Inleiding
Persen is een essentieel productieproces met een grote impact op verschillende industrieën. Dit artikel duikt in de wereld van het persgieten, onderzoekt het belang, de uitdagingen en de cruciale rol van simulatiesoftware bij het overwinnen van deze hindernissen.
Compression molding is een veelgebruikte productietechniek om complexe onderdelen te maken van een groot aantal materialen, waaronder kunststoffen, composieten en rubber. Dit proces is van immens belang omdat het het volgende kan opleveren hoogwaardige onderdelen met precisie, waardoor het onmisbaar is in industrieën als de auto-industrie, lucht- en ruimtevaart en consumentengoederen.
Hoewel compressievormen vele voordelen biedt, is het niet zonder complexiteit en uitdagingen. Het bereiken van optimale resultaten bij persen vereist een delicaat evenwicht van parameters, waaronder temperatuur, druk, materiaaleigenschappen en persgieten grondbeginselen en ontwerp. Het samenspel van deze factoren kan ingewikkeld zijn en leiden tot problemen zoals holtes, kromtrekken en inconsistente materiaalstroom. Deze uitdagingen vragen om innovatieve oplossingen om de productkwaliteit te verbeteren, afval te verminderen en de productie te optimaliseren.
Dit is waar simulatiesoftware het toneel betreedt. Simulatiesoftware heeft zich ontpopt tot een krachtig hulpmiddel dat fabrikanten in staat stelt om de fijne kneepjes van het persgieten rechtstreeks aan te pakken. Door virtuele modellen te maken en simulaties van het vullen van compressievormen uit te voeren, kunnen fabrikanten resultaten voorspellen, parameters optimaliseren en potentiële defecten identificeren - en dat allemaal zonder dure fysieke prototypes. Het belang van eindige-elementensimulatiesoftware bij het aanpakken van de complexiteit van persgieten kan niet worden overschat, omdat het een cruciale rol speelt bij het verhogen van de efficiëntie, het verbeteren van de kwaliteit en uiteindelijk het vormgeven van de toekomst van de productie.
In de volgende secties zullen we dieper ingaan op de persgietproces, onderzoeken op welke manieren simulatiesoftware effectief kan worden ingezet en praktische inzichten bieden voor het optimaliseren van compressievormresultaten.
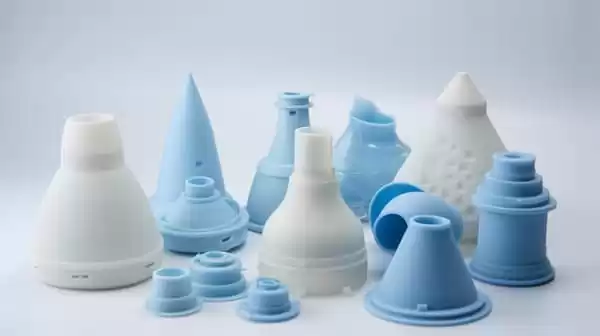
II. Compressievormen begrijpen
Compression molding is een productieproces waarbij verschillende stappen en verschillende kritische parameters komen kijken. In deze sectie zullen we de basisprincipes van het compressievormproces uitsplitsen en licht werpen op de belangrijkste parameters en variabelen die de resultaten aanzienlijk beïnvloeden.
De basisstappen van het persen
1. Voorbereiding:
Het persgietproces begint met de voorbereiding van de grondstof, meestal in de vorm van korrels of voorvormen. Dit materiaal wordt in een vormholte geladen, een nauwkeurig ontworpen ruimte die de uiteindelijke vorm van het product bepaalt.
2. Verwarming:
Zodra de matrijsholte gevuld is met materiaal, wordt hij gesloten en wordt het materiaal verhit. Door de warmte wordt het materiaal zachter, waardoor het kneedbaarder wordt en klaar is om te gieten.
3. Compressie:
Nadat de gewenste temperatuur is bereikt, wordt druk uitgeoefend op het materiaal. Deze compressie dwingt het materiaal om de matrijsholte volledig te vullen en de vorm van de matrijs aan te nemen.
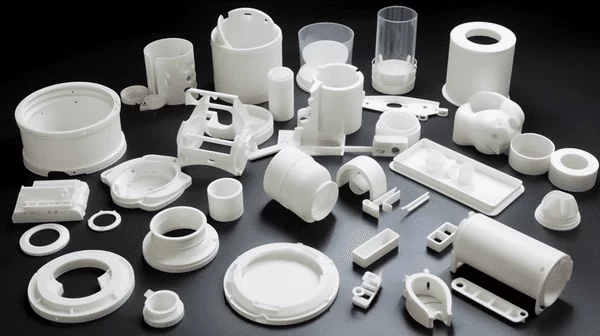
4. Koeling:
Na de compressiefase wordt de mal afgekoeld om het materiaal te laten stollen. De afkoeltijd wordt zorgvuldig gecontroleerd om ervoor te zorgen dat het materiaal zijn vorm en structurele integriteit behoudt.
5. Uitwerping:
Zodra het materiaal voldoende is afgekoeld en gestold, wordt het eindproduct uit de mal geworpen. Het product is dan klaar voor verdere verwerking of gebruik.
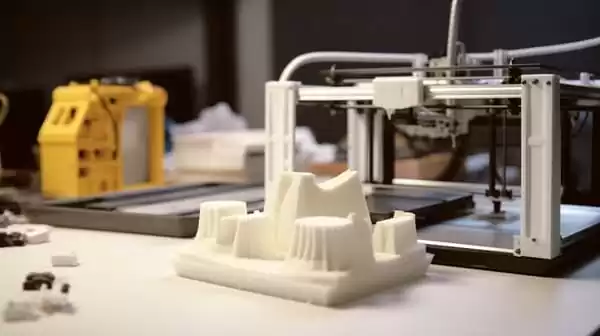
Belangrijke parameters en variabelen bij het persen
Het bereiken van optimale resultaten bij persen hangt af van een zorgvuldige balans tussen verschillende kritische parameters en variabelen, waaronder:
Temperatuur: De temperatuur waarop het materiaal verwarmd wordt, speelt een fundamentele rol in het gedrag van het materiaal tijdens het spuitgieten. Het beïnvloedt de vloei-eigenschappen, uitharding en algemene prestaties van het materiaal.
Druk: Druk is nodig om ervoor te zorgen dat het materiaal de matrijsholte volledig vult. Een goede drukregeling voorkomt defecten en zorgt voor een gelijkmatige vulling van de matrijs.
Tijd: De duur van elke fase van het spuitgietproces, inclusief verwarmen, comprimeren en afkoelen, heeft een directe invloed op de kwaliteit en eigenschappen van het eindproduct.
Materiaaleigenschappen: Materiaaleigenschappen zoals viscositeit, smeltsnelheid en uithardingsgedrag zijn essentiële overwegingen bij het persen. De materiaalkeuze heeft een grote invloed op het spuitgietproces en de kwaliteit van het eindproduct.
Vormontwerp: De geometrie vezeloriëntatie van de matrijsholte en eigenschappen zoals openingen en runners hebben een aanzienlijke invloed op de materiaalstroom en de structuur van het uiteindelijke onderdeel.
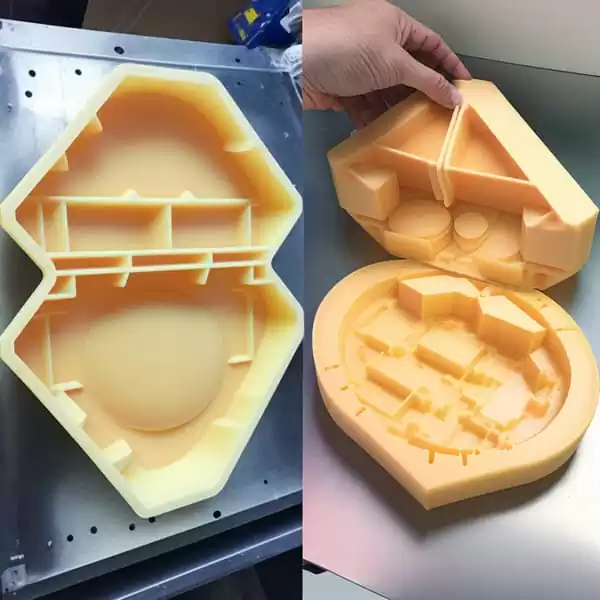
Koelsnelheid: De snelheid waarmee de top sheet molding compound wordt afgekoeld na compressie heeft invloed op de kristallisatie van het materiaal en vervolgens op de mechanische eigenschappen.
In het volgende deel gaan we na hoe simulatiesoftware gebruikt kan worden om deze parameters en variabelen te optimaliseren, wat uiteindelijk leidt tot betere persgietresultaten.
III. Rol van simulatiesoftware
Simulatiesoftware is een spelbreker op het gebied van persen. In dit hoofdstuk introduceren we het concept van simulatiesoftware in de context van persen, waarbij we benadrukken hoe het dient als een krachtig hulpmiddel voor het voorspellen van resultaten, het optimaliseren van procesparameters, het verminderen van defecten, het ontwerpen van matrijzen, het verbeteren van de materiaalselectie en uiteindelijk het besparen van tijd en waardevolle middelen.
Simulatiesoftware introduceren
Simulatiesoftware, in de context van persen, verwijst naar geavanceerde computergebaseerde tools waarmee fabrikanten virtuele modellen kunnen maken van het volledige spuitgietproces. Deze virtuele modellen bootsen echte omstandigheden na, waardoor ingenieurs en fabrikanten waardevolle inzichten krijgen in hoe verschillende parameters en variabelen het eindproduct zullen beïnvloeden. In wezen is het een digitale zandbak waar geëxperimenteerd wordt zonder dat er fysieke prototypes nodig zijn.
Uitkomsten met precisie voorspellen
Een van de belangrijkste voordelen van simulatiesoftware bij persgieten is de mogelijkheid om de resultaten nauwkeurig te voorspellen. Ingenieurs kunnen specifieke parameters zoals temperatuur, druk en materiaaleigenschappen in de simulatie invoeren. De software berekent dan hoe deze parameters op elkaar inwerken, zodat ze een duidelijk beeld krijgen van wat ze kunnen verwachten tijdens de eigenlijke productie. Dit voorspellend vermogen stelt fabrikanten in staat om hun processen nauwkeurig af te stellen voor optimale resultaten.
Procesparameters optimaliseren
Simulatiesoftware stopt niet bij voorspellen, maar blinkt ook uit in optimalisatie. Door simulaties uit te voeren met verschillende parametercombinaties kunnen fabrikanten de ideale instellingen voor hun persgietproces bepalen. Zo kunnen ze bijvoorbeeld de optimale temperatuur-drukcombinatie bepalen die resulteert in kortere cyclustijden, lagere productiekosten en een betere productkwaliteit. Deze optimalisatie is een cruciale stap in het bereiken van de best mogelijke simulatieresultaten van het compressievormproces.
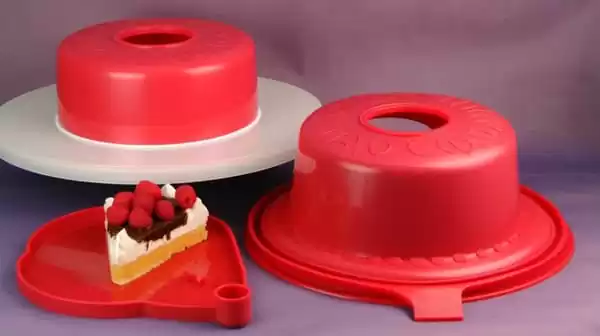
Reductie van defecten en verbetering van kwaliteit
In het streven naar uitmuntendheid is simulatiesoftware een krachtig hulpmiddel om defecten te beperken. Door het spuitgietproces te simuleren, kunnen fabrikanten potentiële defecten zoals holtes, kromtrekken of problemen met de materiaalstroom identificeren voordat ze zich in de echte productie voordoen. Gewapend met deze kennis kunnen er aanpassingen worden gemaakt aan het proces, waardoor defecten effectief worden verminderd en de algehele kwaliteit van het eindproduct wordt verbeterd.
Efficiënte mallen ontwerpen
Het ontwerpen van matrijzen is een cruciaal aspect van persgieten en simulatiesoftware helpt daar aanzienlijk bij. Ingenieurs kunnen de software gebruiken om matrijzen te ontwerpen met ingewikkelde geometrieën die alleen met vallen en opstaan moeilijk te realiseren zijn. De software zorgt ervoor dat matrijzen efficiënt zijn en consistent onderdelen van hoge kwaliteit kunnen produceren.
Verbeterde materiaalselectie
Met simulatiesoftware kunnen fabrikanten evalueren hoe verschillende materialen zich gedragen tijdens het persen. Dit is vooral waardevol bij geavanceerde materialen zoals vezelversterkte composieten. Door verschillende materiaalopties te simuleren, kunnen fabrikanten weloverwogen beslissingen nemen over welk materiaal het meest geschikt is voor een specifieke toepassing en zo optimale prestaties garanderen.
Tijd en middelen besparen
Een van de meest aantrekkelijke aspecten van simulatiesoftware is misschien wel de mogelijkheid om tijd en middelen te besparen. Traditionele trial-and-error methodes kunnen kostbaar en tijdrovend zijn, met meerdere fysieke prototypes en iteraties. Simulatiesoftware maakt veel van deze trial-and-error overbodig doordat ingenieurs processen digitaal kunnen verfijnen voordat ze overgaan tot fysieke productie.
In het volgende deel gaan we dieper in op de praktische stappen die fabrikanten kunnen nemen om de kracht van simulatiesoftware effectief in te zetten in het compressievormproces.
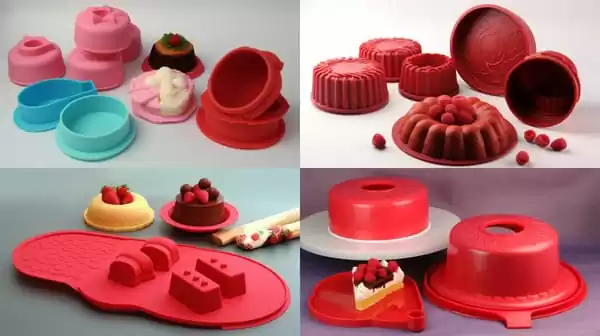
IV. Stappen om simulatiesoftware effectief te gebruiken
Simulatiesoftware effectief gebruiken bij persgieten vereist een systematische aanpak. Fabrikanten kunnen een stap-voor-stap handleiding volgen om de voordelen van dit krachtige hulpmiddel te maximaliseren. Hier volgt een uitgebreid overzicht van de belangrijkste stappen:
1. Gegevensverzameling
Effectieve simulatie begint met robuuste gegevensverzameling. Fabrikanten moeten alle relevante gegevens verzamelen, waaronder:
- Materiaaleigenschappen: Uitgebreide informatie over het gebruikte materiaal, zoals de viscositeit, smeltsnelheid, thermische geleidbaarheid en uithardingsgedrag.
- Vormspecificaties: Gedetailleerde specificaties van de mal, inclusief afmetingen, geometrie en ontluchtingsdetails.
- Procesparameters: Nauwkeurige gegevens over procesparameters zoals temperatuur, druk en cyclustijden.
- Historische gegevens: Alle productiegegevens uit het verleden of gegevens over defecten die het simulatieproces kunnen informeren.
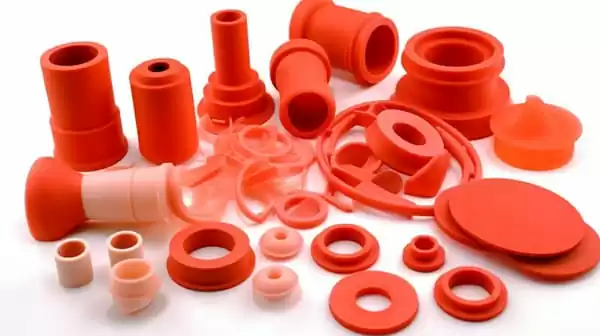
2. Modelcreatie
Met de gegevens in de hand is de volgende stap het maken van een virtueel model van het persgietproces. Dit houdt in:
- Geometrie creëren: Een 3D-weergave van de mal en het materiaal bouwen in de simulatiesoftware.
- Parameter Invoer: Alle verzamelde gegevens, inclusief materiaaleigenschappen en procesparameters, invoeren in het simulatiemodel.
- Randvoorwaarden: Randvoorwaarden definiëren, zoals begintemperaturen en drukken.
3. Simulatie
Zodra het model is voorbereid, wordt simulatiesoftware gebruikt om virtuele persgietprocessen uit te voeren. Tijdens deze fase:
- Simuleer het proces: De software voert simulaties uit op basis van het gedefinieerde model, waarbij het werkelijke compressievormproces wordt nagebootst.
- Gedrag controleren: Ingenieurs kunnen controleren hoe het materiaal stroomt, hoe de druk wordt verdeeld en hoe de temperatuur verandert binnen de virtuele mal.
4. Analyse
Nadat de simulatieruns zijn voltooid, is het tijd voor een grondige analyse:
- Identificatie van defecten: Bestudeer de simulatieresultaten om mogelijke defecten of problemen in het proces te identificeren. Denk hierbij aan holtes, kromtrekken of een inconsistente materiaalstroom.
- Mechanische eigenschappen: Analyseer de voorspelde mechanische eigenschappen van het eindproduct, zoals sterkte, stijfheid en veerkracht.
- Materiaalgedrag: Begrijpen hoe het materiaal zich gedraagt onder verschillende omstandigheden en drukken.
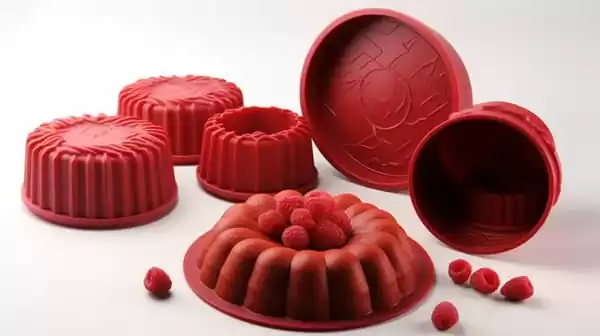
5. Optimalisatie
Met een duidelijk inzicht in de simulatieresultaten en geïdentificeerde verbeterpunten kunnen fabrikanten verder gaan met optimalisatie:
- Parameteraanpassingen: Procesparameters wijzigen, zoals temperatuur, druk of cyclustijd, om het persgietproces te optimaliseren.
- Materiaalkeuze: Overweeg op basis van simulatieresultaten verschillende materialen of materiaalmengsels die de eigenschappen van het eindproduct kunnen verbeteren.
- Vormontwerp: Pas het matrijsontwerp aan om de materiaalstroom te verbeteren en defecten te minimaliseren.
6. Validatie
Validatie is een cruciale stap om ervoor te zorgen dat de simulatieresultaten overeenkomen met de werkelijke resultaten:
- Vergelijk met gegevens uit de echte wereld: Valideer de simulatieresultaten door ze te vergelijken met werkelijke productiegegevens en fysieke prototypes.
- Itereren indien nodig: Als er verschillen worden vastgesteld, pas dan het simulatiemodel aan en voer aanvullende tests uit totdat de resultaten overeenkomen met de prestaties in de praktijk.
7. Implementatie
Implementeer ten slotte het geoptimaliseerde proces op basis van de simulatiebevindingen:
- Procesaanpassing: De herziene procesparameters, matrijsontwerpen of materiaalselecties implementeren in de werkelijke productie.
- Continue bewaking: De productie voortdurend bewaken om ervoor te zorgen dat de verbeteringen die door simulatie zijn bereikt, blijvend zijn.
- Terugkoppelingslus: Zorg voor een feedback-loop waarbij gegevens uit de echte wereldproductie worden gebruikt om het simulatiemodel verder te verfijnen en te verbeteren voor toekomstig gebruik.
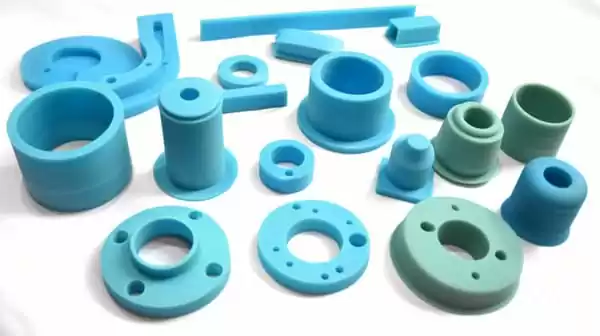
Door deze stappen systematisch te volgen, kunnen fabrikanten het volledige potentieel van simulatiesoftware voor persgieten benutten, wat leidt tot een betere productkwaliteit, minder defecten en efficiëntere productieprocessen.
IV. Wat is Moldflow-simulatie?
In de ingewikkelde wereld van de kunststofindustrie komt Moldflow-simulatie naar voren als een gespecialiseerd en onmisbaar hulpmiddel. In dit hoofdstuk wordt Moldflow simulatie gedefinieerd en uitgelegd, en wordt de rol belicht die het speelt bij het begrijpen van materiaalstroming en -distributie binnen matrijzen.
Moldflow-simulatie definiëren
Moldflow-simulatie is zeer gespecialiseerde software die gebruikt wordt in de kunststofindustrie. De belangrijkste functie is het creëren van virtuele representaties van het gehele spuitgietproces, zodat fabrikanten een goed inzicht krijgen in hoe gesmolten kunststof materiaal stroomt en zich verspreidt binnen matrijzen. Deze tool fungeert als een virtueel laboratorium dat inzicht geeft in het complexe gedrag van materialen tijdens het spuitgietproces.
Materiaalstroom en distributie begrijpen
Moldflow simulatie blinkt uit in zijn vermogen om materiaalstroming en -distributie met een hoge mate van precisie te simuleren en te analyseren. Dit is hoe het dit bereikt:
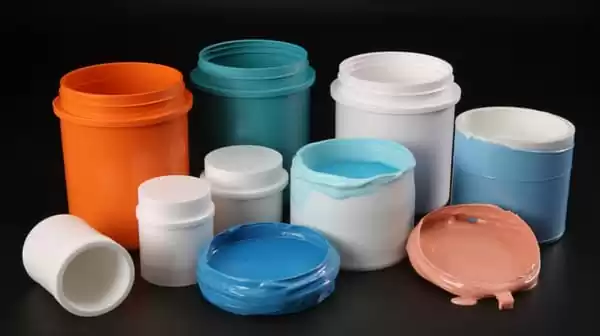
- Materiaalgedrag: Moldflow simulatie begint met het beschouwen van de eigenschappen van het gebruikte kunststofmateriaal. Dit omvat aspecten zoals smeltviscositeit, temperatuurafhankelijk gedrag en reologische eigenschappen.
- Meetkundige analyse: De software houdt vervolgens rekening met de geometrie van de matrijsholte, inclusief de ingewikkelde elementen, poorten, runners en koelkanalen. Deze analyse is cruciaal om te begrijpen hoe het materiaal in de matrijs zal stromen.
- Injectiesimulatie: Het hart van de Moldflow simulatie ligt in het vermogen om de injectiefase te simuleren. Het voorspelt hoe het gesmolten kunststofmateriaal de matrijs ingaat, hoe het alle hoeken en gaten vult en hoe de druk wordt verdeeld.
- Stroom Visualisatie: Door de simulatie genereert Moldflow visuele weergaven van de materiaalstroom. Dit kunnen stromingsfronten, drukprofielen en temperatuurgradiënten zijn, zodat ingenieurs en fabrikanten een duidelijk beeld krijgen van wat er in de matrijs gebeurt.
- Identificatie van defecten: Moldflow simulatie is ook bedreven in het identificeren van potentiële defecten die kunnen optreden tijdens het spuitgietproces. Hieronder vallen zaken als luchtinsluitingen, lasnaden, zinksporen en onvolledig vullen.
Rol in matrijsontwerp en -optimalisatie
Moldflow simulatie gaat niet alleen over het begrijpen van de materiaalstroom; het is ook belangrijk bij het ontwerpen en optimaliseren van matrijzen. Dit is hoe:
- Vormontwerp: Ingenieurs kunnen Moldflow-simulatie gebruiken om matrijsontwerpen te verfijnen, zodat de materiaalstroom uniform is en defecten tot een minimum worden beperkt. Dit kan inhouden dat de poortlocaties worden gewijzigd, runnersystemen worden aangepast en koelstrategieën worden geoptimaliseerd.
- Materiaalkeuze: Met de simulatie kunnen verschillende materialen en hun gedrag in de matrijs worden geëvalueerd. Fabrikanten kunnen op basis van de simulatieresultaten het meest geschikte materiaal kiezen.
- Optimalisatie: Moldflow simulatie helpt bij het optimaliseren van procesparameters, zoals injectiesnelheid, smelttemperatuur en koelsnelheid, om de best mogelijke spuitgietresultaten te verkrijgen.
Samengevat is Moldflow-simulatie een gespecialiseerd softwareprogramma dat is ontworpen voor de kunststofindustrie. Het speelt een centrale rol in het begrijpen hoe gesmolten kunststof materiaal stroomt en zich verdeelt binnen matrijzen tijdens het spuitgietproces. Door materiaalgedrag, matrijsgeometrie en de injectiefase te simuleren, biedt Moldflow inzichten van onschatbare waarde in de complexe wereld van het spuitgieten van kunststoffen. Het helpt niet alleen bij het identificeren van defecten, maar stuurt ook het matrijsontwerp en de procesoptimalisatie, wat uiteindelijk leidt tot efficiëntere en effectievere spuitgietprocessen. plastic onderdelen van hogere kwaliteit.
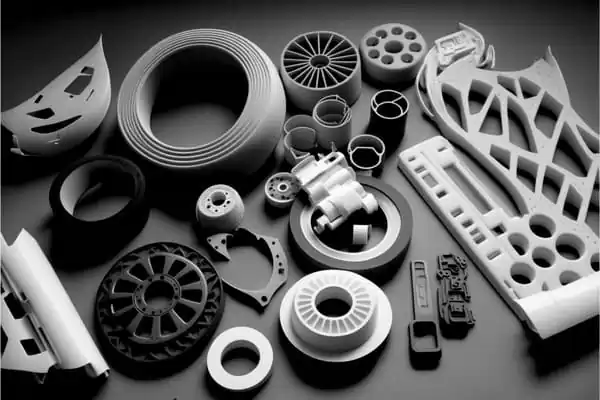
V. Parameters regelen in het persgietproces
Het succes van het compressievormproces hangt af van een zorgvuldige controle van verschillende parameters en variabelen. In dit hoofdstuk geven we een overzicht van en uitleg over de regelparameters die een cruciale rol spelen bij het bereiken van optimale compressievormresultaten:
1. Temperatuur:
- Uitleg: Temperatuurregeling is fundamenteel bij persen. Het beïnvloedt het materiaalgedrag door de viscositeit, de smeltstroom en de uithardingseigenschappen te beïnvloeden. Het precieze temperatuurprofiel tijdens de verwarmings- en afkoelfasen is cruciaal voor de productkwaliteit.
2. Druk:
- Uitleg: Druk is een andere belangrijke parameter bij persen. Een goed gecontroleerde druk zorgt voor een gelijkmatige verdeling van het materiaal, minimaliseert defecten zoals holtes of kromtrekken en verdicht het materiaal in de gewenste vorm in de matrijsholte.
3. Tijd:
- Uitleg: Tijd is een kritieke parameter die de duur van elke fase van het persgietproces bepaalt. Zorgvuldige timing is essentieel om de gewenste materiaalharding, koeling en algemene procesefficiëntie te bereiken.
4. Materiaaleigenschappen:
- Uitleg: De eigenschappen van het materiaal dat gevormd wordt, hebben een grote invloed op het compressievormproces. Deze eigenschappen omvatten viscositeit, smeltsnelheid, thermische geleidbaarheid, uithardingsgedrag en zelfs de reologische eigenschappen van het materiaal. Het begrijpen en optimaliseren van deze materiaaleigenschappen is essentieel voor succesvol gieten.
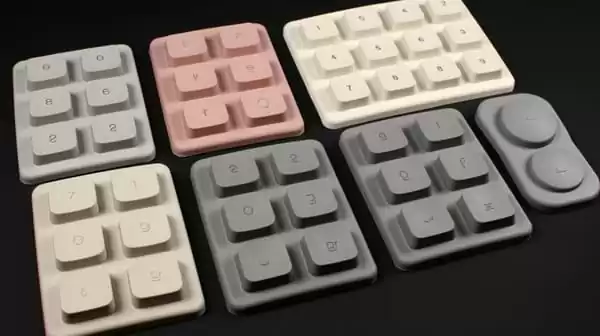
5. Vormontwerp:
- Uitleg: De geometrie van de matrijsholte en andere kenmerken zoals openingen, runners en koelkanalen hebben een grote invloed op de materiaalstroom, de distributie en de uiteindelijke kwaliteit van het product. Een goed ontworpen matrijs zorgt voor een efficiënte materiaalverdichting en minimaliseert defecten.
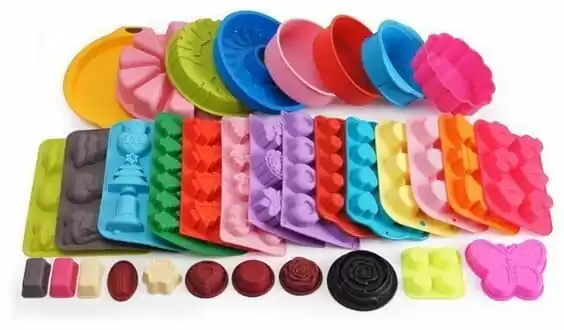
6. Drukverdeling:
- Uitleg: Niet alleen de totale druk is cruciaal, maar ook de verdeling van de druk over het matrijsoppervlak. Een gelijkmatige drukverdeling zorgt voor een consistente materiaalverdichting en minimaliseert defecten zoals ongelijke dikte of holtes in het eindproduct.
7. Koelsnelheid:
- Uitleg: De snelheid waarmee de matrijs na compressie wordt afgekoeld, heeft een grote invloed op de kristallisatie van het materiaal en dus op de mechanische eigenschappen. Een nauwkeurige regeling van de koelsnelheid is essentieel om de gewenste deeleigenschappen te bereiken.
8. Temperatuur maloppervlak:
- Uitleg: Het regelen van de temperatuur van het matrijsoppervlak is van vitaal belang om ervoor te zorgen dat het materiaal goed uithardt en vrijkomt uit de matrijs. De temperatuur van het matrijsoppervlak beïnvloedt het gedrag van het materiaal tijdens zowel de verwarmings- als de afkoelfase.
9. Materiaalstroomanalyse:
- Uitleg: Begrijpen hoe het materiaal in de matrijs stroomt, is essentieel om parameters zoals druk en temperatuur te controleren. Het analyseren van de materiaalstroom kan helpen om probleemgebieden te identificeren en het spuitgietproces te optimaliseren.
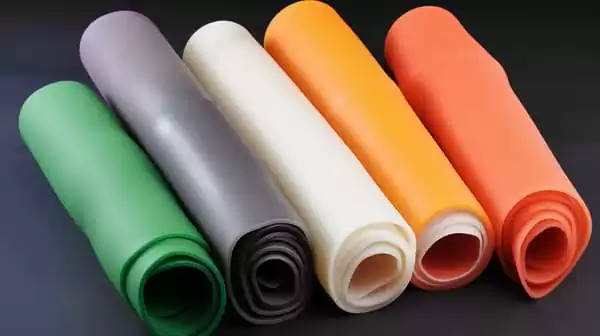
10. Ventilatie en luchtafvoer:
- Uitleg: Een goede ontluchting en luchtafvoer zijn nodig om te voorkomen dat er lucht of gas in de mal blijft hangen. Een goede ontluchting zorgt voor een volledige materiaalverdichting en minimaliseert defecten.
Deze regelparameters bepalen samen de omstandigheden waaronder het persgieten plaatsvindt. Het nauwkeurige beheer van deze parameters is van cruciaal belang om consistente resultaten van hoge kwaliteit te bereiken en een efficiënte productie van spuitgietproducten te garanderen. Fabrikanten moeten elke parameter zorgvuldig overwegen en optimaliseren om te voldoen aan hun specifieke productvereisten en kwaliteitsnormen.
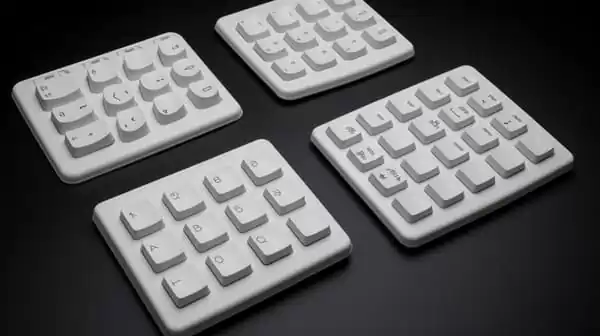
Conclusie
Concluderend kan gesteld worden dat dit artikel het domein van compressievormen heeft verkend en het belang en de fijne kneepjes van het bereiken van optimale resultaten heeft belicht. We hebben de cruciale rol van simulatiesoftware benadrukt bij het aanpakken van deze uitdagingen en het optimaliseren van het compressievormproces. Dit zijn de belangrijkste punten:
- Betekenis van persen: Compression molding is een cruciaal productieproces dat in verschillende industrieën wordt gebruikt en waarmee complexe onderdelen met precisie en efficiëntie kunnen worden gemaakt.
- Uitdagingen bij het persen: Om optimale compressievormresultaten te bereiken, moeten parameters zoals temperatuur, druk, tijd, materiaaleigenschappen en matrijsontwerp nauwkeurig geregeld worden. Complexiteit in materiaalgedrag en matrijsontwerp kan leiden tot defecten en inefficiëntie.
- De kracht van simulatiesoftware: Simulatiesoftware is een spelbreker op het gebied van persgieten. Het stelt fabrikanten in staat om virtuele modellen van het proces te maken, resultaten te voorspellen, parameters te optimaliseren en defecten te verminderen voordat de fysieke productie begint.
- Stappen naar effectief simulatiegebruik: Fabrikanten kunnen een gestructureerde aanpak volgen, inclusief het verzamelen van gegevens, het maken van modellen, simulatie, analyse, optimalisatie, validatie en implementatie, om simulatiesoftware effectief te gebruiken.
- Moldflow-simulatie: Moldflow-simulatie, een gespecialiseerd hulpmiddel voor de kunststofindustrie, speelt een cruciale rol bij het begrijpen van materiaalstroming en -distributie binnen matrijzen. Het helpt bij defectidentificatie, matrijsontwerp, materiaalselectie en procesoptimalisatie.
- Parameters regelen: De belangrijkste controleparameters bij persen zijn temperatuur, druk, tijd, materiaaleigenschappen, matrijsontwerp, drukverdeling, koelsnelheid, matrijsoppervlaktetemperatuur, materiaalstroomanalyse en ontluchting. Een nauwkeurige regeling van deze parameters is essentieel voor consistente resultaten van hoge kwaliteit.
- De toekomst van simulatie van spuitgieten: Het artikel eindigt met het onderstrepen van het belang van simulatiesoftware voor het bereiken van consistente en superieure compressievormresultaten. Het is via het digitale domein van simulatie dat fabrikanten kunnen innoveren, optimaliseren en zich aanpassen aan het veranderende landschap van werktuigbouwkunde en polymeerverwerking. Naarmate de technologie voortschrijdt, kunnen we verwachten dat simulatietools nog belangrijker worden bij het vormgeven van de toekomst van productie.
In de steeds veranderende wereld van werktuigbouwkunde en polymeerverwerking is simulatiesoftware het kompas dat ons leidt naar grotere efficiëntie, innovatie en uitmuntendheid in compressievormen. Met elke simulatie komen we dichter bij het perfectioneren van de kunst van het maken van precisiecomponenten terwijl we kostbare tijd en middelen besparen. Als we vooruit kijken, verwachten we dat simulatiesoftware een transformerende rol zal blijven spelen in het verleggen van de grenzen van wat mogelijk is in productie, zodat compressievormen een hoeksteen van de moderne productie blijft.