Struktur cetakan injeksi karet silikon cair termoset (LSR) umumnya mirip dengan cetakan yang digunakan untuk senyawa termoplastik, tetapi ada beberapa perbedaan yang signifikan.
Sebagai contoh, senyawa LSR umumnya memiliki viskositas yang rendah dan oleh karena itu waktu pengisiannya sangat singkat, bahkan pada tekanan injeksi yang sangat rendah. Untuk menghindari terperangkapnya udara, sangat penting untuk memiliki perangkat ventilasi udara yang baik di dalam cetakan.
Selain itu, senyawa LSR tidak menyusut sebanyak senyawa termoplastik di dalam cetakan; senyawa ini cenderung mengembang saat panas dan sedikit menyusut saat dingin. Akibatnya, produk tidak selalu berada di sisi cembung cetakan seperti yang diharapkan, tetapi tertahan di rongga dengan luas permukaan yang lebih besar.
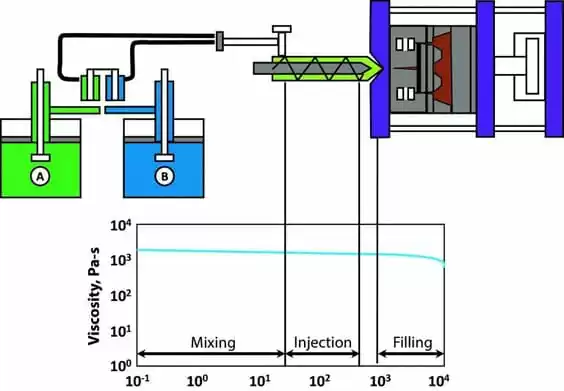
1. Penyusutan
Meskipun LSR tidak menyusut di dalam cetakan, namun sering kali menyusut 2,5% hingga 3% setelah demolding dan pendinginan. Jumlah penyusutan yang tepat tergantung sampai batas tertentu pada formulasi senyawa itu.
Namun demikian, dari perspektif cetakan, penyusutan dapat dipengaruhi oleh beberapa faktor, termasuk suhu cetakan, suhu kompon ketika dibentuk, serta tekanan dalam rongga cetakan, dan kompresi kompon selanjutnya.
Lokasi titik injeksi juga perlu dipertimbangkan, karena penyusutan ke arah aliran perekat biasanya lebih besar daripada penyusutan ke arah yang tegak lurus dengan aliran perekat.
Ukuran produk juga memengaruhi penyusutannya, dengan produk yang lebih tebal umumnya memiliki penyusutan yang lebih sedikit daripada produk yang lebih tipis. Jika vulkanisasi sekunder diperlukan, penyusutannya mungkin akan bertambah 0,5%-0,7%.
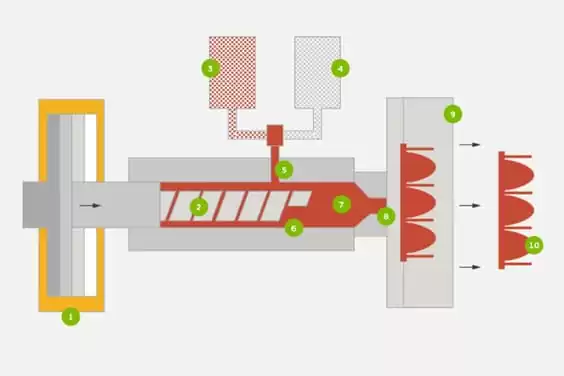
2. Garis perpisahan
Menentukan lokasi garis perpisahan adalah salah satu dari beberapa langkah pertama dalam merancang cetakan injeksi karet silikon. Ventilasi dicapai terutama dengan menggunakan alur yang terletak pada garis perpisahan, yang harus berada di area di mana senyawa injeksi akan bertahan. Hal ini membantu menghindari gelembung udara internal dan mengurangi hilangnya kekuatan pada sambungan lem.
Karena viskositas LSR yang rendah, garis perpisahan harus tepat untuk menghindari tumpahan. Meski begitu, garis pemisah sering kali terlihat pada produk yang berbentuk. Pelepasan cetakan dipengaruhi oleh geometri komponen dan posisi permukaan perpisahan. Merancang bagian dengan sedikit talang akan membantu memastikan afinitas yang konsisten untuk bagian lain yang diinginkan cetakan injeksi rongga.
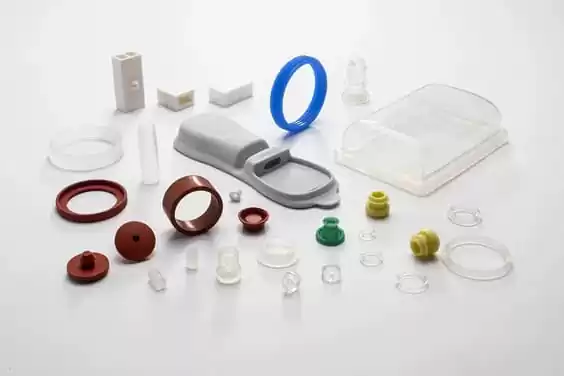
3. Ventilasi
Saat LSR diinjeksikan, udara yang terperangkap di dalam rongga dikompresi saat cetakan menutup dan kemudian dikeluarkan melalui alur ventilasi saat cetakan terisi.
Jika udara tidak sepenuhnya keluar, udara akan terperangkap dalam perekat (yang sering menyebabkan bagian produk menunjukkan tepi putih). Alur ventilasi pada umumnya memiliki lebar mm-3mm dan kedalaman 0,004mm-0,005mm.
Efek ventilasi terbaik bisa diciptakan dengan menyedot debu di dalam cetakan. Hal ini dicapai dengan mendesain paking pada garis perpisahan dan secara cepat mengevakuasi semua rongga ke ruang hampa udara dengan pompa vakum. Setelah vakum mencapai level yang ditetapkan, cetakan ditutup sepenuhnya dan proses injeksi dimulai.
Beberapa peralatan cetakan injeksi memungkinkan pengoperasian pada gaya penutupan variabel, yang memungkinkan prosesor untuk menutup cetakan pada tekanan rendah hingga 90-95% rongga diisi dengan LSR (sehingga lebih mudah bagi udara untuk keluar), dan kemudian beralih ke gaya penutupan yang lebih tinggi untuk menghindari karet silikon ekspansi dan luapan.
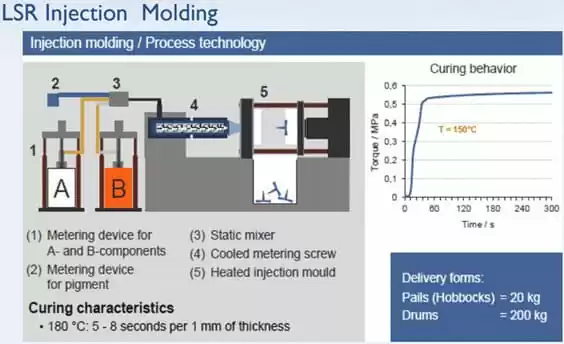
4. Titik injeksi
Sistem cold runner digunakan ketika mencetak LSR. Keuntungan dari hal ini karet silikon dapat dimaksimalkan dan efisiensi produksi dapat ditingkatkan secara maksimal.
Dengan memproses produk sedemikian rupa, maka tidak perlu melepas saluran injeksi, sehingga menghindari peningkatan tenaga kerja untuk operasi dan terkadang limbah material dalam jumlah besar. Dalam banyak kasus, konstruksi tanpa jalur juga mengurangi waktu pengoperasian.
Nosel injeksi dikendalikan oleh katup jarum untuk aliran positif, dan banyak produsen sekarang menawarkan nosel dengan sakelar pneumatik sebagai perlengkapan standar dan dapat diatur di berbagai bagian cetakan.
Beberapa cetakan injeksi pembuatnya telah mengembangkan sistem cold runner terbuka yang sangat kecil sehingga beberapa titik injeksi (dan dengan demikian seluruh rongga) harus diatur dalam ruang cetakan yang sangat terbatas.
Teknologi ini memungkinkan untuk menghasilkan kualitas tinggi dalam jumlah besar produk karet silikon tanpa harus memisahkan port injeksi.
Jika sistem cold runner digunakan, penting untuk membuat pemisahan suhu yang efektif antara rongga panas dan cold runner. Jika runner terlalu panas, karet dapat mulai memvulkanisasi sebelum diinjeksikan. Tetapi jika mendingin terlalu cepat, ia akan menyerap terlalu banyak panas dari area sariawan cetakan injeksiyang mengakibatkan vulkanisasi tidak sempurna.
Untuk produk yang diinjeksikan dengan sariawan konvensional (misalnya sariawan terendam dan sariawan berbentuk kerucut), sebaiknya gunakan port injeksi berdiameter kecil (biasanya 0,2 mm-0,5 mm) untuk injeksi.
Dengan senyawa LSR dengan viskositas rendah, seperti halnya senyawa termoplastik, penting untuk menyeimbangkan sistem runner sehingga semua rongga terisi secara merata dengan senyawa. Perangkat lunak simulasi untuk mendesain sistem runner dapat sangat menyederhanakan pengembangan cetakan dan membuktikan keefektifannya dengan menggunakan uji pengisian cetakan.
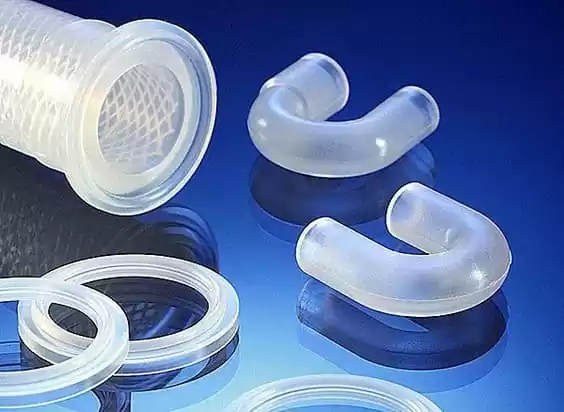
5. Demolding
Cetakan silikon cair, melalui vulkanisasi, cenderung melekat pada permukaan logam, dan kelenturan produk dapat membuatnya sulit untuk dilepaskan. Kekuatan sobek suhu tinggi dari LSR memungkinkannya dilepaskan dalam kondisi normal tanpa merusak produk yang lebih besar.
Teknik pelepasan yang paling umum termasuk pelepasan pelat stripper, pelepasan pin stripper, dan pelepasan pneumatik. Teknik umum lainnya adalah pengikisan rol, pelepasan pelat ekspor, dan pelepasan cetakan otomatis.
Apabila menggunakan sistem pelepasan, yang penting adalah menjaganya agar tetap berada dalam tingkat akurasi yang tinggi. Jika terdapat terlalu banyak jarak bebas antara pin dorong atas dan selongsong pin pemandu, atau jika celah di antara bagian-bagiannya menjadi besar akibat keausan dari waktu ke waktu, maka, dapat terjadi tumpahan lem.
Pin dorong atas berbentuk kerucut terbalik atau berbentuk jamur sangat efektif karena memungkinkan tekanan kontak yang lebih besar untuk diterapkan dan memfasilitasi peningkatan tujuan penyegelan.
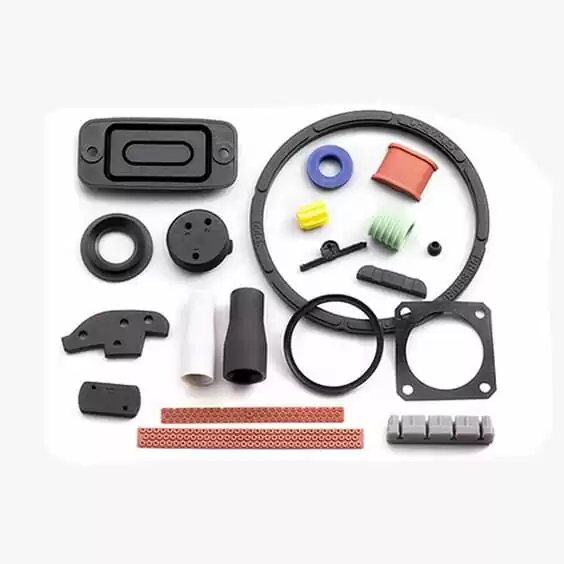
6. Bahan cetakan
Palet cetakan sering kali dibuat dari baja perkakas non-paduan (no.1.1730, kode DIN C45W). Untuk palet cetakan yang harus tahan terhadap suhu tinggi 170 ℃ -210 ℃, palet tersebut harus dibuat dari baja pra-temper (no.1.2312, kode DIN 40 CrMn-M oS 8 6) dengan mempertimbangkan ketahanan benturan.
Untuk palet cetakan dengan rongga cetakan, palet tersebut harus terbuat dari baja perkakas etil yang diberi perlakuan panas nitridasi atau temper untuk memastikan ketahanannya terhadap suhu tinggi.
Untuk LSR dengan kapasitas pengisian yang tinggi, seperti LSR kelas tahan minyak, disarankan untuk menggunakan bahan yang lebih keras untuk pembuatan cetakan, seperti baja berlapis krom cerah atau logam bubuk yang dikembangkan khusus untuk tujuan ini (no.1.2379, DINcode X 155 CrVMo121).
Saat merancang cetakan injeksi untuk material dengan tingkat keausan tinggi, bagian-bagian yang mengalami gesekan tinggi harus dirancang untuk dibentuk dengan cara yang dapat diganti sehingga seluruh cetakan tidak perlu diganti.
Permukaan bagian dalam rongga cetakan memiliki dampak yang signifikan pada hasil akhir produk. Yang paling jelas yaitu, bahwa produk yang dibentuk akan cocok dengan permukaan rongga secara sempurna. Cetakan injeksi untuk produk transparan harus terbuat dari baja yang dipoles. Baja Chin/Nickel yang diberi perlakuan permukaan sangat tahan aus, sedangkan PTFE/Nickel memudahkan pelepasan cetakan.
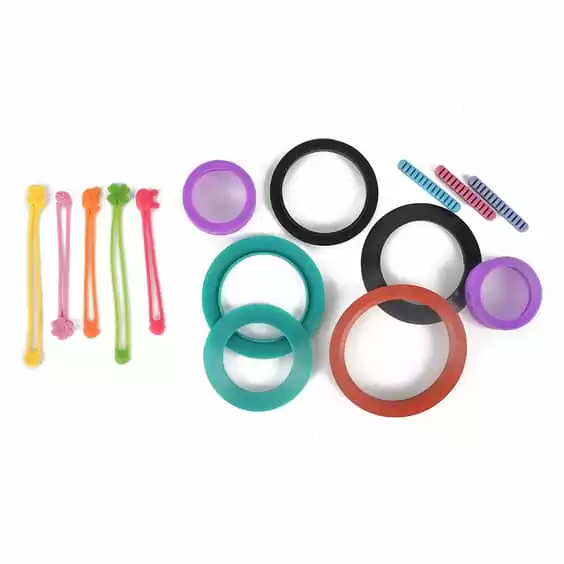
7. Kontrol suhu
Secara umum, pencetakan LSR lebih disukai untuk dipanaskan dengan pemanas listrik, biasanya dengan pemanas pita, pemanas kartrid, atau pelat pemanas.
Kuncinya adalah membuat bidang suhu terdistribusi secara merata di seluruh cetakan untuk mendorong pengawetan LSR yang seragam. Pada cetakan besar, merupakan metode pemanasan yang hemat biaya saat mendorong pemanasan kontrol suhu oli.
Membungkus cetakan dengan pelat isolasi membantu mengurangi kehilangan panas. Ketidaksesuaian bagian mana pun dari cetakan panas dapat menyebabkannya mengalami fluktuasi suhu yang besar di antara proses pengoperasian atau menyebabkan aliran udara.
Jika suhu permukaan turun terlalu rendah, kecepatan pengeringan perekat akan melambat, yang sering kali mencegah produk dilepaskan dari cetakan injeksi dan menyebabkan masalah kualitas.
Jarak tertentu harus dijaga antara pemanas dan garis perpisahan untuk mencegah templat menekuk dan berubah bentuk serta membentuk duri lem yang meluap pada produk jadi. Jika cetakan didesain dengan sistem cold runner, ujung panas dan ujung dingin harus benar-benar terpisah satu sama lain.
Paduan Chin khusus (mis. 3.7165 [TiA16V4]) dapat digunakan, karena konduktivitas termalnya yang jauh lebih rendah dibandingkan dengan baja lainnya. Untuk sistem pemanas cetakan injeksi integral, pelindung panas harus dipasang di antara cetakan dan palet cetakan untuk meminimalkan kehilangan panas. Desain dan konsepsi yang tepat dapat memastikan cetakan injeksi LSR, di mana cetakan sangat penting.
Prinsip-prinsip desain cetakan di atas ditujukan untuk mengisi rongga cetakan dengan karet, mempersingkat waktu pengawetan, dan mencapai kualitas unggul dan hasil yang tinggi dari produk jadi, sehingga menyediakan cairan cetakan karet silikon prosesor dengan manfaat ekonomi yang baik.