Introducción
El moldeo de caucho de silicona desempeña un papel fundamental en la fabricación moderna, ya que sirve de base para producir una amplia gama de productos que encontramos a diario. Este versátil proceso hace gala de una notable capacidad para aprovechar las propiedades únicas del caucho de silicona, como su flexibilidad, resistencia al calor y durabilidad. Sin embargo, como cualquier método de fabricación, el moldeo de caucho de silicona no está exento de problemas y defectos. En este artículo, profundizaremos en la importancia del moldeo de caucho de silicona en el panorama de la fabricación y arrojaremos luz sobre los retos y defectos comunes que pueden surgir durante este intrincado proceso.
Fabricantes de diversos sectores confían en moldeo de caucho de silicona para crear componentes que van desde piezas críticas de automoción hasta dispositivos médicos que salvan vidas e incluso bienes de consumo cotidianos. Su importancia radica en su capacidad para producir piezas de alta calidad, diseñadas con precisión y con unas características de rendimiento excepcionales. La resistencia inherente del caucho de silicona a las temperaturas extremas, los productos químicos y el envejecimiento lo convierten en la mejor opción para aplicaciones que exigen durabilidad y fiabilidad.
En las secciones siguientes, exploraremos en profundidad estos retos comunes y ofreceremos soluciones prácticas para mitigarlos o eliminarlos. Al conocer en profundidad los entresijos del moldeo de caucho de silicona y cómo superar los defectos asociados, los fabricantes pueden garantizar que sus productos cumplen o superan las estrictas normas de sus respectivos sectores. Emprendamos este viaje para desentrañar los secretos de la excelencia en el moldeo de caucho de silicona.
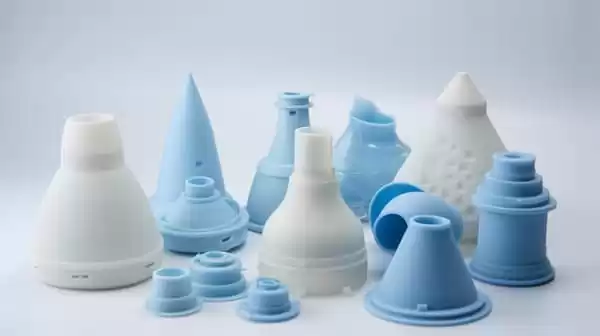
II. Defectos del material del molde
Impacto en el producto final
Los defectos del material del molde pueden ensombrecer todo el proceso de fabricación. Estos defectos pueden incluir imperfecciones, impurezas o incoherencias en el propio material del molde. Cuando están presentes, estos defectos pueden provocar una serie de problemas que afectan directamente a la calidad e integridad del producto final de caucho de silicona. Estas son algunas de las formas en que los defectos del material del molde pueden afectar al producto final:
Imperfecciones superficiales: Los defectos del material del molde pueden transferirse a la superficie de la pieza moldeada, dando lugar a irregularidades, texturas rugosas o incluso marcas de hundimiento. Estas imperfecciones no solo afectan a la estética, sino que también pueden comprometer la funcionalidad del componente.
Reducción de la vida útil del molde: Los materiales defectuosos de los moldes pueden desgastarse o degradarse con mayor rapidez, lo que acorta la vida útil de los moldes. Esto puede aumentar los costes de producción y el tiempo de inactividad debido a las frecuentes sustituciones de moldes.
Contaminación del material: Las impurezas del material de moldeo pueden mezclarse con las piezas de caucho de silicona líquida utilizadas durante el proceso de moldeo, provocando la contaminación del material. Esta contaminación puede dar lugar a debilidades estructurales, disminución de la integridad del material y una mayor probabilidad de defectos en el producto final.
Moldeado incoherente: Los defectos del material del molde pueden dar lugar a un moldeo incoherente, con variaciones en las dimensiones y el grosor de las paredes, lo que dificulta el cumplimiento de especificaciones y tolerancias precisas.
Medidas preventivas para evitar defectos en el material de moho
Prevenir cualquier defecto de moldeo y de material es crucial para garantizar la fiabilidad y consistencia del moldeo de caucho de silicona. Estas son las medidas preventivas clave a tener en cuenta:
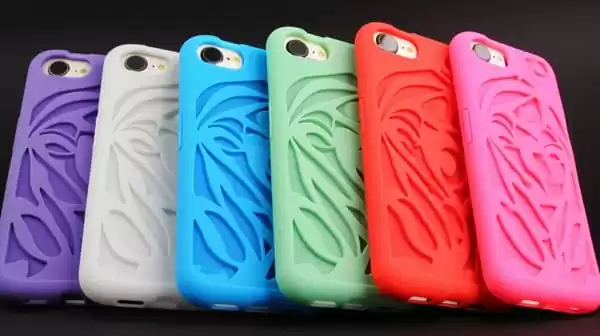
Elija materiales de molde de alta calidad: Empiece por seleccionar materiales para moldes conocidos por su calidad y fiabilidad. Invertir en materiales de primera calidad puede reducir significativamente el riesgo de defectos.
Inspección y mantenimiento periódicos: Implemente un riguroso programa de inspección y mantenimiento de sus moldes. Examine periódicamente las superficies de los moldes para detectar signos de desgaste, daños o defectos, y resuelva cualquier problema con prontitud.
Almacenamiento adecuado: Almacene los materiales del molde en un entorno controlado que minimice la exposición a la humedad, los contaminantes y las fluctuaciones de temperatura. Un almacenamiento adecuado puede ayudar a preservar la integridad de los materiales.
Control de calidad: Instituir estrictos procesos de control de calidad en todo el ciclo de fabricación. Esto incluye la inspección de los materiales de moldeo entrantes para detectar defectos y garantizar su conformidad con las especificaciones.
Consulta a los proveedores: Colabore estrechamente con los proveedores de materiales para moldes, que pueden orientarle sobre las mejores prácticas de selección, manipulación y almacenamiento de materiales.
III. Soluciones para los defectos de moldeo por compresión
Defectos comunes en el moldeo por compresión
Relleno incompleto: Uno de los principales retos del moldeo por compresión es conseguir un llenado completo del material dentro de la temperatura de la cavidad del molde. Esto puede dar lugar a piezas con secciones faltantes o huecos.
Irregularidades superficiales: Pueden aparecer imperfecciones en la superficie, como texturas rugosas o incoherencias, que afectan a la estética y la funcionalidad del producto final.
Deformación y distorsión: Piezas moldeadas por compresión a veces pueden sufrir alabeos o distorsiones debido a un enfriamiento desigual o a problemas de expulsión.
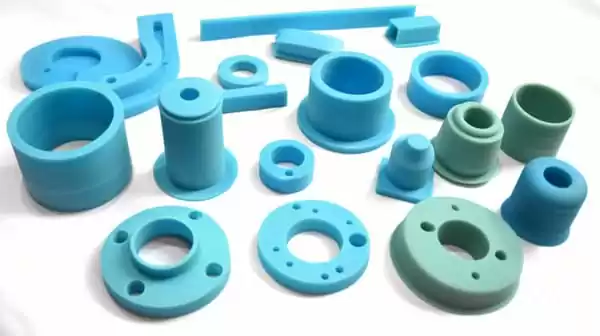
Contaminación del material: Los contaminantes o impurezas en el material de silicona pueden provocar debilidades estructurales y defectos en la pieza moldeada.
Remedios y ajustes
Para subsanar estos defectos comunes en moldeo por compresiónConsidere los siguientes remedios y ajustes:
Optimizar la temperatura y la presión: Ajuste la temperatura y la presión para garantizar un flujo adecuado del material y llenar completamente la cavidad del molde. Experimente con diferentes ajustes para encontrar la combinación ideal para su material y diseño de molde específicos.
Distribución uniforme del material: Garantice una distribución uniforme del material dentro de la cavidad del molde aplicando una presión constante durante todo el proceso de compresión. Esto ayuda a evitar un llenado incompleto e irregularidades en la superficie.
Ventilación adecuada: Implemente sistemas de ventilación eficaces dentro del molde para permitir la salida del aire atrapado durante el proceso de compresión. Una ventilación adecuada reduce el riesgo de huecos y mejora la calidad de la superficie.
Utilice desmoldeantes de calidad: Aplique agentes de desmoldeo de alta calidad a las superficies del molde para mejorar el desmoldeo de las piezas y minimizar las imperfecciones de la superficie.
Control de las tasas de enfriamiento: Gestione cuidadosamente el proceso de enfriamiento para conseguir un enfriamiento uniforme y evitar el alabeo o la distorsión. Un enfriamiento adecuado ayuda a mantener la integridad de la pieza.
Control de calidad del material: Priorizar utilizando material de silicona de alta calidad, libre de contaminantes o impurezas. Inspeccione periódicamente los lotes de material para comprobar su consistencia y pureza.
Mantenimiento y limpieza: Establezca un programa de mantenimiento rutinario para sus moldes. Limpie e inspeccione periódicamente las superficies de los moldes en busca de desgaste, daños o contaminación. Solucione cualquier problema con prontitud.
Fuerza de sujeción adecuada: Asegúrese de que el molde está bien sujeto para evitar fugas de material y conseguir un grosor uniforme de la pieza.
IV. Prevención de defectos plásticos
La importancia de los materiales plásticos de alta calidad
Los materiales plásticos utilizados en el moldeo de caucho de silicona influyen significativamente en la calidad general, la durabilidad y el rendimiento del producto final. He aquí por qué es crucial optar por materiales plásticos de alta calidad:
Integridad del material: Los materiales plásticos de alta calidad tienen menos probabilidades de contener impurezas, contaminantes o inconsistencias. Esto garantiza que el material mantenga su integridad estructural durante todo el proceso de moldeo, reduciendo así el riesgo de defectos.
Coherencia: Los materiales plásticos de primera calidad presentan propiedades y comportamiento uniformes. La consistencia es esencial para lograr un flujo uniforme del material, un llenado completo de la cavidad del molde y un enfriamiento controlado, todo lo cual contribuye a evitar defectos.
Estabilidad dimensional: Los plásticos de calidad son menos propensos a sufrir cambios dimensionales, como encogimiento o alabeo, durante el enfriamiento. Esta estabilidad ayuda a mantener la precisión de las dimensiones del producto final.
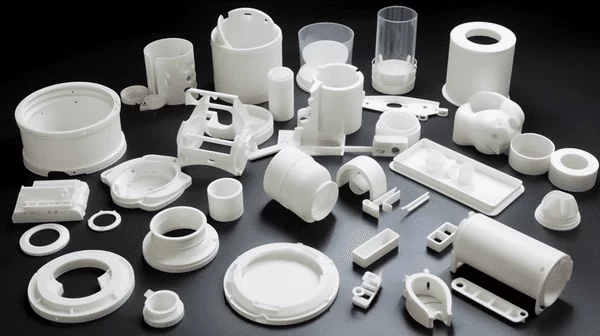
Reducción de la contaminación del material: Los materiales plásticos de alta calidad tienen menos probabilidades de introducir contaminantes en la película de caucho de silicona líquida, reduciendo así el riesgo de contaminación del material y de defectos estructurales en la pieza moldeada.
Condiciones de procesamiento coherentes
Mantener unas condiciones de procesamiento constantes es igualmente vital para prevenir los defectos de plástico en el moldeo de caucho de silicona. A continuación se explica cómo unas condiciones uniformes pueden contribuir a la prevención de defectos:
Control de la temperatura: El control preciso de los ajustes de temperatura del material durante el proceso de moldeo es fundamental. Las temperaturas constantes garantizan un flujo uniforme del material, reducen el riesgo de deformación y ayudan a mantener las dimensiones de las piezas.
Regulación de la presión: Un control adecuado de la presión, incluida la presión de inyección y la presión de mantenimiento, es esencial para lograr una densidad constante de las piezas y reducir la probabilidad de defectos.
Velocidad de inyección: La velocidad de inyección constante ayuda a mantener una distribución uniforme del material dentro de la cavidad del molde, lo que evita la formación de huecos, imperfecciones en la superficie y un llenado incompleto.
Tarifas de refrigeración: La gestión de las velocidades de enfriamiento garantiza que el material se enfríe uniformemente, minimizando el riesgo de alabeo, defectos superficiales e inestabilidad del material.
Manipulación de materiales: La manipulación y el almacenamiento adecuados de los materiales plásticos son cruciales para evitar la contaminación y mantener la integridad del material. Evite la exposición a la humedad, los contaminantes y las fluctuaciones de temperatura.
Control de calidad y seguimiento
Además de utilizar materiales plásticos de alta calidad y el mantenimiento de unas condiciones de procesamiento uniformes, son esenciales un control y una supervisión exhaustivos de la calidad. Inspeccione periódicamente los lotes de material entrante, controle los ajustes de temperatura y presión y realice inspecciones visuales del proceso de moldeo para detectar cualquier desviación o anomalía.
V. Causas de los defectos en el moldeo por inyección
Causas comunes de defectos
Diseño inadecuado del molde: El diseño del molde es un factor crítico en el moldeo por inyección. Pueden producirse defectos cuando el diseño del molde carece de precisión, tiene una ventilación inadecuada o una ubicación incorrecta de las compuertas del molde, lo que provoca problemas como rebabas o líneas de soldadura de llenado incompleto de la cavidad del molde.
Control inadecuado de la temperatura: El control de la temperatura es primordial en el moldeo por inyección. Las variaciones en la temperatura del molde y del material pueden provocar defectos como alabeos, imperfecciones superficiales e inestabilidad dimensional.
Mala calidad del material: La calidad del material de caucho de silicona utilizado en el moldeo por inyección influye directamente en el producto final. Los defectos o inconsistencias del material pueden provocar problemas como la contaminación del material, la formación de huecos y la reducción de la integridad de la pieza.
Tratamiento incoherente de los parámetros de inyección: Las desviaciones en los parámetros de inyección, como la presión, la velocidad y el tiempo, pueden provocar defectos. Una presión de inyección insuficiente o una presión o velocidad de inyección excesivamente altas, por ejemplo, pueden provocar un llenado incompleto o líneas de flujo.
Ventilación inadecuada del moho: Una ventilación inadecuada del molde puede atrapar aire dentro de la cavidad del molde, provocando burbujas de aire o huecos en el componente moldeado.
Contaminación del material: Los contaminantes o impurezas en el material de silicona pueden comprometer la integridad del producto final y provocar defectos estructurales.
Rugosidad de la superficie del molde: La rugosidad de la superficie del molde puede transferirse a la pieza moldeada, dando lugar a imperfecciones o defectos superficiales.
Causas y prevención
Para mitigar los defectos en el moldeo por inyección, tenga en cuenta las siguientes ideas:
Diseño de moldes: Invierta en un diseño preciso del molde, con paredes de grosor uniforme, canales de ventilación adecuados y compuertas estratégicamente situadas. Solucione rápidamente cualquier defecto de diseño.
Control de la temperatura: Mantener temperaturas constantes del molde y del material durante todo el proceso de inyección. Utilice sistemas de control de temperatura para minimizar las variaciones de temperatura.
Calidad del material: Obtenga material de caucho de silicona de alta calidad de proveedores de confianza. Inspeccione periódicamente los lotes de material para comprobar su consistencia y pureza.
Parámetros de inyección: Supervise y ajuste cuidadosamente los parámetros de inyección para conseguir un flujo óptimo del material, llenar completamente la cavidad del molde y evitar defectos como huecos y líneas de flujo.
Ventilación de moho: Implemente una ventilación eficaz del molde para permitir que el aire atrapado escape durante la inyección, reduciendo el riesgo de burbujas de aire y vacíos.
Contaminación del material: Mantenga un entorno de fabricación limpio y controlado para evitar la contaminación del material. Filtre o tamice el material de silicona antes de la inyección.
Acabado de la superficie del molde: Preste atención al acabado de la superficie del molde para garantizar un acabado liso en el producto final. Utilice agentes desmoldeantes si es necesario.
V. Causas de los defectos en el moldeo por inyección
Causas comunes de defectos
Diseño inadecuado del molde:
El diseño del molde es un factor crítico en el moldeo por inyección. Los defectos pueden producirse cuando el diseño del molde carece de precisión, tiene una ventilación inadecuada, una ubicación incorrecta de las compuertas o no tiene en cuenta la contracción, lo que provoca problemas como rebabas, disparos cortos o un llenado incompleto de la cavidad del molde.
Control inadecuado de la temperatura:
El control de la temperatura es primordial en el moldeo por inyección. Las variaciones en la temperatura del molde y del material pueden provocar defectos como alabeos, imperfecciones superficiales e inestabilidad dimensional.
Mala calidad del material:
La calidad del material de caucho de silicona utilizado en moldeo por inyección repercute directamente en el producto final. Los defectos o incoherencias de los materiales pueden provocar problemas como la contaminación del material, la formación de huecos y la reducción de la integridad de las piezas.
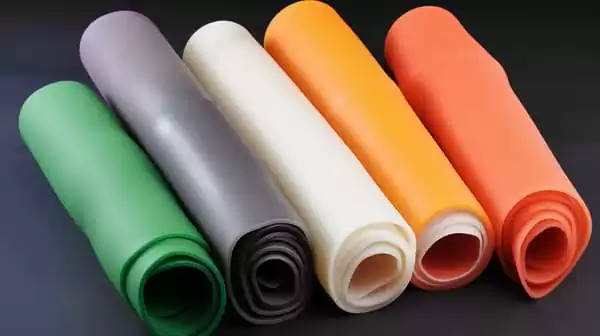
Parámetros de inyección incoherentes: Las desviaciones en los parámetros de inyección, como la presión, la velocidad y el tiempo, pueden provocar defectos. Una presión de inyección insuficiente o una velocidad de inyección excesivamente alta, por ejemplo, pueden provocar un llenado incompleto o líneas de flujo.
Ventilación inadecuada del moho: Una ventilación inadecuada del molde puede atrapar aire dentro de la cavidad del molde, provocando burbujas de aire o huecos en el componente moldeado.
Contaminación del material: Los contaminantes o impurezas en el material de silicona pueden comprometer la integridad del producto final y provocar defectos estructurales.
Rugosidad de la superficie del molde: La rugosidad de la superficie del molde puede transferirse a la pieza moldeada, dando lugar a imperfecciones o defectos superficiales.
Causas y prevención
Para mitigar los defectos en el moldeo por inyección, tenga en cuenta las siguientes ideas:
Diseño de moldes: Invierta en un diseño preciso del molde, con paredes de grosor uniforme, canales de ventilación adecuados y compuertas estratégicamente situadas. Solucione rápidamente cualquier defecto de diseño.
Control de la temperatura: Mantener temperaturas constantes del molde y del material durante todo el proceso de inyección. Utilice sistemas de control de temperatura para minimizar las variaciones de temperatura.
Calidad del material: Obtenga material de caucho de silicona de alta calidad de proveedores de confianza. Inspeccione periódicamente los lotes de material para comprobar su consistencia y pureza.
Parámetros de inyección: Supervise y ajuste cuidadosamente los parámetros de inyección para conseguir un flujo óptimo del material, llenar completamente la cavidad del molde y evitar defectos como huecos y líneas de flujo.
Ventilación de moho: Implemente una ventilación eficaz del molde para permitir que el aire atrapado escape durante la inyección, reduciendo el riesgo de burbujas de aire y vacíos.
Contaminación del material: Mantenga un entorno de fabricación limpio y controlado para evitar la contaminación del material. Filtre o tamice el material de silicona antes de la inyección.
Acabado de la superficie del molde: Preste atención al acabado de la superficie del molde para garantizar un acabado liso en el producto final. Utilice agentes desmoldeantes si es necesario.
VI.Defectos comunes y soluciones
1. Burbujas de aire:
Defecto: Las burbujas de aire son bolsas de aire atrapadas dentro de la pieza moldeada, que pueden debilitar su estructura y afectar a la estética.
Solución: Para evitar las burbujas de aire, asegúrese de que el molde esté bien ventilado y utilice parámetros de inyección constantes, como la temperatura del molde y la presión de inyección. Los canales de ventilación y el mantenimiento de una temperatura adecuada del molde ayudan a que el aire salga durante la inyección.
2. Imperfecciones superficiales:
Defecto: Las imperfecciones de la superficie, como texturas rugosas o irregularidades, pueden estropear el aspecto y la funcionalidad del pieza moldeada.
Solución: Consiga un acabado superficial liso manteniendo una rugosidad precisa de la superficie del molde. La aplicación adecuada de lubricante para moldes también puede mejorar el acabado.
3. Flash:
Defecto: Las rebabas se producen cuando el exceso de material se escapa de la cavidad del molde, dando lugar a proyecciones finas no deseadas a lo largo de los bordes de la pieza.
Solución: Mejore el diseño del molde y asegúrese de que se sujeta correctamente para evitar el parpadeo. Además, controle la presión de inyección, la temperatura y la velocidad de inyección para evitar el sobrellenado.
4. Relleno incompleto:
Defecto: Un llenado incompleto da lugar a piezas con secciones faltantes o huecos.
Solución: Ajuste los parámetros de inyección, incluidas la velocidad y la presión de inyección, para favorecer el llenado completo de la cavidad del molde. Una ventilación adecuada del molde también puede ayudar al llenado.
5. Deformación:
Defecto: Pueden producirse alabeos o distorsiones debido a velocidades de enfriamiento desiguales, lo que provoca deformaciones en las piezas.
Solución: Controlar las velocidades de enfriamiento y mantener temperaturas constantes del molde y del material para evitar deformaciones. Conseguir un enfriamiento uniforme mediante diseño de moldes.
6. Contaminación del material:
Defecto: La contaminación del material puede debilitar el caucho de silicona y provocar defectos estructurales.
Solución: Obtenga material de silicona de alta calidad, mantenga un entorno de fabricación limpio y filtre o tamice los materiales para evitar la contaminación.
7. Líneas de flujo:
Defecto: Las líneas de flujo son líneas o rayas visibles en la superficie de la pieza causadas por incoherencias en el flujo del material.
Solución: Ajuste los parámetros de inyección, incluida la velocidad de inyección, para favorecer un flujo uniforme del material. El diseño adecuado del molde y la ventilación pueden aumentar la velocidad de inyección y también ayudar a eliminar las líneas de flujo.
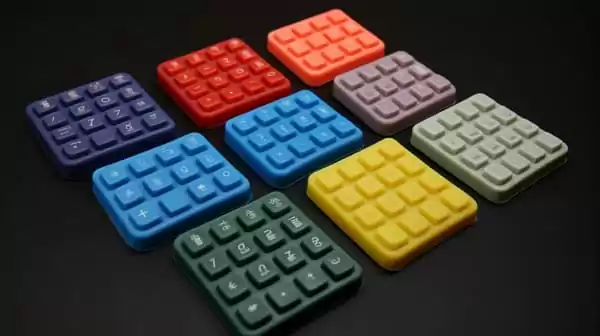
Conclusión
El moldeo de caucho de silicona es un método de fabricación muy eficaz, pero no está exento de dificultades. Los defectos comunes pueden comprometer la calidad y la integridad del producto final. Sin embargo, mediante la aplicación de soluciones clave y mejores prácticas, los fabricantes pueden superar estos obstáculos y producir componentes de caucho de silicona de alta calidad.
En el mundo del moldeo de caucho de silicona, la búsqueda de la perfección es un viaje continuo. Al adoptar estos consejos y hacer hincapié en la importancia de la supervisión y la mejora continuas, los fabricantes no solo pueden resolver los defectos comunes, sino también mejorar la calidad y la eficiencia generales de sus procesos de moldeo de caucho de silicona. Con cada perfeccionamiento, se acercan más a la consecución de los más altos niveles de excelencia en sus operaciones de fabricación.