1. Kenmerken van siliconenmateriaal
A. Siliconengrondstoffen zijn over het algemeen gelvormig, enigszins te vergelijken met plasticine, kleurloos, doorzichtig en geurloos.
B. De belangrijkste eigenschappen zijn zowel hoge temperatuurbestendigheid (tot 300°C) als lage temperatuurbestendigheid (minimaal -100°C), wat momenteel het beste koudebestendige en hoge temperatuurbestendige rubber is; tegelijkertijd heeft het uitstekende elektrische isolatie en een hoge stabiliteit tegen thermische oxidatie en ozon, en is het chemisch inert.
Het nadeel is dat de mechanische sterkte laag is, de oliebestendigheid, oplosmiddelbestendigheid en zuur- en alkalibestendigheid slecht zijn, het moeilijk is om te vulkaniseren en de prijs duurder is. Bedrijfstemperatuur: -60℃~+200℃. Het bovenstaande is de beschrijving van siliconenrubber in de handleiding.
C. Gebruikstemperatuur: Zoals hierboven vermeld, wordt hij meestal ingesteld op -40°C tot 200°C en kan hij in korte tijd 230°C bereiken.
D. Verouderingsprobleem: oliebestendigheid, zuur- en alkalibestendigheid zijn slecht en het heeft weinig te maken met stress.
E. Hechtingsprobleem: Vóór de oppervlaktebehandeling, naast het gebruik van siliconenproducten als lijm om te hechten met siliconen onderdelen, moet de hechting aan andere onderdelen aan het oppervlak worden geactiveerd en kan het lijmoppervlak worden uitgehard door vulkanisatie.
Alle stoffen die met rubber kunnen reageren of het kunnen laten verknopen, worden samen vulkaniseermiddelen genoemd, ook wel verknopingsmiddelen genoemd. Er zijn veel soorten vulkaniseermiddelen en het aantal neemt nog steeds toe.
Tot de gebruikte vulkaniseermiddelen behoren zwavel, selenium, tellurium, zwavelhoudende verbindingen, metaaloxiden, peroxiden, harsen, chinonen en aminen.
F. Materiaalhardheid: Volgens de Shore hardheid kunnen de plastic onderdelen theoretisch worden gekozen tussen 10 graden en 80 graden op de binnenlandse markt.
Degene die gemakkelijk te vinden zijn, zijn over het algemeen 20 tot 70 graden, en de meest gebruikte zijn 40 tot 50 graden.
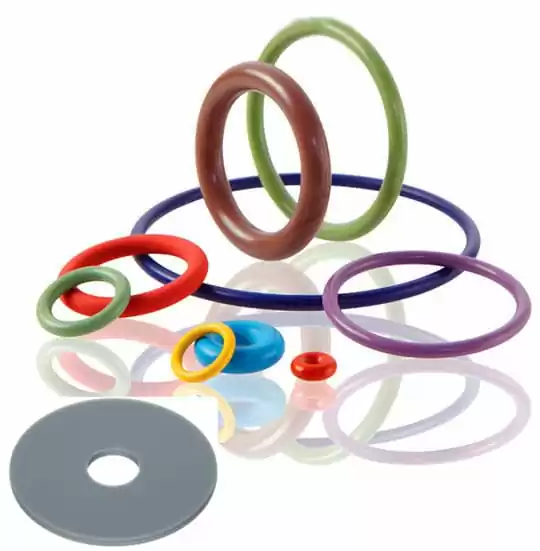
2. Het productieproces van siliconenproducten
A: Vorm en kleur van grondstoffen
B: Na kleuraanpassing en kneden worden de vlokken van verschillende kleuren getransformeerd van melkwitte silicagel.
C: Na het kneden en vormen worden de grondstoffen in stroken geperst en in stroken gesneden.
D: Vulkanisatie spuitgieten
E: Bijsnijden, randen verwijderen, inspectie, verpakking
F: Voltooid siliconenproducten
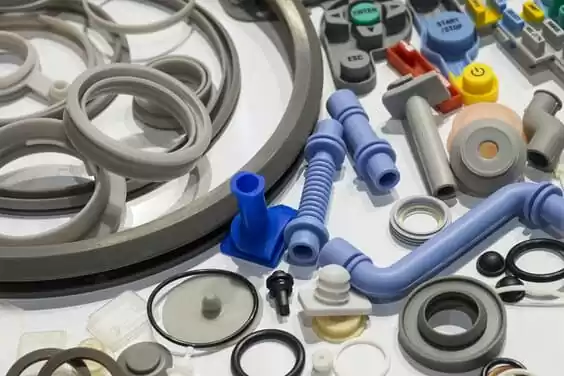
3. Productgrootte en -kenmerken
A. Beperkte grootte: Het dikste deel kan 15~20MM zijn, als het een bol is, kan de diameter 30MM zijn. Over het algemeen is de aanbevolen dikte niet meer dan 3MM.
Als het groter is dan 3MM, kost het meer vulkanisatietijd en stijgen de kosten. Het dunste deel kan theoretisch 0,2 mm zijn, maar bij het ontwerp wordt meestal de dunste 0,3 mm genomen en wordt 0,4 mm aanbevolen.
B. Relatieve grootte: Wat het dikteverschil betreft, wordt aanbevolen dat het dunste deel en het dikste deel niet meer dan 3 keer zo groot zijn. Dergelijke problemen hangen voornamelijk af van de temperatuur- en drukvereisten wanneer het materiaal gevulkaniseerd wordt.
C. Krimpsnelheid: De krimpsnelheid van de siliconenmateriaal is gerelateerd aan de hardheid van het materiaal. De meeste secundaire materialen die door de fabrikant worden geleverd, hebben een hardheid tussen 1,022 en 1,042.
Voor materialen met een graad van 40 tot 50 graden is de krimpsnelheid meestal 1,03. Vergeleken met kunststof hebben siliconenproducten geen last van vergelijkbare zichtbare oppervlaktedefecten als gevolg van krimp.
D. Maatnauwkeurigheid: Omdat de meeste siliconenrubber producten een matrijs zijn met meerdere holtes, is het aantal holtes erg groot in vergelijking met kunststof producten. Daarom is het niet zo handig als plastic producten om de grootte te regelen.
De algemene nauwkeurigheid is plus of min 0,1 en het zeer nauwkeurige product is plus of min 0,05. Als het wordt gebruikt om het gat van het plastic onderdeel en de knop op elkaar af te stemmen, is de minimale speling 0,1 per kant en de aanbevolen waarde is 0,2 per kant.
E. Vormontwerp: Voor rubberen hoesdelen is het over het algemeen voldoende om de originele tekening aan de matrijsfabriek te verstrekken volgens de tekening van de productvorm en het bijpassende probleem uit te leggen, dat wordt besloten door de matrijsfabriek.
Onder normale omstandigheden, afhankelijk van de grootte van het product, is de coördinatie tussen de rubberen hoes en het product over het algemeen een negatieve afwijking van 0,2 ~ 0,5 kleine aan één kant.
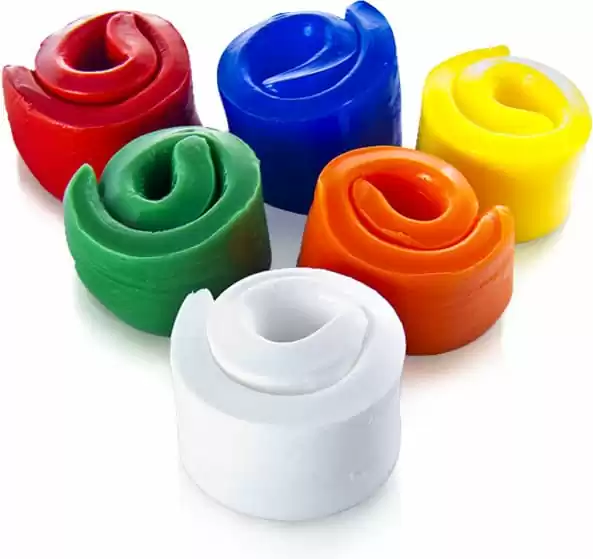
4. Vormstructuur
A. Bovengrens vormdikte:
Voorlopig 250 mm, de grootte kan oplopen tot 500 x 500, en het product kan tot 400 x 400 in de mal gebied. De matrijsstructuur is over het algemeen verdeeld in de bovenste matrijs, onderste matrijs, bodemplaat, bovenste plaat, uitwerppin, matrijskern, scharnier en andere hulpstukken. Bij het ontwerpen van siliconenproductenmoet aandacht worden besteed aan de kenmerken van hun mallen en productieprocessen:
B. Ontvormen:
Siliconenproducten kunnen direct en geforceerd worden vrijgegeven. Voor producten zonder ontwerpfouten ligt de vereiste grootte voor geforceerde vrijgave voornamelijk in de verhouding van de omtrek van het grootste deel van de matrijskern tot het kleinste afsluitende deel tijdens het ontvormen. Voor producten onder 55° kan het 2-3 keer gebeuren. Er kunnen scheuren en scherpe hoeken ontstaan bij de opening.
Omdat tijdens het vulkaniseren een temperatuur van 180 graden Celsius vereist is, gebeurt het ontvormen bijna volledig handmatig, met uitzondering van het scheiden van de boven- en onderkant van de mal zelf. Daarom moet bij het ontwerp van de onderdelen rekening worden gehouden met het gemak en de snelheid van het verwijderen.
Om de vulkanisatiekwaliteit en de massaproductie-efficiëntie van de onderdelen niet te beïnvloeden door de lange ontvormtijd. Omdat de vrijgavemethode van siliconen voornamelijk handmatig is en de actieslag van de bovenplaat ook klein is, heeft de siliconenmal geen hellende bovenkant in vergelijking met de plastic vorm. Over het algemeen wordt er geen kerntrekkracht geleverd.
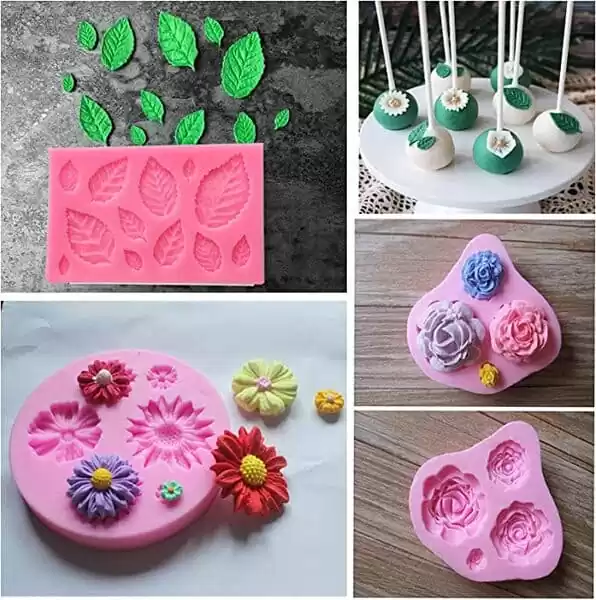
C. Bevestiging van de kern:
In tegenstelling tot kunststof mallen worden de kernen van siliconen mallen meestal samen met de productonderdelen verwijderd wanneer de spuitgietvorm wordt geopend en de onderdelen worden eruit gehaald. Daarom zijn de fixatie en nauwkeurige positionering van de matrijskern moeilijker te hanteren dan de kunststof matrijs en is de stijfheid van de matrijskern hoger.
De kernen worden meestal samen gemaakt en alle kernen worden in één keer vastgezet. Of haal de matrijskern door hulpgereedschap om hem snel te kunnen positioneren. Omdat er veel druk is bij het opspannen van de matrijs, moet strikt worden voorkomen dat de matrijskern beweegt.
D. Kerntrekken:
Over het algemeen kan het niet automatisch worden verplaatst, maar het kan wel worden geforceerd, en het kerntrekken wordt alleen gebruikt voor kleine constructies. De kerntrekinstelling is vergelijkbaar met die van de plastic vormmaar het wordt handmatig verwijderd als de mal wordt geopend.
Bovendien neemt het kerntrekken een grote ruimte in de matrijs in, wat niet alleen ingewikkeld is om te verwerken in de overtollige siliconen mal in één matrijs, maar heeft ook een laag gebruik van de matrijsruimte. Trek dus zo min mogelijk aan de kern.
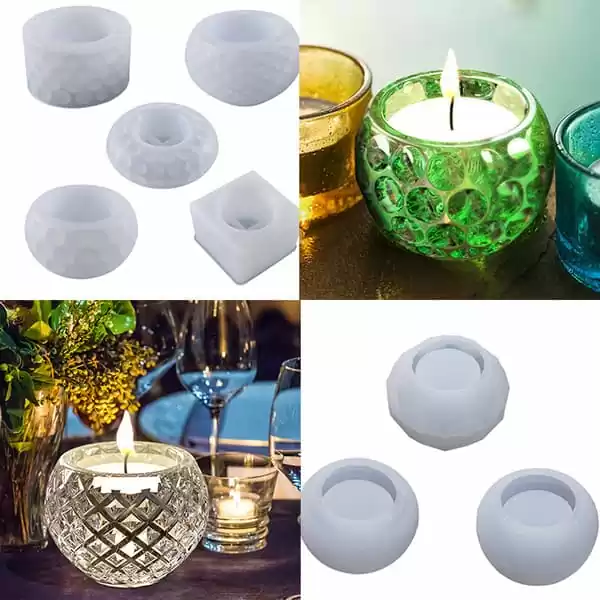
E. Vorm:
Siliconen producten hebben een grote taaiheid als het oppervlak intact is, maar als er eenmaal scheurtjes zijn, zullen de scheurtjes snel uitzetten onder invloed van externe krachten. Dit gezegd zijnde, siliconenproducten zijn erg gevoelig voor scheuren.
Met het oog op deze problemen moet aandacht worden besteed aan het juiste matrijsontwerp van siliconen onderdelen: er mogen geen scherpe hoeken in alle posities zijn om spanningsconcentratie en scheuren te voorkomen. De R-hoek bij de opening mag niet kleiner zijn dan 0,5.
F. Zelfverwijderende rand:
De belangrijkste functie van de zelfverwijderende rand: is om overtollig rubber op te vangen; vergemakkelijkt schimmeluitlaat; gemakkelijk om de flits te trimmen.
De zelfverwijderende rand bestaat over het algemeen uit een dunne rand aan het scheidingsoppervlak van het onderdeel en een bijbehorende relatief sterke scheurrand. De dikte van de dunne rand is meestal 0,1~0,2, de dikte van de scheurrand is meestal 0,8 en de breedte is meestal 1~2MM.
G. Invoegen:
Er kunnen verschillende soorten inzetstukken in siliconenproducten worden geplaatst, maar er moet wel op een aantal zaken worden gelet Ten eerste moet het oppervlak van de ingebedde onderdelen worden voorbehandeld, voornamelijk oppervlaktevulkanisatie of oppervlakteactivering.
Anders zal het moeilijk zijn om het inzetstuk en de lijm stevig te verbinden. De tweede is de vaste positionering van de insert, die in één richting in verticale richting kan worden vastgezet, maar in andere richtingen volledig moet worden vastgezet. Om te voorkomen dat het inzetstuk beweegt tijdens het volledige vormproces.
De derde is de dikte van de lijm rond de insert. Voor onderdelen die volledig ingekapseld zijn (waarbij alle oppervlakken ingekapseld zijn, zodat het inzetstuk niet gepositioneerd kan worden), moet een minimale dikte van 0,5 mm rond het inzetstuk gebruikt worden. Voor inzetstukken met positionering moet de dikte van de perifere lijmlaag meer dan 0,4 mm zijn.
H. Andere ondersteunende processen:
Lijm injecteren (lijmen):
Vergelijkbaar met de spuitgieten In het proces worden de te injecteren onderdelen eerst gefixeerd en wordt de eerste laag van de mal gesloten om te voorkomen dat de grondstoffen tijdens het injecteren de onderdelen die niet voor injectie bedoeld zijn, besmetten. Vervolgens wordt de tweede matrijslaag gesloten en wordt het rubbermengsel in vorm geperst.
Walsproces: rubber eerst voorvormen
Vormen: Dit productieproces kan worden gebruikt in het geval van volledige inkapseling.
Dompelen: De grondstof van het rubber (rubber) lichaam is vloeibaar en het werkstuk wordt vele malen in de grondstof gedompeld. De binnenste laag grondstof wordt gevulkaniseerd en vervolgens opnieuw gedompeld totdat de gewenste dikte is bereikt.
Epoxy: De grondstof heeft een goede vloeibaarheid, vergelijkbaar met verf, en wordt gevulkaniseerd bij kamertemperatuur. De mal is een relatief eenvoudige, meestal handmatige bewerking en de volgende coating wordt aangebracht wanneer de eerste laag snel is uitgehard.
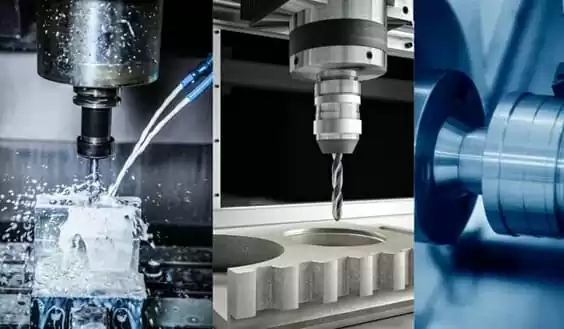
L. Meerkleurige producten:
A is verdeeld in 2 sets van vulkanisatie mallen, en B is met de hand gekleurd, eenmaal gevulkaniseerd, de kleur scheiding deel van de onderdelen is vereist voor een bepaalde hoogte, om de combinatie van kleur mengen geleidende lijm, secundaire vulkanisatie siliconen en te voorkomen silicone (rubber) kan direct worden gevulkaniseerd zonder behandeling Verbinding 5. Hardheidsmeting en gereedschappen.
Het meest gebruikte instrument om de hardheid van rubber te meten is de Shore (ook bekend als Shore) durometer. Gebruik een veer om een metalen indruklichaam in het oppervlak van het materiaal te drukken en meet hoe diep het indringt.
Het instrument meet indringdiepten van nul tot 0,100 inch. Een waarde van nul op de schaal betekent dat het indringlichaam de limietdiepte heeft bereikt, terwijl een waarde van 100 betekent dat de indringdiepte nul is. Er zijn verschillende shore hardheidsmeters met verschillende hardheidsbereiken en automatiseringsgraden.
Een van de meest gebruikte schalen is de Shore A schaal. Shore A durometers hebben een stomp indringlichaam en een gemiddelde veer. Bij metingen boven de 90 wordt de Shore A durometer onnauwkeurig. Voor dergelijke hardere materialen wordt een Shore D durometer gebruikt. Deze heeft een scherp indringlichaam en een sterke veer voor een diepe indringing.
Gebruik voor het meten van hardere kunststoffen een durometer met een scherper en veerkrachtiger indringlichaam, zoals een Rockwell durometer. Aan het andere uiterste worden Shore 00 durometers gebruikt om zachte gels en schuimrubbers te meten.

De meeste meervoudige materialen kunnen de initiële spanning weerstaan, maar zullen na verloop van tijd bezwijken door kruip en ontspanning. Durometer metingen kunnen direct worden uitgevoerd of na een bepaalde vertragingstijd, meestal 5 tot 10 seconden. Directe metingen zullen altijd hogere (of hardere) metingen laten zien dan vertraagde metingen.
Vertragingsmetingen zijn niet alleen representatiever voor de hardheid van het materiaal, maar ook voor de elasticiteit. Een zwakker, minder elastisch materiaal is gevoeliger voor kruip dan een sterker en elastischer materiaal.
Om de geldigheid van de gegevens te garanderen zijn nauwkeurige testprocedures nodig. Om een nauwkeurige meting te krijgen, moet je een teststuk hebben dat vlak en dik genoeg is zodat het indringlichaam niet beïnvloed wordt door het steunoppervlak.
Gewoonlijk is de vereiste dikte 0,200 inch, maar stijve materialen met minder vervorming kunnen nauwkeurig getest worden bij dunnere diktes.