熱硬化性液状シリコーンゴム(LSR)射出成形用金型の構造は、一般的に熱可塑性コンパウンド用の金型と似ているが、いくつかの大きな違いがある。
例えば、LSRコンパウンドは一般に粘度が低いため、非常に低い射出圧力でも充填時間が非常に短くなる。空気の滞留を避けるためには、金型内に優れた空気抜き装置を設置することが不可欠です。
また、LSRコンパウンドは熱可塑性コンパウンドほど金型内で収縮せず、高温時には膨張し、低温時にはわずかに収縮する傾向がある。その結果、製品は金型の凸面に期待通りに留まるとは限らず、表面積の大きいキャビティに保持される。
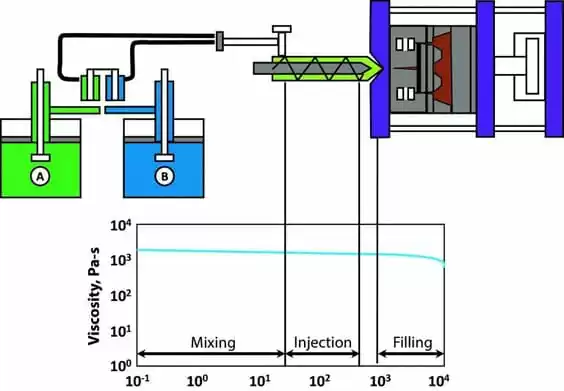
1.収縮率
LSRは金型内では収縮しないが、脱型・冷却後に2.5%~3%収縮することが多い。収縮の正確な量は、そのコンパウンドの配合にある程度依存する。
しかし、金型の観点から見ると、収縮率は、金型の温度、脱型時のコンパウンドの温度、金型キャビティ内の圧力、その後のコンパウンドの圧縮など、いくつかの要因によって影響を受ける可能性がある。
通常、接着剤の流れ方向の収縮は、接着剤の流れに垂直な方向の収縮よりも大きいため、注入点の位置も考慮する価値がある。
製品の大きさも収縮率に影響し、一般的に厚い製品の方が薄い製品よりも収縮率が小さくなります。二次加硫が必要な場合、収縮率はさらに0.5%~0.7%になることがあります。
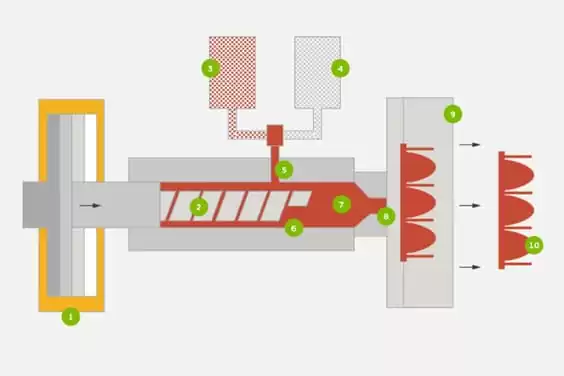
2.パーティングライン
パーティングラインの位置を決定することは、設計における最初の数ステップのひとつである。 シリコーンゴム射出成形金型.ガス抜きは、主にパーティングライン上にある溝を使って行われる。これは、内部の気泡を避け、接着剤の接合部の強度低下を抑えるのに役立ちます。
LSRは粘度が低いため、パーティングラインは流出を避けるために正確でなければなりません。それでも、成形品にパーティングラインが見られることはよくあります。離型性は、部品の形状とパーティング面の位置に影響されます。パーツをわずかに面取りして設計することで、希望するもう半分のパーツの親和性を一定に保つことができます。 射出成形金型 キャビティ
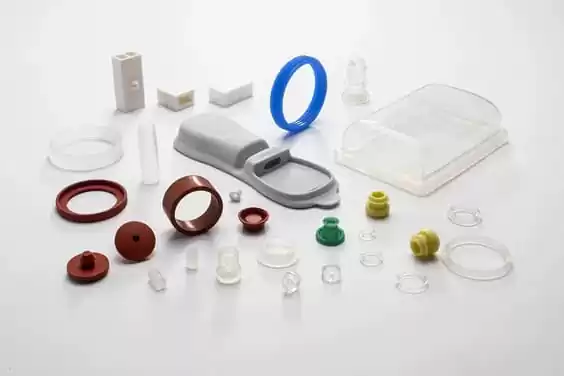
3.排気
LSRが注入されると、キャビティに閉じ込められた空気は金型が閉じるときに圧縮され、金型が充填されるときに通気溝を通って排出される。
空気が完全に排出されないと、空気が接着剤に閉じ込められます(その結果、製品の一部が白く縁取られることがよくあります)。通気溝の幅は一般的にmm-3mm、深さは0.004mm-0.005mmです。
金型内を真空にすることで、最良のベント効果を得ることができる。これは、パーティングラインにガスケットを設計し、真空ポンプですべてのキャビティを素早く真空にすることで達成されます。真空度が定格レベルに達すると、金型は完全に閉じられ、射出プレスが開始されます。
射出成形機の中には、型閉め力を変化させることができるものがあります。この場合、キャビティの90~95%がLSRで充填されるまで(空気が抜けやすくなるまで)低圧で型閉めし、その後、型閉め力が高くなるのを防ぐために型閉め力を高くすることができます。 シリコーンゴム 膨張とオーバーフロー。
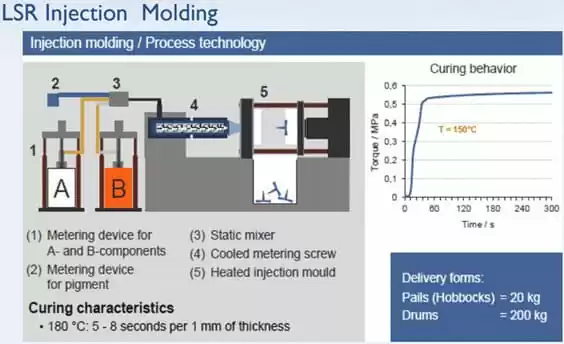
4.注入ポイント
LSRの成形にはコールドランナーシステムが使用される。その利点は シリコーンゴム を最大化し、生産効率を最大限に高めることができる。
このように製品を加工することで、射出チャンネルを取り外す必要がないため、作業労力の増加や、場合によっては大量の材料廃棄を避けることができる。多くの場合、レーンフリー構造は作業時間も短縮する。
射出ノズルはニードルバルブで制御され、ポジティブフローを実現する。現在、多くのメーカーが空気圧スイッチ付きのノズルを標準装備しており、金型のさまざまな部分に設置することができる。
一部 射出成形金型 メーカーは、複数の射出ポイント(ひいてはキャビティ全体)を非常に限られた金型スペースに設定しなければならないほど小型のオープンコールドランナーシステムを開発した。
この技術は、高品質の製品を大量に生産することを可能にする。 シリコーンゴム製品 インジェクションポートを分離する必要がない。
コールド・ランナー・システムを使用する場合、ホット・キャビティとコールド・ランナーの間に効果的な温度分離を作ることが重要である。ランナーの温度が高すぎると、ゴムは射出される前に加硫し始める可能性がある。しかし、ランナーが急速に冷えすぎると、射出される前にゴムがスプルー部から熱を吸収しすぎてしまいます。 射出成形金型その結果、加硫が不完全になる。
従来のスプルー(浸漬型スプルーや円錐型スプルーなど)で射出する製品の場合、射出には小径の射出口(通常0.2mm~0.5mm)を使用するのが適切である。
低粘度のLSRコンパウンドでは、熱可塑性コンパウンドと同様に、すべてのキャビティにコンパウンドが均一に充填されるようにランナーシステムのバランスをとることが重要です。ランナーシステムを設計するためのシミュレーションソフトウェアは、金型の開発を大幅に簡素化し、金型充填試験でその有効性を証明することができます。
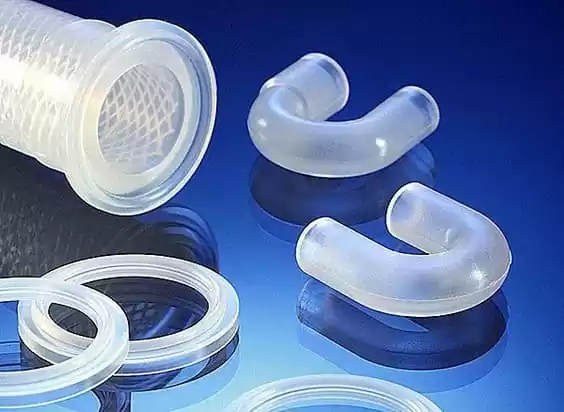
5.脱型
液状シリコーン成形品は、加硫により金属表面に付着する傾向があり、製品の柔軟性により離型が困難になることがあります。LSRは高温引裂強度があるため、通常の条件下では大きな製品でも破損することなく離型することができます。
最も一般的な離型技術には、ストリッパープレート離型、ストリッパーピン離型、空気圧離型がある。その他の一般的な技法としては、ローラー掻取り、輸出プレート離型、自動離型がある。
リリースシステムを使用する場合、高い精度の範囲内に収めることが重要です。トップ・プッシュ・ピンとガイド・ピン・スリーブとのクリアランスが大きすぎたり、経年劣化により部品間の隙間が大きくなると、接着剤がこぼれることがあります。
逆円錐形またはマッシュルーム形のトッププッシュピンは、より大きな接触圧を加えることができ、シール目的の向上を容易にするため、非常に効果的である。
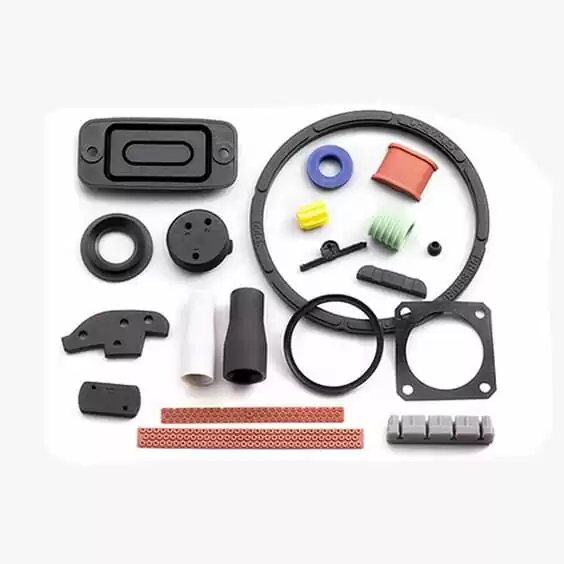
6.金型材料
金型パレットは非合金工具鋼(no.1.1730、DINコードC45W)で作られることが多い。170℃~210℃の高温に耐える必要がある金型用パレットには、耐衝撃性を考慮してプリテンパー鋼(No.1.2312、DINコード40 CrMn-M oS 8 6)を使用する。
金型キャビティのあるモールドパレットは、耐高温性を確保するため、窒化処理または焼戻し熱処理を施したエチル工具鋼を使用する。
耐油グレードのLSRのような充填量の多いLSRの場合、金型の製造には、光沢クロムメッキ鋼やこの目的のために特別に開発された粉末金属(No.1.2379、DINcode X 155 CrVMo121)のような、より硬い材料を使用することをお勧めします。
設計時 射出成形金型 高摩耗材料の場合、高摩擦を受ける部品は、金型全体を交換する必要がないように、交換可能な方法で形成されるように設計されるべきである。
金型キャビティの内面は、製品の仕上がりに大きな影響を与える。最も明らかなのは、成形された製品がキャビティの表面に完全に一致することです。 射出成形金型 透明な製品の場合、研磨されたスチール製が望ましい。表面処理されたチン/ニッケル鋼は耐摩耗性に優れ、PTFE/ニッケルは離型を容易にする。
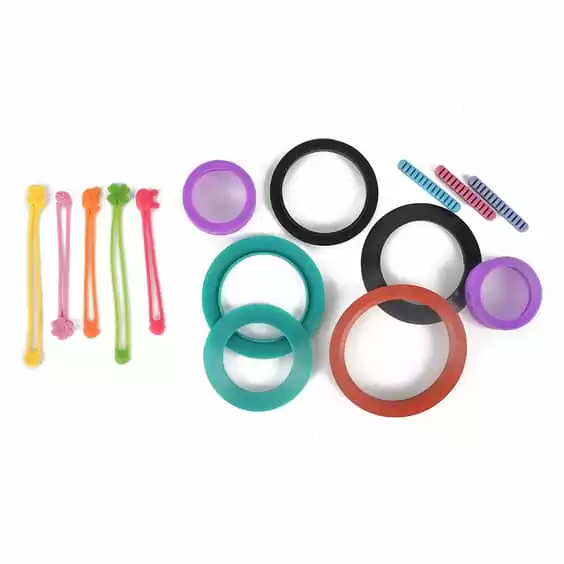
7.温度制御
一般的に、LSRの成形は電気加熱、通常はバンドヒーター、カートリッジヒーター、または加熱プレートによって加熱することが好ましい。
重要なのは、LSRの均一な硬化を促進するために、温度フィールドを金型全体に均等に分布させることです。大きな金型では、油温制御加熱をプッシュする場合、費用対効果の高い加熱方法です。
金型を断熱板で包むと熱損失が少なくなる。熱間金型のどこかが不適当であると、工程間の温度変動が大きくなったり、エア上がりを起こしたりすることがある。
表面温度が下がり過ぎると、接着剤の硬化速度が遅くなり、多くの場合、製品が 射出成形金型 そして品質問題を引き起こす。
テンプレートが曲がって変形し、完成品にはみ出し糊バリができるのを防ぐため、ヒーターとパーティングラインの間に一定の距離を保つ必要があります。金型がコールド・ランナー方式で設計されている場合は、ホット・エンドとコールド・エンドを完全に分離する必要があります。
特殊チン合金(例えば3.7165[TiA16V4])は、他の鋼に比べて熱伝導率が非常に低いため、使用することができます。一体型射出成形金型加熱システムの場合、熱損失を最小限に抑えるために、遮熱板を金型と金型パレットの間に設置する必要があります。適切な設計と構想は、金型が非常に重要であるLSR射出成形を確実にすることができます。
上記の金型設計の原則は、金型キャビティにゴムを充填し、硬化時間を短縮し、完成品の優れた品質と高い歩留まりを達成することを目的としており、その結果、液状ゴムを提供する。 シリコーンゴム成形 経済効果の高い加工業者。