Préface
Le caoutchouc de silicone est une sorte de caoutchouc synthétique et de matériau élastique polymère semi-inorganique contenant une structure silicium-oxygène dans la chaîne principale de la molécule. Il est formé par hydrolyse et polycondensation de monomères de silicone bifonctionnels tels que le diméthyldichlorosilane. Le caoutchouc de silicone ressemble beaucoup au caoutchouc naturel ordinaire, mais il présente un degré élevé de stabilité thermique et d'élasticité. Il conserve ses caractéristiques d'origine entre -60 et 300°C. Il se rétracte très peu lorsqu'il est comprimé à haute température et reprend sa forme initiale une fois la force extérieure supprimée. Livre chimique. Caoutchouc de silicone Selon la méthode de vulcanisation, on distingue le type de vulcanisation à chaud et le type de vulcanisation à température ambiante. Ce dernier se développe plus rapidement.
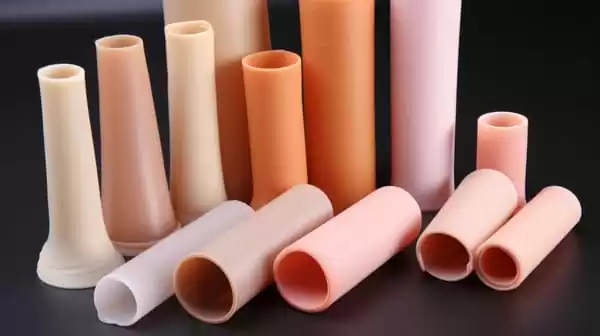
Les couches de caoutchouc de silicone peuvent être utilisées pour les fils, les câbles, les couches de protection des pièces métalliques, les pièces d'isolation, les joints d'étanchéité, les matières premières chimiques, les produits d'étanchéité comprennent les bagues d'étanchéité arrière du vilebrequin de moteur automobile, les joints de pompe à carburant, les joints de tampon de climatisation, les bagues d'isolation de potentiomètre et les matériaux d'empotage, etc. Il est utilisé pour fabriquer des joints d'isolation résistants aux températures élevées, des matériaux médicaux, des câbles à haute tension, des adhésifs, etc. Cependant, des bulles apparaissent souvent dans les produits en caoutchouc de silicone au cours du processus de production. L'apparition de bulles et de pores affecte la qualité du produit. Par conséquent, si une usine de produits en caoutchouc de silicone souhaite améliorer le taux de qualification de ses produits, elle peut commencer par éviter les bulles dans ses produits. Cet article vous informera sur les causes et les solutions des bulles dans les produits en caoutchouc silicone. produits en caoutchouc de silicone.
II. les causes des bulles générées
(1) Le système de contrôle de la température de vulcanisation du matériau en caoutchouc est trop bas ou la température de vulcanisation est trop élevée, ce qui est l'une des principales causes de la formation de cloques dans les feuilles de silicone thermoconductrices. La température de vulcanisation est un paramètre important lors du moulage du caoutchouc silicone. En général, les produits en silicone sont réglés à 160~200 degrés Celsius. Cependant, il arrive que le moule n'ait pas été chauffé par le vulcanisateur pendant une longue période en raison d'une opération de démoulage trop longue ou d'autres raisons. En conséquence, la température du moule de moulage en silicone est basse et la température de vulcanisation du silicone est basse, ce qui entraînera la formation de bulles d'air dans le produit après la formation de la feuille de silicone thermoconductrice. Dans ce cas, il suffit d'augmenter la température de moulage ou de placer le moule vide dans la machine et de le chauffer pendant un certain temps pour résoudre le problème. Si la température de vulcanisation est trop élevée et que la température de moulage est trop élevée, des bulles apparaîtront également dans la feuille de silicone thermoconductrice. Pourquoi ? Lorsque la température de moulage est trop élevée, la matière première silicone sur la surface du moule a commencé à se former pendant le processus de fermeture et de pressurisation du moule. À ce moment-là, l'air a été piégé à l'intérieur et il est difficile de l'évacuer, ce qui provoque des bulles dans le moulage de la feuille de silicone thermoconductrice. C'est pourquoi il suffit d'abaisser la température de moulage de manière appropriée.
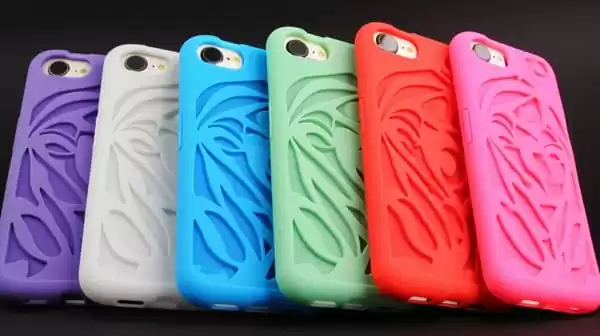
(2) La présence de bulles dans les produits en silicone s'explique par une évacuation insuffisante. Une fois que le matériau en caoutchouc de silicone est placé dans le moule en silicone, une grande quantité d'air est introduite au moment de la fermeture de la ligne d'échappement du moule. Il est impossible d'intégrer l'air à la matière première en silicone. L'air est évacué, ce qui provoque l'apparition de bulles à la surface du bouton en silicone ou des lignes d'échappement du moule après sa formation.
(3) La structure du moule n'est pas raisonnable. Une conception déraisonnable de la cavité du moule de moulage en silicone, l'humidité intérieure, provoquera également des bulles dans le moule de moulage en silicone. moulage de silicone. Par exemple, la disposition de la ligne d'échappement, la distribution des produits dans le moule, la méthode de partitionnement, la méthode de séparation du moule, la conception de la taille du moule, etc. Le coût de l'ouverture d'un ensemble de moules est très élevé et il n'est pas facile de le modifier.
(4) Le temps de vulcanisation est trop court. Tout comme la température de vulcanisation, le temps de vulcanisation est également l'un des paramètres importants pour le moulage de la feuille de silicone thermoconductrice. La durée de la vulcanisation détermine si la feuille de silicone thermoconductrice peut être complètement vulcanisée. Si le temps de vulcanisation est trop court, non seulement la feuille de silicone thermoconductrice deviendra molle après le moulage, mais des bulles se formeront facilement à la surface de la feuille de silicone thermoconductrice. Si de tels défauts apparaissent, le temps de vulcanisation du silicone peut être prolongé de manière appropriée.
(5) Le processus de production est également crucial : l'agent antivieillissement RD est susceptible de former des bulles pendant l'opération de mélange du broyeur ouvert. Ce phénomène est principalement dû au point de fusion de l'agent antivieillissement RD et à la température de fonctionnement plus basse du broyeur à ciel ouvert. En ce qui concerne le caoutchouc de mélange, une attention particulière doit être accordée à la dispersion de l'oxyde de zinc pendant le mélange. Sa dispersion uniforme provoquera également la formation de mousse sur les feuilles de silicone, de sorte que le processus de mélange du caoutchouc est également une étape très importante.
(6) La teneur en humidité des matières premières utilisées dans la formule et l'adéquation du séchage pendant l'opération de mélange et après que le produit a été extrudé et refroidi à l'eau sont principalement dues à la puissance de l'humidité pendant l'ajout de la vulcanisation.
III. Mesures de solution pour la prévention des bulles
1. Ajuster la proportion de particules de gel de silice
L'une des sources de bulles de silicone réside dans les quantités excessives de gel de silice dans les produits ; pour remédier à ce problème, il convient d'ajuster ce ratio de manière appropriée afin de réduire la formation de bulles et de les éviter complètement. Des tests et des vérifications expérimentales peuvent être nécessaires avant toute décision finale sur la mise en œuvre de cette stratégie.
2. Utiliser un équipement d'extraction sous vide
Lors de la fabrication de produits en silicone, l'utilisation d'un équipement d'évacuation sous vide peut aider à expulser les gaz qu'ils contiennent et à réduire efficacement les bulles qui s'y trouvent. Pour résoudre le problème des bulles au cours des processus de production, l'évacuation sous vide doit absolument faire partie de leur plan de solution.
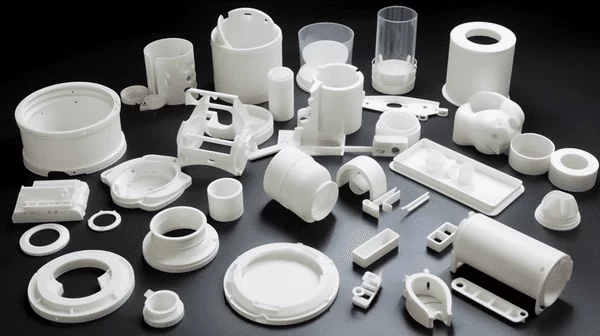
3. Régler la température de production
La température joue un rôle essentiel dans la fabrication des produits en silicone, car le choix d'une température incorrecte peut entraîner la formation de bulles à l'intérieur de ces produits. Par conséquent, au cours de la production, la température doit être correctement réglée afin de limiter autant que possible la formation de bulles et de maintenir un contrôle raisonnable en fonction des situations actuelles pour minimiser la production de bulles.
4. Ajouter l'agent tensioactif
Les produits à base de silicium présentent souvent des problèmes de formation de bulles au cours de la production. En encourageant les molécules de gel de silice à s'adsorber les unes les autres plus efficacement et en réduisant la formation de bulles, les surfactants peuvent contribuer à augmenter la qualité tout en améliorant les processus de production.
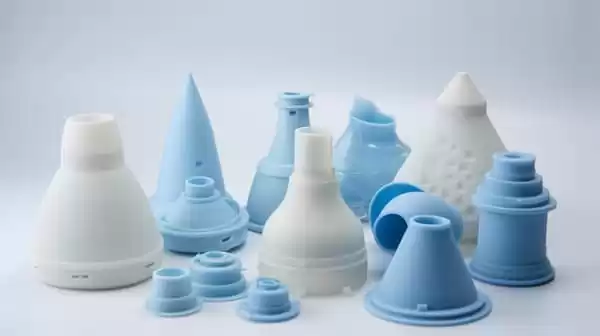
Conclusion
Souvent, la formation de bulles n'est pas due à un seul facteur, mais à une combinaison de plusieurs raisons. Pour résoudre le problème des bulles, il est difficile de suivre des règles générales et les problèmes spécifiques doivent être analysés en détail. Il faut d'abord déterminer la cause première des bulles et trouver des idées et des méthodes pour résoudre le problème en fonction de cette cause. Il y a souvent plus d'une solution, et il est préférable d'utiliser une approche à plusieurs volets. Le mieux est de prévenir la formation de bulles. D'une part, des réglages d'échappement adéquats doivent être effectués lors de la conception du moule ; d'autre part, la précuisson du flan en caoutchouc et d'autres matériaux avant la vulcanisation peut éliminer efficacement la volatilisation à l'intérieur du matériau en caoutchouc. Il s'agit d'un moyen efficace de prévenir la formation de bulles dans les produits.