Wprowadzenie:
Formowanie tłoczne jest szeroko stosowanym procesem produkcyjnym w różnych branżach, w tym motoryzacyjnej, lotniczej i towarów konsumpcyjnych. Polega on na zastosowaniu ciepła i ciśnienia do formowania materiałów takich jak tworzywa termoplastyczne i polimery termoutwardzalne w pożądane kształty. Proces ten oferuje kilka zalet, w tym możliwość produkcji złożonych części o doskonałej stabilności wymiarowej i właściwościach mechanicznych.
W każdym procesie produkcyjnym krytycznym celem jest skrócenie czasu cyklu. Czas cyklu odnosi się do całkowitego czasu wymaganego do ukończenia jednego cyklu formowania, w tym załadunku materiału, kompresji, chłodzenia i wyrzucania części. Minimalizując czas cyklu, producenci mogą zwiększyć produktywność, wydajność produkcji i zoptymalizować koszty.
Znaczenie skrócenia czasu cyklu w formowaniu tłocznym jest nie do przecenienia. Krótsze czasy cykli bezpośrednio przekładają się na szybsze tempo produkcji i niższe koszty w przeliczeniu na część. Producenci mogą skuteczniej spełniać wymagania klientów i zyskać przewagę konkurencyjną na rynku.
Co więcej, skrócenie czasu cyklu w formowanie tłoczne oferuje korzyści wykraczające poza zwiększoną produktywność i efektywność kosztową. Może to prowadzić do poprawy efektywności energetycznej, zmniejszenia zużycia sprzętu i poprawy zrównoważonego rozwoju poprzez zmniejszenie ogólnego zużycia energii i śladu węglowego procesu produkcyjnego.
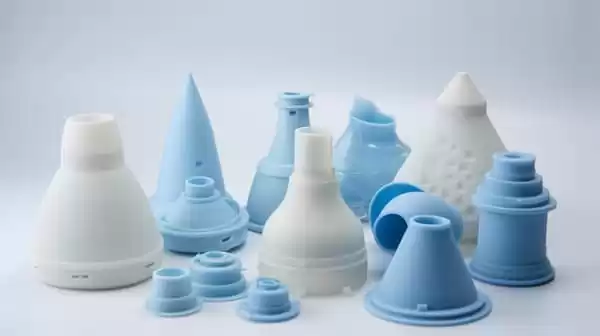
W tym artykule zagłębimy się w skuteczne strategie optymalizacji procesu formowania tłocznego w celu osiągnięcia znacznego skrócenia czasu cyklu. Wdrażając te strategie, producenci mogą odblokować pełny potencjał formowania tłocznego i napędzać swoje działania w kierunku większego sukcesu.
II. Zrozumienie procesu formowania tłocznego
Formowanie tłoczne to proces produkcyjny polegający na wykorzystaniu ciepła i ciśnienia do kształtowania i formowania materiałów w pożądane formy. Jest szeroko wykorzystywany do różnych zastosowań, w tym do produkcja części samochodowych, obudowy elektryczne i towary konsumpcyjne.
Kluczowe cechy formowania tłocznego:
1. zastosowanie ciepła i ciśnienia: Formowanie tłoczne stosuje ciepło i ciśnienie do materiału, powodując jego przepływ i dopasowanie do kształtu wnęki formy.
2. proces w stanie stałym: W przeciwieństwie do procesów takich jak formowanie wtryskowe, w których materiał jest w stanie stopionym, formowanie tłoczne wykorzystuje surowce stałe, takie jak granulki, preformy lub materiały arkuszowe.
3. precyzyjna kontrola umieszczania materiału: Materiał jest umieszczany w określonej ilości w gnieździe formy, zapewniając dokładność i spójność produktu końcowego.
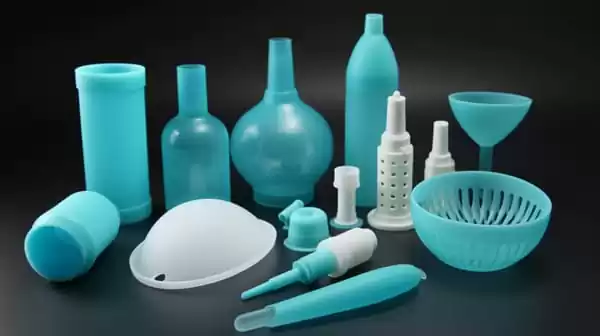
4. powolny proces chłodzenia: W porównaniu z innymi procesami formowania, formowanie tłoczne ma zazwyczaj wolniejszy proces chłodzenia ze względu na charakter materiału w stanie stałym i grubsze sekcje formowanej części.
Różnice między formowaniem tłocznym a innymi procesami formowania:
1. formowanie wtryskowe: W formowaniu wtryskowym materiał jest topiony i wtryskiwany do formy pod wysokim ciśnieniem. Formowanie wtryskowe dobrze nadaje się do produkcji wielkoseryjnej, skomplikowanych geometrii i krótkich czasów cyklu. W przeciwieństwie do tego, formowanie tłoczne lepiej nadaje się do mniejszych ilości produkcji, większych i grubszych części oraz materiałów, których nie można łatwo stopić.
2. formowanie z transferem żywicy (RTM): RTM polega na wtryskiwaniu żywicy do zamkniętej wnęki formy z materiałami wzmacniającymi. Jest powszechnie stosowany do produkcji różnych materiałów kompozytowych i części o wysokiej wytrzymałości i lekkości. Formowanie tłoczneZ drugiej strony, nie obejmuje wtryskiwania żywicy do formy, ale raczej stosuje ciepło i ciśnienie do wstępnie umieszczonego materiału.
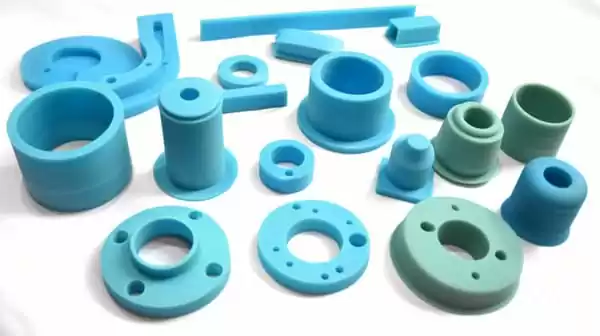
3. przepływ i dystrybucja materiału: W przypadku formowania wtryskowego stopiony materiał jest zmuszany do płynięcia i wypełniania wnęk formy, zapewniając skomplikowane detale i złożone kształty. W przypadku formowania tłocznego, przepływ i dystrybucja materiału zachodzą z powodu przyłożonego ciśnienia, co skutkuje mniej skomplikowanymi geometriami części.
4. czas cyklu: formowanie wtryskowe ma generalnie krótsze czasy cyklu w porównaniu do formowania tłocznego ze względu na szybkie chłodzenie stopionego materiału. Formowanie tłoczneZe względu na wolniejszy proces chłodzenia może wymagać więcej czasu na cykl.
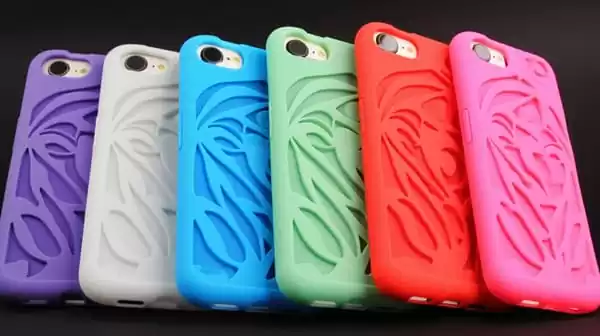
Zrozumienie cech i różnic między formowaniem tłocznym a innymi procesami formowania jest niezbędne do określenia najbardziej odpowiedniej metody dla określonych wymagań produkcyjnych. Wybierając odpowiedni proces formowania, producenci mogą osiągnąć optymalne wyniki pod względem złożoności części, wielkości produkcji i wydajności czasu cyklu.
III. Czynniki wpływające na czas cyklu w formowaniu tłocznym
Na czas cyklu w formowaniu tłocznym mają wpływ różne czynniki, które wpływają na całkowity czas trwania procesu formowania. Zrozumienie tych czynników i ich wpływu ma kluczowe znaczenie dla optymalizacji czasu cyklu i zwiększenia wydajności operacji formowania tłocznego. Przeanalizujmy główne czynniki wpływające na czas cyklu formowania wtryskowego i omówmy wpływ doboru materiału, konstrukcji wtryskarki, parametrów procesu i czasu chłodzenia:
1. wybór materiału:
Wybór materiału znacząco wpływa na czas cyklu formowania tłocznego. Różne materiały mają różne charakterystyki płynięcia, czasy utwardzania i szybkości chłodzenia. Materiały o niższej lepkości i krótszym czasie utwardzania pozwalają na szybsze wypełnienie gniazda formy i skrócenie czasu cyklu. Ważne jest, aby wybrać materiały, które równoważą właściwości płynięcia z pożądanymi właściwościami mechanicznymi i termicznymi końcowej formowanej części.
2.Konstrukcja formy:
Konstrukcja formy odgrywa kluczową rolę w optymalizacji czasu cyklu. Efektywny projekt formy zapewnia prawidłowy przepływ materiału i minimalne straty ciepła podczas procesu formowania. Czynniki takie jak liczba i złożoność wnęk, systemy odpowietrzania i konstrukcja wlewu wpływają na etapy napełniania i chłodzenia, ostatecznie wpływając na czas cyklu. Dobrze zaprojektowane formy ułatwiają szybsze i równomierne chłodzenie, co skutkuje krótszymi czasami cyklu.
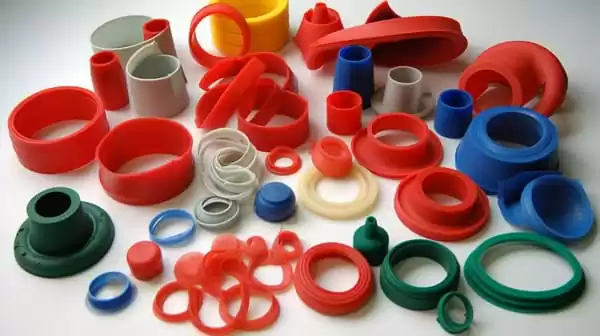
3. parametry procesu:
Optymalizacja parametrów procesu ma znaczący wpływ na czas cyklu. Parametry takie jak temperatura, ciśnienie i ustawienia czasu mają bezpośredni wpływ na przepływ materiału, etapy utwardzania i chłodzenia. Dostrajając te parametry, producenci mogą zidentyfikować optymalną kombinację, która minimalizuje czas cyklu przy zachowaniu pożądanej jakości formowanych części. Dokładne eksperymenty i analiza procesu są niezbędne do określenia krytycznych parametrów przetwarzania, które wpływają na czas cyklu.
4.Czas chłodzenia:
Czas chłodzenia jest krytycznym etapem formowania tłocznego, który wpływa na czas cyklu. Proces chłodzenia pozwala formowanej części zestalić się i osiągnąć wymagane właściwości mechaniczne. Grubość i złożoność części, a także przewodność cieplna materiału wpływają na czas chłodzenia. Efektywne techniki chłodzenia, takie jak wykorzystanie kanałów chłodzących lub wdrożenie metod szybkiego chłodzenia, mogą pomóc skrócić czas chłodzenia i ogólny czas cyklu.
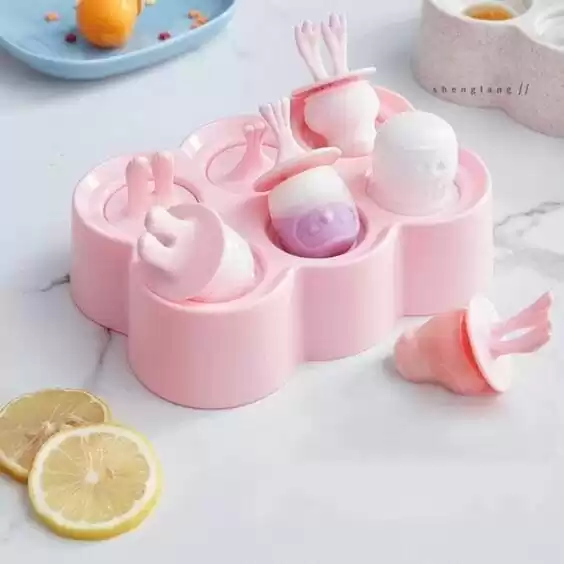
Dzięki starannemu doborowi materiałów, projekt formyDzięki optymalizacji parametrów procesu i czasu chłodzenia producenci mogą znacznie skrócić czas cyklu formowania tłocznego. Optymalizacja tych czynników zapewnia szybsze cykle produkcyjne, zwiększoną produktywność i lepszą efektywność kosztową. Niezbędne jest przeprowadzenie dokładnej analizy, eksperymentów i ciągłego doskonalenia procesu w celu zidentyfikowania optymalnych warunków, które minimalizują czas cyklu przy zachowaniu pożądanej jakości formowanych części.
IV. Strategie optymalizacji procesu formowania tłocznego
A. Wybór materiału i optymalizacja parametrów procesu
Wybór materiału i optymalizacja parametrów procesu są kluczowymi etapami optymalizacji. Proces formowania tłocznego i skrócenie czasu cyklu. Strategie te przyczyniają się do poprawy produktywności i efektywności kosztowej.
1.Podkreślenie znaczenia wyboru materiału i jego wpływu na czas cyklu:
Omówienie znaczenia wyboru materiałów o korzystnej charakterystyce płynięcia, krótkim czasie utwardzania i wysokiej stabilności wymiarowej.
Wyjaśnij, w jaki sposób materiały o niższej lepkości ułatwiają szybsze wypełnianie gniazda formy, co prowadzi do skrócenia czasu cyklu.
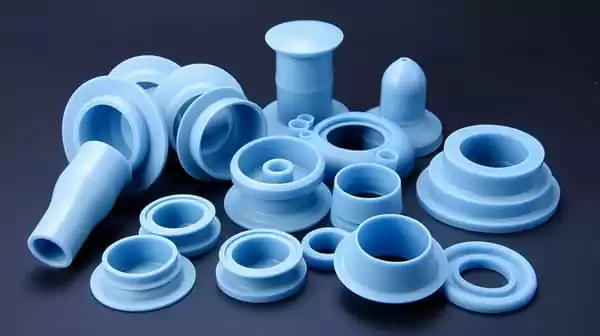
2.Wyjaśnij znaczenie optymalizacji parametrów procesu w celu skrócenia czasu cyklu:
1.Podkreślenie roli ustawień temperatury, ciśnienia i czasu w procesie chłodzenia. Proces formowania tłocznego.
2.Podkreśl znaczenie przeprowadzania dokładnych eksperymentów w celu zidentyfikowania optymalnej kombinacji parametrów procesu, które minimalizują czas cyklu bez uszczerbku dla jakości części.
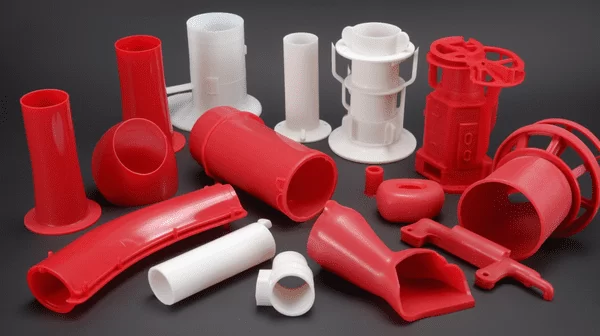
B. Konstrukcja formy i kontrola temperatury
Konstrukcja formy i kontrola temperatury są krytycznymi czynnikami w osiąganiu krótszych czasów cyklu w formowanie tłoczne.
1.Omów rolę projektu formy w osiągnięciu krótszego czasu cyklu:
Wyjaśnij, w jaki sposób wydajna konstrukcja formy optymalizuje przepływ materiału i minimalizuje straty ciepła podczas procesu formowania.
Podkreśl znaczenie odpowiedniej wentylacji, systemów wlotowych i konstrukcji wnęki dla szybkiego odprowadzania powietrza i łatwego napełniania.
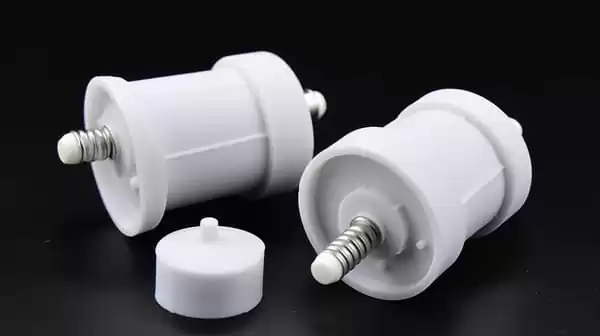
2.Wyjaśnienie znaczenia właściwej kontroli temperatury formy i jej wpływu na czas cyklu:
Omówienie wpływu temperatury formy na przepływ materiału, etapy utwardzania i chłodzenia.
Podkreśl znaczenie utrzymywania formy w odpowiedniej temperaturze, aby przyspieszyć utwardzanie i skrócić czas cyklu.
C. Automatyzacja, szybkie oprzyrządowanie i czas wymiany formy
Automatyzacja, szybkie oprzyrządowanie i wydajne procesy wymiany form przyczyniają się do skrócenia czasu cyklu i zwiększenia wydajności formowania tłocznego.
1.Omów korzyści płynące z automatyzacji i robotyzacji w formowanie tłoczne:
Wyjaśnij, w jaki sposób automatyzacja i robotyka usprawniają załadunek materiału, zamykanie formy i wyrzucanie części, prowadząc do skrócenia czasu cyklu.
Podkreśl zalety dokładności i szybkości zautomatyzowanych systemów w porównaniu z pracą ręczną.
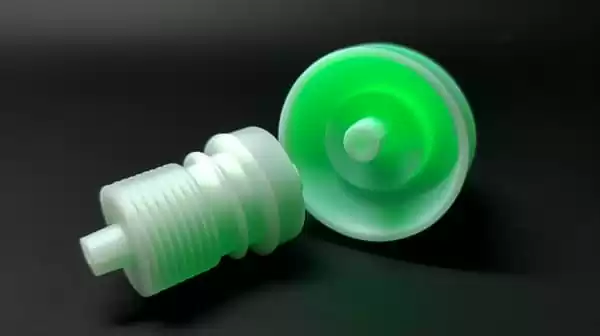
2.Podkreślenie znaczenia technik szybkiego oprzyrządowania i wydajnych procesów wymiany form:
Wyjaśnij, w jaki sposób techniki szybkiego oprzyrządowania minimalizują czas zmiany formy, umożliwiając szybsze przejścia między różnymi formami.
Omów korzyści płynące z wydajnej koordynacji między zespołami, usprawnionych procedur oprzyrządowania i dobrze zaplanowanych zmian form.
D. Czas chłodzenia i optymalizacja
Skrócenie czasu chłodzenia jest kluczowym aspektem optymalizacji czasu cyklu w formowanie tłoczne.
1.Wyjaśnij znaczenie skrócenia czasu chłodzenia w formowaniu tłocznym:
Podkreśl, jak czas chłodzenia wpływa na ogólny czas cyklu i wydajność produkcji.
Omów, w jaki sposób szybsze chłodzenie prowadzi do skrócenia czasu cyklu i zwiększenia produktywności.
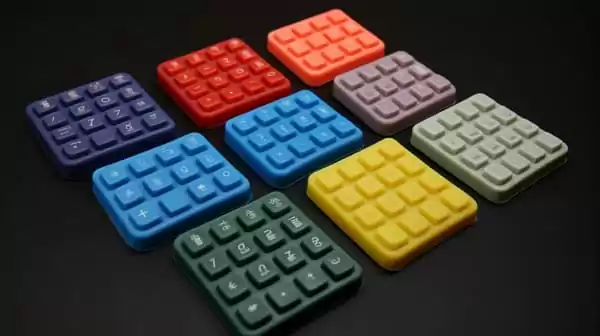
2.Omówienie różnych technik chłodzenia i ich wpływu na czas cyklu:
Zapoznaj się z metodami, takimi jak chłodzenie wodą lub powietrzem, które przyspieszają krzepnięcie formowanych części. Podkreśl zalety i rozważania każdej techniki chłodzenia pod względem skrócenia czasu cyklu.
E. Ciągłe doskonalenie procesów i analiza danych
Ciągłe doskonalenie procesu i analiza danych są integralną częścią optymalizacji procesu formowania tłocznego i skracania czasu cyklu.
1.Podkreśl znaczenie ciągłego doskonalenia w skracaniu czasu cyklu:
Omówienie korzyści płynących z proaktywnego podejścia do identyfikacji i wdrażania usprawnień procesów.
Podkreśl znaczenie regularnego monitorowania i analizowania wydajności procesów.
2.Omówienie roli analizy danych i optymalizacji procesu w osiąganiu optymalnych parametrów formowania tłocznego:
Wyjaśnij, w jaki sposób podejmowanie decyzji w oparciu o dane poprawia czas cyklu i ogólną wydajność procesu.
Omówienie wykorzystania metod statystycznej kontroli procesu i technik analizy danych w celu identyfikacji trendów i optymalizacji krytycznych parametrów przetwarzania.
Poprzez wdrożenie tych strategii optymalizacji Proces formowania tłocznegoProducenci mogą osiągnąć znaczne skrócenie czasu cyklu, zwiększyć produktywność i osiągnąć efektywność kosztową. Ciągłe doskonalenie, analiza danych oraz integracja technik automatyzacji i szybkiego oprzyrządowania są kluczowymi elementami w osiąganiu optymalnych parametrów formowania tłocznego i ogólnej wydajności procesu
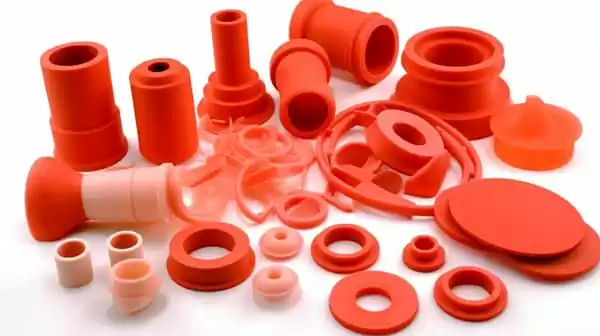
Wnioski
W tym artykule przeanalizowaliśmy strategie optymalizacji procesu formowania tłocznego w celu skrócenia czasu cyklu, ostatecznie zwiększając produktywność i efektywność kosztową. Omówiliśmy kluczowe czynniki wpływające na czas cyklu, w tym wybór materiału, projekt formy, parametry procesu i czas chłodzenia. Uwzględniając te czynniki, producenci mogą znacznie usprawnić swoje operacje formowania tłocznego.
Optymalizacja doboru materiałów i parametrów procesu ma kluczowe znaczenie dla skrócenia czasu cyklu. Wybór materiałów o korzystnej charakterystyce przepływu i optymalizacja optymalnych parametrów przetwarzania, takich jak ustawienia temperatury, ciśnienia i czasu, przyczyniają się do szybszego napełniania, utwardzania i chłodzenia, prowadząc do skrócenia czasu cyklu bez pogorszenia jakości części.
Konstrukcja formy i kontrola temperatury odgrywają kluczową rolę w osiąganiu krótszych czasów cyklu. Efektywne projekty form optymalizują przepływ materiału, minimalizują straty ciepła i zapewniają równomierne chłodzenie. Właściwa kontrola temperatury formy przyspiesza utwardzanie i chłodzenie, dodatkowo skracając czas cyklu.
Automatyzacja, szybkie oprzyrządowanie i wydajne procesy wymiany form usprawniają operację formowania, minimalizując pracę ręczną i przestoje. Integracja automatyki i robotyki zwiększa produktywność i zapewnia precyzyjne i szybkie operacje. Techniki szybkiego oprzyrządowania i dobrze zaplanowane zmiany form umożliwiają szybsze przejścia między formami, maksymalizując czas sprawności produkcji.
Skrócenie czasu chłodzenia jest krytycznym aspektem czasu cyklu i samego procesu optymalizacji. Wdrożenie wydajnych technik chłodzenia i wykorzystanie zaawansowanych metod chłodzenia, takich jak konforemne kanały chłodzące, przyspiesza krzepnięcie i poprawia jakość części przy jednoczesnym skróceniu czasu cyklu.
Ciągłe doskonalenie procesu i analiza danych są niezbędne do optymalizacji formowania tłocznego. Dzięki regularnemu monitorowaniu i analizowaniu wydajności procesu, producenci mogą identyfikować obszary wymagające ulepszeń i podejmować decyzje oparte na danych w celu osiągnięcia optymalnych parametrów formowania tłocznego.
Podsumowując, optymalizacja procesu formowania tłocznego w celu skrócenia czasu cyklu ma zasadnicze znaczenie dla poprawy produktywności i efektywności kosztowej. Wdrażając strategie, takie jak optymalizacja doboru materiałów, różne parametry formowania wtryskowego, ulepszenia projektowe, automatyzacja i ciągłe doskonalenie procesów, producenci mogą osiągnąć znaczne skrócenie czasu cyklu, zwiększyć wydajność produkcji i poprawić ogólną konkurencyjność na rynku. Przyjmując te strategie, producenci mogą uwolnić pełny potencjał formowania tłocznego i osiągnąć sukces w swoich branżach.
Podsumowując, optymalizacja procesu formowania tłocznego w celu skrócenia czasu cyklu ma zasadnicze znaczenie dla poprawy produktywności i efektywności kosztowej. Wdrażając strategie, takie jak optymalizacja doboru materiałów, ulepszenia konstrukcji form, automatyzacja i ciągłe doskonalenie procesów, producenci mogą osiągnąć znaczne skrócenie czasu cyklu, zwiększyć wydajność produkcji i poprawić ogólną konkurencyjność na rynku. Przyjmując te strategie, producenci mogą uwolnić pełny potencjał formowania tłocznego i osiągnąć sukces w swoich branżach.
Podsumowując, optymalizacja procesu formowania tłocznego w celu skrócenia czasu cyklu ma zasadnicze znaczenie dla poprawy produktywności i efektywności kosztowej. Wdrażając strategie, takie jak optymalizacja doboru materiałów, ulepszenia konstrukcji form, automatyzacja i ciągłe doskonalenie procesów, producenci mogą osiągnąć znaczne skrócenie czasu cyklu, zwiększyć wydajność produkcji i poprawić ogólną konkurencyjność na rynku. Przyjmując te strategie, producenci mogą uwolnić pełny potencjał formowania tłocznego i osiągnąć sukces w swoich branżach.
Podsumowując, optymalizacja procesu formowania tłocznego w celu skrócenia czasu cyklu ma zasadnicze znaczenie dla poprawy produktywności i efektywności kosztowej. Wdrażając strategie, takie jak optymalizacja doboru materiałów, ulepszenia konstrukcji form, automatyzacja i ciągłe doskonalenie procesów, producenci mogą osiągnąć znaczne skrócenie czasu cyklu, zwiększyć wydajność produkcji i poprawić ogólną konkurencyjność na rynku. Przyjmując te strategie, producenci mogą uwolnić pełny potencjał formowania tłocznego i osiągnąć sukces w swoich branżach.