Introducción
El moldeo de caucho de silicona es un método estándar de la industria utilizado para producir componentes de caucho de alta calidad para productos que van desde sellos y juntas hasta complejas herramientas médicas y componentes de automoción. El moldeo por compresión destaca entre los distintos métodos de moldeo como la técnica más utilizada para producir fuelles y diafragmas de caucho de silicona de la máxima calidad.
Los fuelles y diafragmas son componentes esenciales en muchos sectores, desde la sanidad hasta la automoción, pasando por la fabricación aeroespacial, y se utilizan para regular la presión, controlar los fluidos y amortiguar las vibraciones. El moldeo por compresión ha demostrado ser un proceso eficaz para producir en serie estas piezas con una calidad constante y cumpliendo estrictos controles de tolerancia. En este artículo exploramos este método aplicado a fuelles y diafragmas de caucho de silicona, sus ventajas y desventajas, así como los diferentes moldes utilizados durante el moldeo por compresión. moldeo por compresión de caucho procesos.
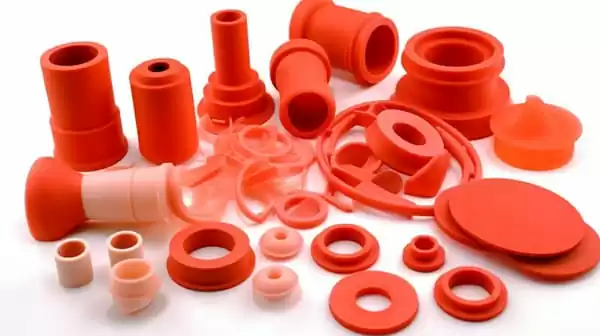
Proceso de moldeo por compresión de caucho de silicona
Fabricación de moldes de compresión Proceso en el que el material de caucho de silicona calentado se coloca en una cavidad de molde a alta presión bajo compresión hasta que adopta la forma de la cavidad de molde prevista. Una vez curado a cierta temperatura durante un periodo de tiempo determinado, el molde se abre y se desmolda para liberar la pieza.
El moldeo por compresión de caucho de silicona ofrece muchas ventajas, como la producción de grandes cantidades con una calidad y tolerancias constantes que cumplen o superan las especificaciones del cliente, la rentabilidad para series de producción de bajo volumen, la versatilidad al utilizar materiales de caucho de silicona líquido para producir geometrías complejas con tolerancias ajustadas, así como la amplia selección de materiales que permiten su uso durante el proceso de moldeo por compresión de silicona.
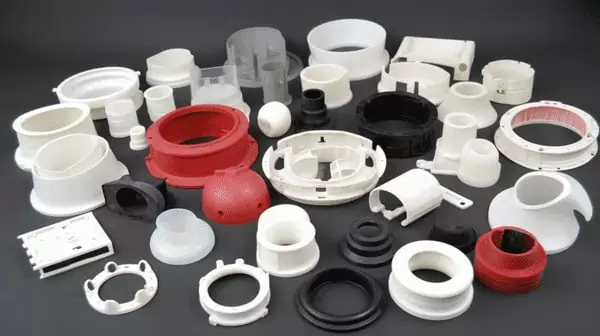
Sin embargo, el moldeo por compresión tiene sus inconvenientes. Por un lado, puede llevar mucho tiempo y requerir mucha mano de obra en comparación con el moldeo por inyección; y controlar su proceso de curado puede resultar complicado; puede ser necesario recortar el material sobrante de los productos finales como resultado de un proceso de curado excesivo. Aun así, el moldeo por compresión sigue siendo una opción popular cuando producción de componentes de caucho moldeados a medida como fuelles y diafragmas para campanas o diafragmas.
Idoneidad del moldeo por compresión para fuelles y diafragmas
El moldeo por compresión es un método ideal para fabricar fuelles y diafragmas de caucho de silicona, gracias a su capacidad para producir piezas con una alta calidad constante y tolerancias ajustadas. Además, el proceso de moldeo por compresión permite la producción de piezas de diversos grosores con geometrías complejas, una característica esencial en la fabricación de fuelles o diafragmas.
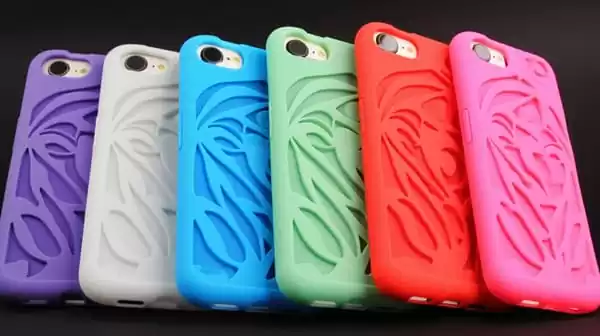
El moldeo por compresión ofrece varias ventajas claras en comparación con otros métodos de moldeo, como la inyección o el moldeo por transferencia. El moldeo por compresión funciona mejor para producir piezas con paredes más gruesas o formas complejas que sus competidores, como la inyección y el moldeo por transferencia; además, sus menores requisitos de volumen de producción implican un uso más económico de los recursos materiales que sus alternativas.
Por otro lado, el moldeo por inyección es ideal para series de producción de gran volumen y para crear piezas con paredes muy finas o detalles intrincados. Además, este proceso es mucho más rápido que el moldeo por compresión, por lo que produce menos material de desecho y piezas más rápidas en general. El moldeo por transferencia ofrece las ventajas de ambas técnicas, pero requiere equipos y herramientas más complejos.
El moldeo por compresión sigue siendo una solución más rentable para producir fuelles y diafragmas de caucho de silicona de alta calidad, sobre todo cuando se producen series de menor volumen con piezas de diferentes grosores o geometrías complejas.
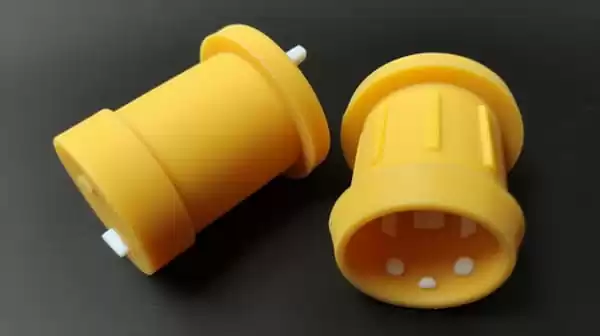
Tipos de moldes de moldeo por compresión
Existen varios moldes de moldeo por compresión para producir piezas de caucho de silicona de alta calidad como fuelles y diafragmas, incluidos los fuelles. Algunos de los moldes más utilizados son:
Moldes abiertos: Estos moldes son los más fáciles de usar y consisten en dos placas planas colocadas juntas para formar una cavidad dentro de la cual se pueden producir piezas de molde con espesor uniforme y fácil desmoldeo. Los moldes abiertos son muy adecuados para producir piezas sencillas de grosor uniforme que requieren procesos de desmoldeo rápidos.
Moldes cerrados: Los moldes cerrados están diseñados para producir piezas más complejas con espesores no uniformes y geometrías intrincadas, como las fabricadas con telas no tejidas o intrincados moldes de plástico. Constan de varias placas diseñadas para abrirse y cerrarse siguiendo patrones específicos con el fin de producir las formas deseadas.
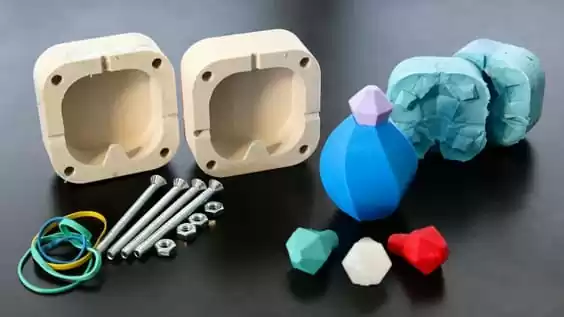
Moldes de transferencia por compresión: Los moldes de transferencia por compresión se parecen a los moldes cerrados tradicionales en que el material se transfiere entre cavidades durante el moldeo; estos moldes pueden ayudar a crear piezas con grosor o contenido de material variable, así como aplicaciones de sobremoldeo.
La elección del material del molde y las consideraciones de diseño dependen de varios factores, como la complejidad de la pieza, el material utilizado, el volumen de producción necesario y el volumen de producción deseado. Entre los materiales más utilizados para los moldes se encuentran el aluminio, el acero y el epoxi, cada uno de los cuales presenta sus propias ventajas e inconvenientes, como el coste, la durabilidad y la facilidad de mecanizado.
Las consideraciones de diseño para los moldes moldeados por compresión de caucho de silicona incluyen los ángulos de desmoldeo, el grosor de la pared y la ubicación de la compuerta. Los ángulos de desmoldeo deben ser suficientes para facilitar el desmoldeo, mientras que el grosor de la pared debe ser uniforme para mantener la calidad de la pieza. La ubicación de la compuerta desempeña un papel importante en el control del flujo de material en la cavidad del molde para evitar bolsas de aire o defectos que comprometerían la calidad de la pieza.
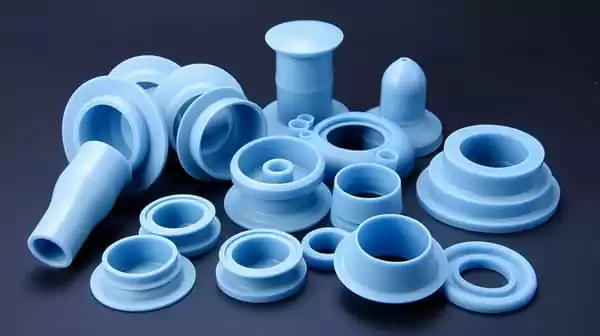
Seleccionar el moldeo por compresión el moldeo por inyección líquida y el material son partes integrales de la producción de piezas de caucho de silicona de alta calidad, como fuelles y diafragmas, teniendo en cuenta la facilidad y la consistencia de la producción. Las consideraciones de diseño también deben tenerse en cuenta para garantizar una calidad constante de las piezas y, al mismo tiempo, mantener bajos los costes durante la producción.
Materiales utilizados para el moldeo por compresión
El caucho de silicona es un material elastómero sintético extremadamente flexible que se utiliza habitualmente en el moldeo por compresión para fabricar fuelles y diafragmas. Como material elastómero sintético, el caucho de silicona ofrece varias características únicas, como resistencia al calor, resistencia química y propiedades de aislamiento eléctrico, por no mencionar que puede presentarse en una gran variedad de colores y niveles de dureza para fines de producción.
El caucho de silicona tiene muchas ventajas sobre otros materiales elastoméricos como el caucho natural y el EPDM, incluida una resistencia al calor que alcanza los 200degC. Además, su resistencia química lo hace perfecto para aplicaciones de alta temperatura, ya que resiste ácidos, bases y otras sustancias potencialmente corrosivas.
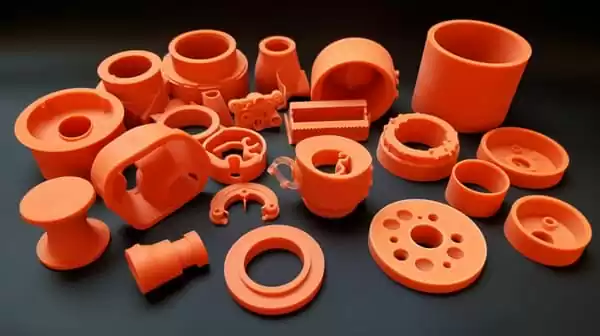
El caucho natural es más rentable y suele preferirse en aplicaciones en las que el coste es la consideración primordial. Presume de una excelente elasticidad y resistencia a la abrasión, lo que lo hace adecuado para neumáticos y juntas; sin embargo, debido a su baja resistencia química y a la temperatura, puede limitar su uso en determinadas aplicaciones.
El EPDM es otro elastómero ampliamente utilizado con una excelente resistencia a la intemperie y flexibilidad a bajas temperaturas, que se encuentra a menudo en aplicaciones de automoción como burletes y juntas. Por desgracia, el EPDM carece de resistencia al calor y a los productos químicos en comparación con su homólogo de caucho de silicona, y no puede soportar temperaturas superiores a 140 F durante periodos prolongados.
En general, el caucho de silicona sigue siendo una opción de material atractiva para el moldeo por compresión debido a sus propiedades únicas y a su versatilidad; sin embargo, la selección del material dependerá en última instancia de las necesidades de cada aplicación y de los criterios de rendimiento.
Proceso de producción de fuelles y diafragmas de moldeo por compresión
Los fuelles y diafragmas de moldeo por compresión requieren múltiples pasos para su producción: desde el diseño y la preparación del molde, pasando por la selección del material, los procesos de moldeo y curado y, por último, el desmoldeo.
Diseño y preparación de moldes Para iniciar el proceso de moldeo, primero es necesario diseñar un molde de acuerdo con la forma de fuelle o diafragma que prefiera. El molde debe tener en cuenta el grosor, la forma, las muescas o las características de la pieza, así como estar limpio y lubricado para garantizar un proceso de moldeo sin problemas.
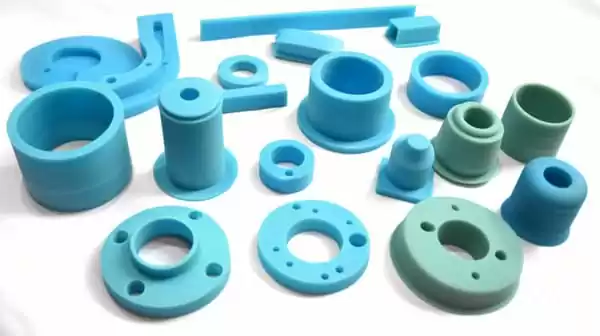
Una vez seleccionada una pieza, es esencial elegir un material adecuado, como caucho de silicona, caucho de silicona líquida u otros elastómeros, antes de mezclar los aditivos o colorantes necesarios para obtener las propiedades deseadas.
Moldeado y curado: Una vez colocado en la cavidad de un molde, el material se comprime a alta presión con una prensa hidráulica antes de calentarlo a una temperatura ideal para un curado prolongado -lo que garantiza que posea todas las propiedades deseadas, como flexibilidad y dureza- antes de liberarlo para la producción.
Desmoldeo: Una vez fraguada la pieza, debe abrirse su molde y desmoldarse. Hay que recortar el material sobrante y dar los toques finales que se deseen, como texturizar o pintar la superficie.
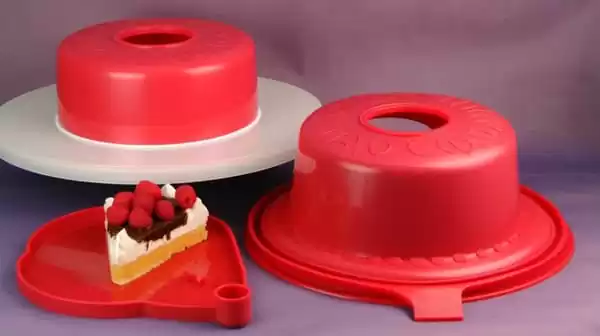
El moldeo por compresión puede adaptarse tanto a series de producción de bajo como de alto volumen; las prensas manuales suelen servir para volúmenes más bajos, mientras que las prensas automatizadas pueden ser más adecuadas para volúmenes más altos. Los requisitos de su proyecto y el volumen de las piezas determinarán qué prensa es la más adecuada.
El moldeo por compresión de fuelles y diafragmas implica varias etapas clave, desde el diseño y la preparación del molde, la selección y mezcla de materiales, el moldeo, el curado y el desmoldeo. Puede utilizarse tanto para series de producción de bajo volumen como para grandes series con piezas de grosor variable o geometrías complejas.
Aplicaciones de fuelles y diafragmas moldeados por compresión
Los fuelles y diafragmas moldeados por compresión son componentes integrales de numerosos sectores, como la sanidad, la automoción, la industria aeroespacial y la fabricación industrial. Se utilizan para regular la presión, controlar los fluidos y amortiguar las vibraciones.
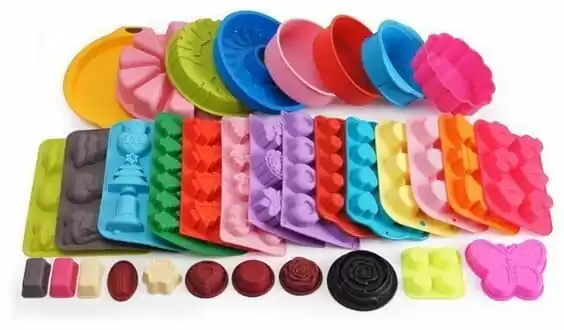
Los fuelles y diafragmas moldeados por compresión se utilizan mucho en la industria médica, a menudo como componentes de dispositivos como sacaleches, inhaladores y jeringuillas. Los diafragmas de los sacaleches fabricados con caucho de silicona deben soportar el uso repetido, así como los procesos de limpieza periódicos, sin degradarse con el paso del tiempo.
Las industrias de automoción utilizan ampliamente fuelles y diafragmas moldeados por compresión en componentes como bombas de combustible, sistemas de frenos y sistemas de gestión del motor. Las válvulas de diafragma también desempeñan un papel esencial en el control del flujo de fluidos y gases en entornos de automoción.
Los fuelles y diafragmas moldeados por compresión forman parte integral de muchos componentes aeroespaciales, como los sistemas de aire acondicionado y de combustible, y están fabricados con materiales como caucho de silicona o EPDM para soportar las condiciones extremas asociadas a los viajes espaciales.
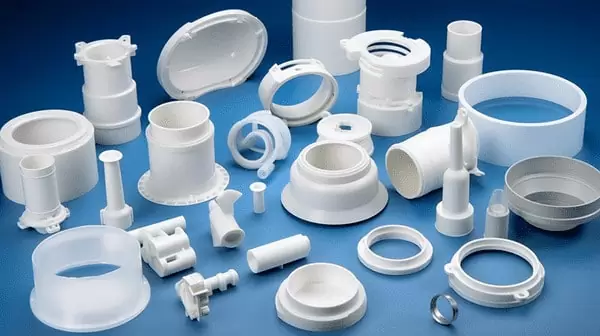
Los fuelles y diafragmas moldeados por compresión tienen múltiples usos en la fabricación industrial, desde bombas y sensores de presión hasta reguladores de presión y gomas y botas moldeadas -que protegen los equipos del polvo y la suciedad- fabricadas con tecnología de moldeo por compresión.
Los fuelles y diafragmas moldeados por compresión desempeñan un papel indispensable en muchas industrias y aplicaciones, ya que admiten altas presiones, controlan el flujo de fluidos y amortiguan las vibraciones, características esenciales para que los sistemas funcionen con eficacia y sin problemas.
Ventajas del moldeo por compresión de fuelles y diafragmas
El moldeo por compresión ofrece numerosas ventajas a la hora de fabricar fuelles y diafragmas de alta calidad, entre ellas:
Alta calidad: El moldeo por compresión ofrece piezas de calidad constante y tolerancias precisas gracias al uso de técnicas de moldeo a alta presión y a la distribución uniforme del material durante los procesos de moldeo.
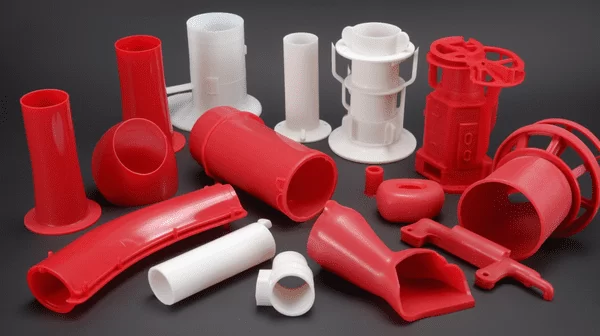
El moldeo por compresión ofrece un estricto control de las tolerancias para garantizar que cada pieza producida refleje un nivel constante de exactitud y precisión.
Rentable: El moldeo por compresión ofrece una opción económica para series de producción de bajo volumen, ya que no requiere costosos equipos de moldeo por inyección ni grandes cantidades de material.
El moldeo por compresión puede utilizar diversos materiales, incluida la goma de silicona líquida. Esto permite a los fabricantes producir piezas con geometrías complejas y tolerancias estrechas con este proceso.
En comparación con los métodos de moldeo por inyección y transferencia, el moldeo por compresión ofrece varias ventajas claras sobre sus homólogos. Es ideal para producir piezas con paredes más gruesas y formas más complejas, mientras que sus series de producción de bajo volumen no requieren equipos costosos ni grandes cantidades de material.
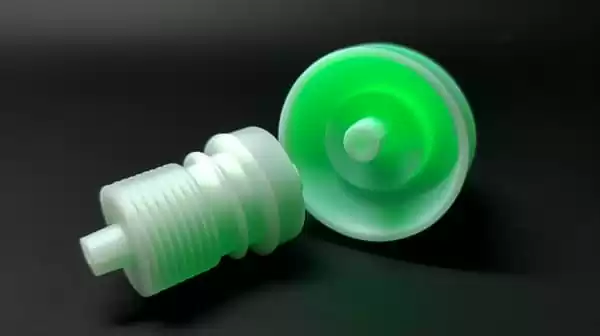
Por otro lado, el moldeo por inyección es ideal para series de producción de gran volumen, ya que produce piezas con paredes extremadamente finas y detalles intrincados. Además, este proceso es más rápido que el moldeo por compresión y produce menos material de desecho; el moldeo por transferencia combina elementos de ambas técnicas, pero requiere equipos y herramientas más complejos para su aplicación.
El moldeo por compresión sigue siendo un medio eficaz para producir fuelles y diafragmas de la máxima calidad gracias a su fabricación uniforme con un estricto control de las tolerancias.
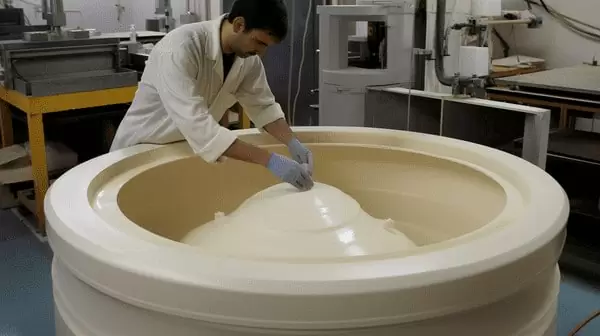
Conclusión
El moldeo por compresión es un método de fabricación indispensable para producir fuelles y diafragmas de caucho de silicona de la máxima calidad, ya que proporciona una calidad constante con tolerancias ajustadas, un factor esencial cuando se producen piezas que requieren estrictas medidas de control de calidad.
El moldeo por compresión puede ser una solución económica para series de producción de bajo volumen y la creación rápida de prototipos. Admite el uso de diversos materiales -incluido el caucho de silicona líquida-, así como la producción de piezas con geometrías complejas y tolerancias ajustadas.
En general, moldeo por compresión es un medio fiable y flexible de producir fuelles y diafragmas de alta calidad que se utilizan en sectores como el médico, el automovilístico y el aeroespacial. Gracias a su capacidad para producir constantemente piezas de primera calidad a bajo coste, el moldeo por compresión ofrece a los fabricantes una forma ideal de producir componentes de caucho de silicona con un estricto control de las tolerancias sin dejar de ser rentable.