Inleiding:
Drukgieten van siliconenrubber is een veelgebruikt productieproces waarbij vloeibaar siliconenrubber in een vormholte wordt gevormd en uitgehard. Deze veelzijdige methode staat bekend om zijn vermogen om duurzame en hittebestendige producten te maken. Bij de productie van grote volumes kunnen zich echter bepaalde uitdagingen voordoen die een zorgvuldige afweging en strategische oplossingen vereisen.
Productie van grote volumes brengt unieke uitdagingen met zich mee bij het spuitgieten van siliconenrubber. De schaal en de snelheid van de productie kunnen van invloed zijn op factoren zoals de consistentie van de matrijsvulling, de efficiëntie van de cyclustijd en het optreden van defecten zoals uitvloeiing. Deze uitdagingen kunnen de productiviteit belemmeren, de productkwaliteit beïnvloeden en de productiekosten verhogen als ze niet op de juiste manier worden aangepakt.
Het aanpakken van deze uitdagingen is van het grootste belang voor een succesvolle productie. Door effectieve strategieën te begrijpen en te implementeren, kunnen fabrikanten het compressievormproces optimaliseren, productieproblemen minimaliseren en een consistente kwaliteit bereiken bij de productie van grote volumes. Dit zorgt ervoor dat producten voldoen aan de eisen van de markt, voldoen aan strenge specificaties en betrouwbare prestaties leveren.
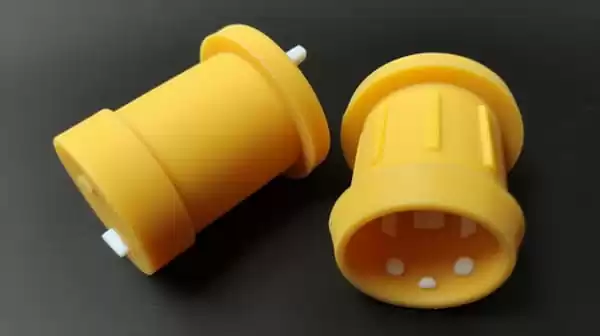
In de volgende paragrafen gaan we dieper in op de specifieke uitdagingen in grote volumes spuitgieten van siliconenrubber en ontdek waardevolle inzichten over hoe deze effectief kunnen worden overwonnen. Door deze uitdagingen frontaal aan te pakken, kunnen fabrikanten het volledige potentieel van hoogvolumeproductie benutten en uitzonderlijke siliconenrubberproducten leveren aan diverse industrieën.
Problemen met persen:
Compression molding is weliswaar een veelgebruikt productieproces, maar niet zonder uitdagingen. Fabrikanten krijgen vaak te maken met een aantal veelvoorkomende problemen die de productie-efficiëntie en productkwaliteit kunnen beïnvloeden. Hier zijn enkele belangrijke problemen in verband met persen:
1.Inconsistente vormvulling:
Een consistente vulling van de matrijs is essentieel voor het verkrijgen van uniform gegoten producten. Bij de productie van grote volumes kunnen variaties optreden in de materiaalstroom en -verdeling, wat kan leiden tot een inconsistente vulling van de matrijsholten. Dit kan leiden tot variaties in productafmetingen, oppervlaktedefecten en een verminderde productkwaliteit.
2.Langere cyclustijden:
In vergelijking met andere spuitgiettechnieken, zoals spuitgieten, heeft compressievormen over het algemeen een langere cyclustijd. Het proces omvat het samendrukken en uitharden van het siliconenrubber in de matrijs, wat meer tijd in beslag kan nemen. In hoog-volume productieLangere cyclustijden kunnen de totale output beperken en het productieproces vertragen.
3.Flitsvorming:
Flash verwijst naar overtollig materiaal dat uit de matrijsholte ontsnapt tijdens het persgieten. Het ontstaat door factoren zoals een verkeerd matrijsontwerp, een te grote hoeveelheid materiaal of onvoldoende klemkracht. Bij flashvorming wordt niet alleen materiaal verspild, maar is ook extra nabewerking nodig om het overtollige materiaal te verwijderen of bij te snijden. Dit leidt tot hogere productiekosten en mogelijke kwaliteitsproblemen.
Deze problemen kunnen de productie-efficiëntie en de productkwaliteit bij grote volumes persgieten aanzienlijk beïnvloeden. Inconsistente matrijsvulling kan resulteren in onderdelen met verschillende afmetingen en oppervlaktedefecten, wat leidt tot afgekeurde producten en meer afval. Langere cyclustijden verlagen de totale productie-output, wat het vermogen om aan de marktvraag te voldoen beïnvloedt. Flashvorming zorgt niet alleen voor meer materiaalverspilling, maar vereist ook extra tijd en middelen voor nabewerking, wat de algehele productiviteit en kosteneffectiviteit van het productieproces beïnvloedt.
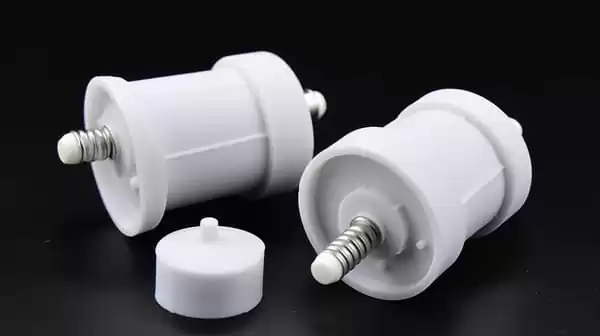
Het aanpakken van deze problemen is cruciaal om een efficiënte productie van hoge kwaliteit te garanderen. In de volgende secties verkennen we effectieve strategieën om deze uitdagingen te overwinnen in Hoog-volume siliconenrubber compressie en spuitgiettoepassingen. Door deze strategieën te implementeren, kunnen fabrikanten het proces optimaliseren, de productiviteit verhogen en superieure producten leveren die voldoen aan de eisen van de markt.
Groot nadeel van persen:
Het grote nadeel van compressievormen, vooral bij grote productievolumes, is de lagere productiesnelheid in vergelijking met andere spuitgiettechnieken. In tegenstelling tot snellere processen zoals spuitgieten, zijn er bij persen extra stappen nodig zoals de voorbereiding van het materiaal, het handmatig of automatisch vullen van de matrijs en het comprimeren en uitharden van het siliconenrubber. Deze stappen zorgen voor langere cyclustijden, wat de totale productie kan beperken en de efficiëntie van volumeproductie kan beïnvloeden.
De gevolgen van een lagere productiesnelheid bij grote volumes persgieten zijn aanzienlijk. Ten eerste kan het een belemmering vormen om strakke productiedeadlines te halen en aan de marktvraag te blijven voldoen. De langere cyclustijden die gepaard gaan met persen kunnen niet overeenkomen met de gewenste productiesnelheden die nodig zijn om grote orders binnen een kort tijdsbestek uit te voeren. Dit kan leiden tot vertragingen in de productlevering en mogelijk de klanttevredenheid beïnvloeden.
Bovendien kan een lagere productiesnelheid financiële gevolgen hebben. Bij productie van grote volumes wordt vaak gestreefd naar schaalvoordelen, waarbij hogere productiehoeveelheden helpen om de kosten per eenheid te verlagen. De lagere snelheid van compressievormen kan echter de totale output verlagen, wat resulteert in hogere productiekosten per eenheid. Dit kan de winstgevendheid en het concurrentievermogen op de markt beïnvloeden.
Daarnaast kan de lagere productiesnelheid van invloed zijn op het vermogen om zich snel aan te passen aan veranderingen in de markt of om nieuwe productontwerpen te introduceren. In snelle industrieën is het van cruciaal belang om snel te kunnen reageren op vragen uit de markt of wijzigingen in het ontwerp. Het tijdrovende karakter van persgieten kan de beweeglijkheid en flexibiliteit in de productie beperken.
Ondanks dit nadeel biedt compressievormen voordelen op het vlak van veelzijdigheid, materiaalopties en de mogelijkheid om complexe deelgeometrieën te verwerken. Het heeft vaak de voorkeur voor specifieke toepassingen die unieke eigenschappen of ingewikkelde ontwerpen vereisen. Door strategieën te implementeren om het proces te optimaliseren en de cyclustijden te minimaliseren, kunnen fabrikanten de impact van een lagere productiesnelheid beperken en de voordelen van compressievormen maximaliseren in scenario's met hoge volumes.
Factoren die het persgietproces beïnvloeden:
Verschillende sleutelfactoren beïnvloeden het persgietproces en spelen een cruciale rol bij het vullen van de matrijs, het persen, het ontvormen en de algehele productkwaliteit. Het begrijpen en effectief beheren van deze factoren is essentieel voor het bereiken van consistente resultaten van hoge kwaliteit. Laten we de sleutelfactoren eens nader bekijken:
1.Mold Ontwerp:
Het matrijsontwerp speelt een cruciale rol bij persen. Factoren zoals matrijsholtes, runnersystemen en deellijnen beïnvloeden de materiaalstroom, het vullen van de matrijs en de compressie van het product. Goed ontworpen matrijzen zorgen voor een gelijkmatige materiaalverdeling, waardoor de afmetingen van het product consistent blijven en er minder defecten optreden.
2.Mold Temperatuur:
Het regelen van de matrijstemperatuur is cruciaal bij persen. De matrijstemperatuur beïnvloedt de materiaalstroom, het vulkanisatieproces en de eigenschappen van het product. Een goed beheer van de matrijstemperatuur zorgt voor een optimale materiaalstroom in de matrijsholten, bevordert een gelijkmatige uitharding en verbetert de mechanische eigenschappen van het eindproduct.
3.Klemkracht:
De juiste klemkracht is essentieel voor een goede compressie en consolidatie van het onderdeel. Onvoldoende klemkracht kan leiden tot onvolledige vulling en slechte productkwaliteit, terwijl overmatige klemkracht kan leiden tot vliesvorming. Zorgvuldige controle van de klemkracht zorgt voor een gelijkmatige compressie in de matrijsholten, wat leidt tot consistente productafmetingen en oppervlakteafwerking.
4.Materiaaleigenschappen:
De eigenschappen van het siliconenrubber dat bij het persen wordt gebruikt, hebben een grote invloed op het proces en de productkwaliteit. Viscositeit, uithardingstijd, rubber met een hoge consistentie en mechanische eigenschappen van het materiaal beïnvloeden de vulling van de matrijs, de vloei en de prestaties van het uiteindelijke onderdeel. Het selecteren van het juiste materiaal met geschikte eigenschappen voor de toepassing is cruciaal om de gewenste resultaten te bereiken.
5.Mold Lossingsmiddelen:
Lossingsmiddelen worden gebruikt om het ontvormen van de uitgeharde onderdelen uit de mal te vergemakkelijken. Een juiste toepassing van lossingsmiddelen minimaliseert het kleven en zorgt voor een soepele verwijdering van de onderdelen, waardoor de kans op schade of defecten tijdens het ontvormen afneemt.
6.Sprue Bushing Ontwerp:
Het ontwerp van de schroefdraadbus, die de matrijs met de injectie-eenheid verbindt, kan de materiaalstroom en het vullen van de matrijsholten beïnvloeden. Een efficiënt ontwerp van de doorvoerbus helpt om de stroomsnelheid te regelen, luchtinsluiting te voorkomen en een gelijkmatige materiaalverdeling in de matrijs te garanderen.
Deze factoren hebben samen invloed op het vullen van de matrijs, het persen, het ontvormen en de algehele productkwaliteit bij persen. Een optimaal matrijsontwerp, de juiste regeling van de matrijstemperatuur, nauwkeurig beheer van de sluitkracht, geschikte materiaalselectie, effectief gebruik van lossingsmiddelen voor matrijzen en een doordacht ontwerp van de doorvoeropeningen dragen bij tot consistente productafmetingen, minder defecten en een betere kwaliteit van het eindproduct.
Door deze factoren te begrijpen en te optimaliseren, kunnen fabrikanten de procesefficiëntie verbeteren, de gewenste producteigenschappen bereiken en het succes van hun producten garanderen. productie van hoogwaardige siliconenrubberproducten door persgieten.
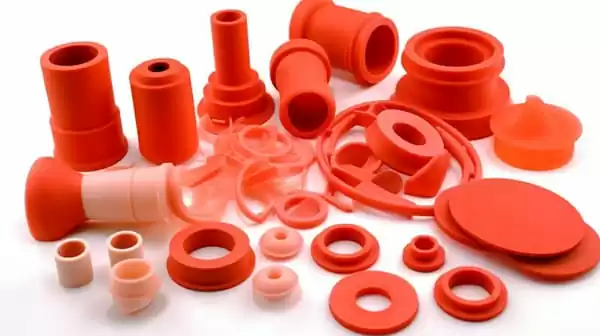
Defecten aan rubbergieten:
Rubbergieten, inclusief het rubberpersgietproces, kan gevoelig zijn voor verschillende defecten die de functionaliteit en het uiterlijk van het eindproduct kunnen beïnvloeden. Het aanpakken en minimaliseren van deze defecten is cruciaal voor het bereiken van resultaten van hoge kwaliteit. Laten we eens kijken naar enkele veelvoorkomende defecten bij het spuitgieten van rubber:
1.Flash:
Flash verwijst naar overtollig materiaal dat tijdens het spuitgieten uit de matrijsholte ontsnapt. Het komt meestal voor bij de deellijnen of gebieden van de matrijs met openingen of verkeerde uitlijning. Flash kan de maatnauwkeurigheid van het product in gevaar brengen en resulteren in overtollig materiaal of ongewenste uitsteeksels op het uiteindelijke onderdeel. Het kan extra nabewerking vereisen, zoals bijsnijden of secundaire bewerkingen, om de uitsteeksels te verwijderen, waardoor de productietijd en -kosten toenemen.
2.Luchtinsluiting:
Luchtinsluiting doet zich voor wanneer er tijdens het spuitgietproces lucht of gas vast komt te zitten in het spuitgietproduct. Dit kan worden veroorzaakt door een onjuiste ontluchting, een ondeugdelijk matrijsontwerp of onvoldoende matrijsvulling. Luchtinsluiting kan leiden tot onvolledige vulling, structurele zwakheden en de vorming van holtes in het onderdeel. Deze holtes kunnen de mechanische eigenschappen, zoals sterkte of duurzaamheid, van het eindproduct beïnvloeden, waardoor de functionaliteit in het gedrang komt.
3.Oppervlakteonvolmaaktheden:
Oppervlakte-imperfecties kunnen zich manifesteren als krassen, vlekken, ruwheid of andere onregelmatigheden op het oppervlak van het gegoten product. Deze onvolkomenheden kunnen het gevolg zijn van factoren zoals defecten aan het matrijsoppervlak, slechte materiaalstroom of onvoldoende controle van de matrijstemperatuur. Oppervlakteonvolmaaktheden beïnvloeden niet alleen het esthetische uitzicht van het product, maar kunnen ook de functionaliteit beïnvloeden, vooral in toepassingen waar een glad oppervlak essentieel is, zoals afdichtings- of contactoppervlakken.
4.Inconsistenties in afmetingen:
Maatafwijkingen zijn variaties in grootte, vorm of dikte van het spuitgietproduct. Deze variaties kunnen ontstaan door zaken als onjuiste matrijsontwerpOnjuiste vulling van de matrijs of ongelijkmatige compressie. Maatafwijkingen kunnen de pasvorm, assemblage of prestaties van het eindproduct beïnvloeden, waardoor het een uitdaging wordt om nauwkeurige toleranties te bereiken of aan specifieke functionele eisen te voldoen.
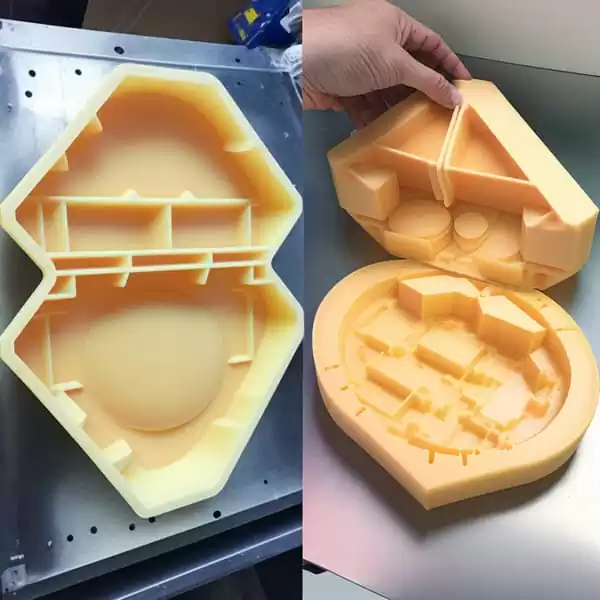
Deze defecten kunnen belangrijke gevolgen hebben voor de functionaliteit en het uiterlijk van het eindproduct. Overmatige vervorming kan leiden tot een slechte esthetiek, de functionaliteit van het product verstoren of problemen veroorzaken tijdens de assemblage. Luchtinsluiting en holtes kunnen de structurele integriteit van het onderdeel verzwakken, waardoor de sterkte of duurzaamheid wordt aangetast. Oppervlakte-imperfecties brengen niet alleen de visuele aantrekkingskracht in gevaar, maar kunnen ook de functionele eigenschappen beïnvloeden, zoals wrijving, afdichtingsvermogen of contacteigenschappen. Inconsistenties in de afmetingen kunnen een goede passing belemmeren, interfereren met parallelle onderdelen of resulteren in verkeerde uitlijningen, wat de algehele prestaties of functionaliteit van het product beïnvloedt.
Door het implementeren van een effectief ontwerp van het transfer gietproces, het optimaliseren van de procesparameters en het uitvoeren van strenge kwaliteitscontrolemaatregelen, kunnen fabrikanten deze defecten bij het rubbergieten minimaliseren en zo producten van hoge kwaliteit garanderen die voldoen aan de gewenste functionele en esthetische eisen.
Strategieën voor het overwinnen van uitdagingen bij het hoogvolume spuitgieten van siliconenrubber:
De uitdagingen van grote volumes spuitgieten van siliconenrubber vereist een systematische aanpak en implementatie van effectieve strategieën. Hier volgen enkele belangrijke strategieën om deze uitdagingen aan te gaan:
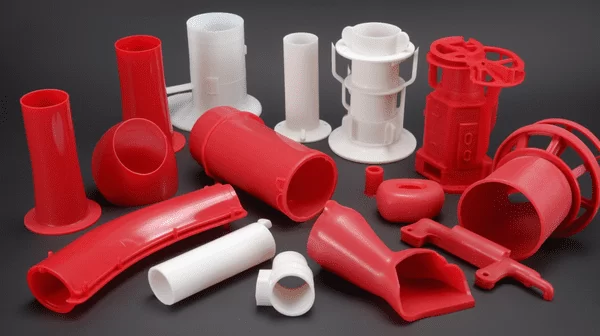
1. Consistente vormvulling:
Optimaliseer het matrijsontwerp om te zorgen voor het juiste ontwerp van de runner en het gatesysteem voor een gelijkmatige materiaalstroom.
Gebruikmaken van geavanceerde procesbewakingstechnieken zoals real-time druk- en temperatuurmeting om variaties te identificeren en de nodige aanpassingen te doen.
Voer een matrijsstroomanalyse uit om de matrijsontwerp en zorgen voor een consistente vulling van de mal.
2.Efficiënte cyclustijden:
Geavanceerde software voor matrijsontwerp en simulatietools gebruiken om mogelijke knelpunten te identificeren en het matrijsontwerp te optimaliseren voor snellere cyclustijden.
Selecteer hoogwaardige siliconenrubberverbindingen speciaal geformuleerd voor snelle uitharding om de totale cyclustijd te verkorten.
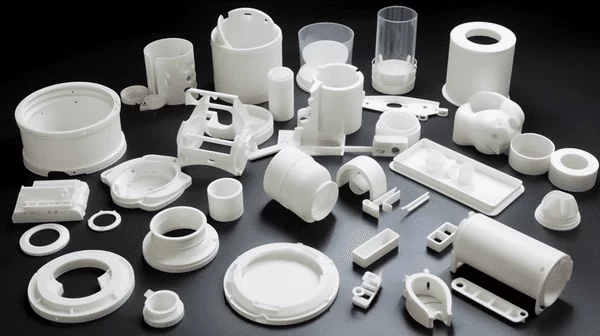
Optimaliseer procesparameters zoals temperatuur, druk en tijd om de uithardingstijd te minimaliseren en de productie-efficiëntie te verhogen.
3. Flitsbesturing:
Richt je op het juiste matrijsontwerp en precieze controle van de klemkracht om de vorming van flash te minimaliseren.
De matrijstemperatuur regelen om een goede materiaalstroom te garanderen en overmatige flash te voorkomen.
Strikte kwaliteitscontrolemaatregelen implementeren, waaronder regelmatige inspectie en controle, om vlamgerelateerde defecten snel te identificeren en aan te pakken.
4.Schimmel Onderhoud:
Stel een preventief onderhoudsschema op voor matrijzen om hun levensduur en consistente prestaties te garanderen.
Maak mallen regelmatig schoon en gebruik geschikte lossingsmiddelen om plakken te voorkomen en het ontvormen te verbeteren.
De juiste opslagtechnieken voor mallen toepassen om schade te voorkomen en ervoor te zorgen dat mallen klaar zijn voor efficiënte productie.
5. Materiële kwaliteit:
Nauw samenwerken met gerenommeerde materiaalleveranciers om te zorgen voor consistente en hoogwaardige siliconenrubbersamenstellingen.
Stel duidelijke specificaties en normen op voor materiaaleigenschappen en voer regelmatig testen uit om te controleren of deze worden nageleefd.
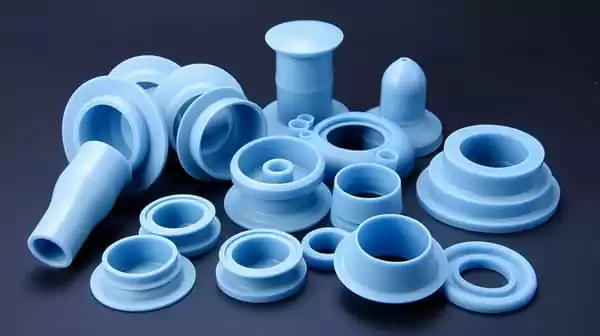
Voer strenge materiaaltests uit om de geschiktheid van het rubbermateriaal voor de beoogde toepassing te garanderen en defecten te minimaliseren.
6.Optimalisatie van het matrijsontwerp:
Geavanceerde software voor matrijsontwerp en simulatietools gebruiken om matrijsholten, runnersystemen en deellijnen te optimaliseren voor efficiënte productie en minimaal afval.
Mallen ontwerpen met de juiste ontluchtings- en afsluitsystemen om luchtinsluiting te minimaliseren en een gelijkmatige materiaalstroom te garanderen.
Houd rekening met factoren zoals de matrijstemperatuur, het ontwerp van de doorvoeropeningen en lossingsmiddelen om een goede materiaalstroom, ontvorming en oppervlaktekwaliteit te bevorderen.
7.Procesbewaking en inspectie:
Real-time procesbewakingstechnieken implementeren om variaties en potentiële problemen tijdens de productie te identificeren.
Het persgietproces regelmatig inspecteren en controleren om ervoor te zorgen dat de kwaliteitsnormen worden nageleefd en om eventuele afwijkingen of defecten te identificeren.
Statistische procescontrolemethoden (SPC) gebruiken om procesgegevens bij te houden en te analyseren, zodat proactieve aanpassingen en voortdurende verbetering mogelijk zijn.
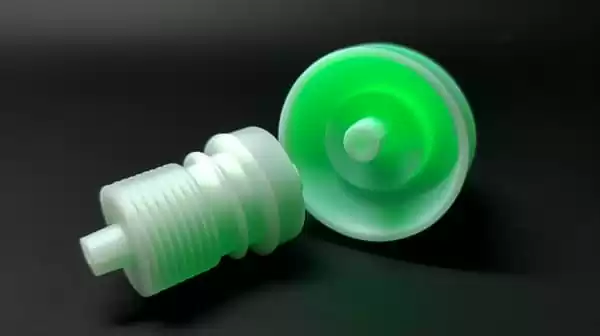
Door deze strategieën te implementeren, kunnen fabrikanten de uitdagingen van grote volumes spuitgieten van siliconenrubber. Consistente matrijsvulling, efficiënte cyclustijden, spanningscontrole, matrijsonderhoud en materiaalkwaliteit spelen een cruciale rol bij het bereiken van succesvolle productieresultaten. Het optimaliseren van het matrijsontwerp, het bewaken van het proces en het werken met gerenommeerde materiaalleveranciers dragen bij aan een hogere productiviteit, verbeterde productkwaliteit en kosteneffectieve productie.
Conclusie:
Samenvattend heeft het vormen van grote volumes siliconenrubber compressiegieten zijn eigen unieke uitdagingen die moeten worden aangepakt voor een succesvolle productie. In dit artikel hebben we deze uitdagingen onderzocht en waardevolle inzichten gegeven in hoe ze effectief overwonnen kunnen worden.
Consistente matrijsvulling, efficiënte cyclustijden, knippatrooncontrole, matrijsonderhoud en materiaalkwaliteit zijn belangrijke aandachtspunten. Door deze aspecten zorgvuldig te plannen en te optimaliseren, kunnen fabrikanten de productiviteit aanzienlijk verbeteren en de kwaliteit van de eindproducten verhogen.
Om de uitdagingen van het persen van grote volumes siliconenrubber het hoofd te bieden, zijn een systematische aanpak en de implementatie van effectieve strategieën nodig. Dit omvat het optimaliseren van spuitgieten met vloeistof door het ontwerp, het gebruik van geavanceerde procesbewakingstechnieken, regelmatige inspecties en het werken met gerenommeerde materiaalleveranciers.
Door deze uitdagingen te overwinnen, kunnen fabrikanten hun productiviteit verhogen, de productkwaliteit verbeteren en effectief voldoen aan de eisen van de markt. Dit kan leiden tot grotere klanttevredenheid, hogere winstgevendheid en een concurrentievoordeel in de branche.
De conclusie is dat zorgvuldige planning, optimalisatie en implementatie van deze strategieën van cruciaal belang zijn voor fabrikanten die grote volumes siliconenrubber willen persen. Door hun processen voortdurend te verbeteren en te verfijnen, kunnen fabrikanten het volledige potentieel van deze productiemethode benutten en uitzonderlijke siliconenrubberproducten leveren die voldoen aan de uiteenlopende behoeften van de markt.