Introducción
El diseño de los moldes desempeña un papel fundamental en la fabricación de productos de caucho de silicona de alta calidad. Los moldes utilizados para moldear y dar forma al caucho de silicona influyen directamente en su calidad final, funcionalidad y eficiencia; optimizar el diseño de estos moldes es cada vez más importante, ya que los productos de caucho de silicona siguen ganando popularidad en numerosos sectores.
Productos de caucho de silicona son muy codiciados por sus extraordinarias propiedades de resistencia al calor, flexibilidad y durabilidad. El caucho de silicona ha encontrado aplicaciones en numerosos sectores, como la automoción, la electrónica, los dispositivos médicos y la producción de bienes de consumo; su versatilidad y fiabilidad lo convierten en el material preferido de los fabricantes que buscan desarrollar productos innovadores y de alto rendimiento.
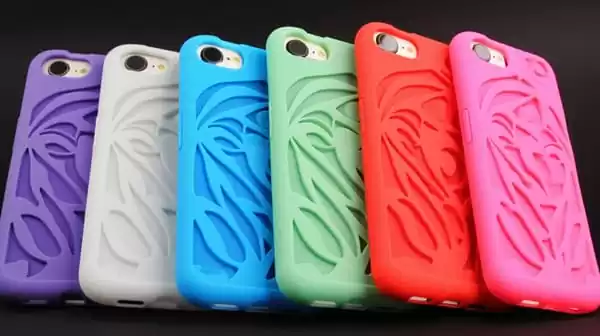
Los diseños de moldes optimizados pueden ayudar a los fabricantes a liberar todo el potencial del caucho de silicona y satisfacer la creciente demanda de productos de calidad por parte de los consumidores, ya que garantizan un flujo de material eficiente, reducen los defectos y aseguran una calidad constante de las piezas. Optimizar el diseño de los moldes no solo garantiza una mayor productividad, sino que también contribuye a su éxito y competitividad en el mercado.
II. Comprensión de los procesos de moldeo de caucho de silicona líquida (LSR)
A. Definición del moldeo de LSR como proceso de moldeo por inyección para productos de caucho de silicona
El moldeo de LSR (o moldeo de caucho de silicona líquida ) es una técnica de proceso de moldeo por inyección líquida utilizada para fabricar productos de caucho de silicona. La técnica consiste en inyectar caucho de silicona líquido a alta presión y temperatura en las cavidades del molde, para conseguir la forma y las propiedades deseadas. El moldeo con LSR ofrece varias ventajas sobre el moldeo por inyección convencional, como alta precisión, excelente calidad de las piezas y capacidad para producir geometrías complejas.
El inicio del proceso implica la creación de material de caucho de silicona líquido, que suele constar de dos componentes -polímero de silicona base y catalizador/reticulante cruzado- mezclados en proporciones precisas para obtener las propiedades del material y las características de curado deseadas.
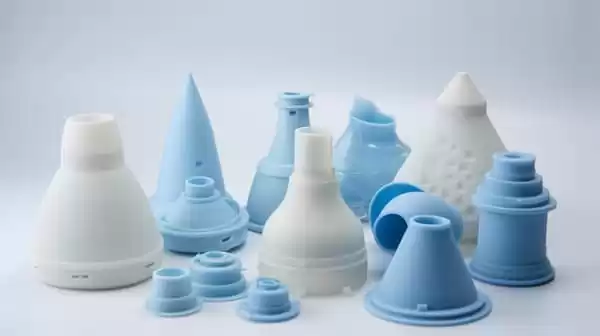
El caucho de silicona líquido se introduce en una máquina de moldeo por inyección, que consta de un cilindro calentado, un mecanismo de tornillo o émbolo para el suministro de material y una cavidad de molde. Aquí, el material se calienta antes de ser forzado a alta presión en su forma de molde y cavidad deseadas.
Una vez que el caucho de silicona líquido se ha inyectado en un molde, debe pasar por un proceso de curado en el que se puede utilizar el calentamiento o el enfriamiento para promover el curado adecuado y la solidificación de su material. Una vez completado, el molde puede abrirse y la pieza de caucho de silicona solidificada puede expulsarse del mismo.
B. Visión general de la máquina de moldeo por inyección y su papel en el proceso
La máquina de moldeo por inyección es un componente crucial en la Proceso de moldeo de LSR. Consta de varios elementos clave que facilitan la inyección y el moldeado de caucho de silicona líquido en el producto deseado. A continuación se ofrece un resumen de los principales componentes y sus funciones:
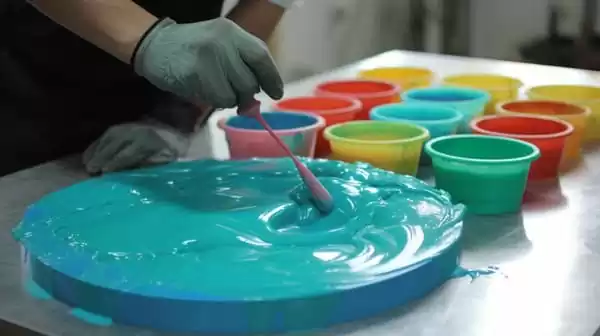
1.Mecanismo de cañón y tornillo/émbolo:
El cilindro aloja el material de caucho de silicona líquido y lo calienta a una temperatura controlada. A continuación, el mecanismo de tornillo o émbolo avanza para inyectar el material en la cavidad del molde.
2.Cavidad del molde:
La cavidad del molde es el espacio hueco del molde que define la forma final del producto de caucho de silicona. Se diseña para acomodar la geometría, las características y las dimensiones deseadas de la pieza.
3.Sistemas de calefacción y refrigeración:
La máquina de moldeo por inyección incluye sistemas de calentamiento y enfriamiento que regulan la temperatura del molde. El calentamiento es necesario para facilitar el flujo y el curado del material, mientras que el enfriamiento ayuda a solidificar la pieza de caucho de silicona para su expulsión.
4.Unidad de sujeción:
La unidad de cierre mantiene unidas las mitades del molde durante el proceso de inyección, garantizando una alineación correcta y evitando fugas de material. Ejerce la fuerza necesaria para mantener el molde cerrado durante la inyección y abierto para la expulsión de la pieza.
La máquina de moldeo por inyección proporciona un control preciso de la velocidad de inyección, la presión, la temperatura y otros parámetros del proceso, lo que garantiza la consistencia de la inyección. producción y productos de caucho de silicona de alta calidad.
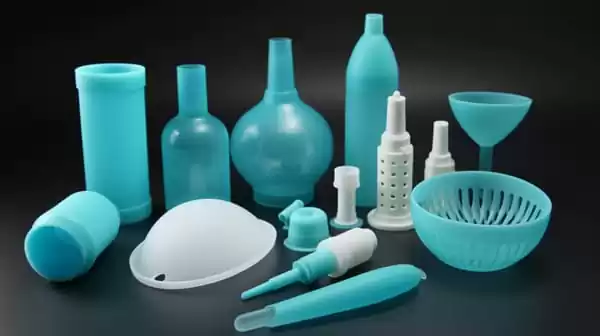
III. Consideraciones clave para la optimización del diseño de moldes
A. Importancia de comprender los requisitos del producto para el éxito del diseño del molde
Para optimizar el diseño de moldes para productos de caucho de silicona, es fundamental conocer a fondo los requisitos del producto. Esto incluye factores como las dimensiones, la complejidad, el acabado superficial y los atributos funcionales. Al comprender estos requisitos, los fabricantes pueden adaptar el diseño del molde para satisfacer necesidades específicas, garantizando la producción de productos de caucho de silicona de alta calidad que se ajusten a las expectativas del cliente.
B. Diseño para la moldeabilidad: evitar geometrías intrincadas, esquinas afiladas y socavaduras.
Diseñar productos de caucho de silicona teniendo en cuenta la moldeabilidad es esencial para optimizar el diseño del molde. Es aconsejable evitar las geometrías complejas, las esquinas afiladas y los rebajes, ya que pueden plantear problemas durante el desmoldeo y afectar a la calidad de las piezas. En su lugar, incorpore curvas suaves y ángulos de desmoldeo para facilitar el desmoldeo y garantizar un flujo de material adecuado dentro de la cavidad del molde.
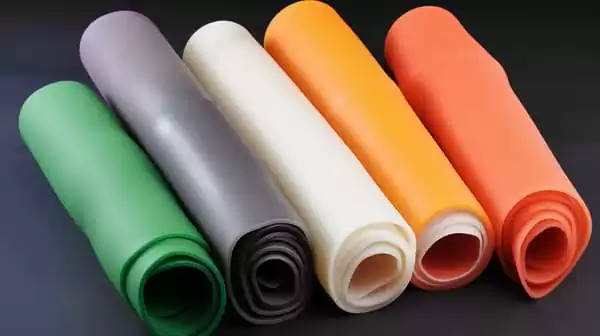
C. Consideraciones sobre el grosor de las paredes y su repercusión en la calidad de las piezas y el flujo de material
Un grosor de pared adecuado es fundamental para lograr un diseño óptimo del molde. Mantener un grosor de pared constante y adecuado en todo el producto de caucho de silicona garantiza un curado uniforme y evita problemas como las trampas de aire o las restricciones de flujo de material. Las desviaciones en el grosor de la pared pueden provocar variaciones en la calidad de la pieza, incluidos defectos como alabeos o marcas de hundimiento. La consideración cuidadosa del grosor de la pared durante el proceso de diseño es esencial para conseguir una calidad de la pieza y un flujo del material uniformes.
D. Técnicas de ventilación y desgasificación para una liberación eficaz del aire y los gases durante el curado.
La ventilación y desgasificación efectivas son cruciales en la optimización del diseño de moldes para productos de caucho de silicona. La incorporación de respiraderos en el molde permite que el aire o los gases atrapados escapen durante el proceso de curado. Una ventilación adecuada evita la formación de defectos como burbujas de aire o huecos que pueden comprometer la integridad del producto. La colocación cuidadosa de los orificios de ventilación en las zonas donde es probable que quede atrapado aire o gas garantiza una evacuación eficaz del aire y un curado óptimo.
E. Diseño del sistema de refrigeración y su efecto en los tiempos de ciclo y la estabilidad dimensional
Un diseño eficaz del sistema de refrigeración es esencial para optimizar el diseño del molde y conseguir tiempos de ciclo más cortos y estabilidad dimensional en la fabricación de productos de caucho de silicona. Una refrigeración adecuada ayuda a controlar el proceso de curado, reducir la contracción de las piezas y mantener la precisión dimensional. La colocación estratégica de los canales de refrigeración dentro del molde, junto con los medios de refrigeración adecuados, garantiza una refrigeración uniforme y una disipación eficaz del calor. Los sistemas de refrigeración bien diseñados mejoran la productividad, minimizan el tiempo de curado y contribuyen a una calidad constante de las piezas.
Al tener en cuenta estos factores clave durante el proceso de optimización del diseño del molde, los fabricantes pueden lograr diseños de molde óptimos que den como resultado productos de caucho de silicona de alta calidad. Estas consideraciones, incluidos los requisitos del producto, la moldeabilidad, el grosor de la pared, la ventilación y la refrigeración, desempeñan un papel fundamental en la mejora de la calidad de las piezas, la eficiencia de la producción y la satisfacción del cliente.
IV. Técnicas avanzadas para la optimización del diseño de moldes
A. El moldeo por inserción y sus ventajas para incorporar componentes adicionales o insertos
El moldeo por inserción es una técnica avanzada utilizada en la optimización del diseño de moldes para productos de caucho de silicona. Consiste en colocar componentes adicionales o insertos en la cavidad del molde antes de inyectar el caucho de silicona líquido. Las ventajas del moldeo por inserción incluyen:
Mayor funcionalidad de la pieza: El moldeo por inserción permite integrar componentes funcionales, como insertos metálicos o conectores eléctricos, directamente en la producto de caucho de silicona. Esto mejora el rendimiento y la funcionalidad del producto.
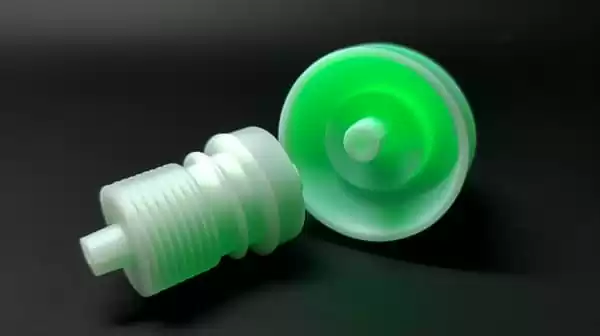
Mayor resistencia y estabilidad de la pieza: Al unir firmemente los insertos con el caucho de silicona, el moldeo por inserción mejora la integridad estructural y la estabilidad del producto final. Elimina la necesidad de procesos de montaje secundarios, reduciendo costes y posibles puntos de fallo.
Flexibilidad de diseño: El moldeo por inserción ofrece flexibilidad de diseño, lo que permite crear geometrías complejas y productos multimaterial. Permite combinar distintos materiales con propiedades variables, lo que amplía la gama de aplicaciones de los productos de caucho de silicona.
B. Utilización de herramientas de simulación y análisis de elementos finitos (FEA) para mejorar la precisión del diseño
Las herramientas de simulación y el análisis de elementos finitos (FEA) son potentes herramientas para la optimización del diseño de moldes. Ayudan a mejorar la precisión del diseño, predecir el flujo de material, identificar posibles defectos y optimizar los parámetros del proceso. Utilizando herramientas de simulación y AEF, los fabricantes pueden:
Visualice y analice el patrón de llenado: Las herramientas de simulación proporcionan una representación visual de cómo fluye el caucho de silicona líquido dentro de la cavidad del molde. Esto permite identificar posibles problemas relacionados con el flujo, como trampas de aire, llenado inadecuado o cizallamiento excesivo del material.
Optimizar la ubicación y el tamaño de las compuertas: Las herramientas de simulación ayudan a determinar las ubicaciones y tamaños óptimos de las compuertas para los puntos de inyección. Esto garantiza un flujo de material adecuado, minimiza los defectos relacionados con el flujo y mejora la calidad de las piezas.
Predecir la contracción y el alabeo de las piezas: El AEF puede predecir la contracción y el alabeo de la pieza, lo que permite realizar ajustes en el diseño para minimizar estos problemas. Garantiza la precisión dimensional y reduce la probabilidad de distorsiones tras el moldeo.
C. Consideraciones para socavados, líneas de separación y superficies de separación
A la hora de optimizar el diseño de moldes para productos de caucho de silicona, es esencial tener en cuenta las consideraciones relacionadas con los rebajes, las líneas de partición y las superficies de partición. Estos factores incluyen:
- Socavaduras: Las socavaduras son características o hendiduras en la geometría del producto que dificultan la extracción de la pieza. Pueden emplearse técnicas innovadoras de diseño de moldes, como los núcleos plegables o las correderas mecánicas, para dar cabida a las socavaduras y permitir un desmoldeo satisfactorio.
- Líneas de separación: Las líneas de separación son las zonas en las que se unen las mitades del molde, dando lugar a una línea visible en el producto acabado. Debe prestarse especial atención a la colocación de las líneas de separación para minimizar su impacto en el aspecto estético y la funcionalidad del producto.
- Superficies de separación: Las superficies de separación se refieren a las superficies del molde que separan las mitades del molde. Garantizar que las superficies de separación sean lisas y precisas ayuda a lograr una alineación adecuada y evita la formación de rebabas durante el proceso de moldeo de silicona.
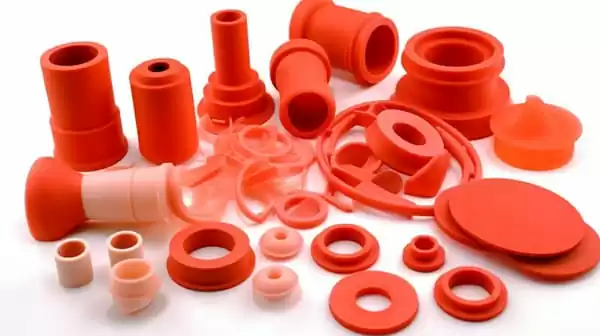
D. Optimización de la temperatura del molde, la presión de inyección y la presión de la cavidad para obtener una calidad constante
Optimizar la temperatura del molde, la presión de inyección y la presión de la cavidad es crucial para conseguir una calidad constante en los productos de caucho de silicona. Las consideraciones clave incluyen:
- Temperatura del molde: El control adecuado de la temperatura del molde influye en el flujo del material, el tiempo de curado y la estabilidad dimensional. Optimizar la temperatura del molde garantiza una calidad constante de las piezas y minimiza las variaciones en las propiedades mecánicas.
- Presión de inyección: La presión de inyección afecta al flujo de material, al comportamiento de llenado y a la reproducción de las características del molde. La optimización de la presión de inyección permite el llenado completo de la cavidad del molde sin una tensión excesiva en el molde o la pieza.
- Presión de la cavidad: La supervisión de la presión de la cavidad durante el proceso de moldeo ayuda a garantizar la calidad constante de las piezas y la precisión dimensional. Permite ajustar en tiempo real los parámetros de inyección, optimizando el proceso de producción.
Mediante la aplicación de estas técnicas avanzadas en la optimización del diseño de moldes, los fabricantes pueden mejorar la funcionalidad, la calidad y la eficacia de los productos de caucho de silicona. Inserto
V. Ventajas del moldeo de LSR para productos de caucho de silicona
A. Ventajas de los materiales LSR, incluida una amplia gama de propiedades mecánicas
El moldeo de LSR ofrece varias ventajas para los productos de caucho de silicona, principalmente debido a las propiedades únicas de los materiales de caucho de silicona líquida. Estas ventajas incluyen:
- Amplia gama de propiedades mecánicas: Los materiales LSR pueden formularse para que presenten una amplia gama de propiedades mecánicas, incluidos distintos niveles de dureza, flexibilidad y elasticidad. Esto permite a los fabricantes adaptar el material para satisfacer los requisitos específicos de productos de diferentes sectores.
- Resistencia al calor y durabilidad: Los materiales LSR ofrecen una excelente resistencia al calor y durabilidad, lo que los hace adecuados para aplicaciones que implican la exposición a altas temperaturas, entornos duros o un uso frecuente. Pueden soportar temperaturas extremas sin comprometer su integridad.
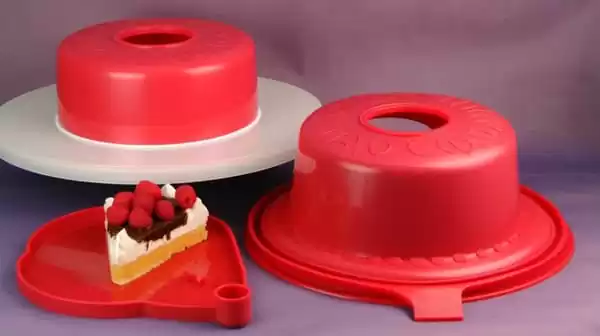
B. Aspecto estético mejorado y superficies más lisas en comparación con el moldeo convencional
El moldeo con LSR proporciona un aspecto estético superior y superficies más lisas en comparación con los métodos de moldeo convencionales. Esto se atribuye a las características únicas del caucho de silicona líquida, como su baja viscosidad y sus propiedades autonivelantes. Las ventajas incluyen:
- Eliminación de defectos superficiales: Los materiales LSR fluyen fácilmente en la cavidad del molde, garantizando una distribución uniforme y minimizando la aparición de defectos superficiales como marcas de hundimiento, líneas de flujo o imperfecciones de la superficie.
- Mejora de la estética de las piezas: El moldeo con LSR permite reproducir detalles intrincados y características finas con gran precisión, lo que da como resultado productos visualmente atractivos. Las superficies lisas que se consiguen con el moldeo de LSR contribuyen a la excelencia estética general de las piezas de caucho de silicona.
C. Capacidad de producción en serie e idoneidad para diversas industrias
El moldeo de LSR es muy adecuado para fabricación de productos de caucho de silicona. Las ventajas incluyen:
- Tiempos de ciclo más cortos: Los materiales de LSR se curan rápidamente, lo que permite tiempos de ciclo de moldeo más cortos en comparación con otros procesos de moldeo de caucho. Esto se traduce en una mayor eficiencia de producción y un mayor rendimiento.
- Consistencia y repetibilidad: El moldeo de LSR permite una producción consistente y repetible de productos de caucho de silicona, garantizando la uniformidad en las dimensiones, propiedades y calidad de las piezas. Esto es crucial para las industrias que requieren una producción de gran volumen con variaciones mínimas.
- Amplia aplicabilidad: El moldeo de LSR es aplicable en diversos sectores, como la automoción, la electrónica, la sanidad y los bienes de consumo. Se adapta a diversos requisitos de producto, desde componentes médicos hasta sellos industriales, juntas y electrónica de consumo.
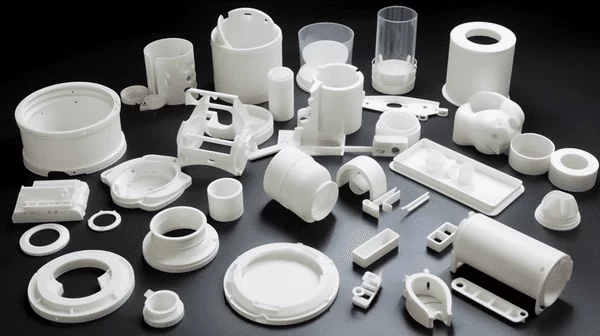
D. Impacto del grosor adecuado de la pared en la integridad de la pieza y en los defectos estéticos
La optimización del espesor de pared en el moldeo de LSR tiene un impacto significativo en la integridad de la pieza y en los defectos cosméticos. Las consideraciones clave incluyen:
- Integridad estructural: Un grosor de pared adecuado garantiza la integridad estructural y la resistencia de los productos de caucho de silicona. Evita problemas como el alabeo, la distorsión o el fallo de la pieza debido a una distribución inadecuada del material o a un curado desigual.
- Defectos cosméticos: El mantenimiento de un espesor de pared adecuado en todo el producto reduce la aparición de defectos cosméticos como variaciones en la superficie, marcas de hundimiento o líneas de flujo visibles. Un grosor de pared uniforme favorece un curado y un flujo de material uniformes, lo que se traduce en piezas visualmente atractivas.
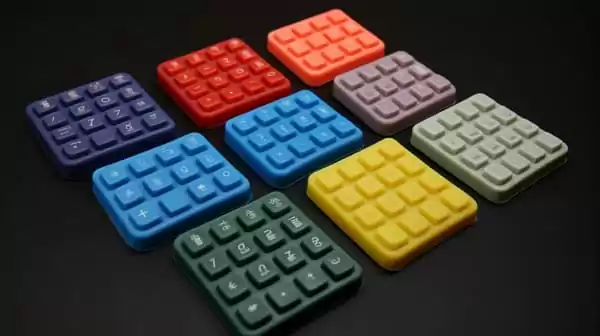
Al aprovechar las ventajas del moldeo de LSR, los fabricantes pueden fabricar productos de caucho de silicona con unas propiedades mecánicas excepcionales, un aspecto estético mejorado y capacidad de producción en serie. La capacidad de conseguir un grosor de pared adecuado garantiza la integridad de la pieza y minimiza los defectos estéticos, lo que contribuye al éxito general y a la competitividad de los productos de caucho de silicona en el mercado.
Conclusión
En conclusión, optimizar el proceso y el diseño del moldeo por inyección de LSR es crucial para conseguir productos de caucho de silicona de alta calidad. Mediante la aplicación de estrategias y consideraciones clave, los fabricantes pueden maximizar el potencial del proceso de moldeo de caucho de silicona líquida (LSR) y ofrecer productos precisos, duraderos y visualmente atractivos.
A lo largo del artículo, hemos hablado de la importancia de comprender los requisitos del producto, diseñar para que sea moldeable, tener en cuenta el grosor de las paredes, incorporar técnicas de ventilación y desgasificación y optimizar los sistemas de refrigeración. Estos factores, entre otros, desempeñan un papel fundamental a la hora de lograr un diseño de molde óptimo para la fabricación de productos de caucho de silicona.
Un diseño meticuloso del molde es esencial para garantizar una calidad constante de las piezas, minimizar los defectos y aumentar la productividad. Si se tienen en cuenta los rebajes, las líneas de apertura y las superficies de apertura, los fabricantes pueden optimizar el diseño del molde y minimizar los defectos estéticos.
Las ventajas del moldeo de LSR, incluida la amplia gama de propiedades mecánicas que ofrecen los materiales de LSR, la mejora del aspecto estético y la idoneidad para la producción en masa, subrayan aún más la importancia de optimizar el diseño del molde. El moldeo de LSR permite fabricar productos de caucho de silicona con un rendimiento, una durabilidad y un atractivo estético excepcionales.
En resumen, prestando especial atención a la optimización del diseño del molde, los fabricantes pueden liberar todo el potencial del proceso de moldeo de LSR. El resultado son productos de caucho de silicona de alta calidad que satisfacen las expectativas de los clientes, cumplen las normas del sector y obtienen una ventaja competitiva en el mercado. Con un diseño meticuloso del molde, los fabricantes pueden garantizar productos de caucho de silicona precisos, duraderos y visualmente atractivos que satisfagan una amplia gama de aplicaciones en diversos sectores.