EPDM(EPDMゴム)は、弾力性、耐摩耗性、耐熱性、耐候性、耐オゾン性、耐淡水性、耐海水性に優れた合成ゴムとして、ドアや窓のシール、油圧ブレーキホースやシール、エアコンの換気ダクト、エンジン冷却システムやエアコン冷凍システムのシール、冷却水搬送用ホースなど、自動車用ゴム製品に広く使用されている。
EPDMゴム は非極性の飽和構造である。いわゆる「無極性」、つまりポリマーを構成する分子は内部に極性基を含まない。
いわゆる "飽和"、つまり分子内に二重結合を含まないポリマーの組成である。一般に、ゴムと熱可塑性エラストマーは、「極性」と「非極性」、「飽和」と「不飽和」のいくつかの構造に分けることができる。
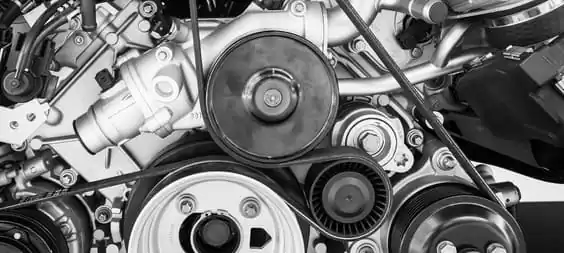
分子そのものが極性基を持つ材料は、一般に「極性」材料である。極性 "構造はポリマーの溶媒に対する耐性を決定し、一般的に類似溶解性の原則に従う。つまり、極性溶媒は極性ポリマーを溶解または膨潤させ、逆もまた同様である。
飽和」構造は、ポリマーの大気老化(酸化)に対する抵抗性に関係している。ポリマー分子が二重結合を含む場合、二重結合は酸化されやすいため、ポリマーは不安定で劣化しやすい。
非極性 "EPDMは、熱水や蒸気、洗剤、有機酸、無機酸、極性溶剤(エタノール、アセトン、エステルなど)、グリコール系ブレーキ液などの極性媒体に耐性がある。
また、鉱物油、ガソリン、動植物油脂、シリコーンオイルなどの非極性媒体には耐性がなく、グリコール系ブレーキ液(SL-DOT4)システム、不凍液を含むエンジン冷却システムに広く使用されている。"飽和 "EPDMとして、オゾンや耐候性に優れ、空気、水などの製造に広く使用されている。
自動車用EPDMの使用温度は一般的に-40℃~120℃です。以下に具体的な使用方法を紹介する。 EPDM製品 自動車に使用される材料、それに対応する材料性能要件、および一般的な故障状況の分析。
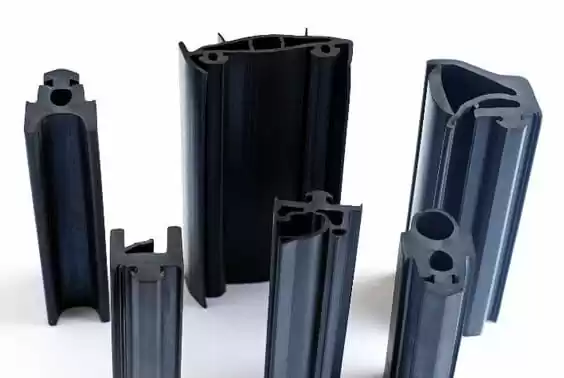
自動車用シール製品への応用
自動車用シールの大部分は、断面が一定で長さが無限の(使用する場合は、必要な長さに応じてインターセプトされる)押出成形装置によって製造されるが、少数の不規則な製品は加硫ダイによって製造される。
押出製品の製造工程は以下の通りである:原料→ゴム混合→複数の材料(硬質ゴム、軟質ゴム、スポンジゴム、着色ゴム、金属骨格、補強ワイヤーなどが含まれる)。
コンパウンド押出→加熱加硫(熱風加硫、加硫槽加硫、マイクロ波加硫、ガラスビーズ沸騰床加硫、塩浴加硫など)→後加工(切断、加硫接合、静電植毛、表面フラッドコーティング、接着など)。
車のフロントガラス、リアガラス、ドア、窓、エンジンルーム、トランクなどに広く使用され、衝撃吸収性、防水性、防塵性、遮音性、装飾性、ドライバーや乗客の保護などの機能を持ち、車体部品間の隙間を埋めるために使用されます。
そのような シリコーンゴム製品 は主に日光、水、オゾンと接触し、-40℃~100℃の温度で使用され、短期耐熱温度は125℃に達することができる。
ゴム製シーリング ストリップの一般的な硬度(Shore A)に使用される EPDM の材料 40 の~選択の間の 90; 引張強さは 7MPa より多くあるべきです; 150% の~ 500% で一般に壊れ目の延長; 圧縮変形(85 の℃、22h)は 45% よりより少しべきです。
引裂強度は5N / m以上でなければなりません。オゾン老化(50pphm、ストレッチ20%、72時間)は亀裂があってはなりません。キセノンランプ老化(キセノンランプ1200機器を使用し、相対湿度80%〜95%、黒板温度55℃〜60℃、1000時間)その引張強さと衰退の伸びは15%を超えることはできません。
そのガラス転移温度(TR)最大-50℃;熱老化試験(100℃、70時間)、その硬度変化は±5であるべきであり、引張強さの変化は±15%であるべきであり、低下の伸びは30%を超えてはならない。
一般的に、自動車用シールの耐用年数は、以下の通りです。 EPDMゴム は10年以上に達します。しかし、実際の生産と応用では、設置後1年経過したドアや窓のシールに、表面のひび割れ、シール性能の低下、表面の曇りなどの不具合現象が発生することもある。
製品テストの表面クラック、そのオゾン耐性テスト20時間後に割れ、標準要件を満たしていない。規格外製品のこのバッチの調査の後、配合ミス (EPDMゴム ゴム・シール面の霜(ブルーム)が原因である。)
原因分析:
(1) 不適切な配合設計。飽和浸水による成分中のイオウイエロー、促進剤、活性剤、酸化防止剤など;無機炭酸カルシウムフィラーのストレス浸水。
(2)ミキシングプロセスの不適切な操作、短すぎる時間、充填剤の不均一な分散、飽和以上のローカルをもたらす。式を変更することにより、混合時間を増加させ、最終的にフラッディングの問題を解決することができます。
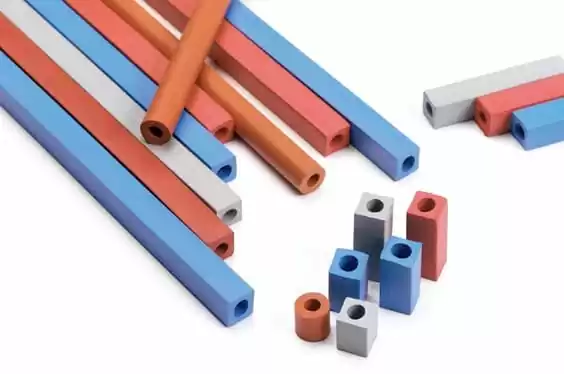
EPDMの油圧ブレーキホースと丸型シールへの応用
EPDMブレーキフルード耐性(DOT3、DOT4、DOT5(シリコーンオイル系))特性を持ち、油圧ブレーキホースのインナーゴム層やブレーキポンプシールの製造に使用される。
これら EPDM製品 は、主媒体ブレーキフルード、-40℃〜120℃の間の温度の使用、および135℃までの短期耐熱温度と接触している。
このような部品はEPDMを使用し、硬度(ショアA)は80である;その引張強さは10.5MPa以上でなければならない;破断伸度は一般的に175%以上である;2.5〜4MPaの固定延長応力の50%の伸び率で;8MPa以上の固定延長応力の100%の伸び率で。
圧縮変形(100 ℃、22 時間)は 40% よりより少しべきである; ガラス転移温度(TR)は最高 -50 ℃である; オゾン老化(50pphm、20% の延長、72h)はひびであってはならない; ブレーキ液体テスト(ブレーキ液体、150 ℃、70h に標本を置く)硬度の変更は 5 であるべきである。
引張強さの変化は±20%、伸びの変化は-15%~20%、体積変化は±20%以内であること。20% の容積変化は ± 5% べきです; 熱テスト(125 ℃、70h)、硬度の変更は ± 5 べきです、引張強さの変更は ± 15% べきです、そして低下の延長は 15% を超過できません。
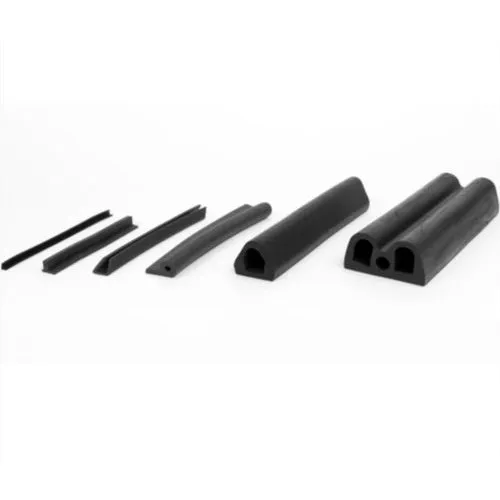
暖房、換気、空調用ホース用途のEPDM
ゴムホースは一般に、内層、中間補強層(化学繊維布または鋼線)、外層の3層で構成される。3層に使用される材料は、実際の要件に応じて選択する必要があります。
内層は供給される媒体の腐食に耐性を持ち、外層は機械的強度を持ち、外部環境に適応していなければならない。
そのため、内側と外側のゴムはゴムでないことが多い。EPDMは、空気、水、オゾン、日光の老化に対する優れた耐性と低温柔軟性を持つ材料であるため、ゴム層の内側と外側の暖房および換気ホース、および外側のゴム層のエアコンホースに広く使用されています。
このようなEPDMを使用した部品は、硬度(ショアA)が70、引張強さが10.5MPa以上、破断伸びが一般的に300%以上、圧縮残留変形(100℃、22時間)が40%以下でなければならない;
そのガラス転移温度(TR)最大-45℃;オゾン老化(50pphm、20%を伸ばし、72時間)はクラックがあってはならない;IRM902油試験(IRM902油に試料を入れ、100℃、70時間)硬度低下最大15、引張強度低下最大30%。
引裂強度の低下は最大30%、体積変化は80%以内であるべきである。熱老化試験(125℃、70時間)、硬度の変化は±5であるべきで、引張強度の変化は±15%であるべきで、伸びの低下は40%を超えることはできない。
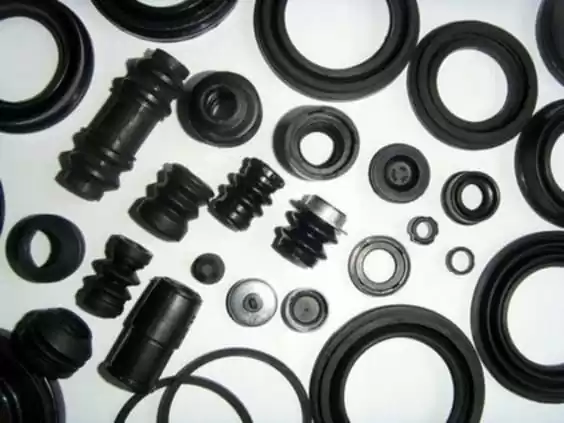
ベルトを引っ張るアプリケーションのEPDM
この種の部品は、主にホイールカバー、バッテリーボックスカバーの締結などの間の接続に使用され、プロセスの使用中に、高い動的および機械的負荷に耐えることができ、常に緊張状態にある。
これら シリコーンゴム製品 は主に日光、水、オゾンにさらされ、-40℃~85℃の温度で使用され、短期耐熱温度は100℃に達することができる。
このような部品を作るために使用されるEPDM材料は、硬度(ショアA)は、一般的に60〜80である;その引張強さは14MPa以上でなければなりません;破断伸度は、一般的に200%〜400%である;引裂強度は7N / m以上でなければなりません;
圧縮残留変形(85℃、22時間)は45%以下、圧縮残留変形(-20℃、22時間)は45%以下、耐オゾン老化(50pphm、20%の延伸、72時間)は亀裂がないこと;キセノンランプ老化(キセノンランプ1200機器を使用し、相対湿度80%〜95%、黒板温度55℃〜60℃、1000時間)引張強さと衰退の伸びは15%を超えてはならない;
そのガラス転移温度(TR)最大-50℃;熱老化試験(100℃、70h)、その硬度変化は±75、引張強さの変化は±15%、伸びの減少は40%を超えてはならない。
バッテリーカバーのストラップの破断とホイールガードのストラップの表面の亀裂は、半年間の負荷の後に生成された。 製品の引張強さ、引裂強さ、オゾン老化試験の失敗の後、実際に達成された結果は、引張強さ8.5MPa、引裂強さ5N / m、オゾン老化42時間の亀裂であり、標準的な要件に達していない。
ゴム式の重要性にテープを引っ張るの個々のメーカーは、EPDMゴムがテープを引っ張るゴムで作られている限り、実際には、異なる製剤のため、製品の性能が大きく異なる場合があることができることを、十分な理解ではありません。
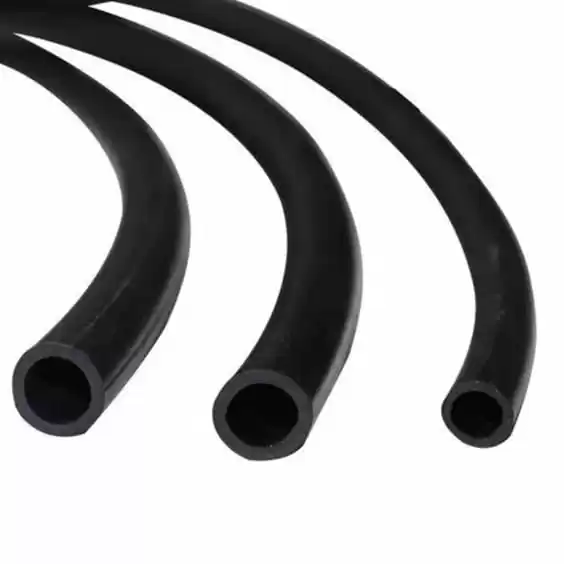
エンジン冷却システムおよび空調・冷凍システムシールへのEPDMの応用
EPDMは、エンジン冷却システムのシールを作るために使用されます。これらの製品は、媒体と接触している不凍液、日光、水、オゾン、-40℃〜125℃の温度の使用、および135℃までの短期耐熱温度である。
このようなEPDMを使用した部品は、60〜80の硬度(ショアA)(冷凍システムのラウンドシールのアプリケーションのための75);その引張強さは10以上でなければなりません。5MPa;破断伸度は一般的に175%以上;1~2MPaの固定伸長応力の50%の伸長率;2~5MPa以上の固定伸長応力の100%の伸長率;収縮変形(150℃、22時間)は20%以下でなければならない;
135℃(22時間)までの耐熱温度は20%以下であること;ガラス転移温度(TR)は最大-50℃であること;耐オゾン老化性(50pphm、20%を延伸、72時間)は亀裂がないこと;
エンジン冷却システムに使用されるシールについては、冷媒試験(試験片を不凍液中に入れ、150℃、166h、試験圧力約0.4MPa)を行い、硬さの変化を±5、引張強さの変化を±20%、破断伸びの変化を-15%~20%、体積の変化を±5%とする;
空調システムに使用されるシールの場合、冷媒試験を実施しなければならない(試験片をP試験(PAG、ND8冷媒に入れ、100℃、70h)硬度変化±5以内、引張強さ変化±20%以内、破断伸び変化-15%~20%以内、体積変化±5%以内;熱老化テスト(150 ℃、70h)、硬度の変化は± 5であるべき、引張強さの低下は10%未満であるべき、伸びの低下は10%を超えることはできません。
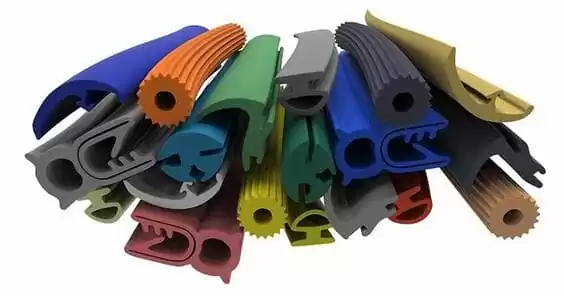
クーラントホースの用途におけるEPDM
EPDMは、エンジンウォーターホースの製造に使用され、その内側と外側のゴム層はEPDM材料で作られています。このような EPDM製品 媒体と接触して不凍液、日光、水、オゾン、-40℃〜125℃の温度の使用であり、短期耐熱温度は150℃に達することができる。
このような部品は、硬度(ショアA)65のEPDMを使用し、その引張強さは10.5MPa以上でなければなりません;300%以上の破断伸度;1〜2MPaの固定延伸応力の50%の伸び率で、2〜4.5MPa以上の固定延伸応力の100%の伸び率;圧縮残留変形(100℃、22時間)は20%未満でなければなりません;
そのガラス転移温度(TR)の最大-50℃;オゾン老化(50pphm、20%を伸ばし、72時間)は亀裂があってはならない;冷却水試験(不凍液、150℃、166時間、約0.4MPaの試験圧力に置かれた試験片)。
硬さの変化は±5、引張強さの変化は±20%、破断伸度の変化は-15%~20%、体積変化は±5%であるべきである。熱老化テスト(150 ℃、70 時間)、硬度の変化は ± 5 であるべきであり、引張強さは 10% よりより少しであるべきであり、低下の延長は 10% を超過するべきではない。