はじめに
これらの複雑な装置は、手動で操作されるものから完全に自動化されたものまであり、それぞれが正確かつ効果的に明確な産業要件を満たすために細心の注意を払って作られている。進化 分注工程技術 は、デジタル化された制御システム、綿密な計量、洗練されたフィードバックループなどの進歩をもたらし、均一で正確なシリコーン塗布を保証している。このような技術的進歩により、ディスペンサーシステムの能力が向上し、多様な材料を管理することができるようになり、電子機器におけるジアファナスシリコーン層の塗布から、自動車部品のシーリングのための大量塗布まで、幅広い用途に対応できるようになりました。

シリコーンの配分の領域を掘り下げるには、単に手順的な領域だけでなく、現代の製造業の風景に大きな影響を与えるという点で、その極めて重要な役割を認識することが不可欠である。効率的かつ正確にシリコンを割り当てる能力は、製造の単なるステップを超越したものであり、現代の産業界の厳しい基準に適合する、高水準で永続的な製品を構想し、製造するための基本的な要素なのである。
シリコーン製品の塗布工程:
シリコーン接着剤塗布は シリコーン加工技術.シリコーン工場Bezhitシリコーン技術者から、我々は、シリコーン接着剤とディスペンシングシステムは現在、接着剤の調剤の2つの方法に分かれていることを学んだ、一方は手動であり、他方は自動機械である。エポキシ接着剤に使用される原料は液体シリコーン材料であり、その実装は塗装に多少似ている。それは非常に興味深いシリコーンの加工技術である。シリコーンの分配は分配機械か手によって達成することができる。
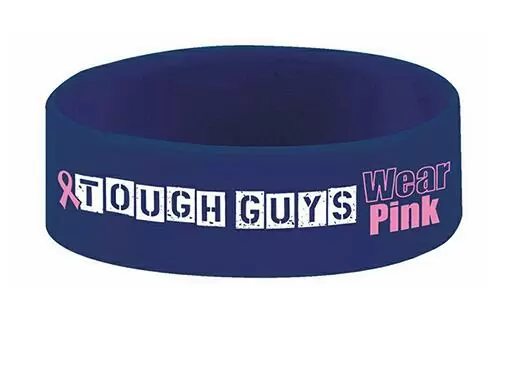
シリコーンの原料は液状である。原料をシリンジに入れる。その原料を空気圧や手作業で金型に落とし、加熱・加硫して成形する。この工程は手作業で人手がかかるため、生産能力は高くない。1つの製品に複数の色を必要に応じて滴下できるという特徴があるため、この製法は主に高級シリコーン製品に使用される。例えば マルチカラーシリコンブレスレットシリコーンのびんカバー、漫画のシリコーンの袋、ハウジング カバー。
高級シリコンギフトなど
シリコーン製品の接着剤塗布工程の詳細紹介
シリコーン製品の接着剤塗布工程で使用される材料は、エポキシ樹脂と硬化剤を混合し、シリコーンボタンの表面に滴下する。一定時間放置すると、エポキシ樹脂と硬化剤が結晶のように乾燥する。シリコーン製品を美しく仕上げるだけでなく、シリコーン製品の表面を傷から守ることができます。
製造工程 シリコーン製品の接着剤滴下工程 は、まず高純度のエポキシ樹脂と硬化剤を一定の割合で用意し、それを接着剤滴下槽に入れるのが一般的だ。接着剤滴下槽を使って、シリコーンボタンの表面に一定量の接着剤を滴下することができます。エポキシ樹脂を塗布し、接着したシリコーン製品を完全に固定するまで約12時間置き(オーブンに入れると完全に固定でき、時間を短縮できる、オーブンの温度は60~70度)、シリコーン製品まで待つ。 固定が完了したら、接着剤塗布工程を終了する!
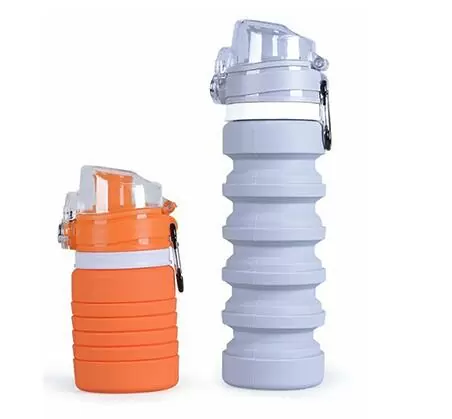
まとめると、シリコーン製品の接着剤塗布工程は、シリコーン製品の製造において重要な部分である。それは、以下のことを達成することができます。 結晶様シリコーン製品 シリコーン製品の接着剤塗布工程では、エポキシ樹脂を入れすぎないこと。ただし、シリコーン製品の接着剤塗布工程では、エポキシ樹脂を入れすぎないようにし、オーブンの温度も高くしすぎないようにします。シリコーン製品に欠陥が生じたり、製品に損失が生じたりするのを避けるために、エポキシ樹脂を使用することをお勧めします。 シリコーン製品工場.
接着剤塗布工程でシリコーン製品を使用する際に注意すべきこと
接着剤塗布工程がシリコーン製品にもたらすメリットは、製品表面を磨耗から守るだけでなく、高品質・精緻な外観を追求することである。一片の製品を黄金色に輝く半透明の外観に仕上げることは難しくない。次のことをしなさい ちょうど数時。
1.接着剤ディスペンス硬化後の表面に不純物、波紋、ピッティングやその他の欠陥を避けるために、接着剤ディスペンス工程中にすべての機器がきれいであることを確認してください。
2.接着剤の割合を正確に計量し、接着剤を均等に撹拌する必要があり、そうでなければ、接着剤の不完全な硬化を引き起こし、硬化するのに長い時間がかかります。
3.接着剤塗布作業環境の湿度は68%内で管理してください。空気湿度が高すぎると、空気中の霧が直接接着剤表面の酸化を引き起こすため、それは、雨の日に接着剤の塗布作業を実行することはお勧めしません。それは、タイトな生産作業の下で空気除湿を使用することをお勧めします。
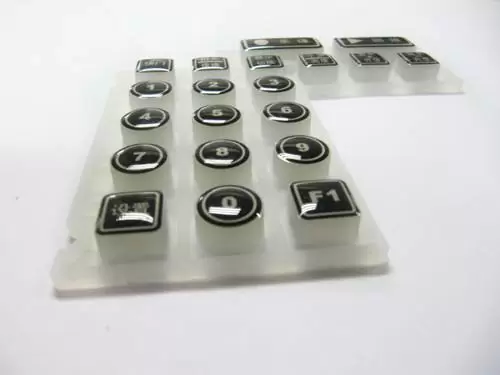
4.接着剤塗布効果の厳しいシリコーン製品は、乾燥させる場所に集中させ、温度は28~40°の間で管理する。
シリコーン塗布プロセスのメカニズム
調剤の基本原則:
シリコーンの分注プロセスは、精度とコントロールが要求される細心の手順です。その中核となるのは、シリコーンを特定の場所や表面に正確に供給する方法です。この工程は、指定されたパターン、厚さ、量を守って正しい量のシリコーンが吐出されるように、精密な制御機構によって管理されています。このプロセスの精度は、最終製品の品質と性能に直接影響するため、最も重要です。
精度 シリコーン分注 は、量だけでなく、シリコーン材料の配置と一貫性についても重要です。これは、シリコーンがシーラントや接着剤として機能する用途では特に重要で、最適な性能を発揮するためには、均一で途切れのない層が不可欠です。電子機器や航空宇宙産業のような製造分野では、部品が非常に繊細であるため、シリコーンの精度は非常に重要です。 シリコーン分注 が成功する製品と失敗する製品の分かれ目になる。
ディスペンシング・システムの種類
業界では、さまざまなニーズに対応するため、さまざまなディスペンシングシステムが採用されている。最も一般的なのは空気圧システムです。これらのシステムは、圧縮空気を使用してシリコーンに圧力をかけ、吐出ノズルからシリコーンを押し出します。シンプルで信頼性が高く、制御が簡単なため、幅広い用途に適しています。
しかし、ディスペンシング・システムの範囲は、空気圧式ソリューションにとどまらない。高度なシステムには、自動制御により高精度を提供するロボット式ディスペンサーが含まれます。これらのロボットシステムはプログラム可能で、複雑な塗布パターンを高い再現性で実行できるため、大規模生産や複雑な塗布設計を必要とするアプリケーションに最適です。
これらのディスペンシング・システムにおける技術の役割は不可欠である。現代の進歩は、より洗練された制御メカニズムの開発につながった。例えば、現在ではセンサーやフィードバックループを組み込んだシステムもあり、粘度の変化や温度変化などの要因に対応しながら、分注プロセスをリアルタイムで調整できるようになっています。このような技術統合は、ディスペンシングプロセスの精度を高めるだけでなく、その効率性と適応性を高め、様々な業界の進化する要求に応えています。
結論として、シリコーン・ディスペンシング・プロセスの力学は、理路整然とした制御と高度なシステムに支えられ、現代の製造業に求められる高い水準を維持する上で極めて重要である。これらのシステムにおける継続的な技術強化は、プロセスを合理化するだけでなく、シリコーンディスペンシングで達成できることの可能性を拡大します。
シリコーン分注の主要部品と材料
敏感な部品とその保護:
シリコーンディスペンサーは、特にエレクトロニクス産業やその他の高精度デバイス製造において、繊細な部品の保護に極めて重要な役割を果たしています。これらの部品は、湿気、ほこり、温度変化などの環境要因によるダメージを受けやすく、長寿命と機能性を確保するために強固な保護が必要です。シリコーンは、その卓越した密封性とコンフォーマルコーティングによる絶縁特性により、この目的に理想的な材料です。
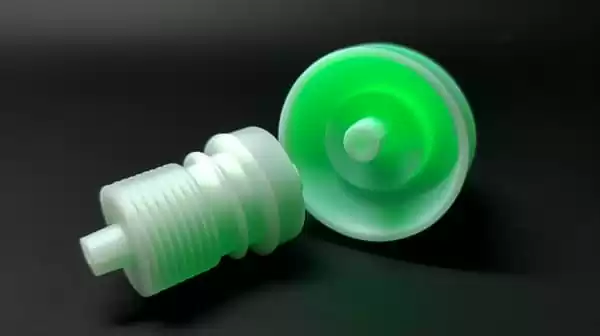
精密なパターンと厚さでシリコーンを塗布し、繊細な部品の上に保護層を形成することができます。例えば、電子機器では、回路基板を湿気や電気的干渉から保護するために、シリコーンの薄い層が使用されます。このカプセル化は、部品を保護するだけでなく、熱安定性を提供し、過熱のリスクを低減することにより、その性能を維持します。
センサーや医療機器のような他のデバイスでは、シリコーン塗布は、コンポーネントが機能的で応答性を維持することを保証しながら、外部汚染物質に対する障壁を作成するために使用されます。このような用途では、シリコーンを正確かつ一貫して塗布する能力が、保護層の有効性と信頼性に直接影響するため、非常に重要です。
使用される材料と化学物質:
シリコーン・ディスペンシング・プロセスでは、それぞれの特性と用途に合わせて選択されたさまざまな材料を使用します。シリコーンは、その汎用性、耐久性、過酷な条件への耐性が評価され、主要な材料となっています。しかし、このプロセスには、純粋なシリコーン以外の材料が使用されることも多い。用途によっては、樹脂や充填剤などの他の材料を加えてシリコーンの特性を変更することもあります。
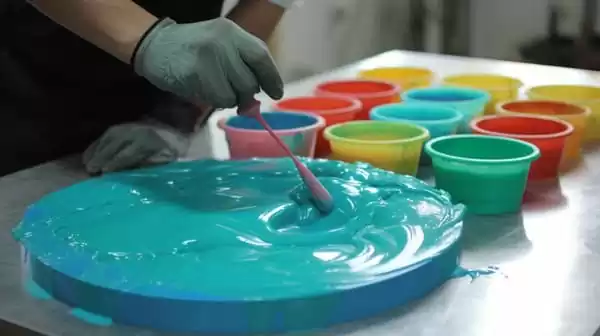
例えば、樹脂はシリコーンに混ぜて接着性を高めたり、粘度を変化させて塗布しやすくしたりすることができる。一方、充填剤はシリコーンを強化し、強度や熱伝導性を向上させるために使用されます。これらの添加剤は、さまざまな用途の特定の要件を満たすためにシリコーンを調整する上で重要な役割を果たしています。
これらの材料の硬化プロセスは、シリコーンディスペンサーのもう一つの重要な側面です。硬化とは、シリコーン混合物が硬化し、最終的な特性を得るまでの化学的プロセスを指します。このプロセスは、熱の印加、空気や湿気への暴露、化学触媒など、さまざまな手段によって開始または促進することができます。硬化方法の選択は、プロセスの所望の速度、シリコーン混合物の特性、およびアプリケーションの仕様などの要因によって異なります。
要約すると、シリコーンディスペンシングプロセスで使用される材料と化学薬品は、プロセスそのものと同じくらい重要です。シリコーン、樹脂、フィラー、硬化方法を適切に組み合わせることで、最終製品の性能と耐久性を大幅に向上させることができ、繊細な部品を適切に保護し、その寿命にわたって機能させることができます。
高度なテクニックと課題
技術の進歩:
近年、シリコーン・ディスペンシング技術の進歩は目覚ましく、このプロセスの効率と能力は大きく変化している。重要な進歩のひとつは、制御システムの改良です。これらの洗練されたシステムは現在、ディスペンス工程においてより高い精度を提供し、より複雑なパターンや一貫した塗布を可能にしています。この精度は、わずかなズレが製品の不具合につながる可能性のある業界では極めて重要です。
もうひとつの大きな進歩は、真空分注技術の登場である。真空ディスペンスは、ディスペンス工程中の気泡除去に特に効果的であり、高純度と均一性が要求される用途には不可欠です。この方法は、シリコーン中の気泡が繊細な部品の絶縁や保護を損なう可能性のあるエレクトロニクス産業において特に有益です。
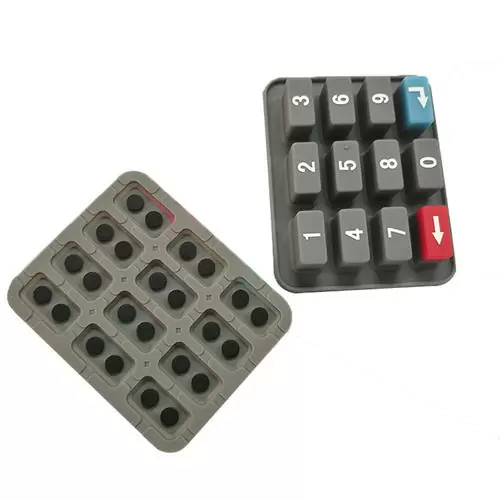
自動化もまた、ディスペンシング技術の進歩に重要な役割を果たしてきた。自動化されたディスペンシングシステムは生産ラインに組み込むことができるようになり、スループットや一貫性を高めると同時に、人件費や人的ミスを減らすことができるようになりました。これらのシステムにはセンサーやフィードバック機構が装備されていることが多く、リアルタイムでの調整が可能で、分注プロセス全体を通して高い精度を確保することができます。
課題に取り組む
こうした技術の進歩にもかかわらず シリコーン分注工程 はいくつかの課題に直面している。最も一般的なものの一つは、シリコーンの粘度への対応である。粘度は配合や温度によって大きく変化し、材料の流れや塗布に影響を与えます。これを管理するには、粘度の変化に対応してリアルタイムでディスペンスパラメーターを調整できる高度な制御システムが必要です。
温度による影響も課題となる。シリコーンの特性は温度変化に応じて変化し、硬化時間や接着性に影響を与えます。これは、温度が変動する環境や、シリコーンを素早く硬化させなければならない用途では、特に難しい問題です。先進のディスペンシングシステムには、このような問題を軽減するための温度制御メカニズムが搭載され、外部の温度条件に関係なく、一貫した塗布と硬化が保証されるようになりました。
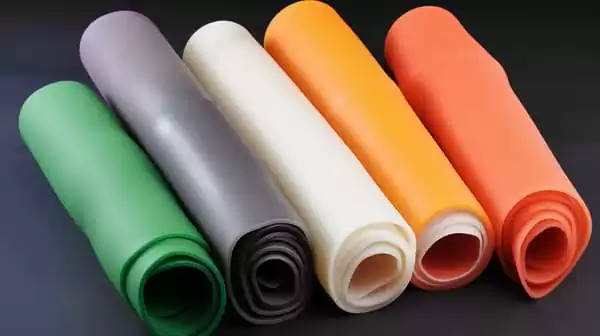
要約すると シリコーン塗布技術 はプロセスを合理化し、強化したが、内在する課題への対処は依然として極めて重要である。これらの課題を克服するには、技術革新、正確な制御、材料特性と環境要因の深い理解の組み合わせが必要です。技術が進化し続けることで、さまざまな産業におけるシリコーンの応用に新たな可能性が生まれ、現代の製造工程におけるシリコーンの役割がさらに確固たるものとなっていく。
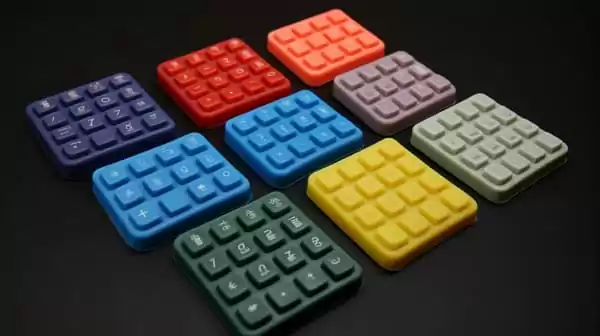
結論
将来に向けて シリコーン分注工程 は、今後も進化を続け、産業用途におけるその役割を拡大していきます。現在進行中の技術革新により、より精密で効率的、そして多用途なディスペンシングシステムの可能性は計り知れません。この進化により、新たな用途が開拓され、既存の製造工程が改善される可能性が高く、産業界におけるシリコーンディスペンサーの重要性が高まっています。
産業が進歩し続け、より洗練された製造ソリューションが求められる中、シリコーン・ディスペンシング・プロセスは間違いなく最前線に立ち続け、変化し続ける現代の製造業のニーズに適応し、革新していくでしょう。シリコーン・ディスペンシングの未来は、精密性、効率性、多用途性においてさらなる飛躍を遂げ、産業革新の原動力となることが期待されています。