forms a three-dimensional network that transforms the material from a liquid into a rubbery solid or elastomer. Because of this structure, silicones can be bent or stretched but always return to their original shape; this also means they can withstand extremely high and low temperatures better than most other materials.
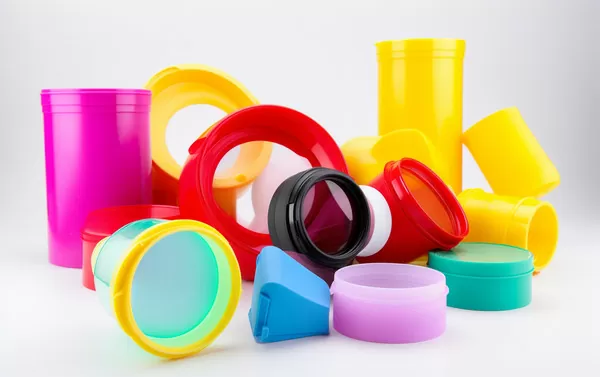
There are two main types of moisture-curable silicones:
1. Acetoxy silicones: These silicones release acetic acid during the curing process and can emit a vinegar-like odor. Additionally, the acidic nature of this by-product has the potential to corrode certain metals. However, on the plus side, they tend to cure faster than their non-acetoxy counterparts.
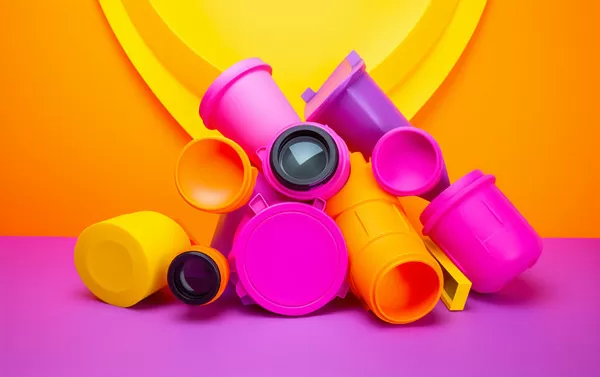
2. Alkoxy Silicones: Unlike acetoxy silicones, these types of silicones do not excrete any acid when drying – only the alcohol. This means that there is no risk of corrosive effects caused solely by acidic residues (although other chemical changes may still occur).
Knowing whether your silicone sealant falls into a certain camp is important for things like ensuring influence curing time impacting technology performs well under real-world conditions.
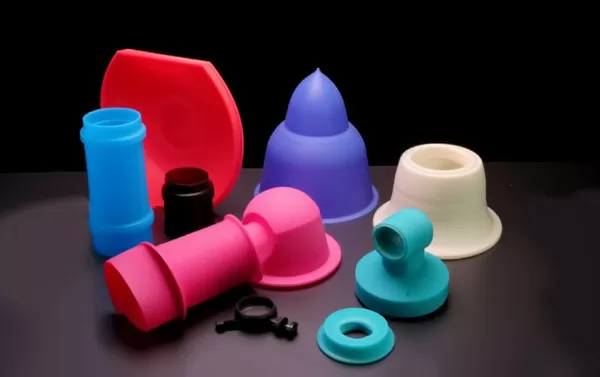
Controlling Environmental Factors
The environmental conditions under which silicones cure completely can significantly impact the speed of the process. These factors include:
1. Humidity
Controlling humidity levels during the curing process can have a significant impact on the speed of curing: in areas with higher humidity, there are more water molecules around, which speeds up the reaction. Conversely, if the weather is very dry, the curing process will take longer. Fortunately, there are ways to help adjust this, and it can be as simple as using a humidifier throughout the work area or while the silicone is curing, or curing the silicone in a humidity chamber.
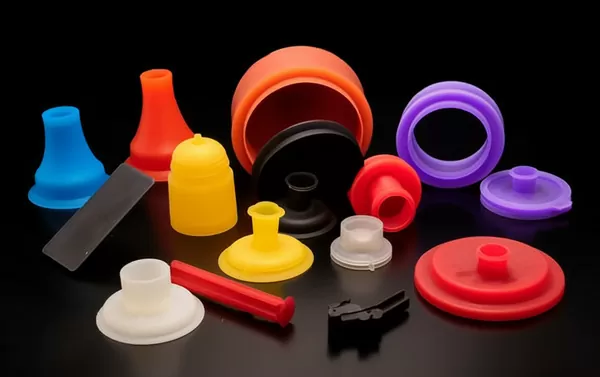
2. Temperature
Increased temperature generally results in a shortened cure duration due to increased kinetic energy due to increased molecular motion during cure. However, although high temperatures can shorten the curing time of silicone, it may also lead to potential problems with product quality after molding. But usually, a moderate increase in heat speeds things up nicely and doesn’t cause any trouble at all.
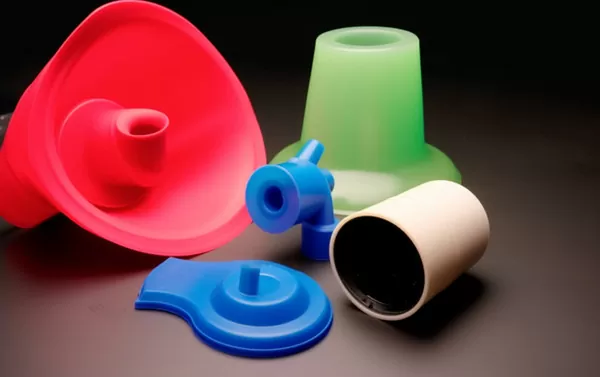
3. Oxygen Inhibition
Oxygen inhibition can occur when silicones are exposed to air. This means that, especially in thicker projects, the curing reaction may not be fully completed. One possible solution to this problem is to use a catalyst or apply a curing agent to create an oxygen barrier over the curing surface, promoting uniform cure.
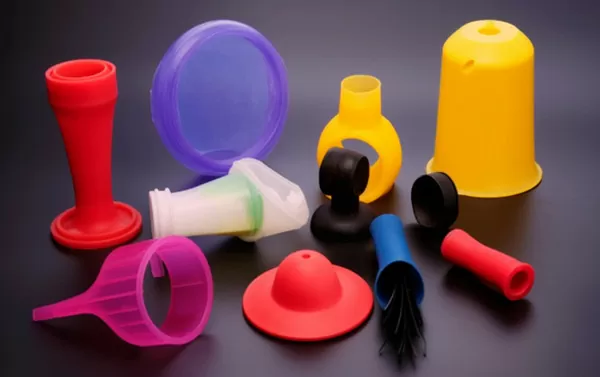
Chemical Accelerators and Catalysts
Certain types of silicones can be accelerated using chemical compounds that promote the cross-linking reaction. These include:
1. Platinum Catalysts
Platinum catalysts are often used to accelerate the curing process of addition-cure silicone rubbers. They are often chosen because their curing systems are much faster than tin catalysts. By adding a platinum catalyst, the cure time of these types of silicones can be significantly reduced.
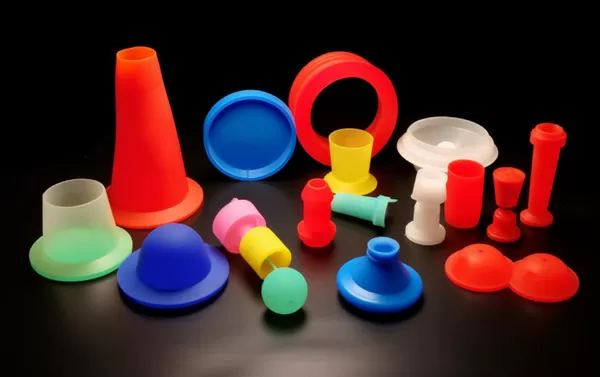
2. Tertiary Amines
Tertiary amines can accelerate the curing process of tin-catalyzed condensation-cure silicones. It works by acting as an accelerator and promoting dehydrogenation (loss of hydrogen atoms) of the silicone, allowing more cross-linking to occur.
However, it should be noted that the use of accelerators may significantly shorten the pot life of the product.
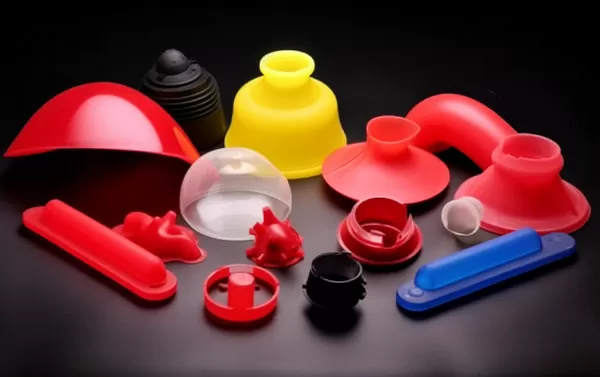
Mechanical Techniques
Mechanical techniques can also be employed to speed up curing.
1. Vibration and Agitation
When vibration or stirring is applied, curing time can be shortened by increasing the speed at which molecules move and interact with each other. This comes in handy when you want to reduce the time it takes for the silicone to flow into its final shape.
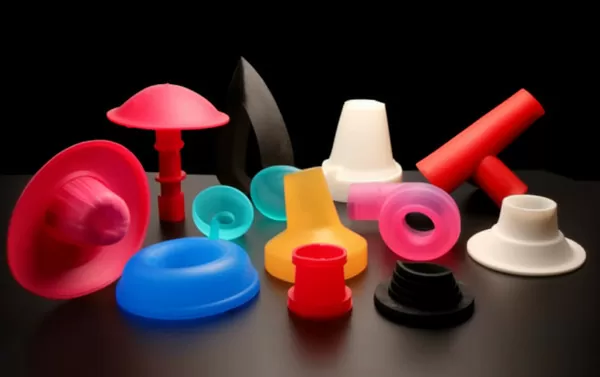
2. Reduced Cure Thickness
Another way to speed up the curing process is to make the silicone thinner. Since the reaction takes place over a shorter distance, the overall time required is also shorter; in fact, thin layers cure faster than thick layers.
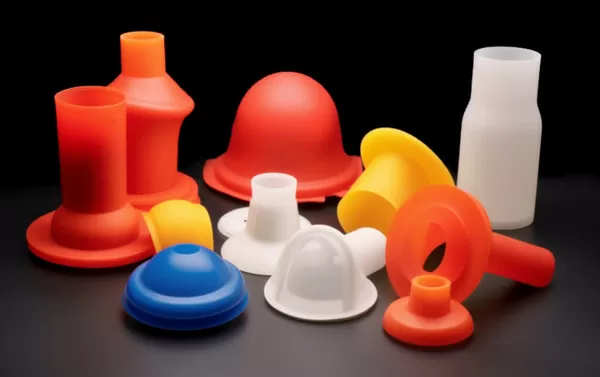
Light-Induced Curing
Silicones, especially UV-curable silicones, can be cured by exposure to certain wavelengths of light. Using this technique allows great control over when and where curing starts and stops, which often means curing can be completed in seconds or less. But you need the right type of light at the right intensity, and concepts like how long the fluctuations last.
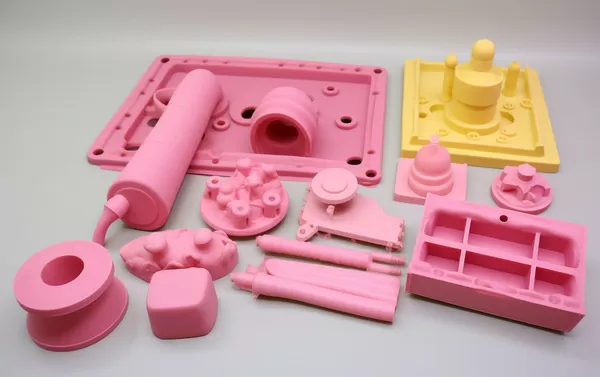
Conclusion
The cure speed of silicone is an important factor to consider in many industries. Being able to cure silicone faster has several benefits: it can increase productivity levels, increase efficiency (meaning less energy wasted), and even open the door to new types of products. However, it’s not just about speed, quality must be maintained in the process. We discuss some methods that can be used to control and accelerate the rate at which these materials harden. But remember, all strategies need to be carefully considered, because while speed may well be desirable from a business perspective, it must not come at the expense of product integrity and end-user security. Increasing the curing speed of silicone, whether in silicone sealants or silicone adhesives, involves addressing their inherently more complex chemical structure.