Introducción
El proceso de moldeo por compresión de caucho de silicona es un método de producción que utiliza alta presión y calor para dar forma de caucho de silicona líquido a los productos deseados. Esta técnica tiene aplicaciones en diversos sectores, como la automoción, la medicina y los bienes de consumo.
En los últimos tiempos, la eficiencia energética se ha convertido en un factor cada vez más importante en los procesos de producción, ya que no sólo reduce el impacto ambiental, sino que también disminuye los costes para los fabricantes. Dado el alto consumo energético producción de caucho de silicona puede ser, es necesario explorar métodos para lograr la eficiencia energética mediante el moldeo por compresión de caucho de silicona. Al hacerlo, los fabricantes pueden reducir el consumo de energía de procesamiento sin dejar de producir bienes de alta calidad de manera eficiente. En este artículo, veremos varios enfoques para lograr la eficiencia energética a través del moldeo por compresión de caucho de silicona líquido.
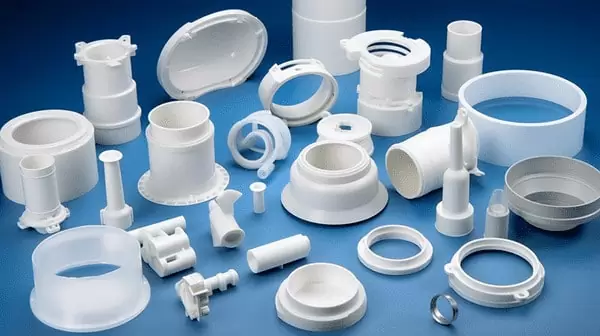
II. Eficiencia energética en el moldeo por compresión de caucho de silicona
El moldeo por compresión de caucho de silicona es un proceso de producción muy utilizado en diversas industrias. Sin embargo, es un gran consumidor de energía, lo que se traduce en unos costes de producción y un impacto medioambiental elevados. Para hacer frente a este problema, los fabricantes pueden aplicar varias estrategias para lograr un mayor consumo de energía y eficiencia en moldeo por compresión de caucho de silicona.
Uso de sistemas de accionamiento que ahorran energía
Se utiliza tecnología avanzada para controlar la velocidad del motor, la potencia de salida y el par, reduciendo el consumo de energía durante el proceso de moldeo. Estos sistemas pueden programarse para funcionar solo cuando sea necesario, lo que reduce el derroche de energía.
Adopta tecnología de moldeo auxiliar
Los equipos y procesos adicionales pueden mejorar la eficiencia de la producción y reducir el consumo de energía. Los moldes de canal caliente pueden eliminar la necesidad de correderas y compuertas, y la soldadura y el ensamblaje en el molde pueden reducir el consumo de energía causado por los pasos de procesamiento secundarios.
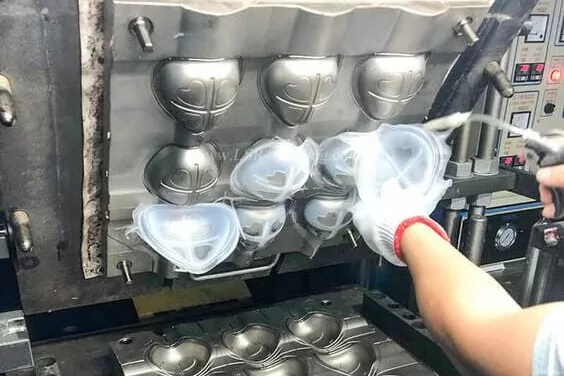
Utilización de sistemas de regeneración de energía
Estos sistemas recuperan y reutilizan la energía residual generada durante el proceso de moldeo. Por ejemplo, un sistema de regeneración de energía puede recuperar el calor del sistema de agua de refrigeración y reutilizarlo para precalentar el material antes de que entre en el molde.
Mejora de las tuberías de calefacción y refrigeración
El uso de sistemas avanzados de calefacción y refrigeración, como la calefacción por infrarrojos o los sistemas de refrigeración de alta eficiencia, puede reducir el derroche y el consumo de energía durante el proceso de moldeo.
La selección correcta máquina de moldeo por inyección
Un líquido fábrica de moldeo por inyección debe tener en cuenta la capacidad de la máquina, el proceso de moldeo por inyección recomendado y la eficacia de la refrigeración a la hora de seleccionar una máquina de moldeo por inyección. Esto puede minimizar el desperdicio de energía y reducir el consumo energético.

Optimización de los parámetros del proceso
El ajuste de los parámetros del proceso, como la temperatura de fusión, puede garantizar un consumo de energía y una eficiencia de producción óptimos.
Reducción de energía y prevención de residuos materiales
Reducir los residuos y evitar el desperdicio de material puede minimizar el consumo de energía y el impacto medioambiental. La optimización del diseño de la cavidad del molde, los esquemas de moldeo unificado y otras tecnologías de procesamiento pueden promover una mejor calidad de la superficie y reducir el desperdicio de material.
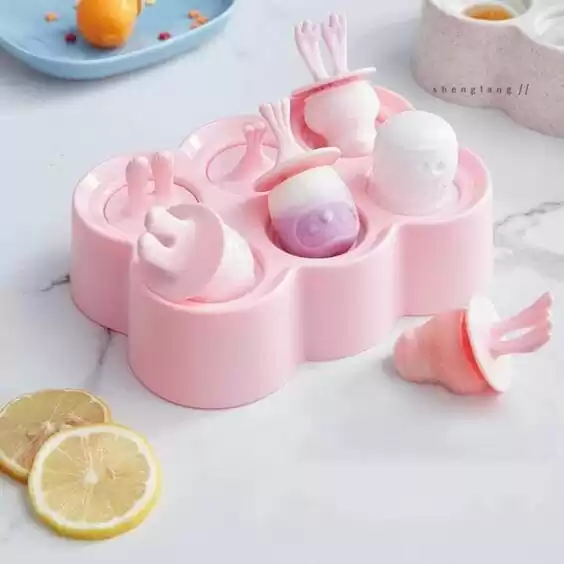
Aplicando estas estrategias, los fabricantes pueden conseguir reducciones significativas del consumo de energía, aumentar la eficiencia de la producción y minimizar su impacto ambiental.
III. ¿Moldeo por compresión frente al moldeo por inyección de silicona?
Aunque caucho de silicona Aunque el moldeo por compresión es un método de producción muy utilizado, el moldeo por inyección también tiene sus ventajas e inconvenientes que deben tenerse en cuenta a la hora de elegir uno u otro.
El moldeo por compresión es una técnica para dar forma al material de caucho de silicona mediante alta presión y calor. Este método funciona mejor cuando se crean piezas grandes con diseños intrincados o piezas con grosores variados; sin embargo, puede ser más lento y menos eficiente.
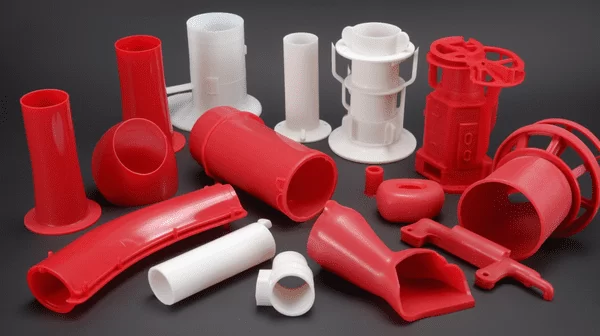
Por otro lado, el moldeo por inyección de silicona consiste en inyectar material en una cavidad bajo una intensa presión. Este método es ideal para producir piezas con excelente precisión y consistencia, ya que es más rápido y eficaz que el moldeo por compresión. Sin embargo, puede no ser ideal para piezas grandes o de grosor variable.
El moldeo por compresión ofrece varias ventajas, como la producción de piezas grandes con espesores variables y diseños intrincados. Además, puede ser rentable para series de producción de menor volumen; sin embargo, puede no ser ideal para series de producción de gran volumen.
El moldeo por inyección de silicona ofrece varias ventajas sobre el moldeo por compresión, como una gran precisión y consistencia en las piezas, series de producción de gran volumen y piezas con geometrías complejas. En el lado negativo, sin embargo, el moldeo por inyección de silicona puede ser más costoso y requerir equipos más complejos que el moldeo por compresión.
Por último, la decisión entre el moldeo por compresión y el moldeo por inyección de silicona depende de varios factores, como el tamaño y la complejidad de la pieza que se va a fabricar, el volumen de producción deseado y los equipos y recursos disponibles.
IV. Mejora de la eficacia de la producción en el moldeo por compresión
Dado que la eficiencia es esencial en el moldeo por compresión de caucho de silicona, aumentar la eficiencia de la producción es igualmente esencial para los fabricantes. He aquí algunas estrategias que pueden emplearse para aumentar la eficiencia de la producción:
Tres formas de reducir el tiempo de producción en el moldeo por compresión
Los fabricantes pueden reducir el tiempo de producción utilizando materiales de curado rápido, optimizando el diseño y empleando máquinas de moldeo por compresión de alta velocidad. Estas estrategias ayudan a aumentar los índices de producción al tiempo que reducen los tiempos de ciclo.
Importancia del análisis del flujo del molde y del proceso de diseño
El análisis del flujo del molde puede ayudar a optimizar el diseño y reducir el tiempo de producción. Analizando el flujo de material dentro del molde, los fabricantes pueden identificar las zonas en las que los materiales pueden quedar atrapados, provocando defectos o ralentizando la producción. Además, la optimización del diseño del molde mejora la eficacia general de todo el proceso de moldeo.
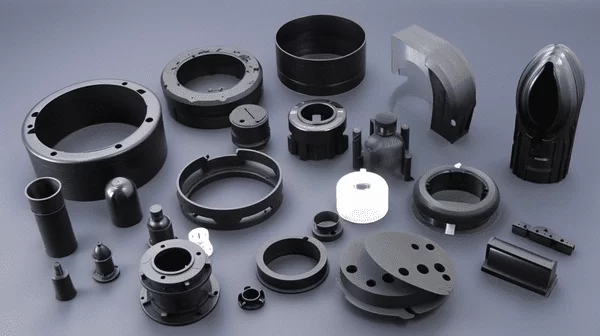
Introducción del uso flexible de la energía
Las empresas pueden ajustar su consumo de energía en función de las demandas de producción instalando sensores y sistemas de control que se ajustan en función del ritmo de producción. Esto garantiza un uso eficiente de los recursos.
Utilización de nuevas tecnologías de calefacción
Las técnicas de calentamiento modernas, como el calentamiento por inducción electromagnética, pueden calentar los moldes con más eficacia que los métodos tradicionales; esto reduce el consumo de energía y aumenta la eficiencia de la producción.
Gestión estable de la producción y mantenimiento de los equipos
Garantizar una gestión fiable de la producción y el mantenimiento de los equipos puede ayudar a evitar interrupciones de la producción y minimizar el tiempo de inactividad. Esto se consigue creando un programa de mantenimiento adecuado, supervisando el rendimiento de los equipos y formando a los operarios sobre cómo identificar y solucionar problemas rápidamente.
Estas estrategias pueden ayudar a los fabricantes a aumentar su eficiencia productiva, acortar los tiempos de producción y optimizar el uso de la energía.
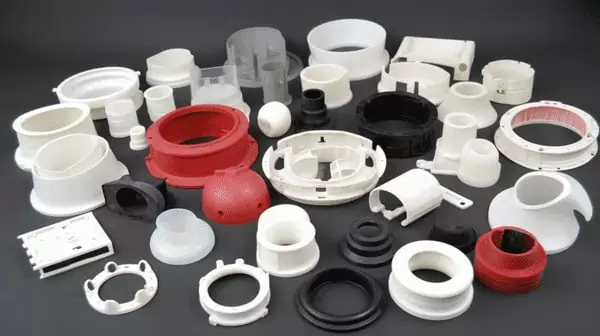
Conclusión
Por último, la eficiencia energética en el moldeo por compresión de caucho de silicona es fundamental para los fabricantes que desean reducir costes y tener un impacto medioambiental mínimo. Mediante el empleo de estrategias de ahorro de energía, como el uso de sistemas de accionamiento de bajo consumo, la adopción de tecnología de moldeo auxiliar, la utilización de sistemas de regeneración de energía y la optimización de los procesos de calentamiento/enfriamiento en consecuencia, los fabricantes pueden reducir significativamente su consumo de energía y la producción de residuos.
Además de la eficiencia energética, los fabricantes pueden aumentar la eficiencia de su producción mediante estrategias como el análisis de flujos, el uso flexible de la energía y la gestión estable de la producción y el mantenimiento de los equipos. Esto les permite fabricar productos de caucho de silicona de alta calidad de forma eficiente y sostenible.
En general, nunca se insistirá lo suficiente en la importancia de la eficiencia energética en el moldeo por compresión de caucho de silicona. Adoptando estrategias de ahorro energético, los fabricantes pueden reducir costes, minimizar su impacto medioambiental y seguir siendo competitivos en el mercado. Con el continuo avance de las nuevas tecnologías y procesos, el logro de la eficiencia energética a través del moldeo por compresión de caucho de silicona será aún más esencial con el tiempo.