Introducción:
El moldeo por compresión de caucho de silicona es un proceso de fabricación muy utilizado que consiste en moldear y curar caucho de silicona líquido en una cavidad de molde. Este método versátil es conocido por su capacidad para fabricar productos duraderos y resistentes al calor. Sin embargo, cuando se trata de la producción de grandes volúmenes, pueden surgir ciertos retos que requieren una cuidadosa consideración y soluciones estratégicas.
La producción de grandes volúmenes plantea retos únicos en el moldeo por compresión de caucho de silicona. La escala y la velocidad de la producción pueden afectar a factores como la consistencia del llenado del molde, la eficacia del tiempo de ciclo y la aparición de defectos como el centelleo. Si no se abordan adecuadamente, estos retos pueden obstaculizar la productividad, afectar a la calidad del producto y aumentar los costes de fabricación.
Afrontar estos retos es de suma importancia para el éxito de la fabricación. Mediante la comprensión y la aplicación de estrategias eficaces, los fabricantes pueden optimizar el proceso de moldeo por compresión, minimizar los problemas de producción y lograr una calidad constante en la producción de grandes volúmenes. Esto garantiza que los productos satisfagan las demandas del mercado, cumplan las estrictas especificaciones y ofrezcan un rendimiento fiable.
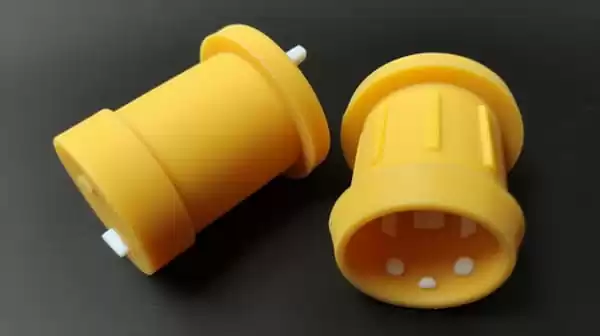
En las siguientes secciones, profundizaremos en los retos específicos a los que se enfrenta la moldeo por compresión de caucho de silicona de gran volumen y explorar ideas valiosas sobre cómo superarlos eficazmente. Al abordar estos retos de frente, los fabricantes pueden liberar todo el potencial de la producción de grandes volúmenes y ofrecer productos excepcionales de caucho de silicona a diversas industrias.
Problemas con el moldeo por compresión:
El moldeo por compresión, aunque es un proceso de fabricación muy utilizado, no está exento de dificultades. Los fabricantes se encuentran a menudo con varios problemas comunes que pueden afectar a la eficacia de la producción y a la calidad del producto. Estos son algunos de los principales problemas asociados al moldeo por compresión:
1.Llenado inconsistente del molde:
Conseguir un llenado uniforme del molde es esencial para obtener productos moldeados uniformemente. En la producción de grandes volúmenes, pueden producirse variaciones en el flujo y la distribución del material, lo que provoca un llenado irregular de las cavidades del molde. Esto puede provocar variaciones en las dimensiones de las piezas, defectos en la superficie y comprometer la calidad del producto.
2. Ciclos más largos:
En comparación con otras técnicas de moldeo, como el proceso de moldeo por inyección, el moldeo por compresión suele tener ciclos más largos. El proceso implica la compresión y el curado del caucho de silicona dentro del molde, lo que puede llevar más tiempo. En la producción de grandes volúmenesLos tiempos de ciclo más largos pueden limitar el rendimiento global y ralentizar el proceso de fabricación.
3.Formación Flash:
La rebaba se refiere al exceso de material que escapa de la cavidad del molde durante el moldeo por compresión. Se produce debido a factores como un diseño inadecuado del molde, una cantidad excesiva de material o una fuerza de cierre insuficiente. La formación de rebabas no sólo supone un desperdicio de material, sino que también requiere un procesamiento posterior adicional para eliminar o recortar el material sobrante. El resultado es un aumento de los costes de producción y posibles problemas de calidad.
Estos problemas pueden afectar significativamente a la eficacia de la producción y a la calidad del producto en el moldeo por compresión de grandes volúmenes. Un llenado inconsistente del molde puede dar lugar a piezas con dimensiones variables y defectos superficiales, lo que provoca productos rechazados y un aumento de los residuos. Los tiempos de ciclo más largos reducen el rendimiento global de la producción, lo que afecta a la capacidad de satisfacer las demandas del mercado. La formación de rebabas no sólo aumenta el desperdicio de material, sino que también requiere tiempo y recursos adicionales para el procesamiento posterior, lo que afecta a la productividad global y a la rentabilidad del proceso de fabricación.
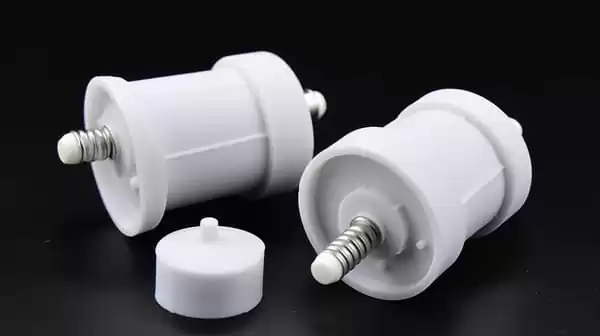
Resolver estos problemas es crucial para garantizar una producción eficiente y de alta calidad. En las siguientes secciones, exploraremos estrategias eficaces para superar estos retos en compresión de caucho de silicona de gran volumen y aplicaciones de moldeo por inyección. Mediante la aplicación de estas estrategias, los fabricantes pueden optimizar el proceso, mejorar la productividad y ofrecer productos superiores para satisfacer las demandas del mercado.
Principales desventajas del moldeo por compresión:
La principal desventaja del moldeo por compresión, especialmente en escenarios de producción de gran volumen, es su menor velocidad de producción en comparación con otras técnicas de moldeo. A diferencia de procesos más rápidos como el moldeo por inyección, el moldeo por compresión implica pasos adicionales como la preparación del material, la carga manual o automatizada del molde, y la compresión y el curado del caucho de silicona. Estos pasos contribuyen a alargar la duración de los ciclos, lo que puede limitar el rendimiento global de la producción y afectar a la eficacia de la fabricación de grandes volúmenes.
Las implicaciones de una menor velocidad de producción en el moldeo por compresión de grandes volúmenes son significativas. En primer lugar, puede obstaculizar la capacidad de cumplir plazos de producción ajustados y seguir el ritmo de las demandas del mercado. Los tiempos de ciclo más largos asociados al moldeo por compresión pueden no coincidir con los ritmos de producción deseados, necesarios para satisfacer grandes pedidos en un plazo breve. Esto puede provocar retrasos en la entrega del producto y afectar potencialmente a la satisfacción del cliente.
Además, una menor velocidad de producción puede tener implicaciones financieras. La producción de grandes volúmenes suele tener como objetivo conseguir economías de escala, en las que mayores cantidades de producción ayudan a reducir los costes por unidad. Sin embargo, la menor velocidad del moldeo por compresión puede reducir la producción total, lo que se traduce en mayores costes de producción por unidad. Esto puede afectar a la rentabilidad y la competitividad en el mercado.
Además, la menor velocidad de producción puede afectar a la capacidad de adaptarse rápidamente a los cambios del mercado o introducir nuevos diseños de productos. En las industrias de ritmo rápido, es crucial poder responder con rapidez a las demandas del mercado o a las modificaciones de diseño. La naturaleza lenta del moldeo por compresión puede restringir la agilidad y la flexibilidad en la fabricación.
A pesar de esta desventaja, el moldeo por compresión ofrece ventajas en términos de versatilidad, opciones de materiales y capacidad para manejar geometrías de pieza complejas. A menudo se prefiere para aplicaciones específicas que requieren propiedades únicas o diseños intrincados. Mediante la aplicación de estrategias para optimizar el proceso y minimizar los tiempos de ciclo, los fabricantes pueden mitigar el impacto de la menor velocidad de producción y maximizar los beneficios del moldeo por compresión en escenarios de producción de gran volumen.
Factores que afectan al proceso de moldeo por compresión:
Varios factores clave influyen en el proceso de moldeo por compresión, desempeñando un papel fundamental en el llenado del molde, la compresión, el desmoldeo y la calidad general del producto. Comprender y gestionar eficazmente estos factores es esencial para lograr resultados uniformes y de alta calidad. Exploremos los factores clave:
1.Diseño del molde:
El diseño del molde desempeña un papel fundamental en el moldeo por compresión. Factores como las cavidades del molde, los sistemas de canales y las líneas de separación influyen en el flujo de material, el llenado del molde y la compresión de las piezas. Los moldes bien diseñados facilitan la distribución uniforme del material, lo que garantiza unas dimensiones uniformes de las piezas y reduce la aparición de defectos.
2.Temperatura del molde:
El control de la temperatura del molde es crucial en el moldeo por compresión. La temperatura del molde afecta al flujo de material, al proceso de vulcanización y a las propiedades de la pieza. Una gestión adecuada de la temperatura del molde garantiza un flujo óptimo del material en las cavidades del molde, favorece un curado uniforme y mejora las propiedades mecánicas del producto final.
3.Fuerza de sujeción:
Una fuerza de apriete adecuada es esencial para conseguir una compresión y consolidación de la pieza correctas. Una fuerza de cierre insuficiente puede provocar un llenado incompleto y una mala calidad de la pieza, mientras que una fuerza excesiva puede causar la formación de rebabas. Un control cuidadoso de la fuerza de cierre garantiza una compresión uniforme en todas las cavidades del molde, lo que se traduce en unas dimensiones y un acabado superficial de la pieza uniformes.
4.Propiedades del material:
Las propiedades del material de caucho de silicona utilizado en el moldeo por compresión influyen enormemente en el proceso y en la calidad del producto. La viscosidad, el tiempo de curado, el caucho de alta consistencia y las propiedades mecánicas del material afectan al llenado del molde, al flujo y al rendimiento final de la pieza. Seleccionar el material correcto con las propiedades adecuadas para la aplicación es crucial para conseguir los resultados deseados.
5. Agentes desmoldeantes:
Los agentes desmoldeantes se utilizan para facilitar el desmoldeo de las piezas curadas del molde. La correcta aplicación de los agentes desmoldeantes minimiza la adherencia y garantiza una extracción suave de las piezas, reduciendo el riesgo de daños o defectos durante el desmoldeo.
6.Diseño del casquillo del bebedero:
El diseño del casquillo del bebedero, que conecta el molde a la unidad de inyección, puede afectar al flujo de material y al llenado de las cavidades del molde. Un diseño eficiente del casquillo del bebedero ayuda a controlar los caudales, evitar el atrapamiento de aire y garantizar una distribución uniforme del material dentro del molde.
Estos factores afectan colectivamente al llenado del molde, la compresión, el desmoldeo y la calidad general del producto en el moldeo por compresión. Un diseño óptimo del molde, un control adecuado de la temperatura del molde, una gestión precisa de la fuerza de cierre, una selección adecuada del material, un uso eficaz de los agentes de desmoldeo y un diseño cuidadoso del casquillo del bebedero contribuyen a que las dimensiones de las piezas sean uniformes, a reducir los defectos y a mejorar la calidad del producto final.
Mediante la comprensión y optimización de estos factores, los fabricantes pueden mejorar la eficacia del proceso, conseguir las propiedades deseadas de las piezas y garantizar el éxito de la producción. fabricación de productos de caucho de silicona de alta calidad mediante moldeo por compresión.
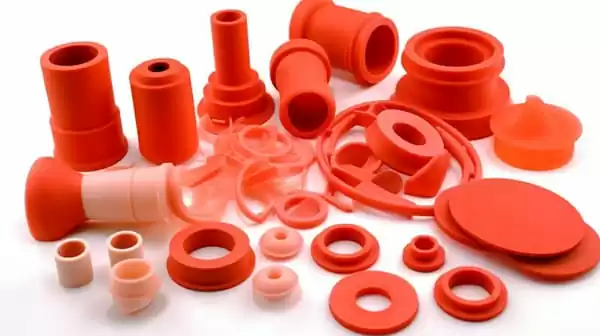
Defectos del moldeo del caucho:
El moldeo de caucho, incluido el proceso de moldeo por compresión de caucho, puede ser susceptible de varios defectos que pueden afectar a la funcionalidad y el aspecto del producto final. Abordar y minimizar estos defectos es crucial para lograr resultados de alta calidad. Exploremos algunos defectos comunes asociados con el moldeo de caucho:
1.Flash:
La rebaba es el exceso de material que se escapa de la cavidad del molde durante el proceso de moldeo. Suele producirse en las líneas de separación o en zonas del molde con huecos o desalineación. Las rebabas pueden comprometer la precisión dimensional del producto y provocar un exceso de material o salientes no deseados en la pieza final. Puede requerir un postprocesado adicional, como recortes u operaciones secundarias, para eliminar la rebaba, lo que aumenta el tiempo y los costes de producción.
2. Atrapamiento aéreo:
El atrapamiento de aire se produce cuando el aire o el gas quedan atrapados dentro de la pieza moldeada durante el proceso de moldeo. Puede deberse a una ventilación inadecuada, a un diseño inadecuado del molde o a un llenado insuficiente del molde. El atrapamiento de aire puede provocar un llenado incompleto, debilidades estructurales y la formación de huecos dentro de la pieza. Estos huecos pueden afectar a las propiedades mecánicas, como la resistencia o la durabilidad, del producto final, comprometiendo su funcionalidad.
3.Imperfecciones superficiales:
Las imperfecciones superficiales pueden manifestarse como arañazos, manchas, asperezas u otras incoherencias en la superficie del producto moldeado. Estas imperfecciones pueden deberse a factores como defectos en la superficie del molde, flujo deficiente del material o control inadecuado de la temperatura del molde. Las imperfecciones de la superficie no sólo afectan al aspecto estético del producto, sino que también pueden afectar a su funcionalidad, sobre todo en aplicaciones en las que una superficie lisa es fundamental, como las superficies de sellado o de contacto.
4.Inconsistencias dimensionales:
Las incoherencias dimensionales se refieren a variaciones en el tamaño, la forma o el grosor de la pieza moldeada. Estas variaciones pueden deberse a problemas tales como diseño de moldesLas inconsistencias dimensionales pueden afectar al ajuste, el ensamblaje o el rendimiento del producto final, dificultando el logro de tolerancias precisas o el cumplimiento de requisitos funcionales específicos. Las incoherencias dimensionales pueden afectar al ajuste, ensamblaje o rendimiento del producto final, dificultando la consecución de tolerancias precisas o el cumplimiento de requisitos funcionales específicos.
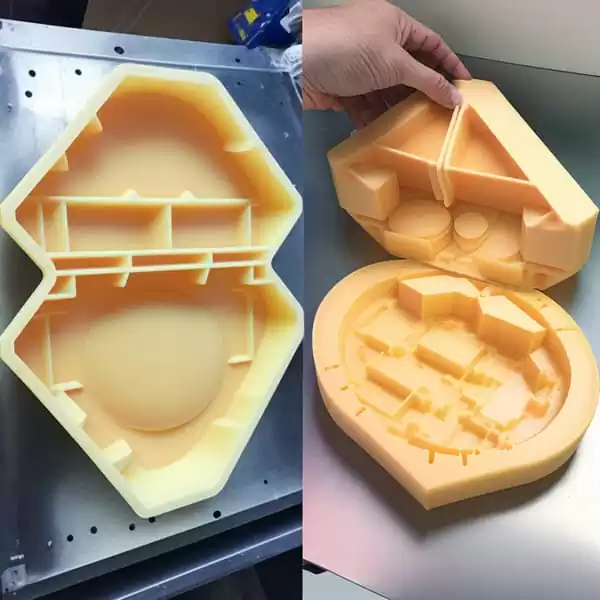
Estos defectos pueden tener importantes repercusiones en la funcionalidad y el aspecto del producto final. El exceso de rebabas puede dar lugar a una estética deficiente, interferir en la funcionalidad del producto o causar dificultades durante el montaje. El aire atrapado y los huecos pueden debilitar la integridad estructural de la pieza, afectando a su resistencia o durabilidad. Las imperfecciones superficiales no sólo comprometen el atractivo visual, sino que también pueden afectar a características funcionales como la fricción, la capacidad de sellado o las propiedades de contacto. Las incoherencias dimensionales pueden dificultar el ajuste correcto, interferir con las piezas acopladas o provocar desalineaciones que afecten al rendimiento o la funcionalidad general del producto.
Mediante un diseño eficaz del proceso de moldeo por transferencia, la optimización de los parámetros del proceso y la aplicación de estrictas medidas de control de calidad, los fabricantes pueden minimizar estos defectos en el moldeo de caucho, garantizando productos de alta calidad que cumplan los requisitos funcionales y estéticos deseados.
Estrategias para superar los retos del moldeo por compresión de caucho de silicona en grandes volúmenes:
Superar los retos de moldeo por compresión de caucho de silicona de gran volumen requiere un enfoque sistemático y la aplicación de estrategias eficaces. He aquí algunas estrategias clave para afrontar estos retos:
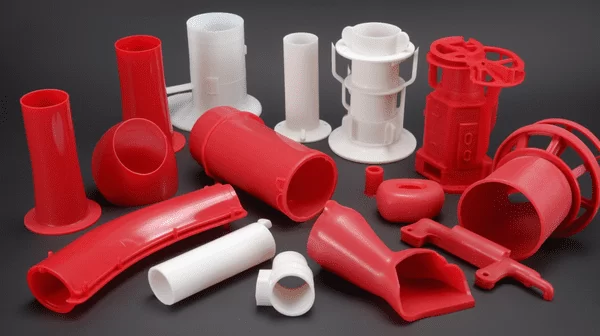
1.Llenado consistente del molde:
Optimizar el diseño del molde para garantizar un diseño adecuado del sistema de canales y compuertas para un flujo uniforme del material.
Utilizar técnicas avanzadas de supervisión de procesos, como la detección de presión y temperatura en tiempo real, para identificar variaciones y realizar los ajustes necesarios.
Realizar análisis de flujo de moldes para optimizar el diseño de moldes y garantizar un llenado uniforme de los moldes.
2.Tiempos de ciclo eficientes:
Utilice software avanzado de diseño de moldes y herramientas de simulación para identificar posibles cuellos de botella y optimizar el diseño del molde para acelerar los tiempos de ciclo.
Seleccione un alto rendimiento compuestos de caucho de silicona formulado específicamente para un curado rápido que reduzca la duración total de los ciclos.
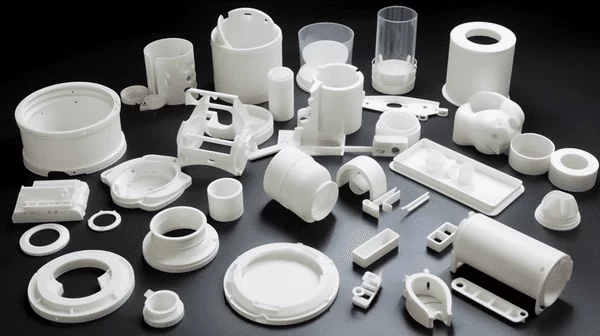
Optimice los parámetros del proceso, como la temperatura, la presión y el tiempo, para minimizar el tiempo de curado y aumentar la eficacia de la producción.
3.Control de flash:
Concéntrese en el diseño adecuado del molde y en el control preciso de la fuerza de cierre para minimizar la formación de rebabas.
Controle la temperatura del molde para garantizar un flujo adecuado del material y evitar un exceso de rebabas.
Aplique estrictas medidas de control de calidad, incluidas inspecciones y controles periódicos, para identificar y tratar con prontitud los defectos relacionados con los destellos.
4. Mantenimiento del molde:
Establezca un programa de mantenimiento preventivo de los moldes para garantizar su longevidad y un rendimiento constante.
Limpie los moldes con regularidad y utilice agentes desmoldeantes adecuados para evitar que se peguen y mejorar el desmoldeo.
Aplique técnicas adecuadas de almacenamiento de moldes para evitar daños y garantizar que los moldes estén listos para una producción eficiente.
5.Calidad del material:
Trabajar en estrecha colaboración con los proveedores de material de confianza para garantizar la coherencia y la calidad de los productos. compuestos de caucho de silicona de alta calidad.
Establecer especificaciones y normas claras para las propiedades de los materiales y realizar pruebas periódicas para verificar su cumplimiento.
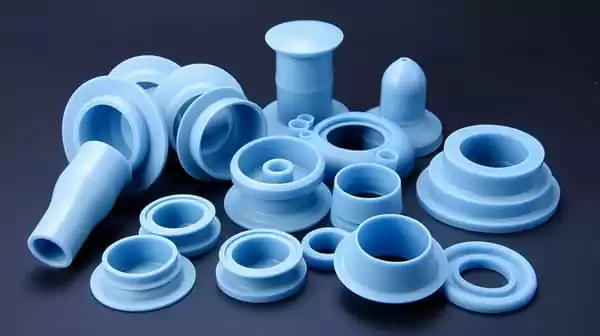
Realizar pruebas rigurosas de los materiales para garantizar la idoneidad del material de caucho para la aplicación prevista y minimizar los defectos.
6.Optimización del diseño de moldes:
Utilizar software avanzado de diseño de moldes y herramientas de simulación para optimizar las cavidades de los moldes, los sistemas de canales y las líneas de separación para lograr una producción eficaz y reducir al mínimo los residuos.
Diseñar moldes con sistemas adecuados de ventilación y compuertas para minimizar el atrapamiento de aire y garantizar un flujo uniforme del material.
Tenga en cuenta factores como la temperatura del molde, el diseño del casquillo del bebedero y los agentes de desmoldeo para favorecer el flujo de material, el desmoldeo y la calidad de la superficie.
7.Control e inspección del proceso:
Aplicar técnicas de supervisión de procesos en tiempo real para identificar variaciones y posibles problemas durante la producción.
Inspeccionar y supervisar periódicamente el proceso de moldeo por compresión para garantizar el cumplimiento de las normas de calidad e identificar cualquier desviación o defecto.
Utilizar métodos de control estadístico de procesos (SPC) para realizar un seguimiento y analizar los datos del proceso, lo que permite realizar ajustes proactivos y mejoras continuas.
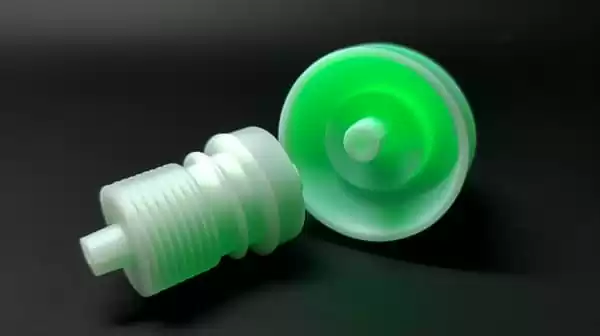
Aplicando estas estrategias, los fabricantes pueden superar los retos de moldeo por compresión de caucho de silicona de gran volumen. El llenado uniforme de los moldes, la duración eficaz de los ciclos, el control de las rebabas, el mantenimiento de los moldes y la calidad de los materiales desempeñan un papel fundamental en el éxito de la producción. Optimizar el diseño del molde, supervisar el proceso y trabajar con proveedores de materiales de confianza contribuye a mejorar la productividad, la calidad del producto y la rentabilidad de la fabricación.
Conclusión:
En conclusión, el moldeo por compresión de caucho de silicona de gran volumen presenta su propio conjunto de desafíos que deben abordarse para una fabricación exitosa. A lo largo de este artículo, hemos explorado estos retos y hemos proporcionado información valiosa sobre cómo superarlos con eficacia.
El llenado uniforme de los moldes, la eficiencia de los tiempos de ciclo, el control de las rebabas, el mantenimiento de los moldes y la calidad de los materiales se han destacado como áreas clave que requieren atención. Planificando y optimizando cuidadosamente estos aspectos, los fabricantes pueden mejorar significativamente la productividad y aumentar la calidad de los productos finales.
Afrontar los retos del moldeo por compresión de caucho de silicona en grandes volúmenes requiere un enfoque sistemático y la aplicación de estrategias eficaces. Esto incluye la optimización del moldeo por inyección de líquidos mediante el diseño, la utilización de técnicas avanzadas de supervisión de procesos, la realización de inspecciones periódicas y la colaboración con proveedores de materiales de confianza.
Al superar estos retos, los fabricantes pueden lograr una mayor productividad, mejorar la calidad de los productos y satisfacer eficazmente las demandas del mercado. Esto puede conducir a una mayor satisfacción del cliente, una mayor rentabilidad y una ventaja competitiva en la industria.
En conclusión, la planificación cuidadosa, la optimización y la aplicación de estas estrategias son cruciales para que los fabricantes tengan éxito en el moldeo por compresión de grandes volúmenes de caucho de silicona. Mediante la mejora y el perfeccionamiento continuos de sus procesos, los fabricantes pueden liberar todo el potencial de este método de fabricación y ofrecer productos de caucho de silicona excepcionales para satisfacer las diversas necesidades del mercado.