Introduction:
Compression molding is a widely utilized manufacturing process in various industries, including automotive, aerospace, and consumer goods. It involves the application of heat and pressure to mold materials such as thermoplastics and thermosetting polymers into desired shapes. The process offers several advantages, including the ability to produce complex parts with excellent dimensional stability and mechanical properties.
In any manufacturing process, reducing cycle time is a critical objective. Cycle time refers to the total time required to complete one molding cycle, including material loading, compression, cooling, and part ejection. By minimizing cycle time, manufacturers can enhance productivity, increase production output, and optimize cost efficiency.
The significance of reducing cycle time in compression molding cannot be overstated. Shorter cycle times directly translate to faster production rates and reduced costs per part. Manufacturers can meet customer demands more efficiently and gain a competitive edge in the market.
Moreover, reducing cycle time in compression molding offers benefits beyond increased productivity and cost efficiency. It can lead to improved energy efficiency, decreased equipment wear and tear, and enhanced sustainability by reducing the overall energy consumption and carbon footprint of the manufacturing process.
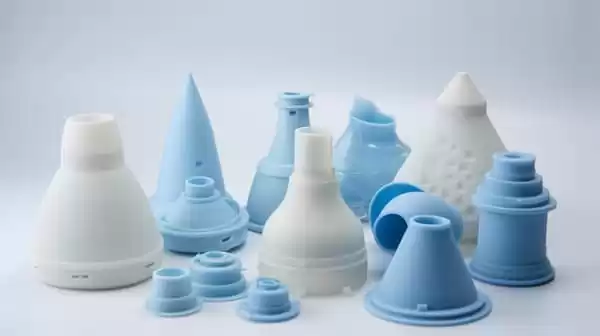
In this article, we will delve into effective strategies for optimizing the compression molding process to achieve significant reductions in cycle time. By implementing these strategies, manufacturers can unlock the full potential of compression molding and propel their operations towards greater success.
II. Understanding the Compression Molding Process
Compression molding is a manufacturing process that involves the use of heat and pressure to shape and mold materials into desired forms. It is widely utilized for a variety of applications, including the production of automotive components, electrical enclosures, and consumer goods.
Key Characteristics of Compression Molding:
1.Heat and Pressure Application: Compression molding applies heat and pressure to the material, causing it to flow and conform to the shape of the mold cavity.
2.Solid-State Process: Unlike processes like injection molding process where the material is in a molten state, compression molding utilizes solid raw materials, such as granules, preforms, or sheet materials.
3.Precise Control of Material Placement: The material is placed in a predetermined amount into the mold cavity, ensuring accuracy and consistency in the final product.
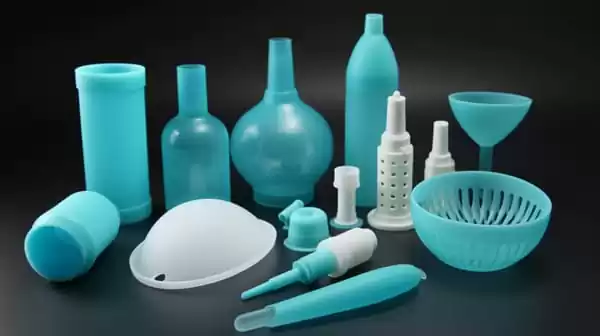
4.Slow Cooling Process: Compared to other molding processes, compression molding typically has a slower cooling process due to the nature of solid-state material and thicker sections of the molded part.
Differences between Compression Molding and Other Molding Processes:
1.Injection Molding: In injection molding, the material is melted and injected into the mold under high pressure. It is well-suited for high-volume production, intricate geometries, and rapid cycle times. In contrast, compression molding is better suited for lower production volumes, larger and thicker parts, and materials that cannot be easily melted.
2.Resin Transfer Molding (RTM): RTM involves the injection of resin into a closed mold cavity with reinforcing materials. It is commonly used for the production of various composite materials and parts with high strength and lightweight properties. Compression molding, on the other hand, does not involve injecting resin into the mold but rather applies heat and pressure to pre-placed material.
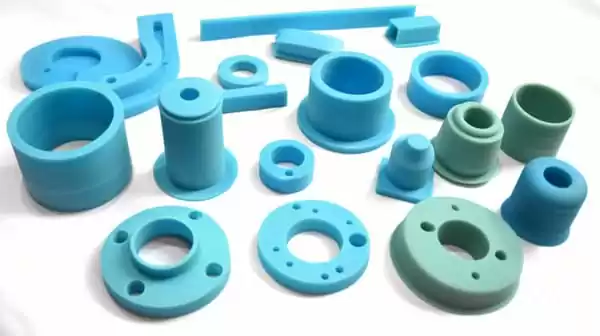
3.Material Flow and Distribution: In injection molding, molten material is forced to flow and fill the mold cavities, ensuring intricate details and complex shapes. In compression molding, material flow and distribution occur due to the applied pressure, resulting in less intricate part geometries.
4.Cycle Time: Injection molding generally has shorter cycle times compared to compression molding due to the rapid cooling of molten material. Compression molding, with its slower cooling process, may require more time per cycle.
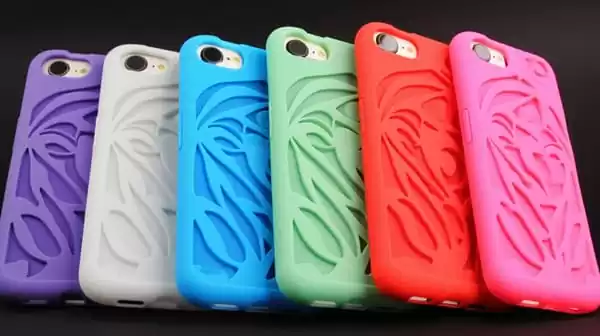
Understanding the characteristics and differences between compression molding and other molding processes is essential in determining the most suitable method for specific manufacturing requirements. By selecting the appropriate molding process, manufacturers can achieve optimal results in terms of part complexity, production volume, and cycle time efficiency.
III. Factors Affecting Cycle Time in Compression Molding
Cycle time in compression molding is influenced by various factors that impact the overall duration of the molding process. Understanding these factors and their effects is crucial for optimizing cycle time and enhancing productivity in compression molding operations. Let’s explore the major factors that influence injection molding cycle time and discuss the impact of material selection, injection molding machine design, process parameters, and cooling time:
1.Material Selection:
The choice of material significantly affects cycle time in compression molding. Different materials have varying flow characteristics, curing times, and cooling rates. Materials with lower viscosity and faster cure times allow for quicker filling of the mold cavity and shorter cycle times. It is important to select materials that balance flow properties with the desired mechanical and thermal properties of the final molded part.
2.Mold Design:
The design of the mold plays a crucial role in cycle time optimization. Efficient mold design ensures proper material flow and minimal heat loss during the molding process. Factors such as the number and complexity of cavities, venting systems, and gating design influence the filling and cooling stages, ultimately affecting cycle time. Well-designed molds facilitate faster and uniform cooling, resulting in shorter cycle times.
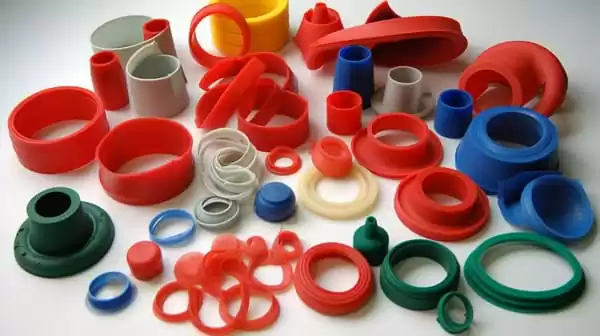
3.Process Parameters:
The optimization of process parameters has a significant impact on cycle time. Parameters such as temperature, pressure, and time settings directly influence the material flow, curing, and cooling stages. By fine-tuning these parameters, manufacturers can identify the optimal combination that minimizes cycle time while maintaining the desired quality of the molded parts. Thorough experimentation and process analysis are essential to determine the critical processing parameters that affect cycle time.
4.Cooling Time:
Cooling time is a critical stage in compression molding that affects cycle time. The cooling process allows the molded part to solidify and achieve the required mechanical properties. The thickness and complexity of the part, as well as the thermal conductivity of the material, influence the cooling time. Efficient cooling techniques, such as utilizing cooling channels or implementing rapid cooling methods, can help reduce cooling time and overall cycle time.
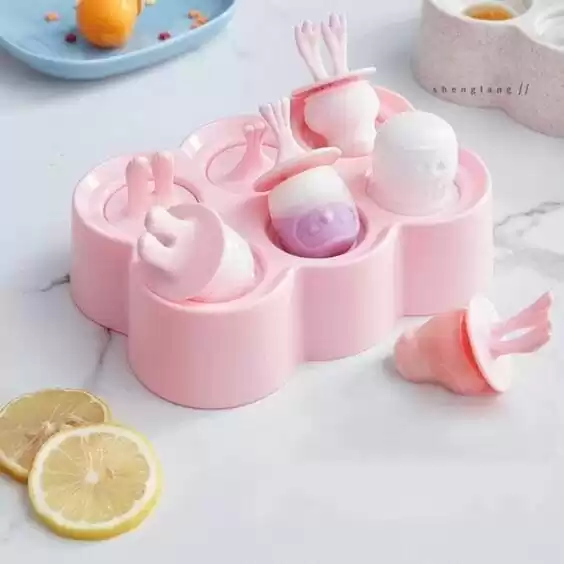
By carefully considering material selection, mold design, process parameters, and cooling time, manufacturers can significantly reduce cycle time in compression molding. Optimization of these factors ensures faster production cycles, increased productivity, and improved cost efficiency. It is essential to conduct thorough analysis, experimentation, and continuous process improvement to identify the optimum conditions that minimize cycle time while maintaining the desired quality of the molded parts.
IV. Strategies for Optimizing the Compression Molding Process
A. Material Selection and Process Parameters Optimization
Material selection and optimization of process parameters are crucial steps in optimizing the compression molding process and reducing cycle time. These strategies contribute to improved productivity and cost efficiency.
1.Highlight the importance of material selection and its impact on cycle time:
Discuss the significance of choosing materials with favorable flow characteristics, quick cure times, and high dimensional stability.
Explain how materials with lower viscosity facilitate faster filling of the mold cavity, leading to shorter cycle times.
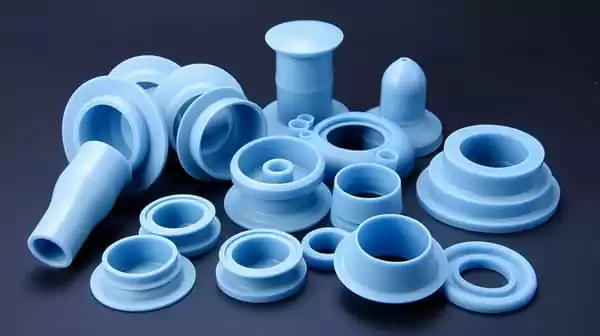
2.Explain the significance of optimizing process parameters to reduce cycle time:
1.Emphasize the role of temperature, pressure, and time settings in the compression molding process.
2.Highlight the importance of conducting thorough experimentation to identify the optimal combination of process parameters that minimize cycle time without compromising part quality.
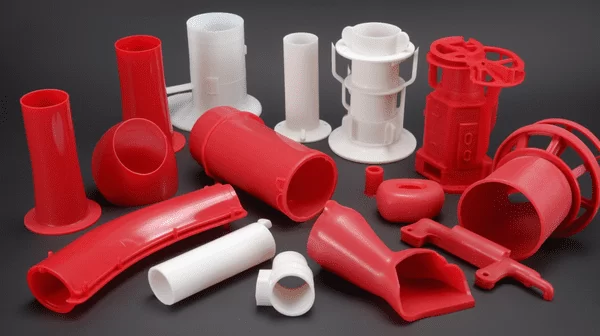
B. Mold Design and Temperature Control
Mold design and temperature control are critical factors in achieving shorter cycle times in compression molding.
1.Discuss the role of mold design in achieving shorter cycle time:
Explain how an efficient mold design optimizes material flow and minimizes heat loss during the molding process.
Highlight the importance of proper venting, gating systems, and cavity design for quick air evacuation and easy filling.
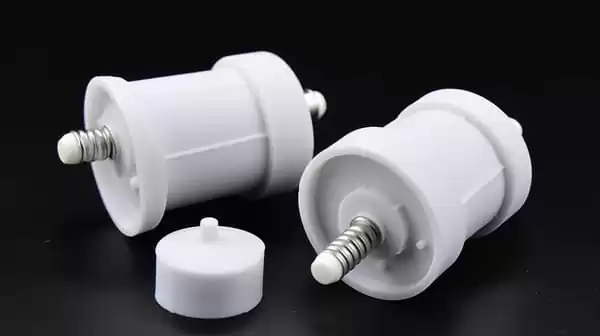
2.Explain the importance of proper mold temperature control and the impact on cycle time:
Discuss how mold temperature affects material flow, curing, and cooling stages.
Highlight the significance of maintaining the mold at the appropriate temperature to expedite curing and reduce cycle time.
C. Automation, Rapid Tooling, and Mold Change Time
Automation, rapid tooling, and efficient mold changeover processes contribute to cycle time reduction and increased productivity in compression molding.
1.Discuss the benefits of automation and robotics in compression molding:
Explain how automation and robotics streamline material loading, mold closing, and part ejection, leading to faster cycle times.
Highlight the accuracy and speed advantages of automated systems over manual labor.
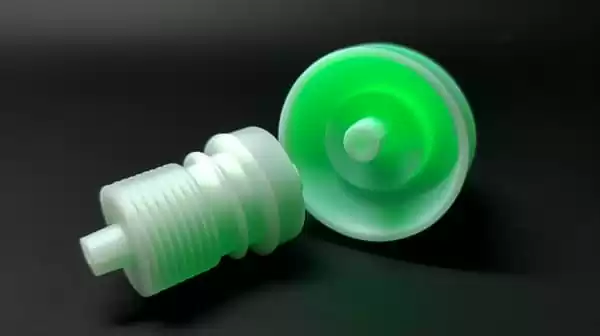
2.Highlight the significance of rapid tooling techniques and efficient mold changeover processes:
Explain how rapid tooling techniques minimize mold change time, allowing for faster transitions between different molds.
Discuss the benefits of efficient coordination between teams, streamlined tooling procedures, and well-planned mold changeovers.
D. Cooling Time and Optimization
Reducing cooling time is a crucial aspect of cycle time optimization in compression molding.
1.Explain the importance of reducing cooling time in compression molding:
Highlight how cooling time affects overall cycle time and production efficiency.
Discuss how faster cooling leads to shorter cycle times and increased productivity.
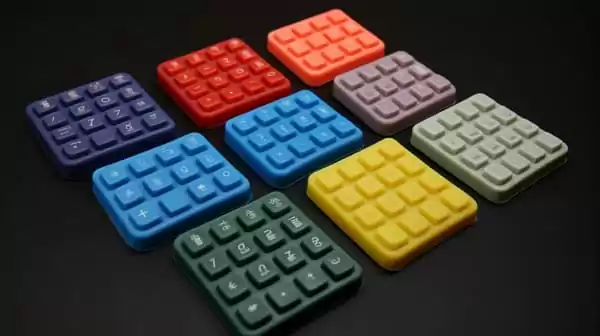
2.Discuss different cooling techniques and their impact on cycle time:
Explore methods such as water or air cooling that expedite the solidification of molded parts.Highlight the advantages and considerations of each cooling technique in terms of cycle time reduction.
E. Continuous Process Improvement and Data Analysis
Continuous process improvement and data analysis are integral to optimizing the compression molding process and reducing cycle time.
1.Emphasize the importance of continuous improvement in cycle time reduction:
Discuss the benefits of a proactive approach to identifying and implementing process enhancements.
Highlight the significance of regularly monitoring and analyzing process performance.
2.Discuss the role of data analysis and process optimization in achieving optimal compression molding parameters:
Explain how data-driven decision-making improves cycle time and overall process efficiency.
Discuss the utilization of statistical process control methods and data analysis techniques to identify trends and optimize critical processing parameters.
By implementing these strategies for optimizing the compression molding process, manufacturers can achieve significant reductions in cycle time, enhance productivity, and achieve cost efficiency. Continuous improvement, data analysis, and the integration of automation and rapid tooling techniques are key elements in achieving optimal compression molding parameters and overall process efficiency
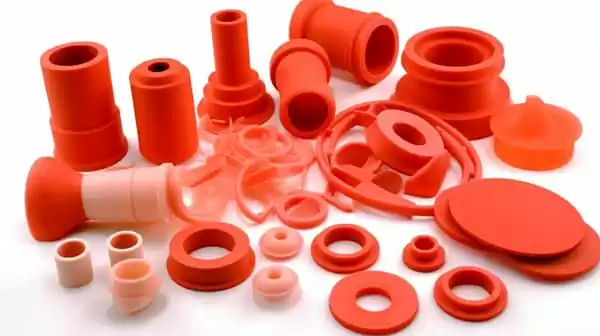
Conclusion
In this article, we have explored strategies for optimizing the compression molding process to reduce cycle time, ultimately enhancing productivity and cost efficiency. We discussed key factors that influence cycle time, including material selection, mold design, process parameters, and cooling time. By addressing these factors, manufacturers can significantly improve their compression molding operations.
Optimizing material selection and process parameters is crucial for cycle time reduction. Choosing materials with favorable flow characteristics and optimizing optimal processing parameters, such as temperature, pressure, and time settings contribute to faster filling, curing, and cooling stages, leading to shorter cycle times without compromising part quality.
Mold design and temperature control play pivotal roles in achieving shorter cycle times. Efficient mold designs optimize material flow, minimize heat loss, and ensure uniform cooling. Proper mold temperature control accelerates curing and cooling, further reducing cycle time.
Automation, rapid tooling, and efficient mold changeover processes streamline the molding operation, minimizing manual labor and downtime. Integrating automation and robotics enhances productivity and ensures precise and rapid operations. Rapid tooling techniques and well-planned mold changeovers enable faster transitions between molds, maximizing production uptime.
Reducing cooling time is a critical aspect of cycle time and optimization process itself. Implementing efficient cooling techniques and utilizing advanced cooling methods, such as conformal cooling channels, expedite solidification and enhance part quality while reducing cycle time.
Continuous process improvement and data analysis are essential for optimizing compression molding. By regularly monitoring and analyzing process performance, manufacturers can identify areas for enhancement and make data-driven decisions to achieve optimal compression molding parameters.
In conclusion, optimizing the compression molding process to reduce cycle time is essential for improved productivity and cost efficiency. By implementing strategies such as material selection optimization, various injection molding parameters, design improvements, automation, and continuous process improvement, manufacturers can achieve significant reductions in cycle time, increase production output, and enhance overall competitiveness in the market. By embracing these strategies, manufacturers can unlock the full potential of compression molding and position themselves for success in their respective industries.
In conclusion, optimizing the compression molding process to reduce cycle time is essential for improved productivity and cost efficiency. By implementing strategies such as material selection optimization, mold design improvements, automation, and continuous process improvement, manufacturers can achieve significant reductions in cycle time, increase production output, and enhance overall competitiveness in the market. By embracing these strategies, manufacturers can unlock the full potential of compression molding and position themselves for success in their respective industries.
In conclusion, optimizing the compression molding process to reduce cycle time is essential for improved productivity and cost efficiency. By implementing strategies such as material selection optimization, mold design improvements, automation, and continuous process improvement, manufacturers can achieve significant reductions in cycle time, increase production output, and enhance overall competitiveness in the market. By embracing these strategies, manufacturers can unlock the full potential of compression molding and position themselves for success in their respective industries.
In conclusion, optimizing the compression molding process to reduce cycle time is essential for improved productivity and cost efficiency. By implementing strategies such as material selection optimization, mold design improvements, automation, and continuous process improvement, manufacturers can achieve significant reductions in cycle time, increase production output, and enhance overall competitiveness in the market. By embracing these strategies, manufacturers can unlock the full potential of compression molding and position themselves for success in their respective industries.