Pendahuluan
Desain rongga cetakan berdiri sebagai penopang keberhasilan pencetakan kompresi, yang memiliki kekuatan untuk membentuk masa depan berbagai industri. Aspek penting dalam manufaktur ini tidak boleh diremehkan, karena memiliki kemampuan untuk memberikan hasil yang berkualitas tinggi dan konsisten-sebuah bukti nyata akan signifikansinya.
Di dunia di mana inovasi dan presisi adalah yang tertinggi, cetakan kompresi muncul sebagai proses manufaktur yang serbaguna dan sangat diperlukan. Dengan aplikasi yang menjangkau berbagai industri, termasuk otomotif, elektronik, dan barang konsumen, proses ini memainkan peran penting dalam membentuk produk yang kita andalkan setiap hari. Dari komponen otomotif yang direkayasa untuk performa dan daya tahan hingga bahan isolasi listrik yang memastikan keamanan kita, compression moulding menyentuh hampir setiap aspek kehidupan kita.
Saat kita mempelajari lebih dalam tentang desain rongga cetakan untuk cetakan kompresikami memulai perjalanan yang mengungkap permadani rumit dari proses ini. Dengan menjelajahi nuansanya, kami akan mengungkap bagaimana desain rongga cetakan yang tepat dapat membuka dunia yang penuh dengan berbagai kemungkinan, membuat produk yang tidak hanya memenuhi tetapi juga sering kali melebihi harapan kami. Bergabunglah bersama kami dalam eksplorasi seni dan ilmu pengetahuan di balik pencetakan kompresi, di mana desain rongga cetakan adalah kompas yang memandu kita menuju lambang keunggulan manufaktur.
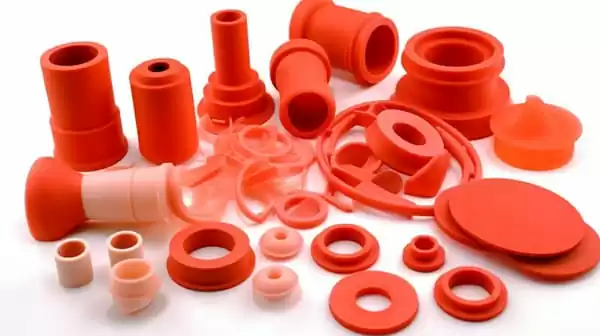
Memahami proses Pencetakan Kompresi
Compression moulding adalah proses manufaktur serbaguna dan digunakan secara luas dengan aplikasi di berbagai industri. Untuk memahami esensi dari teknik ini, sangat penting untuk memecahnya ke dalam komponen-komponen intinya.
1. Proses Pencetakan Kompresi:
Pada intinya, cetakan kompresi adalah proses yang melibatkan pembentukan bahan dengan menggunakan panas dan tekanan. Langkah-langkah yang terlibat adalah sebagai berikut:
Persiapan Bahan: Prosesnya dimulai dengan persiapan bahan baku, biasanya dalam bentuk butiran, pelet, atau senyawa cetakan lembaran (SMC).
Pemanasan: Cetakan, biasanya terdiri atas dua bagian, ditutup di sekeliling bahan. Panas kemudian diterapkan untuk melembutkan atau melelehkan bahan, membuatnya lentur.
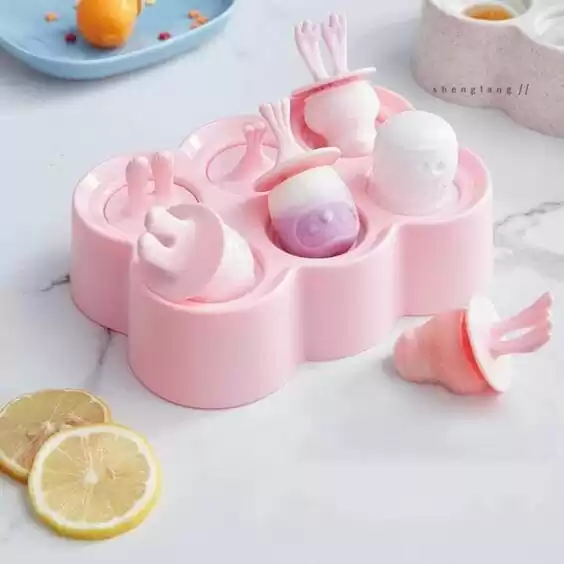
Kompresi: Tekanan diterapkan ke rongga cetakan, memadatkan bahan dan mengambil bentuk yang diinginkan dari produk akhir.
Pendinginan: Setelah bahan mengambil bentuk cetakan, bahan didinginkan untuk mengeras dan cetakan yang dipanaskan mengeras, mempertahankan bentuk yang diinginkan.
Pengeluaran: Terakhir, bagian cetakan dikeluarkan dari rongga cetakan, siap untuk diproses atau digunakan lebih lanjut.
2. Desain Cetakan Kompresi:
Landasan operasi pencetakan kompresi yang sukses terletak pada desain rongga cetakan. Desain cetakan kompresi mencakup beberapa elemen penting:
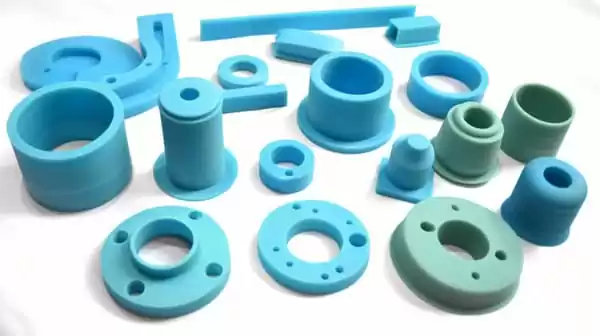
Geometri: Geometri rongga cetakan harus benar-benar sesuai dengan bentuk produk akhir yang diinginkan. Hal ini mencakup pertimbangan seperti ketebalan komponen, sudut rancangan, dan potongan, untuk memastikan pengeluaran yang mulus.
Ventilasi: Ventilasi yang efektif sangat penting untuk memungkinkan udara dan gas yang terperangkap keluar selama pencetakan. Ventilasi yang tepat mencegah cacat seperti kantong udara atau rongga pada produk akhir.
Garis Perpisahan: Garis perpisahan menunjukkan di mana cetakan terpisah untuk melepaskan bagian yang dicetak. Garis ini harus terdefinisi dengan baik dan tidak mengganggu estetika dan fungsionalitas produk.
Desain Gerbang: Gerbang berfungsi sebagai titik di mana bahan cair memasuki rongga cetakan. Desain gerbang yang cermat memastikan pengisian yang seragam dan meminimalkan cacat. Jenis gerbang termasuk gerbang tepi, gerbang pin, dan gerbang terowongan.
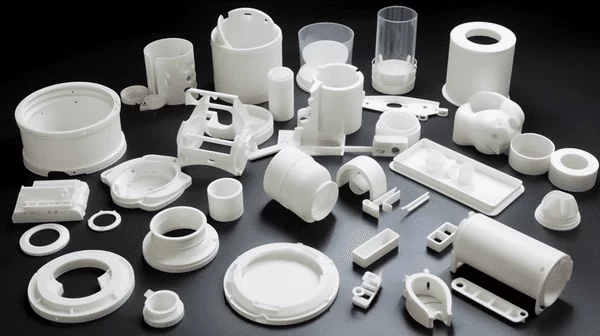
Sistem Pendinginan: Saluran pendinginan yang efisien di dalam cetakan membantu memantapkan bagian yang dicetak dengan cepat, mencegah lengkungan atau distorsi, dan meningkatkan waktu siklus.
Permukaan akhir: Tergantung pada kebutuhan produk, permukaan akhir rongga cetakan dapat dipoles, bertekstur, atau dilapisi untuk meningkatkan estetika produk akhir.
3. Bahan yang Digunakan dalam Cetakan Kompresi:
Cetakan kompresi kompatibel dengan berbagai macam bahan, termasuk bahan termoset seperti resin epoksi, karet silikon, dan resin polimer. Secara khusus unggul dengan bahan resin yang diperkuat serat, seperti serat kaca atau komposit serat karbon. Bahan-bahan ini menawarkan performa mekanis yang istimewa, tahan suhu, dan tahan bahan kimia.
4. Keuntungan dan Kerugian dari Cetakan Kompresi:
Keuntungan:
Hemat Biaya: Pencetakan kompresi sering menggunakan bahan termoplastik daur ulang dan bahan dengan titik leleh yang relatif rendah, sehingga mengurangi biaya produksi.
Kisaran Suhu yang Luas: Ini dapat membuat cetakan untuk komponen dengan rentang suhu yang luas dan persyaratan ketahanan kimia yang tinggi.
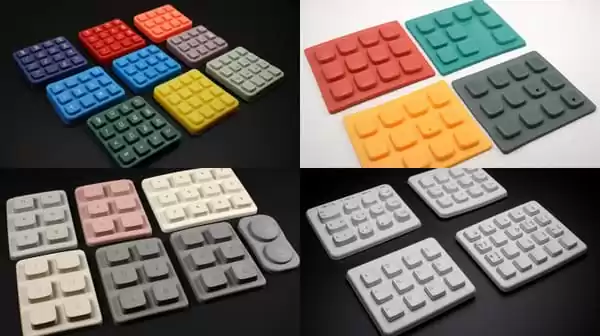
Material Komposit: Ideal untuk bekerja dengan bahan komposit seperti serat kaca dan serat karbon, memungkinkan produksi komponen berkekuatan tinggi dan ringan.
Kekurangan:
Geometri Kompleks: Mungkin tidak cocok untuk memproduksi komponen dengan geometri yang sangat kompleks atau toleransi yang ketat.
Proses yang lebih lambat: Pencetakan kompresi bisa lebih lambat dibandingkan dengan proses pencetakan lainnya seperti pencetakan injeksi, yang dapat memengaruhi laju produksi.
Pada intinya, memahami proses pencetakan kompresi, peran desain cetakan kompresi, keserbagunaan bahan yang digunakan, serta pro dan kontra dari metode ini merupakan dasar untuk memanfaatkan potensinya di berbagai industri. Ini adalah proses yang memadukan presisi, kreativitas, dan rekayasa untuk membentuk bahan mentah menjadi produk yang membuat dunia kita berfungsi.
Bagian 2: Jenis-jenis Cetakan Kompresi
Dalam bidang pencetakan kompresi, jenis cetakan memainkan peran penting dalam menentukan hasil proses. Pilihan cetakan dapat secara signifikan memengaruhi kualitas produk, kompleksitas, dan efisiensi produksi. Mari kita pelajari tiga jenis cetakan utama untuk pencetakan kompresi dan mengungkap karakteristik dan aplikasinya:
1. Cetakan Flash Terbuka:
Karakteristik:
Manajemen Flash: Karakteristik yang menentukan dari cetakan open-flash adalah kelonggaran untuk kelebihan bahan, yang dikenal sebagai "flash", yang keluar selama proses pencetakan kompresi. Flash ini kemudian dipangkas, meninggalkan produk yang diinginkan.
Aplikasi:
Suku Cadang Presisi Rendah: Cetakan open-flash biasanya digunakan ketika presisi bukan merupakan persyaratan penting. Cetakan ini ideal untuk memproduksi komponen yang tidak memerlukan tingkat akurasi dimensi yang tinggi.
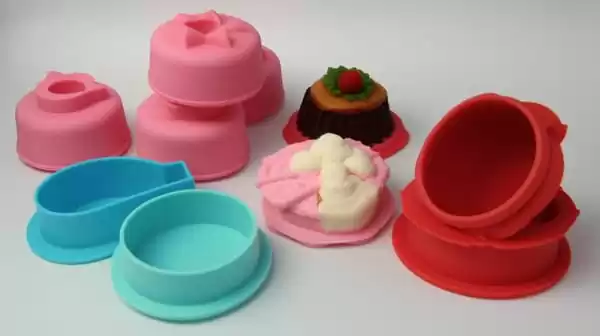
2. Cetakan Tertutup:
Karakteristik:
Presisi: Cetakan tertutup didesain untuk mempertahankan tingkat presisi yang tinggi selama proses pencetakan kompresi. Cetakan ini dirancang untuk meminimalkan flash dan memastikan toleransi yang ketat pada produk akhir.
Aplikasi:
Presisi Kritis: Cetakan tertutup menemukan tempatnya dalam aplikasi yang mengutamakan presisi. Cetakan ini digunakan dalam skenario di mana konsistensi produk dan kepatuhan terhadap toleransi yang ketat tidak dapat dinegosiasikan.
3. Cetakan Semi Tertutup:
Karakteristik:
Pendekatan Hibrida: Cetakan semi tertutup memadukan sejumlah elemen dari cetakan terbuka dan tertutup. Meskipun memungkinkan sebagian kilatan cahaya keluar, namun juga memberikan kontrol atas dimensi bagian.
Aplikasi:
Persyaratan yang Seimbang: Cetakan semi tertutup dipilih apabila ada kebutuhan untuk presisi sedang, dan manajemen flash sangat penting, tetapi tidak sepenting pada cetakan tertutup. Semua ini menawarkan pendekatan seimbang yang sesuai dengan beragam luas persyaratan produk.
Intinya, pilihan antara cetakan terbuka, tertutup, dan semi-tertutup dalam pencetakan kompresi tergantung pada permintaan spesifik dari produk yang diproduksi. Cetakan open-flash cocok jika presisi bukanlah prioritas utama, cetakan tertutup unggul dalam aplikasi yang membutuhkan presisi tertinggi, dan cetakan semi-tertutup menyeimbangkan antara kedua ekstrem ini. Dengan memilih jenis cetakan yang sesuai, produsen dapat mengoptimalkan proses pencetakan kompresi mereka untuk memenuhi kebutuhan unik produk dan industri mereka.
Bagian 3: Jenis Bahan Cetakan Kompresi
Dalam dunia cetakan kompresi, pilihan bahan untuk produk cetakan kompresi sangat penting dalam menentukan sifat dan karakteristik produk akhir. Dua bahan yang umum digunakan dalam proses ini adalah Sheet Molding Compound (SMC) dan Bulk Molding Compound (BMC). Mari kita pelajari bahan-bahan ini dan menjelaskan keuntungan menggunakan bahan termoset dalam pencetakan kompresi:
1. Senyawa Cetakan Lembaran (Sheet Molding Compound/SMC):
Karakteristik:
Diperkuat dengan Serat: SMC adalah bahan yang diperkuat serat yang menggabungkan resin termoseting dengan serat kaca cincang. Penguatan ini memberikan kekuatan dan kekakuan yang sangat baik pada material.
Formulir Lembar: SMC biasanya dipasok dalam bentuk lembaran datar atau gulungan. Lembaran ini telah diresapi sebelumnya dengan resin dan dapat dengan mudah dipotong dan dilapisi di dalam rongga cetakan.
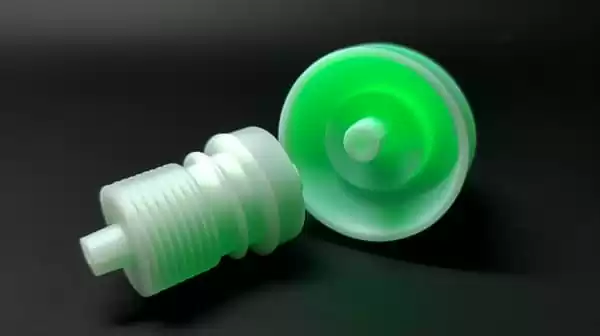
Aplikasi:
Komponen Otomotif: SMC banyak digunakan dalam industri otomotif untuk membuat komponen seperti panel bodi, kap mesin, dan trim eksterior karena kekuatannya yang tinggi, tahan benturan, dan tahan korosi.
Kandang Listrik: Sifat isolasi listriknya membuat SMC menjadi pilihan yang lebih disukai untuk selungkup dan panel listrik.
2. Senyawa Cetakan Massal (BMC):
Karakteristik:
Bahan Termoseting: BMC juga merupakan bahan thermosetting, terdiri dari campuran resin thermosetting, bahan pengisi, dan serat penguat (biasanya kaca).
Bentuk Butiran: Tidak seperti SMC, BMC dipasok dalam bentuk butiran. Konsistensi butiran ini memungkinkan pencetakan bentuk yang rumit secara presisi.
Aplikasi:
Industri Otomotif: BMC mendapatkan tempatnya di industri otomotif untuk memproduksi komponen yang rumit seperti penutup katup, intake manifold, dan komponen di bawah kap mesin. Stabilitas dimensi dan ketahanannya terhadap bahan kimia dan panas menjadikannya pilihan yang ideal.
Listrik dan Elektronik: BMC digunakan dalam aplikasi listrik dan elektronik karena sifat isolasi listrik yang sangat baik dan ketahanan terhadap api.
Keuntungan Menggunakan Bahan Termoset dalam Cetakan Kompresi:
Pilihan bahan termoset, seperti yang digunakan dalam SMC dan BMC, menawarkan sejumlah keuntungan dalam proses pencetakan kompresi:
Tahan Suhu: Bahan termoset unggul dalam lingkungan bersuhu tinggi. Bahan ini dapat menahan suhu tinggi tanpa mengalami perubahan bentuk, sehingga cocok untuk aplikasi yang membutuhkan ketahanan terhadap panas dan siklus termal.
Resistensi Kimia: Bahan-bahan ini menunjukkan ketahanan kimia yang sangat baik, membuatnya ideal untuk aplikasi yang diperkirakan akan terpapar berbagai bahan kimia.
Stabilitas Dimensi: Bahan termoset mempertahankan bentuk dan dimensinya di bawah tekanan dan suhu tinggi, memastikan konsistensi dan presisi pada produk akhir.
Isolasi Listrik: Baik SMC maupun BMC memiliki sifat isolasi listrik yang luar biasa, sehingga sangat diperlukan dalam aplikasi listrik dan elektronik.
Bentuk yang Kompleks: Bentuk granular BMC dan kemampuan layering SMC memungkinkan pencetakan bentuk yang rumit dan rumit, memberikan keserbagunaan dalam desain.
Singkatnya, Senyawa Cetakan Lembaran (SMC) dan Senyawa Cetakan Massal (BMC) adalah contoh bahan termoset yang digunakan dalam pencetakan kompresi. Keunggulan yang melekat pada bahan ini, termasuk ketahanan terhadap suhu dan bahan kimia, stabilitas dimensi, dan sifat insulasi listrik, menjadikannya pilihan yang berharga dalam pembuatan beragam produk di seluruh industri. Pemanfaatan bahan-bahan ini, dikombinasikan dengan ketepatan cetakan kompresimenghasilkan komponen berkualitas tinggi dengan karakteristik dan performa yang disesuaikan.
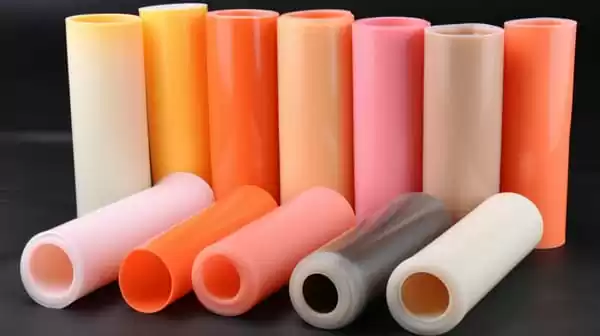
Bagian 4: Proses Pencetakan Kompresi Itu Sendiri
Untuk benar-benar memahami seluk-beluk cetakan kompresi, sangat penting untuk mempelajari inti dari proses itu sendiri. Pada bagian ini, kita akan menjelajahi komponen penting dari cetakan kompresi, memahami pentingnya sifat tekanan tinggi, dan mengungkap proses pengawetan yang bertanggung jawab untuk memantapkan bagian yang dicetak:
1. Komponen Cetakan Kompresi:
Cetakan kompresi adalah jantung dari proses pencetakan kompresi. Cetakan ini terdiri dari beberapa komponen penting:
Rongga cetakan: Di sinilah keajaiban terjadi. Rongga cetakan menentukan bentuk dan dimensi produk akhir. Ini harus dirancang dengan cermat untuk mengakomodasi geometri yang diinginkan, termasuk faktor-faktor seperti ketebalan komponen, sudut rancangan, dan permukaan akhir.
Sistem Pemanas: Cetakan kompresi dilengkapi dengan sistem pemanas yang menaikkan suhu di dalam rongga cetakan. Pemanasan ini sangat penting untuk melembutkan atau melelehkan bahan mentah agar lentur dan mudah dicetak.
Sistem Pendinginan: Saluran atau sistem pendinginan yang efisien mengalir melalui cetakan untuk secara cepat mendinginkan dan memantapkan bagian cetakan setelah terbentuk. Pendinginan yang tepat memastikan pelestarian bentuk yang diinginkan dan mencegah lengkungan atau distorsi.
Mekanisme Tekanan: Cetakan kompresi dikenal karena sifatnya yang bertekanan tinggi. Cetakan ini menggabungkan mekanisme untuk memberikan tekanan yang besar pada rongga cetakan. Tekanan ini bertanggung jawab untuk memadatkan material, memastikan material mengisi setiap sudut dan celah cetakan, dan pada akhirnya menentukan kepadatan dan integritas struktural komponen.
2. Sifat Tekanan Tinggi dari Cetakan Kompresi:
Pencetakan kompresi dicirikan oleh sifat tekanan tinggi yang melekat padanya, yang memainkan peran penting dalam membentuk produk akhir. Signifikansi dari lingkungan bertekanan tinggi ini terletak pada beberapa aspek:
Kompresi Material: Tekanan tinggi yang diterapkan selama pencetakan kompresi memadatkan material di dalam rongga cetakan. Kompresi ini memastikan bahwa material sesuai secara tepat dengan geometri cetakan, sehingga menghasilkan reproduksi bagian yang sangat baik dan akurasi dimensi.
Kontrol Kepadatan: Tekanan menentukan densitas produk akhir. Dengan mengontrol tekanan secara hati-hati, produsen dapat mencapai kepadatan material tertentu, yang memengaruhi sifat mekanik dan kinerja komponen.
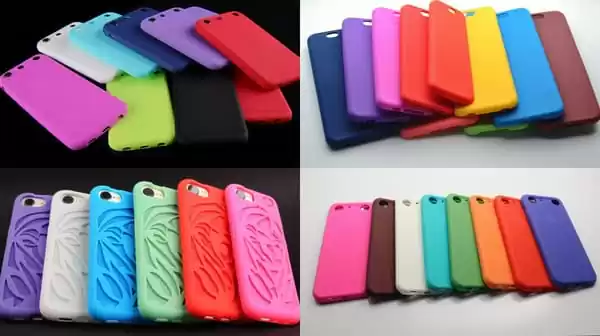
Pengisian Seragam: Tekanan tinggi membantu mengisi rongga cetakan secara seragam. Hal ini meminimalkan risiko rongga, kantong udara, atau cacat lainnya pada produk akhir, yang berkontribusi pada kualitasnya.
3. Proses Pengawetan:
Setelah material mendapatkan bentuk yang diinginkan di dalam rongga cetakan, proses pengawetan mulai dilakukan. Curing adalah langkah yang bertanggung jawab untuk memantapkan bagian yang dicetak dan memberikan integritas struktural akhir. Begini cara kerjanya:
Panas dan Tekanan: Suhu yang meningkat di dalam cetakan, bersama dengan tekanan yang diberikan, memicu reaksi kimia dalam bahan termoseting. Reaksi ini menyebabkan bahan mengeras dan mengatur bentuknya.
Pendinginan: Setelah proses pengawetan selesai, sistem pendingin cetakan diaktifkan untuk menurunkan suhu dengan cepat. Fase pendinginan ini membantu memantapkan bagian, membuatnya kaku dan siap untuk dikeluarkan dari cetakan.
Kesimpulannya, memahami komponen cetakan kompresi, pentingnya lingkungan tekanan tinggi, dan proses pengawetan, memberikan wawasan yang berharga ke dalam mekanisme cetakan kompresi. Interaksi yang rumit antara panas, tekanan, dan rekayasa presisi ini memungkinkan produksi komponen berkualitas tinggi dengan bentuk, densitas, dan sifat mekanis yang diinginkan. Ini adalah perwujudan keunggulan manufaktur, memberikan produk yang memenuhi standar kinerja dan keandalan tertinggi.
Bagian 5: Merancang Rongga Cetakan
Rongga cetakan merupakan inti dari proses pencetakan kompresi. Pada bagian ini, kita akan mengeksplorasi peran penting desain rongga cetakan, menentukan desain cetakan kompresi, dan mempelajari perhitungan tonase-sebuah faktor penting dalam pencetakan kompresi:
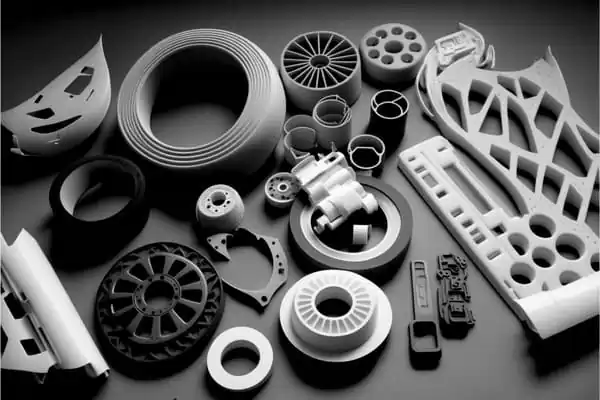
1. Pentingnya Desain Rongga Cetakan:
Desain rongga cetakan adalah yang terpenting dalam memastikan keberhasilan proses pencetakan kompresi. Inilah alasan mengapa hal ini begitu penting:
Presisi dan Konsistensi: Rongga cetakan menentukan bentuk akhir dan dimensi produk. Rongga yang dirancang dengan baik memastikan presisi dan konsistensi pada setiap bagian yang dicetak, memenuhi standar kualitas tertinggi.
Aliran Material: Geometri rongga cetakan menentukan bagaimana material mengalir dan mengisi cetakan. Desain yang tidak tepat dapat menyebabkan distribusi material yang tidak merata, yang mengakibatkan cacat atau ketidakkonsistenan pada produk akhir.
Ventilasi dan Pendinginan: Saluran atau alur ventilasi yang efektif di rongga cetakan memungkinkan udara dan gas yang terperangkap keluar, mencegah cacat seperti kantong udara. Sistem pendinginan di dalam rongga membantu memadatkan komponen dengan cepat, sehingga mengurangi waktu siklus.
Permukaan akhir: Desain rongga cetakan juga berperan dalam mencapai hasil akhir permukaan yang diinginkan pada bagian yang dicetak. Ini dapat dipoles, bertekstur, atau dilapisi untuk memenuhi persyaratan estetika dan fungsional tertentu.
2. Apa itu Desain Cetakan Kompresi?
Desain cetakan kompresi adalah proses menciptakan rongga cetakan secara cermat yang dapat menahan tekanan dan suhu tinggi yang melekat pada cetakan kompresi. Ini mencakup beberapa aspek penting:
Geometri: Rongga cetakan harus secara tepat sesuai dengan bentuk produk akhir yang diinginkan. Hal ini termasuk mempertimbangkan ketebalan komponen, sudut rancangan, dan potongan untuk pengeluaran yang mulus.
Ventilasi: Saluran atau alur ventilasi yang tepat memungkinkan udara dan gas yang terperangkap untuk keluar selama pencetakan, mencegah cacat seperti kantong udara atau lubang pada produk akhir.
Garis Perpisahan: Garis perpisahan menunjukkan di mana cetakan terpisah untuk melepaskan bagian yang dicetak. Garis pemisah harus terdefinisi dengan baik dan tidak mengganggu estetika dan fungsionalitas produk.
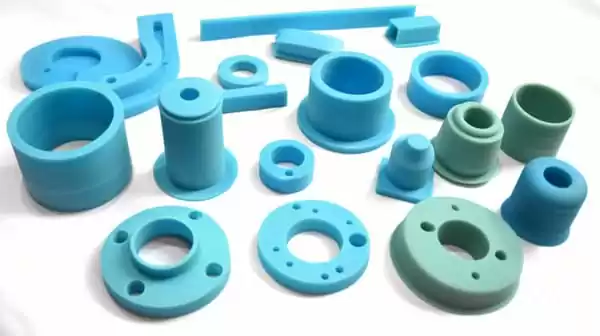
Desain Gerbang: Gerbang berfungsi sebagai titik di mana bahan cair memasuki rongga cetakan. Desain gerbang yang cermat memastikan pengisian yang seragam dan meminimalkan cacat. Jenis gerbang termasuk gerbang tepi, gerbang pin, dan gerbang terowongan.
Sistem Pendinginan: Saluran pendinginan yang efisien di dalam cetakan membantu memantapkan bagian yang dicetak dengan cepat, mencegah lengkungan atau distorsi, dan meningkatkan waktu siklus.
Permukaan akhir: Tergantung pada kebutuhan produk, permukaan akhir rongga cetakan dapat dipoles, bertekstur, atau dilapisi untuk meningkatkan estetika produk akhir.
3. Cara Menghitung Tonase untuk Cetakan Kompresi:
Tonase dalam cetakan kompresi mengacu pada gaya yang diperlukan untuk memampatkan material di dalam rongga cetakan. Ini adalah faktor penting dalam mencapai kompresi material dan kepadatan komponen yang tepat. Untuk menghitung tonase, Anda dapat menggunakan rumus berikut:
Tonase = Tekanan × Luas
Tekanan: Tekanan biasanya diukur dalam PSI (Pound per Square Inch).
Area: Area mewakili area yang diproyeksikan dari bagian yang sedang dicetak.
Dengan menghitung tonase yang diperlukan, produsen dapat memastikan bahwa mesin cetak yang digunakan dalam proses pencetakan kompresi mengerahkan kekuatan yang diperlukan untuk mencapai kompresi dan kepadatan material yang diinginkan di dalam rongga cetakan.
Pada intinya, desain rongga cetakan adalah landasan keberhasilan pencetakan kompresi. Hal ini menentukan kualitas, presisi, dan konsistensi produk. Desain cetakan kompresi mencakup geometri, ventilasi, garis perpisahan, desain gerbang, sistem pendingin, dan permukaan akhir-semuanya disesuaikan untuk memenuhi persyaratan spesifik dari bagian yang diinginkan. Memahami dan menghitung tonase lebih lanjut memastikan bahwa proses pencetakan kompresi beroperasi secara optimal, menghasilkan komponen berkualitas tinggi yang memenuhi atau melampaui standar industri.
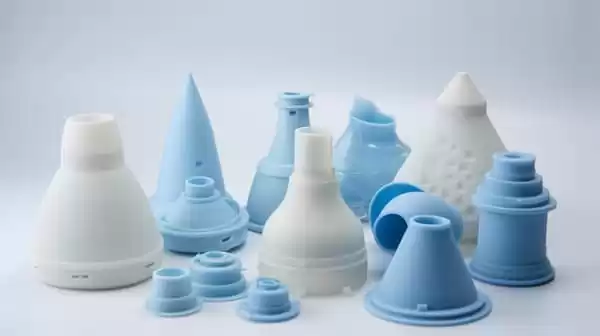
Kesimpulan
Dalam eksplorasi komprehensif mengenai cetakan kompresi dan desain rongga cetakan ini, kami telah menyingkap dunia yang rumit dari proses manufaktur yang meninggalkan jejak yang tidak terhapuskan pada banyak industri.
Setelah kami menyimpulkan eksplorasi kami, kami mendorong para pembaca untuk mempertimbangkan pencetakan kompresi untuk kebutuhan manufaktur mereka. Ketepatan, keserbagunaan, dan kemampuannya untuk menghasilkan komponen berkualitas tinggi menjadikannya sebagai proses yang layak dieksplorasi untuk berbagai aplikasi. Dengan merangkul pencetakan kompresi dan memanfaatkan kekuatan desain rongga cetakan yang tepat, produsen dapat membuka dunia yang penuh dengan kemungkinan, membuat produk yang tidak hanya memenuhi tetapi juga melampaui standar keunggulan tertinggi di bidang manufaktur.