Introduction
Le moulage par compression est un processus de fabrication vital qui a un impact profond sur diverses industries. Cet article se penche sur le monde du moulage par compression, en explorant son importance, ses défis et le rôle critique joué par les logiciels de simulation pour surmonter ces obstacles.
Le moulage par compression est une technique de fabrication largement utilisée pour créer des composants complexes à partir d'une multitude de matériaux, y compris les plastiques, les composites et le caoutchouc. Ce processus revêt une importance considérable en raison de sa capacité à produire des pièces de haute qualité. des pièces de haute qualité avec précision, ce qui le rend indispensable dans des secteurs tels que l'automobile, l'aérospatiale et les biens de consommation.
Si le moulage par compression offre de nombreux avantages, il n'est pas dénué de complexité et de défis. L'obtention de résultats optimaux dans le domaine du moulage par compression nécessite un équilibre délicat entre plusieurs paramètres, notamment la température, la pression, les propriétés des matériaux et la qualité de l'air. moulage par compression les principes fondamentaux et la conception. L'interaction de ces facteurs peut être complexe et entraîner des problèmes tels que des vides, des déformations et des flux de matériaux incohérents. Ces défis nécessitent des solutions innovantes pour améliorer la qualité des produits, réduire les déchets et optimiser la production.
C'est là que les logiciels de simulation entrent en scène. Les logiciels de simulation sont devenus des outils puissants qui permettent aux fabricants de s'attaquer de front aux complexités du moulage par compression. En créant des modèles virtuels et en effectuant des simulations de remplissage de moules à compression, les fabricants peuvent prédire les résultats, optimiser les paramètres et identifier les défauts potentiels, le tout sans avoir à recourir à des prototypes physiques coûteux. L'importance des logiciels de simulation par éléments finis pour aborder les complexités du moulage par compression ne peut être surestimée, car ils jouent un rôle essentiel dans l'amélioration de l'efficacité et de la qualité et, en fin de compte, dans le façonnement de l'avenir de l'industrie manufacturière.
Dans les sections suivantes, nous approfondirons la question de la processus de moulage par compression, explorent les façons dont les logiciels de simulation peuvent être exploités efficacement et fournissent des informations pratiques pour optimiser les résultats du moulage par compression.
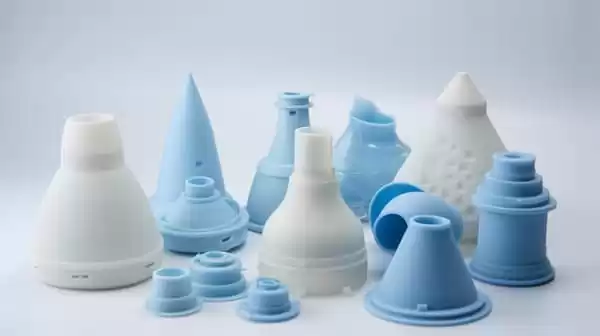
II. Comprendre le moulage par compression
Le moulage par compression est un processus de fabrication qui implique plusieurs étapes distinctes et une variété de paramètres critiques. Dans cette section, nous allons décomposer les bases du processus de moulage par compression et mettre en lumière les paramètres clés et les variables qui ont un impact significatif sur les résultats.
Les étapes de base du moulage par compression
1. Préparation :
Le processus de moulage par compression commence par la préparation de la matière première, qui se présente généralement sous la forme de granulés ou de préformes. Cette matière est chargée dans la cavité d'un moule, un espace conçu avec précision qui détermine la forme finale du produit.
2. Le chauffage :
Une fois que la cavité du moule est chargée de matériau, elle est fermée et la chaleur est appliquée au matériau. La chaleur ramollit le matériau, le rendant plus malléable et prêt à être moulé.
3. Compression :
Après avoir atteint la température souhaitée, une pression est exercée sur le matériau. Cette compression force le matériau à remplir complètement la cavité du moule, prenant ainsi la forme de ce dernier.
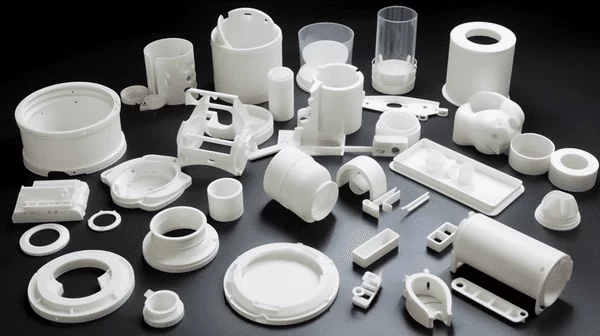
4. Refroidissement :
Après la phase de compression, le moule est refroidi pour solidifier le matériau. Le temps de refroidissement est soigneusement contrôlé pour garantir que le matériau conserve sa forme et son intégrité structurelle.
5. Expulsion :
Une fois le matériau suffisamment refroidi et solidifié, le produit final est éjecté du moule. Le produit est alors prêt à être transformé ou utilisé.
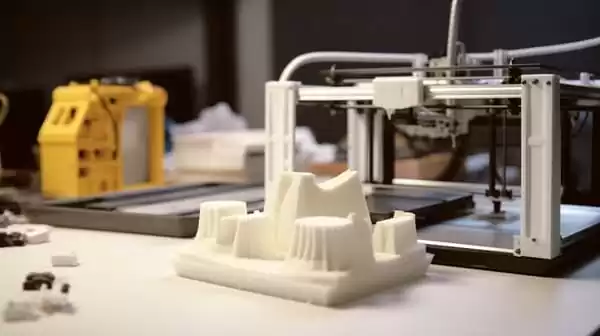
Paramètres et variables clés du moulage par compression
L'obtention de résultats optimaux dans le domaine du moulage par compression dépend d'un équilibre minutieux entre plusieurs paramètres et variables critiques, notamment :
Température : La température à laquelle le matériau est chauffé joue un rôle fondamental dans son comportement au cours du processus de moulage par injection et compression. Elle affecte les caractéristiques d'écoulement du matériau, son durcissement et ses performances globales.
Pression : L'application de la pression est nécessaire pour s'assurer que le matériau remplit complètement la cavité du moule. Un contrôle adéquat de la pression permet d'éviter les défauts et d'assurer l'uniformité du remplissage du moule.
Le temps : La durée de chaque phase du processus de moulage, y compris le chauffage, la compression et le refroidissement, a un impact direct sur la qualité et les propriétés du produit final.
Propriétés du matériau : Les caractéristiques des matériaux, telles que la viscosité, la vitesse d'écoulement de la matière fondue et le comportement au durcissement, sont des éléments essentiels à prendre en compte dans le moulage par compression. Le choix du matériau influence grandement le processus de moulage et la qualité du produit final.
Conception du moule : L'orientation des fibres de la géométrie de la cavité du moule, ainsi que les caractéristiques telles que les évents et les canaux, affectent de manière significative l'écoulement du matériau et la structure de la pièce finale.
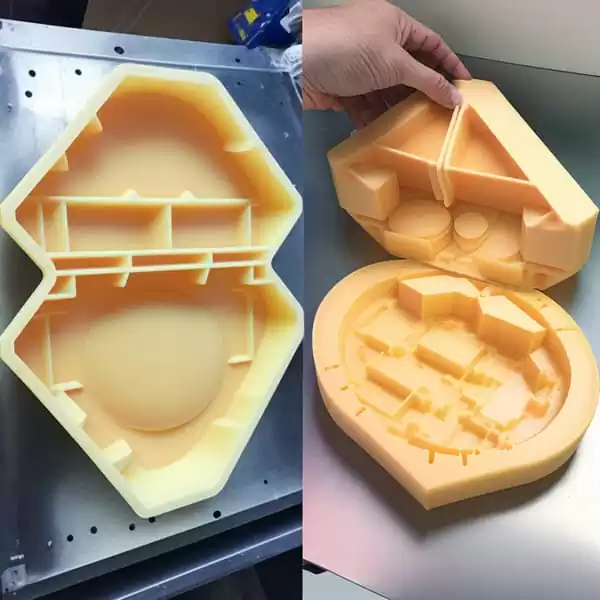
Taux de refroidissement : La vitesse à laquelle le composé de moulage de la feuille supérieure est refroidi après la compression a un impact sur la cristallisation du matériau et, par la suite, sur ses propriétés mécaniques.
Dans la section suivante, nous verrons comment les logiciels de simulation peuvent être utilisés pour optimiser ces paramètres et variables, ce qui permet d'améliorer les résultats du moulage par compression.
III. Rôle des logiciels de simulation
Les logiciels de simulation changent la donne dans le domaine du moulage par compression. Dans cette section, nous présenterons le concept de logiciel de simulation dans le contexte du moulage par compression, en soulignant comment il sert d'outil puissant pour prédire les résultats, optimiser les paramètres du processus, réduire les défauts, concevoir des moules, améliorer la sélection des matériaux et, en fin de compte, gagner du temps et économiser des ressources précieuses.
Présentation du logiciel de simulation
Dans le contexte du moulage par compression, les logiciels de simulation sont des outils informatiques avancés qui permettent aux fabricants de créer des modèles virtuels de l'ensemble du processus de moulage. Ces modèles virtuels imitent les conditions réelles, ce qui permet aux ingénieurs et aux fabricants d'obtenir des informations précieuses sur la manière dont les différents paramètres et variables affecteront le produit final. Il s'agit essentiellement d'un bac à sable numérique où l'on peut expérimenter sans avoir à recourir à des prototypes physiques.
Prédire les résultats avec précision
L'un des principaux avantages des logiciels de simulation dans le domaine du moulage par compression est leur capacité à prédire les résultats avec précision. Les ingénieurs peuvent introduire dans la simulation des paramètres spécifiques, tels que la température, la pression et les propriétés des matériaux. Le logiciel calcule ensuite l'interaction de ces paramètres, ce qui donne une idée précise de ce à quoi il faut s'attendre pendant la production réelle. Cette capacité prédictive permet aux fabricants d'affiner leurs processus pour obtenir des résultats optimaux.
Optimisation des paramètres du processus
Les logiciels de simulation ne se limitent pas à la prédiction ; ils excellent également dans l'optimisation. En effectuant des simulations avec différentes combinaisons de paramètres, les fabricants peuvent déterminer les réglages idéaux pour leur processus de moulage par compression. Par exemple, ils peuvent identifier la combinaison optimale température-pression qui permet de réduire les temps de cycle, de diminuer les coûts de production et d'améliorer la qualité des produits. Cette optimisation est une étape cruciale pour obtenir les meilleurs résultats possibles de la simulation du processus de moulage par compression.
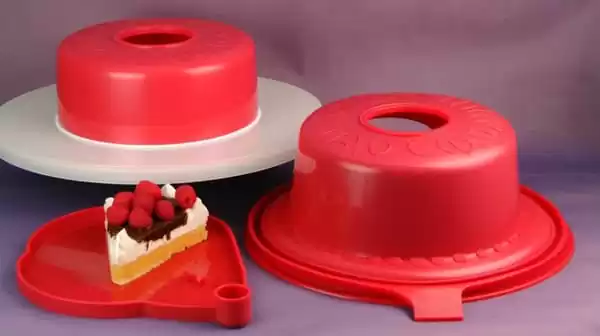
Réduction des défauts et amélioration de la qualité
Dans la quête de l'excellence, les logiciels de simulation constituent un outil puissant pour la réduction des défauts. En simulant le processus de moulage, les fabricants peuvent identifier les défauts potentiels tels que les vides, les déformations ou les problèmes de flux de matière avant qu'ils ne se produisent dans la production réelle. Forts de ces connaissances, des ajustements peuvent être apportés au processus, ce qui permet de réduire efficacement les défauts et d'améliorer la qualité globale du produit final.
Conception de moules efficaces
La conception des moules est un aspect essentiel du moulage par compression, et les logiciels de simulation sont d'une aide précieuse dans ce domaine. Les ingénieurs peuvent utiliser le logiciel pour concevoir des moules avec des géométries complexes qu'il est difficile de réaliser uniquement par essais et erreurs. Le logiciel garantit que les moules sont efficaces et capables de produire régulièrement des pièces de haute qualité.
Améliorer la sélection des matériaux
Les logiciels de simulation permettent aux fabricants d'évaluer le comportement des différents matériaux lors du moulage par compression. Ce logiciel est particulièrement utile lorsqu'il s'agit de matériaux avancés tels que les composites renforcés de fibres. En simulant différentes options de matériaux, les fabricants peuvent prendre des décisions éclairées sur le matériau le mieux adapté à une application spécifique, garantissant ainsi des performances optimales.
Gagner du temps et des ressources
L'un des aspects les plus convaincants des logiciels de simulation est sans doute leur capacité à économiser du temps et des ressources. Les méthodes traditionnelles d'essai et d'erreur peuvent être coûteuses et chronophages, car elles impliquent de nombreux prototypes physiques et itérations. Les logiciels de simulation éliminent une grande partie de ces essais et erreurs en permettant aux ingénieurs d'affiner les processus numériquement avant de s'engager dans la production physique.
Dans la section suivante, nous examinerons les mesures pratiques que les fabricants peuvent prendre pour exploiter efficacement la puissance des logiciels de simulation dans le processus de moulage par compression.
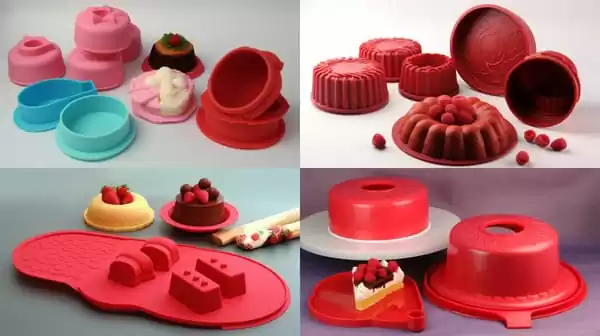
IV. Étapes de l'utilisation efficace d'un logiciel de simulation
L'utilisation efficace d'un logiciel de simulation dans le domaine du moulage par compression nécessite une approche systématique. Les fabricants peuvent suivre un guide étape par étape pour maximiser les avantages de cet outil puissant. Voici un aperçu complet des principales étapes à suivre :
1. Collecte des données
Une simulation efficace commence par une solide collecte de données. Les fabricants doivent rassembler toutes les données pertinentes, notamment
- Propriétés du matériau : Informations complètes sur le matériau utilisé, telles que sa viscosité, son taux de fluidité, sa conductivité thermique et son comportement en matière de durcissement.
- Spécifications des moules : Spécifications détaillées du moule, y compris les dimensions, la géométrie et les détails de la ventilation.
- Paramètres du processus : Des données précises sur les paramètres du processus tels que la température, la pression et les temps de cycle.
- Données historiques : Toutes les données de production antérieures ou les enregistrements de défauts qui peuvent éclairer le processus de simulation.
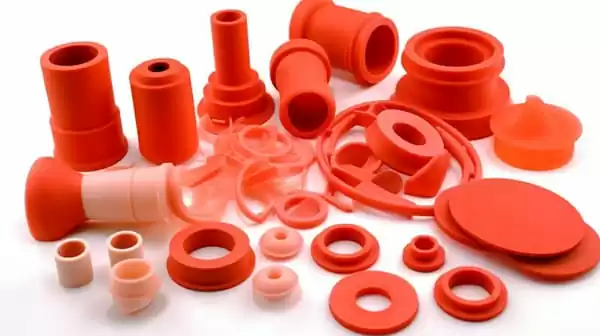
2. Création du modèle
Une fois les données en main, l'étape suivante consiste à créer un modèle virtuel du processus de moulage par compression. Il s'agit de
- Création de géométrie : Construire une représentation 3D du moule et du matériau dans le logiciel de simulation.
- Paramètre d'entrée : Introduire toutes les données recueillies, y compris les propriétés des matériaux et les paramètres du processus, dans le modèle de simulation.
- Conditions limites : Définir les conditions limites, telles que les températures et les pressions initiales.
3. La simulation
Une fois le modèle préparé, un logiciel de simulation est utilisé pour exécuter des processus virtuels de moulage par compression. Au cours de cette phase :
- Simuler le processus : Le logiciel effectue des simulations basées sur le modèle défini, reproduisant le processus réel de moulage par compression.
- Surveiller le comportement : Les ingénieurs peuvent contrôler l'écoulement du matériau, la répartition de la pression et l'évolution de la température dans le moule virtuel.
4. L'analyse
Une fois les simulations terminées, il est temps de procéder à une analyse approfondie :
- Identification des défauts : Examinez les résultats de la simulation pour identifier les défauts ou les problèmes potentiels dans le processus. Il peut s'agir de vides, de déformations ou d'un flux de matière incohérent.
- Propriétés mécaniques : Analyser les propriétés mécaniques prévues du produit final, telles que la résistance, la rigidité et la résilience.
- Comportement matériel : Comprendre le comportement du matériau dans différentes conditions et pressions.
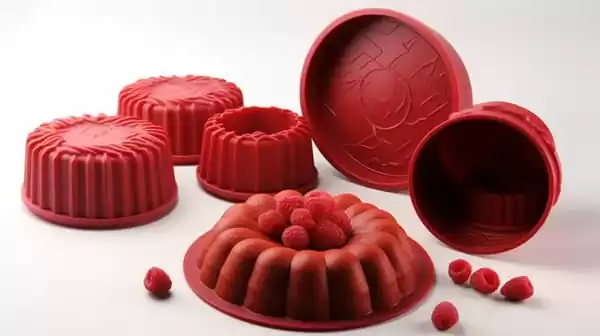
5. Optimisation
Avec une compréhension claire des résultats de la simulation et des domaines d'amélioration identifiés, les fabricants peuvent procéder à l'optimisation :
- Réglages des paramètres : Modifier les paramètres du processus, tels que la température, la pression ou la durée du cycle, afin d'optimiser le processus de moulage par compression.
- Sélection des matériaux : Sur la base des résultats de la simulation, envisager différents matériaux ou mélanges de matériaux susceptibles d'améliorer les propriétés du produit final.
- Conception du moule : Ajuster la conception du moule pour améliorer le flux de matière et minimiser les défauts.
6. La validation
La validation est une étape cruciale pour s'assurer que les résultats de la simulation correspondent aux résultats du monde réel :
- Comparer avec des données réelles : Valider les résultats de la simulation en les comparant aux données de production réelles et aux prototypes physiques.
- Itérer si nécessaire : Si des disparités sont constatées, il convient d'apporter les ajustements nécessaires au modèle de simulation et d'effectuer des tests supplémentaires jusqu'à ce que les résultats correspondent aux performances réelles.
7. Mise en œuvre
Enfin, mettre en œuvre le processus optimisé sur la base des résultats de la simulation :
- Ajustement du processus : Mettre en œuvre les paramètres de processus révisés, les conceptions de moules ou les sélections de matériaux dans la production réelle.
- Contrôle continu : Contrôler en permanence la production pour s'assurer que les améliorations obtenues grâce à la simulation sont maintenues.
- Boucle de rétroaction : Établir une boucle de rétroaction dans laquelle les données de la production réelle sont utilisées pour affiner et améliorer le modèle de simulation en vue d'une utilisation future.
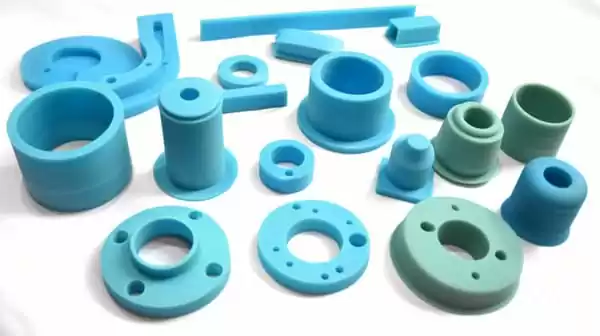
En suivant systématiquement ces étapes, les fabricants peuvent exploiter tout le potentiel des logiciels de simulation dans le domaine du moulage par compression, ce qui permet d'améliorer la qualité des produits, de réduire les défauts et d'améliorer l'efficacité des processus de production.
IV. Qu'est-ce que la simulation de l'écoulement des moules ?
Dans le monde complexe de l'industrie plastique, la simulation de l'écoulement des moules apparaît comme un outil spécialisé et indispensable. Cette section définit et explique la simulation de l'écoulement des moules, en mettant en lumière son rôle dans la compréhension du flux et de la distribution des matériaux dans les moules.
Définition de la simulation de l'écoulement des moules
La simulation de l'écoulement des moules est un outil logiciel hautement spécialisé utilisé dans l'industrie des matières plastiques. Sa fonction première est de créer des représentations virtuelles de l'ensemble du processus de moulage par injection, ce qui permet aux fabricants d'acquérir une connaissance approfondie de la manière dont la matière plastique fondue s'écoule et se répartit dans les moules. Cet outil sert de laboratoire virtuel et permet de comprendre le comportement complexe des matériaux au cours du processus de moulage.
Comprendre le flux et la distribution des matières
La simulation Moldflow excelle dans sa capacité à simuler et à analyser le flux et la distribution des matériaux avec un haut degré de précision. Voici comment elle y parvient :
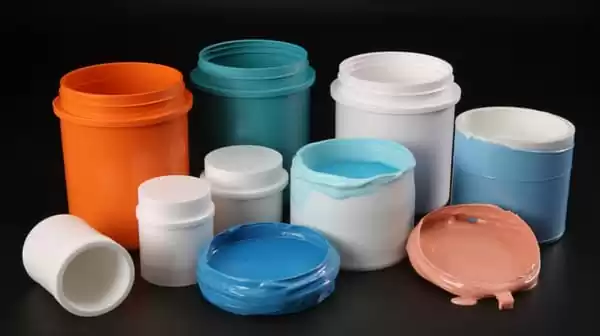
- Comportement matériel : La simulation de l'écoulement des moules commence par la prise en compte des propriétés de la matière plastique utilisée. Cela inclut des aspects tels que la viscosité de la matière fondue, le comportement en fonction de la température et les caractéristiques rhéologiques.
- Analyse géométrique : Le logiciel prend ensuite en compte la géométrie de la cavité du moule, y compris ses caractéristiques complexes, ses portes, ses glissières et ses canaux de refroidissement. Cette analyse est cruciale pour comprendre comment le matériau s'écoulera dans le moule.
- Simulation d'injection : Le cœur de la simulation Moldflow réside dans sa capacité à simuler la phase d'injection. Elle prédit comment la matière plastique en fusion va pénétrer dans le moule, comment elle va en remplir tous les coins et recoins et comment la pression va être répartie.
- Visualisation des flux : Grâce à la simulation, Moldflow génère des représentations visuelles de l'écoulement des matériaux. Il peut s'agir de fronts d'écoulement, de profils de pression et de gradients de température, offrant aux ingénieurs et aux fabricants une image claire de ce qui se passe à l'intérieur du moule.
- Identification des défauts : La simulation Moldflow permet également d'identifier les défauts potentiels qui peuvent survenir au cours du processus de moulage par injection. Il s'agit notamment de problèmes tels que les pièges à air, les lignes de soudure, les marques d'enfoncement et les remplissages incomplets.
Rôle dans la conception et l'optimisation des moules
La simulation de l'écoulement des moules ne se limite pas à la compréhension du flux des matériaux ; elle joue également un rôle essentiel dans la conception et l'optimisation des moules. Voici comment :
- Conception du moule : Les ingénieurs peuvent utiliser la simulation Moldflow pour affiner la conception des moules, en veillant à ce que le flux de matière soit uniforme et que les défauts soient réduits au minimum. Il peut s'agir de modifier l'emplacement des portes, d'ajuster les systèmes de canaux et d'optimiser les stratégies de refroidissement.
- Sélection des matériaux : La simulation permet d'évaluer différents matériaux et leur comportement dans le moule. Les fabricants peuvent choisir le matériau le plus approprié sur la base des résultats de la simulation.
- Optimisation : La simulation de l'écoulement des moules permet d'optimiser les paramètres du processus, tels que la vitesse d'injection, la température de la matière fondue et la vitesse de refroidissement, afin d'obtenir les meilleurs résultats de moulage possibles.
En résumé, la simulation Moldflow est un outil logiciel spécialisé conçu pour l'industrie des plastiques. Il joue un rôle essentiel dans la compréhension de l'écoulement et de la distribution des matières plastiques fondues dans les moules au cours du processus de moulage par injection. En simulant le comportement des matériaux, la géométrie des moules et la phase d'injection, Moldflow fournit des informations inestimables sur le monde complexe du moulage des matières plastiques. Il permet non seulement d'identifier les défauts, mais aussi de guider la conception des moules et l'optimisation des processus, ce qui permet en fin de compte d'obtenir des produits plus efficaces et plus rentables. des composants en plastique de meilleure qualité.
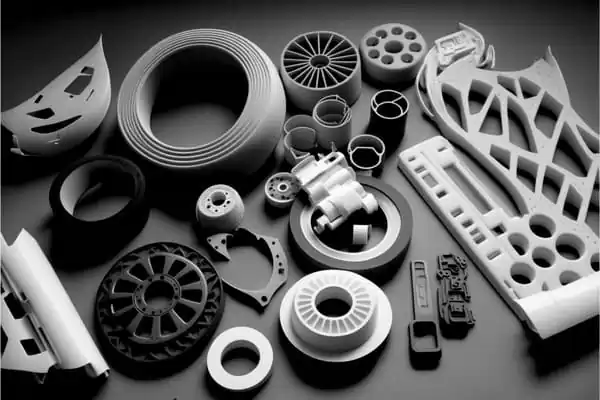
V. Paramètres de contrôle du processus de moulage par compression
Le succès du processus de moulage par compression dépend du contrôle minutieux de divers paramètres et variables. Dans cette section, nous énumérons et expliquons les paramètres de contrôle qui jouent un rôle essentiel dans l'obtention de résultats optimaux en matière de moulage par compression :
1. La température :
- Explication : Le contrôle de la température est fondamental dans le moulage par compression. Elle influe sur le comportement du matériau en affectant sa viscosité, l'écoulement de la matière fondue et les propriétés de durcissement. La précision du profil de température pendant les phases de chauffage et de refroidissement est essentielle pour la qualité du produit.
2. Pression :
- Explication : La pression est un autre paramètre clé du moulage par compression. Une pression bien contrôlée assure une distribution uniforme du matériau, minimise les défauts tels que les vides ou les déformations, et compacte le matériau dans la forme souhaitée à l'intérieur de la cavité du moule.
3. Le temps :
- Explication : Le temps est un paramètre critique qui régit la durée de chaque phase du processus de moulage par compression. Il est essentiel de bien choisir le moment pour obtenir le durcissement du matériau, le refroidissement et l'efficacité globale du processus.
4. Propriétés des matériaux :
- Explication : Les propriétés du matériau moulé ont un impact significatif sur le processus de moulage par compression. Ces propriétés comprennent la viscosité, le débit de la matière fondue, la conductivité thermique, le comportement au durcissement et même les caractéristiques rhéologiques du matériau. Il est essentiel de comprendre et d'optimiser les propriétés de ces matériaux pour réussir le moulage.
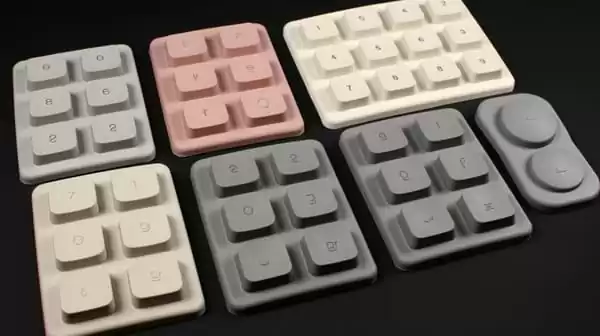
5. Conception des moules :
- Explication : La géométrie de l'empreinte du moule et d'autres caractéristiques telles que les évents, les glissières et les canaux de refroidissement ont un impact profond sur le flux et la distribution des matériaux, ainsi que sur la qualité de la pièce finale. Un moule bien conçu assure un compactage efficace de la matière et minimise les défauts.
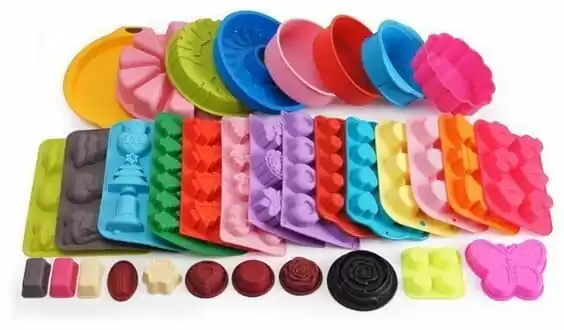
6. Distribution de la pression :
- Explication : Ce n'est pas seulement la pression globale qui est cruciale, mais aussi la répartition de la pression sur la surface du moule. Une répartition uniforme de la pression garantit un compactage homogène du matériau et minimise les défauts tels qu'une épaisseur inégale ou des vides dans le produit final.
7. Taux de refroidissement :
- Explication : La vitesse de refroidissement du moule après la compression affecte de manière significative la cristallisation du matériau et, par conséquent, ses propriétés mécaniques. Un contrôle précis de la vitesse de refroidissement est essentiel pour obtenir les propriétés souhaitées de la pièce.
8. Température de surface du moule :
- Explication : Le contrôle de la température de la surface du moule est essentiel pour assurer la polymérisation et le démoulage corrects du matériau. La température de la surface du moule a un impact sur le comportement du matériau pendant les phases de chauffage et de refroidissement.
9. Analyse des flux de matières :
- Explication : Il est essentiel de comprendre comment le matériau s'écoule dans le moule pour contrôler des paramètres tels que la pression et la température. L'analyse du flux de matière permet d'identifier les zones à risque et d'optimiser le processus de moulage.
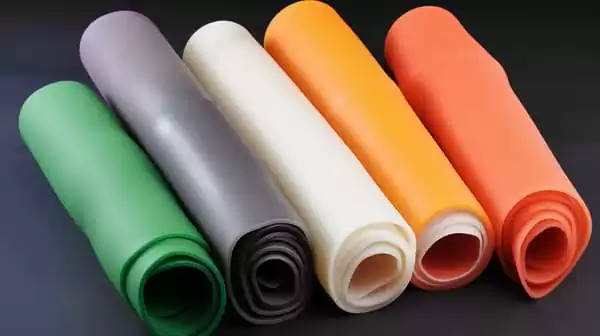
10. Ventilation et évacuation de l'air :
- Explication : Une ventilation et une évacuation de l'air appropriées sont nécessaires pour éviter l'emprisonnement d'air ou de gaz dans le moule. Une ventilation efficace assure un compactage complet du matériau et minimise les défauts.
Ces paramètres de contrôle définissent collectivement les conditions dans lesquelles le moulage par compression a lieu. La gestion précise de ces paramètres est essentielle pour obtenir des résultats cohérents et de haute qualité et pour garantir une production efficace des composants moulés. Les fabricants doivent examiner attentivement et optimiser chaque paramètre pour répondre aux exigences spécifiques de leurs produits et à leurs normes de qualité.
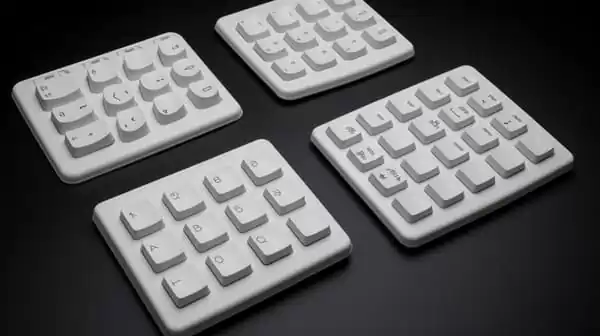
Conclusion
En conclusion, cet article a exploré le domaine du moulage par compression, en soulignant son importance et les complexités liées à l'obtention de résultats optimaux. Nous avons souligné le rôle essentiel des logiciels de simulation pour relever ces défis et optimiser le processus de moulage par compression. En voici les principaux enseignements :
- Importance du moulage par compression : Le moulage par compression est un processus de fabrication crucial utilisé dans tous les secteurs, qui permet de créer des composants complexes avec précision et efficacité.
- Les défis du moulage par compression : Pour obtenir des résultats optimaux en matière de moulage par compression, il faut contrôler avec précision des paramètres tels que la température, la pression, la durée, les propriétés des matériaux et la conception des moules. La complexité du comportement des matériaux et de la conception des moules peut entraîner des défauts et des inefficacités.
- La puissance des logiciels de simulation : Les logiciels de simulation changent la donne dans le domaine du moulage par compression. Il permet aux fabricants de créer des modèles virtuels du processus, de prédire les résultats, d'optimiser les paramètres et de réduire les défauts avant le début de la production physique.
- Les étapes d'une utilisation efficace de la simulation : Les fabricants peuvent suivre une approche structurée, comprenant la collecte de données, la création de modèles, la simulation, l'analyse, l'optimisation, la validation et la mise en œuvre, afin d'utiliser efficacement les logiciels de simulation.
- Simulation de l'écoulement des moules : La simulation de l'écoulement des moules, un outil spécialisé pour l'industrie des plastiques, joue un rôle crucial dans la compréhension de l'écoulement et de la distribution des matériaux à l'intérieur des moules. Elle facilite l'identification des défauts, la conception des moules, la sélection des matériaux et l'optimisation des processus.
- Paramètres de contrôle : Les principaux paramètres de contrôle du moulage par compression sont la température, la pression, le temps, les propriétés des matériaux, la conception du moule, la répartition de la pression, le taux de refroidissement, la température de la surface du moule, l'analyse du flux de matériaux et l'aération. Un contrôle précis de ces paramètres est essentiel pour obtenir des résultats cohérents et de haute qualité.
- L'avenir de la simulation du moulage : L'article conclut en soulignant l'importance des logiciels de simulation pour obtenir des résultats cohérents et supérieurs en matière de moulage par compression. C'est grâce au domaine numérique de la simulation que les fabricants peuvent innover, optimiser et s'adapter à l'évolution du paysage de l'ingénierie mécanique et de la transformation des polymères. Au fur et à mesure que la technologie progresse, nous pouvons nous attendre à ce que les outils de simulation deviennent encore plus essentiels pour façonner l'avenir de la fabrication.
Dans le monde en constante évolution de l'ingénierie mécanique et du traitement des polymères, les logiciels de simulation sont la boussole qui nous guide vers plus d'efficacité, d'innovation et d'excellence dans le domaine du moulage par compression. Avec chaque simulation, nous nous rapprochons du perfectionnement de l'art de fabriquer des composants de précision tout en économisant un temps et des ressources précieux. Pour l'avenir, nous nous attendons à ce que les logiciels de simulation continuent à jouer un rôle transformateur en repoussant les limites de ce qui est possible dans la fabrication, en veillant à ce que le moulage par compression reste une pierre angulaire de la production moderne.