탄성, 내마모성, 내열성, 내후성, 내오존성, 담수 및 해수 저항성이 우수한 합성 고무인 EPDM은 도어 및 윈도우 씰, 유압 브레이크 호스 및 씰, 에어컨 환기 덕트, 엔진 냉각 시스템 및 에어컨 냉동 시스템의 씰, 냉각수 이송용 호스 등 자동차 고무 제품에 널리 사용됩니다.
EPDM 고무 는 비극성 포화 구조입니다. 소위 "비극성", 즉 폴리머를 구성하는 분자는 내부에 극성기를 포함하지 않습니다.
소위 "포화", 즉 폴리머의 조성은 분자 내부에 이중 결합을 포함하지 않습니다. 일반적으로 고무 및 열가소성 엘라스토머는 "극성"과 "비극성", "포화"와 "불포화"로 나눌 수 있으며 여러 구조로 나눌 수 있습니다.
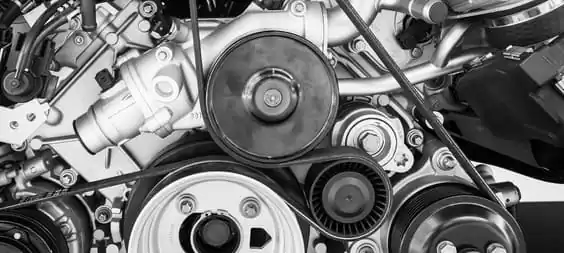
분자 자체에 극성기가 포함된 물질은 일반적으로 "극성" 물질입니다. "극성" 구조는 일반적으로 유사한 용해도, 즉 극성 용매가 극성 폴리머를 용해하거나 부풀리는 원리에 따라 폴리머의 용매에 대한 저항성을 결정하며, 그 반대의 경우도 마찬가지입니다.
"포화" 구조는 폴리머의 대기 노화(산화)에 대한 저항성과 관련이 있습니다. 폴리머 분자에 이중 결합이 포함되어 있으면 이중 결합이 쉽게 산화되기 때문에 폴리머가 불안정하고 분해되기 쉽습니다.
따라서 온수 및 증기, 세제, 유기산 및 무기산, 극성 용제(에탄올, 아세톤, 에스테르 등), 글리콜 기반 브레이크액 등과 같은 극성 매질에 강한 "비극성" EPDM으로, 극성 물질에 대한 내성이 강합니다.
또한 광유, 가솔린, 동식물성 지방, 오일, 실리콘 오일 등과 같은 비극성 매체에 내성이 없으며 글리콜 기반 브레이크액(SL-DOT4) 시스템, 부동액이 포함된 엔진 냉각 시스템에 널리 사용되며 오존 및 풍화에 대한 저항성이 뛰어난 "포화" EPDM으로 공기, 물 등의 생산에 널리 사용되고 있습니다.
자동차 사용 온도는 일반적으로 -40℃ ~ 120℃입니다. 다음은 사용에 대한 구체적인 소개입니다. EPDM 제품 자동차의 소재 성능 요구 사항, 일반적인 고장 상황을 분석합니다.
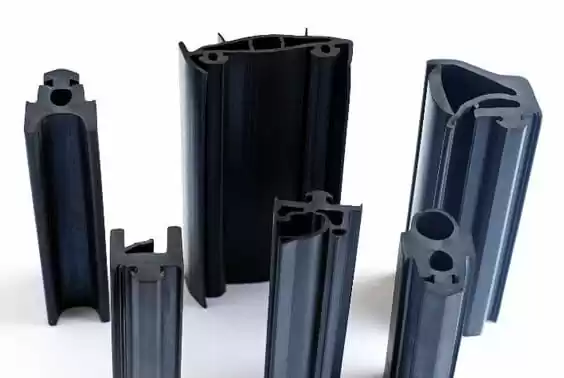
자동차 씰링 제품에 적용
대부분의 자동차 씰은 단면이 일정하고 길이가 무한한 압출 장비로 생산되며(사용 시 필요한 길이에 따라 차단), 소수의 불규칙한 제품은 가황 금형을 통해 생산됩니다.
압출 제품의 공정은 다음과 같습니다: 재료 → 고무 혼합 → 여러 재료(경질 고무, 연질 고무, 스폰지 고무, 유색 고무, 금속 골격, 강화 와이어 등 포함 가능).
복합 압출 → 가열 가황 (예 : 열풍 가황, 가황 탱크 가황, 마이크로파 가황, 유리 구슬 끓는 층 가황, 염욕 가황 등)→ 후 처리 (절단, 가황 접합, 정전기 플록, 표면 홍수 코팅, 본딩 등).
자동차의 앞뒤 유리, 문, 창문, 엔진룸, 트렁크 및 기타 부품에 널리 사용되며 충격 흡수, 방수, 방진, 방음, 장식, 운전자 및 승객 보호 및 기타 기능으로 차체 부품 사이의 틈새를 메우는 데 사용됩니다.
그런 실리콘 고무 제품 는 주로 햇빛, 물 및 오존과 접촉하며 -40 ℃ ~ 100 ℃의 온도를 사용하며 단기 내열 온도는 125 ℃에 도달 할 수 있습니다.
고무 씰링 스트립에 사용되는 EPDM 소재는 일반 경도(Shore A) 40~90, 인장 강도 7MPa 이상, 파단 연신율 150%~500%, 압축 변형(85℃, 22시간) 45% 미만이어야 함. 선택 사항 중 하나.
인열 강도는 5N / m 이상이어야합니다. 오존 노화 (50pphm, 스트레치 20%, 72 시간)는 균열이 없어야합니다. 제논 램프 노화 (제논 램프 1200 장비 사용, 상대 습도 80% ~ 95%, 흑판 온도 55 ℃ ~ 60 ℃, 1000h) 인장 강도 및 연신율 감소는 15%를 초과 할 수 없습니다.
유리 전이 온도(TR) 최대 -50℃, 열노화 시험(100℃, 70시간), 경도 변화 ± 5, 인장 강도 변화 ± 15%, 연신율 감소는 30%를 초과하지 않아야 합니다.
일반적으로 자동차 씰의 수명은 다음과 같이 구성됩니다. EPDM 고무 의 수명은 10년 이상에 달할 수 있습니다. 그러나 실제 생산 및 적용 과정에서 설치 1년 후 도어 및 창문 씰의 표면 균열, 씰링 성능 저하, 표면 성애 및 기타 고장 현상도 발생했습니다.
제품 테스트의 표면 균열, 20시간 후 오존 저항성 테스트에서 균열이 발생하여 표준 요구 사항을 충족하지 못했습니다. 이 불량 제품 배치에 대한 조사 후, 제형 오류가 발견되었습니다. (EPDM 고무 함량이 적음)의 원인은 고무 씰링 표면 서리(블룸)입니다.
원인 분석:
(1) 부적절하게 설계된 제형. 포화 범람으로 인한 성분의 황황색, 촉진제, 활성제, 항산화제 등; 무기 탄산칼슘 충전제 스트레스 범람.
(2) 혼합 공정의 부적절한 작동, 너무 짧은 시간으로 인해 필러가 고르지 않게 분산되어 포화보다 국부적으로 더 많이 분산됩니다. 공식을 수정하고 혼합 시간을 늘리고 마지막으로 홍수 문제를 해결할 수 있습니다.
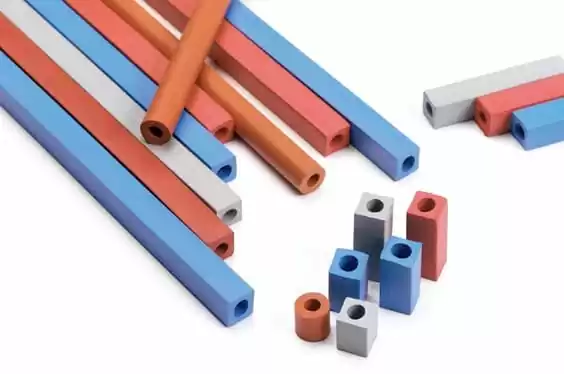
유압 브레이크 호스 및 원형 씰에 EPDM 적용
유압 브레이크 호스 내부 고무층 및 브레이크 펌프 씰 생산에 사용되는 EPDM 브레이크액 내성(DOT3, DOT4, DOT5(실리콘 오일 기반) 특성).
이러한 EPDM 제품 주 중간 브레이크액과 접촉하는 경우, -40℃ ~ 120℃의 온도, 최대 135℃의 단기 내열 온도를 사용해야 합니다.
이러한 부품은 EPDM을 사용하며 경도(Shore A)는 80, 인장 강도는 10.5MPa 이상, 파단 연신율은 일반적으로 175% 이상, 연신율 50%의 고정 연신 응력 2.5 ~ 4MPa, 연신율 100%의 고정 연신 응력 8MPa 이상이어야 합니다.
압축 변형(100℃, 22시간) 40% 미만, 유리 전이 온도(TR) 최대 -50℃, 오존 노화(50pphm, 20% 연신율, 72시간) 균열이 없어야 하며 브레이크액 테스트(시편을 브레이크액에 넣고 150℃, 70시간) 경도 변화가 5이어야 합니다.
인장 강도 변화는 ± 20%, 연신율 변화는 -15% ~ 20%, 부피 변화는 ± 20% 이내여야 합니다. 20%, 부피 변화는 ± 5%, 열 시험 (125 ℃, 70 시간), 경도 변화는 ± 5, 인장 강도 변화는 ± 15%, 연신율 감소는 15%를 초과 할 수 없습니다.
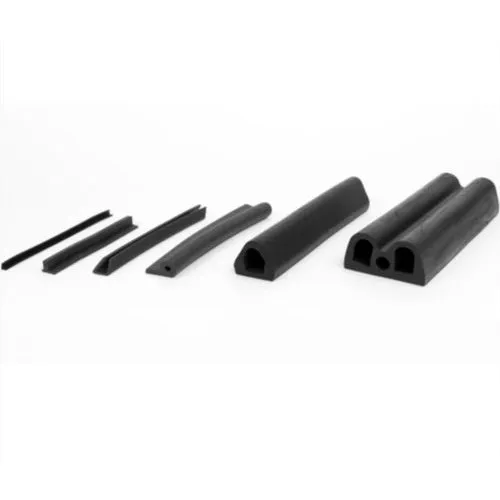
난방, 환기 및 공조 호스 애플리케이션의 EPDM
고무 호스는 일반적으로 내부 레이어, 중간 보강 레이어(화학 섬유 직물 또는 강철 와이어) 및 외부 레이어의 세 가지 레이어로 구성됩니다. 세 가지 레이어에 사용되는 재료는 실제 요구 사항에 따라 선택해야 합니다.
내부 레이어는 전달되는 매체의 부식에 강해야 하며, 외부 레이어는 기계적 강도가 있고 외부 환경에 적응할 수 있어야 합니다.
따라서 내부 및 외부 고무는 종종 고무가 아닙니다. EPDM은 공기, 물, 오존, 햇빛 노화, 저온 유연성에 대한 저항성이 우수하여 고무 층 안팎의 난방 및 환기 호스와 외부 고무 층의 에어컨 호스에 널리 사용되어 왔습니다.
EPDM을 사용하는 부품의 경도(Shore A)는 70, 인장 강도는 10.5MPa 이상, 파단 연신율은 일반적으로 300% 이상, 압축 잔류 변형(100℃, 22시간)은 40% 미만이어야 합니다;
유리 전이 온도(TR) 최대 -45℃, 오존 노화(50pphm, 연신 20%, 72시간) 균열이 없어야 하며, IRM902 오일 테스트(시편을 IRM902 오일에 100℃, 70시간) 경도 감소 최대 15, 인장 강도 감소 최대 30%가 없어야 합니다.
인열 강도 감소 최대 30%, 부피 변화는 80% 이내, 열 노화 시험(125℃, 70시간), 경도 변화 ± 5, 인장 강도 변화 ± 15%, 연신율 감소는 40%를 초과할 수 없습니다.
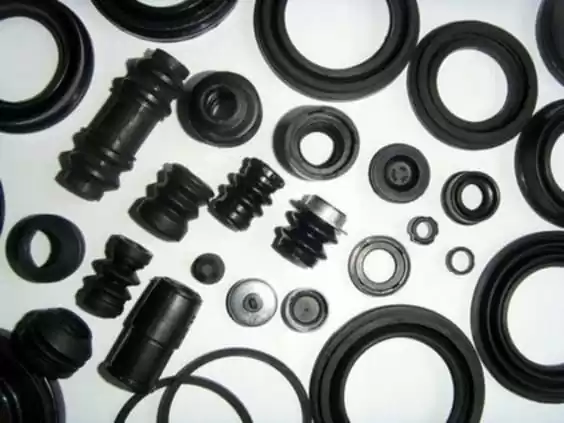
벨트를 당기는 응용 분야의 EPDM
주로 휠 커버, 배터리 박스 커버 고정 등의 연결에 사용되는 이러한 종류의 부품은 공정 사용시 높은 동적 및 기계적 부하를 견딜 수 있으며 항상 장력 상태에 있습니다.
이러한 실리콘 고무 제품 는 주로 햇빛, 물 및 오존에 노출되며 -40 ℃ ~ 85 ℃의 온도를 사용하며 단기 내열 온도는 100 ℃에 도달 할 수 있습니다.
이러한 부품을 만드는 데 사용되는 EPDM 소재의 경도(Shore A)는 일반적으로 60~80, 인장 강도는 14MPa 이상, 파단 연신율은 일반적으로 200%~400%, 인열 강도는 7N/m 이상이어야 합니다;
압축 잔류 변형 (85 ℃, 22 시간)은 45% 미만이어야하며 압축 잔류 변형 (-20 ℃, 22 시간)은 45% 미만이어야하며 오존 노화에 대한 내성 (50pphm, 스트레칭 20%, 72 시간)은 균열이 없어야합니다; 크세논 램프 노화 (크세논 램프 1200 장비 사용, 상대 습도 80% ~ 95%, 흑판 온도 55 ℃ ~ 60 ℃, 1000h) 인장 강도 및 연신율은 15%를 초과하지 않아야합니다;
유리 전이 온도(TR) 최대 -50℃, 열 노화 시험(100℃, 70시간), 경도 변화 ±75, 인장 강도 변화 ±15%, 연신율 감소 40%를 초과하지 않아야 합니다.
배터리 커버 스트랩의 파손과 휠 가드 스트랩 표면의 균열은 반년 동안 하중을 가한 후에 발생했습니다. 제품 인장 강도, 인열 강도 및 오존 노화 테스트 실패 후 실제 결과는 인장 강도 8.5MPa, 인열 강도 5N / m, 오존 노화 42 시간 균열로 표준 요구 사항에 미치지 못했습니다.
고무 공식의 중요성에 대한 당김 테이프의 개별 제조업체는 EPDM 고무가 고무 당김 테이프로 만들어지는 한 실제로 다른 공식으로 인해 제품 성능이 크게 달라질 수 있다는 것을 충분히 이해하지 못합니다.
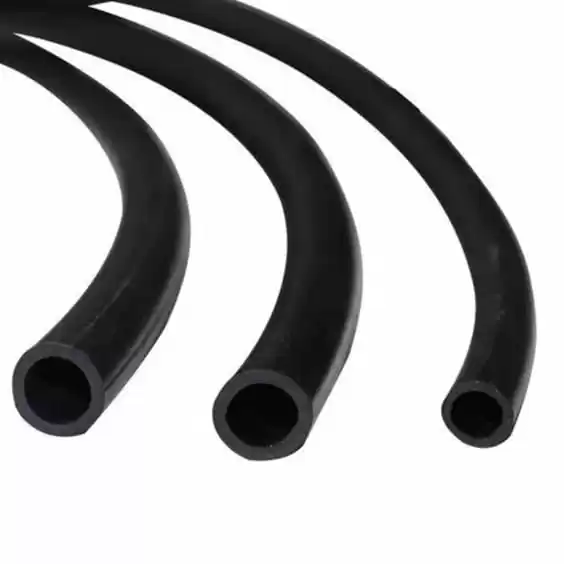
엔진 냉각 시스템 및 공조 및 냉장 시스템 씰에 EPDM 적용
EPDM은 엔진 냉각 시스템에서 씰을 만드는 데 사용됩니다. 이 제품은 부동액, 햇빛, 물, 오존, -40℃ ~ 125℃의 온도 사용, 최대 135℃의 단기 내열 온도와 접촉하는 매체와 접촉합니다.
60 ~ 80 (냉동 시스템의 원형 씰 적용의 경우 75)의 경도 (Shore A)를 사용하는 이러한 부품; 인장 강도는 10 이상이어야합니다.5MPa; 파단 연신율은 일반적으로 175% 이상; 1 ~ 2MPa의 고정 신장 응력의 50% 연신율에서; 위의 2 ~ 5MPa의 고정 신장 응력의 100% 연신율에서; 수축 변형 (150 ℃, 22 시간)은 20% 미만이어야합니다;
내열 온도는 최대 135℃(22시간), 유리 전이 온도(TR)는 최대 -50℃, 오존 노화 저항(50pphm, 연신 20%, 72시간)은 균열이 없어야 합니다;
엔진 냉각 시스템에 사용되는 씰의 경우 냉매 시험(부동액에 시험편을 넣고 150°C, 166시간, 시험 압력 약 0.4MPa)을 실시하며 경도 변화는 ±5, 인장 강도 변화는 ±20%, 파단 연신율 변화는 -15% ~ 20%, 부피 변화는 ±5%로 합니다;
공조 시스템에 사용되는 씰의 경우 냉매 시험 (P 시험 (시편을 PAG, ND8 냉매, 100 ℃, 70 시간)에 시편을 넣어 경도 변화 최대 ± 5, 인장 강도 변화 최대 ± 20%, 파단 연신율 변화 최대 -15% ~ 20%, 체적 변화 ± 5% 이내이어야 함)을 수행해야합니다; 열 노화 시험 (150 ℃, 70 시간), 경도 변화는 ± 5, 인장 강도 강하가 10% 미만이어야하며, 연신율 강하는 10%를 초과 할 수 없습니다.
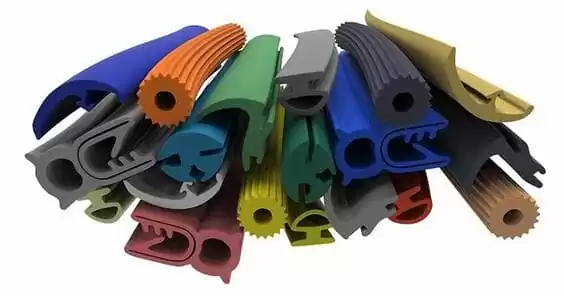
냉각수 호스 적용에 사용되는 EPDM
엔진 워터 호스를 만드는 데 사용되는 EPDM은 내부 및 외부 고무 층이 EPDM 재질로 만들어집니다. 이러한 EPDM 제품 매체와 접촉하는 것은 부동액, 햇빛, 물, 오존, -40 ℃ ~ 125 ℃의 온도 사용, 단기 내열 온도는 150 ℃에 도달 할 수 있습니다.
이러한 부품은 경도(쇼어 A) 65, 인장 강도 10.5MPa 이상, 파단 연신율 300% 이상, 고정 연신 응력 1 ~ 2MPa의 연신율 50%, 고정 연신 응력 2 ~ 4.5MPa 이상의 연신율 100%, 압축 잔류 변형(100 ℃, 22시간) 20% 미만인 EPDM을 사용해야 합니다;
유리 전이 온도(TR) 최대 -50℃, 오존 노화(50pphm, 연신 20%, 72시간), 냉각수 테스트(부동액에 시편을 넣고 150℃, 166시간, 시험 압력 약 0.4MPa).
경도 변화는 ± 5, 인장 강도 변화는 ± 20%, 파단 연신율 변화는 -15% ~ 20%, 체적 변화는 ± 5%이어야 합니다. 열 노화 시험 (150 ℃, 70 시간), 경도 변화는 ± 5, 인장 강도는 10% 미만이어야하며 감소 연신율은 10%를 초과하지 않아야합니다.