1. Características del material de silicona
A. Las materias primas de silicona son generalmente gelatinosas, algo similares a la plastilina, incoloras, translúcidas e inodoras.
B. Sus principales características son la resistencia a altas temperaturas (hasta 300°C) y a bajas temperaturas (mínimo -100°C), que es el mejor caucho resistente al frío y a altas temperaturas en la actualidad; al mismo tiempo, tiene un excelente aislamiento eléctrico y una gran estabilidad a la oxidación térmica y al ozono, químicamente inerte.
La desventaja es que la resistencia mecánica es baja, la resistencia al aceite, a los disolventes y a los ácidos y álcalis es escasa, es difícil de vulcanizar y el precio es más caro. Temperatura de funcionamiento: -60℃~+200℃. Lo anterior es la descripción de caucho de silicona en el manual.
C. Temperatura de uso: Como se mencionó anteriormente, generalmente se ajusta de -40°C a 200°C, y puede alcanzar 230°C en poco tiempo.
D. Problema de envejecimiento: la resistencia al aceite, al ácido y al álcali es escasa, y tiene poco que ver con el estrés.
E. Problema de adherencia: Antes del tratamiento de la superficie, además de utilizar productos de silicona como adhesivos para unir piezas de silicona, la adhesión a otras piezas debe activarse en la superficie, y la superficie del pegamento puede curarse por vulcanización.
Todas las sustancias que pueden reaccionar con el caucho o hacer que reticule se denominan colectivamente agentes vulcanizantes, también conocidos como agentes de reticulación. Existen muchos tipos de agentes vulcanizantes, y siguen aumentando.
Los agentes vulcanizantes que se han utilizado incluyen azufre, selenio, telurio, compuestos que contienen azufre, óxidos metálicos, peróxidos, resinas, quinonas y aminas.
F. Dureza del material: Según la dureza Shore, las piezas de plástico pueden seleccionarse teóricamente entre 10 grados y 80 grados en el mercado nacional.
Los que se pueden encontrar fácilmente suelen ser de 20 a 70 grados, y los más utilizados son de 40 a 50 grados.
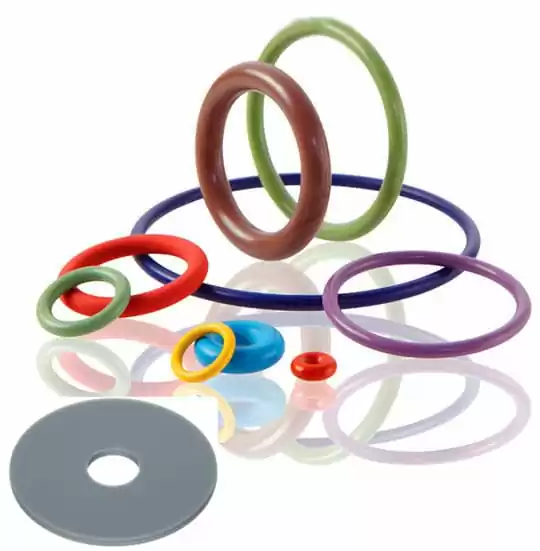
2. El proceso de producción de los productos de silicona
A: Forma y color de las materias primas
B: Tras la igualación de colores y el amasado, los copos de diversos colores se transforman en gel de sílice blanco lechoso.
C: Tras amasar y dar forma, las materias primas se prensan en tiras y se cortan en tiras
D: Moldeo por vulcanización
E: Recorte, eliminación de bordes, inspección, envasado
F: Terminado productos de silicona
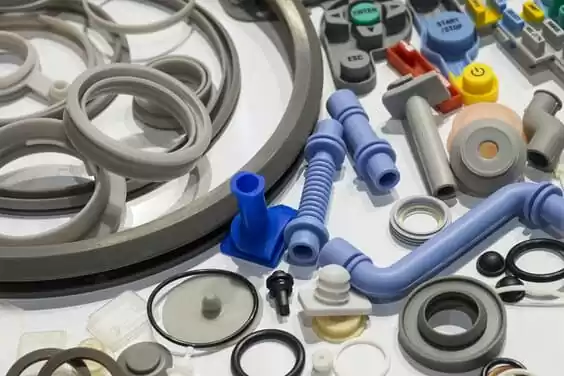
3. Tamaño y características del producto
A. Tamaño límite: La parte más gruesa puede ser de 15~20MM, si es una esfera, el diámetro puede ser de 30MM. Generalmente, el grosor recomendado no supera los 3MM.
Cuando es mayor de 3MM, llevará más tiempo de vulcanización y aumentará el coste. La parte más fina puede alcanzar teóricamente los 0,2MM, pero en el diseño se suelen tomar los 0,3MM más finos, y se recomiendan los 0,4MM.
B. Tamaño relativo: En términos de diferencia de grosor, se recomienda que la parte más fina y la más gruesa no superen 3 veces. Estos problemas dependen principalmente de los requisitos de temperatura y presión cuando se vulcaniza el material.
C. Índice de contracción: El índice de contracción del material de silicona está relacionada con la dureza del material. La mayoría de los materiales secundarios proporcionados por el fabricante se sitúan entre 1,022 y 1,042.
Para materiales con un grado de 40 a 50 grados, el índice de contracción suele ser de 1,03. En comparación con el plástico, los productos de silicona no sufren defectos superficiales aparentes similares debidos a la contracción.
D. Precisión dimensional: Debido a que la mayoría de los productos de caucho de silicona son un molde con múltiples cavidades, el número de cavidades es muy grande en comparación con los productos de plástico. Por lo tanto, no es tan conveniente como los productos de plástico en el control de tamaño.
La precisión general es de más o menos 0,1, y la del producto de alta precisión es de más o menos 0,05. Cuando se utiliza para hacer coincidir el orificio de la pieza de plástico y el botón, la holgura mínima es de 0,1 por lado, y el valor recomendado es de 0,2 por lado.
E. Diseño de la forma: Para las piezas de manguitos de caucho, por lo general es suficiente proporcionar el dibujo original a la fábrica de moldes de acuerdo con el dibujo de la forma del producto, y explicar el problema de coincidencia, que es decidido por la fábrica de moldes.
En circunstancias normales, dependiendo del tamaño del producto, la coordinación entre el manguito de goma y el producto suele tener una desviación negativa de 0,2~0,5 pequeña por un lado.
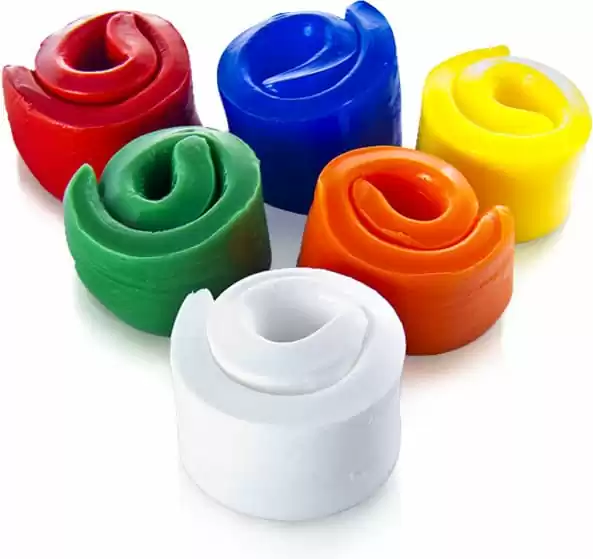
4. Estructura del molde
A. Límite superior del espesor del molde:
Tentativamente 250mm, el tamaño puede llegar a 500X500, y el producto puede ser de hasta 400X400 en el área del molde. La estructura del molde se divide generalmente en el molde superior, el molde inferior, la placa inferior, la placa superior, el pasador eyector, el núcleo del molde, la bisagra y otras partes auxiliares. Al diseñar productos de silicona, debe prestarse atención a las características de sus moldes y procesos de producción:
B. Desmoldeo:
El desmoldeo de los productos de silicona puede ser directo y forzado. Para productos sin defectos de diseño, el requisito de tamaño para el desmoldeo forzado radica principalmente en la relación entre la circunferencia de la parte más grande del núcleo del molde y la parte de cierre más pequeña durante el desmoldeo. Para productos por debajo de 55°, puede hacerse 2-3 veces. Es posible que se produzcan roturas y esquinas afiladas en la abertura.
Dado que durante la vulcanización se requiere una temperatura de 180 grados centígrados, el trabajo de desmoldeo es casi todo manual, excepto la separación superior e inferior del propio molde. Por lo tanto, la comodidad y rapidez del desmoldeo deben tenerse en cuenta en el diseño de las piezas.
Para no afectar a la calidad de vulcanización y a la eficiencia de producción en masa de las piezas debido al largo tiempo de desmoldeo. Debido a que el método de desmoldeo de la silicona es principalmente manual, y la carrera de acción de la placa superior también es pequeña, el molde de silicona no tiene la parte superior inclinada en comparación con el molde de molde de plástico. Por lo general, no se proporciona ningún tirón del núcleo.
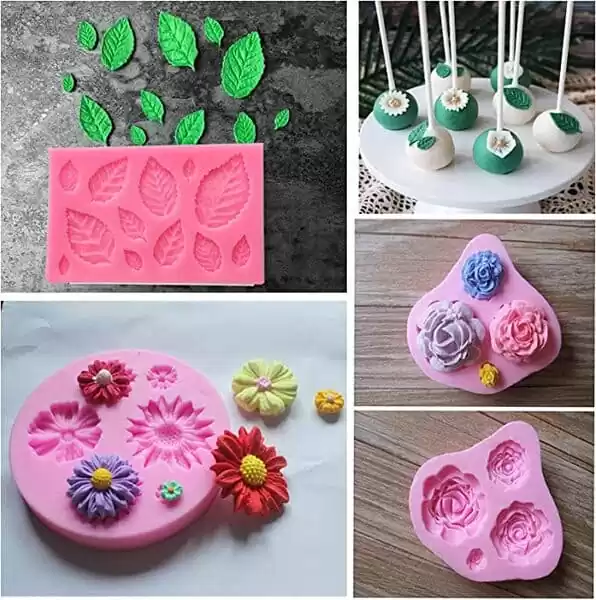
C. Fijación del núcleo:
A diferencia de los moldes de plástico, los núcleos de los moldes de silicona suelen retirarse junto con las piezas del producto cuando el molde de inyección se abre y se extraen las piezas. Por lo tanto, la fijación y el posicionamiento preciso del núcleo del molde son más difíciles de manejar que el molde de plástico, y la rigidez del núcleo del molde es mayor.
Por lo general, los machos se fabrican juntos y todos los machos se fijan a la vez. O bien se pasa el núcleo del molde por herramientas auxiliares para poder colocarlo rápidamente. Como hay mucha presión en el proceso de fijación del molde, es necesario evitar estrictamente que el núcleo del molde se mueva.
D. Tirón del núcleo:
Por lo general, no se puede desplazar automáticamente, pero se puede forzar su retirada, y la extracción del núcleo sólo se utiliza para estructuras de pequeño tamaño. La configuración de la extracción de testigos es similar a la del molde de plásticopero se retira manualmente cuando se abre el molde.
Además, la extracción del núcleo ocupa un gran espacio en el molde, lo que no sólo es complicado de procesar en el exceso de molde de silicona en un molde, pero también tiene una baja utilización del espacio del molde. Así que no tire del núcleo tanto como sea posible.
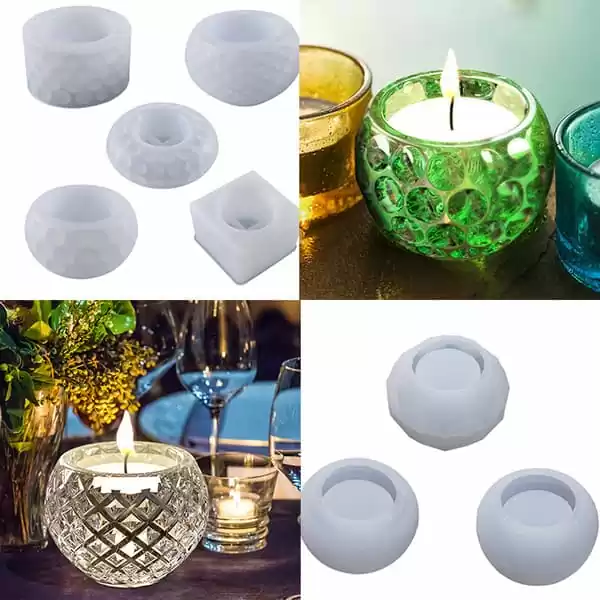
E. Forma:
Los productos de silicona tienen una gran tenacidad cuando la superficie está intacta, pero una vez que hay grietas, éstas se expanden rápidamente bajo la acción de una fuerza externa. Dicho esto, productos de silicona son muy sensibles a las grietas.
Teniendo en cuenta estos problemas, debe prestarse atención al correcto diseño del molde de las piezas de silicona: no debe haber esquinas afiladas en todas las posiciones, para evitar la concentración de tensiones y las grietas. El ángulo R en la abertura no debe ser inferior a 0,5.
F. Borde autorretráctil:
La función principal del borde auto extraíble: es acomodar el exceso de goma; facilitar el escape del molde; fácil de recortar el destello.
El borde de auto-desmontaje se compone generalmente de un borde delgado en la superficie de separación de la pieza y un correspondiente borde de desgarro relativamente fuerte. El grosor del borde fino es generalmente de 0,1~0,2, el grosor del borde de desgarro es generalmente de 0,8, y la anchura es generalmente de 1~2MM.
G. Insertar:
Se pueden colocar varios tipos de insertos en los productos de silicona, pero hay que prestar atención a varias cuestiones En primer lugar, la superficie de las piezas incrustadas debe recibir un tratamiento previo, principalmente vulcanización superficial o activación superficial.
De lo contrario, será difícil unir firmemente el inserto y la cola. La segunda es la posición fija del inserto, que puede fijarse en una dirección en sentido vertical, pero debe fijarse completamente en otras direcciones. Para evitar el movimiento del inserto durante el proceso de moldeado completo.
El tercero es el grosor de la cola alrededor del inserto. Para piezas totalmente encapsuladas (en las que todas las superficies están encapsuladas, por lo que el inserto no puede posicionarse), debe utilizarse un grosor mínimo de 0,5 mm alrededor del inserto. Para insertos con posicionamiento, el grosor de la capa adhesiva periférica debe ser superior a 0,4MM.
H. Otros procesos auxiliares:
Proceso de inyección de cola (encolado):
Similar a la moldeo por inyección En el proceso de inyección, primero se fijan las piezas que se van a inyectar y se cierra la primera capa del molde para controlar que las materias primas no contaminen durante la inyección las piezas que no están diseñadas para la inyección. A continuación, se cierra la segunda capa del molde y se presiona el compuesto de caucho para darle forma.
Proceso de laminación: primera mano-preformar la goma
Moldeado: Este proceso de fabricación puede utilizarse en caso de encapsulación total.
Inmersión: La materia prima del cuerpo de caucho (goma) es fluida, y la pieza se sumerge en la materia prima muchas veces. La capa interior de materia prima se vulcaniza y se vuelve a sumergir hasta alcanzar el grosor deseado.
Epoxi: La materia prima tiene buena fluidez, similar a la pintura, y se vulcaniza a temperatura ambiente. El moldeado es una operación relativamente sencilla, generalmente manual, y el siguiente revestimiento se aplica cuando la primera capa se cura rápidamente.
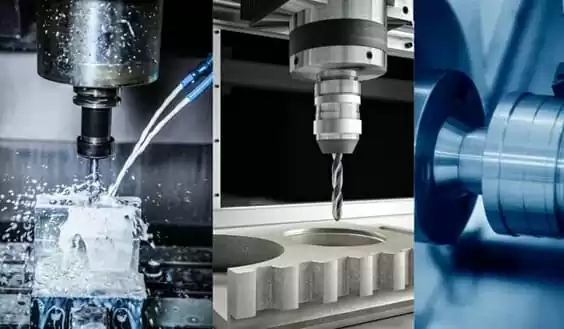
L. Productos multicolor:
A se divide en 2 conjuntos de moldes de vulcanización, y B es de color a mano, una vez vulcanizado, la parte de separación de color de las partes es necesario tener una cierta altura, para evitar la combinación de mezcla de colores adhesivo conductor, la vulcanización secundaria de silicona y silicona (caucho) puede vulcanizarse directamente sin tratamiento Bonding 5. Medición de la dureza y herramientas.
El instrumento más utilizado para medir la dureza del caucho se llama durómetro Shore (también conocido como Shore). Utiliza un muelle para presionar un penetrador metálico en la superficie del material y medir la profundidad a la que penetra.
El instrumento mide profundidades de penetración de cero a 0,100 pulgadas. Una lectura de cero en la escala significa que el penetrador ha penetrado la profundidad límite, mientras que una lectura de 100 significa que la profundidad de penetración es cero. Existen varios durómetros Shore con diferentes rangos de dureza y grados de automatización.
Una de las escalas más utilizadas es la escala Shore A. Los durómetros Shore A tienen un penetrador romo y un muelle mediano. Cuando las lecturas son superiores a 90, el durómetro Shore A se vuelve impreciso. Para materiales más duros, se utiliza un durómetro Shore D. Tiene un penetrador afilado y un muelle fuerte. Tiene un penetrador afilado y un muelle fuerte para una penetración profunda.
Para medir plásticos más duros, utilice un durómetro con un penetrador más afilado y resistente, como un durómetro Rockwell. En el extremo opuesto, los durómetros Shore 00 se utilizan para medir geles blandos y cauchos espumados.

La mayoría de los materiales múltiples pueden soportar la tensión inicial, pero con el tiempo cederán debido a la fluencia y la relajación. Las lecturas del durómetro pueden tomarse instantáneamente o tras un cierto tiempo de retardo, normalmente de 5 a 10 segundos. Las lecturas inmediatas siempre mostrarán lecturas más altas (o más duras) que las lecturas retardadas.
Las lecturas de retardo son más representativas no sólo de la dureza del material, sino también de su elasticidad. Un material más débil y menos elástico es más propenso a la fluencia que los que son más resistentes y elásticos.
Para garantizar la validez de los datos, se requieren procedimientos de prueba precisos. Para obtener una lectura precisa, hay que disponer de una pieza de ensayo lo suficientemente plana y gruesa para que el penetrador no se vea afectado por la superficie de apoyo.
Normalmente, el grosor requerido es de 0,200 pulgadas, pero los materiales rígidos con menos deformación pueden someterse a ensayo con precisión cuando el grosor es menor.