Inleiding
Productie van persgieten proces is een veelgebruikt proces voor het maken van composietmaterialen met superieure sterkte en duurzaamheid. Er wordt een intense druk en temperatuur uitgeoefend op het vormmateriaal in een vormholte, waardoor het de gewenste vorm aanneemt. Materialen die gebruikt worden bij compressievormen kunnen variëren van thermohardende materialen zoals epoxyhars en bulk molding compound (BMC), tot polymeer matrix composieten (PMC) en sheet molding compounds (SMC).
De viscositeit van het materiaal speelt een belangrijke rol bij het persen en bepaalt de weerstand tegen vloeien en vervorming onder spanning. De viscositeit speelt een integrale rol bij het controleren van de materiaalstroom tijdens het vormen en beïnvloedt de mechanische eigenschappen en de maatnauwkeurigheid.
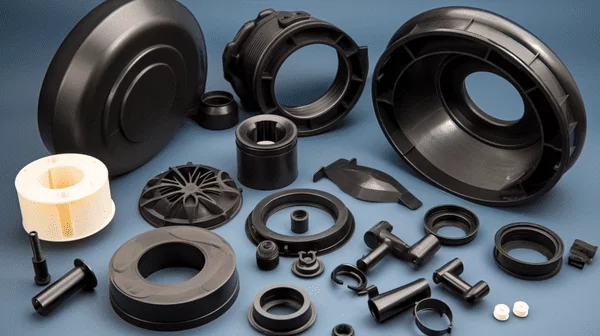
In dit artikel onderzoeken we de factoren die van invloed zijn op persgieten proces en de gebruikte materialen. Daarnaast bespreken we belangrijke overwegingen tijdens het matrijsontwerp, zoals de viscositeit van materialen die gebruikt worden bij compressievormen. Bovendien behandelen we verschillende compressievormprocessen en hun mechanische eigenschappen, toepassingen van compressievormen en mogelijke toekomstige ontwikkelingen binnen de productie.
II. Factoren die het spuitgietproces beïnvloeden
Persgieten is een zeer gespecialiseerd productieproces waarbij zorgvuldig rekening moet worden gehouden met meerdere factoren. Deze omvatten vereisten voor hoge druk en temperatuur, vormmateriaal en -samenstelling, vormontwerp en -complexiteit, uithardingsproces en -tijd.
De druk en temperatuur die nodig zijn voor het persen verschillen afhankelijk van het materiaal dat gevormd wordt en de complexiteit van het matrijsontwerp. Bovendien spelen het type en de samenstelling van het vormmateriaal een belangrijke rol in deze stap; u moet zorgvuldig overwegen welk materiaal aan de vereisten van uw toepassing voldoet voordat u met deze stap begint.
Het ontwerp en de complexiteit van een matrijs kunnen van grote invloed zijn op de benodigde druk en temperatuur en de maatnauwkeurigheid van het eindproduct. Een goed matrijsontwerp is essentieel om de gewenste mechanische eigenschappen en maatnauwkeurigheid te bereiken.
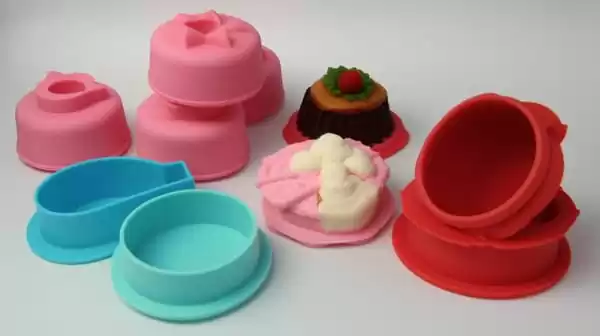
Uithardingsproces en -tijd zijn vitale elementen in persgieten. De duur van het uitharden hangt af van het materiaal dat gegoten wordt, het matrijsontwerp en de temperatuur en druk die tijdens de procedure worden toegepast. Nauwkeurige controle over deze variabelen is nodig om de gewenste mechanische eigenschappen en maatnauwkeurigheid in het eindproduct te verkrijgen.
Al met al is een goede afweging van al deze elementen essentieel voor het verkrijgen van consistente en hoogwaardige resultaten bij het persgieten.
III. Materialen gebruikt bij persen
Compression molding kan gebruikt worden met een hele reeks materialen, waarvan de populairste thermohardende materialen, polymeer matrix composieten (PMC) en sheet molding compounds (SMC) zijn.
Thermohardende materialen
Thermohardende materialen zoals epoxyhars en bulk molding compound (BMC) worden veel gebruikt in persgieten vanwege hun superieure sterkte, stijfheid en maatvastheid. Deze polymeren ondergaan een chemische reactie bij verhitting en uitharding, waardoor een extreem sterk materiaal ontstaat met uitstekende mechanische eigenschappen.
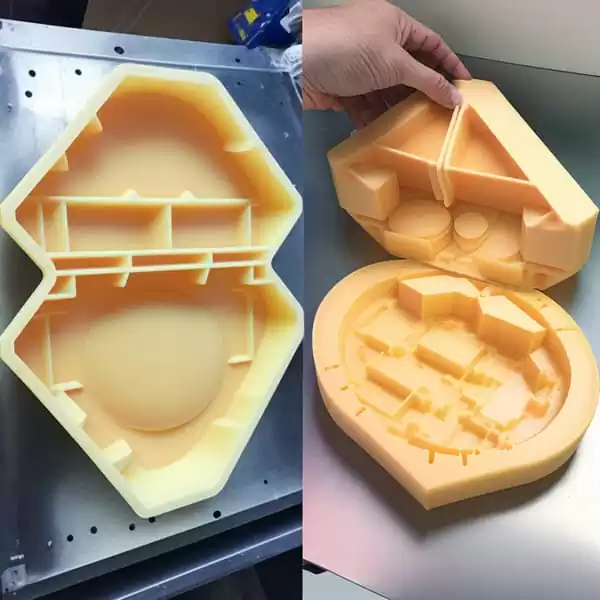
Polymeer matrix composieten (PMC)
Polymeer matrix composiet (PMC) is een ander materiaal dat vaak gebruikt wordt bij het persen. Deze composieten bestaan uit een polymeerharsmatrix versterkt met vezels zoals glas, koolstof of aramide voor meer sterkte en stijfheid. Daarom hebben PMC's toepassingen waar een hoge sterkte nodig is.
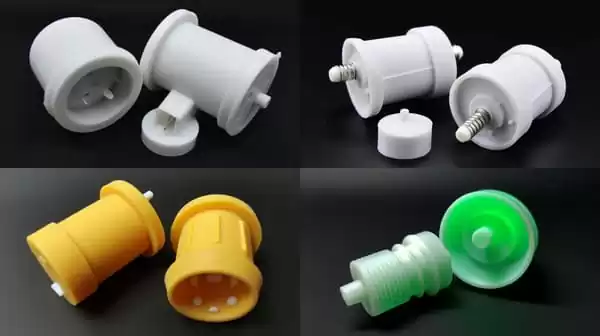
Sheet molding compounds (SMC) en glasmat thermoplasten (GMT)
Sheet molding compounds (SMC) en glasmat thermoplasten (GMT) worden beide gebruikt bij persen. SMC bestaat uit een thermohardende harsmatrix, gehakte glasvezels en minerale vulstoffen, terwijl GMT een acrylharsmatrix heeft met willekeurig georiënteerde glasvezels. Beide materialen bieden een uitstekende sterkte, stijfheid en maatvastheid wanneer ze worden samengedrukt.
Bij het selecteren van materiaal voor compressievormen zijn er een paar dingen om rekening mee te houden: gewenste mechanische eigenschappen, kostenefficiëntie en productievolume. Een juiste materiaalkeuze is essentieel om de gewenste resultaten te bereiken bij persen.
IV. Overwegingen bij het matrijsontwerp voor persgieten
Ben je op zoek naar een persvorm? Houd rekening met deze ontwerpfactoren bij het maken van je ontwerp.
Wanneer het ontwerpen van een matrijs voor persgietenHet ontwerp van de mal is van het grootste belang om succes te boeken. Houd rekening met alle relevante vereisten bij het maken van je ontwerp; hier zijn enkele belangrijke aspecten om in gedachten te houden bij het maken van deze belangrijke stap:
Vormholteontwerp en materiaalselectie
Bij het ontwerpen van een matrijsholte moet rekening worden gehouden met de vorm en grootte. Zorg er bovendien voor dat het gebruikte materiaal een uitstekende thermische geleiding heeft en bestand is tegen slijtage.
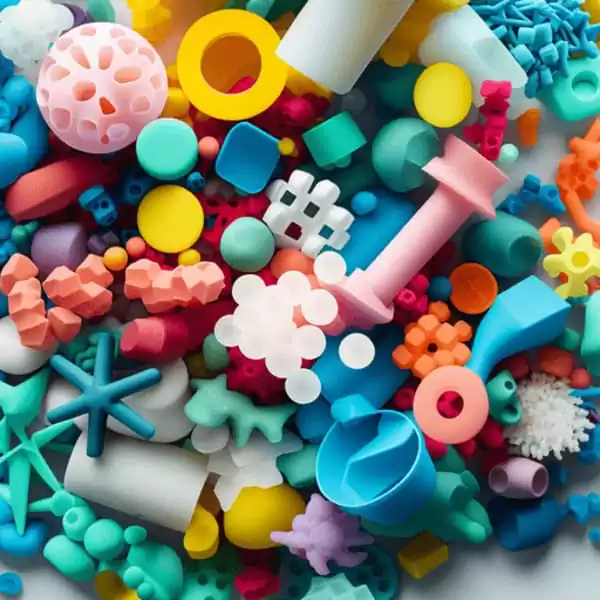
Interne structuur van de mal
De interne structuur van een matrijs, inclusief de plaatsing en verdeling van openingen en poorten, kan de materiaalstroom tijdens het gieten beïnvloeden. Een juiste plaatsing en verdeling van openingen en poorten helpt een gelijkmatige materiaalverdeling door de holte te garanderen.
Schimmeltemperatuur en -druk
De vormtemperatuur en -druk moeten zorgvuldig geregeld worden, afhankelijk van het materiaal dat gegoten wordt en de complexiteit van het matrijsontwerp. Zowel de temperatuur als de druk hebben een effect op de mechanische eigenschappen en de maatnauwkeurigheid van het eindproduct.
Oppervlakteafwerking en dimensionale stabiliteit
Om de gewenste esthetiek en functionele vereisten te bereiken, moeten de onderdelen een gladde, glanzende oppervlakteafwerking hebben. Daarom is het essentieel dat de matrijs wordt ontworpen om deze gewenste oppervlakteafwerking te produceren. Bovendien moet ook de matrijsstabiliteit worden gegarandeerd; dimensionale veranderingen tijdens het gieten moeten tot een minimum worden beperkt.
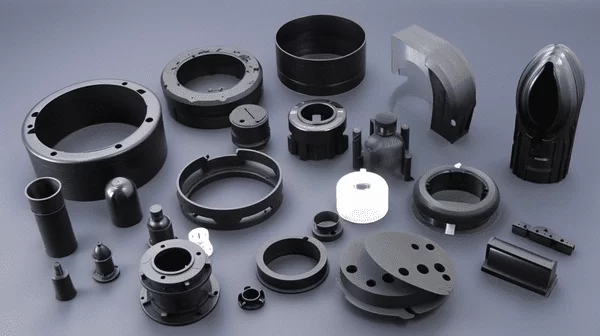
Restspanningen in gegoten onderdelen
In spuitgietproducten kunnen restspanningen ontstaan door afkoeling en uitharding tijdens het productieproces. Daarom moet het matrijsontwerp worden geoptimaliseerd om deze spanningen, die de mechanische eigenschappen en maatnauwkeurigheid van het eindproduct negatief kunnen beïnvloeden, te minimaliseren.
Om de gewenste mechanische eigenschappen, maatnauwkeurigheid en oppervlakteafwerking van het eindproduct te verkrijgen, is het essentieel om al deze variabelen in overweging te nemen bij het ontwerpen van een compound voor volbladspuitgieten.
V. De rol van materiaalviscositeit bij persen
Definitie van materiaalviscositeit
De viscositeit van het materiaal is een kritieke factor in de persgieten proces. Viscositeit verwijst naar de weerstand van een materiaal tegen vloeien en vervorming onder toegepaste spanning en bepaalt bij persen het vloeigedrag tijdens persen.
Hoe materiaalviscositeit het persgieten beïnvloedt
De viscositeit van een materiaal heeft invloed op hoe goed het een matrijsholte vult en door de holte verdeelt. Hoge viscositeiten vereisen hogere drukken en temperaturen voor een goede stroming, terwijl lage viscositeiten te vrij stromen, wat leidt tot uitvloeiing of vervorming van het materiaal. Viscositeit heeft ook een effect op de mechanische eigenschappen en de maatnauwkeurigheid van het eindproduct.
Het belang van het kiezen van de juiste viscositeit voor het materiaal dat gegoten wordt
Het selecteren van de juiste viscositeit voor een te gieten materiaal is essentieel om de gewenste resultaten te bereiken. Factoren zoals temperatuur, druk en uithardingstijd kunnen allemaal worden aangepast om dit evenwicht te bereiken. Een gelijkmatige vulling van de vormholte door de juiste viscositeitsregeling zorgt voor een gelijkmatig eindproduct van hoge kwaliteit.
Tot slot speelt de materiaalviscositeit een cruciale rol in de persgieten proces. Door de viscositeit van het materiaal goed te beheren en te controleren, kan men consistente en hoogwaardige resultaten garanderen bij het persen.
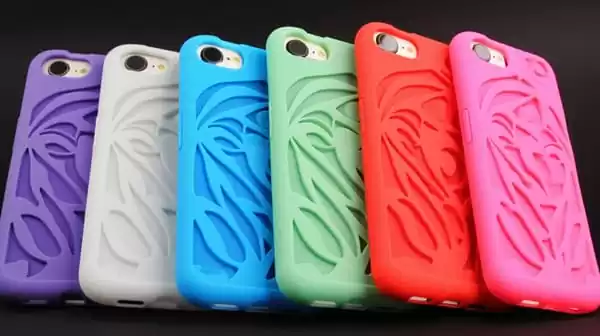
VI. Processen voor persen
Compressievormen is een populaire productietechniek om composietmaterialen met hoge sterkte te maken. Er zijn verschillende persgietprocessen, zoals nat persgieten, resin transfer molding (RTM) en spuitgieten.
Nat persgieten
Bij nat persen worden versterkingsvezels geïmpregneerd met een vloeibare hars voordat ze in een vormholte worden geplaatst. Eenmaal gesloten worden druk en warmte toegepast om het materiaal uit te harden - een efficiënte methode voor het produceren van composietonderdelen met hoge sterkte en hoge prestaties.
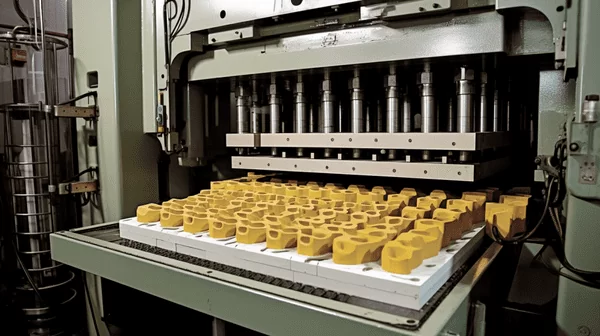
Harstransfer spuitgieten (RTM)
RTM is een gesloten vormproces waarbij vloeibare hars in een vormholte wordt geïnjecteerd. Versterkingsvezels worden in de holte geplaatst voordat de hars onder druk wordt geïnjecteerd om ze met hars te doordrenken. Tot slot wordt warmte toegepast om het materiaal uit te harden, waardoor RTM populair is voor het produceren van grote composietonderdelen met complexe vormen.
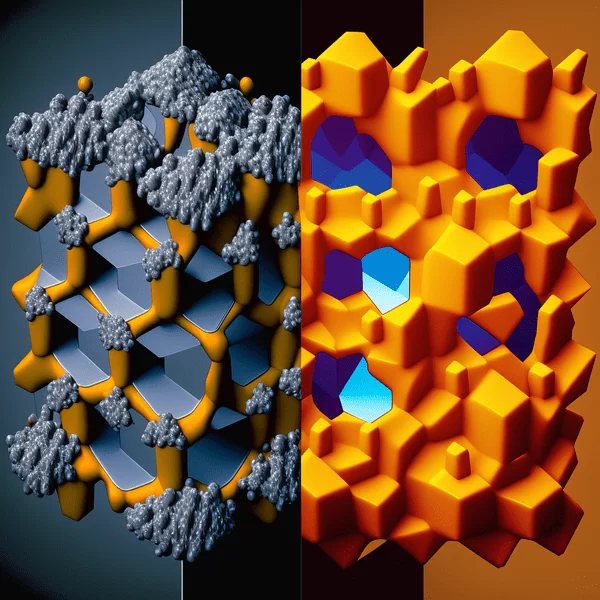
Spuitgieten
Bij spuitgieten wordt thermoplastisch materiaal in een vormholte gespoten. Nadat het is afgekoeld en gestold, kan het onderdeel worden vrijgegeven. Deze methode is ideaal voor het produceren van grote aantallen goedkope onderdelen met complexe geometrieën.
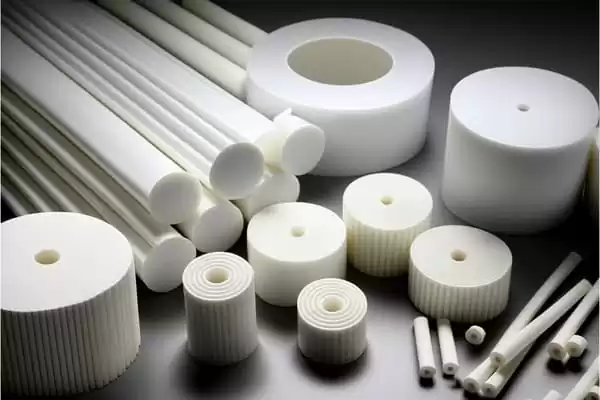
Verschillen tussen persen en andere spuitgiettechnieken
Compression molding heeft enkele overeenkomsten met andere spuitgiettechnieken, zoals spuitgieten. Er zijn echter belangrijke verschillen. Bij persen worden bijvoorbeeld een hogere druk en temperatuur gebruikt, wat resulteert in materialen met een grotere sterkte en stijfheid. Bovendien maakt persen het gebruik van versterkingsvezels mogelijk, wat de materiaaleigenschappen nog verbetert.
Over het algemeen biedt compressievormen duidelijke voordelen ten opzichte van andere vormprocessen, waardoor het een populaire keuze is voor het maken van composietmaterialen met hoge sterkte.
VII. Mechanische eigenschappen van persdelen
Persgietonderdelen hebben de mechanische eigenschappen die ervan verwacht worden, omdat hun constructie geen enkele versterking vereist.
Drukgegoten onderdelen moeten voldoen aan bepaalde mechanische specificaties, afhankelijk van hun materiaalsamenstelling en de gebruikte vezelversterking.
Polymeercomposieten worden vaak gebruikt in persgietenHet materiaal bestaat uit een polymeerharsmatrix versterkt met vezels zoals glas, koolstof of aramide. De vezelversterking verhoogt de sterkte en stijfheid van het materiaal, waardoor het ideaal is voor toepassingen die hoge mechanische prestaties vereisen.
Bij persgietprocessen worden verschillende versterkingsvezels gebruikt, waarbij het type en de hoeveelheid een belangrijke invloed hebben op de mechanische eigenschappen van het eindproduct. Koolstofvezels bijvoorbeeld kunnen materialen produceren met een superieure sterkte en stijfheid, terwijl glasvezels een hogere stijfheid maar een lagere sterkte bieden.
Naast vezelversterking kan polyethyleen met hoge dichtheid (HDPE) bij persgieten ook de thermische eigenschappen van het materiaal verbeteren. De uitstekende thermische geleidbaarheid van HDPE helpt om warmte effectiever af te voeren, waardoor materialen met een verbeterde thermische stabiliteit ontstaan.
In het algemeen worden de mechanische eigenschappen van persdelen bepaald door verschillende factoren, zoals de samenstelling van het materiaal, het type en de hoeveelheid gebruikte versterkingsvezels en additieven zoals HDPE. Om de gewenste mechanische prestaties uit deze factoren te halen, is een zorgvuldige selectie nodig.
VIII.Compression Molding toepassingen
Persgieten is een uitstekend hulpmiddel om verschillende producten te maken door er druk op uit te oefenen.
Compressievormen is een innovatief productieproces met talrijke toepassingen in verschillende industrieën en toepassingen. Bekende voorbeelden van persen zijn:
Auto-industrie
Persgieten wordt veel gebruikt in de auto-industrie om motoronderdelen en andere complexe geometrieën te maken. Door de hoge sterkte en stijfheid zijn materialen die geproduceerd worden door middel van persen ideaal voor toepassingen waar prestaties en duurzaamheid essentiële factoren zijn.
Ruimtevaarttoepassingen
Compressievormen wordt vaak gebruikt in de ruimtevaartindustrie om lichtgewicht composietonderdelen met hoge sterkte te maken. De kostenvoordelen en snelle productieprocessen in verband met persen maken het een aantrekkelijke optie voor ruimtevaartfabrikanten.
Medische industrie
Compressievormen wordt veel gebruikt in de medische industrie om onderdelen zoals spuitstoppen te maken. Met zijn superieure precisie en maatnauwkeurigheid biedt compressievormen de ideale oplossing voor het maken van onderdelen met strakke toleranties.
Tot slot is compressievormen een veelgebruikt productieproces in verschillende industrieën en toepassingen. Het vermogen om zeer sterke materialen met complexe geometrieën en nauwe toleranties te produceren, maakt het ideaal voor industrieën waar prestaties en duurzaamheid essentiële factoren zijn.
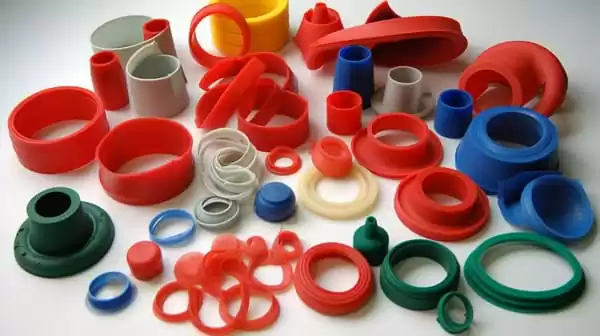
Conclusie
Compression molding is een uitgebreid productieproces dat in veel industrieën en toepassingen wordt gebruikt. Het maakt gebruik van hoge druk en temperatuur om sterke composietmaterialen te produceren met complexe geometrieën en nauwe toleranties.
De viscositeit van het materiaal speelt een belangrijke rol in persgietenDe viscositeit heeft immers een directe invloed op het vloeigedrag en de mechanische eigenschappen van het eindproduct. Om consistente resultaten van hoge kwaliteit te bereiken, moet de viscositeit van het materiaal tijdens het persgieten goed onder controle gehouden worden.
Bij toekomstige ontwikkelingen op het gebied van persen zullen geavanceerde materialen worden gebruikt, zoals nanocomposieten en materialen op biologische basis, evenals nieuwe productiemethoden zoals additive manufacturing. Deze innovaties zullen naar verwachting de prestaties, efficiëntie en duurzaamheid van het compressievormproces verbeteren.
Over het algemeen is persen een betrouwbaar en rendabel productieproces met tal van voordelen, zoals hoge sterkte en stijfheid, complexe geometrieën en nauwe toleranties. Door op de juiste manier rekening te houden met alle factoren die een rol spelen bij persen - inclusief materiaalviscositeit - kan men het gewenste resultaat garanderen en voldoen aan specifieke vereisten voor verschillende toepassingen.