Introduction
These intricate apparatuses span from the manually operated to the wholly automated, each meticulously crafted to fulfill distinct industrial requisites with accuracy and efficacy. The evolution of dispensing processes technology has ushered in advancements such as digitized control systems, meticulous metering, and sophisticated feedback loops, guaranteeing uniform and precise silicone application. This technological progression has augmented the dispensing systems’ capabilities, empowering them to manage diverse materials and cater to an extensive range of implementations, from the application of diaphanous silicone layers in electronic apparatuses to the allocation of more substantial amounts for automotive component sealing.

In delving into the realm of silicone allocation, it’s imperative to acknowledge its pivotal role not just in the procedural domain but also in its expansive influence on the landscape of modern manufacturing. The capacity to allocate silicone with both efficiency and accuracy transcends a mere step in manufacturing; it represents a fundamental element in the conception and fabrication of high-caliber, enduring products that conform to the stringent criteria of contemporary industrial spheres.
Silicone products dispensing process:
Silicone glue dispensing is a silicone processing technology. From the silicone factory Bezhit silicone technicians, we learned that silicone glue and dispensing system is now divided into two methods of glue dispensing, one is manual and the other is automatic machine . The raw material used in epoxy glue is liquid silicone material, and their implementation is somewhat similar to painting. It is a very interesting silicone processing technology. Silicone dispensing can be achieved by dispensing machine or by hand.
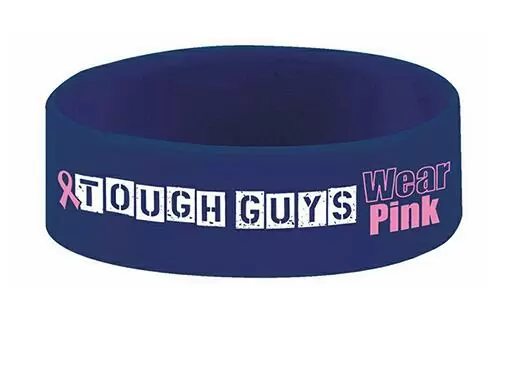
The raw material of silicone is in liquid state. The raw material is placed in the syringe. The raw material is dropped onto the mold using pneumatic and manual operation, and is heated and vulcanized to form. This process is a manual process and requires a lot of labor, so the production capacity is not high. It has a feature that one product can be dripped with multiple colors as required, so this process is mostly used to make high-end silicone products. Such as: multi-color silicone bracelets, silicone bottle covers, cartoon silicone bags, housing covers,
high-end silicone gifts, etc.
Detailed introduction to the glue dispensing process for silicone products
The material used in the glue dispensing processes of silicone products is to mix epoxy resin and curing agent and then drip it on the surface of the silicone button. After leaving it for a period of time, the epoxy resin and curing agent will dry into a crystal-like effect. The dispensing processes not only It can make silicone products beautiful and protect the surface of silicone products from damage.
The manufacturing process of silicone products’ glue dripping process is generally to first prepare high-purity epoxy resin and curing agent in a certain proportion, and then put them into a glue dripping tank. You can use the glue dripping tank to drip a certain amount of glue onto the surface of the silicone button. Epoxy resin, and then place the glued silicone product for about 12 hours until it is completely fixed (it can be placed in the oven to completely fix it, which can shorten the time, and the oven temperature is 60-70 degrees), and wait until the silicone product After the fixation is complete, the glue dispensing process is completed!
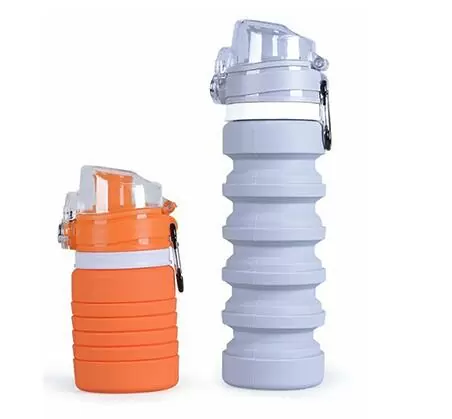
In summary, the glue dispensing process for silicone products is an important part of the production of silicone products. It can achieve crystal-like silicone products while maintaining good feel and gloss. However, you should not put too much epoxy resin during the glue dispensing process of silicone products, and the oven temperature should not be too high. To avoid causing defective silicone products and causing losses to the silicone product factory.
Things to pay attention to when using silicone products with glue dispensing process
The benefits brought by the glue dispensing process to silicone products are not only the protection of the product surface from wear and tear, but also the pursuit of high quality and exquisite appearance. It is not difficult to make a piece of product into a golden and translucent appearance. Do the following Just a few o’clock.
1. Ensure that all equipment is clean during the glue dispensing process to avoid impurities, ripples, pitting and other defects on the surface after the glue dispense is cured.
2. The glue proportion must be accurately weighed and the glue must be stirred evenly, otherwise it will cause incomplete curing of the glue and take a long time to cure.
3. The humidity of the glue dispensing working environment is controlled within 68%. It is not recommended to perform glue dispensing work on rainy days, because when the air humidity is too high, the fog in the air will directly cause the oxidation of the glue surface. It is recommended to use air dehumidification under tight production tasks. device.
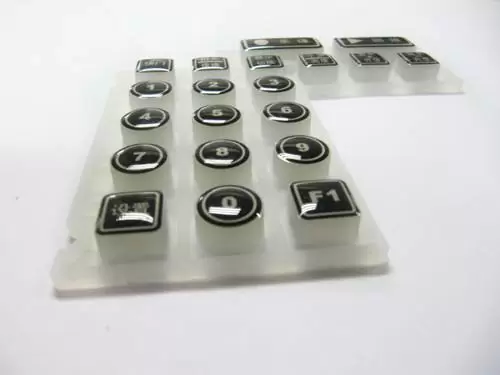
4. Silicone products with strict glue dispensing effect should be concentrated in the area to be dried, and the temperature should be controlled between 28-40°.
The Mechanics of the Silicone Dispensing Process
Basic Principles of Dispensing:
The dispensing process of silicone is a meticulous procedure that demands precision and control. At its core, the method involves accurately delivering silicone to specific locations or surfaces. This process is governed by precise control mechanisms to ensure the correct amount of silicone is dispensed, adhering to the designated patterns, thickness, and volume. The accuracy of this process is paramount, as it directly impacts the quality and performance of the final product.
Precision in silicone dispensing is not just about the quantity but also about the placement and consistency of the silicone material. This is especially crucial in applications where silicone acts as a sealant or adhesive, where an even and uninterrupted layer is essential for optimal performance. In manufacturing sectors like electronics or aerospace, where components are highly sensitive, the precision of silicone dispensing can be the difference between a successful product and a faulty one.
Types of Dispensing Systems:
Various dispensing systems are employed in the industry to cater to different needs. Pneumatic pressure systems are among the most common. These systems use compressed air to exert pressure on the silicone, pushing it through a dispensing nozzle. They are favored for their simplicity, reliability, and ease of control, making them suitable for a wide range of applications.
However, the spectrum of dispensing systems extends far beyond pneumatic solutions. Advanced systems may include robotic dispensers, which offer high precision through automated controls. These robotic systems are programmable and can execute complex dispensing patterns with high repeatability, making them ideal for large-scale production or applications requiring intricate dispensing designs.
The role of technology in these dispensing systems is integral. Modern advancements have led to the development of more sophisticated control mechanisms. For instance, some systems now incorporate sensors and feedback loops that allow real-time adjustments to the dispensing process, accommodating factors like changing viscosity or temperature variations. This technological integration not only enhances the precision of the dispensing process but also increases its efficiency and adaptability, meeting the evolving demands of various industries.
In conclusion, the mechanics of the silicone dispensing process, underpinned by methodical control and advanced systems, are crucial in maintaining the high standards required in modern manufacturing. The ongoing technological enhancements in these systems not only streamline the process but also expand the possibilities of what can be achieved with silicone dispensing.
Key Components and Materials in Silicone Dispensing
Sensitive Components and Their Protection:
Silicone dispensing plays a pivotal role in the protection of sensitive components, especially in the electronics industry and other high-precision device manufacturing. These components, often susceptible to damage from environmental factors such as moisture, dust, and thermal fluctuations, require robust protection to ensure longevity and functionality. Silicone, with its exceptional sealing and conformal coating insulating properties, is an ideal material for this purpose.
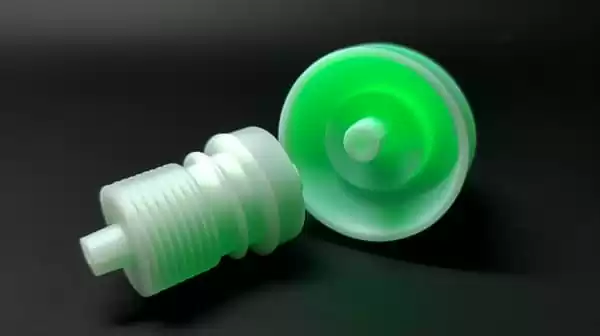
The dispensing process allows for the application of silicone in precise patterns and thicknesses, forming a protective layer over sensitive components. In electronics, for instance, a thin layer of silicone is used to encapsulate circuit boards, safeguarding them against moisture and electrical interference. This encapsulation not only protects the components but also maintains their performance by providing thermal stability and reducing the risk of overheating.
In other devices, such as sensors or medical equipment, silicone dispensing is used to create barriers against external contaminants, while ensuring that the components remain functional and responsive. The ability to apply silicone accurately and consistently is crucial in these applications, as it directly impacts the efficacy and reliability of the protective layer.
Materials and Chemicals Used:
The silicone dispensing process utilizes a range of materials, each selected for specific properties and applications. Silicones are the primary material, valued for their versatility, durability, and resistance to extreme conditions. However, the process often involves more than just pure silicone. Depending on the application, other materials such as resins and fillers may be added to modify the properties of the silicone.
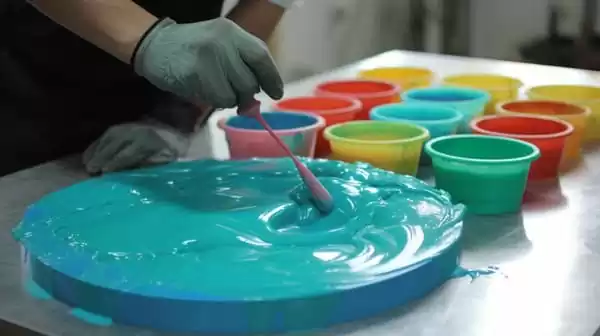
Resins, for example, can be mixed with silicone to enhance its adhesive properties or to alter its viscosity for easier application. Fillers, on the other hand, are used to reinforce the silicone, improving its strength and thermal conductivity. These additives play a significant role in tailoring the silicone to meet specific requirements of different applications.
The curing process of these materials is another critical aspect of silicone dispensing. Curing refers to the chemical process through which the silicone mixture hardens and achieves its final properties. This process can be initiated or accelerated by various means, such as the application of heat, exposure to air or moisture, or through chemical catalysts. The choice of curing method depends on factors like the desired speed of the process, the properties of the silicone mixture, and the specifics of the application.
In summary, the materials and chemicals used in the silicone dispensing process are as important as the process itself. The right combination of silicones, resins, fillers, and curing methods can significantly enhance the performance and durability of the final product, ensuring that sensitive components are adequately protected and functional over their lifespan.
Advanced Techniques and Challenges
Technological Advancements:
Recent years have witnessed remarkable advancements in silicone dispensing technology, transforming the efficiency and capabilities of this process. One of the key developments is the refinement of control systems. These sophisticated systems now offer greater precision in the dispensing process, allowing for more intricate patterns and consistent application. This precision is crucial in industries where even a minor deviation can lead to product failure.
Another significant advancement is the advent of vacuum dispensing technology. Vacuum dispensing is particularly effective in eliminating air bubbles during the dispensing process, which is essential for applications requiring high purity and uniformity. This method is especially beneficial in the electronics industry, where air bubbles in silicone can compromise the insulation and protection of sensitive components.
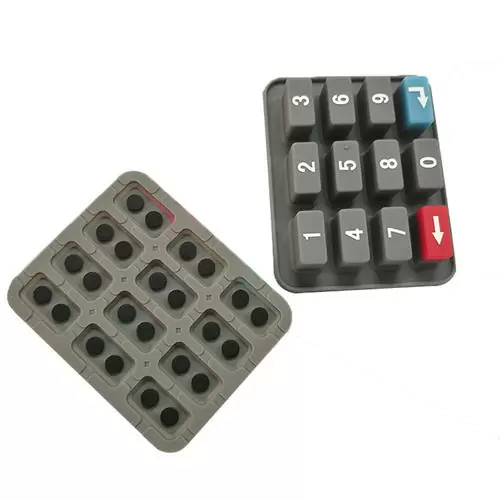
Automation has also played a significant role in advancing dispensing technology. Automated dispensing systems can now be integrated into production lines, increasing throughput and consistency while reducing labor costs and human error. These systems are often equipped with sensors and feedback mechanisms, allowing for real-time adjustments and ensuring a high level of accuracy throughout the dispensing process.
Addressing Challenges:
Despite these technological advancements, the silicone dispensing process faces several challenges. One of the most prevalent is dealing with the viscosity of silicone. The viscosity can vary significantly depending on the formulation and temperature, affecting the flow and application of the material. Managing this requires sophisticated control systems that can adjust the dispensing parameters in real-time to accommodate changes in viscosity.
Temperature-related influences also pose a challenge. Silicone’s properties can change in response to temperature variations, impacting its curing time and adhesion. This is particularly challenging in environments with fluctuating temperatures or in applications where the silicone must cure quickly. Advanced dispensing systems now include temperature control mechanisms to mitigate these issues, ensuring consistent application and curing regardless of external temperature conditions.
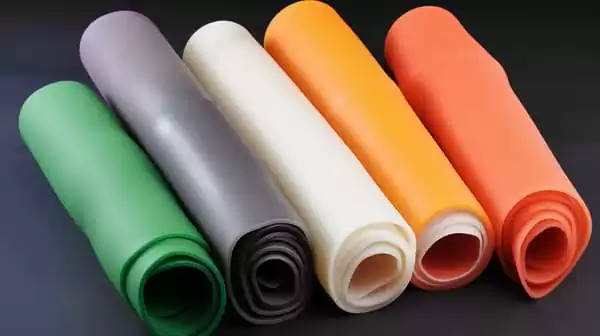
In summary, while the advancements in silicone dispensing technology have streamlined and enhanced the process, addressing the inherent challenges remains crucial. Overcoming these challenges requires a combination of technological innovation, precise control, and a deep understanding of the material properties and environmental factors involved. As the technology continues to evolve, it opens up new possibilities for the application of silicone in various industries, further solidifying its role in modern manufacturing processes.
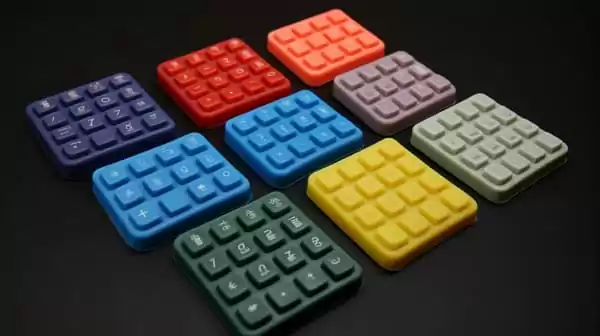
Conclusion
Looking to the future, the silicone dispensing process is poised to continue evolving and expanding its role in industrial applications. With ongoing technological innovations, the potential for more precise, efficient, and versatile dispensing systems is immense. This evolution will likely open up new applications and improve existing manufacturing processes, reinforcing the importance of silicone dispensing in the industrial landscape.
As industries continue to advance and demand more sophisticated manufacturing solutions, the silicone dispensing process will undoubtedly remain at the forefront, adapting and innovating to meet the ever-changing needs of modern manufacturing. The future of silicone dispensing holds promise for even greater achievements in precision, efficiency, and versatility, continuing to drive industrial innovation forward.