Silicone rubber is an excellent material with excellent qualities, which is why it is widely used in the manufacture of many different products. For example, the material can withstand heat, exposure to weather and chemicals, and won’t break down over time as easily as some plastics. It is also somewhat flexible (more flexible than regular rubber) and biocompatible enough to be used in medical devices that remain in the body for months or years at a time. Despite these useful properties, getting involved in the production of custom silicone rubber products can be difficult, whether you are new to the field or an industry expert. This article aims to break down the production process, design considerations, and explore their wide range of applications by providing comprehensive design guidelines, explaining how they are manufactured, and outlining their many uses in diverse fields such as consumer goods and aerospace engineering.
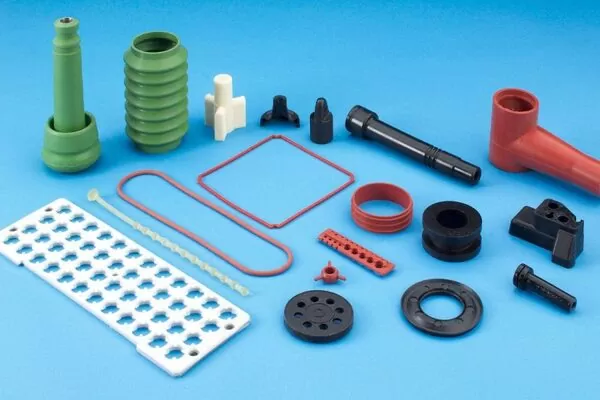
Ⅰ. Understanding the Basics of Silicone Rubber
Before we delve into custom products, let’s first familiarize ourselves with the silicone rubber material. Silicone rubber is a man-made polymer containing silicon, carbon, hydrogen and oxygen atoms. Due to its special molecular composition, this material has some key characteristics: it is chemically stable, remaining stable over time and not reacting much with other chemicals; and it has low thermal conductivity.
What Makes Silicone Rubber Unique?
1. Thermal Stability: Silicone rubber can withstand temperatures from sub-zero to hundreds of degrees without any change in structure.
2. Chemically Inert: Silicone rubber is resistant to most solvents and chemicals and will not decompose or corrode when used.
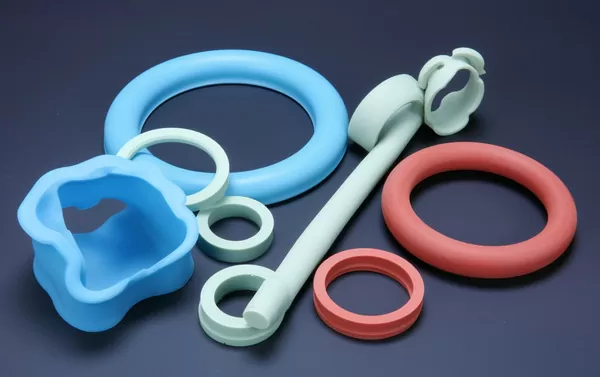
3. Flexibility: Silicone rubber can be stretched to several times and will still return to its original shape.
4. Biocompatibility: Non-toxic; does not cause allergic reactions – this is why it is used in medical implants such as pipes and catheters.
Ⅱ. The Custom Silicone Production Process
Customizing individual silicone rubber products requires many steps, such as careful formulation, shaping, finishing and curing. At every stage of production, we pay close attention to detail and quality control: this is what is needed to ensure that the final result fully meets the customer’s needs.
Formulation and Mixing
The custom silicone production process begins with a stage called formulation preparation. The formulation stage involves taking the appropriate base polymer selection and adding a variety of cross-linkers, additives and catalysts. It is then prepared by high-torque mixing, which mixes the ingredients evenly and completely eliminates air bubbles, as even small air bubbles can affect the final quality.
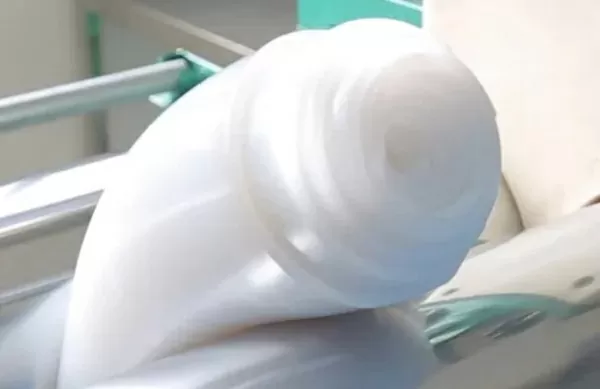
Molding
When a silicone rubber product is molded, it can take on a variety of shapes. There are several different processes commonly used:
1. Compression Molding: Traditional manufacturing methods, this technique is suitable for creating simple shapes. First, heat the material. Next, place them into the mold. Finally, apply a lot of pressure. The silicone will take on the shape of the mold.
2. Injection Molding: This is the first choice when complex shapes are required. Liquid silicone rubber is pushed into the mold under high pressure. It’s ideal when you need to complete some complex product (like many details) and all parts must be unified.
3. Transfer Molding: This method combines the characteristics of compression molding and injection molding because the material is thermoset before being injected into the cavity.
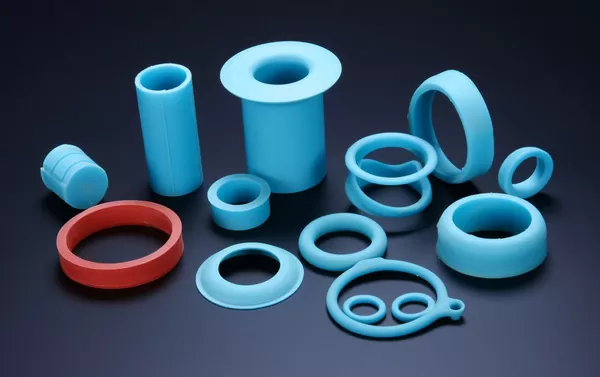
4. Calendering: Silicone rubber is kneaded, mixed with white carbon black, silicone oil, etc. to make mixed rubber, and then rolled out using a calender. The calendering effect is related to the composition of the compound, calendering temperature, speed ratio and other factors. Used for larger products, such as silicon wafers, silicone rubber sheets, etc.
5. Pouring: The operation method of filling or pouring mold: Pouring mold or pouring mold is used for relatively smooth or simple products. There is no mold line to save manpower and time, that is, the product or model you want to copy is covered by a rubber plate or glass plate. Surrounded by a vacuum pump, the silicone is poured directly into the product. It is a solid-liquid combination and is used in products such as mobile phone cases and luggage cases.
6. Extrusion: Extrusion molding manufacturing process and extruded silicone rubber products are usually formed using a silicone molding extruder. Generally, the extruded silicone has a long shape and can be cut into tubular shapes at will. The extrusion process is relatively simple, and most of them are strip-shaped.
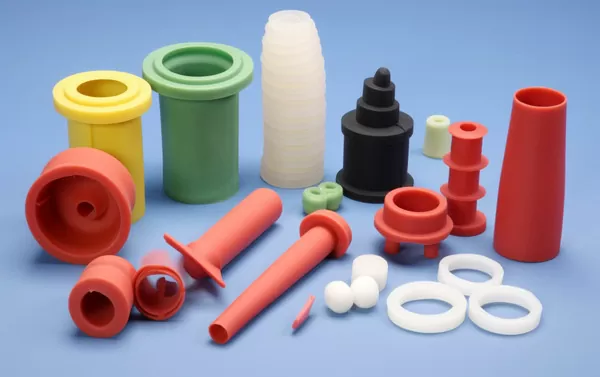
Curing
After molding, the silicone solidifies and cools to form its final structure. For specific applications that require rapid processing, curing methods can range from heat and pressure in an autoclave to ultraviolet light.
Post-Curing and Finishing
Once the silicone has finished curing, some trimming and inspection is required to get the perfect product. Depending on its use, the product may also be post-cured at this stage to make it as strong and flexible as possible. This extra work improves tensile strength as well as tear resistance and elongation.
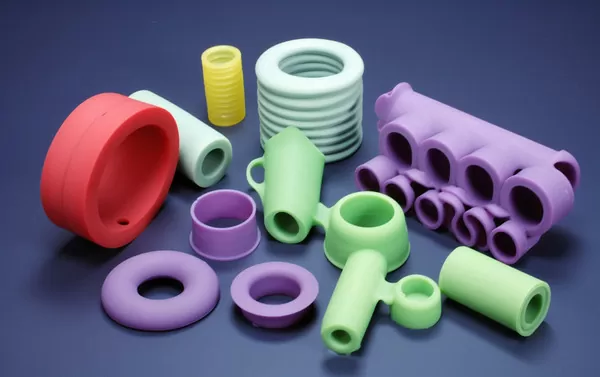
Ⅲ. Design Considerations for Custom Silicone Products
Attention to detail is crucial when creating custom silicone products. Decisions made during the design phase will directly impact the functionality, performance, and manufacturability of the product.
1. Selecting the Right Type of Silicone
If you want the perfect design, the most important decision is determining which silicone is best for the application. Determining the appropriate material requires a thorough understanding of specific parameters such as temperature, chemical exposure, and physical properties to aid selection.
2. Prototype Development
Prototyping is an important part of custom silicone products because it allows you to test and refine your design without the expensive tooling business. This is a great opportunity to evaluate whether something will work (its shape, size, functionality) before going into full production.
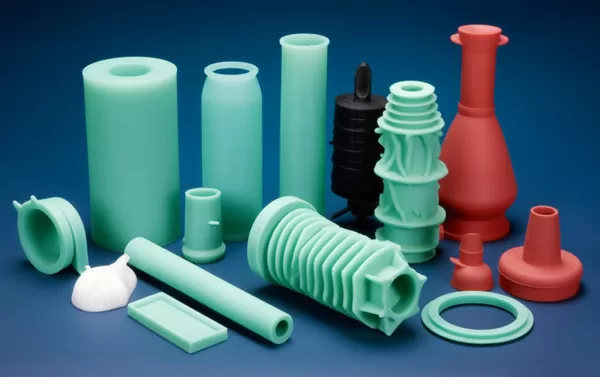
3. Tooling and Molding
There are various molds for making silicone products, and it is quite difficult to make special-shaped workpieces. Optimal mold design takes into account factors such as gate location, parting lines, and venting to ensure high-quality parts.
4. Material Thickness and Shrinkage
Silicone materials may shrink when molded and cured. It is important to know how much they shrink so that the mold can be made accurately.
5. Consideration for Undercuts and Draft Angles
Parts getting stuck in the mold due to undercuts can cause problems with the product. However, if the draft angle is built into its design, the product is more likely to come out of the mold smoothly without being damaged.
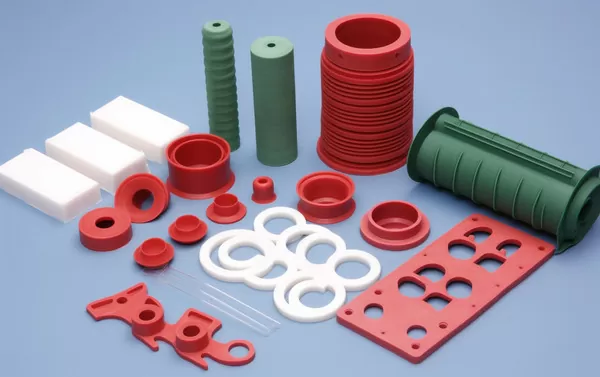
Ⅳ. Applications of Custom Silicone Rubber Products
Silicone rubber is so versatile that it now has a place in countless different industries, thanks to the many premium properties of silicone products. These specialty products are crafted to meet the needs of their own specific industry, examples include:
Aerospace and Automotive
Silicone rubber is used in the aerospace and automotive sectors for its ability to withstand varying temperatures and resist oils and fuels. It is found in shock absorbers, O-rings, gaskets and seals.
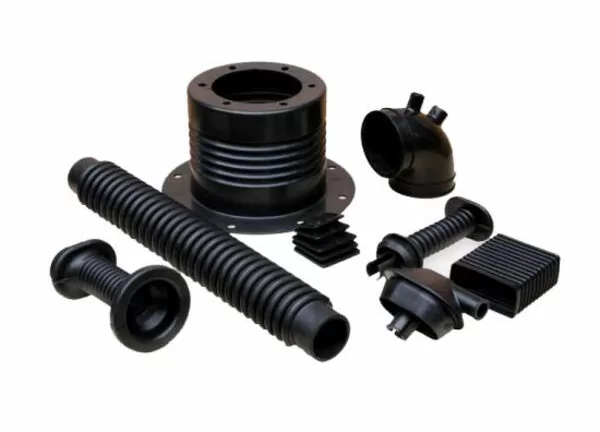
Healthcare and Medical Devices
When hygiene, biocompatibility and sterilization are important issues in medical devices, this material also plays its role: catheters, implants and seals all play an important role together with orthopedic products.
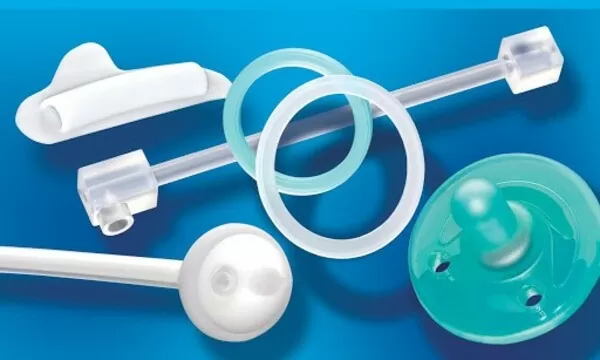
Electronics and Consumer Goods
The insulating properties of silicone rubber have been widely used in electronic products such as keyboards, housings and seals. And its flexibility and touch-friendliness lends itself to consumer products such as kitchenware, food grade products and sports equipment.
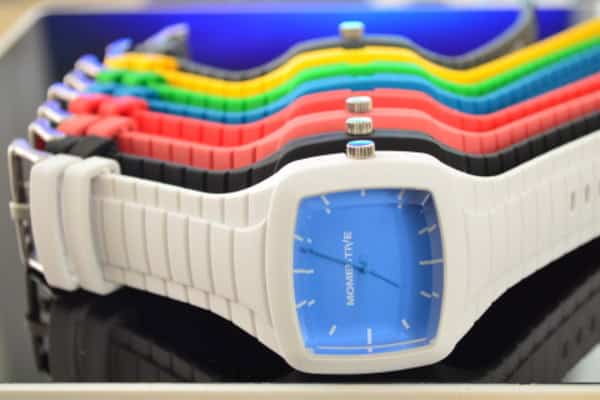
Ⅴ. How to Choose a Silicone Manufacturer?
Choosing the right manufacturer is critical to the success of any custom silicone project. What you need is a partner with the following capabilities:
1. Silicone Formulation Technology: In addition to a range of formulations, good manufacturers can produce custom compounds as needed.
2. Different Molding Experience or Skills: Production costs and speeds may be affected by whether the supplier has mature skills or whether the supplier has experience in the industry.
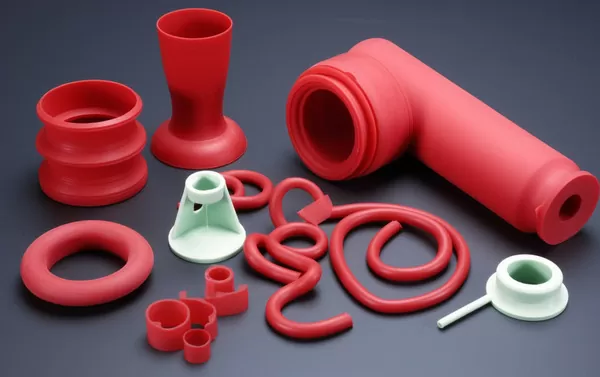
3. Quality Control Standards: If the end product is to be good, it must be done perfectly every time, so make sure manufacturers follow strict quality control processes to ensure consistency and reliability.
4. Proven Track Record in Your Industry: Understanding industry-specific requirements can save time and resources during the design and approval process.
5. Responsive Customer Service: Being able to speak clearly with your vendors and for them to be comfortable working with you is an important factor in things running smoothly, once both parties come to an agreement, ensuring the project can move forward smoothly.
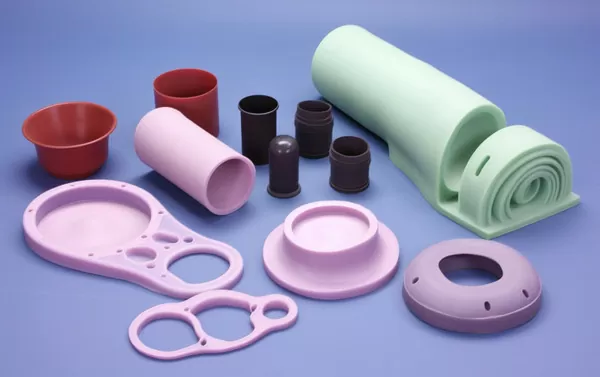
ZetarMold
Over the past 18+ years, we have built our company into a Silicone Rubber Product Design, Silicone Rubber Mold Making, Silicone Rubber Product Manufacturing, Assembly, Post-processing and Packaging all in one juggernaut. Through steady organic growth and strategic acquisitions, we’ve seen decades of excellent performance.
Zetar have 7 senior silicone rubber molding product and silicone rubber mold designing engineers, 30 silicone rubber mold making and silicone rubber molded engineers and a group of skilled senior workers.
We have very strong sales team with more than 20 English speakers are experienced and certified in their English language skills.Let Zetar help you achieve business success.
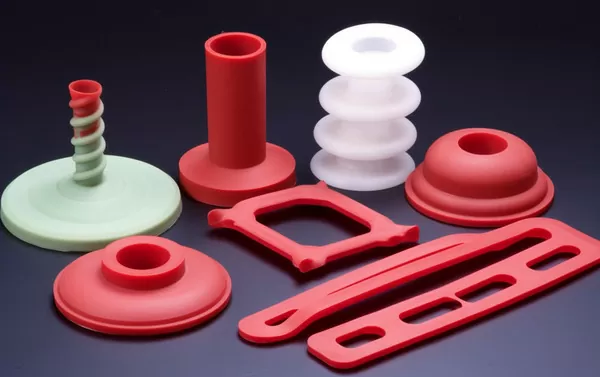
No matter what style of silicone rubber molded products you need, we have the experience and knowledge to manufacture it to your exact specifications. As an experienced rubber products manufacturer and silicone products supplier, we are committed to providing you with exceptional products that meet the highest standards of quality. You can trust us to deliver the products you need on time and on budget, without sacrificing quality or functionality.
Ⅶ. Conclusion
Learn everything you need to know about custom silicone products, including custom silicone molds, protective silicone skin, mold cavity considerations and cost-effective solutions with this in-depth look at custom silicone products. Custom silicone rubber products are not just a niche market, they demonstrate how custom solutions are transforming modern manufacturing. These products are manufactured to meet specific needs; by doing this perfectly in design and material selection, companies across many different industries can meet performance goals, increase safety levels and/or extend the life of their products.
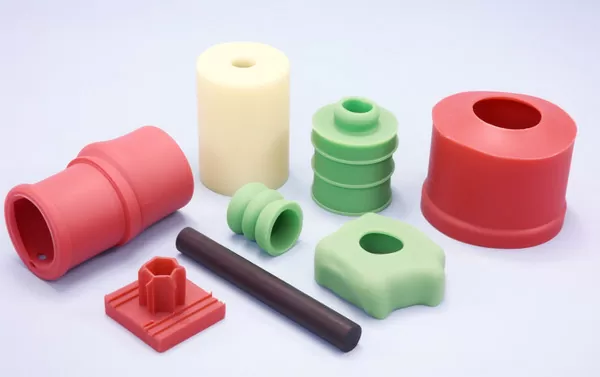
Countless opportunities exist in custom silicone products, allowing people to continue to innovate while enjoying a variety of options. Developing high-quality products that meet the individual needs of customers requires a thorough understanding of materials and production techniques, not to mention design factors. If a company takes all this into consideration while working with an experienced silicone rubber product manufacturer, they not only have access to expert help, but also to those who can help them realize their ideas.
If you need a product that can withstand harsh conditions over the long term without losing precision or quality, then custom silicone products will be perfect for your needs! Businesses looking to bolster their product lineups may also find what they need in this area—just as others looking for rugged components with great performance. While the process from initial idea to final product is certainly complex, once it’s complete, there’s no doubt how well these things will work in every conceivable application area.