Wprowadzenie
Konstrukcja gniazda formy jest podstawą udanego formowania tłocznego, posiadając moc kształtowania przyszłości wielu gałęzi przemysłu. Nie można lekceważyć tego krytycznego aspektu produkcji, ponieważ ma on zdolność do dostarczania wysokiej jakości, spójnych wyników - co jest prawdziwym świadectwem jego znaczenia.
W świecie, w którym królują innowacje i precyzja, formowanie tłoczne staje się wszechstronnym i niezbędnym procesem produkcyjnym. Dzięki zastosowaniom obejmującym wiele branż, w tym motoryzację, elektronikę i towary konsumpcyjne, odgrywa kluczową rolę w kształtowaniu produktów, na których codziennie polegamy. Od komponentów samochodowych zaprojektowanych z myślą o wydajności i trwałości po materiały do izolacji elektrycznej zapewniające nasze bezpieczeństwo, formowanie tłoczne dotyka niemal każdego aspektu naszego życia.
Gdy zagłębiamy się w królestwo Konstrukcja gniazda formy do formowania tłocznegoWyruszamy w podróż, która odkrywa skomplikowany gobelin tego procesu. Badając jego niuanse, odkryjemy, w jaki sposób odpowiednia konstrukcja gniazda formy może odblokować świat możliwości, tworząc produkty, które nie tylko spełniają, ale często przekraczają nasze oczekiwania. Dołącz do nas w tej eksploracji sztuki i nauki stojącej za formowaniem tłocznym, gdzie projekt gniazda formy jest kompasem prowadzącym nas w kierunku uosobienia doskonałości produkcji.
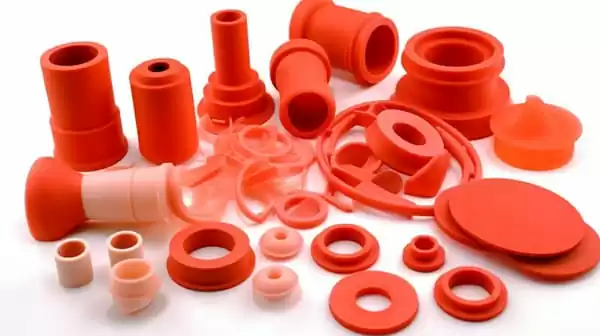
Zrozumienie procesów formowania tłocznego
Formowanie tłoczne jest wszechstronnym i szeroko stosowanym procesem produkcyjnym o zastosowaniach w różnych branżach. Aby zrozumieć istotę tej techniki, kluczowe jest podzielenie jej na podstawowe elementy.
1. Proces formowania tłocznego:
W samym sercu, formowanie tłoczne to proces polegający na kształtowaniu materiałów przy użyciu ciepła i ciśnienia. Etapy tego procesu są następujące:
Przygotowanie materiału: Proces rozpoczyna się od przygotowania surowców, zazwyczaj w postaci granulek, peletek lub mieszanek do formowania arkuszy (SMC).
Ogrzewanie: Forma, często składająca się z dwóch połówek, jest zamykana wokół materiału. Następnie stosuje się ciepło w celu zmiękczenia lub stopienia materiału, czyniąc go giętkim.
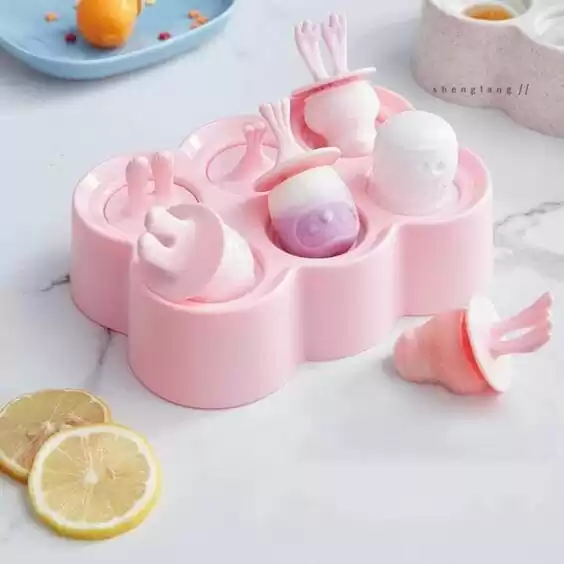
Kompresja: Ciśnienie jest przykładane do wnęki formy, zagęszczając materiał i nadając mu pożądany kształt produktu końcowego.
Chłodzenie: Gdy materiał przyjmie kształt formy, jest schładzany w celu zestalenia, a rozgrzana forma twardnieje, zachowując pożądaną formę.
Wyrzucenie: Na koniec uformowana część jest wyrzucana z gniazda formy, gotowa do dalszej obróbki lub użycia.
2. Projektowanie form do prasowania:
Podstawą udanej operacji formowania tłocznego jest konstrukcja gniazda formy. Konstrukcja formy do prasowania obejmuje kilka kluczowych elementów:
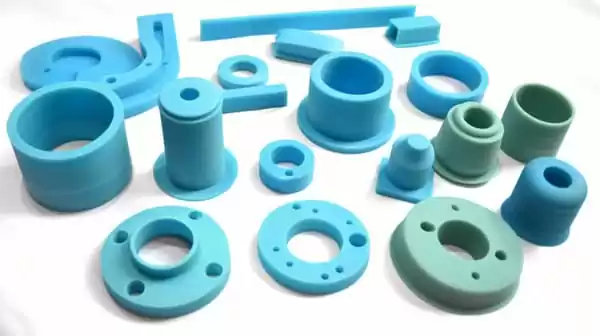
Geometria: Geometria gniazda formy musi dokładnie odpowiadać zamierzonemu kształtowi produktu końcowego. Obejmuje to takie kwestie, jak grubość części, kąty pochylenia i podcięcia, zapewniając płynne wyrzucanie.
Wentylacja: Skuteczne odpowietrzanie jest niezbędne, aby umożliwić ucieczkę uwięzionego powietrza i gazów podczas formowania. Prawidłowe odpowietrzanie zapobiega powstawaniu wad, takich jak kieszenie powietrzne lub puste przestrzenie w produkcie końcowym.
Linia podziału: Linia podziału wyznacza miejsce, w którym forma oddziela się, aby uwolnić uformowaną część. Musi być dobrze zdefiniowana i nie rzucać się w oczy dla estetyki i funkcjonalności produktu.
Konstrukcja bramy: Brama służy jako punkt, przez który stopiony materiał wchodzi do gniazda formy. Staranna konstrukcja bramy zapewnia równomierne wypełnienie i minimalizuje defekty. Typy bram obejmują bramy krawędziowe, bramy sworzniowe i bramy tunelowe.
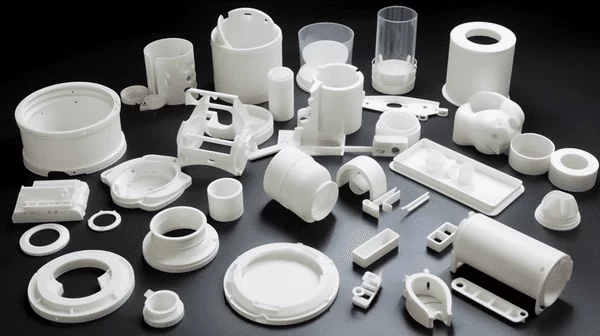
Układ chłodzenia: Wydajne kanały chłodzące wewnątrz formy pomagają szybko zestalić uformowaną część, zapobiegają wypaczaniu lub odkształceniom i skracają czas cyklu.
Wykończenie powierzchni: W zależności od wymagań produktu, wykończenie powierzchni gniazda formy może być polerowane, teksturowane lub powlekane, aby poprawić estetykę produktu końcowego.
3. Materiały stosowane w formowaniu tłocznym:
Formowanie tłoczne jest kompatybilne z szeroką gamą materiałów, w tym z materiałami termoutwardzalnymi, takimi jak żywica epoksydowa, guma silikonowa i żywice polimerowe. Szczególnie dobrze sprawdza się w przypadku materiałów żywicznych wzmocnionych włóknami, takich jak kompozyty z włókna szklanego lub węglowego. Materiały te oferują doskonałą wydajność mechaniczną, odporność na temperaturę i odporność chemiczną.
4. Zalety i wady formowania tłocznego:
Zalety:
Opłacalność: Formowanie tłoczne często wykorzystuje materiały termoplastyczne z recyklingu i materiały o stosunkowo niskich temperaturach topnienia, co zmniejsza koszty produkcji.
Szeroki zakres temperatur: Może tworzyć formy dla części o szerokim zakresie temperatur i wysokich wymaganiach w zakresie odporności chemicznej.
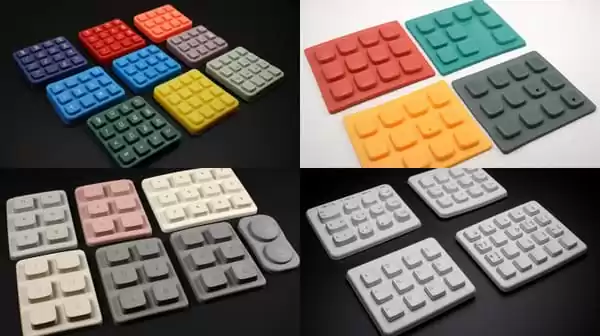
Materiały kompozytowe: Idealny do pracy z materiałami kompozytowymi, takimi jak włókna szklane i węglowe, umożliwiając produkcję lekkich komponentów o wysokiej wytrzymałości.
Wady:
Geometrie złożone: Może nie nadawać się do produkcji komponentów o bardzo złożonej geometrii lub wąskich tolerancjach.
Wolniejszy proces: Formowanie tłoczne może być wolniejsze w porównaniu z innymi procesami formowania, takimi jak formowanie wtryskowe, co może mieć wpływ na tempo produkcji.
Zasadniczo zrozumienie procesu formowania tłocznego, roli projektowania form tłocznych, wszechstronności stosowanych materiałów oraz zalet i wad tej metody stanowi podstawę do wykorzystania jej potencjału w różnych branżach. Jest to proces, który łączy w sobie precyzję, kreatywność i inżynierię w celu formowania surowców w produkty, które sprawiają, że nasz świat funkcjonuje.
Sekcja 2: Rodzaje formowania tłocznego
W dziedzinie formowania tłocznego typy form odgrywają kluczową rolę w określaniu wyników procesu. Wybór formy może znacząco wpłynąć na jakość produktu, złożoność i wydajność produkcji. Zagłębmy się w trzy podstawowe typy form do formowania tłocznego i odkryjmy ich cechy i zastosowania:
1. Forma typu Open-Flash:
Charakterystyka:
Flash Management: Cechą charakterystyczną form z otwartym wypływem jest możliwość wydostania się nadmiaru materiału, znanego jako "wypływka", podczas procesu formowania tłocznego. Nadmiar ten jest później przycinany, pozostawiając pożądany produkt.
Zastosowania:
Części o niskiej precyzji: Formy typu open-flash są powszechnie stosowane, gdy precyzja nie jest krytycznym wymogiem. Są one idealne do produkcji części, w przypadku których wysoki stopień dokładności wymiarowej nie jest konieczny.
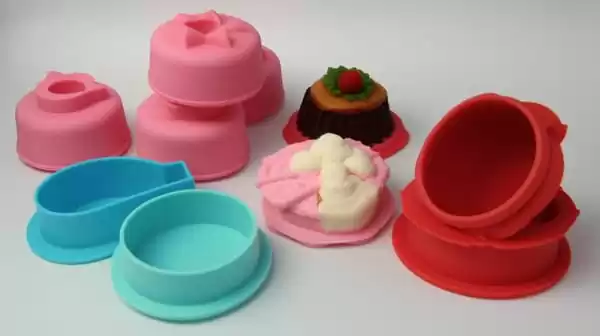
2. Forma zamknięta:
Charakterystyka:
Precyzja: Formy zamknięte są zaprojektowane tak, aby utrzymać wysoki stopień precyzji w całym procesie formowania tłocznego. Zostały zaprojektowane tak, aby zminimalizować wypływki i zapewnić wąskie tolerancje w produkcie końcowym.
Zastosowania:
Krytyczna precyzja: Formy zamknięte znajdują swoją niszę w zastosowaniach, w których precyzja jest najważniejsza. Są one stosowane w scenariuszach, w których spójność produktu i przestrzeganie ścisłych tolerancji nie podlegają negocjacjom.
3. Forma półzamknięta:
Charakterystyka:
Podejście hybrydowe: Formy półzamknięte łączą w sobie elementy form otwartych i zamkniętych. Pozwalają one na wydostanie się części wypływki, a jednocześnie zapewniają kontrolę nad wymiarami części.
Zastosowania:
Zrównoważone wymagania: Formy półzamknięte są wybierane, gdy istnieje potrzeba umiarkowanej precyzji, a zarządzanie błyskiem jest niezbędne, ale nie tak krytyczne jak w przypadku form zamkniętych. Oferują one zrównoważone podejście, które odpowiada szerokiemu zakresowi wymagań dotyczących produktu.
Zasadniczo wybór między formami otwartymi, zamkniętymi i półzamkniętymi w formowaniu tłocznym zależy od konkretnych wymagań wytwarzanego produktu. Formy otwarte są odpowiednie, gdy precyzja nie jest najwyższym priorytetem, formy zamknięte wyróżniają się w zastosowaniach wymagających najwyższej precyzji, a formy półzamknięte zapewniają równowagę między tymi dwoma skrajnościami. Wybierając odpowiedni typ formy, producenci mogą zoptymalizować swoje procesy formowania tłocznego, aby spełnić unikalne potrzeby swoich produktów i branż.
Sekcja 3: Rodzaje materiałów do formowania tłocznego
W świecie formowania tłocznego wybór materiałów do formowania tłocznego ma kluczowe znaczenie dla określenia właściwości i cech produktu końcowego. Dwa powszechnie stosowane materiały w tym procesie to Sheet Molding Compound (SMC) i Bulk Molding Compound (BMC). Zagłębmy się w te materiały i rzućmy światło na zalety wykorzystania materiałów termoutwardzalnych w formowaniu tłocznym:
1. Sheet Molding Compound (SMC):
Charakterystyka:
Wzmocnione włóknami: SMC to materiał wzmocniony włóknami, który łączy żywice termoutwardzalne z ciętymi włóknami szklanymi. Wzmocnienie to nadaje materiałowi doskonałą wytrzymałość i sztywność.
Formularz arkusza: SMC jest zazwyczaj dostarczany w postaci płaskich arkuszy lub rolek. Arkusze te są wstępnie impregnowane żywicą i mogą być łatwo cięte i układane warstwowo w gnieździe formy.
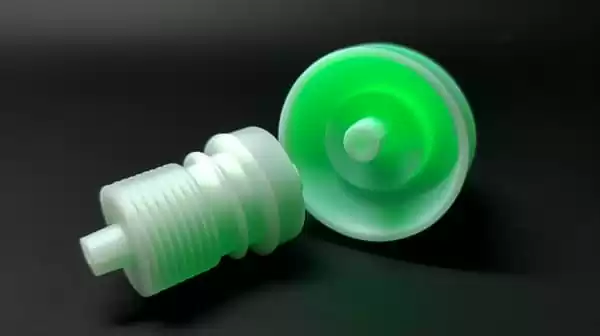
Zastosowania:
Części samochodowe: SMC jest szeroko stosowany w przemyśle motoryzacyjnym do produkcji komponentów, takich jak panele nadwozia, maski i wykończenia zewnętrzne, ze względu na wysoką wytrzymałość, odporność na uderzenia i odporność na korozję.
Obudowy elektryczne: Jego właściwości elektroizolacyjne sprawiają, że SMC jest preferowanym wyborem dla obudów i paneli elektrycznych.
2. Bulk Molding Compound (BMC):
Charakterystyka:
Materiał termoutwardzalny: BMC jest również materiałem termoutwardzalnym, składającym się z mieszaniny żywicy termoutwardzalnej, materiałów wypełniających i włókien wzmacniających (zazwyczaj szklanych).
Postać granulatu: W przeciwieństwie do SMC, BMC jest dostarczany w postaci granulatu. Ta ziarnista konsystencja pozwala na precyzyjne formowanie złożonych kształtów.
Zastosowania:
Przemysł motoryzacyjny: BMC znajduje swoje miejsce w przemyśle motoryzacyjnym do produkcji złożonych komponentów, takich jak pokrywy zaworów, kolektory dolotowe i części pod maską. Jego stabilność wymiarowa oraz odporność na chemikalia i wysoką temperaturę sprawiają, że jest to idealny wybór.
Elektryka i elektronika: BMC jest używany w zastosowaniach elektrycznych i elektronicznych ze względu na jego doskonałe właściwości elektroizolacyjne i odporność na płomienie.
Zalety stosowania materiałów termoutwardzalnych w formowaniu tłocznym:
Wybór materiałów termoutwardzalnych, takich jak te stosowane w SMC i BMC, oferuje kilka korzyści w procesie formowania tłocznego:
Odporność na temperaturę: Materiały termoutwardzalne doskonale sprawdzają się w środowiskach o wysokiej temperaturze. Mogą wytrzymać podwyższone temperatury bez deformacji, dzięki czemu nadają się do zastosowań wymagających odporności na ciepło i cykle termiczne.
Odporność chemiczna: Materiały te wykazują doskonałą odporność chemiczną, dzięki czemu idealnie nadają się do zastosowań, w których spodziewana jest ekspozycja na różne chemikalia.
Stabilność wymiarowa: Materiały termoutwardzalne zachowują swój kształt i wymiary pod wpływem ciśnienia i wysokich temperatur, zapewniając spójność i precyzję produktu końcowego.
Izolacja elektryczna: Zarówno SMC, jak i BMC posiadają wyjątkowe właściwości elektroizolacyjne, co czyni je niezbędnymi w zastosowaniach elektrycznych i elektronicznych.
Złożone kształty: Ziarnista forma BMC i możliwość nakładania warstw SMC umożliwiają formowanie złożonych i skomplikowanych kształtów, zapewniając wszechstronność w projektowaniu.
Podsumowując, Sheet Molding Compound (SMC) i Bulk Molding Compound (BMC) są przykładowymi materiałami termoutwardzalnymi stosowanymi w formowaniu tłocznym. Ich nieodłączne zalety, w tym odporność na temperaturę i chemikalia, stabilność wymiarowa i właściwości izolacji elektrycznej, sprawiają, że są one cennym wyborem w produkcji różnorodnych produktów w różnych branżach. Wykorzystanie tych materiałów, w połączeniu z precyzją formowanie tłoczneRezultatem są wysokiej jakości komponenty o dopasowanej charakterystyce i wydajności.
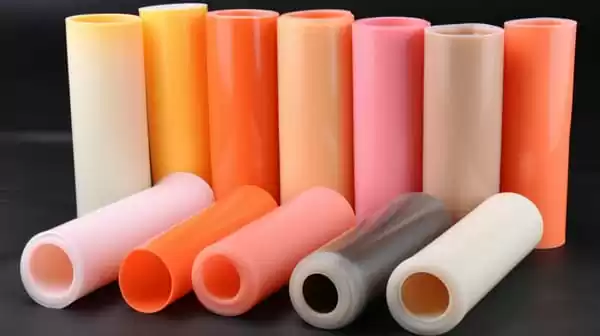
Sekcja 4: Sam proces formowania tłocznego
Aby naprawdę zrozumieć zawiłości formowania tłocznego, konieczne jest zagłębienie się w istotę samego procesu. W tej sekcji zbadamy podstawowe elementy formy do prasowania, zrozumiemy znaczenie jej wysokociśnieniowego charakteru i rozwikłamy proces utwardzania odpowiedzialny za zestalenie uformowanej części:
1. Elementy formy do ściskania:
Forma do prasowania jest sercem procesu formowania tłocznego. Składa się z kilku kluczowych elementów:
Wnęka formy: To tutaj dzieje się magia. Wnęka formy definiuje kształt i wymiary produktu końcowego. Musi być skrupulatnie zaprojektowana, aby pomieścić pożądaną geometrię, w tym czynniki takie jak grubość części, kąty pochylenia i wykończenie powierzchni.
System ogrzewania: Formy ciśnieniowe są wyposażone w system grzewczy, który podnosi temperaturę w gnieździe formy. Ogrzewanie to jest niezbędne do zmiękczenia lub stopienia surowca, aby uczynić go giętkim i podatnym na formowanie.
Układ chłodzenia: Wydajne kanały lub systemy chłodzenia przebiegają przez formę, aby szybko schłodzić i zestalić uformowaną część po nadaniu jej kształtu. Odpowiednie chłodzenie zapewnia zachowanie pożądanego kształtu i zapobiega wypaczeniom lub zniekształceniom.
Mechanizm nacisku: Formowanie tłoczne jest znane ze swojej wysokociśnieniowej natury. Forma zawiera mechanizm wywierający znaczny nacisk na wnękę formy. Ciśnienie to jest odpowiedzialne za zagęszczenie materiału, zapewniając wypełnienie każdego zakamarka formy i ostatecznie definiując gęstość i integralność strukturalną części.
2. Wysokociśnieniowy charakter formowania tłocznego:
Formowanie tłoczne charakteryzuje się wysokim ciśnieniem, które odgrywa kluczową rolę w kształtowaniu produktu końcowego. Znaczenie tego wysokociśnieniowego środowiska leży w kilku aspektach:
Kompresja materiału: Wysokie ciśnienie stosowane podczas formowania tłocznego powoduje zagęszczenie materiału w gnieździe formy. Kompresja ta zapewnia dokładne dopasowanie materiału do geometrii formy, co skutkuje doskonałym odwzorowaniem części i dokładnością wymiarową.
Kontrola gęstości: Ciśnienie dyktuje gęstość produktu końcowego. Starannie kontrolując ciśnienie, producenci mogą osiągnąć określoną gęstość materiału, która wpływa na właściwości mechaniczne i wydajność części.
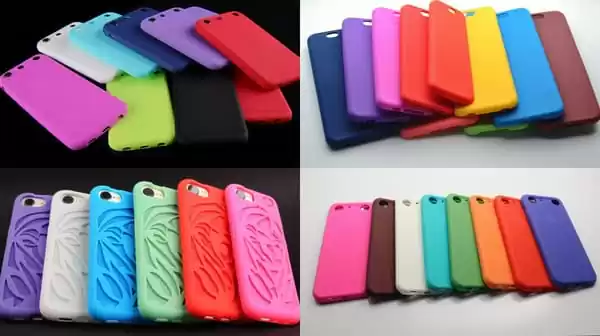
Jednolite wypełnienie: Wysokie ciśnienie pomaga w równomiernym wypełnieniu gniazda formy. Minimalizuje to ryzyko powstawania pustych przestrzeni, kieszeni powietrznych lub innych wad w produkcie końcowym, przyczyniając się do poprawy jego jakości.
3. Proces utwardzania:
Po tym, jak materiał przyjmie pożądany kształt w gnieździe formy, rozpoczyna się proces utwardzania. Utwardzanie jest etapem odpowiedzialnym za zestalenie uformowanej części i nadanie jej ostatecznej integralności strukturalnej. Oto jak to działa:
Ciepło i ciśnienie: Podwyższona temperatura wewnątrz formy, w połączeniu z zastosowanym ciśnieniem, wyzwala reakcję chemiczną w materiale termoutwardzalnym. Reakcja ta powoduje utwardzenie materiału i utrwalenie jego kształtu.
Chłodzenie: Po zakończeniu procesu utwardzania aktywowany jest system chłodzenia formy w celu szybkiego obniżenia temperatury. Ta faza chłodzenia pomaga zestalić część, czyniąc ją sztywną i gotową do wyrzucenia z formy.
Podsumowując, zrozumienie elementów formy do prasowania, znaczenia środowiska wysokociśnieniowego i procesu utwardzania zapewnia cenny wgląd w mechanikę formowania tłocznego. Ta skomplikowana interakcja ciepła, ciśnienia i precyzyjnej inżynierii umożliwia produkcję Wysokiej jakości komponenty o pożądanym kształcie, gęstości i właściwościach mechanicznych. Jest ucieleśnieniem doskonałości produkcyjnej, dostarczając produkty spełniające najwyższe standardy wydajności i niezawodności.
Sekcja 5: Projektowanie gniazda formy
Wnęka formy znajduje się w samym sercu procesu formowania tłocznego. W tej sekcji zbadamy kluczową rolę projektu gniazda formy, zdefiniujemy projekt formy do prasowania i zagłębimy się w obliczenia tonażu - kluczowego czynnika w formowaniu tłocznym:
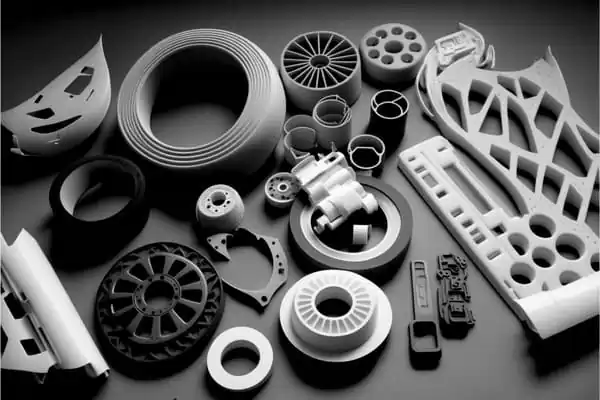
1. Znaczenie konstrukcji wnęki formy:
Konstrukcja gniazda formy ma kluczowe znaczenie dla zapewnienia sukcesu procesu formowania tłocznego. Oto dlaczego ma to takie znaczenie:
Precyzja i spójność: Wnęka formy definiuje ostateczny kształt i wymiary produktu. Dobrze zaprojektowana wnęka zapewnia precyzję i spójność każdego formowanego elementu, spełniając najwyższe standardy jakości.
Przepływ materiału: Geometria gniazda formy określa sposób, w jaki materiał przepływa i wypełnia formę. Niewłaściwa konstrukcja może prowadzić do nierównomiernego rozprowadzania materiału, co skutkuje wadami lub niespójnościami w produkcie końcowym.
Wentylacja i chłodzenie: Skuteczne kanały wentylacyjne lub rowki w gnieździe formy umożliwiają ucieczkę uwięzionego powietrza i gazów, zapobiegając powstawaniu wad, takich jak kieszenie powietrzne. System chłodzenia w gnieździe pomaga szybko zestalić część, skracając czas cyklu.
Wykończenie powierzchni: Konstrukcja gniazda formy odgrywa również rolę w uzyskaniu pożądanego wykończenia powierzchni formowanej części. Może być ona polerowana, teksturowana lub powlekana, aby spełnić określone wymagania estetyczne i funkcjonalne.
2. Czym jest projektowanie form ciśnieniowych?
Konstrukcja formy do prasowania to proces skrupulatnego tworzenia wnęki formy, która może wytrzymać wysokie ciśnienia i temperatury nieodłącznie związane z formowaniem tłocznym. Obejmuje on kilka krytycznych aspektów:
Geometria: Wnęka formy musi dokładnie odpowiadać zamierzonemu kształtowi produktu końcowego. Obejmuje to uwzględnienie grubości części, kątów pochylenia i podcięć zapewniających płynne wyrzucanie.
Wentylacja: Odpowiednie kanały wentylacyjne lub rowki pozwalają uwięzionemu powietrzu i gazom wydostać się podczas formowania, zapobiegając defektom, takim jak kieszenie powietrzne lub puste przestrzenie w produkcie końcowym.
Linia rozstania: Linia podziału wyznacza miejsce, w którym forma oddziela się, aby uwolnić uformowaną część. Musi być dobrze zdefiniowana i nie rzucać się w oczy dla estetyki i funkcjonalności produktu.
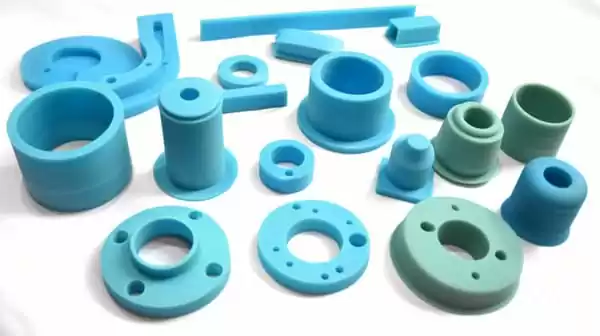
Konstrukcja bramy: Brama służy jako punkt, przez który stopiony materiał wchodzi do gniazda formy. Starannie zaprojektowana brama zapewnia równomierne wypełnienie i minimalizuje defekty. Typy bram obejmują bramy krawędziowe, bramy sworzniowe i bramy tunelowe.
Układ chłodzenia: Wydajne kanały chłodzące wewnątrz formy pomagają szybko zestalić uformowaną część, zapobiegają wypaczaniu lub odkształceniom i skracają czas cyklu.
Wykończenie powierzchni: W zależności od wymagań produktu, wykończenie powierzchni gniazda formy może być polerowane, teksturowane lub powlekane, aby poprawić estetykę produktu końcowego.
3. Jak obliczyć tonaż dla formowania tłocznego:
Tonaż w formowanie tłoczne odnosi się do siły wymaganej do ściśnięcia materiału w gnieździe formy. Jest to kluczowy czynnik w osiągnięciu odpowiedniej kompresji materiału i gęstości części. Aby obliczyć tonaż, można użyć następującego wzoru:
Tonaż = Ciśnienie × Powierzchnia
Ciśnienie: Ciśnienie jest zwykle mierzone w PSI (funtach na cal kwadratowy).
Obszar: Obszar reprezentuje przewidywany obszar formowanej części.
Obliczając wymagany tonaż, producenci mogą zapewnić, że prasa używana w procesie formowania tłocznego wywiera siłę niezbędną do osiągnięcia pożądanej kompresji i gęstości materiału w gnieździe formy.
Zasadniczo, konstrukcja gniazda formy jest kamieniem węgielnym udanego formowania tłocznego. Decyduje o jakości, precyzji i spójności produktu. Projekt formy ciśnieniowej obejmuje geometrię, odpowietrzanie, linie podziału, konstrukcję wlewu, systemy chłodzenia i wykończenie powierzchni - wszystko dostosowane do konkretnych wymagań pożądanej części. Zrozumienie i obliczenie tonażu dodatkowo zapewnia, że proces formowania tłocznego działa optymalnie, wytwarzając wysokiej jakości komponenty, które spełniają lub przekraczają standardy branżowe.
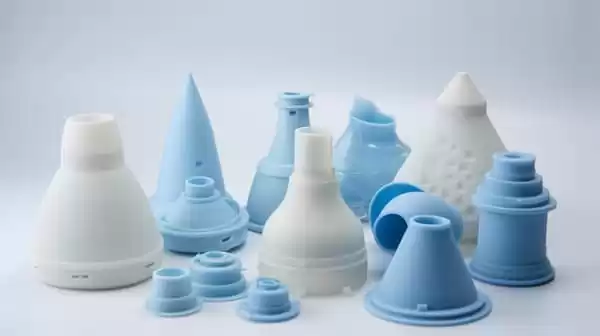
Wnioski
W tym kompleksowym badaniu formowania tłocznego i projektowania gniazd form, odkryliśmy skomplikowany świat procesu produkcyjnego, który pozostawia niezatarty ślad w wielu branżach.
Kończąc naszą analizę, zachęcamy czytelników do rozważenia formowania tłocznego dla swoich potrzeb produkcyjnych. Jego precyzja, wszechstronność i zdolność do dostarczania wysokiej jakości komponentów sprawiają, że jest to proces warty zbadania w szerokim zakresie zastosowań. Stosując formowanie tłoczne i wykorzystując moc odpowiedniej konstrukcji gniazda formy, producenci mogą odblokować świat możliwości, tworząc produkty, które nie tylko spełniają, ale przekraczają najwyższe standardy doskonałości w produkcji.