From daily life to the food field to the aviation field, the use of silicone rubber products has grown exponentially in various fields. Their wide range of uses and excellent versatility make them very popular. However, bubbles that may appear on or inside silicone rubber products during the production process may cause problems when using the product. If they contain air bubbles, their integrity may be compromised. This blog post will delve into why such bubbles appear during the manufacturing process; what are the risks of using defective materials? Also important are tips on how to minimize eliminate bubbles when producing silicone.
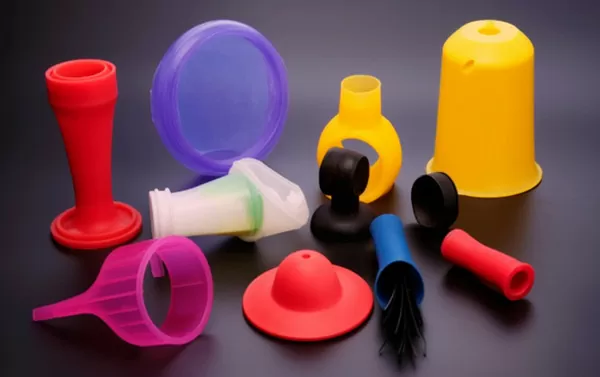
Understanding the Bubbles in Silicone Rubber
Identifying the Catalysts
Three types of bubbles may appear in silicone rubber products. They may appear when the materials are mixed, during the molding process, or after molding. In each case, there could be several reasons for these unwanted bubbles:
Surface Contaminants: Sometimes dirt or other contaminants (such as water) on the mold surface or the tool itself can cause bubbles to form as solidification occurs around these impurities.
Air Trapped During Mixing: If the compound is not mixed thoroughly, tiny residue from incomplete mixing may create air bubbles when casting resin/injected into the mold.
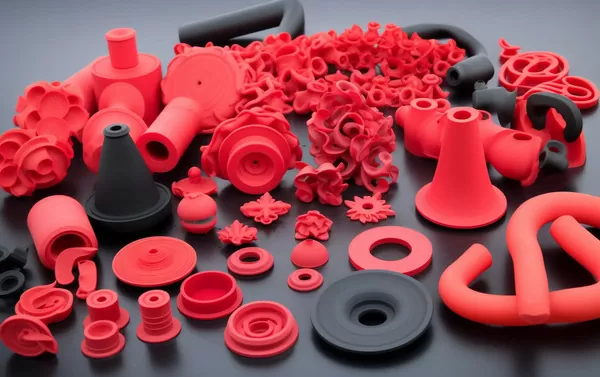
Inadequate Degassing: Many manufacturers use a vacuum degassing process to remove air bubbles from materials. Insufficient degassing can cause traces of air to be pushed into the silica gel, forming bubbles as it expands at higher temperatures.
The Impact on Product Quality
Air bubbles can have a variety of negative effects on silicone rubber products. These include
Aesthetics: Bubbles can ruin a product’s surface finish, making it look defective and therefore unsaleable based on appearance alone.
Mechanical Properties: Especially in medical or aerospace applications, air bubbles can significantly weaken the material. This in turn affects tear resistance and tensile strength.
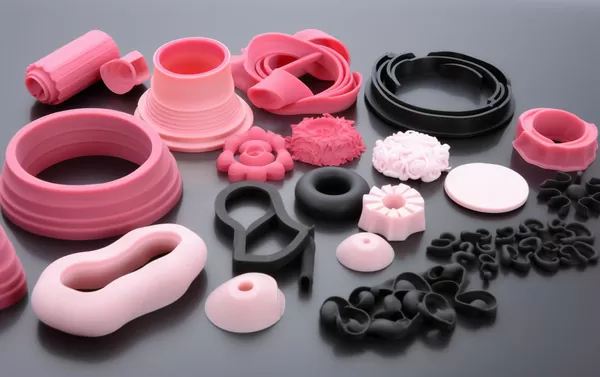
Insulation and Sealing: Products that need to be used under high air pressure or sealed products must prevent any moisture from getting into them at all costs, while both types need to be sealed against gases or dust. Bubbles can become conduits for moisture, dust or gases, compromising insulation and sealing properties.
The Principle of Silicone Bubble Generation
Silicone rubber is an amazing substance that few of its kind can match in terms of its benefits and performance in use. However, there is a problem that often occurs in the production process of silicone rubber products: bubbles will form on or inside the product during curing. The reasons may include the following: whether it occurs due to the presence of volatile compounds in the materials used; air entrapment inside or the materials are not mixed together correctly. These causes can cause defects in finished products and can also make them look inferior by creating surface imperfections.
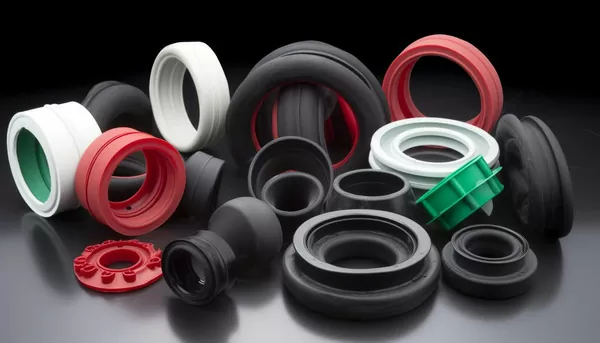
In order to combat this, it’s essential to understand the root of the problem. For instance, too rapid a curing time can trap gasses that would otherwise escape gradually, leading to bubbles. On the other hand, differential atmospheric pressure across the mold or poor degassing of the material pre-casting can create voids that turn into bubbles as the silicone cures.
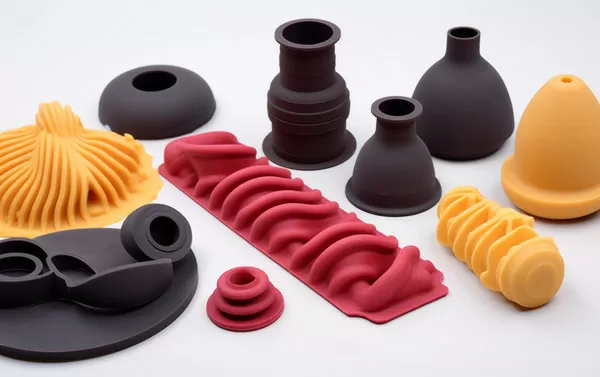
Why Bubbles are Bad News for Silicone Rubber?
Bubbles in silicone rubber can also cause a number of problems that reduce the value of your product. , the possible impacts include:
This weakens the overall strength of the rubber. Reduces its tear strength and tensile strength, making it easier to break. Chemical resistance becomes poorer, causing it to wear faster when exposed to certain chemicals. Preventing its normal insulation. Surface imperfections that cannot be sanded away. It is crucial to understand the adverse effects of bubbles. It’s not just about ensuring good looks; it’s about delivering products that meet the functionality and safety standards that customers rely on.
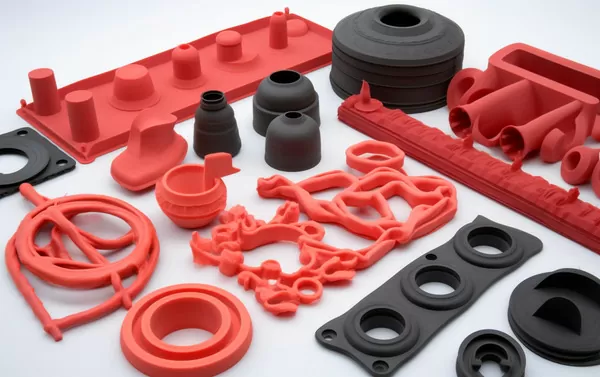
Quality Control for Silicone Rubber
Quality control is as important as the production process itself. By conducting frequent visual inspections, performing tensile strength tests, and even using microscopes to study surfaces on a microscopic level, you can not only spot bubbles but also ensure that only products that meet your high standards leave your facility.
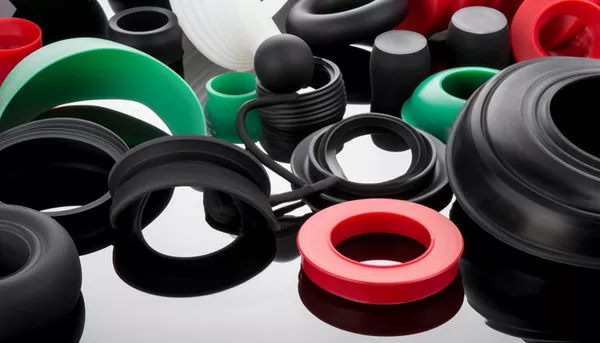
What Causes Bubbles on the Surface of Silicone Rubbers Products?
1. Insufficient exhaust: After the liquid silicone raw material is placed in the molding mold, a lot of air will be brought in at the moment of mold closing, and the air cannot be integrated with the silicone raw material. If the air is not discharged, it will cause Bubbles appear on the surface of silicone buttons after molding.
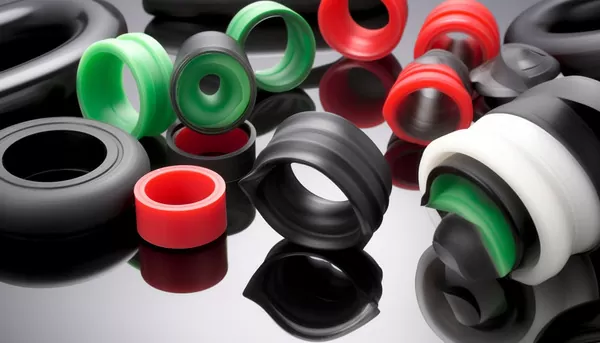
2. The vulcanization temperature is too low: The vulcanization temperature is an important parameter when molding silicone rubber. Usually silicone products are set at 160~200 degrees Celsius. However, sometimes the mold takes a long time due to too long out-of-mold operation time or other reasons. If the vulcanizer is not turned on for heating, the temperature of the silicone mold will be lower than the vulcanization temperature of the silicone. This will cause bubbles in the molded product. For this, we only need to increase the molding temperature, or put the empty mold into the machine to heat it for a period of time before operating to solve the problem.
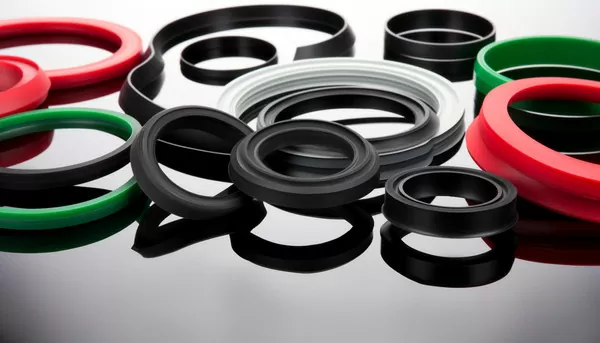
3. The vulcanization temperature is too high: I just mentioned that too low a vulcanization temperature will cause silicone molding bubbles. In fact, in many cases, too high a molding temperature will also cause silicone molding bubbles. Why? I personally understand it this way. When the molding temperature is too high, the silicone raw material on the surface has begun to mold during the mold closing and pressurization process. At this time, the air has been trapped inside and is difficult to discharge, so molding bubbles will be caused. For this reason, the molding temperature only needs to be appropriately lowered.
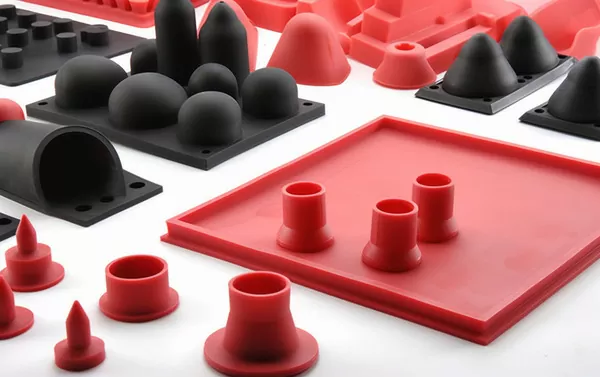
4. The vulcanization time is too short: Like the vulcanization temperature, the vulcanization time is also one of the important parameters for silicone molding. The length of the vulcanization time determines whether the silicone can be completely vulcanized. The structure of the mold is unreasonable: If the design of the silicone mold is unreasonable, it will also cause bubbles in the silicone molding. Failure to grasp the vacuuming time and vacuuming intensity during the use of the silicone vacuum machine will lead to obvious quality problems with bubbles.
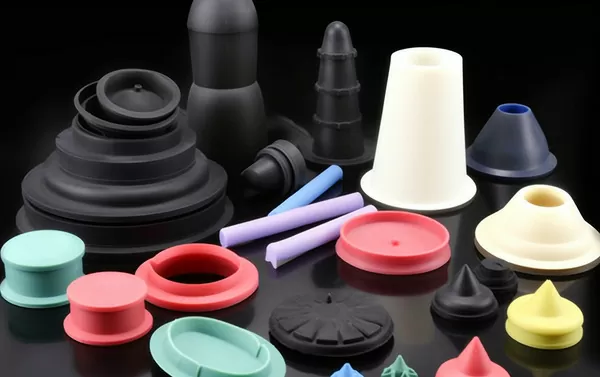
5. Just set the program of the silicone vacuum machine at the right time and grasp the intensity of extraction to reduce the source of bubbles and reduce defective products. After using the silicone vacuum machine to extract the vacuum, start filling the mold. During the filling process, be sure to remember not to fill too little. , less material is wasted, more filling is required and more material can be recycled, because the liquid silicone and PVC flow before the hot pressing is fixed, which can effectively reduce the gap between the mold and the product and reduce bubbles The presence. The mold was not cleaned thoroughly during cleaning. When cleaning the abrasive tools, pay attention to the method and try to scrub gently with soft fabric to avoid deformation of the abrasive tools.
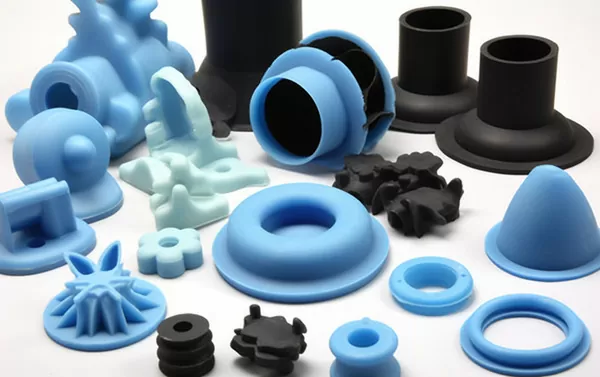
How to Reduce Bubbles?
Reducing air bubbles during production is a complex issue. Careful consideration needs to be given to which materials to use, which equipment works best, and how these factors interact during curing (the process by which silicone becomes solid).
1. Materials Matter: Starting with the source material, confirm that your silicone compound has been formulated to minimize volatile content. This will help minimize the possibility of air bubbles during subsequent production processes. You can also switch to low-viscosity silicones because they create fewer bubbles during curing, or explore materials with high tear strength, tensile strength, and elongation at break; such materials will also reduce bubbles in the finished product.
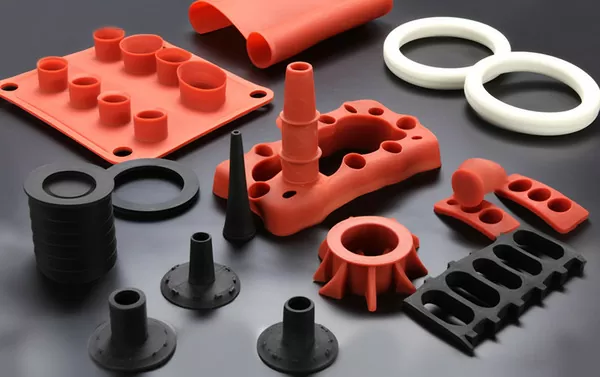
2. Degassing Excellence: Next review the degassing procedures during production. Are they thorough enough and effective? Typically used to remove air and potential gas issues before a batch of pre-poured silicone reaches the mold/cavity. The size of the vacuum chamber must be suitable for various factors such as the volume of the product, and the total time spent on the procrastination process should be so done that once cured, there will not be any residual gas etc. left in it.
When degassing silicone rubber, a vacuum chamber is often used. Here are some effective method you can make this process better:
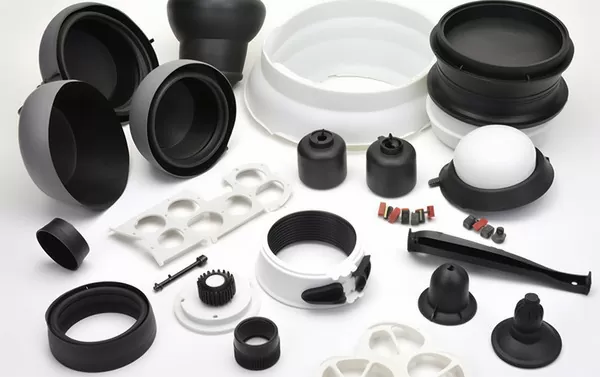
Altitude and Compression: Silicone is more likely to trap air at higher altitudes. Please check to make sure your materials and degassing equipment are at sea level.
Timing and Technique: For best results, make sure the silicone is degassed immediately before pouring—and use proper technique while doing so.
Headroom: Do not completely fill the degassing chamber. Leave room for expansion so trapped air has somewhere to go.
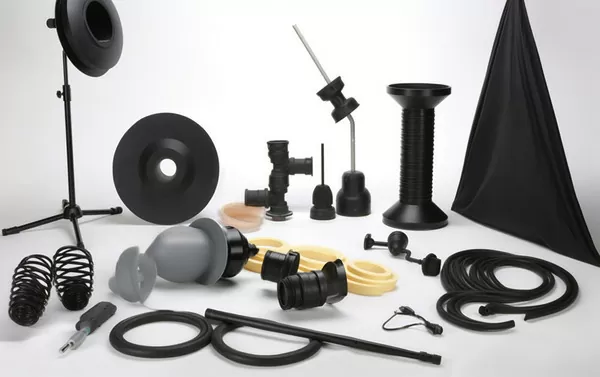
3. Mixing: The mixing process is an important process that people often overlook. It’s a scientific process that needs to be done carefully: Mixing for too long can increase air bubbles, but if you don’t mix enough, the uncured material can over-harden causing bubbles or blemishes. Automate the mixing process whenever possible and always follow the manufacturer’s recommended methods.
4. Mold Release Management: In some cases, bubbles may be caused by the release agent or curing agent itself. Certain release agents may interfere with or even stick to the silicone as it sets, causing trapped air to create bubbles. Using a proper release agent as little as possible will help, but also make sure your mold is clean and free of anything else that could cause air bubbles (contaminants).
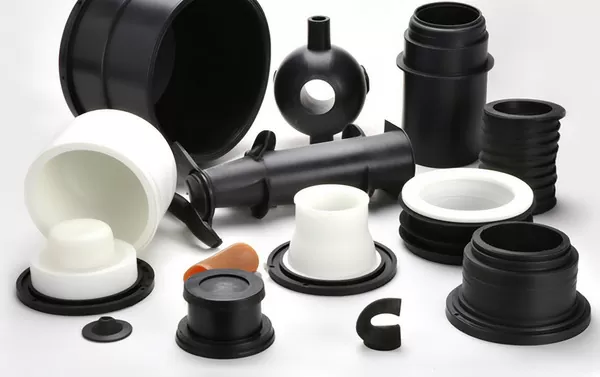
5. Environmental Control: To reduce bubbles, it is important to control the environment in which silicone is cured. Changes in temperature and humidity can affect when curing occurs as well as the rate of degassing, all factors that can cause bubbles to form. By maintaining a consistent curing environment, temperature control, and humidity control throughout the entire process, you will be able to reduce these risks overall.
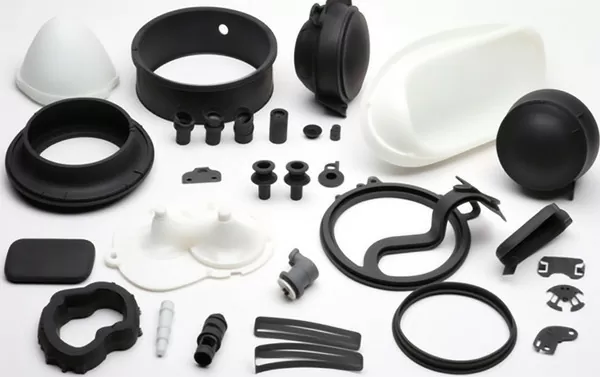
Propelling Quality with Prevention Techniques
1. Mold Maintenance and Fabrication: It is important that molds and tools are kept very clean if you want to prevent contaminants from entering your product. This means they need to be inspected and cleaned regularly! Here are some other considerations: Using a higher quality mold with a non-porous surface can also help ensure that no contaminants get into places where they shouldn’t be.
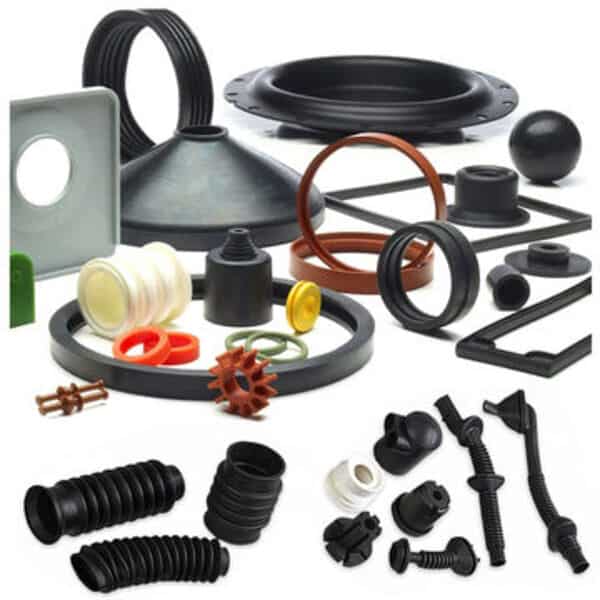
2. Material Handling and Mixing Best Practices: It is important to have a blender that is well maintained and used correctly. You can do this by changing the mix speed or mix speed, mix time. If possible, use silicone products made from a low-viscosity base, as these products allow air bubbles to escape better than other types of products.
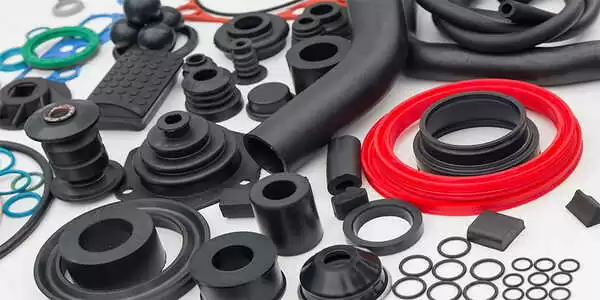
Conclusion
Currently, the demand for silicone rubber products is soaring across various industries, which is no surprise considering its unique properties. But if bubbles form during the manufacturing process, the special qualities of these products may be compromised, leading to consumer dissatisfaction. But by mastering the science of bubbles, adopting preventive measures as standard, and continually seeking improvements, silicone rubbers manufacturers can reduce bubble-related problems in silicone production. Implement the methods outlined in this blog, explore new solutions as they emerge, and maintain strict quality control procedures: this way, you can ensure your silicone products become and remain at the forefront of your industry. To minimize bubbles during the production process of silicone rubber products, ensure the efficient operation of the vacuum pump while using silicone molds within a tightly sealed mold box, optimizing curing time in accordance with the intricacies of the original model.