Introducción
El moldeo por compresión es un proceso de fabricación vital con un profundo impacto en diversas industrias. Este artículo se adentra en el mundo del moldeo por compresión, explorando su importancia, sus retos y el papel fundamental que desempeña el software de simulación para superar estos obstáculos.
El moldeo por compresión es una técnica de fabricación muy utilizada para fabricar componentes complejos a partir de multitud de materiales, como plásticos, compuestos y caucho. Este proceso es muy importante por su capacidad de producir piezas de alta calidad con precisión, lo que la hace indispensable en sectores como la automoción, la industria aeroespacial y los bienes de consumo.
Aunque el moldeo por compresión ofrece numerosas ventajas, no está exento de complejidades y desafíos. Conseguir resultados óptimos en el moldeo por compresión requiere un delicado equilibrio de parámetros, como la temperatura, la presión, las propiedades de los materiales y la temperatura. moldeo por compresión fundamentos y diseño. La interacción de estos factores puede ser compleja y dar lugar a problemas como huecos, alabeos y flujos de material incoherentes. Estos retos exigen soluciones innovadoras para mejorar la calidad del producto, reducir los residuos y optimizar la producción.
Aquí es donde el software de simulación entra en escena. El software de simulación se ha convertido en una poderosa herramienta que permite a los fabricantes enfrentarse a las complejidades del moldeo por compresión. Mediante la creación de modelos virtuales y la realización de simulaciones de llenado de moldes de compresión, los fabricantes pueden predecir resultados, optimizar parámetros e identificar posibles defectos, todo ello sin necesidad de costosos prototipos físicos. No se puede exagerar la importancia del software de simulación de elementos finitos para abordar las complejidades del moldeo por compresión, ya que desempeña un papel fundamental a la hora de impulsar la eficiencia, mejorar la calidad y, en última instancia, dar forma al futuro de la fabricación.
En las secciones siguientes profundizaremos en la proceso de moldeo por compresión, explorará las formas en que el software de simulación puede aprovecharse eficazmente y proporcionará ideas prácticas para optimizar los resultados del moldeo por compresión.
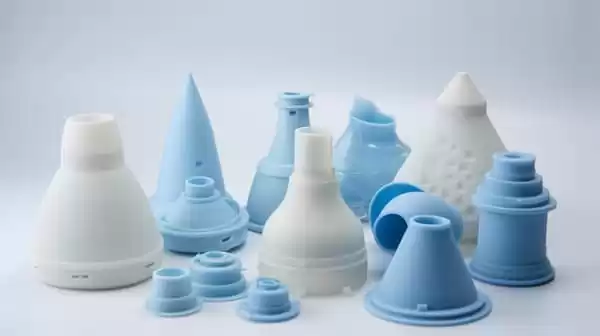
II. Comprender el moldeo por compresión
El moldeo por compresión es un proceso de fabricación que implica varios pasos distintos y una variedad de parámetros críticos. En esta sección, desglosaremos los aspectos básicos del proceso de moldeo por compresión y arrojaremos luz sobre los parámetros y variables clave que influyen significativamente en los resultados.
Pasos básicos del moldeo por compresión
1. Preparación:
El proceso de moldeo por compresión comienza con la preparación de la materia prima, que suele presentarse en forma de gránulos o preformas. Este material se carga en una cavidad de molde, que es un espacio diseñado con precisión que determina la forma final del producto.
2. Calefacción:
Una vez cargada de material la cavidad del molde, se cierra y se aplica calor al material. El calor ablanda el material, lo hace más maleable y lo prepara para el moldeo.
3. Compresión:
Una vez alcanzada la temperatura deseada, se aplica presión al material. Esta compresión obliga al material a llenar completamente la cavidad del molde, adoptando la forma de éste.
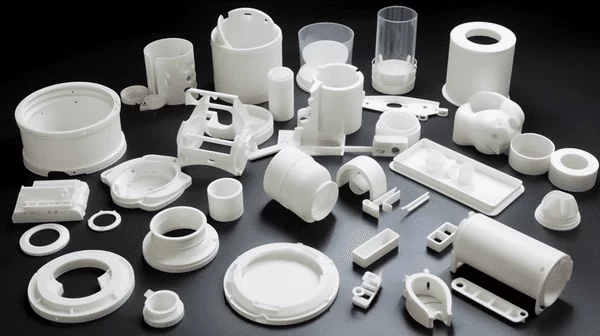
4. Refrigeración:
Tras la fase de compresión, el molde se enfría para solidificar el material. El tiempo de enfriamiento se controla cuidadosamente para garantizar que el material conserve su forma e integridad estructural.
5. Expulsión:
Una vez que el material se ha enfriado y solidificado lo suficiente, el producto final se expulsa del molde. A continuación, el producto está listo para su posterior procesamiento o uso.
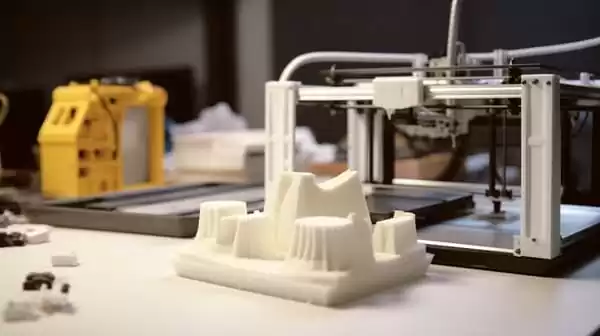
Parámetros y variables clave en el moldeo por compresión
La obtención de resultados óptimos en el moldeo por compresión depende de un cuidadoso equilibrio de varios parámetros y variables críticos, entre los que se incluyen:
Temperatura: La temperatura a la que se calienta el material desempeña un papel fundamental en su comportamiento durante el proceso de moldeo por inyección y compresión. Afecta a las características de flujo, curado y rendimiento general del material.
Presión: La aplicación de presión es necesaria para garantizar que el material llene completamente la cavidad del molde. Un control adecuado de la presión evita defectos y garantiza la uniformidad del llenado del molde.
La hora: La duración de cada fase del proceso de moldeo, incluidos el calentamiento, la compresión y el enfriamiento, influye directamente en la calidad y las propiedades del producto final.
Propiedades del material: Las características del material, como la viscosidad, la velocidad de flujo de la masa fundida y el comportamiento de curado, son consideraciones esenciales en el moldeo por compresión. La elección del material influye enormemente en el proceso de moldeo y en la calidad del producto final.
Diseño del molde: La orientación de la fibra de la geometría de la cavidad del molde, así como elementos como los orificios de ventilación y los canales, afectan significativamente al flujo de material y a la estructura de la pieza final.
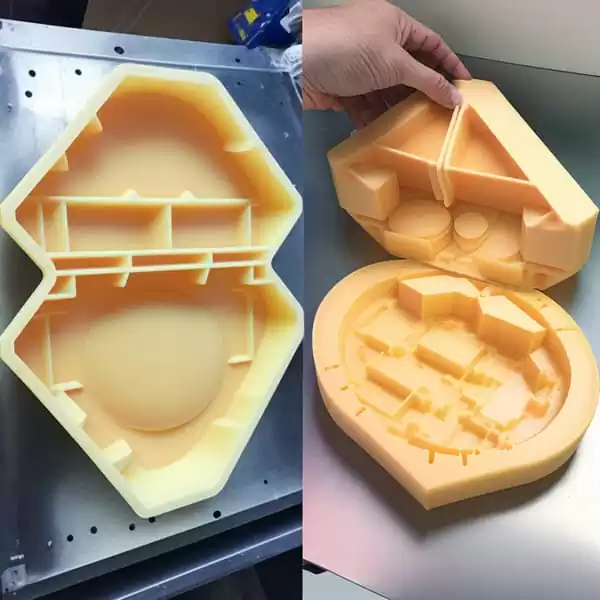
Tasa de enfriamiento: La velocidad a la que se enfría el compuesto de moldeo de la lámina superior tras la compresión influye en la cristalización del material y, posteriormente, en sus propiedades mecánicas.
En la siguiente sección, exploraremos cómo se puede aprovechar el software de simulación para optimizar estos parámetros y variables, lo que en última instancia conduce a mejores resultados de moldeo por compresión.
III. Papel del software de simulación
El software de simulación cambia las reglas del juego en el ámbito del moldeo por compresión. En esta sección, introduciremos el concepto de software de simulación en el contexto del moldeo por compresión, destacando cómo sirve como una poderosa herramienta para predecir resultados, optimizar los parámetros del proceso, reducir defectos, diseñar moldes, mejorar la selección de materiales y, en última instancia, ahorrar tiempo y recursos valiosos.
Software de simulación
El software de simulación, en el contexto del moldeo por compresión, hace referencia a herramientas informáticas avanzadas que permiten a los fabricantes crear modelos virtuales de todo el proceso de moldeo. Estos modelos virtuales imitan las condiciones del mundo real, lo que permite a los ingenieros y fabricantes obtener información valiosa sobre cómo los diferentes parámetros y variables afectarán al producto final. Básicamente, se trata de una caja de arena digital donde se experimenta sin necesidad de prototipos físicos.
Predecir resultados con precisión
Una de las ventajas más significativas del software de simulación en el moldeo por compresión es su capacidad para predecir resultados con precisión. Los ingenieros pueden introducir en la simulación parámetros específicos, como la temperatura, la presión y las propiedades del material. A continuación, el software calcula cómo interactuarán estos parámetros, proporcionando una imagen clara de lo que cabe esperar durante la producción real. Esta capacidad de predicción permite a los fabricantes ajustar sus procesos para obtener resultados óptimos.
Optimización de los parámetros del proceso
El software de simulación no se limita a la predicción, sino que también destaca en la optimización. Al ejecutar simulaciones con varias combinaciones de parámetros, los fabricantes pueden determinar los ajustes ideales para su proceso de moldeo por compresión. Por ejemplo, pueden identificar la combinación óptima de temperatura y presión que reduzca los tiempos de ciclo, disminuya los costes de producción y mejore la calidad del producto. Esta optimización es un paso crucial para conseguir los mejores resultados posibles en la simulación del proceso de moldeo por compresión.
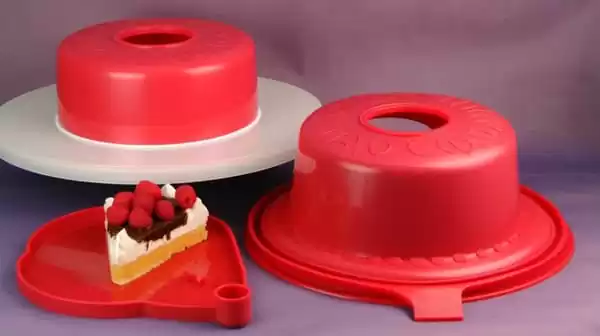
Reducción de defectos y mejora de la calidad
En la búsqueda de la excelencia, el software de simulación es una potente herramienta para reducir los defectos. Al simular el proceso de moldeo, los fabricantes pueden identificar posibles defectos como huecos, alabeos o problemas con el flujo de material antes de que se produzcan en la producción real. Con este conocimiento, se pueden realizar ajustes en el proceso, reduciendo eficazmente los defectos y mejorando la calidad general del producto final.
Diseño de moldes eficientes
El diseño de moldes es un aspecto crítico del moldeo por compresión, y el software de simulación ayuda significativamente en esta área. Los ingenieros pueden utilizar el software para diseñar moldes con geometrías complejas que son difíciles de conseguir únicamente mediante ensayo y error. El software garantiza que los moldes sean eficientes y capaces de producir piezas de alta calidad de forma constante.
Mejorar la selección de materiales
El software de simulación permite a los fabricantes evaluar cómo se comportarán los distintos materiales durante el moldeo por compresión. Esto es especialmente valioso cuando se trata de materiales avanzados como los compuestos reforzados con fibra. Mediante la simulación de diferentes opciones de materiales, los fabricantes pueden tomar decisiones informadas sobre qué material es el más adecuado para una aplicación específica, garantizando un rendimiento óptimo.
Ahorro de tiempo y recursos
Quizá uno de los aspectos más atractivos del software de simulación sea su capacidad para ahorrar tiempo y recursos. Los métodos tradicionales de ensayo y error pueden ser costosos y requerir mucho tiempo, con múltiples prototipos físicos e iteraciones. El software de simulación elimina gran parte de este proceso de prueba y error, ya que permite a los ingenieros perfeccionar los procesos digitalmente antes de pasar a la producción física.
En la siguiente sección, profundizaremos en los pasos prácticos que pueden dar los fabricantes para aprovechar eficazmente el poder del software de simulación en el proceso de moldeo por compresión.
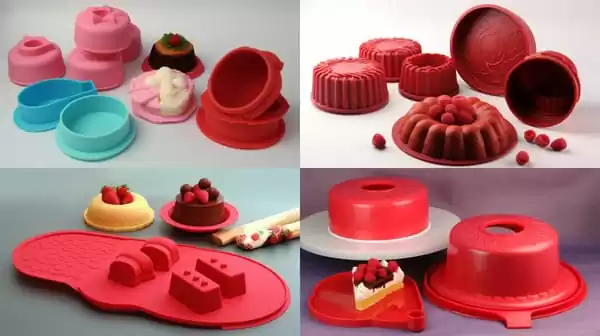
IV. Pasos para utilizar eficazmente el software de simulación
La utilización eficaz del software de simulación en el moldeo por compresión requiere un enfoque sistemático. Los fabricantes pueden seguir una guía paso a paso para maximizar los beneficios de esta potente herramienta. He aquí un esquema exhaustivo de los pasos clave:
1. 1. Recogida de datos
Una simulación eficaz comienza con una recopilación de datos sólida. Los fabricantes deben recopilar todos los datos pertinentes:
- Propiedades del material: Información completa sobre el material utilizado, como su viscosidad, velocidad de fusión, conductividad térmica y comportamiento de curado.
- Especificaciones del molde: Especificaciones detalladas del molde, incluidas dimensiones, geometría y detalles de ventilación.
- Parámetros del proceso: Datos precisos sobre parámetros de proceso como temperatura, presión y tiempos de ciclo.
- Datos históricos: Todos los datos de producción anteriores o registros de defectos que puedan informar el proceso de simulación.
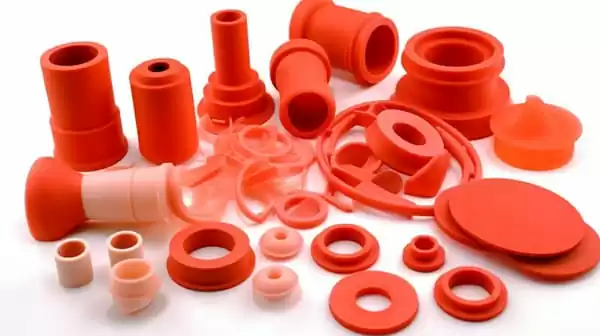
2. Creación de modelos
Con los datos en la mano, el siguiente paso es crear un modelo virtual del proceso de moldeo por compresión. Esto implica:
- Creación de geometría: Creación de una representación en 3D del molde y el material en el software de simulación.
- Entrada de parámetros: Introducción en el modelo de simulación de todos los datos recopilados, incluidas las propiedades de los materiales y los parámetros del proceso.
- Condiciones límite: Definir las condiciones de contorno, como las temperaturas y presiones iniciales.
3. Simulación
Una vez preparado el modelo, se emplea un software de simulación para ejecutar procesos virtuales de moldeo por compresión. Durante esta fase:
- Simule el proceso: El software realiza simulaciones basadas en el modelo definido, replicando el proceso real de moldeo por compresión.
- Supervisar el comportamiento: Los ingenieros pueden controlar cómo fluye el material, cómo se distribuye la presión y cómo cambia la temperatura dentro del molde virtual.
4. Análisis
Una vez finalizadas las simulaciones, es hora de analizarlas en profundidad:
- Identificación de defectos: Examine los resultados de la simulación para identificar posibles defectos o problemas en el proceso. Puede tratarse de huecos, alabeos o flujos de material incoherentes.
- Propiedades mecánicas: Analizar las propiedades mecánicas previstas del producto final, como la resistencia, la rigidez y la elasticidad.
- Comportamiento material: Comprender cómo se comporta el material en diferentes condiciones y presiones.
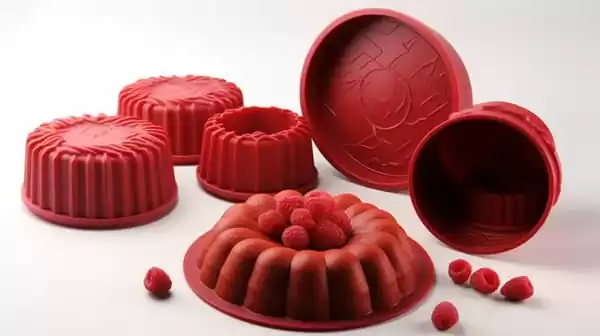
5. Optimización
Con una comprensión clara de los resultados de la simulación y de las áreas de mejora identificadas, los fabricantes pueden proceder a la optimización:
- Ajuste de parámetros: Modificar los parámetros del proceso, como la temperatura, la presión o el tiempo de ciclo, para optimizar el proceso de moldeo por compresión.
- Selección de materiales: Basándose en los resultados de la simulación, considere diferentes materiales o mezclas de materiales que puedan mejorar las propiedades del producto final.
- Diseño del molde: Ajuste el diseño del molde para mejorar el flujo de material y minimizar los defectos.
6. Validación
La validación es un paso crucial para garantizar que los resultados de la simulación coinciden con los del mundo real:
- Comparación con datos reales: Validar los resultados de la simulación comparándolos con los datos reales de producción y los prototipos físicos.
- Itere si es necesario: Si se detectan disparidades, realice los ajustes necesarios en el modelo de simulación y ejecute pruebas adicionales hasta que los resultados coincidan con el rendimiento en el mundo real.
7. Aplicación
Por último, aplicar el proceso optimizado basándose en los resultados de la simulación:
- Ajuste del proceso: Aplicar los parámetros de proceso revisados, los diseños de moldes o las selecciones de materiales en la producción real.
- Supervisión continua: Supervisar continuamente la producción para garantizar que se mantienen las mejoras conseguidas mediante la simulación.
- Bucle de retroalimentación: Establecer un circuito de retroalimentación en el que los datos de la producción real se utilicen para perfeccionar y mejorar el modelo de simulación para su uso futuro.
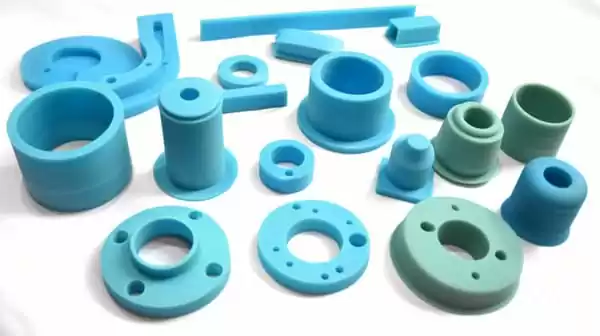
Seguir estos pasos de forma sistemática permite a los fabricantes aprovechar todo el potencial del software de simulación en el moldeo por compresión, lo que se traduce en una mejora de la calidad del producto, una reducción de los defectos y unos procesos de producción más eficaces.
IV. ¿Qué es la simulación Moldflow?
En el intrincado mundo de la industria del plástico, la simulación Moldflow emerge como una herramienta especializada e indispensable. Esta sección definirá y explicará la simulación Moldflow, arrojando luz sobre su papel en la comprensión del flujo de material y la distribución dentro de los moldes.
Definición de la simulación Moldflow
La simulación Moldflow es una herramienta de software altamente especializada empleada en la industria del plástico. Su función principal es crear representaciones virtuales de todo el proceso de moldeo por inyección, lo que permite a los fabricantes comprender en profundidad cómo fluye y se distribuye el material plástico fundido dentro de los moldes. Esta herramienta funciona como un laboratorio virtual que proporciona información sobre el complejo comportamiento de los materiales durante el proceso de moldeo.
Comprender el flujo y la distribución de materiales
La simulación Moldflow destaca por su capacidad para simular y analizar el flujo y la distribución de materiales con un alto grado de precisión. He aquí cómo lo consigue:
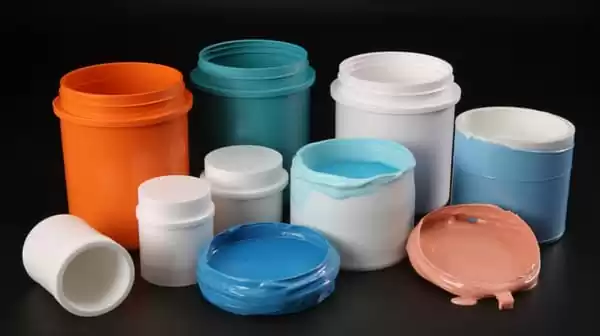
- Comportamiento material: La simulación Moldflow comienza considerando las propiedades del material plástico utilizado. Esto incluye aspectos como la viscosidad de la masa fundida, el comportamiento en función de la temperatura y las características reológicas.
- Análisis geométrico: A continuación, el software tiene en cuenta la geometría de la cavidad del molde, incluidos sus intrincados rasgos, compuertas, canales y canales de refrigeración. Este análisis es crucial para comprender cómo fluirá el material dentro del molde.
- Simulación de inyección: El corazón de la simulación Moldflow reside en su capacidad para simular la fase de inyección. Predice cómo entrará el material plástico fundido en el molde, cómo llenará cada rincón y cómo se distribuirá la presión.
- Visualización de flujos: Mediante la simulación, Moldflow genera representaciones visuales del flujo de material. Esto puede incluir frentes de flujo, perfiles de presión y gradientes de temperatura, lo que ofrece a ingenieros y fabricantes una imagen clara de lo que ocurre en el interior del molde.
- Identificación de defectos: La simulación Moldflow también es competente en la identificación de posibles defectos que puedan producirse durante el proceso de moldeo por inyección. Esto incluye problemas como trampas de aire, líneas de soldadura, marcas de hundimiento y llenado incompleto.
Papel en el diseño y la optimización de moldes
La simulación Moldflow no sólo sirve para comprender el flujo de materiales, sino también para diseñar y optimizar moldes. He aquí cómo:
- Diseño del molde: Los ingenieros pueden utilizar la simulación Moldflow para afinar los diseños de moldes, asegurándose de que el flujo de material es uniforme y de que se minimizan los defectos. Esto puede implicar la modificación de la ubicación de las compuertas, el ajuste de los sistemas de canalización y la optimización de las estrategias de refrigeración.
- Selección de materiales: La simulación permite evaluar distintos materiales y su comportamiento dentro del molde. Los fabricantes pueden elegir el material más adecuado basándose en los resultados de la simulación.
- Optimización: La simulación Moldflow ayuda a optimizar los parámetros del proceso, como la velocidad de inyección, la temperatura de la masa fundida y la velocidad de enfriamiento, para obtener los mejores resultados de moldeo posibles.
En resumen, la simulación Moldflow es una herramienta de software especializada diseñada para la industria del plástico. Desempeña un papel fundamental en la comprensión de cómo el material plástico fundido fluye y se distribuye dentro de los moldes durante el proceso de moldeo por inyección. Mediante la simulación del comportamiento del material, la geometría del molde y la fase de inyección, Moldflow proporciona información muy valiosa sobre el complejo mundo del moldeo de plásticos. No sólo ayuda en la identificación de defectos, sino que también orienta el diseño del molde y la optimización del proceso, lo que en última instancia conduce a un proceso más eficaz y eficiente. componentes de plástico de mayor calidad.
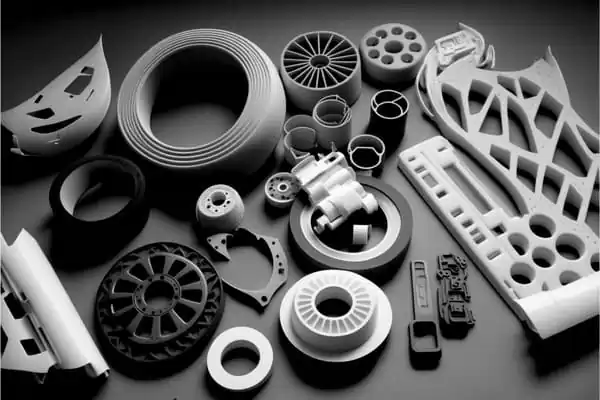
V. Parámetros de control en el proceso de moldeo por compresión
El éxito del proceso de moldeo por compresión depende del control cuidadoso de diversos parámetros y variables. En esta sección, vamos a enumerar y explicar los parámetros de control que desempeñan un papel fundamental en la consecución de resultados óptimos de moldeo por compresión:
1. Temperatura:
- Explicación: El control de la temperatura es fundamental en el moldeo por compresión. Influye en el comportamiento del material al afectar a su viscosidad, flujo de fusión y propiedades de curado. El perfil preciso de temperatura durante las fases de calentamiento y enfriamiento es fundamental para la calidad del producto.
2. Presión:
- Explicación: La presión es otro parámetro clave en el moldeo por compresión. Una presión controlada adecuadamente garantiza una distribución uniforme del material, minimiza defectos como huecos o alabeos y compacta el material en la forma deseada dentro de la cavidad del molde.
3. Tiempo:
- Explicación: El tiempo es un parámetro crítico que rige la duración de cada fase del proceso de moldeo por compresión. Es esencial programar cuidadosamente el tiempo para conseguir el curado deseado del material, el enfriamiento y la eficiencia global del proceso.
4. Propiedades del material:
- Explicación: Las propiedades del material que se moldea influyen significativamente en el proceso de moldeo por compresión. Estas propiedades incluyen la viscosidad, la velocidad de flujo de la masa fundida, la conductividad térmica, el comportamiento de curado e incluso las características reológicas del material. Comprender y optimizar estas propiedades del material es esencial para el éxito del moldeo.
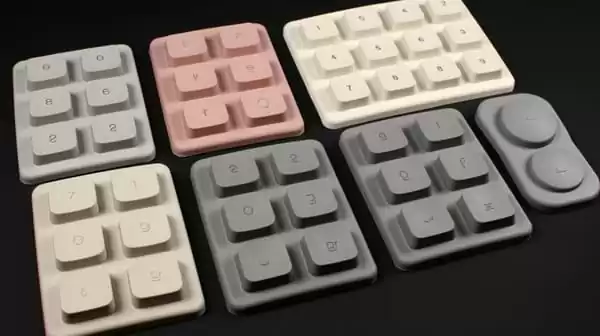
5. Diseño de moldes:
- Explicación: La geometría de la cavidad del molde y otras características, como los orificios de ventilación, las guías y los canales de refrigeración, tienen un profundo impacto en el flujo de material, la distribución y la calidad final de la pieza. Un molde bien diseñado garantiza una compactación eficaz del material y minimiza los defectos.
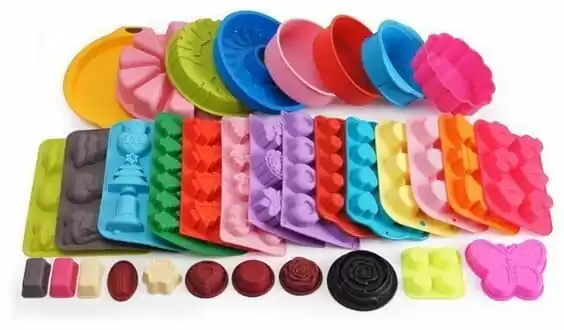
6. Distribución de la presión:
- Explicación: No sólo es crucial la presión global, sino también la distribución de la presión por la superficie del molde. Una distribución uniforme de la presión garantiza una compactación homogénea del material y minimiza defectos como espesores desiguales o huecos en el producto final.
7. Tasa de enfriamiento:
- Explicación: La velocidad a la que se enfría el molde tras la compresión afecta significativamente a la cristalización del material y, en consecuencia, a sus propiedades mecánicas. El control preciso de la velocidad de enfriamiento es esencial para conseguir las propiedades deseadas de la pieza.
8. Temperatura de la superficie del molde:
- Explicación: El control de la temperatura de la superficie del molde es vital para garantizar el correcto curado y desmoldeo del material. La temperatura de la superficie del molde influye en el comportamiento del material durante las fases de calentamiento y enfriamiento.
9. Análisis del flujo de materiales:
- Explicación: Comprender cómo fluye el material dentro del molde es esencial para controlar parámetros como la presión y la temperatura. Analizar el flujo de material puede ayudar a identificar áreas problemáticas y optimizar el proceso de moldeo.
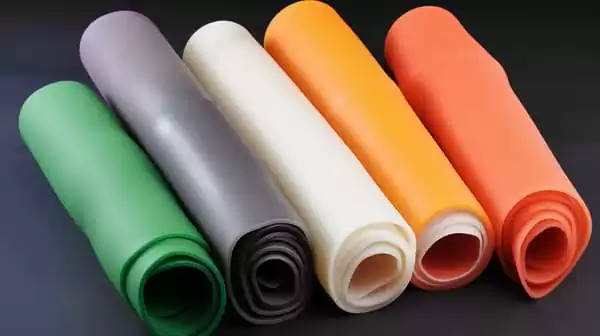
10. Ventilación y evacuación del aire:
- Explicación: Una ventilación y evacuación de aire adecuadas son necesarias para evitar el atrapamiento de aire o gas dentro del molde. Una ventilación eficaz garantiza la compactación completa del material y minimiza los defectos.
Estos parámetros de control definen colectivamente las condiciones en las que tiene lugar el moldeo por compresión. La gestión precisa de estos parámetros es fundamental para lograr resultados uniformes y de alta calidad y garantizar la producción eficaz de componentes moldeados. Los fabricantes deben considerar y optimizar cuidadosamente cada parámetro para satisfacer los requisitos específicos de sus productos y sus normas de calidad.
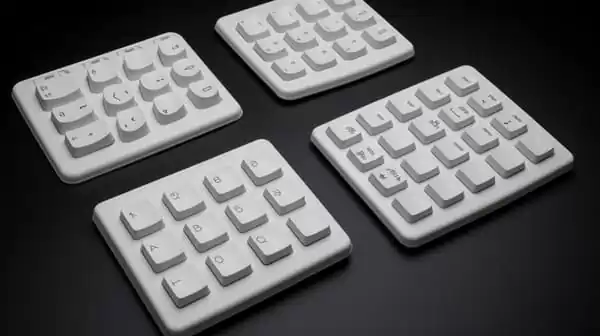
Conclusión
En conclusión, este artículo ha explorado el ámbito del moldeo por compresión, destacando su importancia y las complejidades que conlleva la obtención de resultados óptimos. Hemos hecho hincapié en el papel fundamental que desempeña el software de simulación a la hora de abordar estos retos y optimizar el proceso de moldeo por compresión. He aquí las principales conclusiones:
- Importancia del moldeo por compresión: El moldeo por compresión es un proceso de fabricación crucial que se utiliza en todos los sectores y permite crear componentes complejos con precisión y eficacia.
- Retos del moldeo por compresión: Conseguir resultados óptimos en el moldeo por compresión requiere un control preciso de parámetros como la temperatura, la presión, el tiempo, las propiedades del material y el diseño del molde. Las complejidades en el comportamiento del material y el diseño del molde pueden provocar defectos e ineficiencias.
- El poder del software de simulación: El software de simulación cambia las reglas del juego del moldeo por compresión. Permite a los fabricantes crear modelos virtuales del proceso, predecir resultados, optimizar parámetros y reducir defectos antes de iniciar la producción física.
- Pasos para un uso eficaz de la simulación: Los fabricantes pueden seguir un planteamiento estructurado, que incluya la recopilación de datos, la creación de modelos, la simulación, el análisis, la optimización, la validación y la implantación, para utilizar eficazmente el software de simulación.
- Simulación Moldflow: La simulación Moldflow, una herramienta especializada para la industria del plástico, desempeña un papel crucial en la comprensión del flujo y la distribución del material dentro de los moldes. Ayuda a identificar defectos, diseñar moldes, seleccionar materiales y optimizar procesos.
- Parámetros de control: Los principales parámetros de control en el moldeo por compresión son la temperatura, la presión, el tiempo, las propiedades del material, el diseño del molde, la distribución de la presión, la velocidad de enfriamiento, la temperatura de la superficie del molde, el análisis del flujo de material y la ventilación. El control preciso de estos parámetros es esencial para obtener resultados uniformes y de alta calidad.
- El futuro de la simulación de moldeo: El artículo concluye subrayando la importancia del software de simulación para lograr resultados de moldeo por compresión uniformes y superiores. Es a través del ámbito digital de la simulación como los fabricantes pueden innovar, optimizar y adaptarse al cambiante panorama de la ingeniería mecánica y el procesamiento de polímeros. A medida que avanza la tecnología, podemos esperar que las herramientas de simulación sean aún más integrales en la configuración del futuro de la fabricación.
En el mundo en constante evolución de la ingeniería mecánica y el procesamiento de polímeros, el software de simulación es la brújula que nos guía hacia una mayor eficacia, innovación y excelencia en el moldeo por compresión. Con cada simulación, nos acercamos más al perfeccionamiento del arte de fabricar componentes de precisión ahorrando tiempo y recursos valiosos. De cara al futuro, prevemos que el software de simulación seguirá desempeñando un papel transformador a la hora de ampliar los límites de lo que es posible en la fabricación, garantizando que el moldeo por compresión siga siendo una piedra angular de la producción moderna.